Luận án Nghiên cứu ảnh hưởng của titan và nguyên tố đất hiếm đến tính chất mài mòn, độ dai va đập của gang trắng 13% Crôm
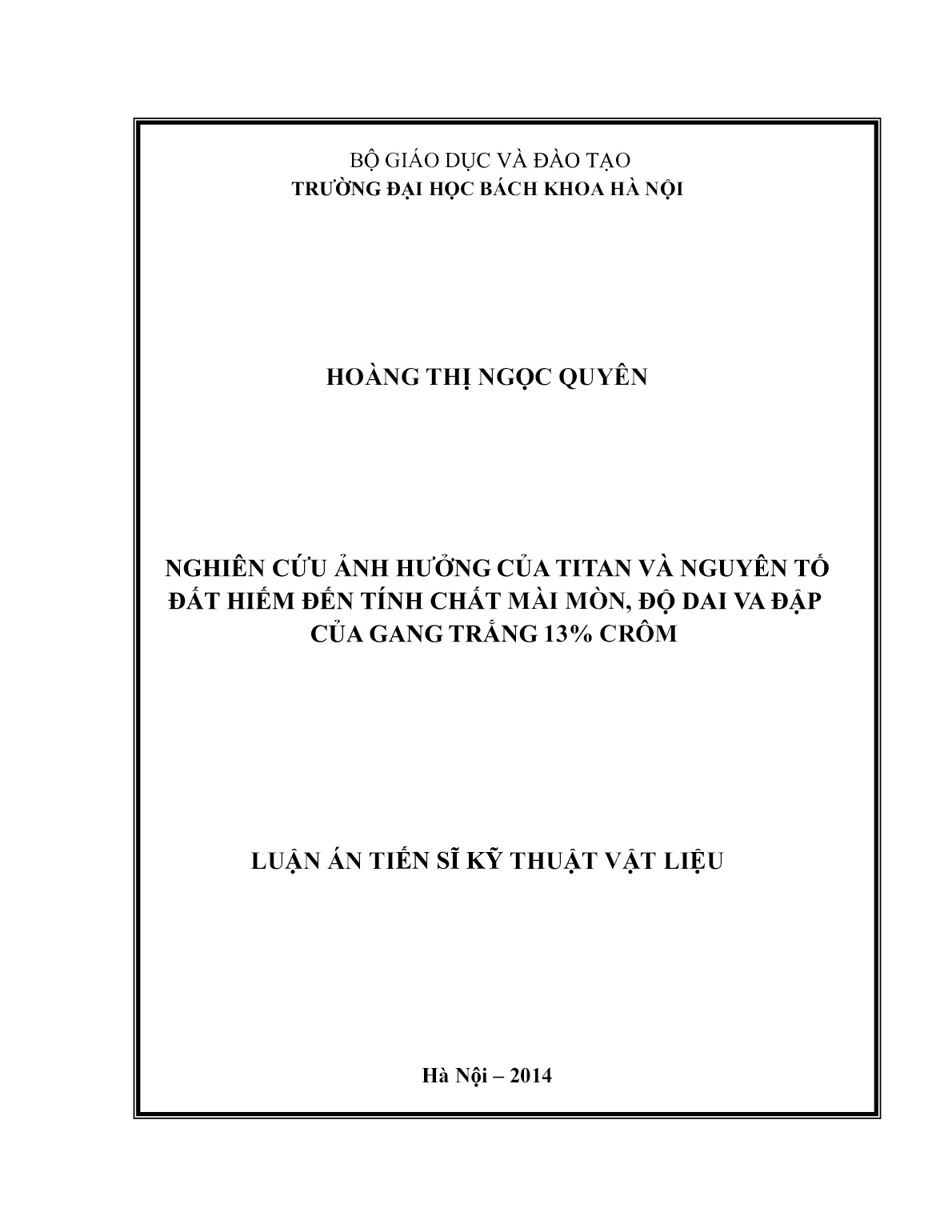
Trang 1
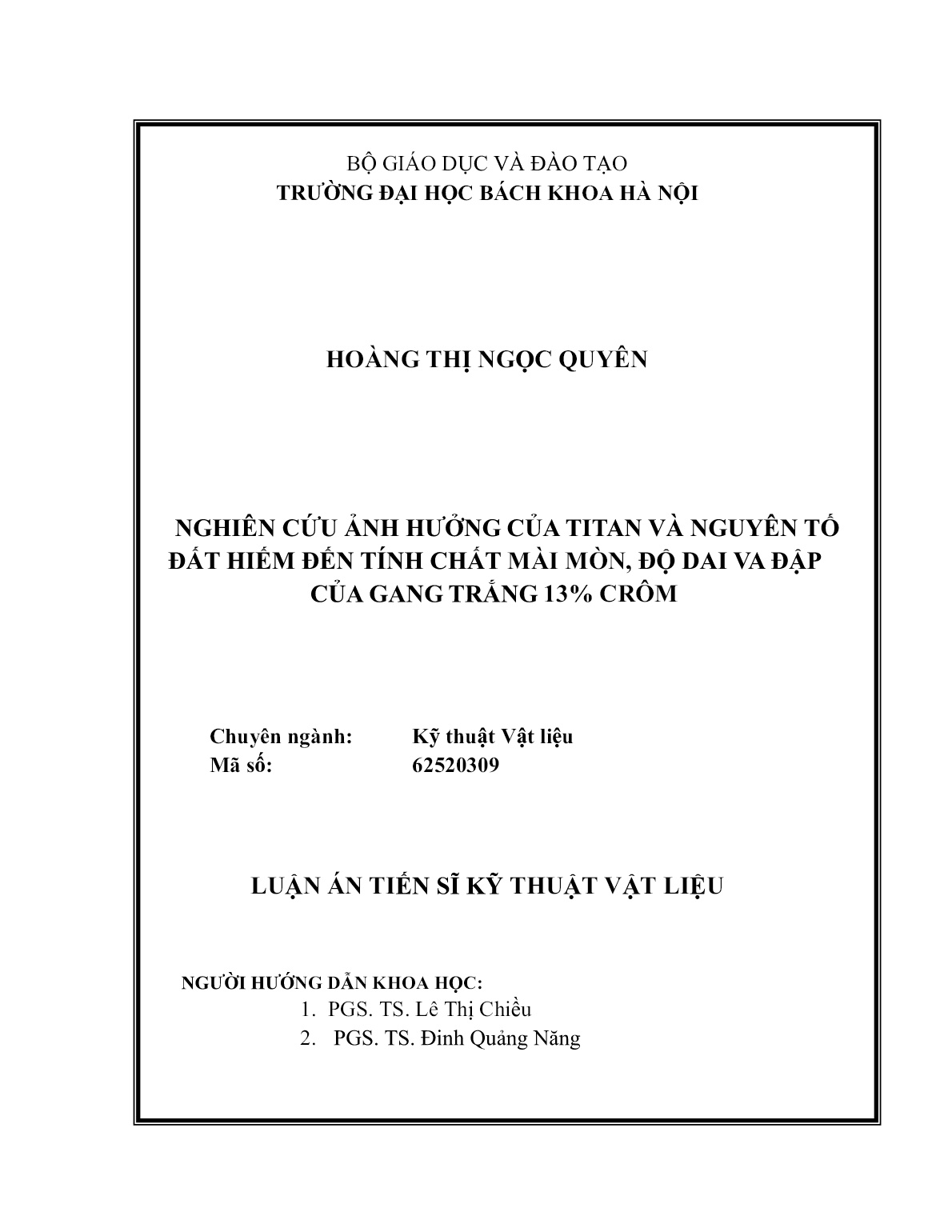
Trang 2
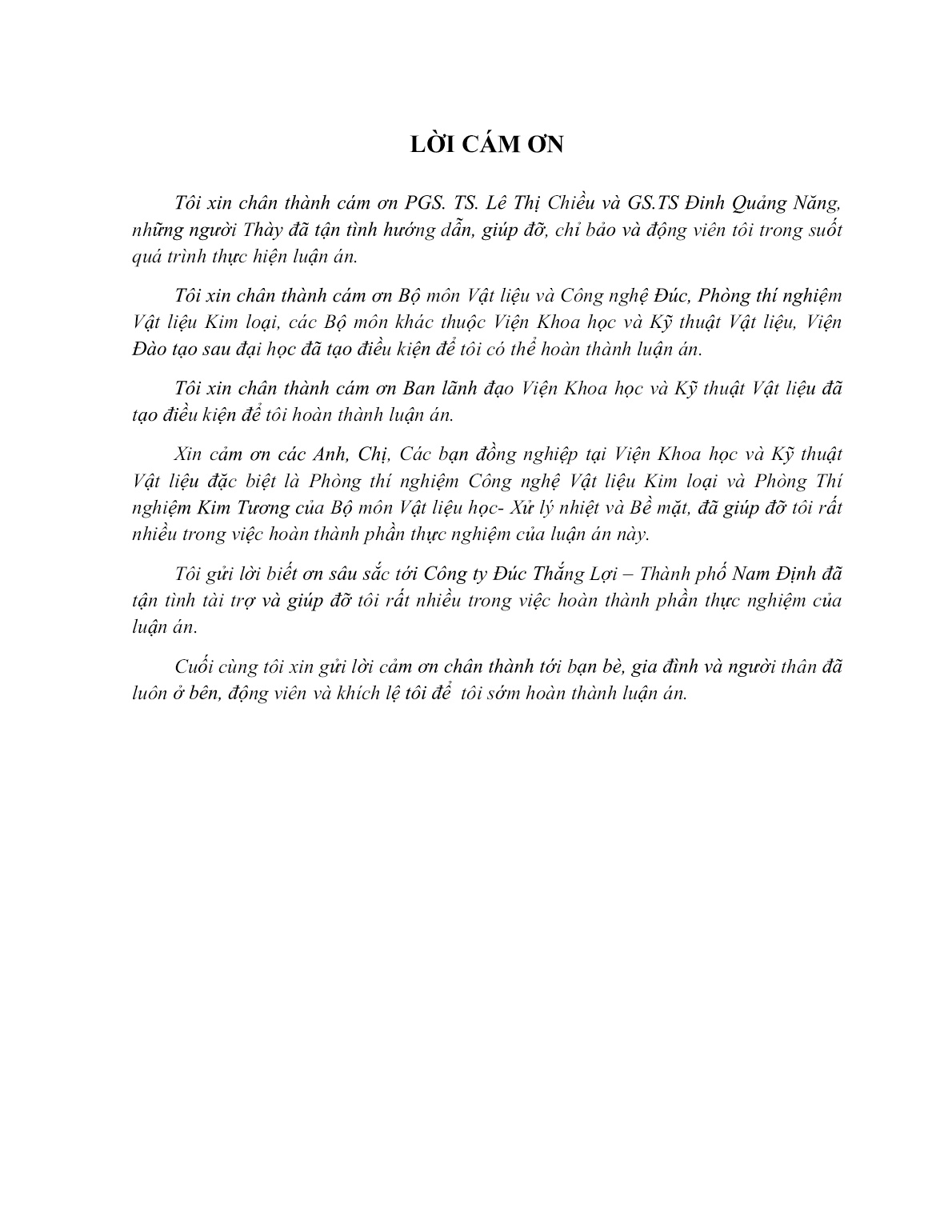
Trang 3
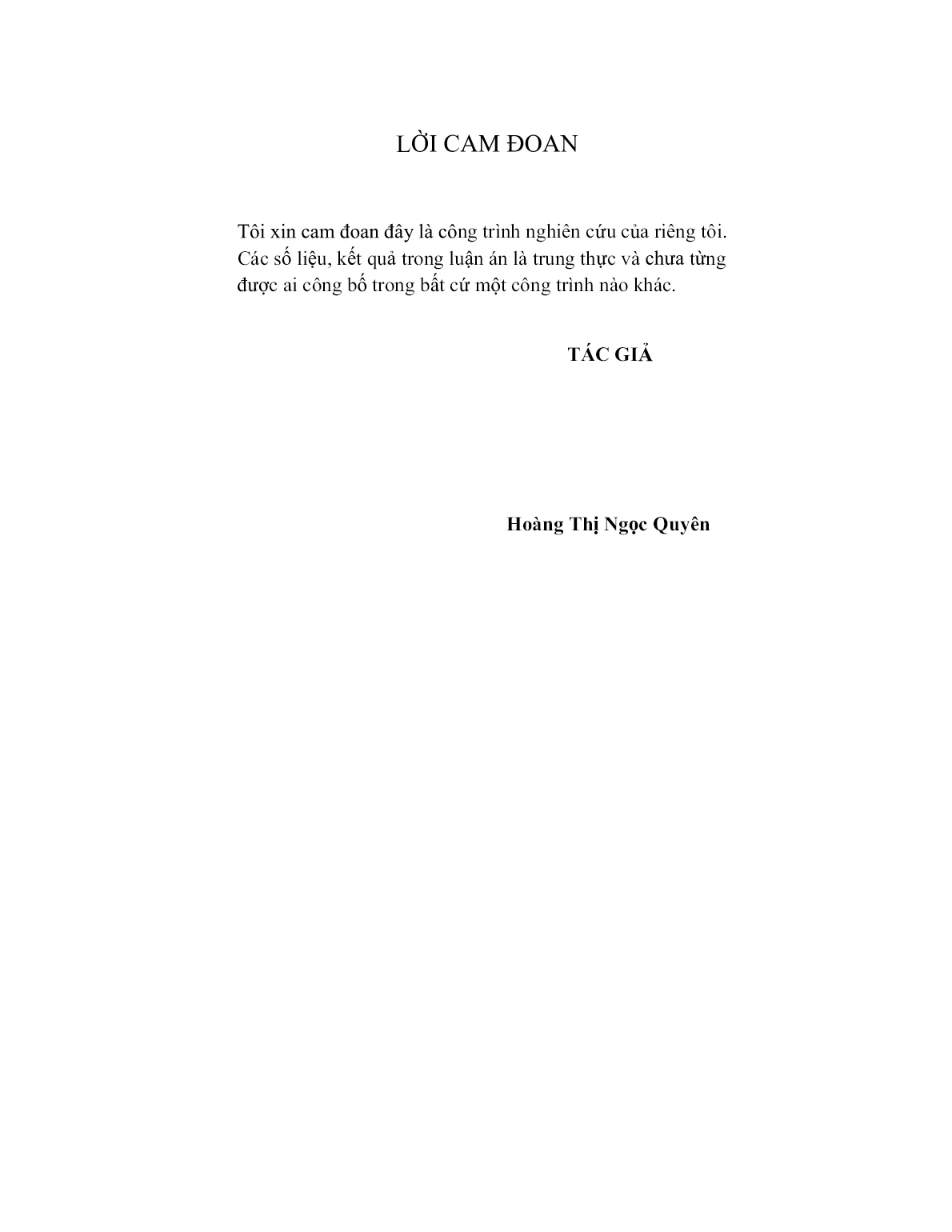
Trang 4
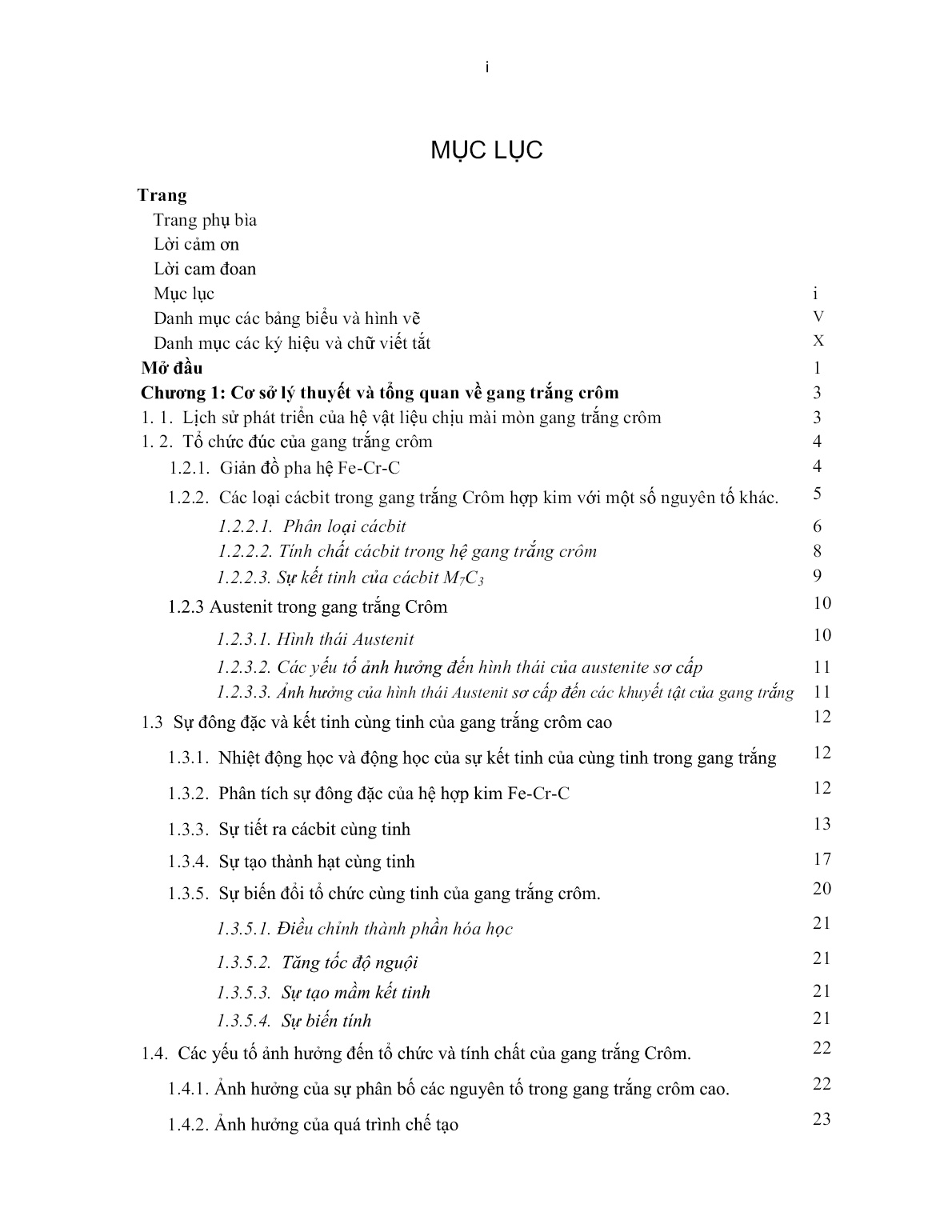
Trang 5
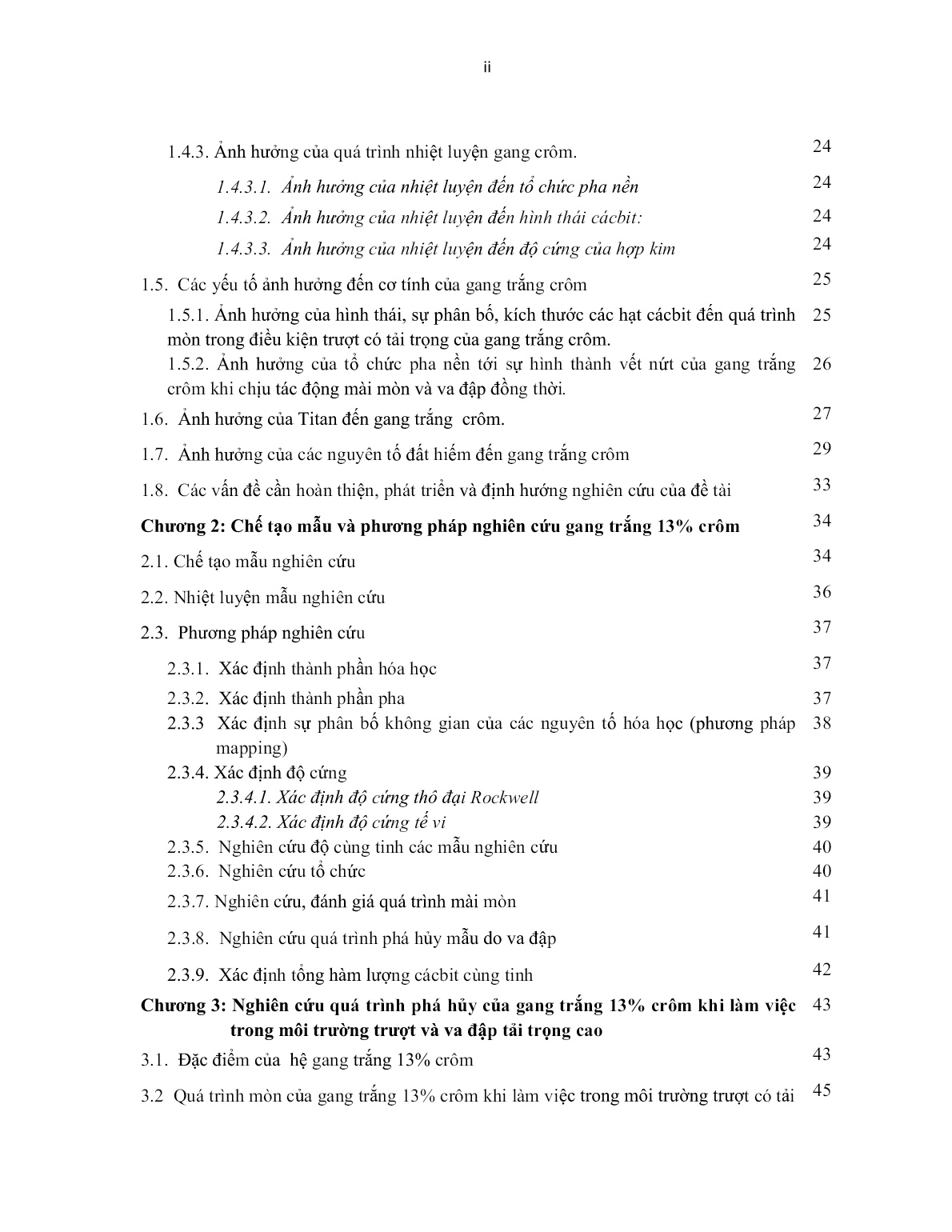
Trang 6
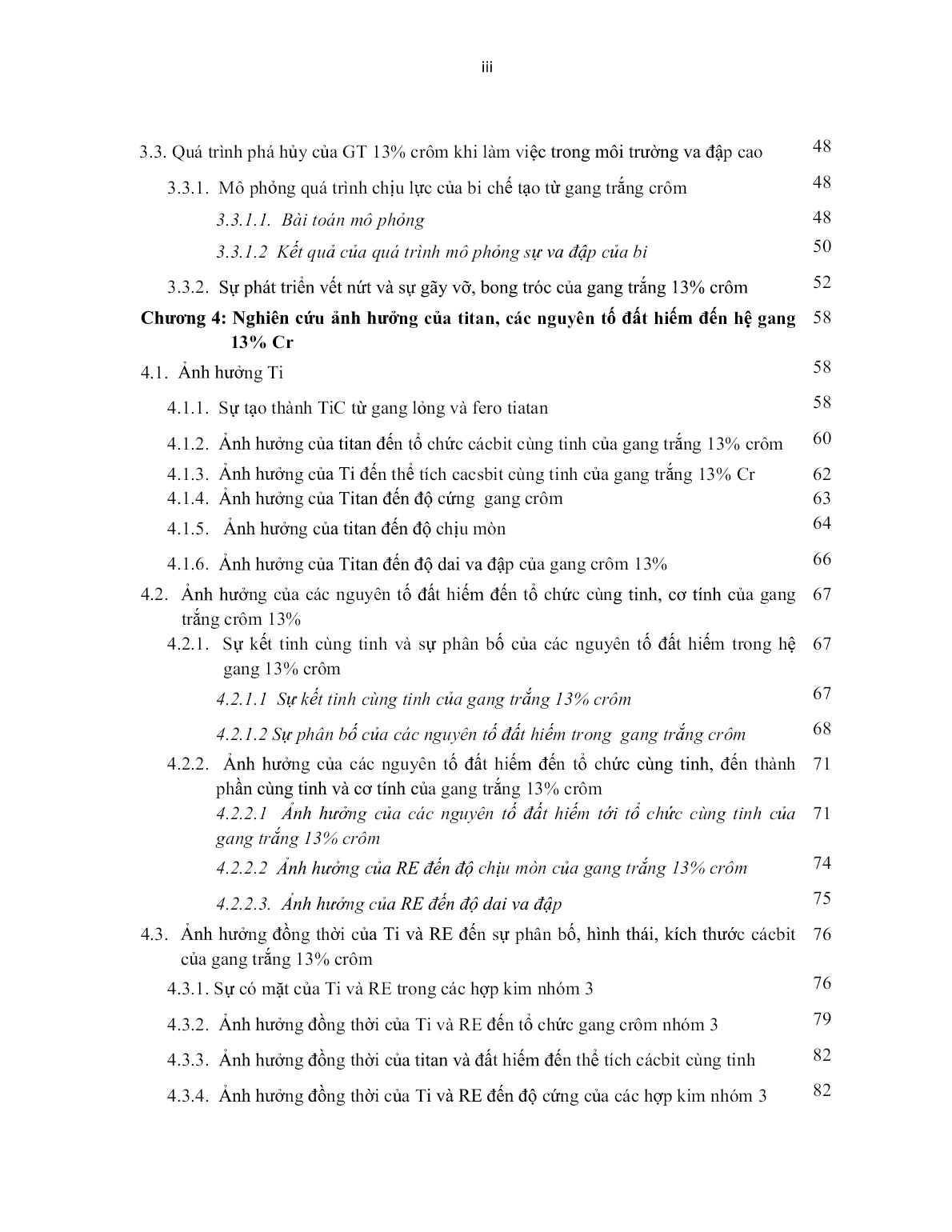
Trang 7
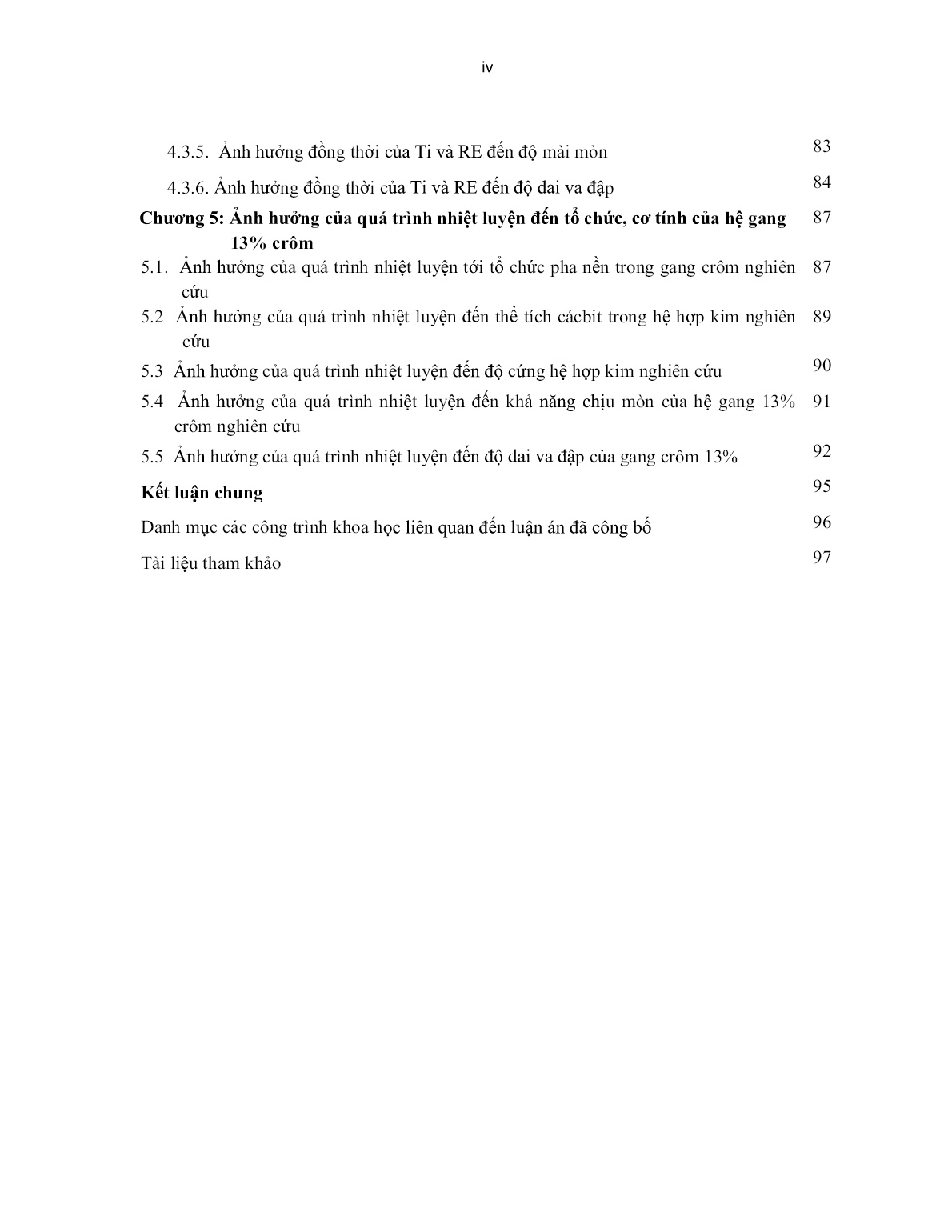
Trang 8
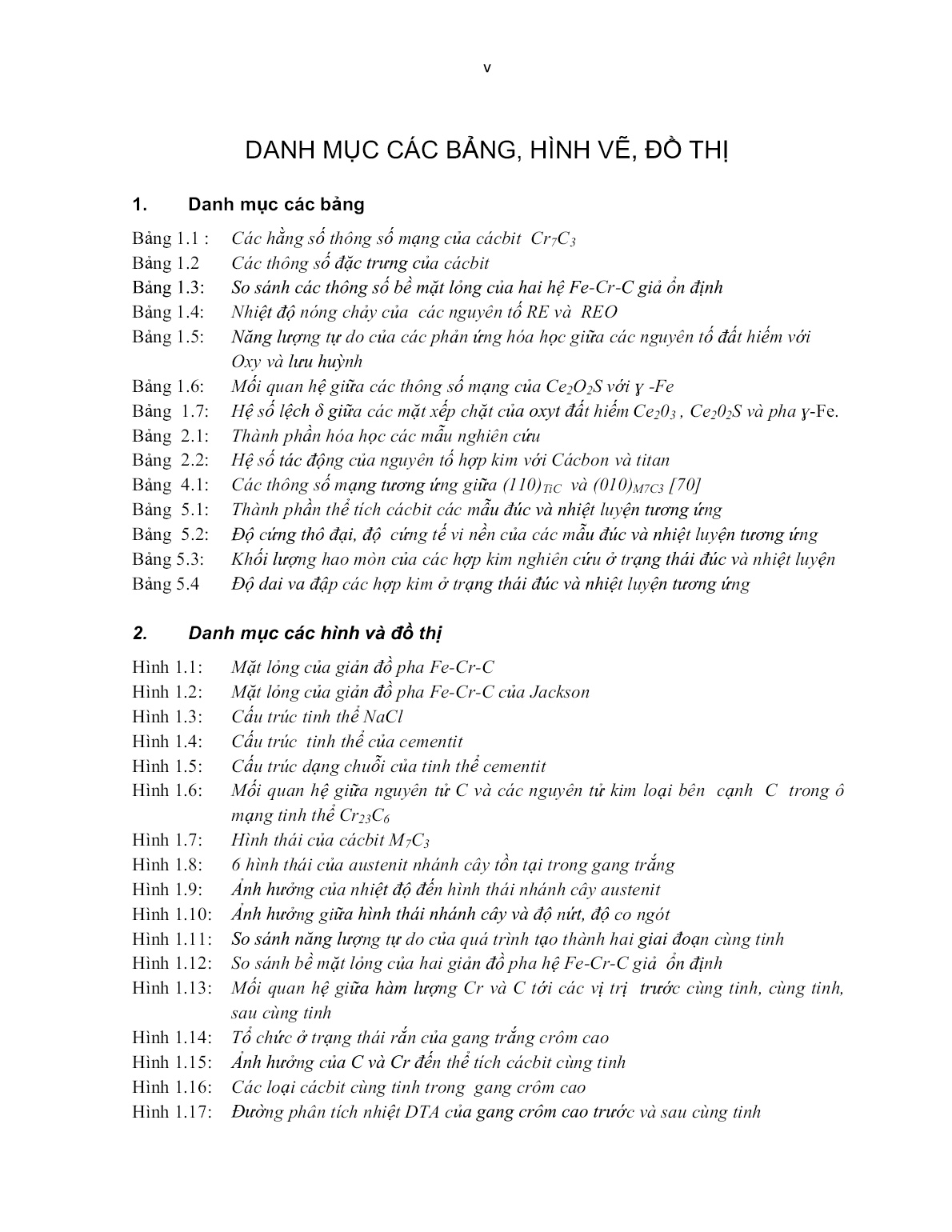
Trang 9
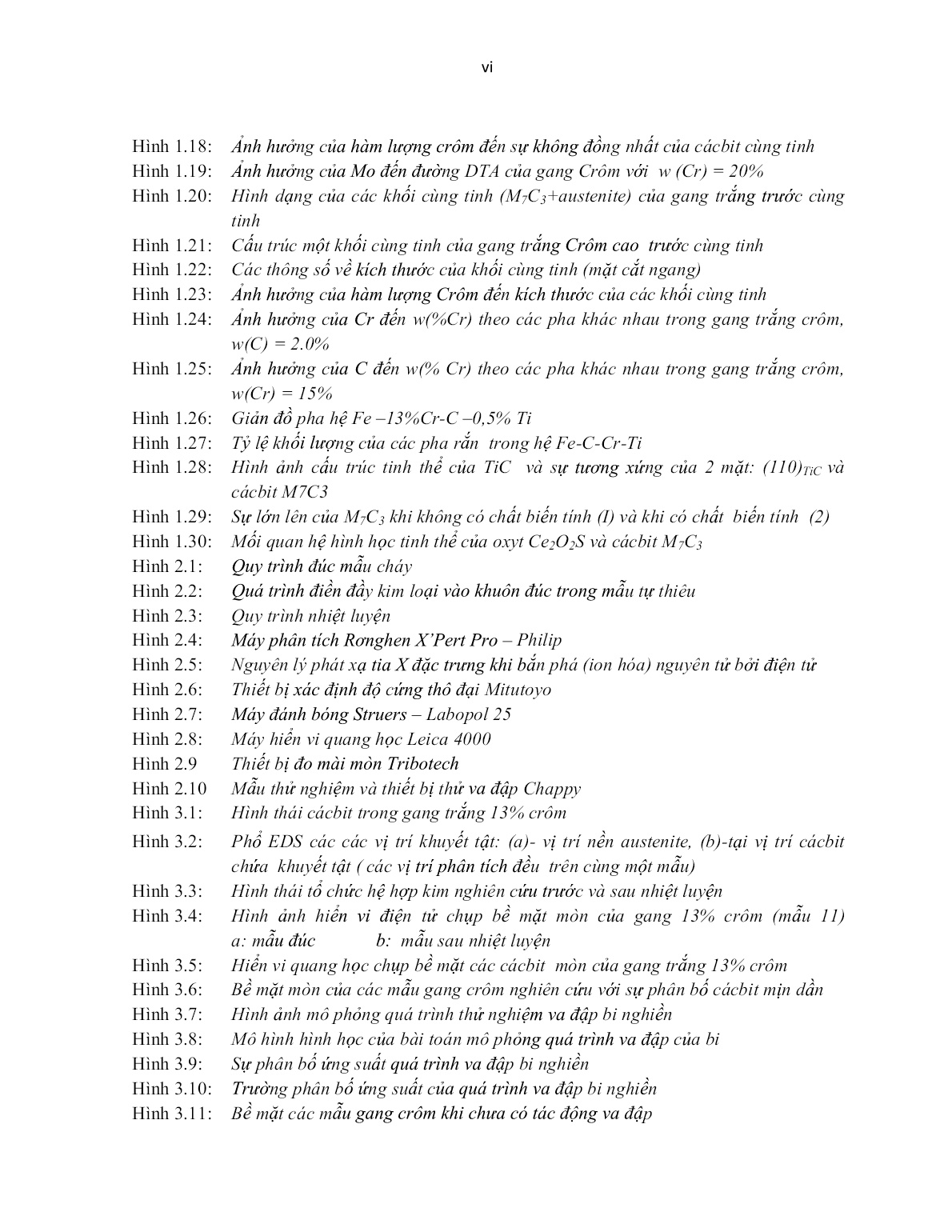
Trang 10
Tải về để xem bản đầy đủ
Bạn đang xem 10 trang mẫu của tài liệu "Luận án Nghiên cứu ảnh hưởng của titan và nguyên tố đất hiếm đến tính chất mài mòn, độ dai va đập của gang trắng 13% Crôm", để tải tài liệu gốc về máy hãy click vào nút Download ở trên.
Tóm tắt nội dung tài liệu: Luận án Nghiên cứu ảnh hưởng của titan và nguyên tố đất hiếm đến tính chất mài mòn, độ dai va đập của gang trắng 13% Crôm
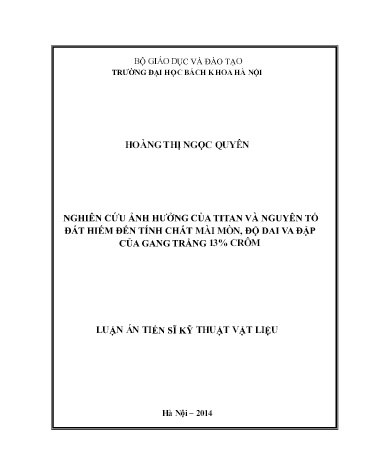
dụng lên thành khuôn gây vỡ khuôn. Sử dụng quy trình đúc mẫu cháy để chế tạo mẫu gang crôm nghiên cứu. Đúc mẫu cháy là phương pháp đúc dùng mẫu là polystyrol, vật liệu làm khuôn là cát khô, không có chất dính. Mẫu được vùi trong khối cát không có chất dính nhưng được tạo hình bằng cách hút chân không. Rót kim loại lỏng vào khuôn, kim loại sẽ dần thay thế khối xốp và hình thành vật đúc. Mẫu hình trụ sau khi đúc có kích thước dài khoảng 300 mm, có đường kính là 30 mm. Bảng 2.1 trình bày thành phần hóa học của 11 mẫu hợp kim đã được lựa chọn cho mục đích nghiên cứu. Các mẫu được chia thành 3 nhóm hợp kim theo mục đích nghiên cứu như sau: Các hợp kim nhóm 1: Gồm các mẫu ký hiệu từ 1 đến 4 là các mẫu gang crôm với hàm lượng crôm trong khoảng 12,8 đến 13,1%, có hàm lượng cácbon trong khoảng 2,14%, có hàm lượng titan trong khoảng 0,2 đến 1%. Các hợp kim nhóm 2: Gồm các mẫu ký hiệu từ 5 đến 8 là các mẫu có hàm lượng crôm 13%, có hàm lượng cácbon trong khoảng từ 3 - 3,2% với thành phần đất hiếm trong khoảng 0,1 đến 0,8%. Các hợp kim nhóm 3: Gồm các mẫu ký hiệu từ 9 đến 11 là các mẫu có hàm lượng crôm dao động trong khoảng 13,1% đến 13,3%, cácbon từ 2,8 với các hàm lượng titan trong khoảng 0,23 đến 0,66% và hàm lượng đất hiếm trong khoảng từ 0,2 đến 0,6%, Các thành phần khác như Si, Mn, P được khống chế để không ảnh hưởng đến chất lượng mẫu nghiên cứu. Sau khi làm nguội vật đúc tiến hành tháo dỡ vật đúc ra khỏi khuôn. Hình 2.2: Quá trình điền đầy kim loại vào khuôn đúc trong mẫu tự thiêu 1- cốc rót; 