Luận án Nghiên cứu một số yếu tố ảnh hưởng của công nghệ tạo vật liệu compozit từ vỏ cây và polyethylene
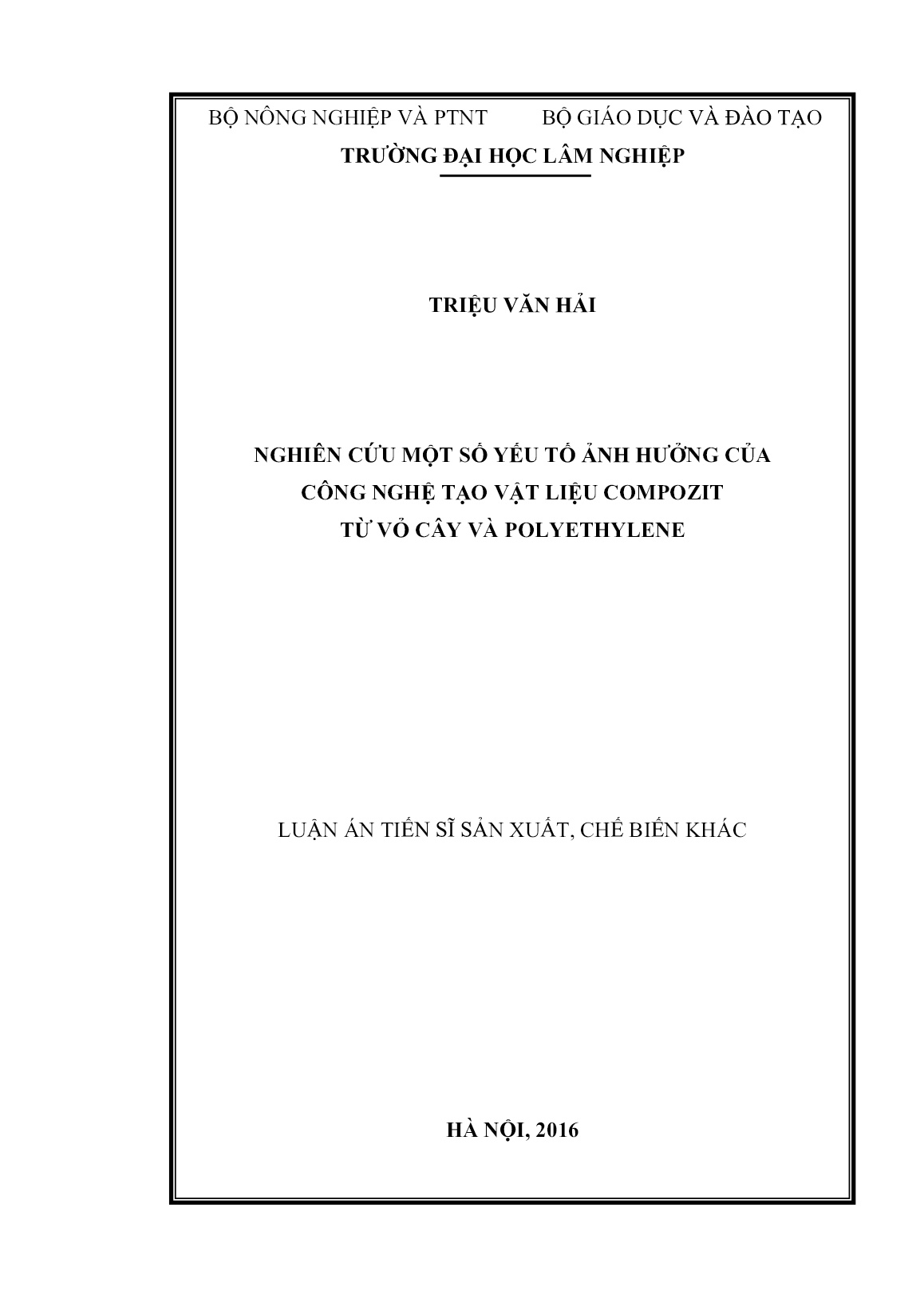
Trang 1
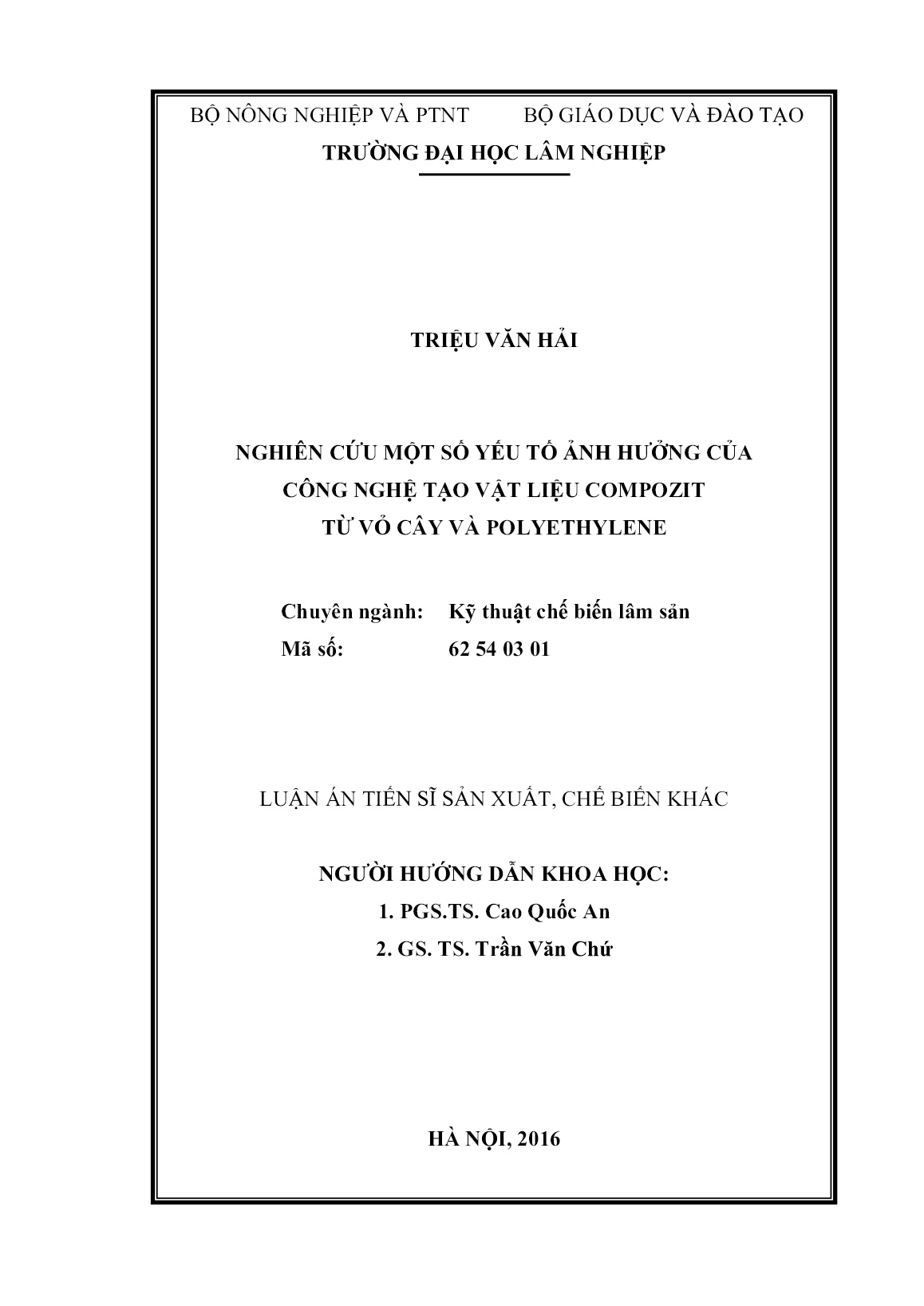
Trang 2
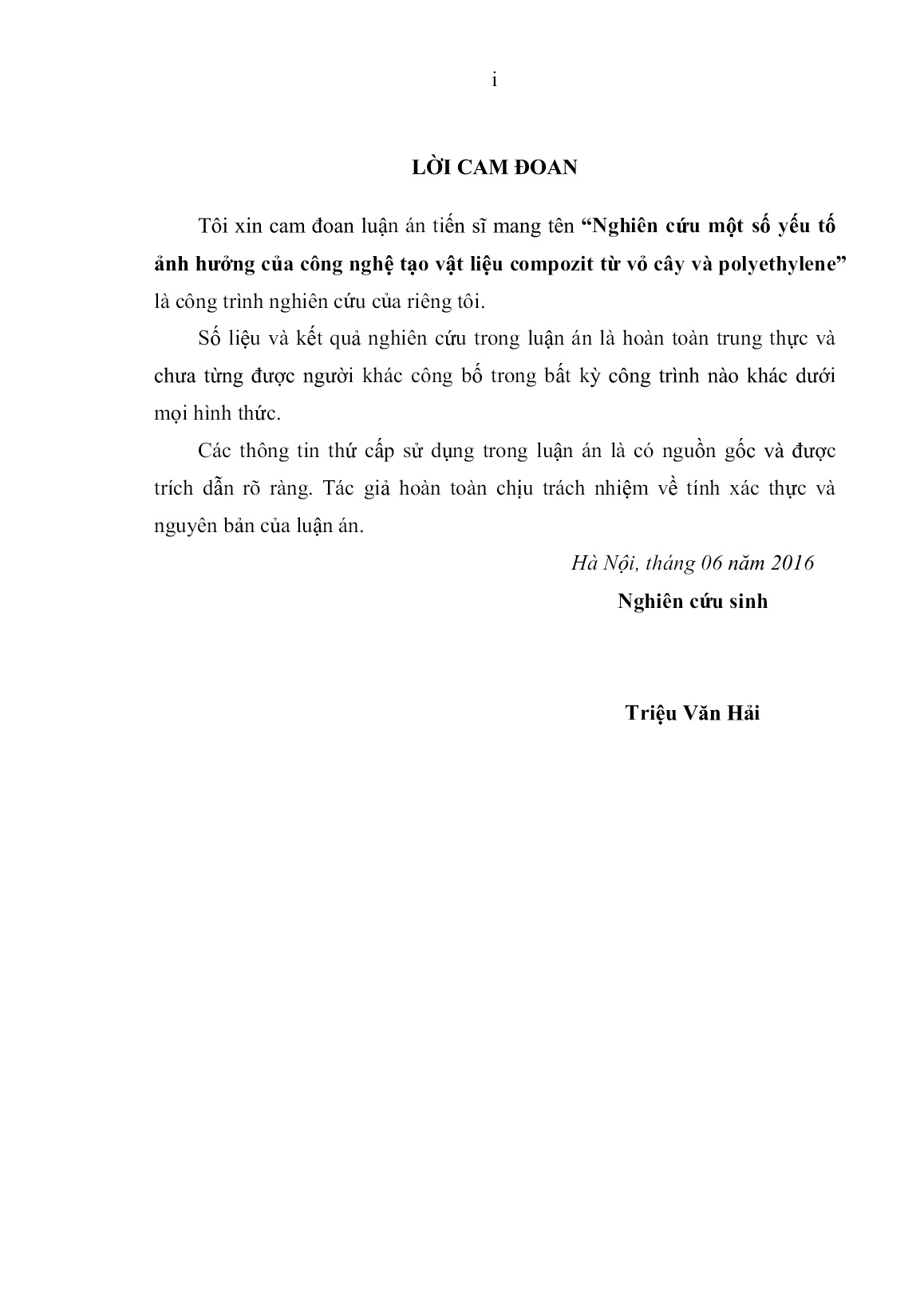
Trang 3
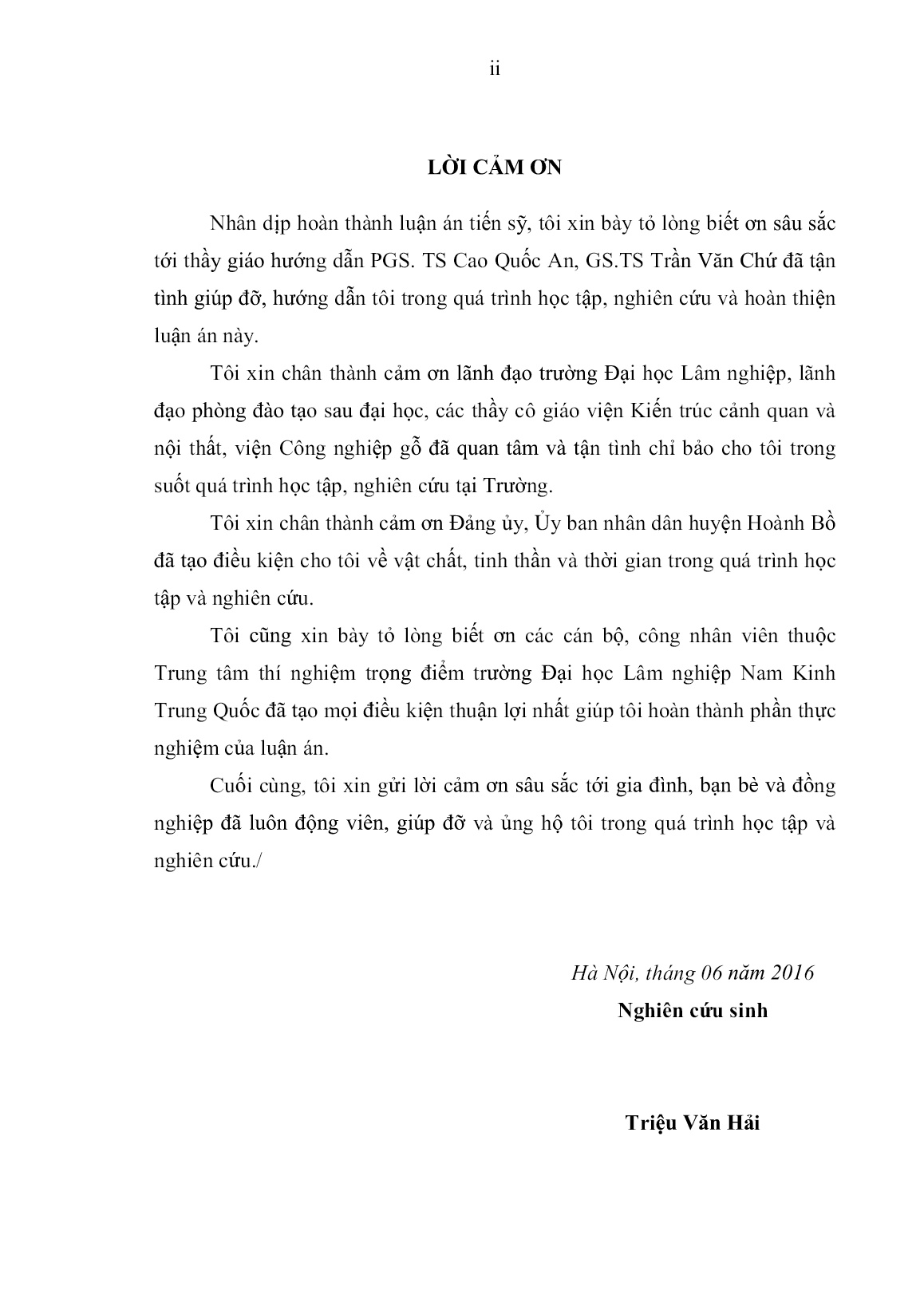
Trang 4
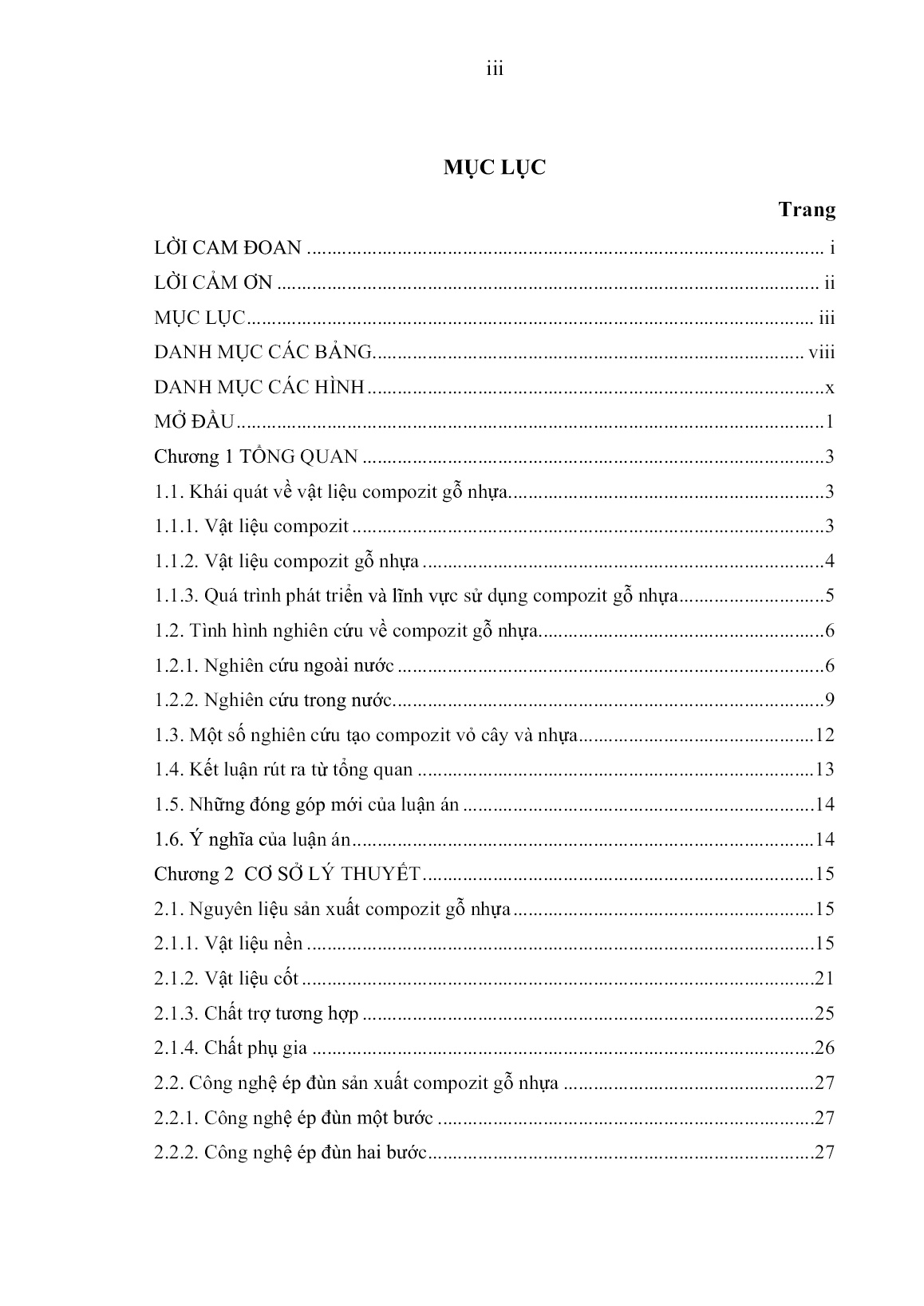
Trang 5
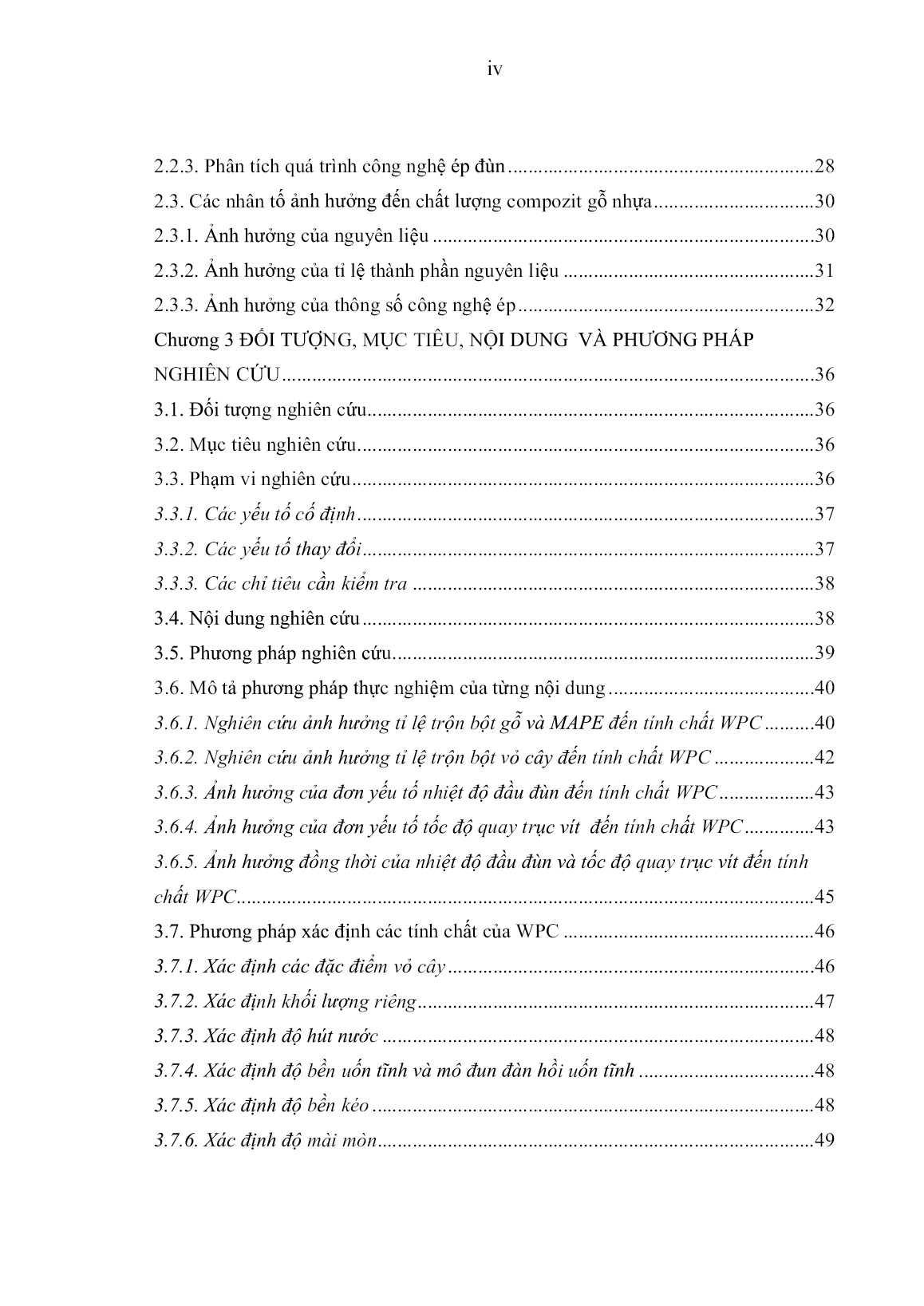
Trang 6
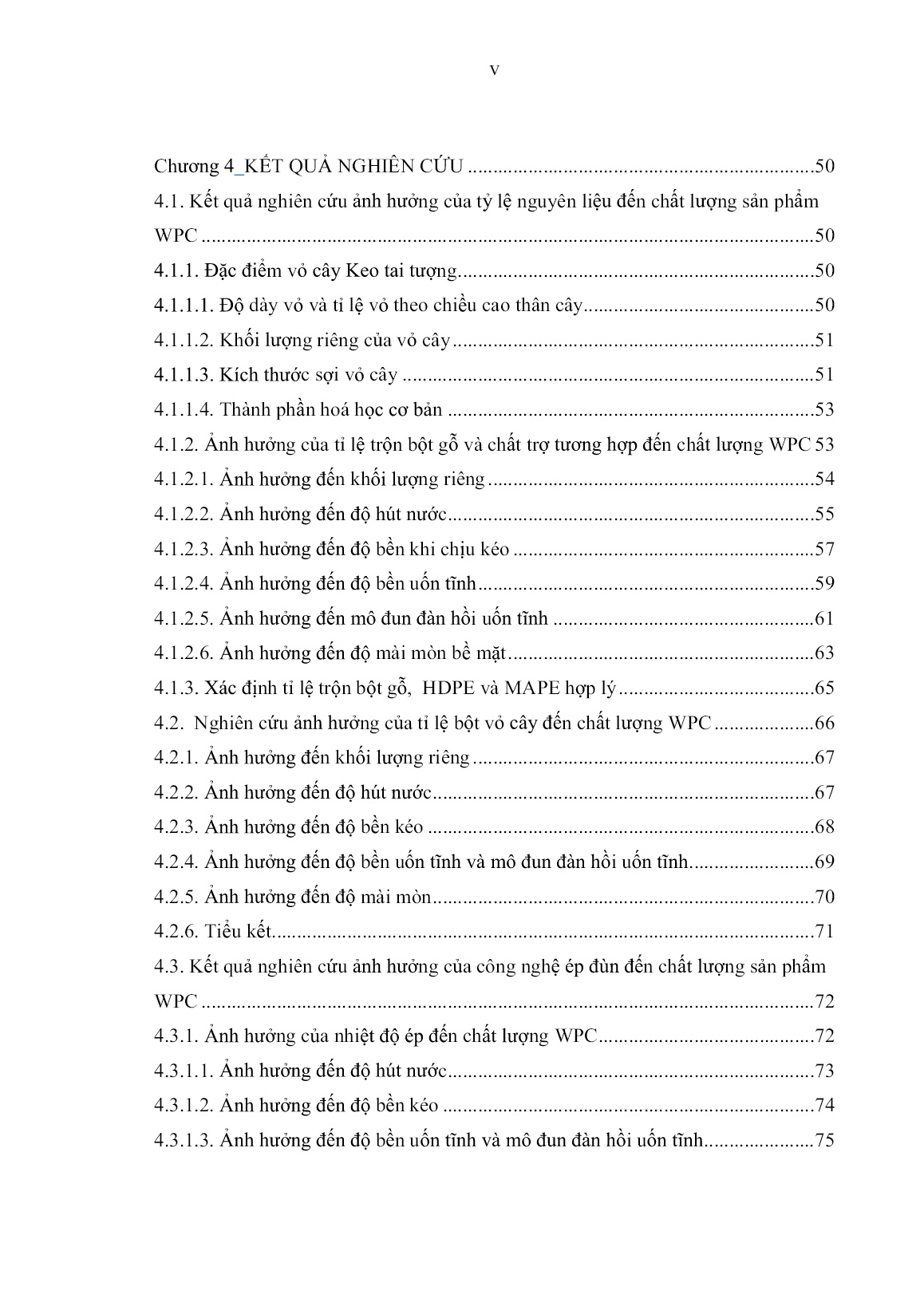
Trang 7
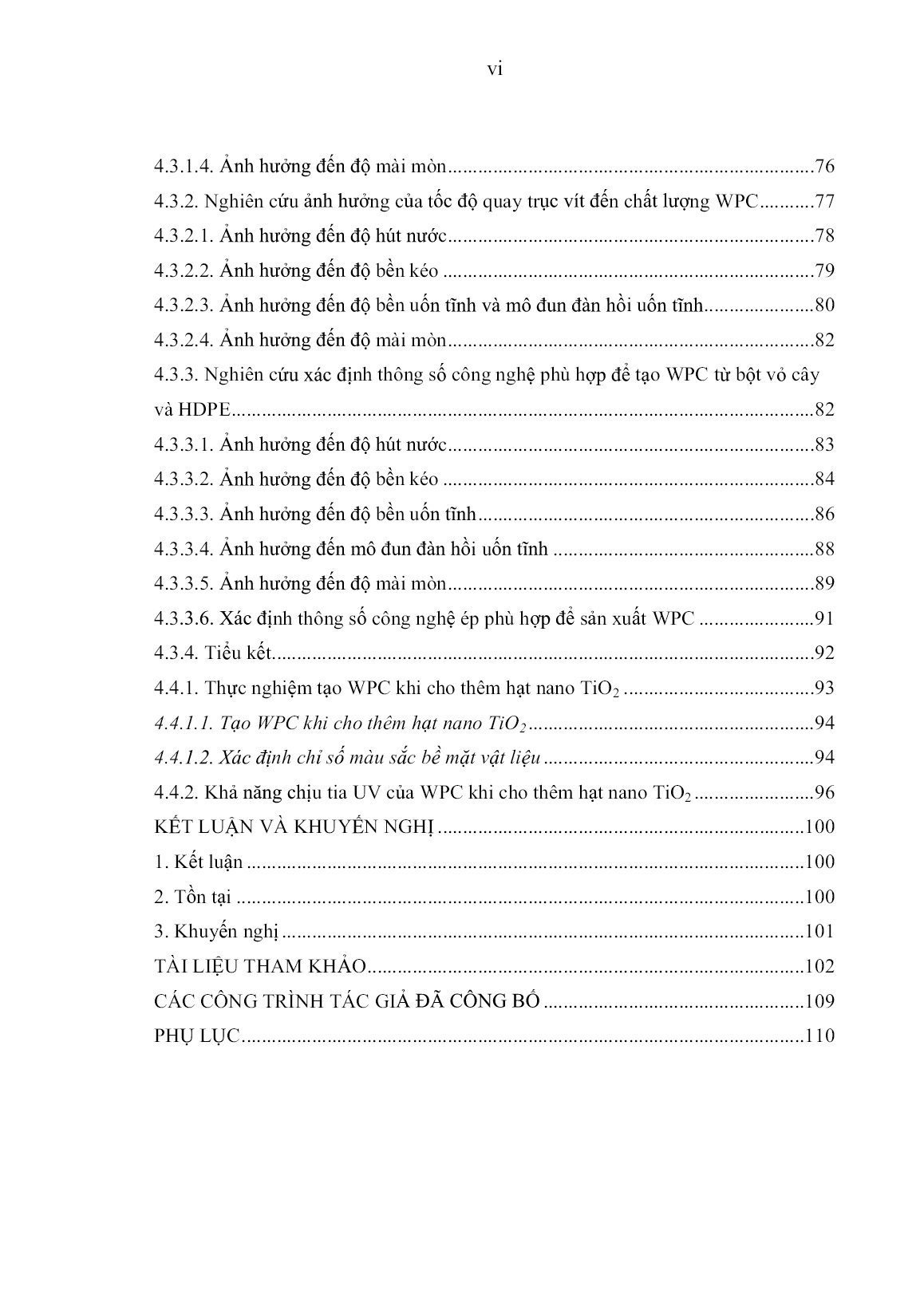
Trang 8
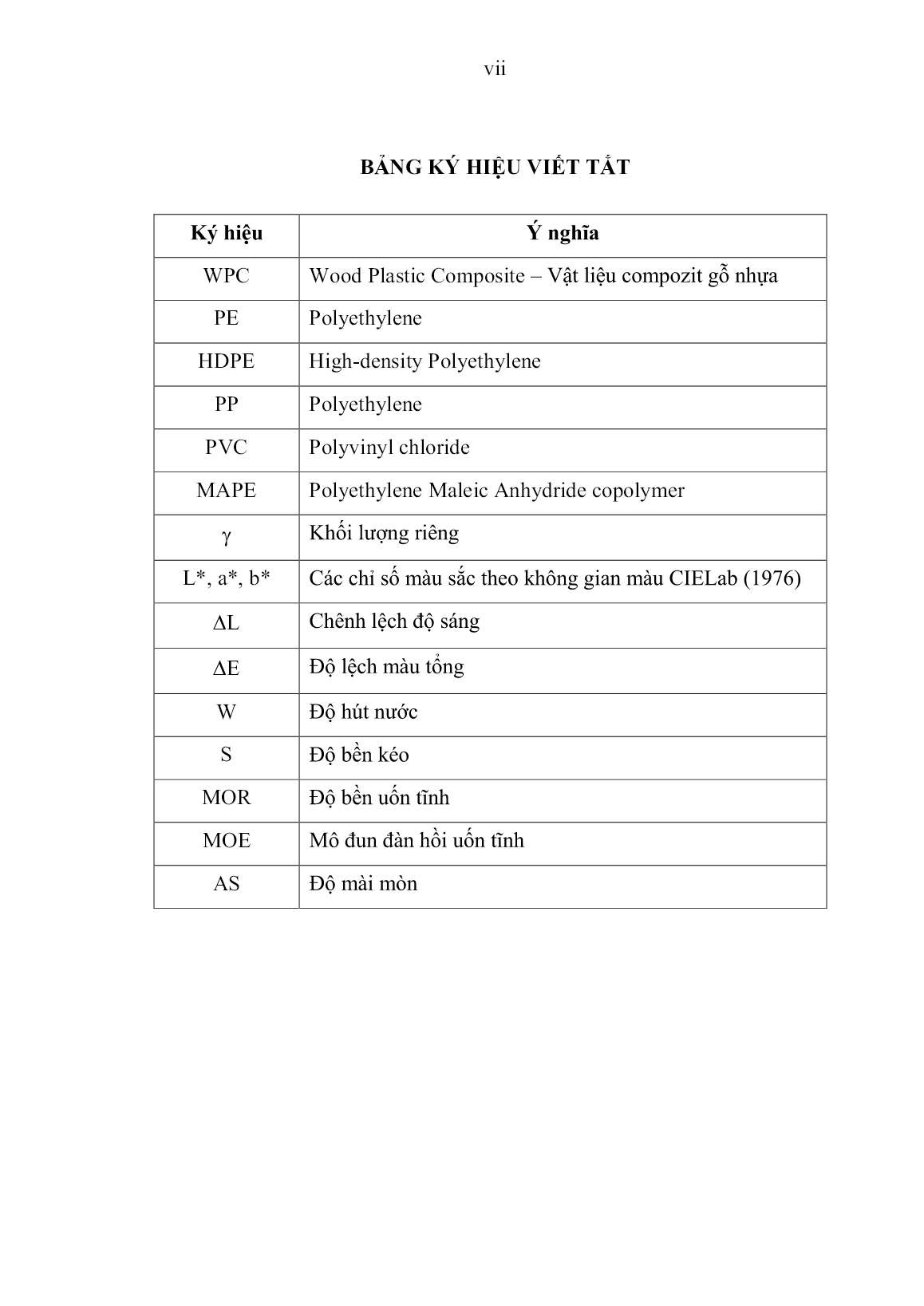
Trang 9
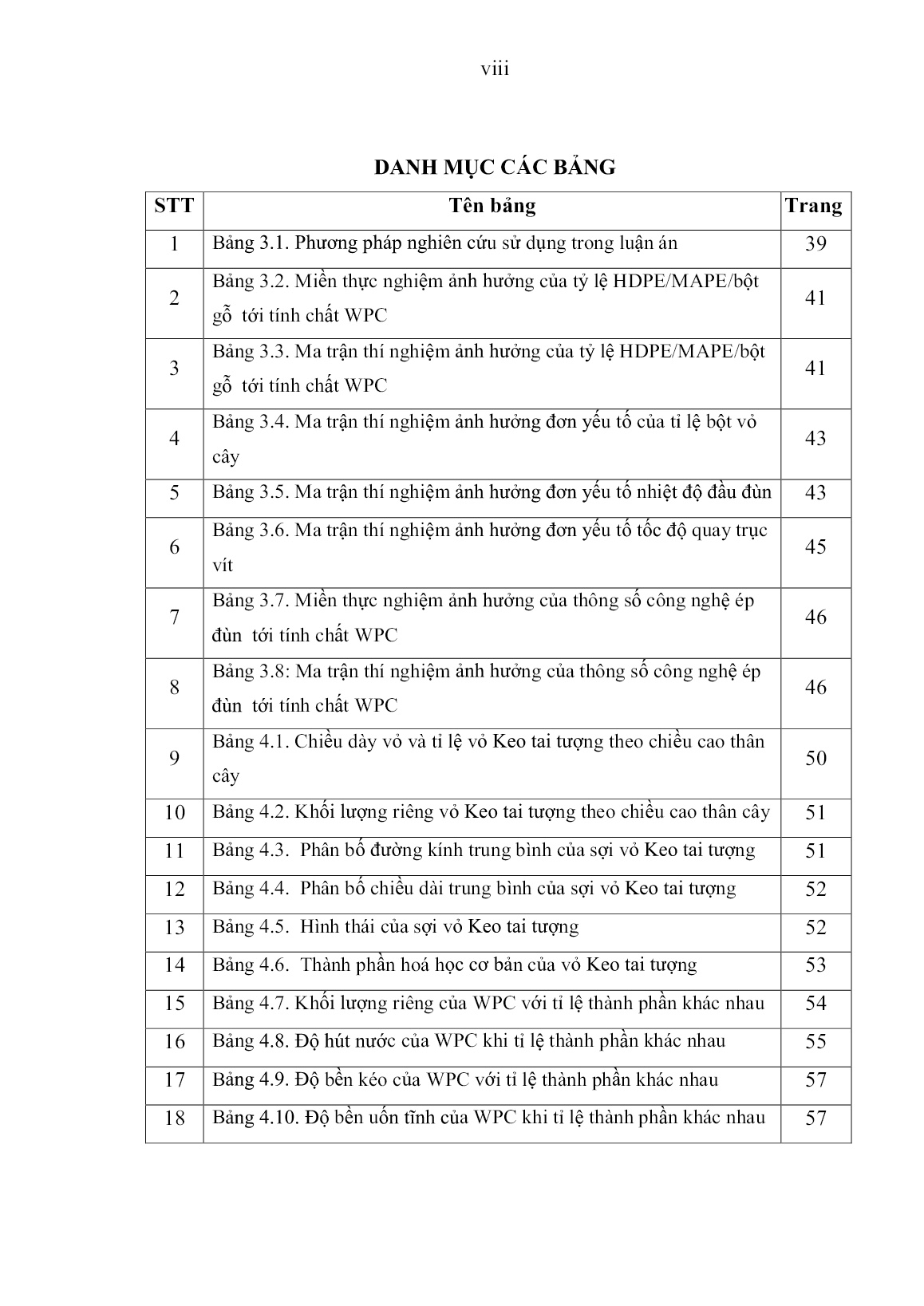
Trang 10
Tải về để xem bản đầy đủ
Bạn đang xem 10 trang mẫu của tài liệu "Luận án Nghiên cứu một số yếu tố ảnh hưởng của công nghệ tạo vật liệu compozit từ vỏ cây và polyethylene", để tải tài liệu gốc về máy hãy click vào nút Download ở trên.
Tóm tắt nội dung tài liệu: Luận án Nghiên cứu một số yếu tố ảnh hưởng của công nghệ tạo vật liệu compozit từ vỏ cây và polyethylene
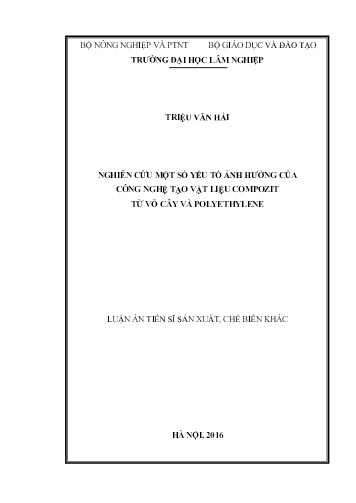
trục ví khi ép đến các chỉ tiêu chất lƣợng của sản phẩm gồm: khối lƣợng riêng, độ hút nƣớc, độ bền kéo, độ bền uốn, mô đun đàn hồi khi uốn, mài mòn. Các thông số thí nghiệm đƣợc bố trí nhƣ sau: - Thay đổi tốc độ quay trục vít (vòng/phút): 10, 15, 20, 25, 30 - Cố định tỉ lệ hỗn hợp trong sản phẩm: (Bột gỗ + bột vỏ cây) : HDPE : MAPE = 50 : 47 : 3. Trong đó tỉ lệ giữa bột gỗ và bột vỏ cây sẽ căn cứ kết quả nghiên cứu ảnh hƣởng của tỉ lệ thay thế bột gỗ bằng bột vỏ cây đến chất lƣợng WPC để chọn (Kết quả của Chƣơng 4). - Cố định nhiệt độ các vùng trên máy ép. - Nhiệt độ đầu đùn: 140 oC Thông số đầu ra là (Y): độ hút nƣớc (Y1), độ bền kéo (Y2), độ bền uốn tĩnh (Y3), mô đun đàn hồi uốn tĩnh (Y4), độ mài mòn (Y5). Bảng 3.6. Ma trận thí nghiệm ảnh hƣởng đơn yếu tố tốc độ quay trục vít Thí nghiệm Thông số đầu vào (tốc độ quay trục vít, vòng/phút) Thông số đầu ra Y1 Y2 Y3 Y4 Y5 Y6 No 1 10 45 No 2 15 No 3 20 No 4 25 No 5 30 3.6.5. Ảnh hưởng đồng thời của nhiệt độ đầu đùn và tốc độ quay trục vít đến tính chất WPC Bố trí thí nghiệm: Sử dụng phƣơng pháp thực nghiệm đa yếu tố toàn phần và các thí nghiệm đƣợc tiến hành bố trí ngẫu nhiên hoàn toàn. Phƣơng trình hồi quy tuyến tính dạng đa thức bậc hai: Y = bo + b1x1 + b2x2 + b12x1x2 + b11x1 2 + b22x2 2 (3.4) Thông số đầu ra là (Y): độ hút nƣớc (Y1), độ bền kéo (Y2), độ bền uốn tĩnh (Y3), mô đun đàn hồi uốn tĩnh (Y4), độ mài mòn (Y5). Yếu tố tác động gồm: nhiệt độ ép và tốc độ quay của trục vít. - Cố định tỉ lệ hỗn hợp trong sản phẩm: (bột gỗ + bột vỏ cây) : HDPE : MAPE theo tỉ lệ xác định đƣợc từ kết quả nghiên cứu ảnh hƣởng của tỉ lệ trộn hỗn hợp (Chƣơng 4) đến chất lƣợng WPC; - Cố định nhiệt độ các vùng trên máy ép. Miền quy hoạch thực nghiệm: trên cơ sở của các nghiên cứu đơn yếu tố của luận án, miền thực nghiệm cho nghiên cứu đa yếu tố nhƣ sau: Bảng 3.7. Miền thực nghiệm ảnh hƣởng của thông số công nghệ ép đùn tới tính chất WPC Yếu tố tác động Mức biến đổi Khoảng biến thiên - -1 0 +1 + V: Tốc độ quay trục vít (vòng/min) X1 18 20 25 30 32 5 T: Nhiệt độ ép (oC) X2 126 130 140 150 154 10 46 Lập ma trận thí nghiệm: dùng phƣơng án bất biến quay bậc hai của BOX và HUNTER Số thí nghiệm: N = 2n + 2n + 1 = 22 + 2x2 + 1 = 9 (3.5) (với n = 2 là số yếu tố ảnh hƣởng) Trị số cánh tay đòn: = 2n/4 = 22/4 = 1,41 (3.6) Bảng 3.8: Ma trận thí nghiệm ảnh hƣởng của thông số công nghệ ép đùn tới tính chất WPC STT X1 X2 Y1 Y2 Y3 Y4 Y5 Y6 1 - - 2 + - 3 - + 4 + + 5 -1,41 0 6 +1,41 0 7 0 -1,41 8 0 +1,41 9 0 0 3.7. Phƣơng pháp xác định các tính chất của WPC 3.7.1. Xác định các đặc điểm vỏ cây - Phƣơng pháp lấy mẫu: áp dụng tiêu chuẩn quốc tế ISO 4471-1982 để chọn cây lấy mẫu; - Xác định chiều dày vỏ (w, cm): đo kích thƣớc chiều dày vỏ ở các độ cao khác nhau của cây; - Xác định tỉ lệ vỏ: Tỉ lệ vỏ cây đƣợc xác định theo công thức sau: (3.7) 47 Trong đó: b- tỉ lệ vỏ (%); w- chiều dày vỏ tại vị trí đo (cm); D- đƣờng kính cây tại vị trí đo chiều dày vỏ (cm). - Xác định hình thái sợi vỏ: + Sử dụng các mẫu vỏ nhỏ dạng que diêm (1,5 x 1,5 x 30mm) đặt vào trong ống nghiệm; + Cho một lƣợng nƣớc vừa đủ vào ống nghiệm, gia nhiệt sao cho các mẫu thí nghiệm chìm xuống; + Đổ nƣớc ở trong ống nghiệm ra, cho một lƣợng vừa đủ dung dịch HNO3 (tỉ lệ HNO3 và nƣớc cất là 1:2), tiếp tục cho thêm 3-5 g KCl; + Gia nhiệt cho ống nghiệm chứa dung dịch và mẫu vỏ đến khi thấy có bọt khí, mẫu gỗ chuyển thành màu trắng (khoảng 10 phút); + Dùng đũa thủy tinh khuấy để tách các sợi rời ra, rửa sạch sợi; + Nhuộm màu cho sợi vỏ đã phân ly bằng Safranin; + Tạo tiêu bản tạm thời để quan sát và chụp ảnh bằng kính hiển vi kết nối với máy tính; + Đo kích thƣớc sợi trên ảnh chụp, số lƣợng sợi cần đo khoảng 50 sợi. 3.7.2. Xác định khối lượng riêng Xác định khối lƣợng riêng của vật liệu composite gỗ nhựa sử dụng tiêu chuẩn GB/T 1463 - 2005. Mẫu thử có kích thƣớc (50x10x4)mm, mỗi seri thí nghiệm 5 mẫu, dùng cân điện tử để cân trọng lƣợng các mẫu thử độ chính xác là 0,001g. Đo kích thƣớc bình quân trên 3 mặt chính xác đến 0,01mm từ đó xác định thể tích của mẫu