Luận án Nghiên cứu ảnh hưởng của một số yếu tố chính đến sự hình thành lớp thấm nitơ bằng phương pháp thấm nitơ plasma xung
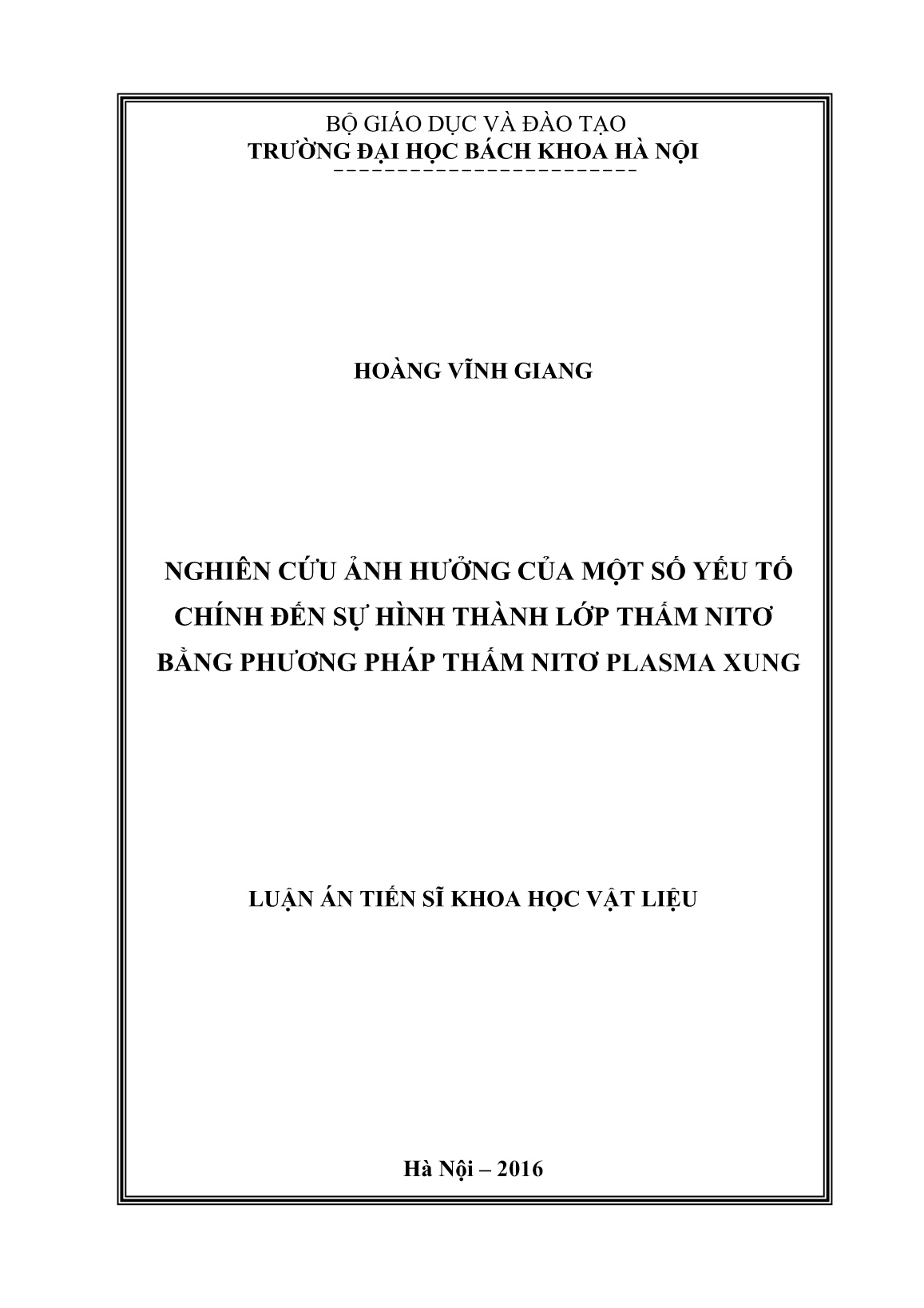
Trang 1
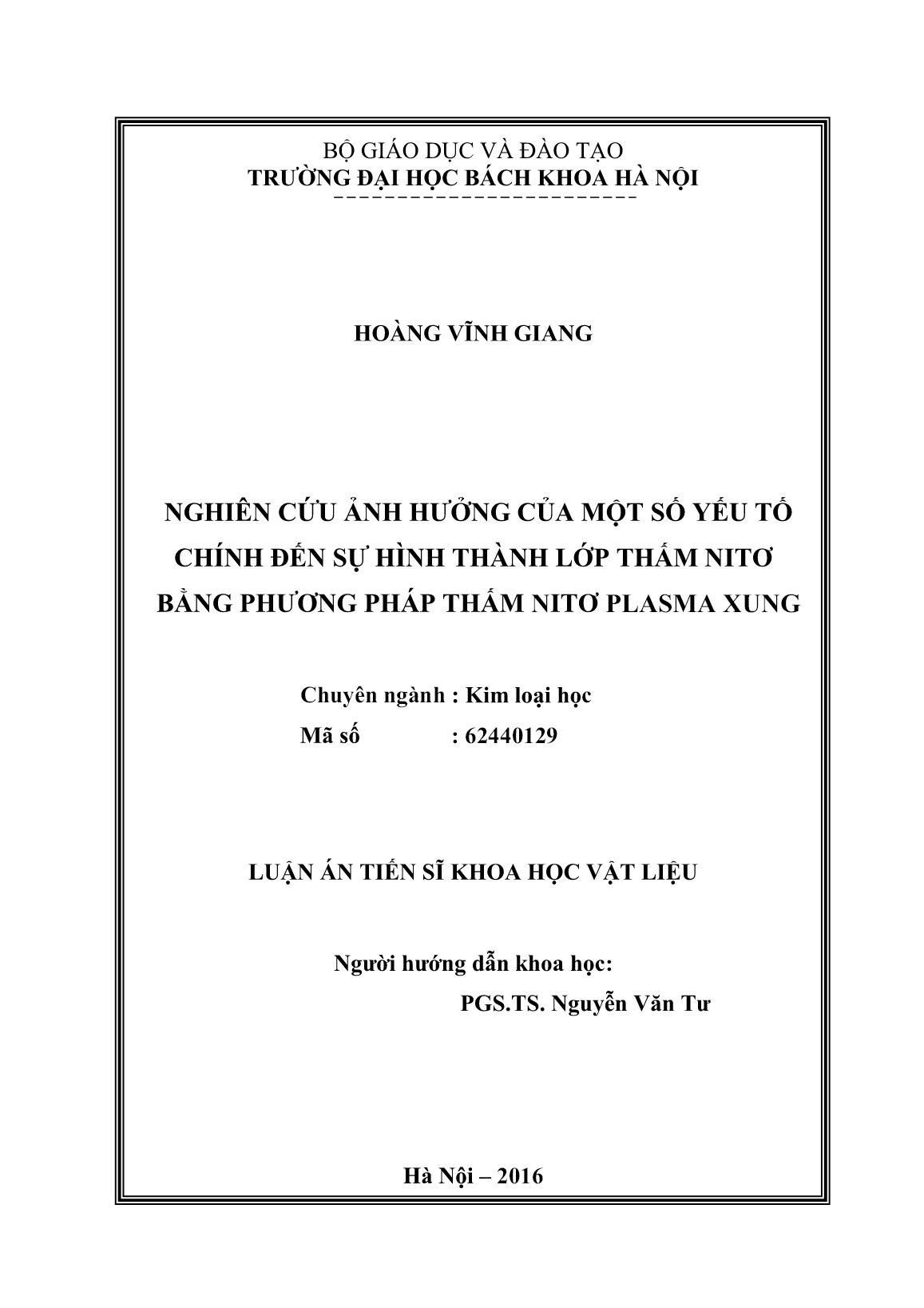
Trang 2
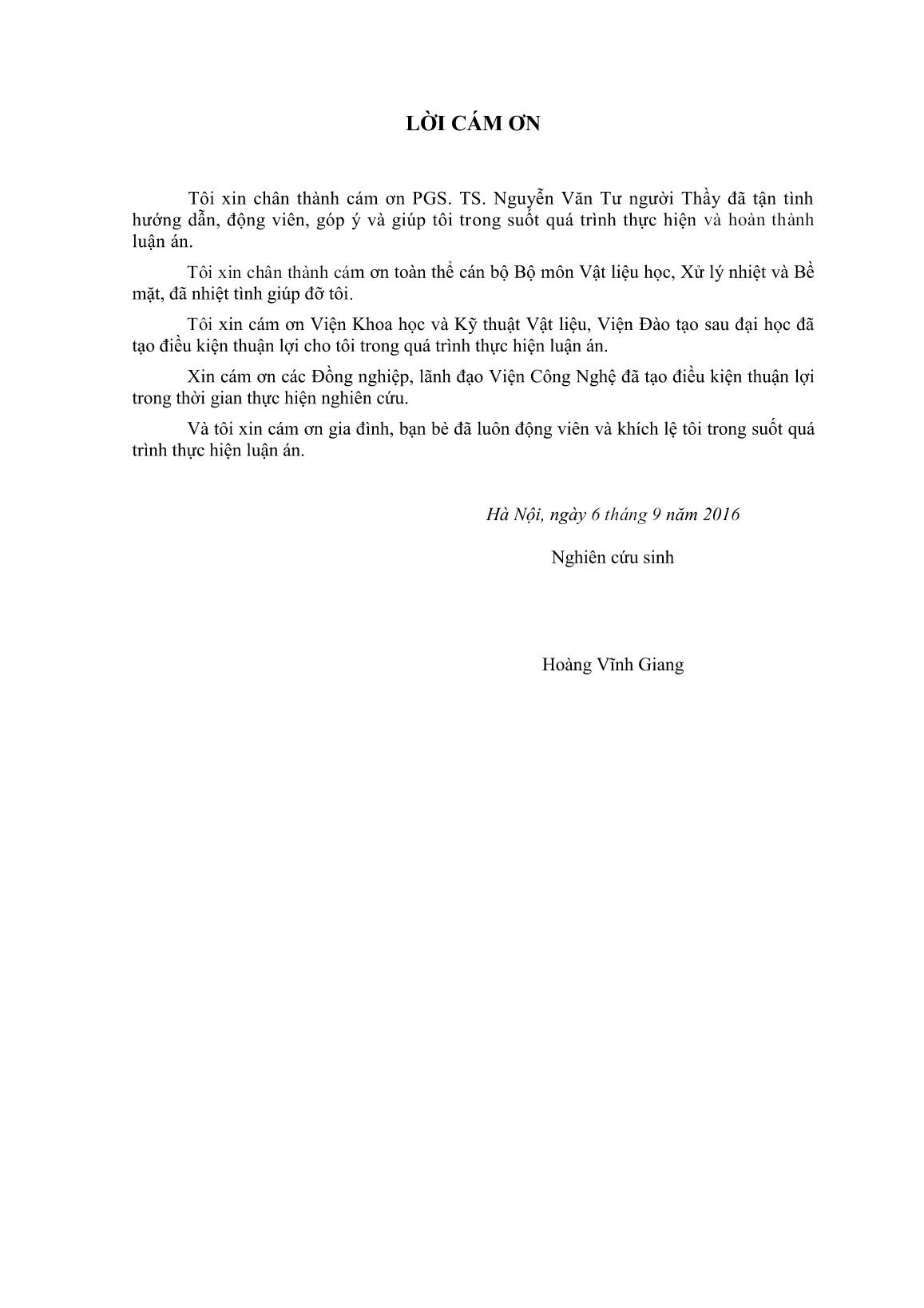
Trang 3
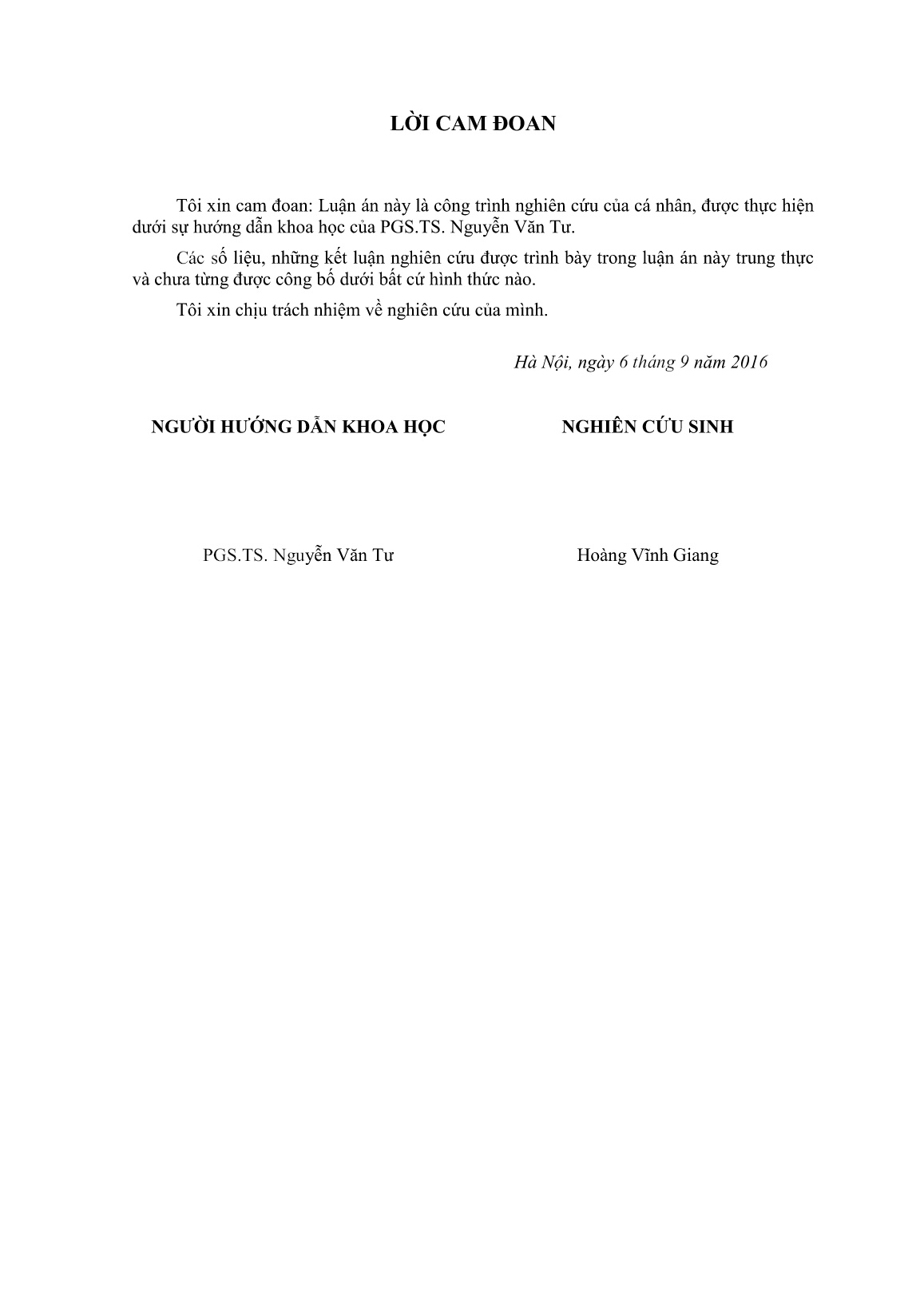
Trang 4
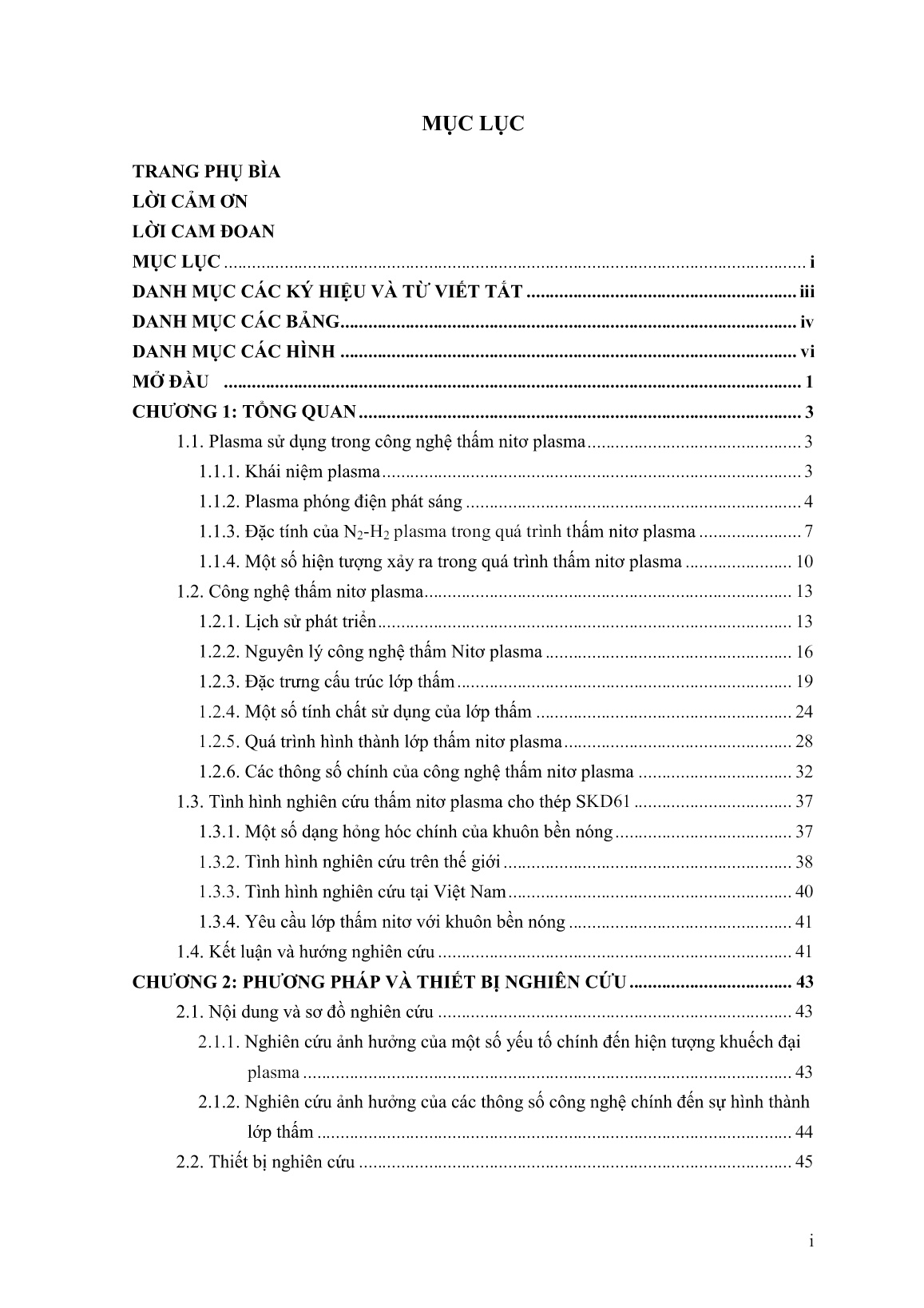
Trang 5
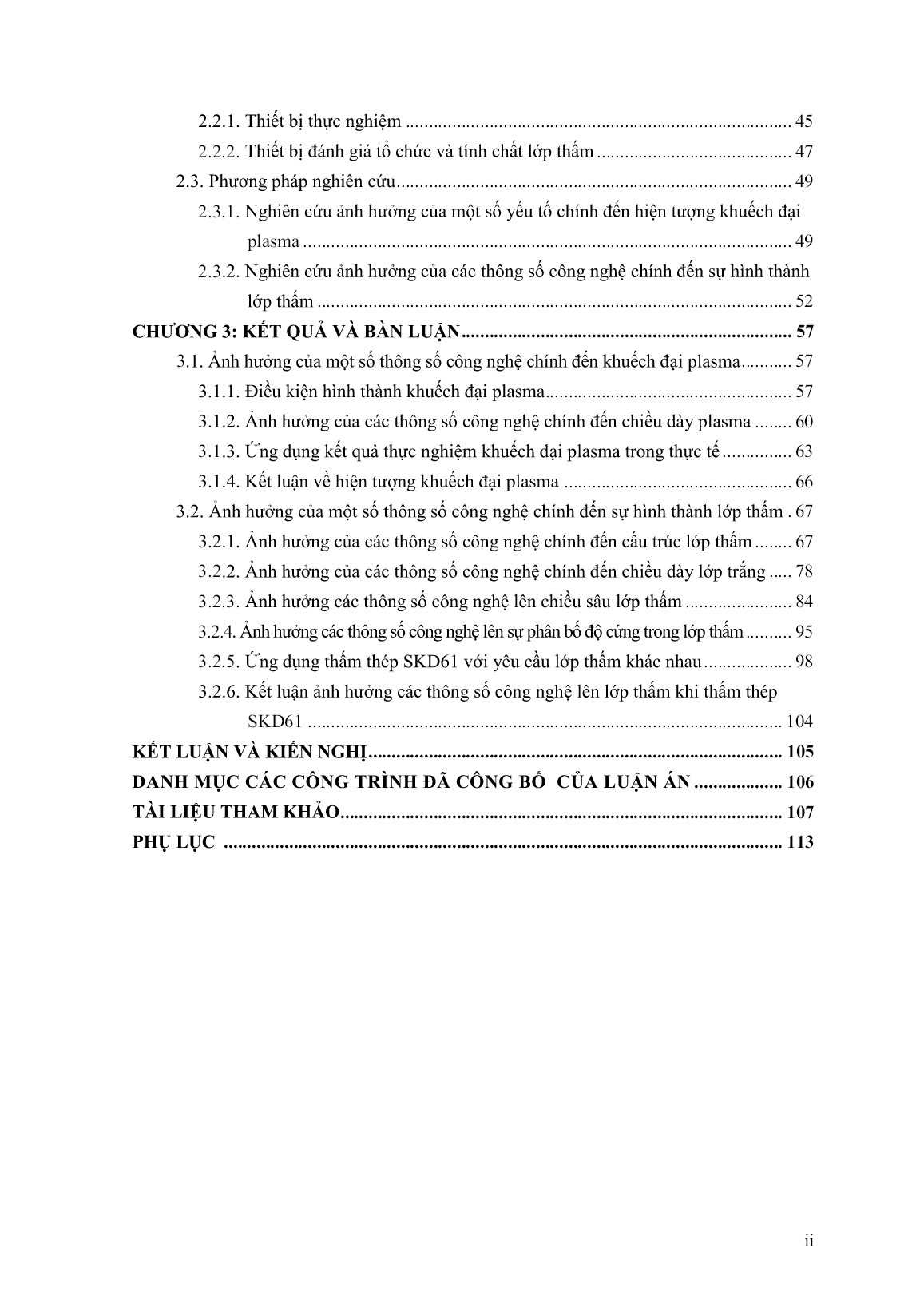
Trang 6
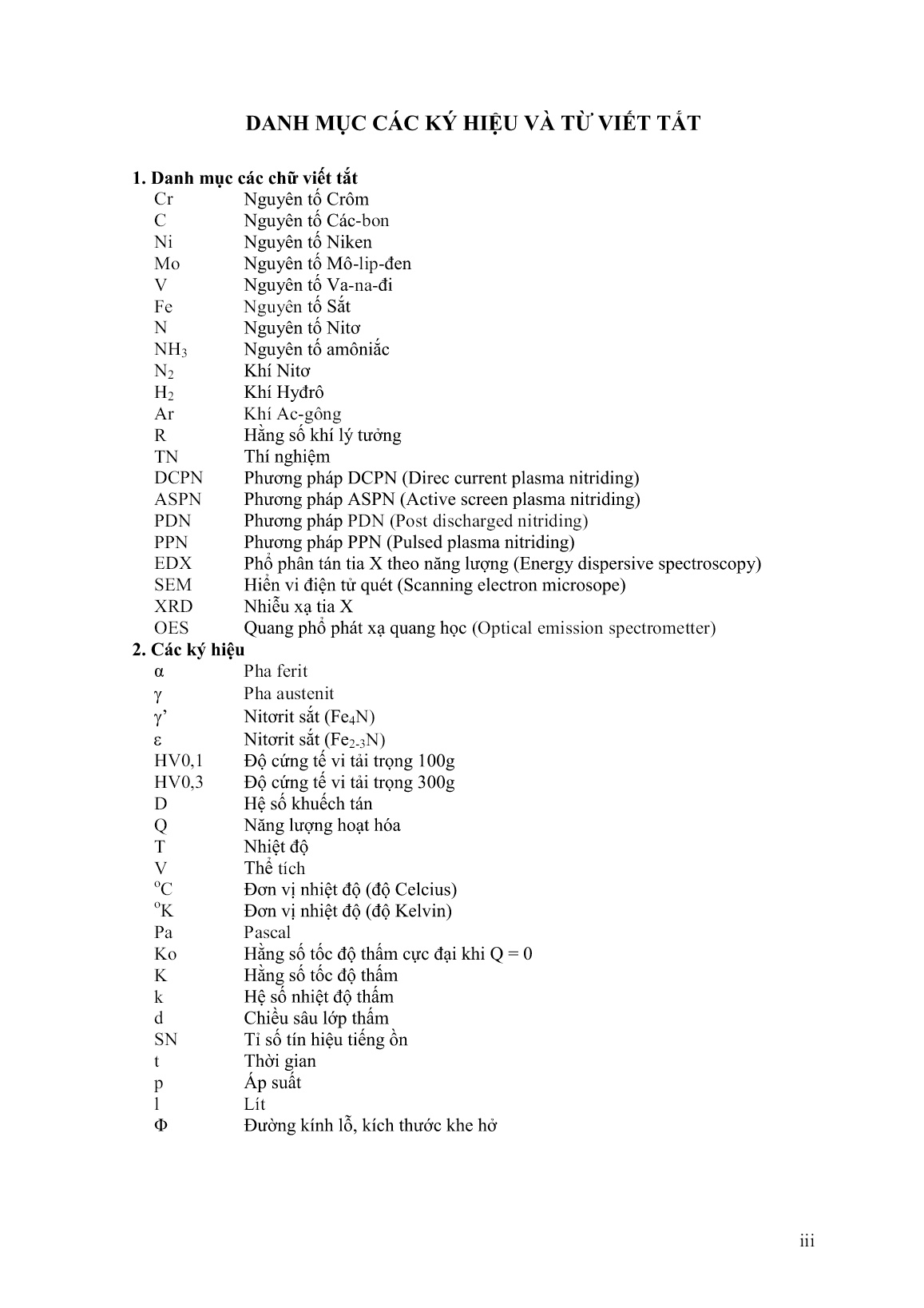
Trang 7
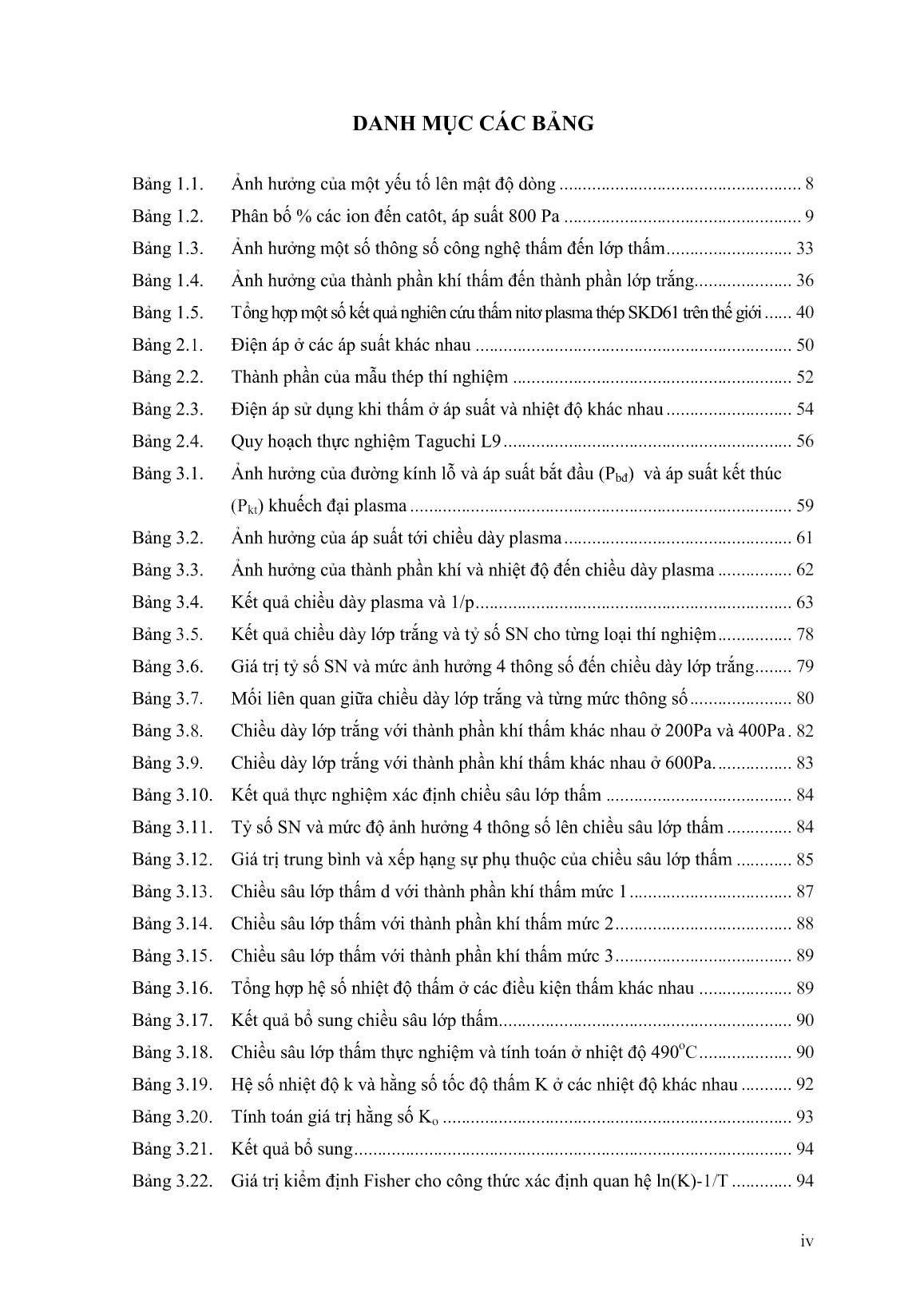
Trang 8
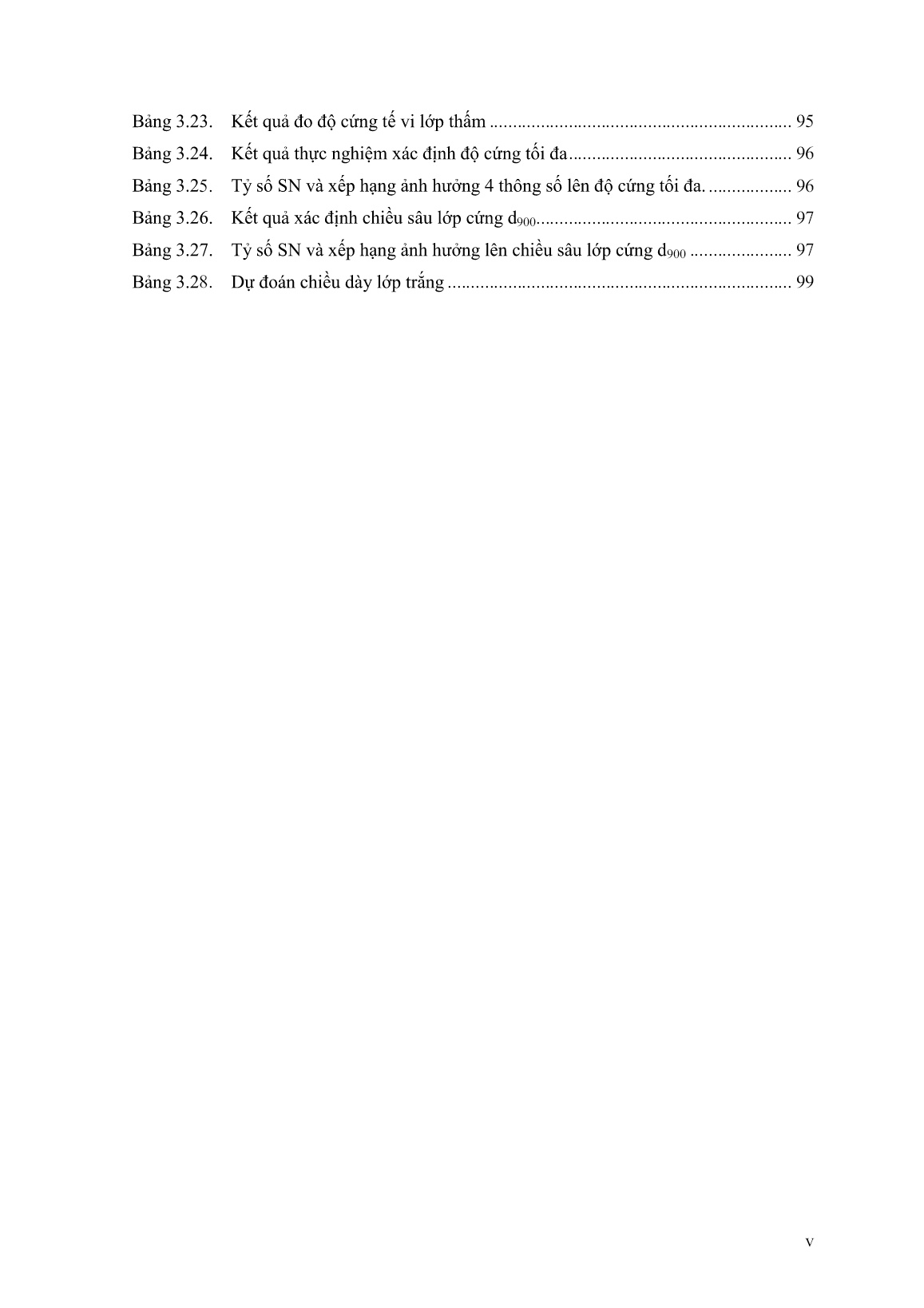
Trang 9
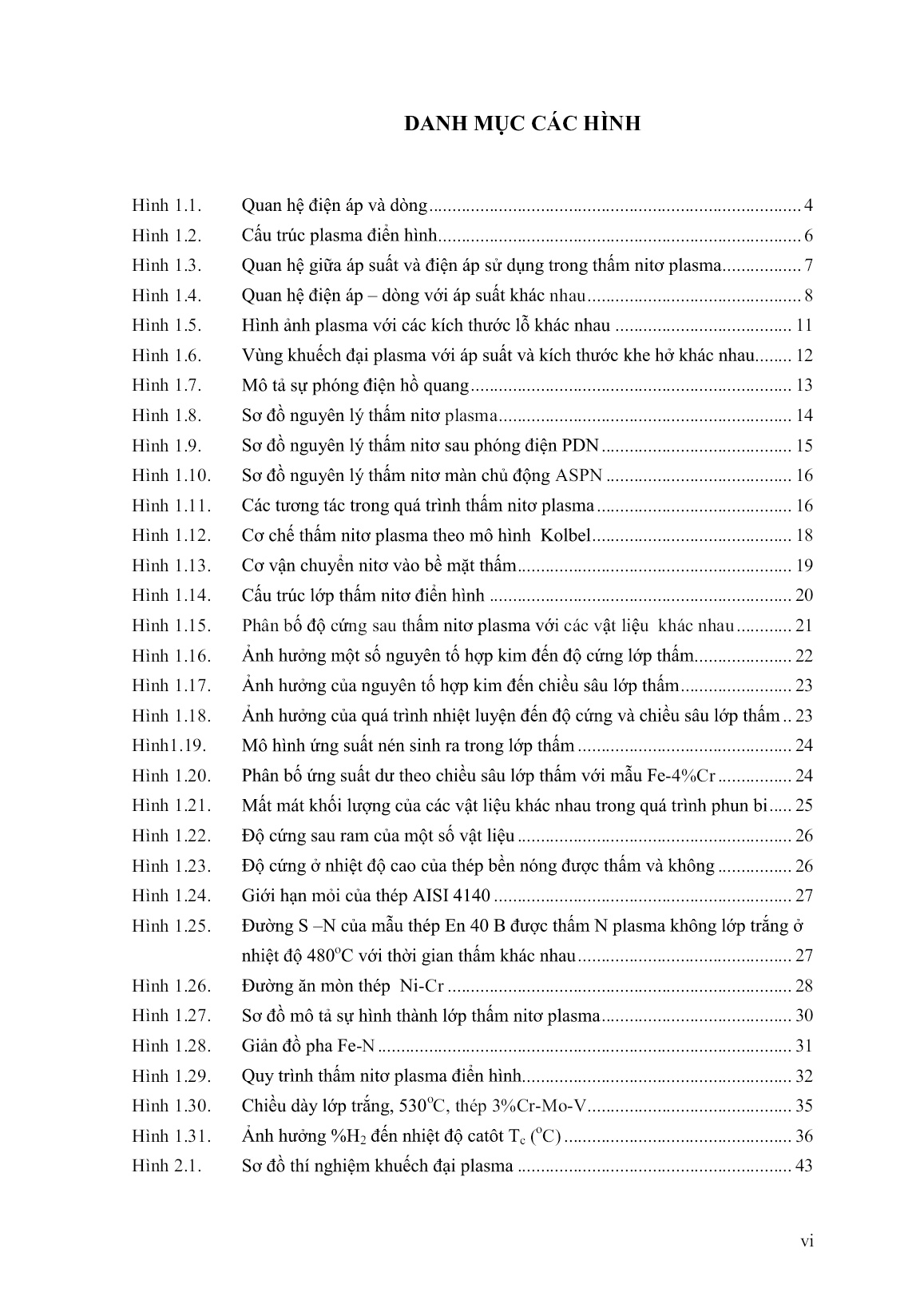
Trang 10
Tải về để xem bản đầy đủ
Bạn đang xem 10 trang mẫu của tài liệu "Luận án Nghiên cứu ảnh hưởng của một số yếu tố chính đến sự hình thành lớp thấm nitơ bằng phương pháp thấm nitơ plasma xung", để tải tài liệu gốc về máy hãy click vào nút Download ở trên.
Tóm tắt nội dung tài liệu: Luận án Nghiên cứu ảnh hưởng của một số yếu tố chính đến sự hình thành lớp thấm nitơ bằng phương pháp thấm nitơ plasma xung
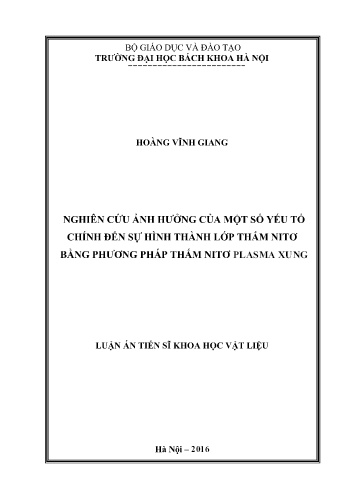
n 5 h, chiều dày lớp trắng tăng khi chu kỳ xung tăng. Có thể giải thích, khi chu kỳ xung tăng lượng khí N2 được ion hóa tăng tương tự như khi %N2 tăng và như vậy chiều dày lớp trắng tăng cũng là điều dễ hiểu. Gần đây, tác giả [55] đã nghiên cứu tăng hiệu quả thấm nitơ plasma cho thép AISI H13 bằng hoạt hóa bề mặt bằng cách phun bi bề mặt vật thấm. Phun bi có thể tạo ra những khuyết tật điểm từ đó thúc đẩy quá trình khuếch tán. Một số kết quả thấm nitơ plasma thép SKD61 hoặc AISI H13 được tổng hợp trong bảng 1.5. 40 Bảng 1.5. Tổng hợp một số kết quả nghiên cứu thấm nitơ plasma thép SKD61 trên thế giới TT Thông số công nghệ chính Chiều sâu [μm] Tài liệu tham khảo Ghi chú Thời gian [h] Khí %N2 Nhiệt độ [ o C] Áp suất [Pa] Lớp thấm Lớp trắng 1 16 10 520 350Pa 150 0 [43, 44] X38CrMoV5 4 10 560 60 0 16 10 560 150 0 16 80 520 260 5÷10 16 80 560 290 7÷15 2 6 <20 500 532 Pa 0 [104] SKD61 3 10 25 500 Không rõ 96,01 0 [100] H13 20 500 113,6 10 550 129,9 20 550 173 4 9 20 400 400Pa 43 3 [61] H13 16 20 400 50 3 36 20 400 73 3 5 7,5 530 550 Pa 100 có [37] H13 6 8 10 480 300Pa 55 0 [76] H13 7 4 20 525÷535 99 2÷4,5 [101] 20 256 3,4÷5,6 60 391 5,6÷6,7 8 18 20 515÷520 300 Pa 200 0 [77] H13 9 2÷16 20 470 9-11torr 0 [64] Thấm 10h, tuổi thọ tăng 8 lần 10 2 20 500 600Pa 38 [31, 32] H12, lớp trắng bão hòa t > 6 h 6 85 11 1 H2:N H3 4:1 500 133 Pa 30 0 [45] SKD61 5 75 0 10 96 2 5 450 35 0 500 75 0 550 100 0 1.3.3. Tình hình nghiên cứu tại Việt Nam Ở Việt Nam chưa có một công trình nghiên