2- Rãnh ngang; 3- Cát khô; 4- Mẫu xốp; 5- Lớp sơn; 6- Mặt phân huỷ mẫu; 7- Mặt thoáng của dòng kim loại lỏng 8- kim loại lỏng 36 Bảng 2.1 Thành phần hóa học các mẫu nghiên cứu Mẫu Fe C Si Mn P S Cr Mo Ni Ti RE Các hợp kim nhóm 1 No.1 83,43 2,14 0,27 0,67 0,01 0,024 12,9 0,049 0,297 0,21 0 No.2 82,83 2,15 0,26 0,69 0,01 0,042 13,2 0,021 0,297 0,5 0 No.3 82,9 2,14 0,19 0,7 0,01 0,06 12,8 0,02 0,3 0,88 0 No.4 82,8 2,14 0,11 0,69 0,07 0,047 12,8 0,029 0,294 1,02 0 Các hợp kim nhóm 2 No.5 82 3,2 0,48 0,8 0,09 0,06 13 0,04 0,32 0 0,2 No.6 83,3 3 0,4 0,92 0,08 0,05 13 0,05 0,28 0 0,3 No.7 82,9 3,1 0,5 0,8 0,09 0,08 13 0,08 0,28 0 0,5 No.8 82,6 3,1 0,5 0,95 0,09 0,05 13 0,05 0,3 0 0,8 Các hợp kim nhóm 3 No.9 81,3 2,89 0,73 0,85 0,05 0,04 13,3 0,04 0,34 0,23 0,23 No.10 80,4 2,82 1,12 0,91 0,07 0,05 13,3 0,05 0,28 0,5 0,5 No.11 80,2 2,85 1,23 0,81 0,08 0,06 13,1 0,06 0,29 0,66 0,66 2.2. Nhiệt luyện các mẫu nghiên cứu Vật đúc được giữ trong khuôn sau khi rót rồi phá dỡ khuôn, cắt bỏ đậu ngót, rãnh dẫn, ba viađánh sạch cát dính ở bề mặt vật đúc. Kiểm tra khuyết tật đúc. Các vật đúc không khuyết tật được chuyển đi một phần để nhiệt luyện. Các quy trình chủ yếu gồm (như hình 2.3): - Ủ nhiệt độ trên 8000 C, tốc độ nâng nhiệt dưới 900C/giờ, giữ nhiệt ổn định từ 2-4 giờ, để nguội cùng lò, nhằm giảm ứng suất, khắc phục sự không đồng đều về mặt thành phần hóa học. - Tôi : Sau quá trình ủ là quá trình tôi, nhiệt độ tôi khoảng 10500C , tốc độ nâng nhiệt dưới 70 0 C/giờ, thời gian giữ nhiệt từ 3 giờ, và làm nguội trong dầu, nhằm nâng cao độ cứng, độ đồng đều, độ bền, và khả năng mài mòn cho mẫu nghiên cứu. - Ram : Sử dụng quy trình ram thấp và ram cao, nhiệt độ ram 2500C, thời gian ram từ 3h, nhằm giảm ứng suất bên trong mà vẫn giữ được độ cứng và tính chống mài mòn sau tôi. 37 2.3. Phương pháp nghiên cứu và các cơ sở tiến hành thực nghiệm 2.3.1. Xác định thành phần hóa học Thành phần hóa học của các mẫu nghiên cứu được phân tích bằng phương pháp quang phổ phát xạ trên máy ARL-3460 của hãng Fisons Thụy Sỹ. Nguyên lý của phương pháp này là sử dụng photon để kích thích phát xạ điện tử thứ cấp ở bề mặt mẫu. Đo và phân tích năng lượng của điện tử phát xạ thứ cấp để biết thông tin về nguyên tố hóa học và các mức liên kết tương ứng . 2.3.2. Xác định thành phần pha Thành phần pha của hợp kim nghiên cứu được xác định bằng phương pháp nhiễu xạ tia X (X-ray) trên máy X’Pert Pro – Philip. Các thông số cơ bản của máy : Điện áp sử dụng: 40 KV 250 0 C 1050 0 C Hình 2.3 Quy trình nhiệt luyện 250 0 C Nhiệt độ (0C) Thời gian (t) Hình 2.4 : Máy phân tích Rơnghen X’Pert Pro – Philip 38 Dòng điện: 30 mA Bước quét: 0,03mm Thời gian quét: 40s/1bước quét, độ phân giải: 10-3 Thành phần của từng pha được phân tích bằng phổ tán xạ tia X theo năng lượng (EDS) trên kính hiển vi điện tử quét (SEM). 2.3.3. Phương pháp xác định sự phân bố không gian của các nguyên tố hóa học (phương pháp mapping) Phương pháp phân tích mapping nguyên tố là một phương pháp phân tích sự phân bố của các nguyên tố, hình ảnh là một bản đồ hiển thị sự phân bố không gian của các nguyên tố trong một mẫu. Có hai kỹ thuật phân tích chủ yếu tùy thuộc vào việc phân tích năng lượng hay bước sóng của tia X đặc trưng phát ra từ mẫu: - Đo sự tán sắc năng lượng : sử dụng cụm đo sự tán sắc năng lượng tia X (Energy dispersive X-ray Spectroscopy: EDXS) thường có trong thiết bị hiển vi điện tử quét SEM - Đo sự tán sắc của bước sóng: sử dụng cụm đo sự tán sắc bước sóng tia X (Wavelength dispersive X-ray Spectroscopy: WDXS) trong thiết bị hiển vi điện tử truyền qua TEM. Bằng kỹ thuật này hay kỹ thuật khác, hình ảnh phân tích được tạo ra bởi chùm tia điện tử quét qua khu vực cần quan tâm. Bản đồ phân bố các nguyên tố thường cho các mầu sắc sai giúp mắt người phân biệt sự thay đổi tinh tế bằng cách mở rộng phạm vi của các màu sắc nhìn thấy được. Nhờ đưa chùm tia đã tiêu tụ lên mẫu có thể xem hình ảnh các nguyên tố có trong mẫu. Nguyên lý phân tích phổ tán sắc năng lượng EDXS (hình 2.5): 2.3.4. Phương pháp xác định độ cứng tế vi Tia X đặc trưng được phát ra khi chùm điện tử tới kích thích các điện tử ở các lớp lõi của nguyên tử, dẫn tới quá trình chuyển dời từ các lớp ngoài vào lớp vỏ bên trong. Nhờ năng lượng cao (5-20keV), chùm tia X đặc trưng được phát xạ ở sâu bên trong khối bên dưới bề mặt Hình 2.5: Nguyên lý phát xạ tia X đặc trưng khi bắn phá (ion hóa) nguyên tử bởi điện tử 39 mẫu. Từ độ sâu vài micromet dưới bề mặt mẫu, nơi chịu tác dụng của chùm tia điện tử, tia X đặc trưng phải đi qua các lớp bề mặt mẫu trước khi đi bay tới detector (EDX) dẫn đến năng năng lượng tia X bị hấp phụ khối. Năng lượng của photon (lượng tử tia X) phát ra chính là độ chênh lệch giữa năng lượng liên kết của lớp vỏ trong và lớp vỏ bên ngoài của quá trình chuyển dời. Năng lượng Rơngen luôn nhỏ hơn năng lượng của chùm tia tới. Các vạch bức xạ đặc trưng này có bước sóng cố định với mỗi loại nguyên tử xác định. Nghĩa là có tính đặc trưng cho nguyên tố hóa học (phân tích định tính). Cường độ của vạch đặc trưng của nguyên tố phụ thuộc vào nồng độ nguyên tử của nó trong mẫu (phân tích định lượng) 2.2.4 Xác định độ cứng 2.3.3.1 Xác định độ cứng thô đại