thử (V). Công thức xác định khối lƣợng riêng: V m (3.8) 48 Trong đó: - khối lƣợng riêng (g/cm3) m - khối lƣợng mẫu thử (g) V - thể tích mẫu thử (cm3) 3.7.3. Xác định độ hút nước Xác định độ hút nƣớc của vật liệu composite gỗ nhựa sử dụng tiêu chuẩn GB/T 1034-1998. Mẫu thử có kích thƣớc (50x10x4) mm, mỗi seri thí nghiệm sử dụng 5 mẫu thử. Mẫu thử đƣợc sấy ở nhiệt độ 105oC trong thời gian 1giờ, sau đó dùng cân điện tử để cân trọng lƣợng các mẫu thử, độ chính xác là 0,001g. Sau đó cho toàn bộ mẫu thử vào nƣớc tinh khiết trong thời gian 24h, dùng giấy thấm hết nƣớc trên bề mặt mẫu. Tiếp theo dùng cân điện tử để cân trọng lƣợng các mẫu thử, độ chính xác đến 0,001g. Công thức xác định độ hút nƣớc: 100 1 12 m mm W (3.9) Trong đó: W – độ hút nƣớc sau 24 giờ (%) m1 – khối lƣợng mẫu trƣớc khi hút nƣớc (g) m2 - khối lƣợng sau khi hút nƣớc (g) 3.7.4. Xác định độ bền uốn tĩnh và mô đun đàn hồi uốn tĩnh Độ bền uốn tĩnh và mô đôn đàn hồi uốn tĩnh đƣợc xác định theo tiêu chuẩn GB/T 9341-2008; Kích thƣớc: chiều dài l = 120 mm, chiều rộng b = 10 mm, chiều dày d = 4 mm, khoảng cách hai gối đỡ = 100 mm; Số lƣợng: 5 mẫu. 3.7.5. Xác định độ bền kéo Xác định độ bền kéo của vật liệu composite gỗ nhựa sử dụng tiêu chuẩn GB/T 1040-2006; Mẫu có dạng hình mái chèo,; 49 Kích thƣớc mẫu thử: chiều dài lớn nhất l = 150 mm, chiều rộng b = 10 mm, chiều dày d = 4 mm, khoảng cách làm việc của mẫu = 100 mm; Số lƣợng: 5 mẫu. 3.7.6. Xác định độ mài mòn Xác định độ bền kéo của vật liệu composite gỗ nhựa sử dụng tiêu chuẩn GB/T 18103-2000; Kích thƣớc mẫu thử: 100 x 100 x t (mm); Số lƣợng: 5 mẫu. 50 Chƣơng 4 KẾT QUẢ NGHIÊN CỨU 4.1. Kết quả nghiên cứu ảnh hƣởng của tỷ lệ nguyên liệu đến chất lƣợng sản phẩm WPC 4.1.1. Đặc điểm vỏ cây Keo tai tƣợng Việc sử dụng vỏ cây làm nguyên liệu gia cƣờng vừa có ý nghĩa trong việc lợi dụng triệt để tài nguyên gỗ đồng thời cũng góp phần giảm thiểu phát thải ra môi trƣờng. Đối với mỗi loài cây khác nhau, lƣợng vỏ cây hay tỉ lệ vỏ cây không giống nhau, ngoài ra, một số đặc điểm khác nhƣ chiều dài và đƣờng kính sợi vỏ cây cũng khác nhau. Do đó luận án đã tiến hành xác định một số đặc điểm cơ bản của vỏ cây làm cơ sở cho việc sử dụng để làm nguyên liệu gia cƣờng trong sản xuất vật liệu WPC từ bột vỏ cây và nhựa HDPE. Các đặc của vỏ cây đƣợc xác định gồm: chiều dày vỏ, tỉ lệ vỏ, khối lƣợng riêng vỏ, kích thƣớc sợi vỏ. Kết quả nghiên cứu đƣợc lần lƣợt thể hiện nhƣ sau: 4.1.1.1. Độ dày vỏ và tỉ lệ vỏ theo chiều cao thân cây Độ dày vỏ và tỉ lệ vỏ gỗ Keo tai tƣợng theo chiều