cứu công nghệ thấm nitơ plasma khảo sát đầy đủ các thông số công nghệ lên sự hình thành và đặc tính của lớp thấm. Trong các công bố [1, 2, 3, 4, 5, 6], các quy trình công nghệ thấm nitơ plasma chủ yếu thực hiện theo hướng dẫn của nhà cung cấp thiết bị. Các nhà công nghệ rất lúng túng khi thiết kế quy trình thấm khác nhau do chưa có hiểu biết đầy đủ về công nghệ thấm nitơ plasma. Hiện nay khuôn bền nóng như khuôn rèn, khuôn đúc, khuôn đùn nhôm được chế tạo từ thép bền nóng SKD61 đang được sử dụng khá phổ biến ở nước ta. Nhiều nghiên cứu đã tiến hành thấm nitơ cho các loại khuôn này nhằm mục đích nâng cao tuổi thọ. Công nghệ thấm plasma có thể tạo ra lớp thấm nitơ có các đặc trưng cấu trúc hoàn toàn đảm bảo yêu cầu làm việc và nâng cao tuổi thọ khuôn. Tuy nhiên các công bố về thấm nitơ plasma thép SKD61 còn rất ít [2, 3, 4], chỉ chủ yếu tập trung vào ảnh hưởng của các thông số công nghệ riêng biệt, các kết quả công bố đến nay còn rời rạc. 41 1.3.4. Yêu cầu lớp thấm nitơ với khuôn bền nóng Khuôn bền nóng thường đòi hỏi phải có các tính chất quan trọng như khả năng chống rạn nứt nóng, độ bền mỏi cao ở nhiệt độ cao, khả năng chịu mòn ở nhiệt độ cao.Thông thường khuôn bền nóng chế tạo từ thép SKD61 được tôi và ram cao đạt độ cứng khoảng (45÷50) HRC, ở trạng thái này khuôn đã có thể sử dụng mà không cần thấm. Tuy nhiên, để nâng cao tuổi thọ khuôn, thấm nitơ là một giả pháp rất hiệu quả. Có thể thấm nitơ thể lỏng, thể khí hoặc plasma. Các nghiên cứu thấm nitơ plasma thường tạo lớp thấm có một số đặc trưng chính sau [7, 9, 41, 44, 51, 56, 64, 66, 80, 100, 101]: - Độ cứng bề mặt cao, thông thường trong khoảng 1000 đến 1300 HV - Chiều sâu lớp thấm khoảng (0,1÷0,2) mm, chiều dày lớp trắng khoảng (0÷6) µm. - Giữ được độ cứng cao ở ngay ở nhiệt độ cao (500÷600)oC do đã được ram cao ở nhiệt đô cao hơn 550 oC vì thế có khả năng chịu mài mòn tốt ở điều kiện làm việc. - Ứng suất nén dư cao làm tăng bền mỏi do độ cứng bề mặt cao Tất cả các đặc tính này của lớp thấm góp phần làm tăng tuổi thọ của khuôn, đây là lý do khuôn được thấm nitơ. Tuy nhiên với các ứng dụng khác nhau, yêu cầu về lớp thấm nitơ cũng khác nhau. Các loại khuôn làm việc trong điều kiện áp lực bề mặt lớn như khuôn rèn, khuôn đúc áp lực, nếu lớp thấm có lớp trắng, đặc biệt lớp trắng dày, bong tróc thường xuất hiện. Với các loại khuôn này cần phải chọn các thông số công nghệ đảm bảo chiều dày lớp trắng nhỏ, mỏng hoặc không lớp trắng. Đối với các loại khuôn hỏng do mài mòn và ăn mòn thì có thể chọn công nghệ cho lớp trắng dày. Thấm nitơ plasma cho phép điều