Rockwell Độ cứng được đo bằng cách ép lên bề mặt vật liệu một mũi đâm làm bằng vật liệu cứng hầu như không như không bị biến dạng dẻo bằng một tải trọng xác định. Khi bỏ tải mũi đâm sẽ để lại trên vật liệu một vết lõm: vết lõm càng to hoặc càng sâu thì giá trị độ cứng càng thấp. Độ cứng có hai loại: độ cứng thô đại và độ cứng tế vi. Độ cứng thô đại với mũi đâm lớn đủ làm biến dạng nhiều hạt và pha (hình 2.6). Độ cứng thô đại của mẫu được xác định theo phương pháp Rockwell (HRC) trên máy ATKF 1000 của hãng Mitutoyo (hình 2.6). Độ cứng Rockwell xác định bằng chiều sâu gây ra bởi tác dụng của tải trọng chính đặt vào. Giá trị của độ cứng Rockwell được tính từ công thức: HR = k-e [2.1] Trong đó: k là chiều sâu quy ước Có nhiều thang đo độ cứng Rockwell phụ thuộc vào loại mũi đâm và tải trọng tác dụng. Độ cứng HRC (mũi kim cương và tải trọng tác dụng P=150kg) cho vật liệu có độ cứng trung bình và cao (HRC từ 20 đến 67) 2.3.4.2 Xác định độ cứng tế vi Độ cứng tế vi được đo với mũi đâm nhỏ với tải trọng nhỏ sẽ tác dụng vào từng pha riêng rẽ với sự trợ giúp của kính hiển vi quang học. Phương pháp xác định độ cứng tế vi theo nguyên lý vicke với tải trọng nhỏ (từ vài gam cho đến vài trăm gam) với mũi đâm làm bằng Hình 2.6: Thiết bị xác định độ cứng thô đại Mitutoyo 40 kim cương, hình tháp bốn mặt đều với góc ở đỉnh giữa hai mặt đối diện là 1360. Khi ấn mũi kim hình tháp tỷ lệ đường chéo vết lõm nhận được khi thay đổi tải trọng luôn luôn không đổi. Số đo độ cứng Vicke được xác định theo công thức: HV= = = 1,854 , kG/mm2 [2.2] Trong đó: P – Tải trọng α =1360 (góc giữa hai mặt đối diện của mũi tháp) d: Giá trị trung bình số học của hai đường chéo vết lõm, mm Độ cứng ở điều kiện tiêu chuẩn chỉ cần viết tắt là HV và số đo, không cần ghi thứ nguyên. Phương pháp này dung trong nghiên cứu để xác định bản chất các pha cũng như sự phân bố vi mô của độ cứng. 2.3.5 Mức độ cùng tinh các mẫu nghiên cứu Gang trắng crôm có thể tồn tại ở dạng gang trước cùng tinh, cùng tinh và sau cùng tinh tùy thuộc vào mức độ cùng tinh. Mức độ cùng tinh được đánh giá thông qua cácbon đương lượng (CE) theo công thức sau: Mức độ cùng tinh = CE/4,3 [2.3] Công thức tính cácbon đương lượng như sau: CE= %C + [2.4] Trong đó:- C là hàm lượng cacbon trong gang (%) - mi là hệ số tác động của nguyên tố hợp kim - Xi là nguyên tố hợp kim khác ngoài cácbon (%) Hệ số tác động của các nguyên tố hợp kim được chỉ ra trong bảng 2.2. Nếu thành phần các nguyên tố Si, Ti, Mn là không đáng kể trong gang crôm thì các bon đương lượng có thể tính theo công thức sau: CE =C +0,05.