cao thân cây đƣợc thể hiện trong bảng sau: Bảng 4.1. Chiều dày vỏ và tỉ lệ vỏ Keo tai tƣợng theo chiều cao thân cây Vị trí theo chiều cao (m) Độ dày vỏ (cm) Tỉ lệ vỏ (%) 0 1,85 7,6 1,3 1,5 7,1 3,6 1,2 6,0 5,6 0,95 5,3 7,6 0,9 5,6 9,6 0,75 5,5 51 >10 0,6 5,1 Trung bình 1,10 6,03 Từ bảng ta thấy theo chiều cao thân cây độ dày vỏ và tỉ lệ vỏ có xu hƣớng giảm dần. Độ dày vỏ trung bình khoảng 1,1 cm, tỉ lệ vỏ trung bình khoảng 6,0% so với thể tích thân cây. 4.1.1.2. Khối lượng riêng của vỏ cây Khối lƣợng riêng của vỏ cây Keo tai tƣợng theo vị trí thân cây đƣợc thể hiện trong bảng sau: Bảng 4.2. Khối lƣợng riêng vỏ Keo tai tƣợng theo chiều cao thân cây Vị trí Khối lƣợng riêng (g/cm3) Sd Gốc 0,453 0,030 Thân 0,285 0,026 Ngọn 0,189 0,042 Trung bình 0,309 Ghi chú: khối lƣợng riêng vỏ cây ở độ ẩm 12% (độ ẩm tƣơng đối không khí 65%, nhiệt độ không khí 20oC). Từ bảng ta thấy ở các vị trí khác nhau khối lƣợng riêng của vỏ cây có sự khác biệt rõ rệt, hơn nữa thay đổi theo quy luật. Vỏ cây ở độ cao lớn có khối lƣợng riêng nhỏ hơn so với ở phía gốc. 4.1.1.3. Kích thước sợi vỏ cây Kích thƣớc sợi vỏ Keo tai tƣợng đƣợc thể hiện trong bảng 4.3 và bảng 4.4: Bảng 4.3. Phân bố đƣờng kính trung bình của sợi vỏ Keo tai tƣợng TT Vùng kích thƣớc (µm) Tần số xuất hiện (%) Gốc Thân Ngọn 1 <=15 4,0 6,0 2,0 2 (15, 20] 36,0 50,0 58,0 52 3 (20, 25] 46,0 40,0 38,0 4 (25, 30] 12,0 2,0 2,0 5 >30 2,0 2,0 0,0 Bảng 4.4. Phân bố chiều dài trung bình của sợi vỏ Keo tai tƣợng TT Vùng kích thƣớc (µm) Tần số xuất hiện (%) Gốc Thân Ngọn 1 <=750 8,0 4,0 4,0 2 (750, 900] 16,0 16,0 12,0 3 (900, 1.050] 26,0 26,0 16,0 4 (1.050, 1.200] 24,0 28,0 34,0 5 (1.200, 1.350] 16,0 20,0 24,0 6 >1.350 10,0 6,0 10,0 Trên cơ sở số liệu xác định đƣờng kính và chiều dài sợi, có thể thấy chiều đƣờng kính sợi vỏ Keo tai tƣợng ở 3 vị trí ngọn, thân và gốc cơ bản khác biệt không lớn, biến động từ 19,7 m đến 21,1 m. Chiều dài sợi biến độc trong khoảng 1.056 m đến 1.107 m. Theo chiều cao thân cây từ gốc lên ngọn chiều dài sợi vỏ tăng dần, nhƣng đƣờng kính sợi vỏ có xu hƣớng giảm dần. Chi tiết có thể thấy trong bảng 4.5. Bảng 4.5. Hình thái của sợi vỏ Keo tai tƣợng Vị trí Chiều dài (µm) Sd Đƣờng kính (µm) Sd Độ thon Sd Gốc 1.056 207 21,1 3,6 51 11,4 Thân 1.077 194 20,0 3,5 55 11 Ngọn 1.107 201 19,7 2,6 57 10 Ghi chú: Số liệu trong bảng là chiều dài và đƣờng kính trung bình, tuy nhiên nên căn cứ vào tần số xuất hiện của chiều dài và đƣờng kính sợi để đánh giá về hình thái sợi. 53 4.1.1.4. Thành phần hoá học cơ bản Căn cứ tiêu chuẩn