chỉnh một số thông số công nghệ chính để nhận được cấu trúc lớp thấm như mong muốn. Vì lý do đó công nghệ thấm nitơ plasma đang ngày càng được ứng dụng rộng rãi để thấm khuôn bền nóng. 1.4. Kết luận và hƣớng nghiên cứu Đặc điểm của công nghệ thấm nitơ plasma là môi trường thấm plasma được hình thành trực tiếp ngay trên sản phẩm và tính chất plasma có thể dễ dàng điều khiển bằng cách thay đổi các thông số công nghệ. Ưu điểm của công nghệ thấm nitơ plasma là cho phép dễ dàng điều chỉnh các thông số công nghệ để nhận được lớp thấm mong muốn. Nhược điểm hay gặp nhất là hiện hiện tượng khuếch đại plasma có thể phá hủy bề mặt sản phẩm thấm. Trên thế giới, thấm nitơ plasma đã được ứng dụng rộng rãi từ lâu trong công nghiệp và mang lại hiệu quả cao, nhất là cho các sản phẩm nhỏ, kết cấu đơn giản, sản lượng lớn. Gần đây công nghệ này cũng đã được nghiên cứu ứng dụng cho những sản phẩm phức tạp đặc biệt là thấm khuôn bền nóng. Ở Việt Nam, chỉ có một số đề tài nghiên cứu áp dụng cho loại thép và thiết bị thấm cụ thể, và hầu như làm theo hướng dẫn sử dụng của nhà cung cấp thiết bị. Các nghiên cứu trên chủ yếu tập trung vào ảnh hưởng riêng biệt của nhiệt độ, thời gian và thành phần khí thấm đến tính chất lớp thấm. Việc mở rộng công nghệ thấm này cho các sản phẩm có kết cấu phức tạp như khuôn bền nóng cần thiết phải có các nghiên cứu về khuếch đại plasma, sự hình thành cấu trúc lớp thấm (lớp trắng) nitơ plasma. Vì lý do đó việc nghiên cứu ảnh hưởng của các thông số công nghệ đến sự hình thành khuếch đại plasma trên các mẫu thép có lỗ và xây dựng phương trình thực nghiệm tính toán chiều dày plasma để từ đó dự báo điều kiện xuất hiện khuếch đại plasma để tránh là hết sức cần thiết. Công nghệ thấm nitơ plasma cho phép kiểm soát lớp trắng rất phù hợp để thấm các sản phẩm đòi hỏi chất lượng cao, như khuôn bền nóng chế tạo từ thép SKD61. Việc nghiên cứu một cách có hệ thống và xây dựng phương trình thực nghiệm về ảnh hưởng của đồng thời một số thông số công nghệ chính đến các đặc trưng cấu trúc cơ bản của lớp thấm cho thép dụng cụ bền nóng SKD61 là rất có ý nghĩa khoa học và giá trị thực tiễn. 42 Mục tiêu và đối tượng nghiên cứu Mục tiêu 1: Kiểm soát, loại trừ khuếch đại plasma thông qua việc xác định được điều kiện hình thành và không hình thành khuếch đại plasma trong quá trình thấm trên cơ sỏ chiều dày plasma. Đối tượng nghiên cứu 1: Cơ chế hình thành khuếch đại plasma, các thông số liên quan đến chiều dày plasma và sự hình thành khuếch đại plasma. Mục tiêu 2: Xác định ảnh hưởng của một số thông số công nghệ chính đến sự