%Cr [2.5] mi có giá trị dương có nghĩa là nguyên tố Xi có khả năng tạo thành cácbit trong hợp kim, nếu mi có giá trị âm thì nguyên tố đó không có khả năng tạo thành cácbit. Nguyên tố Hệ số tác động C Si Mn Cr Ti mTi -0,3 0,05 -0,012 0,055 0,048 mC 0,14 0,08 -0,001 -0,024 -0,08 2.3.6 Nghiên cứu tổ chức Các mẫu trước khi xem tổ chức tế vi phải được mài nhẵn và đánh bóng. Các mẫu nghiên cứu có bề mặt phẳng được mài trên máy Struers – Labopol 25 có lắp giấy ráp SiC (hình 2.7). Bảng 2.2 Hệ số tác động của nguyên tố hợp kim với Cácbon và titan 41 Tốc độ vòng quay tới 500 vòng/phút và được làm mát bằng nước. Mẫu được mài lần lượt trên giấy ráp 80, 320, 400, 600, 800, 1000, 1200 và 1500. Bề mặt đạt được sáng, không có vết xước và cuối cùng được đánh bóng bằng bột Al2O3 cỡ hạt 5µm. Cấu trúc tế vi được quan sát và chụp trên kính hiển vi quang học (HVQH) Leica 4000 ( Hình 2.8 ) có độ phóng đại tối đa là 1000 lần với phần mềm phân tích IPwin32 và trên kính hiển vi điện tử quét SEM (Scanning Electron Microscope) . Hình 2.7 Máy đánh bóng Struers – Labopol Hình 2.8 Máy hiển vi quang học Leica 4000 Tẩm thực mẫu nghiên cứu: Sử dụng phương pháp tẩm thực màu để nghiên cứu cấu trúc cácbit: KOH + K3Fe(CN)6 + H2O, tẩm thực sâu bằng dung dịch tẩm thực Village’s (50ml FeCl3 + 20ml HCl + 20ml etanol) để nghiên cứu nền và tổ chức cácbit các mẫu sau nhiệt luyện. 2.3.7 Nghiên cứu, đánh giá quá trình mài mòn Độ mài mòn của mẫu được kiểm tra trên máy Tribotech như hình 2.9 dưới đây: Độ mài mòn được xác định qua sự hao hụt khối lượng của các mẫu hình trụ có đường kính là 4mm, mài mòn trên giấy ráp cỡ hạt 240 trên quãng đường 2000m, tốc độ quay 300 vòng/phút theo với các tải trọng khác nhau 12N, 20N. Hình 2.9: Thiết bị đánh giá độ mài mòn Tribotech 42 2.3.8 Nghiên cứu quá trình phá hủy mẫu do va đập Các mẫu đo độ dai va đập được chế tạo theo tiêu chuẩn ASTM với khía chữ V trên máy CHAPPY (hình 2.10 b). Mẫu thử có kích thước 10 x10 x 55 mm, khoảng giữa có một rảnh rộng 2x2mm (Hình 2.10 a). Mẫu thử được đặt trên máy thử và nằm trên đường rơi của búa, khi thử nâng đầu búa lên độ cao H cho búa chuyển động theo quỹ đạo vòng tròn, trên đường đi đập vào mẫu làm gãy mẫu thử sau đó đi tiếp sang bên kia ứng với độ cao h, độ dai va đập. Tiêu chuẩn đánh giá là công va đập –hiệu năng lượng trước và sau phá hủy: AV = mg(H-h) [2.6] Độ dai va đập: ak = Av /S0 (J.cm -2 ) [2.7] Trong đó: g là gia tốc trọng trường S0: Diện tích mẫu tại rãnh khía 2.3.9. Xác định tổng hàm lượng cácbit cùng tinh Tổng hàm lượng cácbit cùng tinh được phân tích trên phần mềm image Pro-Plus, là phần mền cài