Luận án Nghiên cứu chế tạo cảm biến khí H2 và H2S trên cơ sở màng SnO2 biến tính đảo xúc tác micro-nano
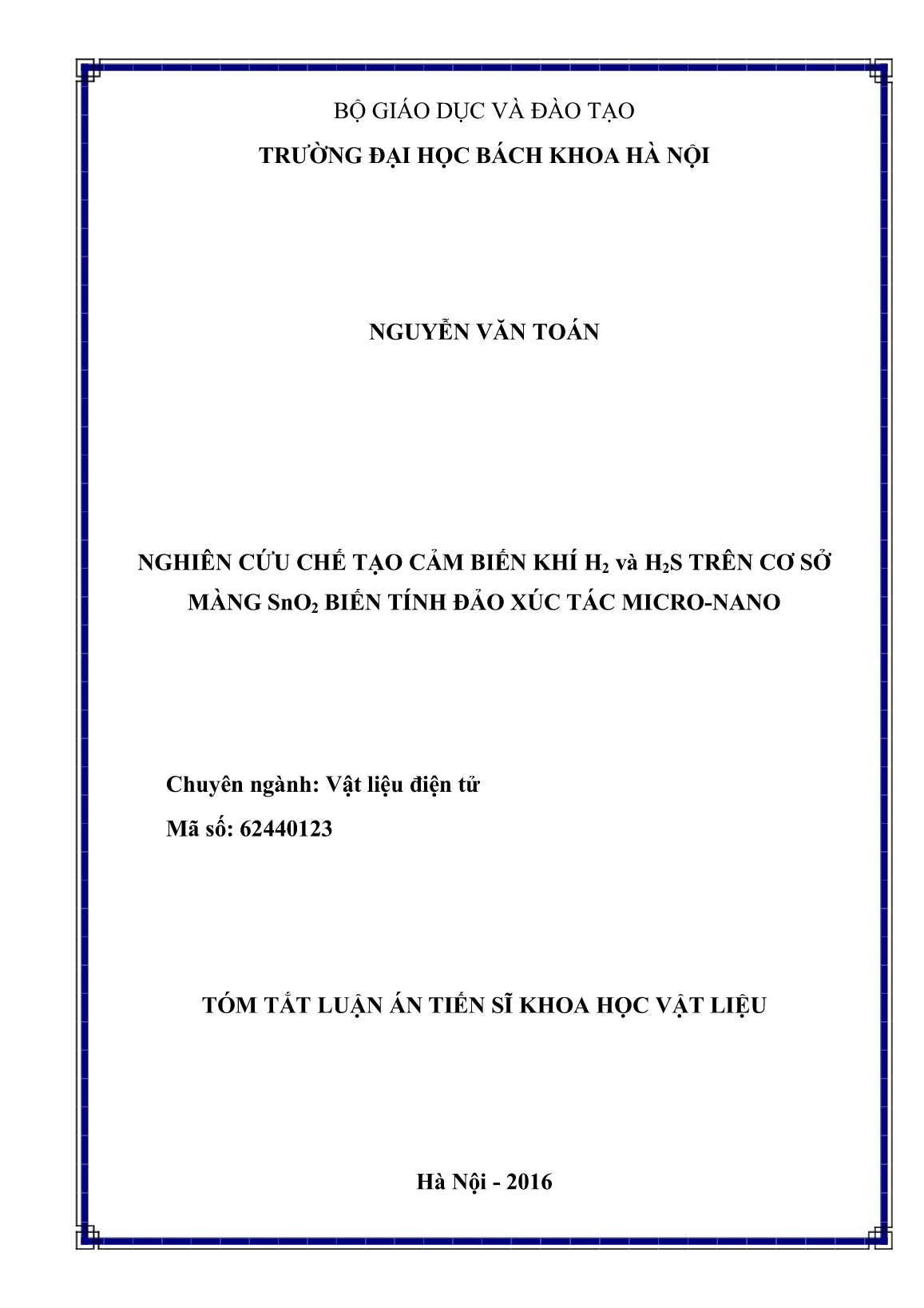
Trang 1
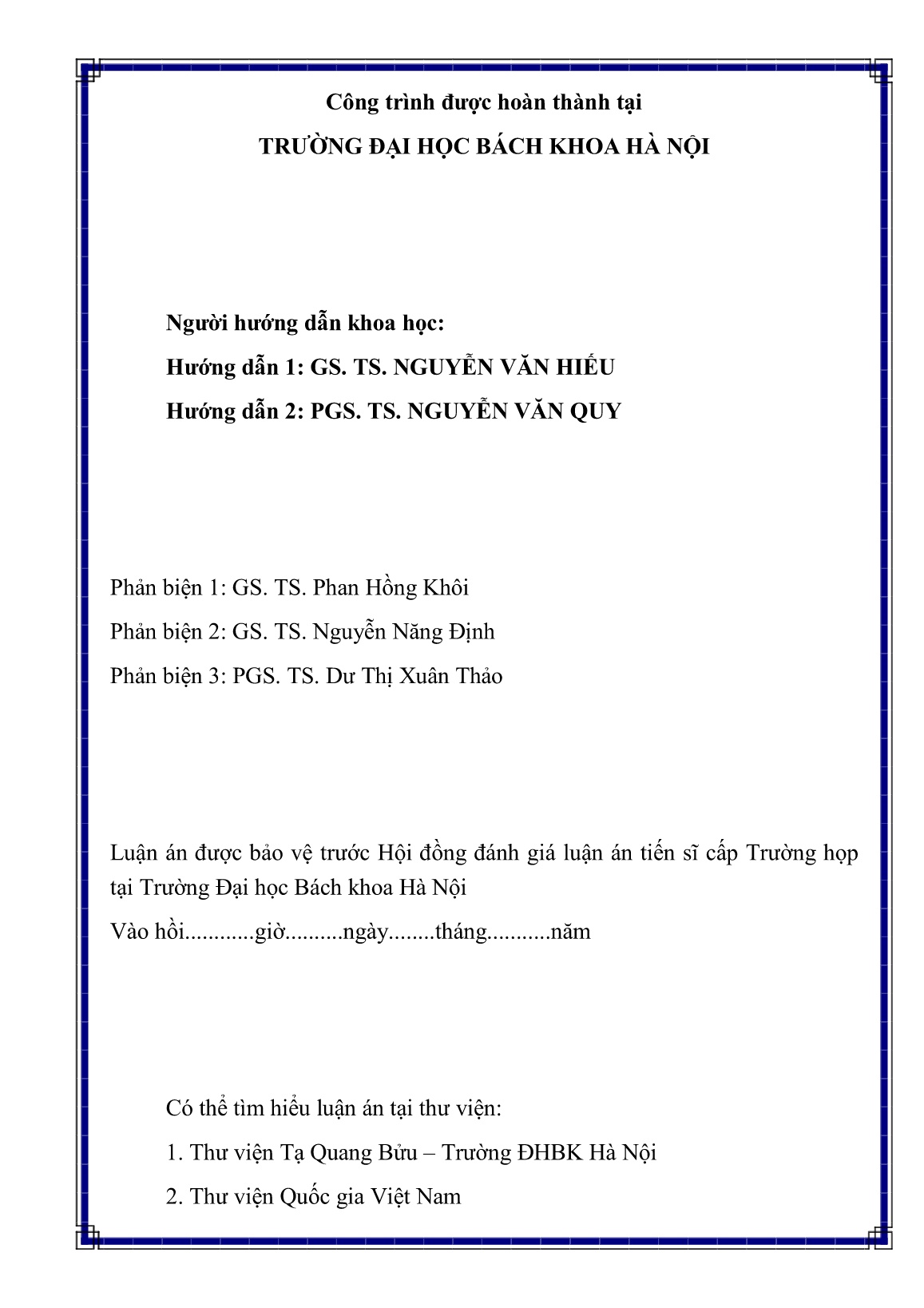
Trang 2
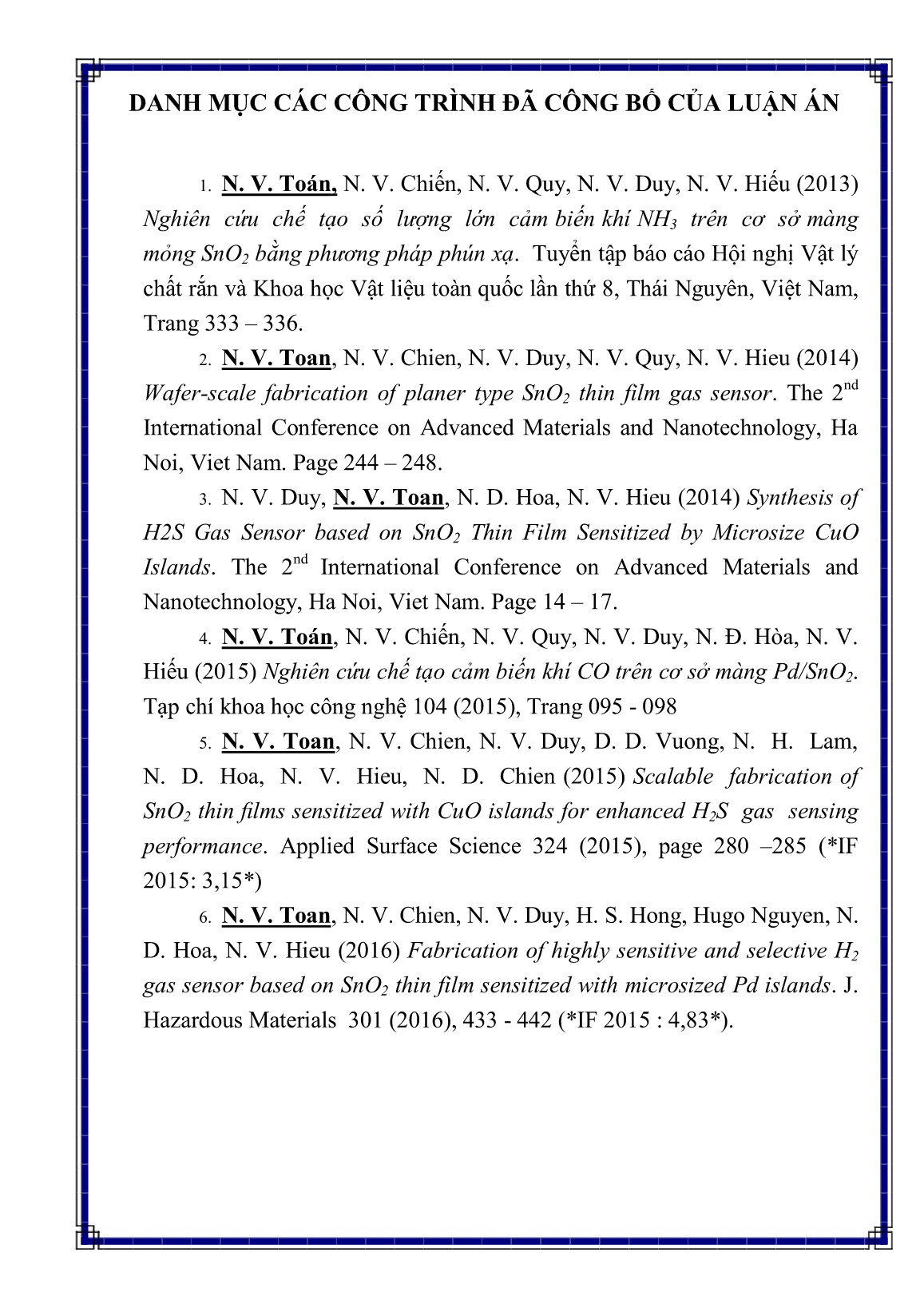
Trang 3
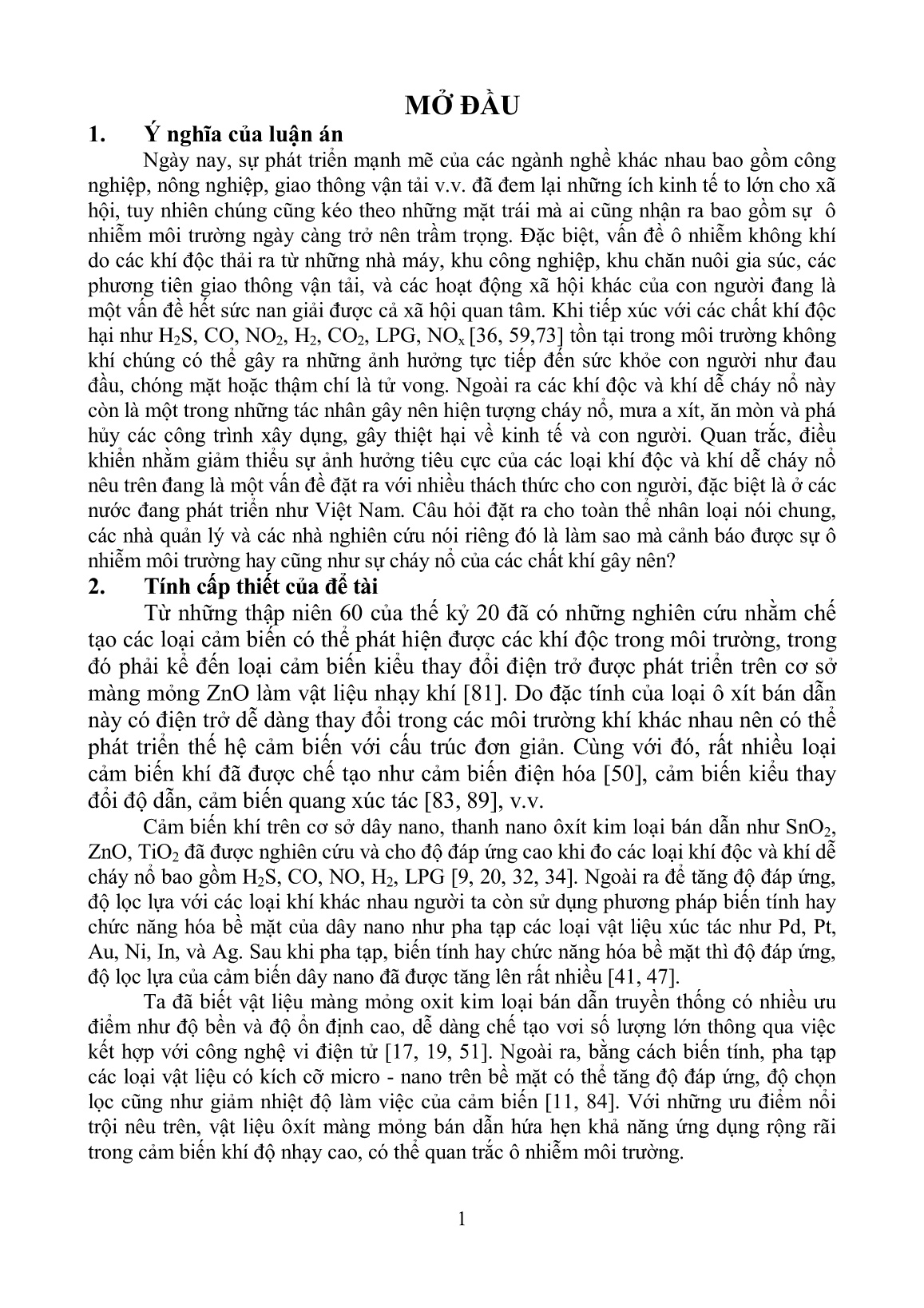
Trang 4
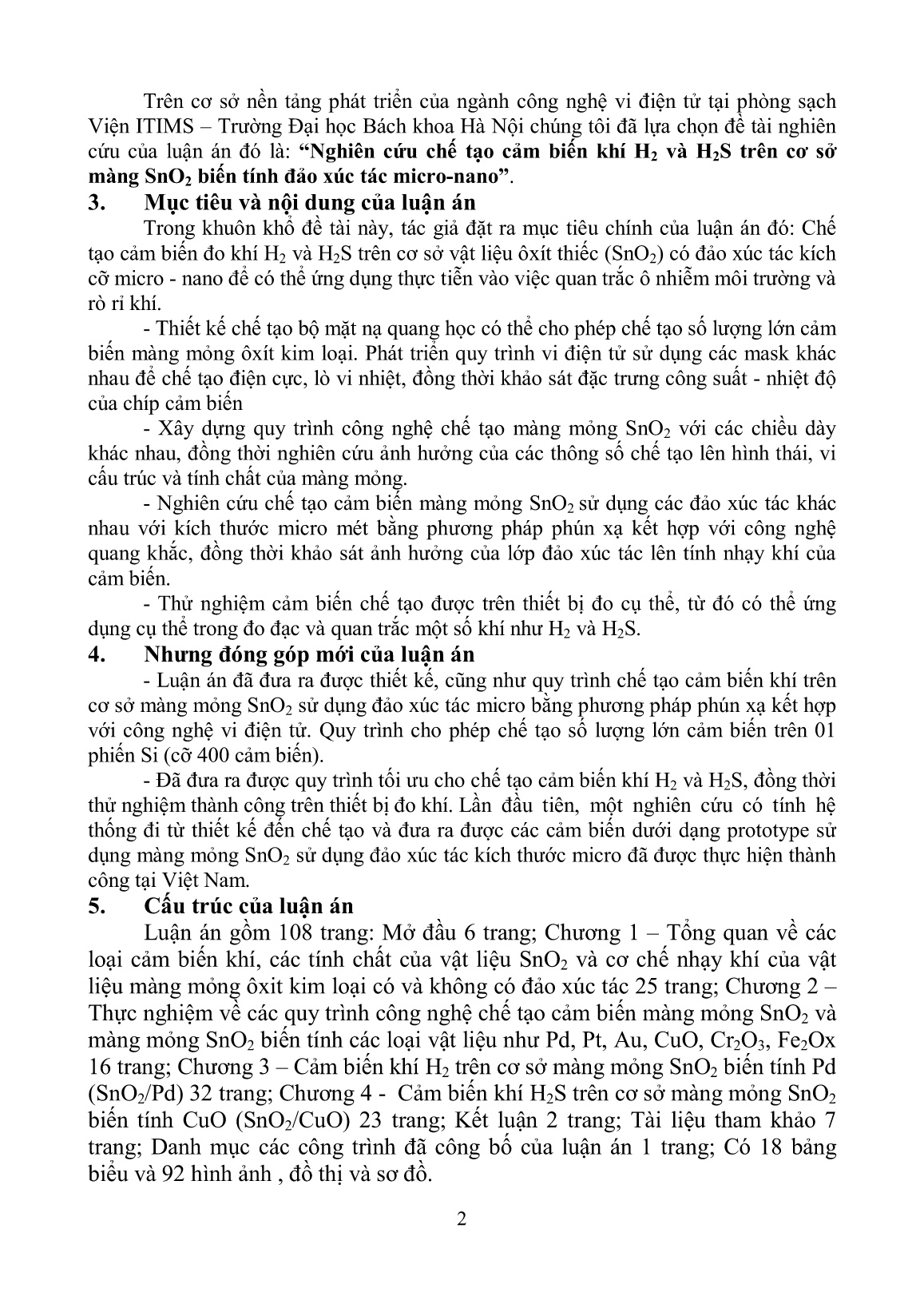
Trang 5
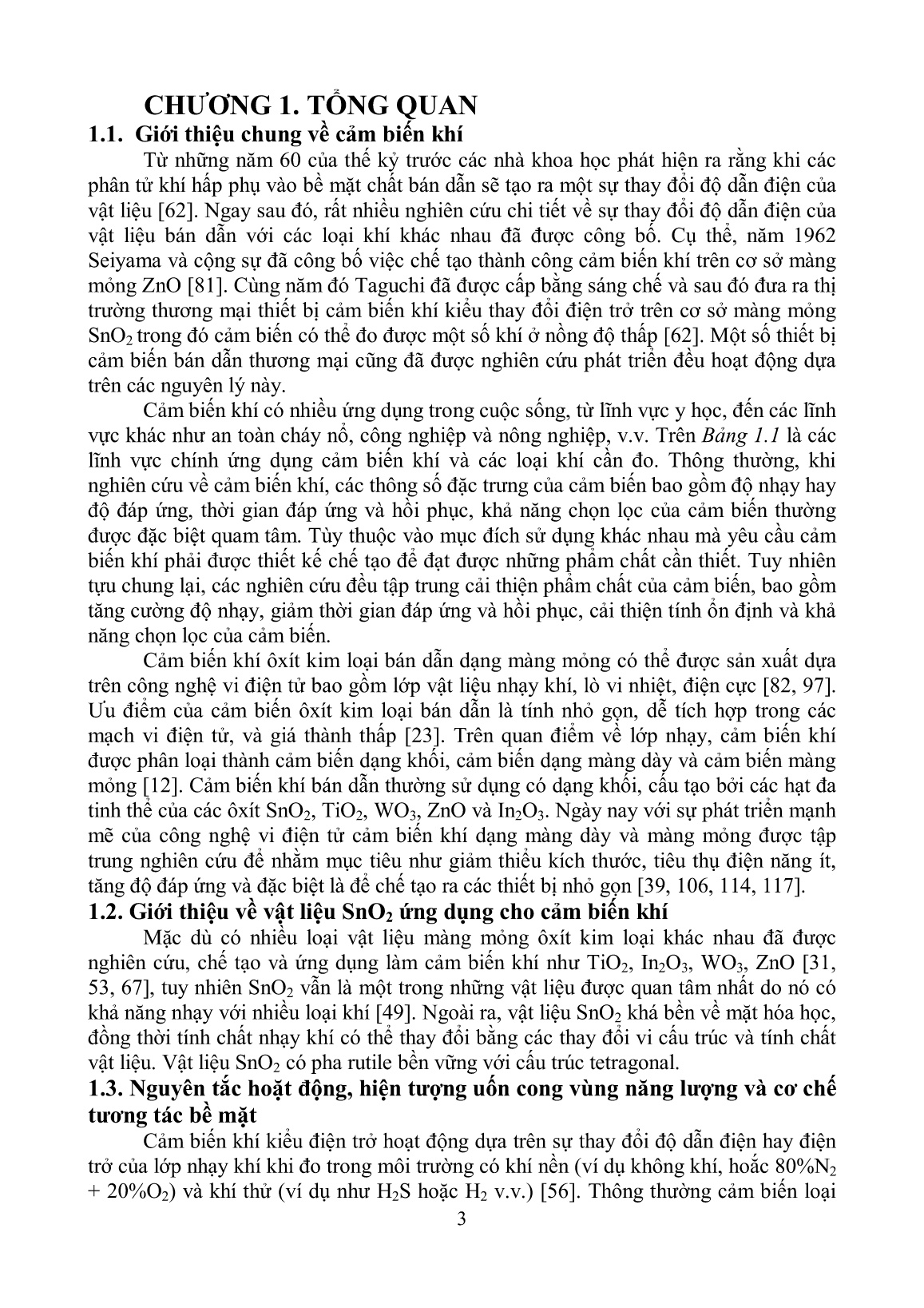
Trang 6

Trang 7
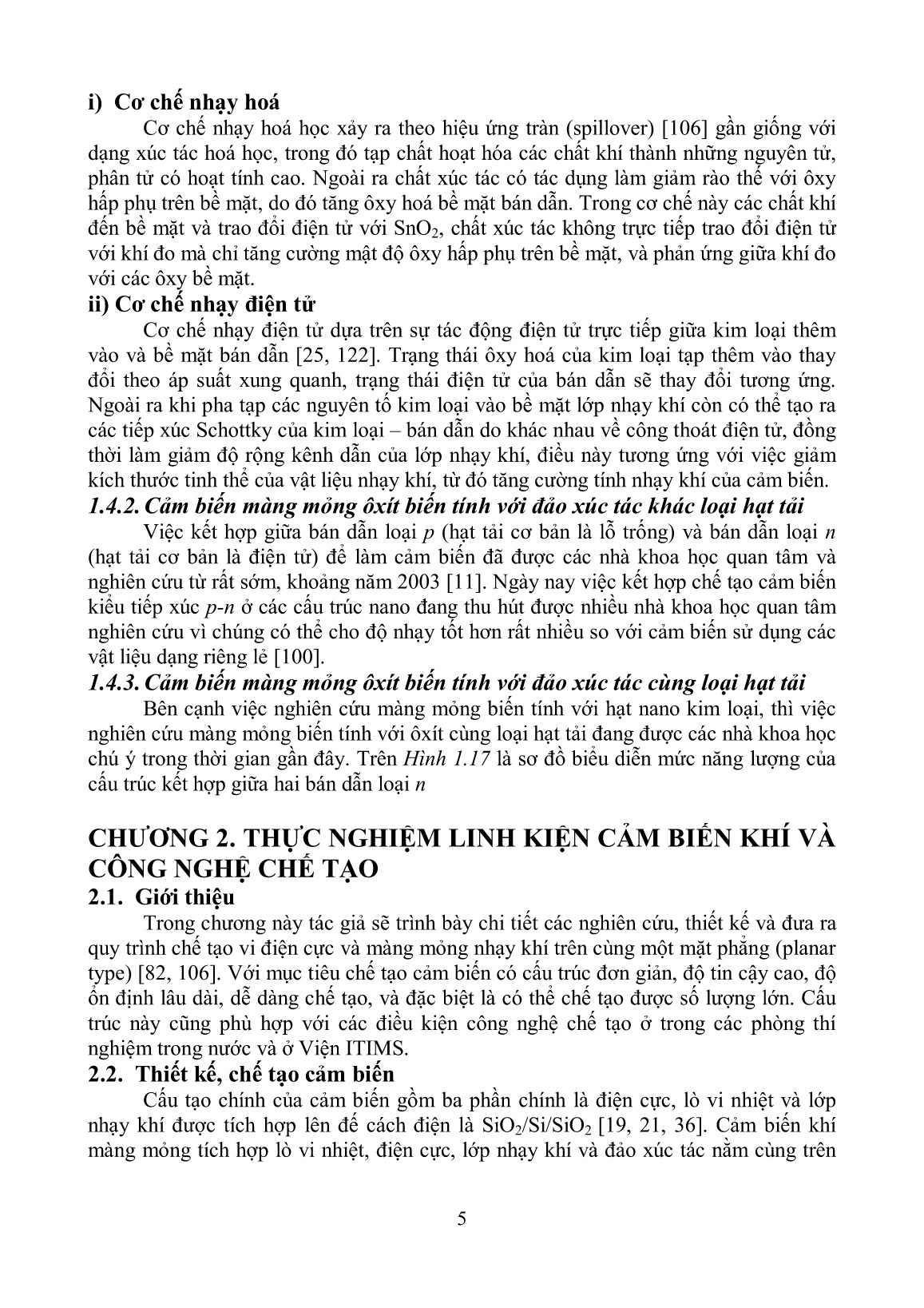
Trang 8
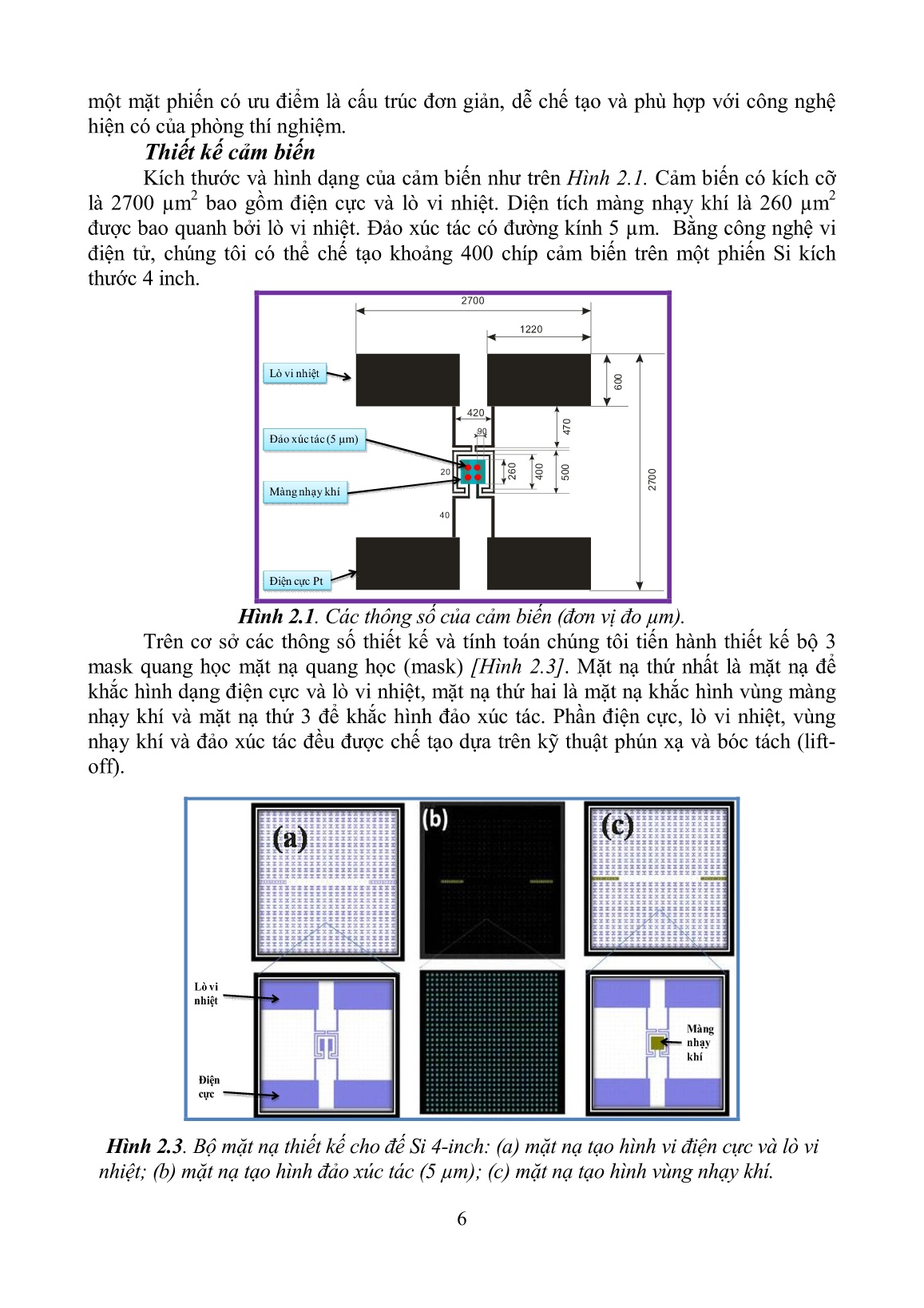
Trang 9
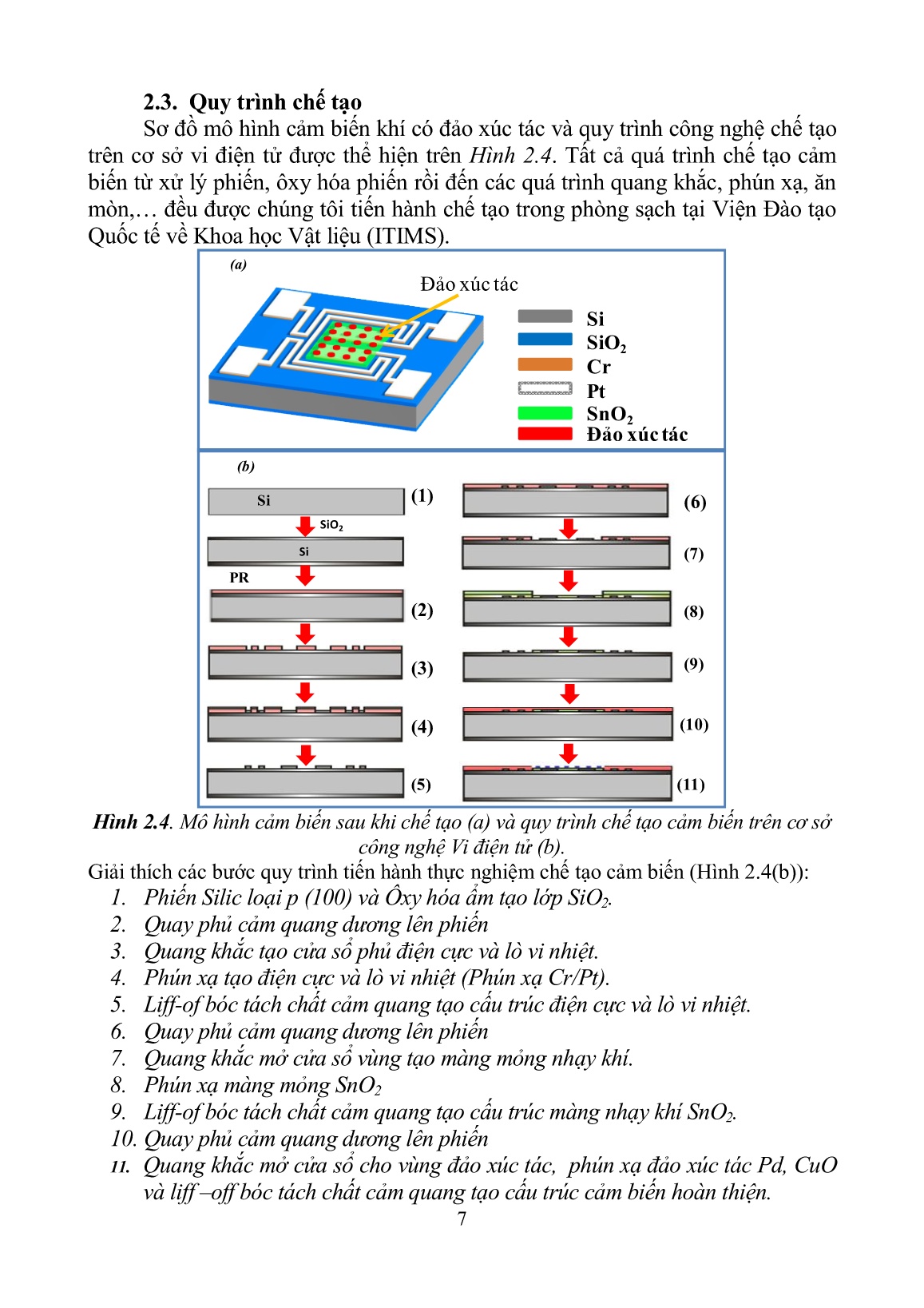
Trang 10
Tải về để xem bản đầy đủ
Bạn đang xem 10 trang mẫu của tài liệu "Luận án Nghiên cứu chế tạo cảm biến khí H2 và H2S trên cơ sở màng SnO2 biến tính đảo xúc tác micro-nano", để tải tài liệu gốc về máy hãy click vào nút Download ở trên.
Tóm tắt nội dung tài liệu: Luận án Nghiên cứu chế tạo cảm biến khí H2 và H2S trên cơ sở màng SnO2 biến tính đảo xúc tác micro-nano
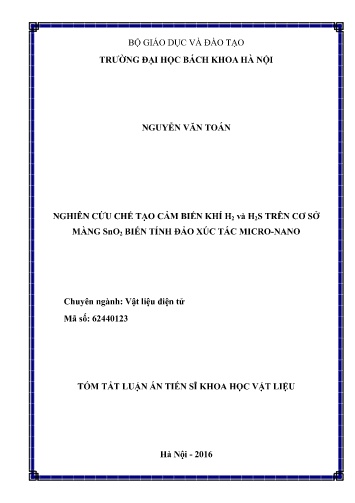
iến có cấu trúc đơn giản, độ tin cậy cao, độ ổn định lâu dài, dễ dàng chế tạo, và đặc biệt là có thể chế tạo được số lượng lớn. Cấu trúc này cũng phù hợp với các điều kiện công nghệ chế tạo ở trong các phòng thí nghiệm trong nước và ở Viện ITIMS. 2.2. Thiết kế, chế tạo cảm biến Cấu tạo chính của cảm biến gồm ba phần chính là điện cực, lò vi nhiệt và lớp nhạy khí được tích hợp lên đế cách điện là SiO2/Si/SiO2 [19, 21, 36]. Cảm biến khí màng mỏng tích hợp lò vi nhiệt, điện cực, lớp nhạy khí và đảo xúc tác nằm cùng trên 5 một mặt phiến có ưu điểm là cấu trúc đơn giản, dễ chế tạo và phù hợp với công nghệ hiện có của phòng thí nghiệm. Thiết kế cảm biến Kích thước và hình dạng của cảm biến như trên Hình 2.1. Cảm biến có kích cỡ là 2700 µm2 bao gồm điện cực và lò vi nhiệt. Diện tích màng nhạy khí là 260 µm2 được bao quanh bởi lò vi nhiệt. Đảo xúc tác có đường kính 5 µm. Bằng công nghệ vi điện tử, chúng tôi có thể chế tạo khoảng 400 chíp cảm biến trên một phiến Si kích thước 4 inch. 2700 1220 Lò vi nhiệt 0 0 6 420 0 7 90 4 Đảo xúc tác (5 µm) 0 0 0 6 0 20 0 0 2 4 0 5 7 Màng nhạy khí 2 40 Điện cực Pt Hình 2.1. Các thông số của cảm biến (đơn vị đo µm). Trên cơ sở các thông số thiết kế và tính toán chúng tôi tiến hành thiết kế bộ 3 mask quang học mặt nạ quang học (mask) [Hình 2.3]. Mặt nạ thứ nhất là mặt nạ để khắc hình dạng điện cực và lò vi nhiệt, mặt nạ thứ hai là mặt nạ khắc hình vùng màng nhạy khí và mặt nạ thứ 3 để khắc hình đảo xúc tác. Phần điện cực, lò vi nhiệt, vùng nhạy khí và đảo xúc tác đều được