hình thành và đặc tính lớp thấm, từ đó xác định các thông số công nghệ thấm hợp lý để nhận được lớp thấm mong muốn khi thấm thép SKD61. Đối tượng nghiên cứu 2: Đặc tính của lớp thấm thép dụng cụ bền nóng SKD61 được thấm nitơ plasma với các thông số công nghệ khác nhau về thành phần khí thấm, nhiệt độ thấm, thời gian thấm và áp suất thấm. 43 CHƢƠNG 2: PHƢƠNG PHÁP VÀ THIẾT BỊ NGHIÊN CỨU 2.1. Nội dung và sơ đồ nghiên cứu Với hai mục tiêu và hai đối tượng nghiên cứu có hai nội dung và hai sơ đồ nghiên cứu tương ứng. 2.1.1. Nghiên cứu ảnh hƣởng của một số yếu tố chính đến hiện tƣợng khuếch đại plasma 2.1.1.1. Các nội dung chính Khuếch đại plasma là một hiện tượng gắn liền với công nghệ thấm nitơ plasma đặc biệt khi thực hiện trên thiết bị tường nguội do sản phẩm thấm đóng vai trò catot luôn chịu tác động một điện áp cao. Mặc dù sử dụng nguồn xung đã giảm đáng kể sự xuất hiện của hiện tượng này, nhưng luôn tồn tại một điều kiện nào đó khiến khuếch đại plasma xuất hiện gây nguy cơ phá hỏng sản phẩm. Vì lý do đó hiểu biết chắc chắn về hiện tượng khuếch đại plasma để tránh hoàn toàn trong quá trình thấm đặc biệt thấm các sản phẩm chất lượng cao, giá thành lớn như khuôn bền nóng là rất cần thiết, nội dung này bao gồm: 1. Xác định điều kiện hình thành khuếch đại plasma. 2. Nghiên cứu ảnh hưởng của một số thông số công nghệ chính (thành phần khí thấm, nhiệt độ, áp suất thấm) đến chiều dày plasma. 3. Xây dựng phương trình thực nghiệm xác định chiều dày plasma ở điều kiện thấm cụ thể. 4. Xây dựng vùng hình thành khuếch đại plasma để tránh trong quá trình thấm. 2.1.1.2. Sơ đồ thực nghiệm tổng quát Sơ đồ thực nghiệm hiện tượng khuếch đại plasma được thể hiện trên hình 2.1. Hình 2.1. Sơ đồ thí nghiệm khuếch đại plasma 44 2.1.2. Nghiên cứu ảnh hƣởng của các thông số công nghệ chính đến sự hình thành lớp thấm 2.1.2.1. Các nội dung chính Nghiên cứu này chọn thấm thép SKD61 đây là mác thép đang sử dụng phổ biến để chế tạo khuôn bền nóng và hiện có nhu cầu cao về thấm nitơ. Nội dung này bao gồm: 1. Thiết kế thực nghiệm bằng phương pháp quy hoạch thực nghiệm Taguchi sử dụng phần mềm Minitab 16. 2. Tiến hành xác định các đặc tính lớp thấm (tổ chức tế vi, thành phần pha, độ cứng, chiều dày lớp trắng, chiều sâu lớp thấm). 3. Đánh giá ảnh hưởng 4 thông số công nghệ chính (nhiệt độ, thời gian, thành phần và áp suất khí thấm) đến sự hình thành lớp thấm thông qua tổ chức tế vi lớp thấm và chiều dày lớp trắng. 