Luận án Nghiên cứu hỗn hợp đá – nhựa nóng cường độ cao dùng trong kết cấu mặt đường ô tô cấp cao ở Việt Nam
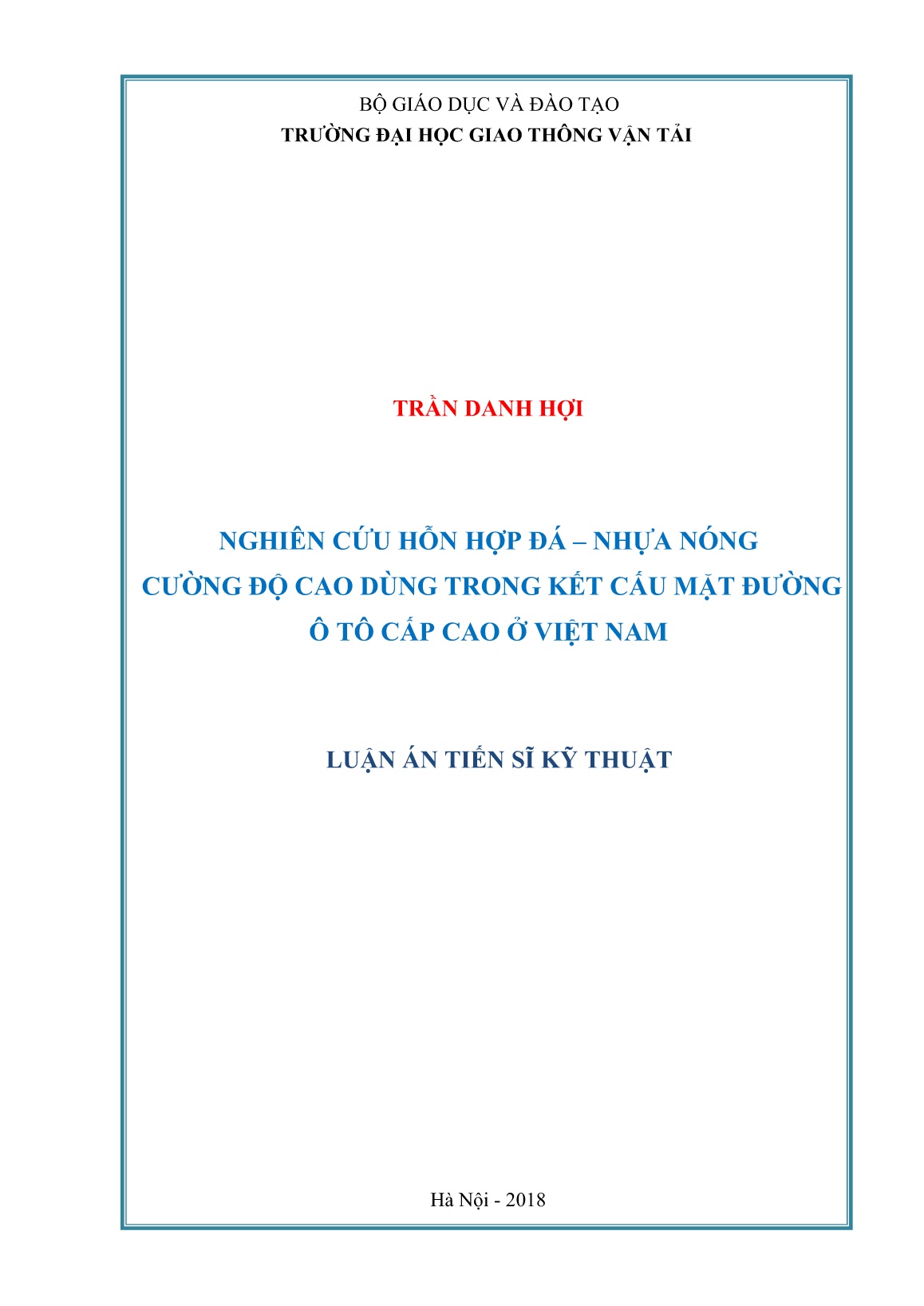
Trang 1
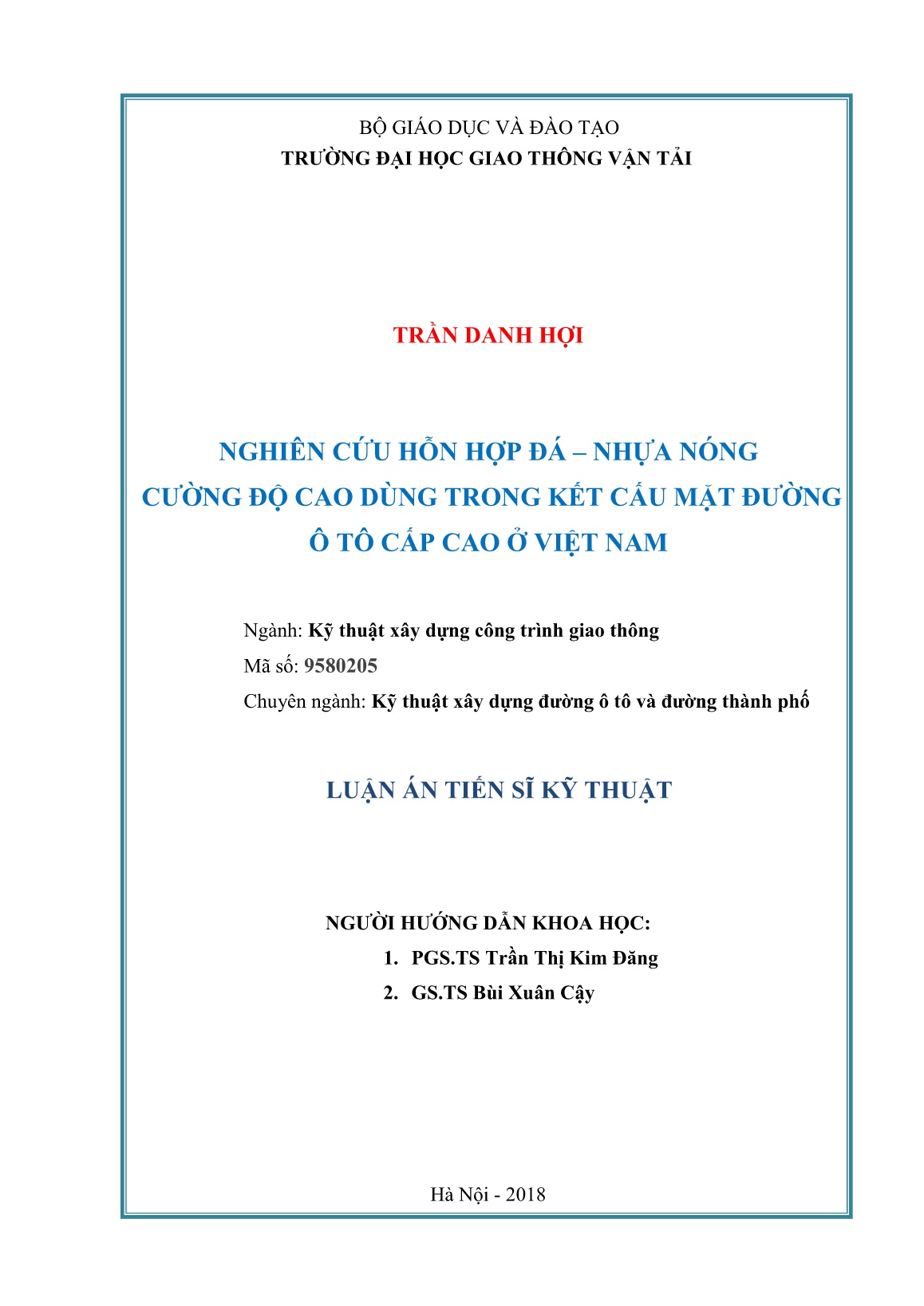
Trang 2
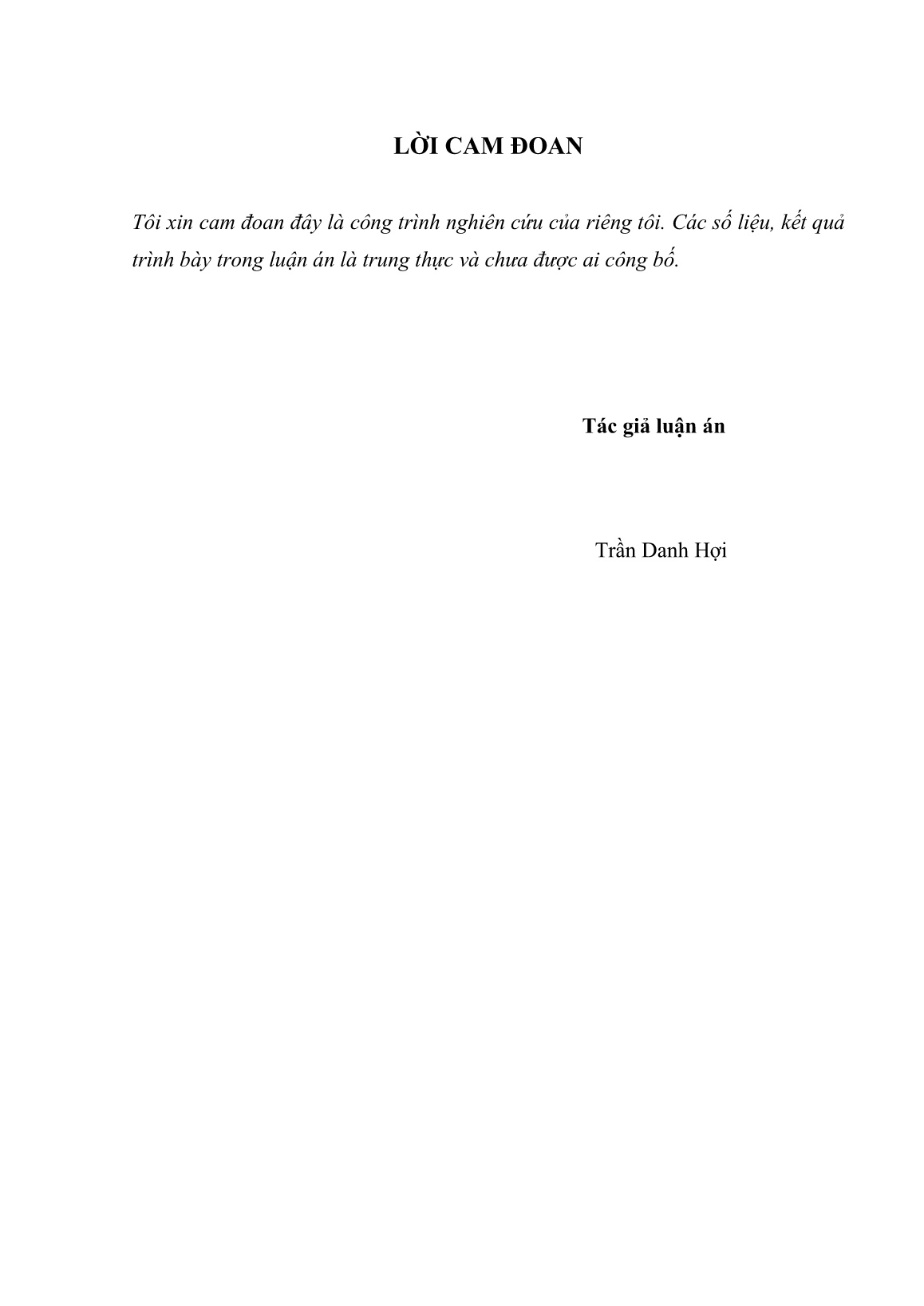
Trang 3
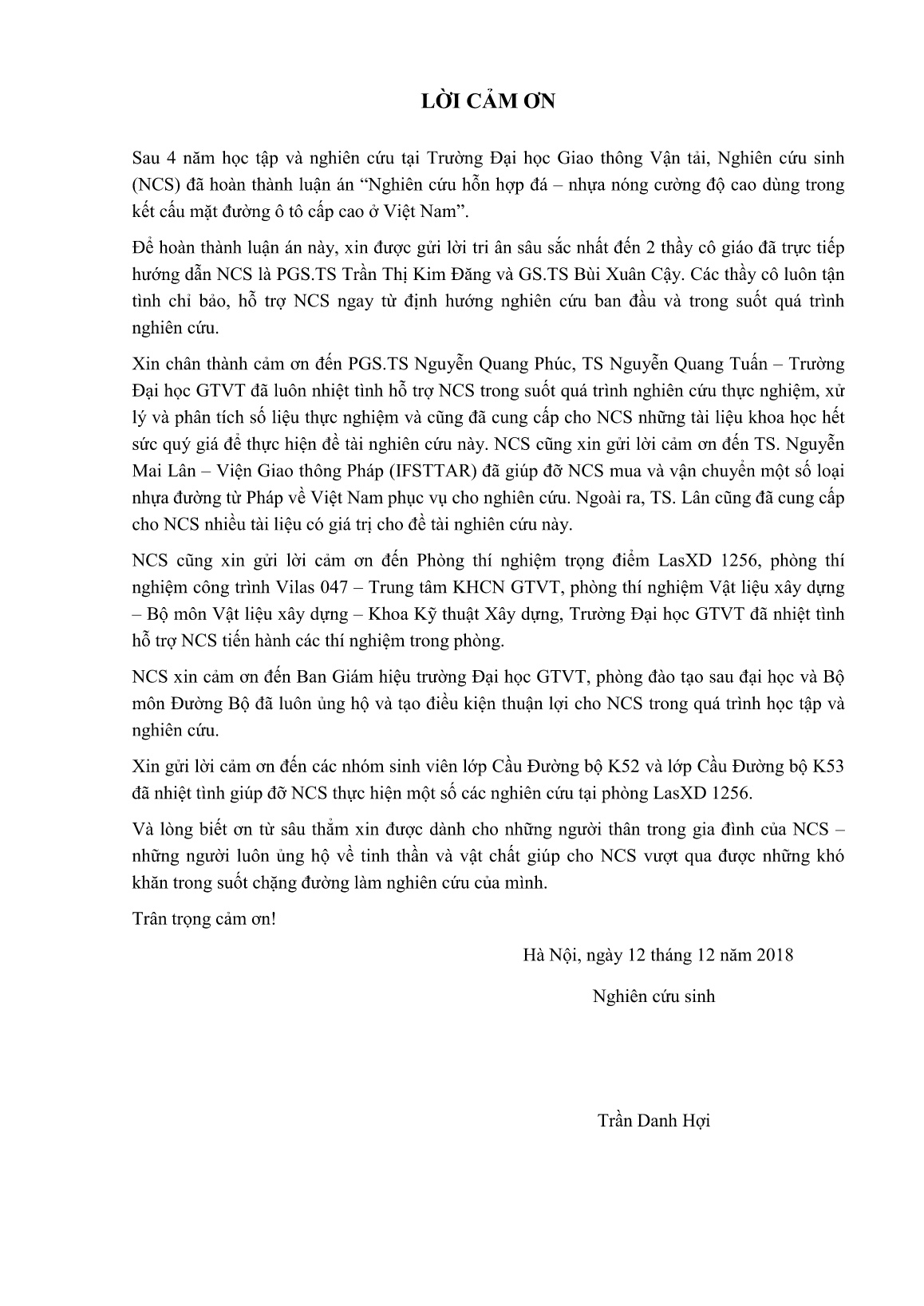
Trang 4
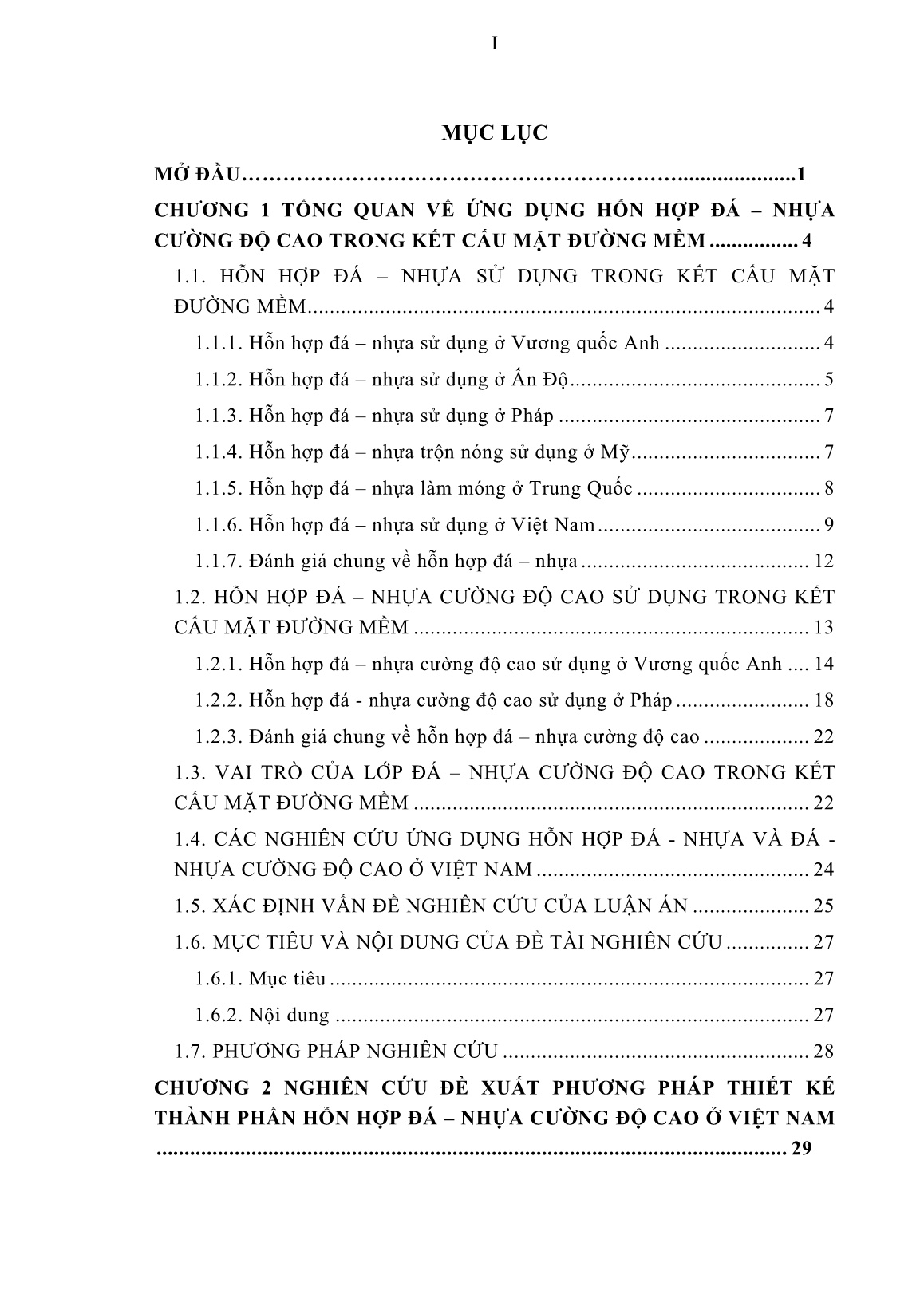
Trang 5
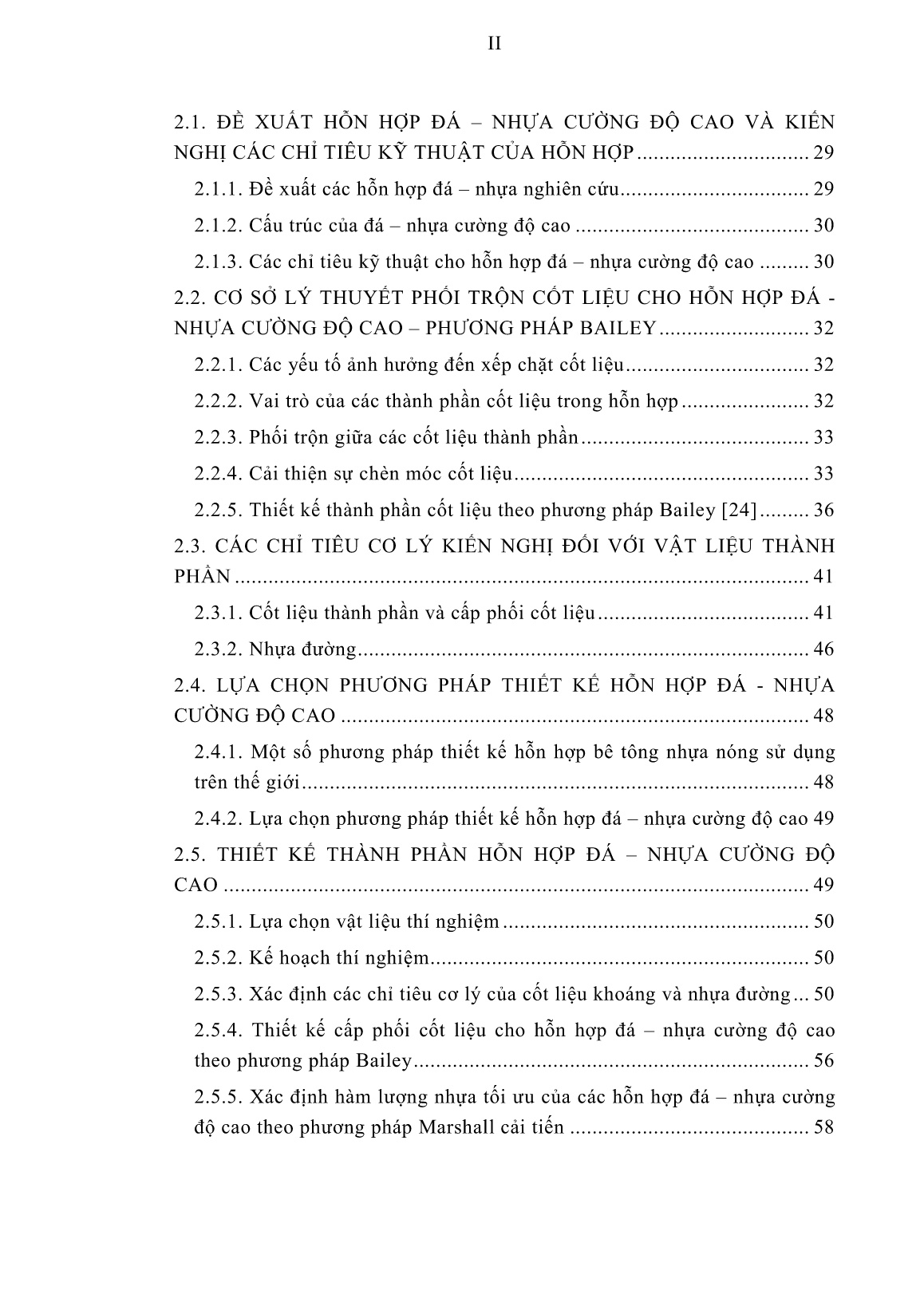
Trang 6
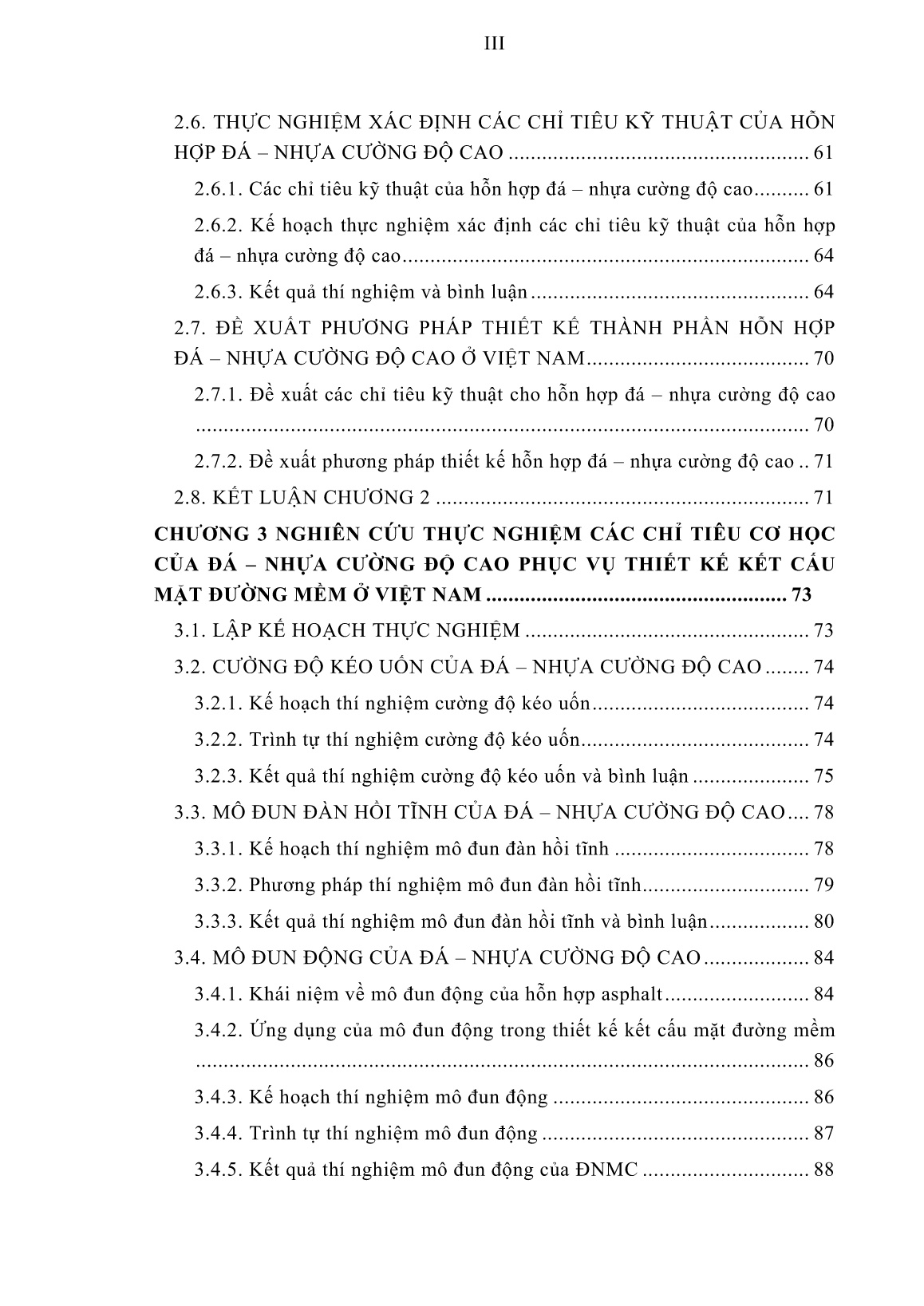
Trang 7
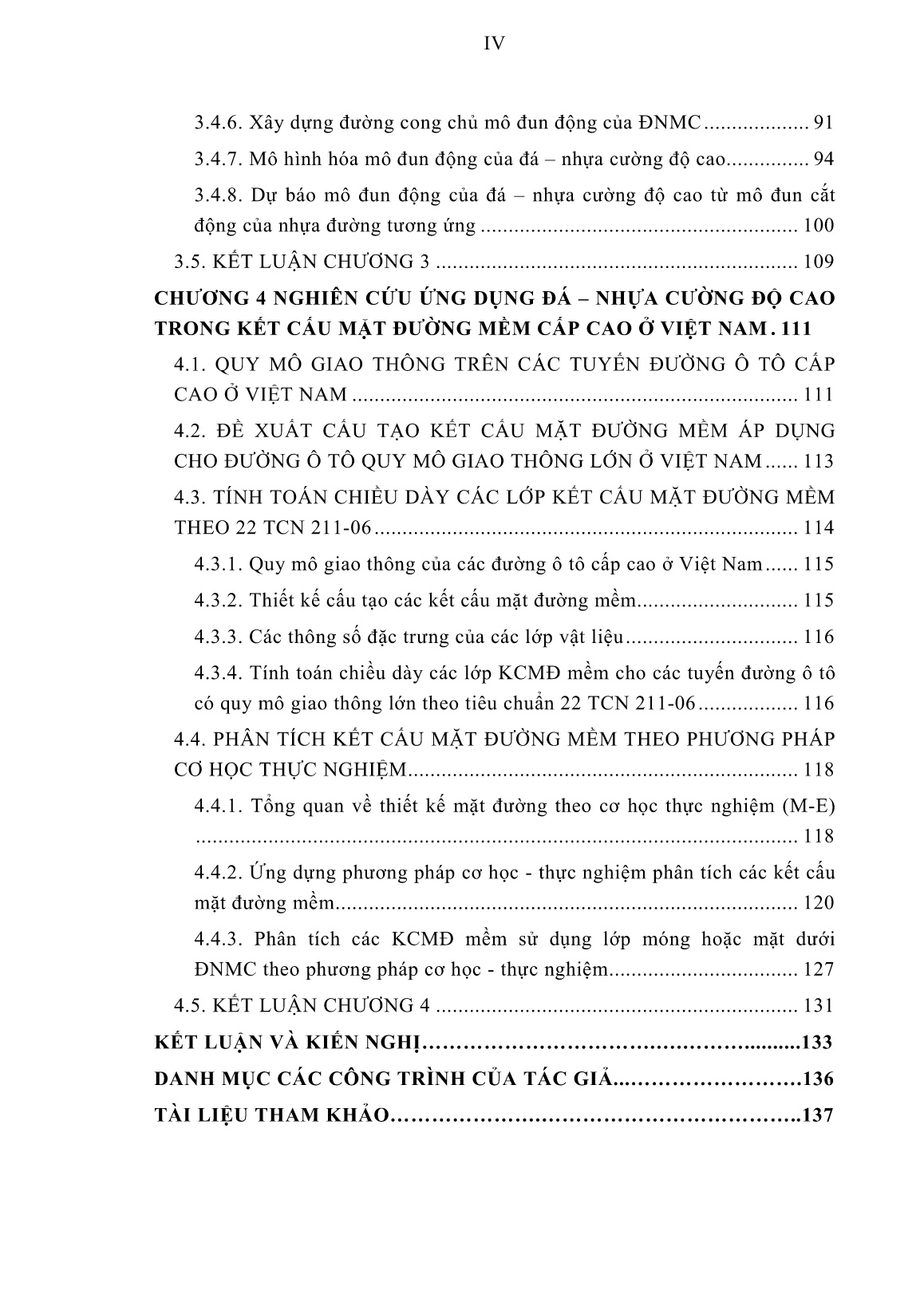
Trang 8
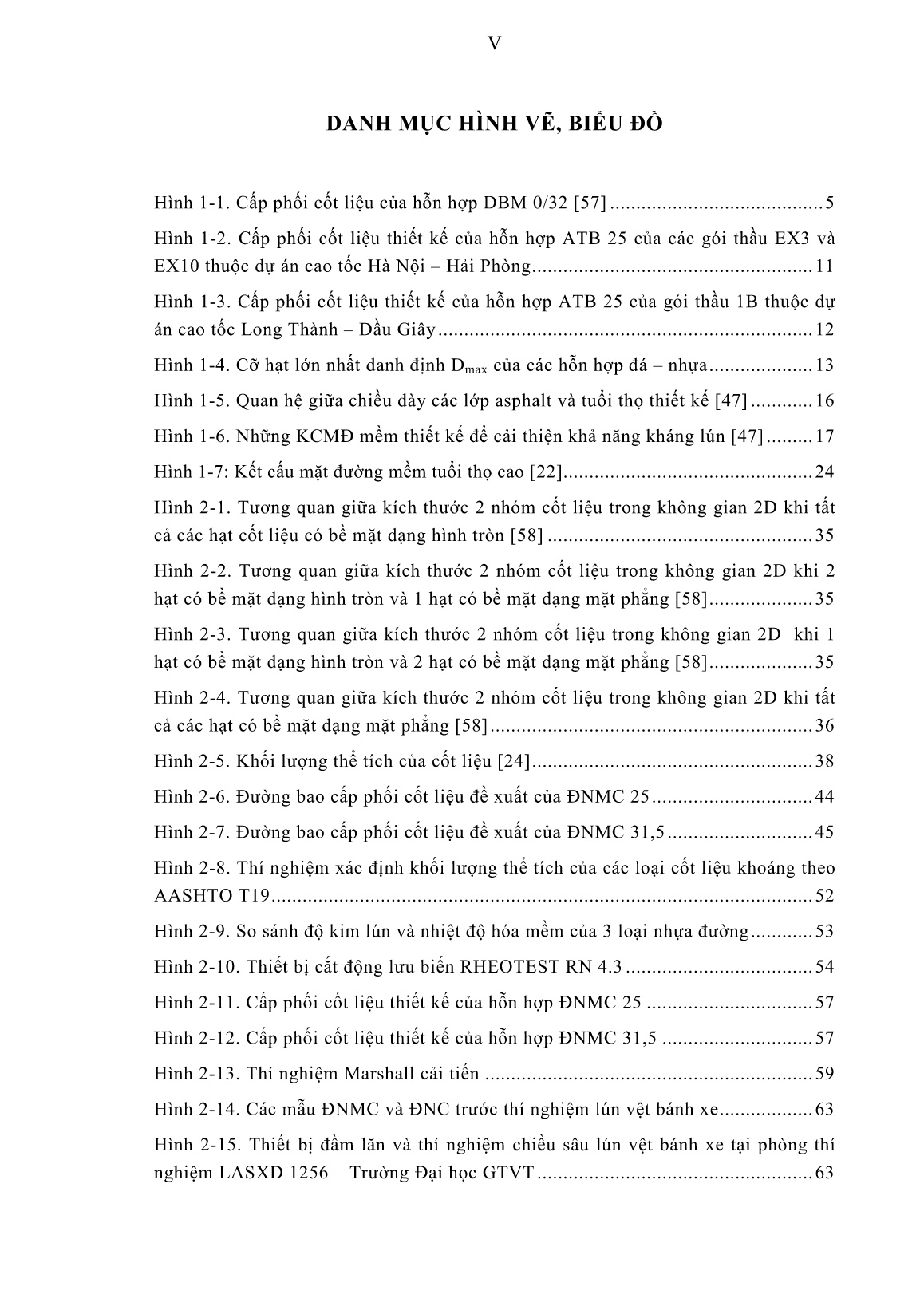
Trang 9
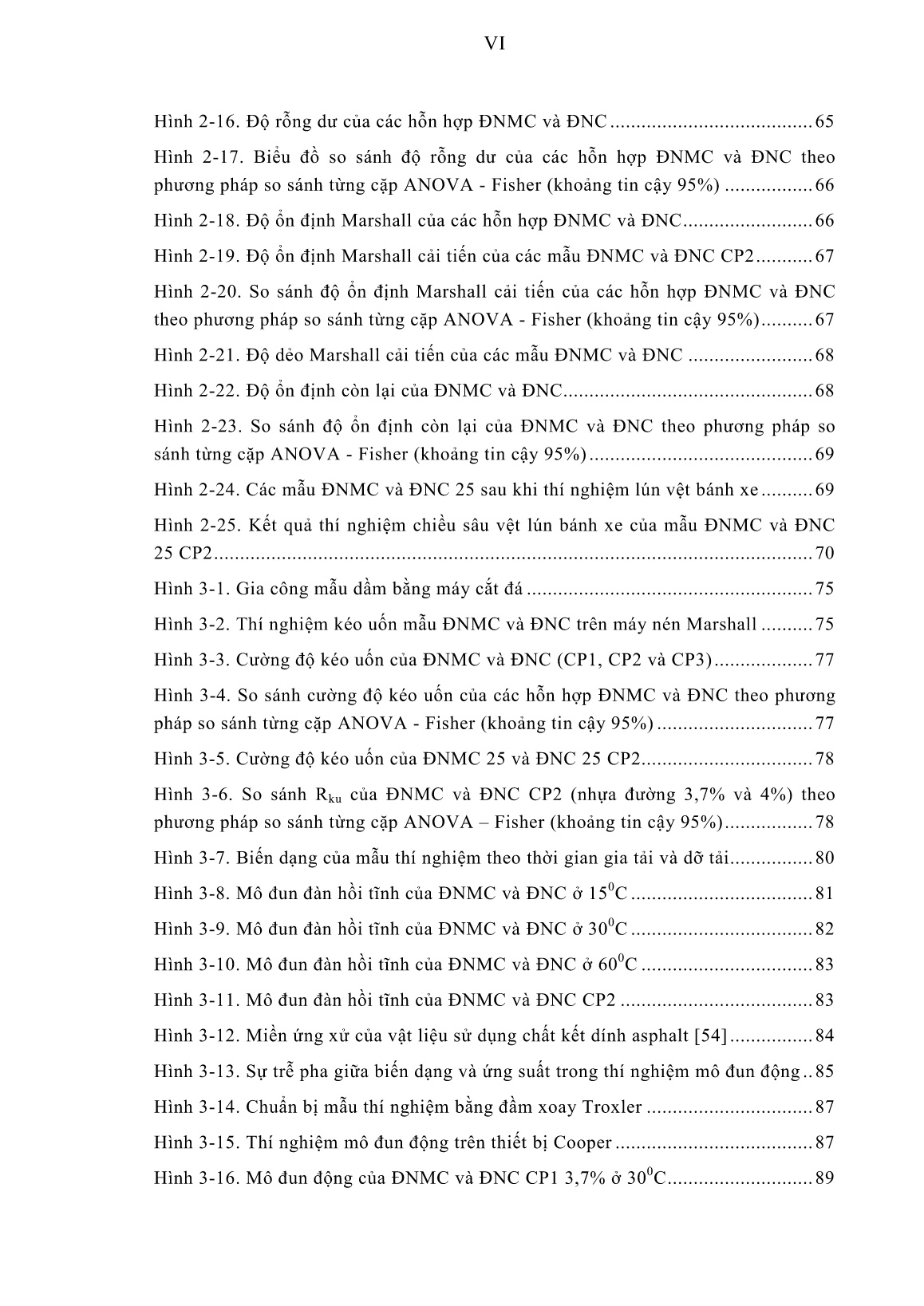
Trang 10
Tải về để xem bản đầy đủ
Bạn đang xem 10 trang mẫu của tài liệu "Luận án Nghiên cứu hỗn hợp đá – nhựa nóng cường độ cao dùng trong kết cấu mặt đường ô tô cấp cao ở Việt Nam", để tải tài liệu gốc về máy hãy click vào nút Download ở trên.
Tóm tắt nội dung tài liệu: Luận án Nghiên cứu hỗn hợp đá – nhựa nóng cường độ cao dùng trong kết cấu mặt đường ô tô cấp cao ở Việt Nam
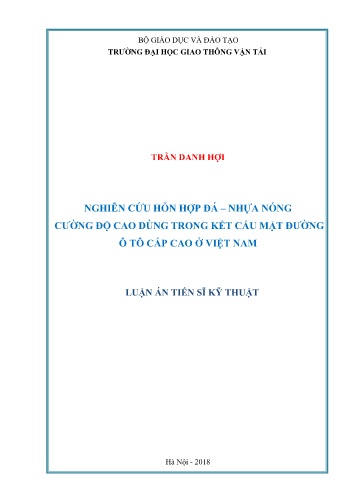
cứu này, phương pháp Marshall được lựa chọn để thiết kế hỗn hợp ĐNMC. Tuy nhiên, do các hỗn hợp ĐNMC thiết kế có Dmax = 25 mm và 31,5 mm kiến nghị sử dụng khuôn Marshall cải tiến. Phương pháp Bailey được sử dụng kết hợp với phương pháp Marshall cải tiến để thiết kế thành phần của các hỗn hợp ĐNMC và ĐNC đối chứng. 2.5. THIẾT KẾ THÀNH PHẦN HỖN HỢP ĐÁ – NHỰA CƯỜNG ĐỘ CAO 50 2.5.1. Lựa chọn vật liệu thí nghiệm - Đá dĕm các loại và cát nghiền được khai thác và gia công tại mỏ đá Thống Nhất, tỉnh Hải Dương. - Bột khoáng sản xuất bởi xí nghiệp tư nhân Hồng Lạc, Hải Dương. - Nhựa đường sử dụng gồm: nhựa đường mác 20/30, 35/50 của hãng Total, Pháp và nhựa đường mác 60/70 của Shell Singapore được nhập khẩu bởi công ty TNHH nhựa đường Petrolimex Việt Nam. 2.5.2. Kế hoạch thí nghiệm Các nghiên cứu thực nghiệm xác định thành phần của hỗn hợp đá – nhựa cường độ cao được thực hiện trong phòng với các nội dung chủ yếu sau: - Xác định các chỉ tiêu cơ lý của cốt liệu khoáng và nhựa đường; - Thiết kế các cấp phối cốt liệu đá – nhựa cường độ cao; - Xác định hàm lượng nhựa tối ưu của các hỗn hợp đá – nhựa cường độ cao tương ứng với các cấp phối thiết kế và nhựa đường lựa chọn. Các thí nghiệm cần thực hiện và số lượng mẫu yêu cầu được thể hiện trong từng nội dung nghiên cứu. 2.5.3. Xác định các chỉ tiêu cơ lý của cốt liệu khoáng và nhựa đường 2.5.3.1. Các chỉ tiêu cơ lý của cốt liệu khoáng Các chỉ tiêu cơ lý cơ bản của các cốt liệu thành phần và bột khoáng được thí nghiệm tại phòng thí nghiệm Lasxd 