trên thiết bị hiển vi quang học Axiovert 25. Hình 2.10: Mẫu thử nghiệm và thiết bị thử va đập Chappy a, b, 43 CHƯƠNG 3: NGHIÊN CỨU QUÁ TRÌNH PHÁ HỦY CỦA GANG TRẮNG CRÔM KHI LÀM VIỆC TRONG MÔI TRƯỜNG MÀI MÒN VÀ VA ĐẬP TẢI TRỌNG CAO 3.1. Đặc điểm của hệ gang trắng 13% crôm Gang trắng với thành phần crôm 13%, cácbon từ 2,14 đến 3,2% có tổ chức trước cùng tinh. Hình 3.1 là hình thái cácbit trong hệ gang crôm nghiên cứu. Là gang trước cùng tinh nên khi kết tinh, austenit nhánh cây tiết ra đầu tiên, sau đó là cùng tinh austenit và M7C3; Các vùng cùng tinh này nằm giữa các nhánh cây và tạo nên khối cùng tinh. Nằm giữa khối cùng tinh là các cácbit mịn, càng xa tâm khối thì cácbit càng trở nên thô hơn. Bên ngoài các khối cùng tinh là các cácbit M7C3 thô có dạng sợi dài. Khi kích thước các khối cùng tinh tăng, ẩn nhiệt kết tinh tăng lên làm thô các hạt cácbit trong khu vực ranh giới, điều này ảnh hưởng đến độ dai và khả năng chịu mòn của gang trắng crôm. Do vậy để nâng cao tuổi thọ gang trắng crôm cùng tinh và trước cùng tinh, ngoài việc làm nhỏ gọn cacbit thô, còn cần phải tìm cách giảm kích thước khối cùng tinh, làm mịn các phần tử cácbit trong khối cùng tinh. Bên trong bề mặt các cácbit M7C3 sơ cấp thô, to thường xuất hiện một lõm trắng (như hình 3.1). Hình 3.2 là hình ảnh phân tích EDS các vị trí khuyết tật, nền và tại cácbit chứa khuyết tật đó.. Về độ lớn của các pic, về hàm lượng các nguyên tố tại các vị trí khuyết tật có sự tương đồng với nền và khác biệt với hạt cácbit chứa khuyết tật. Điều này minh chứng rằng các khuyết tật được tạo ra trong quá trình tạo cùng tinh. Nguyên nhân là khi chất lỏng kết tinh, tổ chức cùng tinh kết tinh thường kèm theo một lượng nhỏ co ngót. Các cácbit xa vùng cùng tinh kết tinh cuối cùng, không còn được bù co, hình thành nên các khuyết tật. Kích thước của khối cùng tinh càng lớn, các cácbit càng xa trung tâm càng lớn, lượng khuyết tật trong các cácbit này càng lớn. Nếu kích thước của các ô cùng tinh giảm thì quá trình bù co cho các khu vực cácbit tại trung tâm của phản ứng cùng tinh giảm, điều này làm giảm các khuyết tật trong các cácbit thô, xa trung tâm ô cùng tinh. Hình 3.1: Hình thái cácbit trong gang trắng 13% crôm ɣ ɣ Khối cùng tinh Khuyết tật đúc 44 a , b, Hình 3.2: Phổ EDS các các vị trí khuyết tật: (a)- vị trí nền austenite, (b)-tại vị trí cácbit chứa khuyết tật ( các vị trí phân tích đều trên cùng một mẫu) c, M %Wt Fe 64,03 Cr 3,66 C 22,43 M %Wt Fe 34,11 Cr 11,61 C 17,72 M %Wt Fe 66,48 Cr 4,35 C 17,67 a, bề mặt mẫu trước nhiệt luyện 45 Hình 3.3 mô tả sự thay đổi của tổ chức pha nền của gang trắng 13% crôm sau khi nhiệt luyện. Tổ chức gang crôm sau nhiệt luyện ngoài mactenxit được chuyển từ austenit còn có các cácbit thứ cấp (phần chấm nhỏ li ti trên hình 3.3b) và một phần austenit dư. Gang crôm sau khi qua xử lý nhiệt nền được tăng cứng rất nhiều. 