chế tạo dựa trên kỹ thuật phún xạ và bóc tách (lift- off). Lò vi nhiệt Màng nhạy khí Điện cực Hình 2.3. Bộ mặt nạ thiết kế cho đế Si 4-inch: (a) mặt nạ tạo hình vi điện cực và lò vi nhiệt; (b) mặt nạ tạo hình đảo xúc tác (5 µm); (c) mặt nạ tạo hình vùng nhạy khí. 6 2.3. Quy trình chế tạo Sơ đồ mô hình cảm biến khí có đảo xúc tác và quy trình công nghệ chế tạo trên cơ sở vi điện tử được thể hiện trên Hình 2.4. Tất cả quá trình chế tạo cảm biến từ xử lý phiến, ôxy hóa phiến rồi đến các quá trình quang khắc, phún xạ, ăn mòn, đều được chúng tôi tiến hành chế tạo trong phòng sạch tại Viện Đào tạo Quốc tế về Khoa học Vật liệu (ITIMS). (a) Đảo xúc tác Si SiO2 Cr Pt SnO2 Đảo xúc tác (b) Si (1) (6) SiO2 Si (7) PR (2) (8) (3) (9) (4) (10) (5) (11) Hình 2.4. Mô hình cảm biến sau khi chế tạo (a) và quy trình chế tạo cảm biến trên cơ sở công nghệ Vi điện tử (b). Giải thích các bước quy trình tiến hành thực nghiệm chế tạo cảm biến (Hình 2.4(b)): 1. Phiến Silic loại p (100) và Ôxy hóa ẩm tạo lớp SiO2. 2. Quay phủ cảm quang dương lên phiến 3. Quang khắc tạo cửa sổ phủ điện cực và lò vi nhiệt. 4. Phún xạ tạo điện cực và lò vi nhiệt (Phún xạ Cr/Pt). 5. Liff-of bóc tách chất cảm quang tạo cấu trúc điện cực và lò vi nhiệt. 6. Quay phủ cảm quang dương lên phiến 7. Quang khắc mở cửa sổ vùng tạo màng mỏng nhạy khí. 8. Phún xạ màng mỏng SnO2 9. Liff-of bóc tách chất cảm quang tạo cấu trúc màng nhạy khí SnO2. 10. Quay phủ cảm quang dương lên phiến 11. Quang khắc mở cửa sổ cho vùng đảo xúc tác, phún xạ đảo xúc tác Pd, CuO và liff –off bóc tách chất cảm quang tạo cấu trúc cảm biến hoàn thiện. 7 c) Quang khắc mặt nạ thứ nhất (Mask 1, chế tạo lò vi nhiệt và điện cực): Bảng 2.3. Quy trình công nghệ quang khắc Hình ảnh các Các bước công nghệ chính bước công nghệ - Bước 1: Quay phủ chất tăng cường bám dính primer (Hexamethyldisilixan- C6H19NSi2) với tốc độ 1.000 vòng/phút trong 5 giây và 3.000 vòng/phút trong 20 giây. - Bước 2: Quay phủ cảm quang OIR 907-12 với tốc độ 1.000 vòng/phút trong 5giây, 3.000 vòng/phút trong 20 giây. o - Bước 3: Ủ phiến ở 95 C trong 90 giây (đóng rắn sơ bộ - soft bake). - Bước 4: Chiếu ánh sáng UV 15 giây để quang khắc để tạo hình ảnh điện cực và lò vi nhiệt - Bước 5: Nhúng vào chất hiện hình (Developer OPD-4262) trong thời gian 60 giây để hiện hình ảnh của điện cực và lò vi nhiệt sau khi quang khắc. Sau đó rửa sạch và sấy khô phiến để kiểm tra chất lượng quang khắc bằng kính hiển vi. Nếu không đạt yêu cầu phải tẩy lớp cảm quang đi và tiến