1256 – Trường Đại học Giao thông Vận tải. Các kết quả thí nghiệm được tổng hợp ở Bảng 2-4. Các chỉ tiêu này đều thỏa mãn các yêu cầu quy định tại quyết định 858/QĐ – BGTVT [2]. Bảng 2-4. Các chỉ tiêu cơ lý của đá dĕm và bột khoáng Chỉ tiêu thí nghiệm Loại cốt liệu Đá 10/31,5 Đá 10/25 Đá 10/20 Đá 5/10 Cát nghiền 0/5 Bột khoáng Tỷ trọng khối (Gsb) 2,741 2,727 2,711 2,707 2,702 2,713 Tỷ trọng khối của mẫu bão hòa khô bề mặt (Gssb) 2,746 2,731 2,717 2,716 2,720 - Tỷ trọng biểu kiến (Gsa) 2,753 2,739 2,727 2,731 2,751 - Khả nĕng hấp phụ (%) 0,154 0,172 0,216 0,320 0,659 - 51 Chỉ tiêu thí nghiệm Loại cốt liệu Đá 10/31,5 Đá 10/25 Đá 10/20 Đá 5/10 Cát nghiền 0/5 Bột khoáng Hàm lượng bụi, bùn, sét (%) 0,377 0,316 0,365 0,702 - 2,329 Hàm lượng hạt thoi dẹt (%) 4,28 3,84 5,79 5,20 - - Mô đun độ lớn của cốt liệu mịn - - - - - 3,285 Hệ số đương lượng cát của cốt liệu mịn (%) - - - - - 73,540 Hàm lượng sét cục (%) - - - - - 0,251 Hàm lượng hạt mềm yếu, phong hóa 0,35 0,42 0,508 0,35 - - Khả nĕng dính bám với nhựa Cấp 3 Thành phần cấp phối cốt liệu của đá dĕm các loại và bột khoáng thể hiện ở Bảng 2-5. Bảng 2-5. Cấp phối cốt liệu của đá dĕm các loại và bột khoáng Cỡ sàng (mm) % lọt sàng Đá 10/40 Đá 10/31,5 Đá 10/20 Đá 5/10 Đá 0/5 Bột khoáng 37,5 100,00 100,00 100,00 100,00 100,00 100,00 31,5 89,89 100,00 100,00 100,00 100,00 100,00 25 57,76 90,84 100,00 100,00 100,00 100,00 19 29,69 37,86 100,00 100,00 100,00 100,00 12,5 3,84 4,89 69,11 100,00 100,00 100,00 9,5 0,51 0,65 21,73 99,12 100,00 100,00 4,75 0,19 0,24 2,21 26,30 99,49 100,00 2,36 0,16 0,20 1,43 1,91 65,89 100,00 1,18 0,13 0,16 1,16 1,46 46,28 100,00 0,6 0,00 0,00 0,96 1,26 31,58 100,00 0,3 0,00 0,00 0,74 1,07 16,07 99,79 0,15 0,00 0,00 0,63 0,97 11,66 98,60 0,075 0,00 0,00 0,38 0,80 8,36 84,89 Để thiết kế cấp phối cốt liệu theo phương pháp Bailey cần xác định khối lượng thể tích của các cốt liệu ở trạng thái xốp và chặt theo AASHTO T19 (xem Hình 2-8). 52 Hình 2-8. Thí nghiệm xác định khối lượng thể tích của các loại cốt liệu khoáng theo AASHTO T19 Kết quả thí nghiệm xác định khối lượng thể tích của cốt liệu khoáng cho các cốt liệu thành phần thể hiện ở Bảng 2-6. Bảng 2-6. Khối lượng thể tích của các cốt liệu thành phần STT Loại cốt liệu Khối lượng thể tích (kg/m 3) Trạng thái xốp Trạng thái chặt 1 Đá dĕm 10/31,5 1455,03 1629,47 2 Đá dĕm 10/25 1421,86 1584,48 3 Đá dĕm 10/20 1393,89 1569,12 4 Đá dĕm 5/10 1318,52 1521,52 5 Cát nghiền 0/5 1629,58 1840,54 2.5.3.2. Nhựa đường a) Các chỉ tiêu cơ bản của nhựa đường Kết quả thí nghiệm