Trung Quốc GB/T 2677.1 đến GB/T 2677.10 tiến hành xác định thành phần hoá học của vỏ cây Keo tai tƣợng, kết quả thể hiện trong bảng sau: Bảng 4.6. Thành phần hoá học cơ bản của vỏ Keo tai tƣợng (giá trị trung bình) Độ pH Xenlulo (%) Hemixenlulo (%) Lignin (%) Chất chiết xuất (%) Nƣớc nguội Nƣớc nóng 1% NaOH 0,45 17,4 25,8 24,7 14,5 19,2 49,8 Từ số liệu thành phần hoá học cho thấy, tỉ lệ thành phần của vỏ cây Keo tai tƣợng có hàm lƣợng xenlulo thấp hơn nhiều so với gỗ nói chung, và hàm lƣợng chất chiết xuất rất lớn, điều này có thể gây ảnh hƣởng nhất định đến công nghệ sản xuất cũng nhƣ chất lƣợng của sản phẩm compozit từ bột vỏ cây và nhựa. 4.1.2. Ảnh hƣởng của tỉ lệ trộn bột gỗ và chất trợ tƣơng hợp đến chất lƣợng WPC Theo các nghiên cứu đã công bố trên thế giới về sản xuất WPC từ vỏ cây cho thấy, không thể sản xuất đƣợc vật liệu WPC đạt chất lƣợng theo yêu cầu từ 100% vỏ cây, mà vỏ cây chỉ đƣợc coi là nguyên liệu thay thế một phần cho bột gỗ. Chính vì vậy, nghiên cứu này đƣợc phân ra làm 2 phần rõ rệt, thứ nhất là nghiên cứu về các yếu tố công nghệ trong sản xuất WPC từ 100% bột gỗ keo tai tƣợng; sau đó mới đi nghiên cứu thay thế từng phần bột vỏ cây keo tai tƣợng để tìm ra lƣợng tối ƣu bột vỏ cây khi sử dụng, để sao cho vật liệu WPC vẫn đảm bảo đƣợc các yêu cầu về chất lƣợng. Trên cơ sở các thông số thí nghiệm đã bố trí nhƣ ở Chƣơng 3, tiến hành tạo vật liệu WPC từ bột gỗ và nhựa polyetylen khối lƣợng riêng lớn (HDPE), và tiến hành đánh giá ảnh hƣởng đồng thời của các nhân tố gồm tỉ lệ trộn bột gỗ và tỉ lệ trộn chất trợ tƣơng hợp MAPE đến một số tính chất cơ bản của 54 WPC nhƣ: khối lƣợng riêng, độ hút nƣớc, độ bền kéo, độ bền uốn tĩnh, mô đun đàn hồi uốn tĩnh và độ mài mòn với mục đích tìm ra tỉ lệ trộn bột gỗ (tỉ lệ vật liệu cốt) và nhựa HDPE (vật liệu nền) phù hợp dùng để nghiên cứu tạo WPC có sử dụng thêm phế thải trong chế biến gỗ - vỏ cây Keo tai tƣợng. Trong thí nghiệm này, các thông số thay đổi là tỉ lệ trộn bột gỗ (X1) và tỉ lệ MAPE (X2), các thành phần khác tạo WPC sẽ thay đổi theo sao cho tổng khối lƣợng các thành phần trong hỗn hợp tạo WPC đạt 100 phần khối lƣợng. 4.1.2.1. Ảnh hưởng đến khối lượng riêng khối lƣợng riêng là một trong những chỉ tiêu quan trọng để đánh giá chất lƣợng vât liệu nói chung, vật liệu WPC nói riêng. Qua nghiên cứu xác định khối lƣợng riêng của WPC với các thông số công nghệ khác nhau cho thấy khối lƣợng riêng của WPC có sự khác biệt không đáng kể (bảng 4.7). Bảng 4.7. Khối lƣợng riêng của WPC với tỉ lệ thành phần khác