hành quang khắc lại. Photoresist - Bước 6: Ủ phiến ở 125 oC trong 15 phút giúp SiO chất cảm quang bám chắc vào đế và tăng độ cứng 2 phục vụ cho quá trình tiếp theo (hard bake). Đế Silic Bảng 2.5. Thông số phún xạ màng mỏng Cr/Pt Bia Cr, Pt Độ tinh khiết 99,99% Lò vi nhiệt Áp suất (µbar) 5* 10-6 Điện cực Áp suất phún xạ (µbar) 3 * 10-3 Tỷ lệ khí Ar (sccm) 30 Điện cực và Công suất W (nguồn DC) 100/60 lò vi nhiệt Thời gian 3/15 SiO2 Đế Silic Chiều dày màng (nm) 10/180 Hình 2.7. Hình ảnh điện cực và lò vi nhiệt sau khi chế tạo 8 Sau khi được phún xạ một lớp Cr/Pt, ta dùng aceton để bóc tách đi những phần Cr/Pt phủ trên chất cảm quang, phần Cr/Pt còn lại bám trên bề mặt SiO2 chính là điện cực và lò vi nhiệt. d) Quang khắc Mask 2 và phún xạ tạo màng mỏng nhạy khí SnO2: Sử dụng kỹ thuật quang khắc như Bảng 2.4, sử dụng Mask 2 [Hình 2.3(c)]. Màng SnO2 chế tạo bằng phương pháp phún xạ hoạt hóa (Reactive sputtering) sử dụng bia kim loại thiếc (Sn) trong điều kiện có ôxy hỗ trợ. Chiều dày màng mỏng được khống chế theo thời gian phún xạ, các thông số như công suất, áp suất phún xạ được giữ nguyên. Bảng 2.6. Thông số phún xạ màng mỏng SnO2 Bảng 2.6. Thông số phún xạ màng mỏng SnO2 Lò vi nhiệt Bia Sn Độ tinh khiết 99,99% Điện cực Áp suất (µbar) 5* 10-6 Áp suất phún xạ (µbar) 3 * 10-3 Màng nhạy khí Tỷ lệ khí Ar : O2 (sccm) 15 : 15 Công suất W (nguồn DC) 50 Màng nhạy Màng nhạy Tùy thuộc vào chiều dày Photoresist Thời gian Điện cực, lò vi nhiệt màng SiO SiO22 Chiều dày màng (nm) 20; 40; 60 và 80 ĐếĐếSilicSilic Hình 2.9. Hình ảnh lớp màng nhạy khí SnO trên điện cực sau khi chế tạo 2 e) Quang khắc Mask 3 và phún xạ đảo xúc tác: Sử dụng mặt nạ thứ 3 [Hình 2.3(b)] để tạo đảo xúc tác . Phún xạ đảo xúc tác: Cảm biến có thể được chế tạo với nhiều loại đảo xúc tác khác nhau. Chúng tôi đã tiến hành phún xạ Pd, Pt, Au, CrO, FeO, và CuO làm đảo xúc tác. Chiều dày đảo xúc tác được chúng tôi khống chế bằng cách thay đổi theo thời gian. Các thông số như công suất và áp suất phún xạ không thay đổi. Các thông số phún xạ được tóm tắt trong Bảng 2.7. Bảng 2.7. Thông số phún xạ đảo xúc tác Bia Pd, Cu Độ tinh khiết 99,99% Lò vi nhiệt Điện cực Áp suất (µbar) 5* 10-6 Màng nhạy khí Áp suất phún xạ (µbar) 3 * 10-3 Đảo xúc tác Tỷ lệ khí Ar (sccm) 30 Đảo xúc tác Công suất W (nguồn DC) 30 Màng nhạy Thời gian Tùy thuộc vào chiều dày màng Điện cực, lò vi nhiệt SiO2 Chiều dày màng (nm) 5, 10, 15, 20 và 40 Đế Silic Hình 2.12. Hình ảnh lớp đảo xúc tác trên màng nhạy khí SnO2 sau khi chế