trong phòng các chỉ tiêu cơ bản của nhựa đường nghiên cứu thể hiện ở Bảng 2-7. Bảng 2-7. Các chỉ tiêu cơ bản của 3 loại nhựa đường nghiên cứu TT Chỉ tiêu Đơn vị Giá trị Phương pháp thử nghiệm Nhựa 20/30 Nhựa 35/50 Nhựa 60/70 1 Độ kim lún ở 25˚C, 0,1mm, 5s 1/10 mm 21,3 40,0 62,0 TCVN 7495:2005 2 Độ kéo dài ở 25 0C, 5 cm/phút cm 69 >100 >100 TCVN 7496:2005 3 Nhiệt độ hóa mềm 0C 61,7 53,2 48,8 TCVN 7497:2005 4 Điểm chớp cháy 0C 332 336 328 TCVN 7498:2005 53 TT Chỉ tiêu Đơn vị Giá trị Phương pháp thử nghiệm Nhựa 20/30 Nhựa 35/50 Nhựa 60/70 5 Tổn thất khối lượng sau khi gia nhiệt 5 giờ ở 1630C so với ban đầu % 0,13 0,14 0,35 TCVN 7495:2005 6 Khối lượng riêng ở 250C g/cm 3 1,044 1,030 1,032 TCVN 7501:2005 7 Độ dính bám với đá cấp 3 cấp 3 cấp 3 TCVN 7504:2005 Các chỉ tiêu cơ bản của 3 loại nhựa đường đều thỏa mãn quy định kỹ thuật đối với nhựa đường dùng trong công trình giao thông ban hành kèm theo thông tư 27/2014/TT-BGTVT của Bộ trưởng Bộ GTVT. Từ biểu đồ Hình 2-9 có thể nhận thấy rằng loại nhựa đường 20/30 có độ kim lún thấp nhất và nhiệt độ hóa mềm cao nhất. Nhiệt độ hóa mềm của loại nhựa đường 20/30 lớn hơn đáng kể (+12,9 0C) so với 60/70. Với 2 loại nhựa đường 35/50 và 60/70 mặc dù độ kim lún có sự chênh lệch lớn nhưng nhiệt độ hóa mềm chỉ cao hơn +4,40C. Nhiệt độ hóa mềm của 2 loại nhựa đường 20/30 và 35/50 cao hơn so với 60/70 là cơ sở để cải thiện tính chất của đá – nhựa nghiên cứu. Hình 2-9. So sánh độ kim lún và nhiệt độ hóa mềm của 3 loại nhựa đường b) Xác định một số chỉ tiêu của nhựa đường theo cấp đặc tính PG Theo tiêu chuẩn AASHTO M320-10 [20], nhựa đường được phân loại theo đặc tính PG (Performance Grade). Phân cấp nhựa đường theo phương pháp này đã xem xét ảnh hưởng của nhiệt độ đến tính chất của nhựa đường, từ đó có thể lựa chọn nhựa đường phù hợp với các vùng khí hậu và điều kiện giao thông khác nhau. Chính vì vậy, việc xác định một số tính chất của nhựa đường 21,3 40 6261,7 53,2 48,8 0 10 20 30 40 50 60 70 0 10 20 30 40 50 60 70 20/30 35/50 60/70 Nh iệt độ hóa mề m ( 0 C) Độ kim lún (1/ 10 mm ) Loại nhựa đường Nhiệt độ hóa mềm Độ kim lún 54 theo cấp đặc tính PG là cần thiết, làm cơ sở dự báo các tính chất của các hỗn hợp đá – nhựa tương ứng. Để phân loại nhựa đường theo đặc tính PG, một trong các thí nghiệm quan trọng nhất là thí nghiệm cắt động lưu biến xác định mô đun cắt động (|G*|) và góc pha () của nhựa đường ở các trạng thái gốc, sau hóa già ngắn hạn RTFO và sau hóa giá dài hạn PAV ở tần số 1,59 Hz. Nghiên cứu này sử dụng thiết bị cắt động lưu