4. Đánh giá ảnh hưởng của các thông số công nghệ chính đến chiều sâu lớp thấm, phân bố độ cứng. 5. Xây dựng mô hình tính toán chiều sâu lớp thấm, hằng số tốc độ thấm và năng lượng hoạt hóa. 6. Ứng dụng kết quả thực nghiệm để thấm thép SKD61 với các yêu cầu khác nhau về đặc tính lớp thấm. 2.1.2.2. Sơ đồ thực nghiệm tổng quát Sơ đồ thực nghiệm ảnh hưởng các thông số công nghệ được thể hiện trên hình 2.2. Hình 2.2. Sơ đồ thực nghiệm ảnh hưởng các thông số đến sự hình thành lớp thấm 45 2.2. Thiết bị nghiên cứu 2.2.1. Thiết bị thực nghiệm Thiết bị nhiệt luyện chân không Hình 2.3: Lò tôi chân không đơn buồng Turbo2 Treater M Lò tôi chân không đơn buồng Turbo2 Treater M của hãng IPSEN (CHLB Đức) với các thông số kỹ thuật như sau: - Phần mềm điều khiển: Vacu-Prof 4.1 - Nhiệt độ làm việc cao nhất: 1350oC - Áp suất khí tôi lớn nhất: 12 MPa - Độ chân không khi nung: <10 Pa - Khối lượng một mẻ tôi tối đa: 800 kg Thiết bị thấm nitơ plasma xung Hình 2.4: Lò thấm nitơ plasma Quá trình thấm được thực hiện trên lò thấm của hãng NITRION, model PN60. Đây là thiết bị thấm nitơ plasma xung tường nguội (hình 2.4) với các thông số chính: - Kích thước buồng: 680x900 mm - Công suất plasma: 60 kVA. - Nhiệt độ thấm max: 700oC - Chu kỳ xung tối đa: 650 µs - Điện áp nung tối đa: 800 V. - Áp suất làm việc: (40 ÷1000) Pa Các thông số của quá trình thấm như: điện áp, chu kỳ xung, nhiệt độ, thành phần khí thấm, thời gian thấm được lập trình bằng chương trình Demig Prosys. Quá trình thấm được kiểm soát hoàn toàn tự động (hình 2.5). 46 Hình 2.5: Giao diện chương trình thấm Khí thấm được cấp vào lò qua hệ thống lưu lượng kế điều khiển bằng van từ (mass-flowmeter) model 1179B của hãng MKS được điều khiển tự động lưu lượng lít/h (hình 2.6) với các dải đo cơ bản như sau: NH3 : 100 l/h CH4 : 30 l/h H2 : 200 l/h CO2 : 30 l/h Ar : 30 l/h N2 : 200 l/h Độ chính xác: ± 0,5% Hình 2.6: Hệ thống lưu lượng kế điều khiển cung cấp khí thấm Nhiệt độ đo bằng can K, đường kính 1,6 mm, dải đo (0 ÷ 1200)oC, được cắm trực tiếp trên mẫu. 47 Hình 2.7: Can nhiệt loại K đo nhiệt độ mẫu thấm Áp suất quá trình thấm được đo bởi sensor đo áp suất model PN5400 (hình 2.8), với dải đo đến 1 MPa với độ chính xác < ± 0,5%, độ lặp lại < ± 0,1. Áp suất trong buồng lò thấm được duy trì bởi 1 bơm chân không 2,2KW được điều khiển tự động. Hình 2.8: Thiết bị đo áp suất 2.2.2. Thiết bị đánh giá tổ chức và tính chất lớp thấm Thiết bị soi chụp kim tương Hình 2.9: Kính hiển vi quang học Axiovert 25A Tổ chức lớp thấm được quan sát trên kính hiển vi quang học Axiovert 25A của hang Carl Zeiss của CHLB Đức (hình 2.9) với độ phóng đại 50x, 100x, 500x. 48 Việc xác định phân bố độ cứng tế vi của lớp thấm được thực