3.2. Quá trình mòn của gang trắng 13% crôm khi làm việc trong môi trường trượt có tải Khi hai bề mặt của vật mài mòn trượt lên nhau, tạo ra ma sát bề mặt và ứng suất tiếp xúc. Trong điều kiện chịu tải trọng lớn sẽ gây ra biến dạng dẻo và biến dạng đàn hồi. Gang trắng crôm với độ cứng cao là vật liệu được sử dụng trong những trường hợp yêu cầu mức độ chịu mài mòn cao. Tính chống mài mòn của hợp kim gang trắng crôm cao chủ yếu là do sự hiện diện của cácbit sơ cấp cứng hoặc các cácbit cùng tinh trong tổ chức tế vi. Những cácbit này đóng một vai trò quan trọng trong hành vi phá hủy gang trắng crôm. Cácbit thứ cấp b, bề mặt mẫu sau nhiệt luyện Hình 3.3: Hình thái tổ chức hệ hợp kim nghiên cứu trước và sau nhiệt luyện Hình 3.4: Hình ảnh hiển vi điện tử chụp bề mặt mòn của gang 13% crôm (mẫu 11) a: mẫu đúc b: mẫu sau nhiệt luyện 46 Gang trắng hợp kim có thành phần crôm 13%, tổ chức đúc bao gồm chủ yếu là austenite và các cacbit M7C3, ở trạng thái đúc gang crôm có độ cứng thấp, sự chênh lệch độ cứng giữa nền và các hạt cácbit cứng cao, khi bị mài mòn có tải trọng vật liệu thường bị mòn nhanh và dễ dàng phá hủy bề mặt mẫu do pha nền dễ bị phồng rộp, biến dạng. Hình 3.4 là hình ảnh hiển vi điện tử chụp bề mặt mòn có tải trọng của mẫu 11 trước và sau nhiệt luyện. Ở hình 3.4(a) là hình ảnh hiển vi chụp bề mặt mẫu đúc với các vết xước sâu, rộng như vậy sự phá hủy bề bề mặt mẫu lớn. Hình 3.4(b) chụp bề mặt mẫu sau nhiệt luyện tương ứng, các vết xước nông và nhạt hơn, mức độ phá hủy bề mặt mẫu giảm đi rất nhiều so với mẫu trước nhiệt luyện. Điều đó chứng tỏ rằng ở trạng thái đúc khi nền là austenit, mẫu có độ bền thấp, do sự chênh lệch độ cứng giữa nền và cacbit, mối liên kết giữa nền và cácbit yếu. Ngoài ra khả năng biến dạng dẻo xảy ra trên bề mặt nền cao làm tăng sự phát triển của các vết nứt dẫn đến sự phá hủy nhanh. Trong quá trình mài mòn có tải trọng lặp lại nhiều lần, biến dạng dẻo xảy ra trên diện rộng, pha nền dễ dàng bị xô lệch, biến dạng, nền không giữ được pha cứng, dẫn đến bong tróc. Khi nền có độ bền cao hơn, ứng suất truyền giữa các phần tử cácbit sẽ giảm do nền phân tán một phần ứng suất đó, pha nền chịu được tải và giữ được các hạt cácbit không bị xô lệch và bong tróc, quá trình biến dạng xảy ra chậm hơn và như vậy quá trình phá hủy bề mặt cũng sẽ chậm