biến DSR RHEOTEST RN 4.3 (xem Hình 2-10). Thí nghiệm cắt động lưu biến được thực hiện với mẫu nhựa đường hình trụ đường kính 25 mm dày 1 mm hoặc đường kính 8 mm dày 2 mm được đặt kẹp giữa 2 đĩa hình tròn.Trong khi thí nghiệm, đĩa phía dưới được cố định trong khi đĩa phía trên dao động điều hòa để tạo ra lực cắt. Thí nghiệm được điều khiển bằng phần mềm chuyên dụng. Hình 2-10. Thiết bị cắt động lưu biến RHEOTEST RN 4.3 Nguyên tắc đo Thực nghiệm được thực hiện bằng cách tạo ra biến dạng góc trên mẫu nhựa đường ở các nhiệt độ và tần số khác nhau. Biến dạng này là một hàm số dạng hình sin của thời gian là một dao động điều hòa. max sin( )t (2-11) Ứng suất cắt đo được có dạng hình sin nhưng có sự lệch pha giữa ứng suất cắt và biến dạng theo công thức: max sin( )t (2-12) Giá trị của mô đun cắt động được tính theo công thức (2-13: Máy tính Thiết bị đo Điều chỉnh nhiệt độ 55 * max max G (2-13) Trình tự thí nghiệm Các mẫu thí nghiệm cắt động được nung nóng đến nhiệt độ xấp xỉ 1630C bằng cách đặt trong tủ sấy và nung cho đến khi nóng chảy theo AASHTO T315-12. Một lượng nhỏ của mỗi loại nhựa được rót vào trong một khuôn nhỏ. Sau đó, các mẫu này sẽ được làm lạnh trong vòng 1,0 giờ trước khi thí nghiệm. Kế hoạch thí nghiệm Số lượng mẫu thử tương ứng với các thí nghiệm cần thực hiện để phân loại nhựa đường theo cấp đặc tính PG được thể hiện ở Bảng 2-8. Bảng 2-8. Số mẫu thí nghiệm phân loại nhựa đường theo cấp đặc tính PG TT Chỉ tiêu thí nghiệm Số lượng mẫu thí nghiệm 20/30 35/50 60/70 Thí nghiệm với nhựa đường gốc 1 Nhiệt độ bắt lửa theo tiêu chuẩn AASHTO T48, 0C 2 2 2 2 Độ nhớt ở 135 0C theo tiêu chuẩn AASHTO T316 2 2 2 3 Mô đun cắt động của nhựa đường gốc (T315), G*/sin, 10 rad/s, nhiệt độ 460C – 820C. 3 3 3 Thí nghiệm với nhựa đường sau RTFO (85 phút, 1630C theo AASHTO T240-13) 4 Tổn thất khối lượng sau RTFO, % 2 2 2 5 Mô đun cắt động của nhựa đường RTFO (T315), G*/sin, 10 rad/s, nhiệt độ 460C – 820C. 3 3 3 Thí nghiệm với nhựa đường sau PAV (20h, 1000C theo AASHTO R28-12) 6 Mô đun cắt động của nhựa đường PAV (T315), G*sin, 10 rad/s. 3 3 3 Kết quả thí nghiệm Các kết quả thí nghiệm cắt động lưu biến đối với các mẫu nhựa đường gốc, sau hóa già ngắn hạn RTFO và sau hóa già dài hạn PAV được thể hiện ở Phụ lục 2. Tổng hợp các kết quả thí nghiệm kiến nghị bước đầu phân cấp 3 loại nhựa đường theo PG như ở Bảng 2-9. 