nhau TT X1 X2 Tỉ lệ bột gỗ (PKL) Tỉ lệ MAPE (PKL) KLTT (g/cm 3 ) 1 -1 -1 30 1 1,030 2 1 -1 50 1 1,092 3 -1 1 30 5 0,988 4 1 1 50 5 1,044 5 1,41 0 54 3 1,080 6 -1,41 0 26 3 0,998 7 0 1,41 40 5,8 1,006 8 0 -1,41 40 0,2 1,070 9 0 0 40 3 1,037 Từ bảng 4.7 cho thấy, khi tỉ lệ bột gỗ tăng lên thì khối lƣợng riêng có xu thế tăng nhẹ. Nguyên nhân dẫn đến hiện tƣợng này có thể do trong quá trình ép tạo vật liệu, dƣới sự tác động của nhiệt độ và áp suất ép đã làm cho bột gỗ nóng chảy và bị ép chặt dẫn đến khối lƣợng riêng của gỗ tăng lên rất nhiều, thậm chí có thể đạt tới khối lƣợng riêng của vách tế bảo (1,53-1,54 g/cm3), hơn nữa, nhƣ ta đã biết khối lƣợng riêng của WPC sẽ là giá trị trung bình cộng của khối lƣợng vật liệu có trong WPC (bột gỗ sau khi ép, HDPE, MAPE, 55 chất phụ gia), vì thế khi khối lƣợng riêng bột gỗ khi ép tăng lên sẽ dẫn đến khối lƣợng riêng WPC tăng nhẹ theo (vì khối lƣợng riêng bộ gỗ sau khi ép có thể lớn hơn khối lƣợng riêng các vật liệu khác trong WPC). Từ kết quả có thể thấy, ảnh hƣởng của tỉ lệ trộn hỗn hợp nguyên liệu trong nghiên cứu đến khối lƣợng riêng là không đáng kể, do đó với chỉ tiêu này luận án không xây dựng phƣơng trình tƣơng quan. 4.1.2.2. Ảnh hưởng đến độ hút nước Độ hút nƣớc của WPC có ảnh hƣởng đến độ bền và độ ổn định của sản phẩm từ WPC trong quá trình sử dụng. Do đó, đây là một chỉ tiêu quan trọng cần đƣợc nghiên cứu, trong sản xuất luôn mong muốn vật liệu có độ hút nƣớc càng nhỏ càng tốt. Trong nghiên cứu này đã xác định độ hút nƣớc sau 4 ngày ngâm trong nƣớc tinh khiết ở nhiệt độ môi trƣờng của WPC khi tỉ lệ thành phần hỗn hợp nguyên liệu thay đổi, kết quả đƣợc trình bày trong bảng 4.8. Bảng 4.8. Độ hút nƣớc của WPC khi tỉ lệ thành phần khác nhau TT X1 X2 Tỉ lệ bột gỗ (PKL) Tỉ lệ MAPE (PKL) Độ hút nƣớc (%) 1 -1 -1 30 1 0,86 2 1 -1 50 1 1,33 3 -1 1 30 5 0,82 4 1 1 50 5 1,29 5 1,41 0 54 3 1,41 6 -1,41 0 26 3 0,81 7 0 1,41 40 5,8 0,98 8 0 -1,41 40 0,2 1,08 9 0 0 40 3 1,05 Để quan sát quy luật thay đổi của độ hút nƣớc khi tỉ lệ thành phần nguyên liệu thay đổi đƣợc dễ dàng hơn, luận án đã xây dựng các đồ thị nhƣ hình 4.1 và 4.2. 56 Hình 4.1. Sự thay đổi độ hút nƣớc khi tỉ lệ dùng bột gỗ thay đổi Hình 4.2. Sự thay đổi độ hút nƣớc khi tỉ lệ dùng MAPE thay đổi Từ đồ thị hình 4.3 và 4.4 cho thấy, mức độ hút nƣớc của vật liệu WPC là rất thấp, tuy nhiên khi tỉ lệ bột gỗ tăng lên thì độ hút nƣớc tăng lên, còn khi tỉ lệ MAPE tăng lên thì độ hút nƣớc có xu hƣớng tăng lên và sau đó giảm xuống. Nguyên nhân dẫn đến hiện tƣợng này có