tạo 9 Trên Hình 2.11 là cảm biến màng mỏng SnO2 pha tạp các loại đảo xúc tác sau khi chế tạo qua các công đoạn dựa trên kỹ thuật vi điện tử và phún xạ hoạt hóa. Số cảm biến sau khi chế tạo đạt khoảng 400 chíp trên một đế silic 4 inch. Các cảm biến này sẽ được đo khảo sát đặc trưng nhạy khí ở các chương tiếp theo. Các cảm biến pha tạp đảo xúc tác kim loại như Pd, Pt, Au được nghiên cứu với khí H2, trong khi các cảm biến biến tính bởi đảo ôxít CuO, NiO, FeO được nghiên cứu với khí H2S theo các nhiệt độ khác nhau. Tính chọn lọc của cảm biến đối với các khí như CO, LPG, NH3 v.v cũng được nghiên cứu. Hình 2.11. Hình ảnh cảm biến sau khi chế tạo: Phiến silic 4 inch (a); Cảm biến màng mỏng SnO2 (b) và cảm biến có đảo xúc tác (c). 2.5. Khảo sát đặt trưng nhạy khí của cảm biến Nghiên cứu tính chất nhạy khí của cảm biến đo độ dẫn chỉ cần đo điện trở của cảm biến theo thời gian. Với điều kiện phòng thí nghiệm, chúng tôi đã chọn nguồn thế để đo điện trở theo thời gian. Để đo đặc trưng nhạy khí của cảm biến chúng tôi sử dụng các khí chuẩn được trộn với không khí khô bằng các bộ điều khiển lưu lượng khí để pha trộn khí tạo ra nồng độ khí cần đo. Nồng độ khí được tính theo công thức: C (ppm) = Ck f/(f + F) trong đó Ck (ppm) là nồng độ khí chuẩn, f là lưu lượng khí chuẩn và F là lưu lượng không khí khô. Sơ đồ nguyên lý của hệ đo được biểu diễn trên Hình 2.12(a). 10 CHƯƠNG 3. CẢM BIẾN KHÍ H2 TRÊN CƠ SỞ MÀNG MỎNG SnO2 BIẾN TÍNH Pd (SnO2/Pd) 3.1. Giới thiệu Trong tương lai khí Hydro (H2) có tiềm năng trở thành một nguồn năng lượng xanh, sạch và năng lượng tái tạo, có thể ứng dụng trong pin nhiên liệu cho các phương tiện vận tải như ô tô, máy phát điện, máy bay, và phi thuyền, v.v [79]. Khí H2 là một chất khí nhẹ, không màu, không mùi, không vị. Do có kích thước phân tử nhỏ, khí H2 rất khó khăn trong việc lưu trữ và vận chuyển vì nó có thể rò rỉ dễ dàng từ các bình chứa. Rò rỉ khí H2 có thể gây nên hậu quả nghiêm trọng đó là hiện tượng cháy nổ [96]. Vì vậy, việc phát hiện rò rỉ khí H2 đã trở thành một vấn đề hết sức quan trọng trong vận chuyển, lưu chữ và sử dụng loại khí này. Để giảm thiểu những dủi do gây bởi sự rò rỉ khí H2 đòi hỏi phải có thế hệ cảm biến khí tiên tiến có thể phát hiện sớm một lượng nhỏ khí H2, đồng thời báo động về sự rò rỉ của khí H2 trong quá sản xuất, bảo quản, vận chuyển và sử dụng [36, 65, 72]. Cảm biến điện trở hoạt động dựa vào sự thay đổi độ dẫn điện trong chất bán dẫn ôxít kim loại có cấu trúc nano khi xảy ra hiện tượng hấp phụ/giải