Luận án Nghiên cứu thiết kế chế tạo vi cảm biến vận tốc góc âm thoa và cảm biến gia tốc kiểu tụ
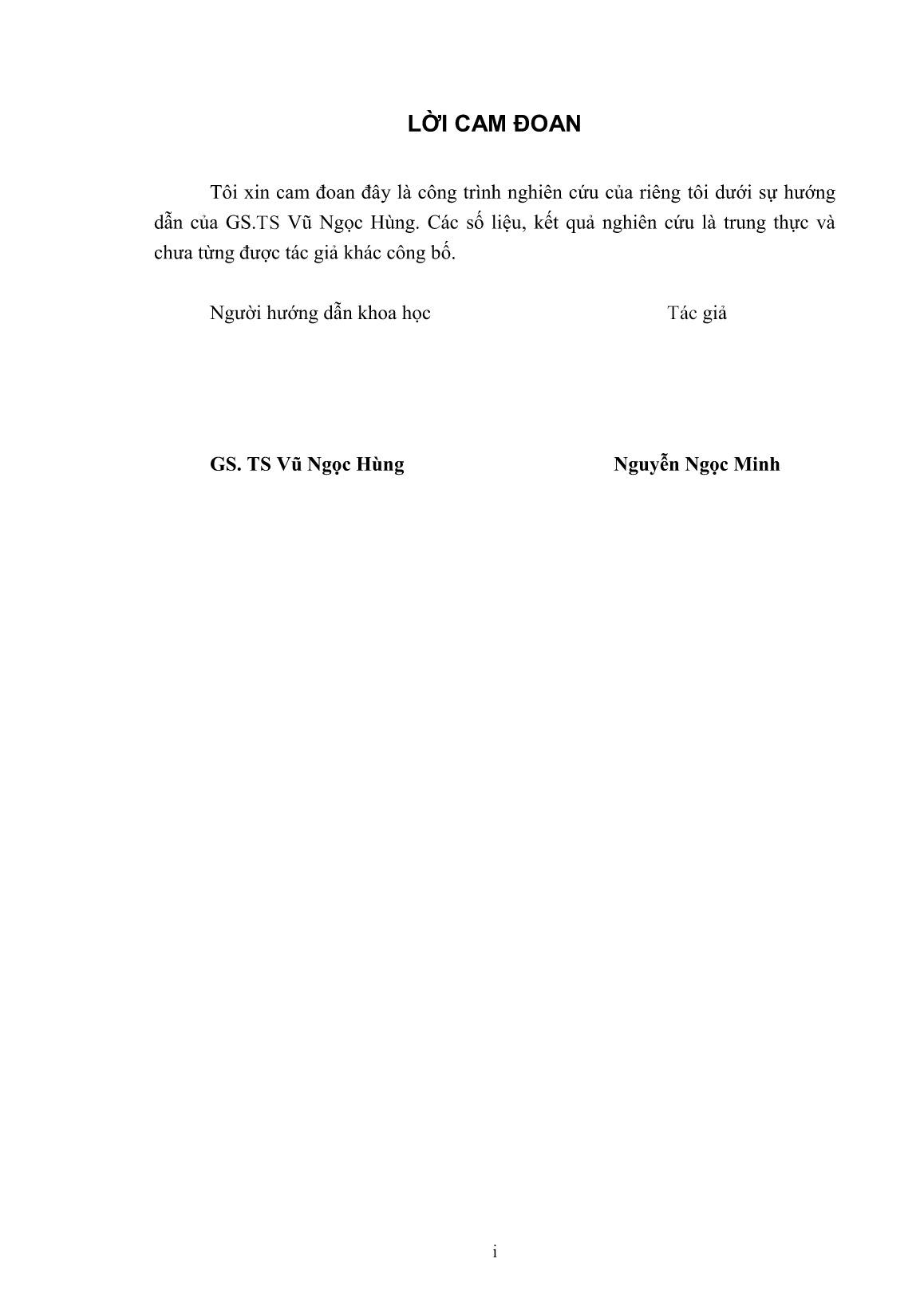