thể giải thích nhƣ sau: bản thân nhựa HDPE không hút nƣớc, tuy nhiên khi phối trộn một lƣợng nhất định bột gỗ, do bột gỗ tuy đã đƣợc nén ép ở nhiệt độ cao đã có sự thay đổi về khả năng hút nƣớc nhƣng vẫn không thể trở thành vật liệu kỵ nƣớc hoàn toàn do đó WPC 0,60 0,70 0,80 0,90 1,00 1,10 1,20 1,30 1,40 1,50 20 30 40 50 60 Đ ộ h ú t n ư ớ c, % Tỉ lệ bột gỗ, % 0,80 0,85 0,90 0,95 1,00 1,05 1,10 1,15 0,0 2,0 4,0 6,0 Đ ộ h ú t n ư ớ c, % Tỉ lệ MAPE, % 57 luôn có khả năng hút nƣớc. Đây cũng chính là nguyên nhân dẫn đến độ hút nƣớc của WPC tăng lên khi lƣợng bột gỗ tăng lên. Đối với vấn đề khi tăng lƣợng MAPE làm cho độ hút nƣớc gỗ lúc đầu vẫn tăng nhẹ và sau giảm mạnh cũng có thể do khả năng hút nƣớc của bột gỗ dẫn đến. Vì khi lƣợng MAPE chƣa đủ lớn (chƣa đạt giá trị phù hợp) thì chƣa tạo ra tác dụng giảm thiểu các nhóm chức ƣa nƣớc trong gỗ (cũng chính là các nhóm có thể tạo ra liên kết với MAPE), khi lƣợng MAPE đủ lớn sẽ làm giảm lƣợng nhóm chức ƣa nƣớc và kết quả là độ hút nƣớc WPC giảm xuống. Phƣơng trình tƣơng quan giữa tỉ lệ trộn bột gỗ (X1) và tỉ lệ trộn MAPE (X2) với độ hút nƣớc (W) của WPC nhƣ sau: W = 1,12-0,17X1 + 0,03X1 2 - 0,23X2 - 0,07X1X2 + 0,03X2 2 Hệ số tƣơng quan: R = 0,89 4.1.2.3. Ảnh hưởng đến độ bền khi chịu kéo Độ bền khi chịu kéo của vật liệu WPC là tiêu chí đánh giá chất lƣợng sản phẩm khi dùng trong các trƣờng hợp chi tiêu chịu lực kéo thƣờng xuyên, do đó đây là chỉ tiêu cơ học cần thiết. Kết quả xác định độ bền kéo của WPC khi tỉ lệ thành phần khác nhau đƣợc trình bày trong bảng 4.9. Bảng 4.9. Độ bền kéo của WPC với tỉ lệ thành phần khác nhau TT X1 X2 Tỉ lệ bột gỗ (PKL) Tỉ lệ MAPE (PKL) Độ bền kéo (MPa) 1 -1 -1 30 1 21,5 2 1 -1 50 1 16,6 3 -1 1 30 5 22,7 4 1 1 50 5 20,7 5 1,41 0 54 3 18,2 6 -1,41 0 26 3 23,5 7 0 1,41 40 5,8 21,5 8 0 -1,41 40 0,2 18,4 9 0 0 40 3 20,6 58 Kết quả xác định cho thấy, độ bền kéo của WPC khi thay đổi tỉ lệ trộn vật liệu nằm trong khoảng từ 16 MPa đến 24 MPa. Đồ thị thể hiện sự ảnh hƣởng của tỉ lệ trộn bột gỗ và tỉ lệ MAPE đến độ bền kéo của WPC đƣợc thể hiện trong hình 4.3 và 4.4. Hình 4.3. Sự thay đổi độ bền kéo khi tỉ lệ dùng bột gỗ thay đổi Hình 4.4. Sự thay đổi độ hút nƣớc khi tỉ lệ dùng MAPE thay đổi Từ hình 4.3 và 4.4 cho thấy khi tỉ lệ bột gỗ tăng lên thì độ bền kéo WPC giảm xuống, ngƣợc lại khi tỉ lệ MAPE tăng lên thì độ bền kéo của WPC tăng 14,00 15,00 16,00 17,00 18,00 19,00 20,00 21,00 22,00 23,00 24,00 25,00 20 30 40 50 60 Đ ộ b ề n k é o , M P a Tỉ lệ bột gỗ, % 18,00 19,00 20,00 21,00 22,00 0,0 