hiện trên máy đo độ cứng tế vi FM-700e, FUTURE-TECH của Nhật Bản (hình 2.10) với các tải trọng 50 g, 100 g, 200 g, 300 g, 500 g và 1000 g. Hình 2.10: Máy đo độ cứng tế vi FM-700e Thiết bị phân tích thành phần hóa học Mẫu thí nghiệm được kiểm tra thành phần hóa học trên thiết bị phân tích quang phổ phát xạ nguyên tử ARL 3460 Thụy Sỹ (hình 2.11) với một số đặc điểm sau: - Nền phân tích: Sắt - Các hệ thép phân tích: thép hợp kim thấp, thép Cr-Ni, thép Cr, thép gió, gang. - Phân tích các nguyên tố: C, Si, P, S, Cu, Cr, Mn, W, Mo, Ni, V, N Hình 2.11: Máy quang phổ phát xạ nguyên tử ARL3460 Thiết bị xác định thành phần pha Để đánh giá sự tồn tại của các pha trong lớp thấm, đề tài đã sử dụng thiết bị phân tích nhiễu xạ tia X D5005 của hãng Siemens (hình 2.12). Các thông số đặc trưng của thiết bị khi sử dụng: - Bức xạ tia X: anôt bằng đồng, = 1,54056 µm - Góc quét 2 từ: 0,2o đến 150o 49 Hình 2.12: Thiết bị nhiễu xạ tia X (D5005) Thiết bị hiển vi điện tử quét (SEM) Hình 2.13: Hiển vi điện tử quét (SEM) Thiết bị hiển vi điện tử quét (SEM) được dùng để xác định sự phân bố các nguyên tố trên mặt cắt ngang của mẫu sau thấm (phổ mapping) và xác định sự tồn tại của các pha cabit, nitơrit trong tổ chức của lớp thấm (hình 2.13) Một số thông số cơ bản của thiết bị: - Độ phân giải cao ~ 2 nm. - Hiệu điện thế gia tốc từ 200 V tới 30 kV. - Độ phóng đại từ 20 đến 1.000.000 lần. 2.3. Phƣơng pháp nghiên cứu 2.3.1. Nghiên cứu ảnh hƣởng của một số yếu tố chính đến hiện tƣợng khuếch đại plasma Sự xuất hiện khuếch đại plasma phụ thuộc vào điều kiện thấm và bản chất vật thấm nhìn từ góc độ hình dáng, kích thước và cách bố trí sản phẩm, không liên quan đến thành phần, tổ chức vật liệu thấm. Thông thường trong quá trình thấm nitơ plasma không được xuất hiện hiện tượng này, còn nếu xuất hiện do chủ định thì lúc này quá trình hình thành lớp thấm cũng khác. Vì lý do đó hiểu biết sâu và chắc chắn về hiện tượng khuếch đại plasma để tránh là rất cần thiết, kết quả nghiên cứu hiện tượng này có thể áp dụng cho bất cứ vật liệu thấm nền sắt nào. 2.3.1.1. Mẫu và bố trí mẫu thí nghiệm - 01 mẫu trụ đường kính ngoài Φ50 mm, mẫu này dùng để đo chiều dày plasma. - 03 mẫu kích thước 50x50x20 mm làm thành 1 catot đơn và catot đôi gồm 2 catot song song cách nhau 7 mm. - 11 mẫu ống thép đường kính trong từ 3 mm đến 13 mm, chiều dày thành ống 2 mm đến 3 mm, chiều dài bằng 2 lần đường kính ống. Thực nghiệm quá trình hình thành và mất đi của hiện tượng khuếch đại plasma và đo chiều dày plasma được thể hiện trên hình 2.14. Thực nghiệm khuếch đại plasma trên các ống rỗng có đường kính khác nhau được bố trí như trên hình 2.15. 