Trang 1
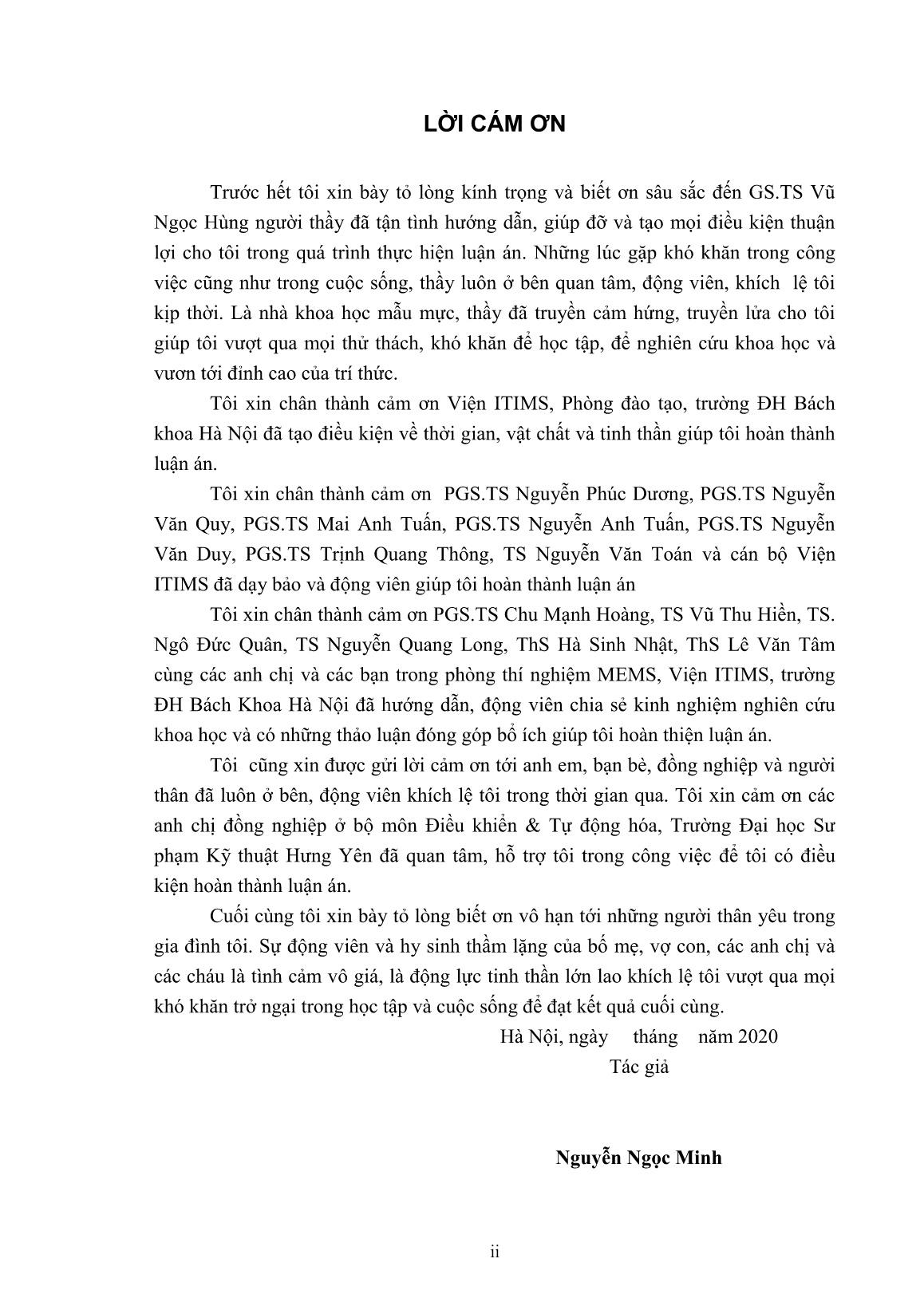
Trang 2