56 Bảng 2-9. Kết quả bước đầu phân cấp nhựa đường theo đặc tính PG TT Cấp nhựa đường theo kim lún Cấp nhựa đường theo PG Ghi chú 1 20/30 PG 82-28 Chưa thực hiện thí nghiệm uốn dầm (BBR) và kéo trực tiếp (DTT) 2 35/50 PG 70-34 3 60/70 PG 64-34 2.5.4. Thiết kế cấp phối cốt liệu cho hỗn hợp đá – nhựa cường độ cao theo phương pháp Bailey Sử dụng phương pháp Bailey để thiết kế cấp phối cốt liệu cho các hỗn hợp ĐNMC 31,5 và ĐNMC 25. 2.5.4.1. Kết quả thiết kế các cấp phối cốt liệu đá – nhựa cường độ cao theo phương pháp Bailey Phối trộn cốt liệu cho hỗn hợp ĐNMC 25 từ 03 loại cốt liệu thô (10/25; 10/20 và 5/10), 01 loại cốt liệu mịn (0/5) và bột khoáng theo phương pháp Bailey cần xác định các thông số sau: Cấp phối của các đống cốt liệu thành phần và tỷ trọng khối của chúng; Khối lượng thể tích ở trạng thái xốp và ở trạng thái chặt theo AASHTO T-19. Ngoài ra, cần phải lựa chọn các thông số của các cốt liệu thành phần gồm: Khối lượng thể tích thiết kế của cốt liệu (lấy theo % của khối lượng thể tích ở trạng thái xốp); Lượng lọt sàng 0,075 mm; Tỷ lệ phối trộn của các cốt liệu thô; Tỷ lệ phối trộn của các cốt liệu mịn. Lựa chọn 3 tỷ lệ phối trộn của các nhóm cốt liệu thô. Các kết quả phối trộn cốt liệu theo phương pháp Bailey được thể hiện ở Bảng 2-10 và Hình 2-11. Tương tự, phối trộn cốt liệu cho hỗn hợp ĐNMC 31,5 từ 03 loại cốt liệu thô (10/31,5; 10/20 và 5/10), 01 loại cốt liệu mịn (0/5) và bột khoáng được kết quả ở Bảng 2-11 và Hình 2-12. 57 Bảng 2-10. Phối trộn cốt liệu cho hỗn hợp ĐNMC 25 TT Loại cấp phối cốt liệu Tỷ lệ phối trộn cốt liệu thô (%) Kết quả thiết kế phối trộn (%) CA#1 CA#2 CA#3 CA#1 CA#2 CA#3 FA#1 MF 1 CP1 40 35 25 25,52 22,15 18,29 31,78 2,26 2 CP2 65 20 15 41,13 12,65 11,10 32,86 2,27 3 CP4 75 15 10 47,43 9,48 7,39 33,44 2,26 Hình 2-11. Cấp phối cốt liệu thiết kế của hỗn hợp ĐNMC 25 Bảng 2-11. Phối trộn cốt liệu cho hỗn hợp ĐNMC 31,5 TT Loại cấp phối cốt liệu Tỷ lệ phối trộn cốt liệu thô (%) Kết quả thiết kế phối trộn (%) CA#1 CA#2 CA#3 CA#1 CA#2 CA#3 FA#1 MF 1 CP 3 65 20 15 42,51 12,78 11,21 31,06 2,43 Hình 2-12. Cấp phối cốt liệu thiết kế của hỗn hợp ĐNMC 31,5 31,525,019,012,59,54,752,361,180,60,30,150,075 0 10 20 30 40 50 60 70 80 90 100 CP1 CP2 CP4 Cận trên Cận dưới Fuller n=0,45 Cỡ sàng (mm) Ph ần trĕ m l ọt s àng (% ) CP2 Fuller n=0,45 CP4 CP1 37,531,5251912,59,54,752,361,180,60,30,150,075 0 10 20 30 40 50 60 70 80 90 100 CP3 ĐNMC 31,5_Cận dưới ĐNMC 31,5_Cận trên Fuller n=0,45 Cỡ sàng (mm) Ph ần trĕ m l ọt s àng (% ) CP3 Fuller n=0,45 58 2.5.4.2. Đánh giá các cấp phối cốt liệu thiết kế bằng phương pháp Bailey Tính toán hệ số của các cấp phối cốt liệu sau khi phối trộn được kết quả thể hiện ở Bảng 2-12. Bảng 2-12. Các hệ số cốt