50 Hình 2.14: Khuếch đại plasma với 2 mẫu cách nhau cố định 7mm Hình 2.15: Bố trí thí nghiệm khuếch đại plasma trên các ống rỗng 2.3.1.2. Các thông số công nghệ chính Đo chiều dày plasma được thực hiện với các thông số chính: Điện áp (400÷700) V, xung on/off: 600 / (600÷200) μs Khí thấm: 65%H2+35%N2 , 75%H2+25%N2, 85%H2+15%N2 Nhiệt độ: 490 oC, 520oC và 550 oC Áp suất thay đổi: (120÷800) Pa Sự khác biệt được chủ động điều chỉnh là điện áp với áp suất và với nhiệt độ thấm. Áp suất thấp cần điện áp cao hơn thì cần duy trì một điện áp cao hơn Bảng 2.1. Điện áp ở các áp suất khác nhau Áp suất [Pa] Điện áp [V] 550 o C 520 o C 490 o C 200 700 660 650 250 650 640 630 300 630 620 610 350 600 590 580 400 580 560 550 500 550 530 510 600 530 500 480 700 500 450 440 800 480 430 420 900 450 420 410 51 Xác định khuếch đại plasma trên các ống rỗng được thực hiện với các thông số chính sau: Điện áp (400÷700) V, xung on/off: 600/(600÷200) μs Khí thấm :75%H2+25%N2 Nhiệt độ 520oC, Áp suất thay đổi: (120÷800) Pa Sự khác biệt được chủ động điều chỉnh bằng thay đổi áp suất. 2.3.1.3. Theo dõi quá trình hình thành và mất đi khuếch đại plasma Plasma được theo dõi qua cửa quan sát làm bằng thủy tinh trong suốt. Khuếch đại plasma hình thành khi vùng sáng âm của 2 catốt chồng lên nhau, lúc này cường độ phát sáng của plasma tăng lên rõ rệt. Dựa vào mức độ phát sáng (quan sát bằng mắt thường) chúng ta dễ dàng phát hiện lúc nào khuếch đại plasma xuất hiện và lúc nào kết thúc. Ứng với mỗi lần xuất hiện hoặc kết thúc, ghi lại các thông số bao gồm đường kính lỗ xuất hiện khuếch đại plasma, áp suất lúc xuất hiện, áp suất kết thúc. 2.3.1.4. Xác định chiều dày plasma Sử dụng camera kỹ thuật số để chụp ảnh cấu trúc plasma từ đó xác định kích thước chiều rộng vùng catôt trên ảnh chụp. Trên ảnh chụp cấu trúc plasma hình thành trên mẫu trụ đường kính ngoài D = 50 mm có thể phân biệt các vùng sáng khác nhau ở gần bề mặt catốt (hình 2.16). Chiều dày tính từ bề mặt catôt đến hết vùng tối gọi là chiều rộng vùng catôt hay chiều dày plasma dc. Tiếp theo là vùng sáng âm, sáng nhất phía catốt và giảm dần về phía anôt. Để xác định chính xác chiều dày plasma cần phải xác định chính xác biên giới giữa 2 vùng này. Khi áp suất thấp ( 400Pa) biên giới giữa vùng sáng âm và vùng tối catôt rõ ràng nên việc xác định dc khá dễ dàng. Khi vùng áp suất cao hơn (từ 500 đến 800 Pa) plasma ôm sát bề mặt catốt, vùng catốt bị thu hẹp lại, biên giới giữa vùng catốt và vùng sáng âm không sắc nét nên việc