hấp của các phân tử khí được cho là phù hợp trong ứng dụng này. Trên cơ sở đó chúng tôi đã lựa chọn và đưa ra được quy trình chế tạo cảm biến khí H2 trên cơ sở màng mỏng SnO2 sử dụng đảo xúc tác là Pd. Chúng tôi cũng chỉ ra rằng cảm biến màng mỏng SnO2 biến tính đảo xúc tác Pd có độ đáp ứng cao và độ chọn lọc tốt. Ở đây, chiều dày màng mỏng SnO2 và đảo Pd được khống chế để tìm ra các thông số tối ưu cho cảm biến khí H2. Đây là tiền đề rất quan trọng để có thể đưa cảm biến đo khí H2 trên cơ sở màng mỏng SnO2/Pd vào ứng dụng trong cuộc sống. 3.2. Kết quả và thỏa luận 3.2.1. Khảo sát hình thái, cấu trúc vật liệu cảm biến màng mỏng SnO2 Để khảo sát cấu trúc tinh thể của màng mỏng SnO2 chúng tôi đã tiến hành đo giản đồ nhiễu xạ tia X của màng mỏng phún xạ trên đế SiO2 với cùng điều kiện. Kết quả thu được chỉ ra trên Hình 3.4 cho thấy giản đồ nhiễu xạ tia X xuất hiện các đỉnh nhiễu xạ lớn nhất tại các góc quét 2 = 26,65o; 33,7o và 51,7o ứng với các mặt (110), (101) và (211) của cấu trúc rutile của SnO2. Kết quả XRD hoàn toàn phù hợp với thư viện phổ JCPDS của SnO2 (thẻ 41-1445). Không thấy các đỉnh nhiễu xạ của các tạp chất như Sn, điều này khẳng định màng mỏng chế tạo là đơn pha SnO2. Chúng tôi cũng đã nghiên cứu kiểm tra hình thái o bề mặt của màng mỏng SnO2 sau khi nung ở nhiệt độ 400 C/2h bằng kính hiển vi điện tử quét phát xạ trường FESEM. Kết quả nghiên cứu hình thái bề mặt của màng SnO2 bằng ảnh FESEM được chỉ ra trên Hình 3.5. Qua hình ảnh FESEM, ta thấy bề mặt màng có độ đồng đều khá cao, bề mặt màng không bị rạn nứt. Màng mỏng được hình thành từ các hạt mịn và có kích thước cỡ 15 nm. 11 (a) (b) Tetragonal SnO 2 JCPDS, 41 - 1445 (110) 100 nm 100 nm (101) (d) (c) Cêng (®.v.t.y.) ®é (211) 20 25 30 35 40 45 50 55 100 nm 100 nm Gãc quÐt 2 (.) Hình 3.4. Giản đồ nhiễu xạ tia X của màng SnO2. Hình 3.5. Ảnh FESEM của màng mỏng SnO2 ở các chiều dày khác nhau: (a) 20; (b) 40; (c) 60 và (d) 80 nm. 3.2. Hình thái cảm biến màng mỏng SnO2/Pd Trên Hình 3.6 là ảnh chụp bằng kính hiển vi điện tử quét phát xạ trường (FESEM) của cảm biến màng mỏng SnO2 đã có đảo xúc tác Pd. Từ kết quả chụp FESEM của màng mỏng SnO2/Pd, ta thấy đã chế tạo thành công lớp đảo xúc tác lên trên lớp màng mỏng SnO2. Hình 2.6(b) và Hình 2.6(c) cho thấy ma trận đảo Pd và đảo Pd có hình tròn, đường kính khoảng 5 μm và được phân bố đều đặn phù hợp với cấu trúc đã thiết kế của cảm biến. 3.3. Khảo sát đặc trưng nhạy khí của cảm biến 3.3.1. Cảm biến màng mỏng SnO2 Cảm biến màng mỏng