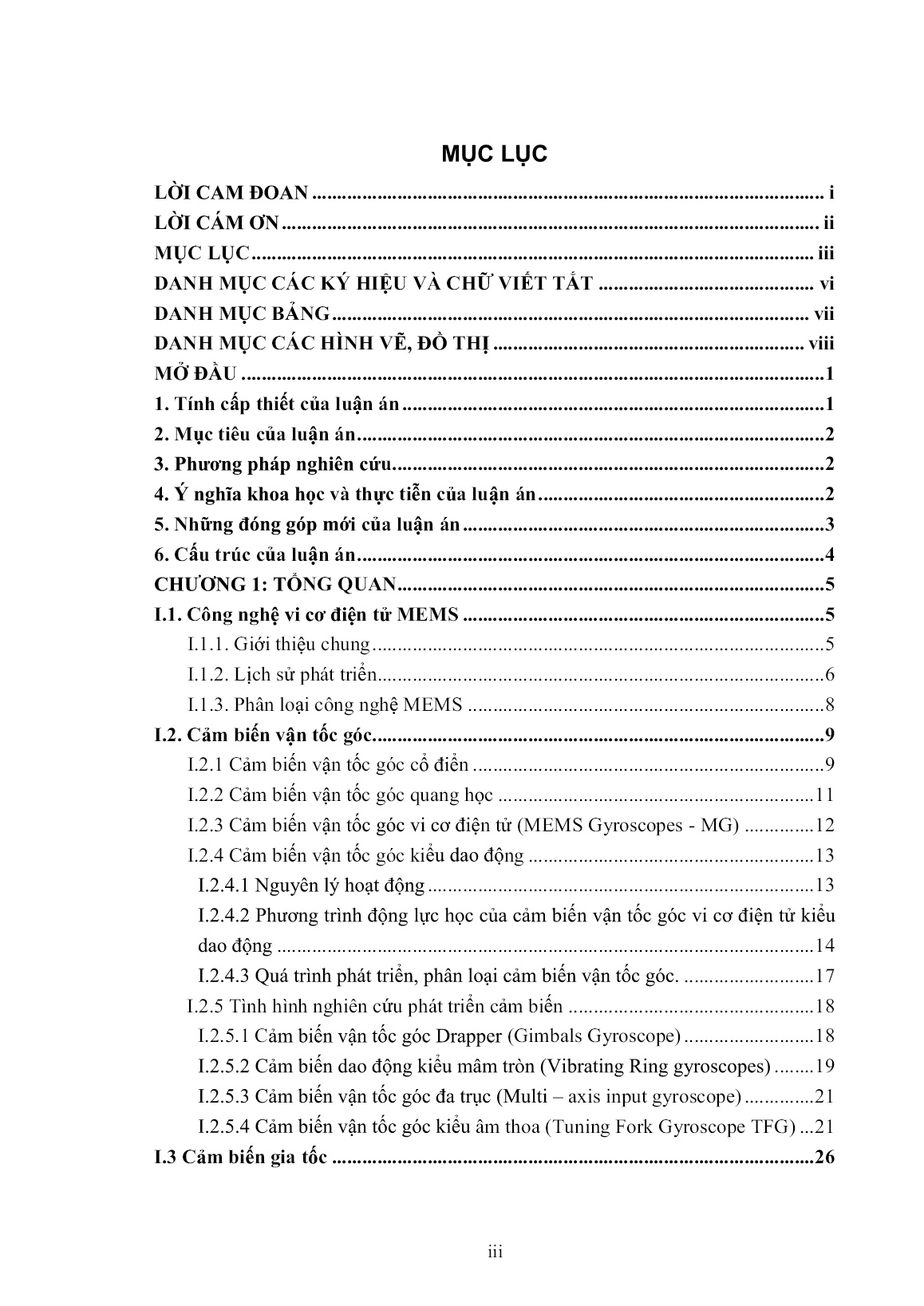
Trang 3
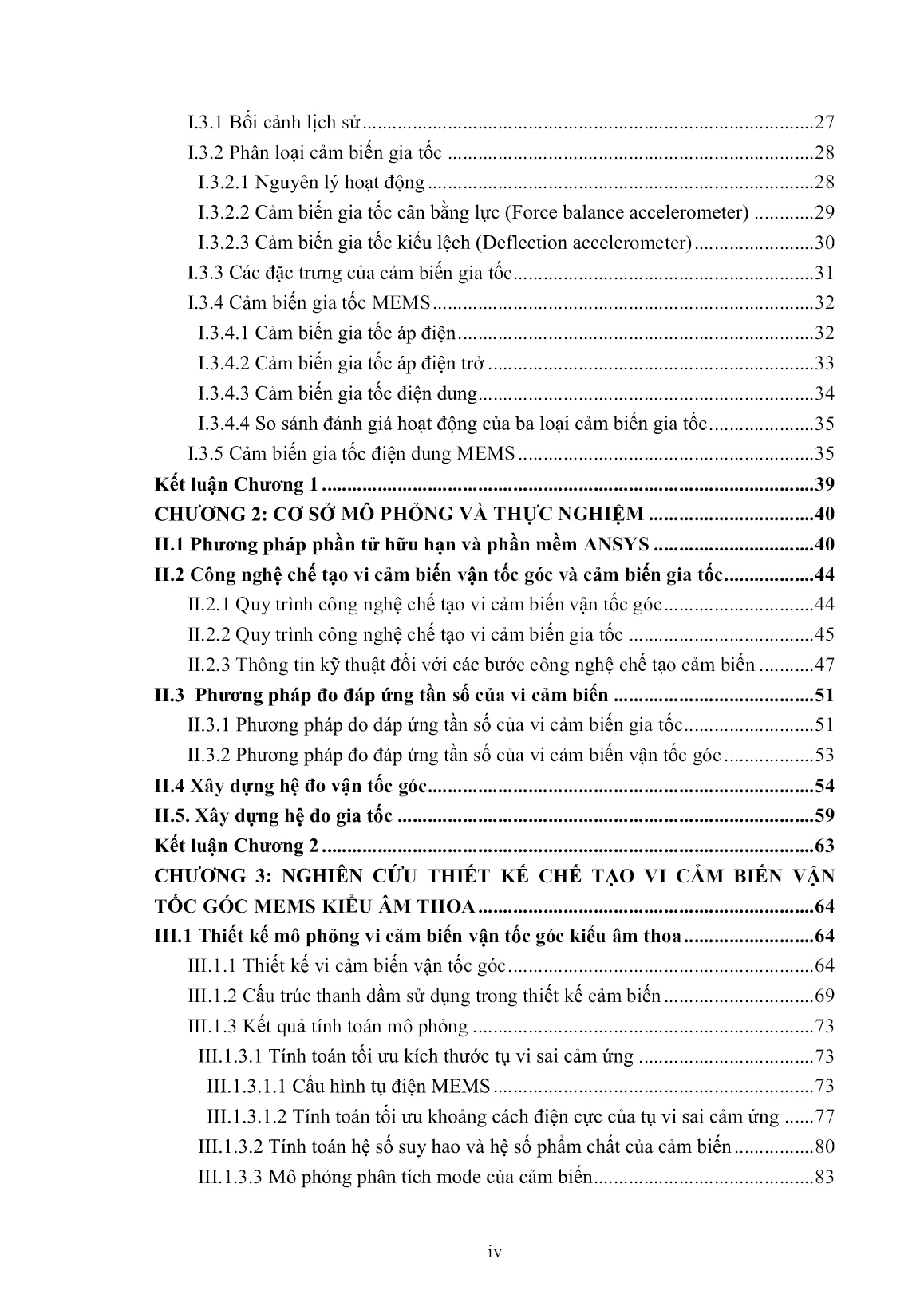