liệu của các cấp phối cốt liệu ĐNMC và ĐNC STT Loại cấp phối cốt liệu Các hệ số đánh giá cấp phối cốt liệu CA FAC FAf 1 CP1 0,95 0,45 0,44 2 CP2 0,44 0,47 0,43 3 CP4 0,29 0,48 0,43 4 CP3 0,41 0,47 0,44 Có thể thấy rằng cấp phối đề xuất CP1, CP2 và CP4 thỏa mãn đường bao cấp phối đề xuất cho hỗn hợp ĐNMC và ĐNC 25, còn cấp phối CP3 cũng thỏa mãn đường bao cấp phối đề xuất cho hỗn hợp ĐNMC và ĐNC 31,5. Khi sử dụng các hệ số của phương pháp Bailey để đánh giá các cấp phối này có nhận xét như sau: CP4 có hệ số CA = 0,29 cho thấy hỗn hợp có tỷ lệ các cỡ hạt trung gian ít có thể tạo ra bộ khung cốt liệu thô tốt nhưng khó thi công do hỗn hợp này dễ phân tầng khi rải; Đối với cấp phối CP1 có CA = 0,95; Cấp phối CP2 có hệ số CA = 0,44 và CP3 có CA = 0,41 đều nằm trong khoảng kiến nghị từ 0,4 – 0,95. Các cấp phối này được kỳ vọng là sẽ tạo ra bộ khung cốt liệu thô vừa hạn chế sự phân tầng và dễ đầm chặt khi thi công. Từ các phân tích ở trên, chọn 3 cấp phối cốt liệu CP1, CP2 và CP3 để tiến hành các nghiên cứu về các chỉ tiêu cơ lý của các hỗn hợp ĐNMC. Các cấp phối này sử dụng cho cả hỗn hợp ĐNMC và hỗn hợp đối chứng ĐNC. 2.5.5. Xác định hàm lượng nhựa tối ưu của các hỗn hợp đá – nhựa cường độ cao theo phương pháp Marshall cải tiến 2.5.5.1. Trình tự xác định hàm lượng nhựa tối ưu theo phương pháp Marshall cải tiến [6] - Thí nghiệm xác định các chỉ tiêu cơ lý của cốt liệu và nhựa đường. - Phối trộn các cốt liệu khoáng theo cấp phối thiết kế. - Chuẩn bị cốt liệu để đúc mẫu: Số lượng mẫu cốt liệu cần thiết là 5 tổ mẫu (mỗi tổ 3 mẫu) và khối lượng 1 mẫu khoảng 4000 g. - Trộn cốt liệu với nhựa đường ở nhiệt độ thích hợp (tham khảo Bảng 2-13). 59 Đối với các loại nhựa đường mác 20/30 và 35/50, nhiệt độ chế tạo hỗn hợp tham khảo theo EN 13108-1:2006 [27], nhựa đường mác 60/70 theo TCVN 8819:2011 [7]. Bảng 2-13. Nhiệt độ của hỗn hợp ĐNMC và ĐNC khi trộn Cấp nhựa đường Nhiệt độ giới hạn (0C) Nhiệt độ trộn hỗn hợp (0C) Tiêu chuẩn tham khảo 20/30 160 – 200 165 -170 EN 13108-1:2006 35/50, 40/60 150 – 190 155- 160 EN 13108-1:2006 60/70 140 - 180 150 - 155 TCVN 8819:2011 - Đầm mẫu mẫu Marshall cải tiến với loại búa đầm 10,2 kg và chiều cao rơi là 457 mm. Chiều cao mẫu sau khi đầm trong khuôn phải nằm trong khoảng quy định 95,2 1,8 mm. - Thí nghiệm và tính toán các chỉ tiêu thể tích của mẫu Marshall cải tiến. - Thí nghiệm xác định độ ổn định và độ dẻo trên các mẫu Marshall cải tiến (xem Hình 2-13a, b) theo các hướng dẫn trong TCVN 8860-1:2011. Kết quả thí nghiệm độ ổn định Marshall cần được