SnO2 với chiều dày lớp màng mỏng khác nhau lần lượt là 20, 40, 60 và 80 nm, được chúng tôi khảo sát tính chất nhạy khí theo các nhiệt độ và nồng độ khí khác nhau. Đầu tiên, khí H2 được lựa chọn để nghiên cứu do H2 là khí khử đặc trưng, có cấu trúc đơn giản, dễ dàng tương tác với vật liệu nhạy khí, và ít có những phản ứng phụ không mong muốn gây biến đổi cấu trúc của các vật liệu. Do cảm biến khí sử dụng vật liệu ô xít kim loại bán dẫn thường làm việc ở nhiệt độ cao, chúng tôi lựa chọn các nhiệt độ khảo sát cảm biến là 300, 350 và 400 oC. Với mục đích khảo sát và so sánh độ đáp ứng của các màng mỏng SnO2 có chiều dày khác nhau với khí H2, dải nồng độ khí H2 được lựa chọn thực hiện đo là 100, 250, 500 và 1000 ppm. Đây là dải nồng độ cao, sẽ cho độ đáp ứng cao, dễ dàng cho việc so sánh kết quả. Kết quả đo đặc trưng nhạy khí của các cảm biến màng mỏng SnO2 có chiều dày khác nhau được trình bày lần lượt dưới đây. Trên Hình 3.9(a) cho thấy đặc trưng hồi đáp khí theo thời gian của cảm biến màng mỏng SnO2 có chiều dày 40 nm khi đo nhạy khí H2 trong khoảng nồng độ 100 – 1000 ppm và giải nhiệt độ từ 300 – 400 ºC. Ta thấy rằng khi nhiệt độ đo và nồng độ khí đo tăng lên thì độ đáp ứng của cảm biến tăng lên. Trên Hình 3.9(c) ta thấy tại nhiệt độ 400 ºC cho độ đáp ứng là cao nhất. Độ đáp ứng khí theo các nồng độ khí đo khác nhau được thể hiện trên Hình 3.9(b), ta nhận thấy độ đáp ứng của cảm biến đạt các giá trị tương ứng lần lượt là: 1,9; 3,1; 5,2 và 11,5 lần. với các nồng độ khí là: 100, 250, 500 và 1000 ppm 12 100 250 500 1000 ppm 12 8 3 0 0 C 3 5 0 C (b) 4 0 0 C C (a) 9 5 300 ) g /R 3 a 6 R ( S 3 6 ) g C /R a 4 R 0 5 00 1 00 0 ( 350 S Nång ®é khÝ H (p p m ) 2 2 12 100 ppm (c) 250 ppm 12 9 500 ppm C ) 1000 ppm 8 g /R 400 a R ( 6 4 S 3 0 200 400 600 800 1000 0 Thêi gian (s) 300 350 400 N hiÖt ®é (C ) Hình 3.9. Các đặc trưng nhạy khí H2 của cảm biến màng mỏng SnO2 dày 40 nm: (a) Đặc trưng đáp ứng của cảm biến ở 300, 350 và 400 °C; độ đáp ứng biểu diễn phụ thuộc vào nồng độ khí (b) và nhiệt độ làm việc (c). 7 7 SnO (20 nm) 2 SnO (20 nm) @ 300 C 2 @ 250 ppm SnO (40 nm) 2 SnO (40 nm) 2 SnO (60 nm) 6 2 6 SnO (60 nm) 2 SnO (80 nm) 2 SnO (80 nm) 2 5 5 ) g /R 4 a 4 R ( S S 3 3 2 2 (a) (b) 1 1 200 400 600 800 1000 300 350 400 Nång ®é khÝ H (ppm) 2 NhiÖt ®é (C) Hình 3.12. Đồ thị so sánh độ đáp ứng của các cảm biến màng mỏng SnO2 có chiều dày khác nhau: Độ đáp ứng biểu diễn phụ thuộc vào nồng độ khí (a) và nhiệt độ làm việc (b). Trên Hình 3.12(a) xét tại thời