hơn. Mặt khác sự tập trung ứng suất tại biên giới giữa một hạt cứng trên một nền dẻo dai có thể dẫn tới việc tạo nên vết nứt dưới tải trọng cao [39]. Gang trắng crôm cao tồn tại các phần tử cácbit cùng tinh hình que trên nền austenit cùng với sự tồn tại nhiều khuyết tật là vật liệu mà ở đó các vết nứt có thể phát triển một cách thuận lợi [40]. Mactexit là pha có độ cứng cao. Khi nền là Mactenxit, sự chênh lệch độ cứng giữa pha cacbit và nền sẽ nhỏ hơn so với nền là austenit. Đó là lý do tại sao muốn tăng tính chống mài mòn cho gang nhiệt luyện là điều bắt buộc. Tuy nhiên trong quá trình chịu tải, vật liệu còn đòi hỏi có những điểm nhỏ có độ cứng thấp hơn để thoát ứng suất, tránh nứt vỡ. Nếu trong tổ chức chỉ toàn là pha cứng thì quá trình nứt vỡ cũng sẽ sớm xảy ra. Vì vậy lượng nhỏ austenit dư trong tổ chức cũng là điều cần thiết. Khả năng chống mài mòn còn phụ thuộc vào độ bền liên kết của pha cứng (pha cácbit) và độ bền liên kết của pha mềm (pha nền). Có nhiều ý kiến xung quanh vai trò của austenit dư trong việc làm chậm quá trình phá hủy, trong đó nổi trội hai luồng ý kiến trái chiều nhau về ảnh hưởng của austenit dư trong quá trình mòn có va đập như sau: một luồng ý kiến cho rằng austenit dư là một nhân tố có lợi vì austenit có tính dẻo và có tính dai, là điểm tích thoát ứng suất. Ngoài ra, khi bề mặt cácbit tích tụ năng lượng cao có thể gây ra và phát triển các vết nứt, năng lượng truyền sang nền, một phần năng lượng đó được tiêu thụ do quá trình chuyển biến từ austenit sang mactenxit, làm giảm năng lượng có thể gây nên quá trình nứt vỡ. Một số nhà khoa học còn cho rằng austenit dư làm giảm sự lan truyền của vết nứt. Luồng ý kiến khác lại cho rằng austenit làm giảm độ cứng của gang và tồn tại ứng suất gây ra bởi quá trình chuyển biến austenit thành mactenxit trong quá trình làm việc (khi chuyển từ austenit sang mactenxit, thể tích tăng từ 5-6%). Trong một bằng sáng chế Hoa Kỳ (4.043.842), đã quy định rằng gang trắng crôm làm việc trong điều kiện chịu tác động va đập lặp đi lặp lại, lượng austenite dư cần thấp hơn 3%; nguyên nhân là, một lượng thích hợp austenite dư có tác dụng chống lại sự nứt vỡ của vật liệu. Ở Nhật lượng austenit dư được khuyến cáo chỉ nên còn khoảng 1% [50]. Hình 3.5 là hình ảnh hiển vi quang học bề mặt, nơi các cácbit bị mòn, bong tróc. Khi chịu tác động mài mòn có tải trọng, do độ cứng cao, khả năng truyền tải trọng kém, các hạt
File đính kèm:
luan_an_nghien_cuu_anh_huong_cua_titan_va_nguyen_to_dat_hiem.pdf
THÔNG TIN MỚI NHẤT VỀ NHỨNG KẾT LUẬN MỚI CỦA LUẬN ÁN TIẾN SỸ.pdf
Tóm tắt Luận Án Quyen.pdf