1,0 2,0 3,0 4,0 5,0 6,0 Đ ộ b ề n k é o , M P a Tỉ lệ MAPE, % 59 lên. Điều này nói lên rằng để tạo ra đƣợc vật liệu có độ bền kéo cao thì lƣợng bột gỗ không quá cao và lƣợng MAPE phải lựa chọn vừa đủ để đạt giá trị lớn nhất. Phƣơng trình tƣơng quan giữa tỉ lệ trộn bột gỗ (X1) và tỉ lệ trộn MAPE (X2) với độ bền khi chịu kéo (S) của WPC nhƣ sau: S = 22,076 + 0,877X1 - 0,441X1 2 - 1,123X2 + 0,233X1X2 + 0,242X2 2 Hệ số tƣơng quan: R = 0,92 4.1.2.4. Ảnh hưởng đến độ bền uốn tĩnh Độ bền uốn tĩnh của vật liệu nói chung, vật liệu WPC nói riêng là chỉ tiêu không thể thiếu để đánh giá chất lƣợng cũng nhƣ làm cơ sở để tính toán thiết kế chi tiết sản phẩm. Trong nghiên cứu này, độ bền uốn tĩnh đã đƣợc xác định với các loại sản phẩm WPC tạo ra với các tỉ lệ trộn nguyên liệu khác nhau. Kết quả nhƣ trong bảng 4.10. Bảng 4.10. Độ bền uốn tĩnh của WPC khi tỉ lệ thành phần khác nhau TT X1 X2 Tỉ lệ bột gỗ (PKL) Tỉ lệ MAPE (PKL) Độ bền uốn (MPa) 1 -1 -1 30 1 22,3 2 1 -1 50 1 20,0 3 -1 1 30 5 23,7 4 1 1 50 5 22,3 5 1,41 0 54 3 20,4 6 -1,41 0 26 3 24,5 7 0 1,41 40 5,8 22,3 8 0 -1,41 40 0,2 19,9 9 0 0 40 3 22,2 Kết quả trong bảng cho thấy độ bền uốn tĩnh của WPC ở các tỉ lệ trộn khác nhau thay đổi từ 19 MPa đến 25 MPa. Để có thể mô tả một cách trực quan sự thay đổi của độ bền uốn tĩnh khi tỉ lệ trộn các thành phần thay đổi, tiến hành xây dựng các đồ thị nhƣ hình 4.5 và 4.6. 60 Hình 4.5. Sự thay đổi độ bền uốn tĩnh khi tỉ lệ dùng bột gỗ thay đổi Hình 4.6. Sự thay đổi độ bền uốn tĩnh khi tỉ lệ dùng MAPE thay đổi Từ kết quả hình 4.5 và 4.6 cho thấy, cũng tƣơng tự nhƣ đối với độ bền kéo, khi tỉ lệ bột gỗ tăng lên thì độ bền uốn của WPC cũng có quy luật biến đổi tƣơng tự. Khi lƣợng bột gỗ trong vật liệu tăng lên thì độ bền uốn giảm xuống và ngƣợc lại khi tỉ lệ chất trợ tƣơng hợp MAPE tăng lên thì độ bền uốn tăng theo, tuy nhiên, lƣợng MAPE tăng đến khoảng 4-5% thì độ bền uốn có xu hƣớng không đổi thậm chí có xu hƣớng giảm. Từ đó cũng có thể thấy, khi sản xuất WPC cần xem xét lựa chọn phù hợp tỉ lệ trộn bột gỗ và tỉ lệ MAPE để thu đƣợc sản phẩm có độ bền uốn tĩnh cao nhất. 18,00 19,00 20,00 21,00 22,00 23,00 24,00 25,00 20 30 40 50 60 Đ ộ b ề n u ố n t ĩn h , M P a Tỉ lệ bột gỗ, % 18,00 19,00 20,00 21,00 22,00 23,00 24,00 0,0 1,0 2,0 3,0 4,0 5,0 6,0 Đ ộ b ề n u ố n t ĩn h , M P a Tỉ lệ MAPE, % 61 Phƣơng trình tƣơng quan giữa tỉ lệ trộn bột gỗ (X1) và tỉ lệ trộn MAPE (X2) với độ bền uốn tĩnh (MOR) của WPC nhƣ s
File đính kèm:
luan_an_nghien_cuu_mot_so_yeu_to_anh_huong_cua_cong_nghe_tao.pdf