điểm nhiệt độ 300 ºC ta thấy rằng, khi ta tăng nồng độ khí lên thì độ đáp ứng tăng theo tỷ lệ thuận và độ đáp ứng cao nhất ở màng mỏng 40 nm và thấp nhất ở màng mỏng 80 nm. Ta nhận thấy, màng mỏng SnO2 với chiều dày 40 nm cho độ đáp ứng cao nhất (đạt giá trị 6,5 khi đo ở 300 ºC với 1000 ppm khí H2). Trên Hình 3.12(b) với 250 ppm khí H2 ta thấy độ đáp ứng của màng SnO2 dày 20 nm là thấp nhất đạt giá trị từ 1,6 ở 300 ºC lên đến giá trị 1.7 ở 400 ºC. 13 3.3.2. Cảm biến màng mỏng SnO2 kết hợp đảo xúc tác Pd (SnO2/Pd) Cho đến nay, đã có nhiều công bố cho thấy vai trò xúc tác của kim loại Pd đối với cảm biến khí H2, không chỉ làm tăng độ nhạy mà nhiệt độ hoạt động của cảm biến cũng giảm đáng kể [115]. Trên cơ sở đó, chúng tôi đã sử dụng Pd để chế tạo lớp đảo xúc tác trên cảm biến màng mỏng SnO2 nhằm ứng dụng cho cảm biến khí H2. Với kết quả thu được trong [phần 3.3.1] ta thấy cảm biến màng mỏng SnO2 có chiều dày màng là 40 nm được chúng tôi lựa chọn để chế tạo lớp đảo xúc tác Pd lên trên. Mục đích là để khảo sát sự ảnh hưởng của các đảo Pd xúc tác đến hiệu suất làm việc của cảm biến (làm tăng độ đáp ứng). Các công đoạn chế tạo đảo xúc tác được trình bày trong [Chương 2]. Sử dụng bia Pd có đường kính 2 inch, độ sạch 99,99%. Công suất nguồn phún xạ là 30 W, tốc độ phún xạ là 10 nm/phút. Các chiều dày lớp màng đảo được chúng tôi tính toán dựa theo thời gian và tốc độ phún xạ của màng mỏng Pd. Chiều dày lớp đảo Pd được chế tạo lần lượt là 5; 10; 25 và 40 nm. Các cảm biến với chiều dày lớp đảo Pd khác nhau được khảo sát đặc trưng bởi sự thay đổi độ đáp ứng khi có sự tác động của khí H2 theo thời gian. Cảm biến được khảo sát trong giải nồng độ thấp của khí H2 (25-250 ppm) và nhiệt độ từ 200 ºC đến 400 ºC giống như khảo sát của màng mỏng SnO2. Kết qua đo khảo sát đặc trưng hồi đáp khí H2 của cảm biến SnO2/Pd với chiều dày lớp đảo Pd 10 nm trong giải nhiệt độ từ 200 ºC đến 400 ºC và trong giải nồng độ 25 - 250 ppm. Đặc trưng hồi đáp khí của cảm biến được trình bày trên Hình 3.19(a). Nhiệt độ làm việc tối ưu nhất của cảm biến là tại giá trị nhiệt độ 300 ºC. Độ đáp ứng của cảm biến là 27,8 ứng với nồng độ khí H2 là 250 ppm, các kết quả này được chỉ ra trên Hình 3.19(b). Cảm biến hoạt động ổn định và có khả năng hồi phục gần 100% tại các nhiệt độ. 250 100 50 25 ppm 30 30 200C @ SnO (40 nm) (a) 2 (b) 20 250C Pd (10 nm) @ 200C 10 300C 25 30 350C 20 400C 10 @ 250C 20 ) g 30 ) g /R a 20 /R R a ( 15 @ 300 C R 10 ( S S 30 S 20 10 @ 350C 10 30 5 20 10 @ 400 C 