xác định biên giới khó khăn hơn, tuy nhiên ngay cả như vậy sai số giá trị của các lần đo dự kiến khoảng 10%. Ảnh hưởng của áp suất đến chiều dày plasma trong khoảng áp suất nghiên cứu là rất lớn, khi thay đổi áp suất thì chiều dày plasma biến đổi mạnh, do đó với độ chính xác phép đo khoảng 10% là chấp nhận được để nghiên cứu. Hình 2.16: Xác định chiều dày plasma dc Chiều dày plasma dc được xác định theo công thức: 2 c c D D d (2.1) Trong đó: D là đường kính catôt (hình 2.16). Dc là đường kính bao trùng cả vùng catốt. 52 2.3.1.5. Xây dựng phương trình tính toán chiều dày plasma Chiều dày plasma dc được tính theo phương trình (1.2) được mô tả trong chương 1: c B d A p Hai hằng số A và B sẽ được xác định bằng thực nghiệm từ kết quả chiều dày plasma đo được ở một điều kiện thấm nhất định về thành phần khí thấm và nhiệt độ thấm với các áp suất thấm khác nhau. 2.3.2. Nghiên cứu ảnh hƣởng của các thông số công nghệ chính đến sự hình thành lớp thấm Quá trình thấm được lập trình và điều khiển tự động bằng phần mềm chuyên dụng thông qua máy tính. Bốn thông số công nghệ chính của quá trình thấm là nhiệt độ, thời gian, thành phần và áp suất khí thấm được lựa chon tùy theo yêu cầu về đặc tính của lớp thấm cần đạt. Đặc tính lớp thấm nhận được phản ảnh kết quả thấm theo chế độ với các thông số công nghệ đã lựa chọn. Các thông số công nghệ này ảnh hưởng lẫn nhau do đó việc xác định thông số công nghệ hợp lý càng trở nên phức tạp hơn. Việc sử dụng phương pháp Taguchi để quy hoạch thực nghiệm một số thông số công nghệ chính có thể cho chúng ta cái nhìn định hướng tổng thể về ảnh hưởng đồng thời của các thông số này đến kết quả thấm từ đó giúp lựa chọn thông số công nghệ thấm hợp lý cho yêu cầu đặt ra. 2.3.2.1. Mẫu và bố trí mẫu thí nghiệm Mục đích của thực nghiệm là nghiên cứu ảnh hưởng của một số thông số công nghệ chính đến sự hình thành và đặc tính lớp thấm. Tuy nhiên sự hình thành cũng như đặc tính lớp thấm phụ thuộc rất lớn vào vật liệu thấm. Nghiên cứu này chỉ nghiên cứu ảnh hưởng của các thông số công nghệ khi thấm thép SKD61 đã được tôi ram đạt độ cứng (45÷50) HRC và trong quá trình thấm không xuất hiện khuếch đại plasma. Mẫu thấm dày 10 mm được cắt từ thép cây đường kính 25 đến 30 mm. Thành phần hóa học được phân tích trên máy quang phổ phát xạ nguyên tử ARL-3460 tại Viện Công nghệ, kết quả phân tích trong Bảng 2.2. Có th
File đính kèm:
luan_an_nghien_cuu_anh_huong_cua_mot_so_yeu_to_chinh_den_su.pdf
THONG TIN TOM TAT KET LUAN MOI (TIENG ANH).pdf
THONG TIN TOM TAT KET LUAN MOI (TIENG VIET).pdf
TOM TAT LUAN AN.pdf