hiệu chỉnh bằng cách nhân với hệ số hiệu chỉnh theo Bảng 2 của tiêu chuẩn này. a) Mẫu Marshall cải tiến b) Thiết bị nén Marshall cải tiến Hình 2-13. Thí nghiệm Marshall cải tiến 152 mm 60 - Lựa chọn hàm lượng nhựa tối ưu: Trước tiên vẽ các đồ thị quan hệ giữa hàm lượng nhựa và các chỉ tiêu liên quan như độ ổn định, độ dẻo, độ rỗng dư, độ rỗng cốt liệu, độ rỗng lấp đầy nhựa, khối lượng thể tích của mẫu đá – nhựa chặt. Sau đó, cĕn cứ vào yêu cầu kỹ thuật đối với hỗn hợp, xác định hàm lượng nhựa tối ưu thỏa mãn các tiêu chí từ 3 – 8 ở Bảng 2-1. 2.5.5.2. Kế hoạch thí nghiệm hàm lượng nhựa tối ưu Xác định hàm lượng nhựa đường tối ưu theo phương pháp Marshall với các hỗn hợp ĐNMC 20/30, ĐNMC 35/50 đối chứng với ĐNC 60/70. Số lượng mẫu thí nghiệm tương ứng với từng hỗn hợp ĐNMC và ĐNC được thể hiện ở Bảng 2-14. Số mẫu thí nghiệm cho mỗi tổ mẫu được lựa chọn được theo tiêu chuẩn TCVN 8820:2011. Để đảm bảo độ tin cậy của các kết quả thí nghiệm, sử dụng tiêu chuẩn ASTM E691 để đánh giá độ chụm của các kết quả thí nghiệm. Nếu thỏa mãn giới hạn về độ chụm theo các tiêu chuẩn tương ứng thì chấp nhận kết quả thí nghiệm và lấy giá trị trung bình làm kết quả đại diện cho tổ mẫu. Trong trường hợp không thỏa mãn độ chụm thì phải làm lại thí nghiệm. Kết quả đánh giá độ chụm của thí nghiệm Marshall được thể hiện ở Phụ lục 3. Bảng 2-14. Số lượng mẫu xác định hàm lượng nhựa tối ưu Hàm lượng nhựa Số lượng mẫu thử Tổng số mẫu ĐNMC 25 và ĐNC 25 CP 1 ĐNMC 25 và ĐNC 25 CP 2 ĐNMC 31,5 và ĐNC 31,5 CP 3 ĐNMC 20/30 ĐNMC 35/50 ĐNC 60/70 ĐNMC 20/30 ĐNMC 35/50 ĐNC 60/70 ĐNMC 20/30 ĐNMC 35/50 ĐNC 60/70 2,7% 3 3 3 3 3 3 3 3 3 27 3,2% 3 3 3 3 3 3 3 3 3 27 3,7% 3 3 3 3 3 3 3 3 3 27 4,2% 3 3 3 3 3 3 3 3 3 27 4,7% 3 3 3 3 3 3 3 3 3 27 Tổng số 15 15 15 15 15 15 15 15 15 135 2.5.5.3. Kết quả xác định hàm lượng nhựa tối ưu Kết quả thí nghiệm xác định hàm lượng nhựa tối ưu cho các hỗn hợp ĐNMC và ĐNC đối chứng được xác định trên cơ sở thỏa mãn các chỉ tiêu cơ lý yêu cầu, thể hiện ở Bảng 2-15. 61 Bảng 2-15. Hàm lượng nhựa tối ưu của các hỗn hợp ĐNMC và ĐNC TT Loại hỗn hợp Cấp phối Loại nhựa đường Hàm lượng nhựa tối ưu (% kl hh) 1 ĐNMC 25 CP1 20/30 3,60 ÷ 4,30 2 ĐNMC 25 CP1 35/50 3,50 ÷ 4,20 3 ĐNC 25 CP1 60/70 3,50 ÷ 4,15 4 ĐNMC 25 CP2 20/30 3,30 ÷ 4,20 5 ĐNMC 25 CP2 35/50 3,30 ÷ 4,15 6 ĐNC 25 CP2 60/70 3,30 ÷ 4,10 7 ĐNMC 31,5 CP3 20/30 3,25 ÷ 4,00 8 ĐNMC 31,5 CP3 35/50 3,20 ÷ 4,00 9 ĐNC 31,5 CP3 60/70 3,20 ÷ 4,00 Giá trị hàm lượng nhựa tối ưu của các hỗn hợp ĐNMC và ĐNC với cùng cấp phối thiết kế (CP1, CP2 hoặc