0 100 200 300 400 500 50 100 150 200 250 Thêi gian (s) Nång ®é khÝ H (ppm) 2 Hình 3.19. Đặc trưng nhạy khí H2 của cảm biến màng mỏng SnO2/Pd (dày 10 nm): (a) Đặc trưng đáp ứng khí ở 200, 250, 300, 350 và 400 °C và (b) Độ đáp ứng biểu diễn phụ thuộc vào nồng độ khí. 14 35 35 SnO /Pd (5 nm) SnO /Pd (5 nm) 2 (a) 2 (b) SnO /Pd (10 nm) SnO /Pd (10 nm) 2 2 30 30 SnO /Pd (25 nm) SnO /Pd (25 nm) 2 @ 250 (ppm) 2 SnO /Pd (40 nm) SnO /Pd (40 nm) 2 2 SnO 25 25 2 @ 300 C 20 20 ) g /R 15 a 15 R ( S 10 10 5 5 0 0 50 100 150 200 250 200 250 300 350 400 Nång ®é khÝ H (ppm) NhiÖt ®é (C) 2 Hình 3.22. Độ đáp ứng của các cảm biến SnO2/Pd biểu diễn phụ thuộc vào nồng độ khí (a)và nhiệt độ làm việc (b). Mặt khác, như trên Hình 3.22(b) ta thấy khi có đảo xúc tác Pd thì nhiệt độ làm việc của cảm biến có thể xuống được đến 200 ºC, trong khi đó cảm biến màng mỏng thuần SnO2 thì nhiệt độ làm việc xuống được 300 ºC. Cơ chế nhạy khí của cảm biến SnO2/Pd: Cơ chế nhạy khí của cảm biến có thể giải thích bằng mô hình suy giảm độ dẫn. Đối với cảm biến thuần màng mỏng SnO2 được hiểu do sự thay đổi độ dẫn bề mặt lớp cảm biến theo cơ chế hấp phụ ôxy. Ban đầu, khí ôxy hấp thụ vật lý trên bề mặt SnO2 dưới dạng các phân tử, sau đó chuyển dần sang hấp phụ hóa học dưới dạng các phân tử riêng lẻ ở nhiệt độ cao. − − O2(khí) → O2(hấp phụ vật lý) → O2 (hấp phụ hóa học) → O ( hấp phụ hóa học) → O2−( hấp phụ hóa học) - - 2- Các phân tử (O2 , O và O ) trên bề mặt bẫy các điện tử của màng SnO2 hình thành vùng nghèo điện tử, kết quả làm tăng rào thế và điện trở của màng. Khi tiếp xúc với khí H2, ôxy hấp phụ trên bề mặt sẽ phản ứng với H2, trả lại điện tử cho màng SnO2, rào thế sẽ bị giảm, dẫn đến sự giảm điện trở của màng mỏng. Phương trình phản ứng: - H2 (khí) + O (hấp phụ) → H2O (khí) + e− Đối với cảm biến SnO2/Pd có 2 cơ chế chính đóng góp vào đặc tính nhạy khí đó là (1) cơ chế hóa học và (2) là cơ chế nhạy điện tử [118]. Cơ chế hóa học dựa vào hoạt động xúc tác của Pd thông qua sự lan tỏa, ở đó sự phân ly của phân tử oxy (i) và phân tử hydro (ii) để tăng cường các ion oxy tiền hấp thụ trên bề mặt của SnO2, cũng như tăng cường tương tác giữa hydro và các ion oxy tiền hấp thụ nhằm tăng độ đáp ứng của cảm biến đối với khí H2. 15 60 60 SnO - Pd 5 nm SnO - Pd 5 nm 2 (a) (b) 2 SnO - Pd 10 nm SnO - Pd 10 nm 2 2 50 SnO - Pd 25 nm 50 SnO - Pd 25 nm 2 2 SnO - Pd 40 nm SnO - Pd 40 nm 2 2 40 40 @ 300 C 30 30 20 20 Thêi
File đính kèm:
nghien_cuu_che_tao_cam_bien_khi_h2_va_h2s_tren_co_so_mang_sn.pdf