CP3) không có sự chênh lệch. Điều này cho thấy chiều dày màng nhựa được tạo ra tương đương nhau khi sử dụng 3 loại nhựa đường 20/30, 35/50 và 60/70 khi chúng được trộn và tạo mẫu ở các nhiệt độ quy định ở Bảng 2-13. Giá trị hàm lượng nhựa tối ưu của các hỗn hợp ĐNMC và ĐNC với 3 cấp phối thiết kế (CP1, CP2 và CP3) nằm trong khoảng 3,2% – 4,3%, thấp hơn so với hàm lượng nhựa tối ưu của hầu hết các hỗn hợp BTNC 12,5 và BTNC 19 (khoảng từ 4,5 - 5,2%) đang sử dụng phổ biến ở Việt Nam hiện nay. Sở dĩ hàm lượng nhựa tối ưu nhỏ hơn là do các hỗn hợp ĐNMC và ĐNC sử dụng cấp phối cốt liệu thô có cỡ hạt danh định lớn nên tỷ diện bề mặt cốt liệu nhỏ hơn so với các hỗn hợp BTNC 12,5 và BTNC 19 thông thường. 2.6. THỰC NGHIỆM XÁC ĐỊNH CÁC CHỈ TIÊU KỸ THUẬT CỦA HỖN HỢP ĐÁ – NHỰA CƯỜNG ĐỘ CAO 2.6.1. Các chỉ tiêu kỹ thuật của hỗn hợp đá – nhựa cường độ cao 2.6.1.1. Các chỉ tiêu thể tích a) Độ rỗng cốt liệu Độ rỗng cốt liệu của đá – nhựa được xác định theo TCVN 8860-10 : 2011. Công thức xác định độ rỗng cốt liệu như sau: s sb mb PG GVMA 100 (2-14) 62 Trong đó: Gsb - tỷ trọng khối của hỗn hợp cốt liệu; Gmb - tỷ trọng khối của mẫu đá – nhựa đã đầm nén; Ps - tỷ lệ cốt liệu, tính theo % khối lượng hỗn hợp. b) Độ rỗng dư Độ rỗng dư của ĐNMC và ĐNC được xác định theo TCVN 8860-9 : 2011. Công thức tính toán như sau: )1.(100 mm mb a G GV (2-15) Trong đó: Gmm - tỷ trọng lớn nhất của hỗn hợp ở trạng thái rời; Gmb - tỷ trọng khối của hỗn hợp đã đầm nén. c) Độ rỗng lấp đầy nhựa Độ rỗng lấp đầy nhựa được xác định theo TCVN 8860-11 : 2011. Công thức tính toán như sau: ).(100 VMA VVMAVFA a (2-16) Trong đó: VMA - độ rỗng cốt liệu, tính bằng phần trĕm (%); Va - độ rỗng dư của hỗn hợp đã đầm nén, tính bằng phần trĕm (%). 2.6.1.2. Độ ổn định và độ dẻo Marshall cải tiến Sau khi xác định khoảng hàm lượng nhựa tối ưu tương ứng với các cấp phối cốt liệu thiết kế với các loại nhựa đường khác nhau, chọn giá trị hàm lượng nhựa tối ưu tương ứng với từng cấp phối và loại nhựa đường để chế tạo các tổ mẫu Marshall cải tiến. Tiến hành thí nghiệm nén Marshall xác định độ ổn định và độ dẻo của các tổ mẫu này trong điều kiện thí nghiệm ngâm mẫu ở 600C trong 60 phút theo TCVN 8860-1:2011. 63 2.6.1.3. Độ ổn định còn lại Độ ổn định còn lại của đá – nhựa (R) xác định theo tiêu chuẩn TCVN 8860- 12:2011, được tính theo công thức (2-17). .100aSR S (2-17) Trong đó:
File đính kèm:
luan_an_nghien_cuu_hon_hop_da_nhua_nong_cuong_do_cao_dung_tr.pdf
TT_VN_TDH.compressed.pdf
TT_EN_TDH.compressed.pdf
Thongtin_TDH.docx
PL_TDH.compressed.pdf