Trang 4
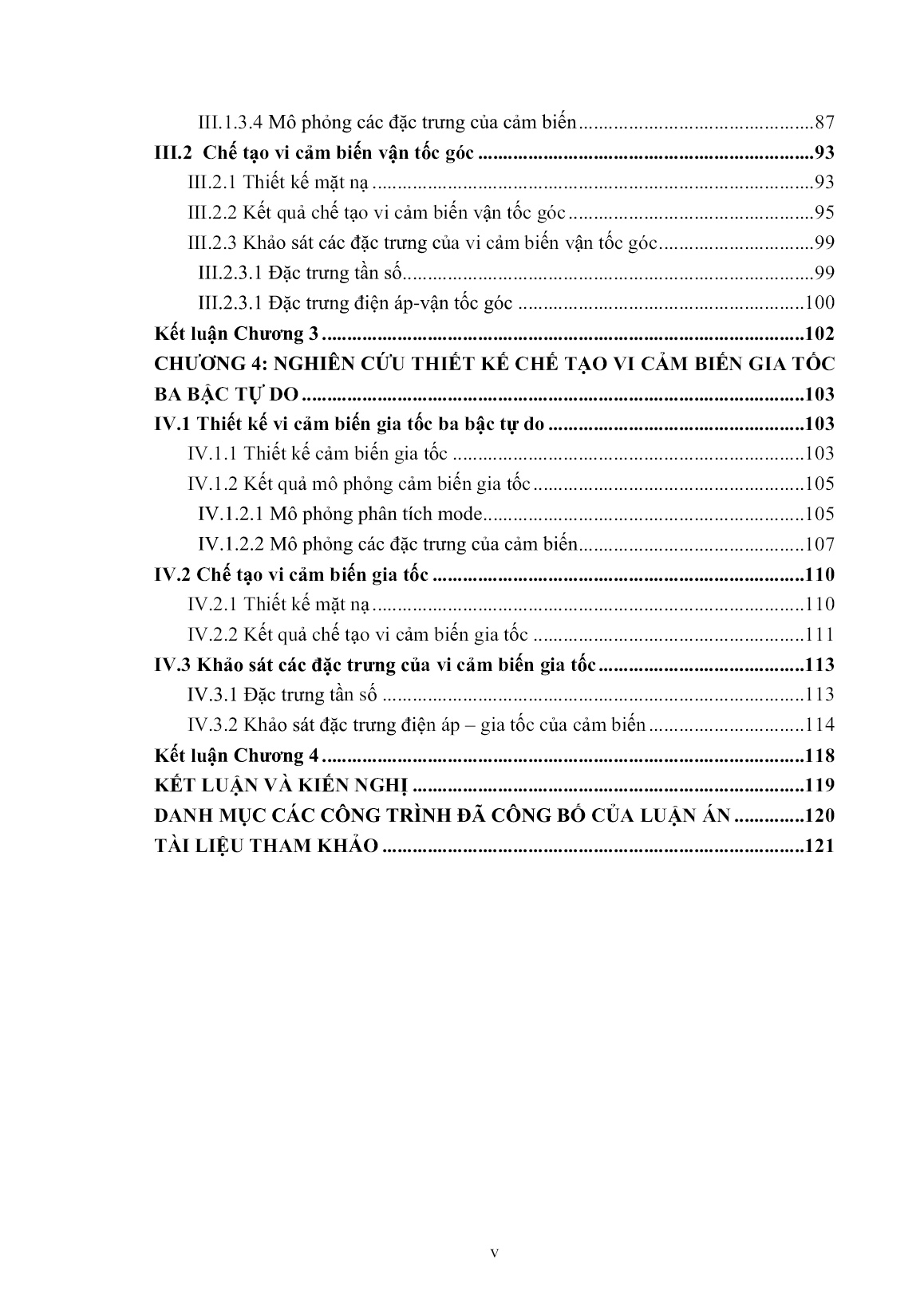
Trang 5
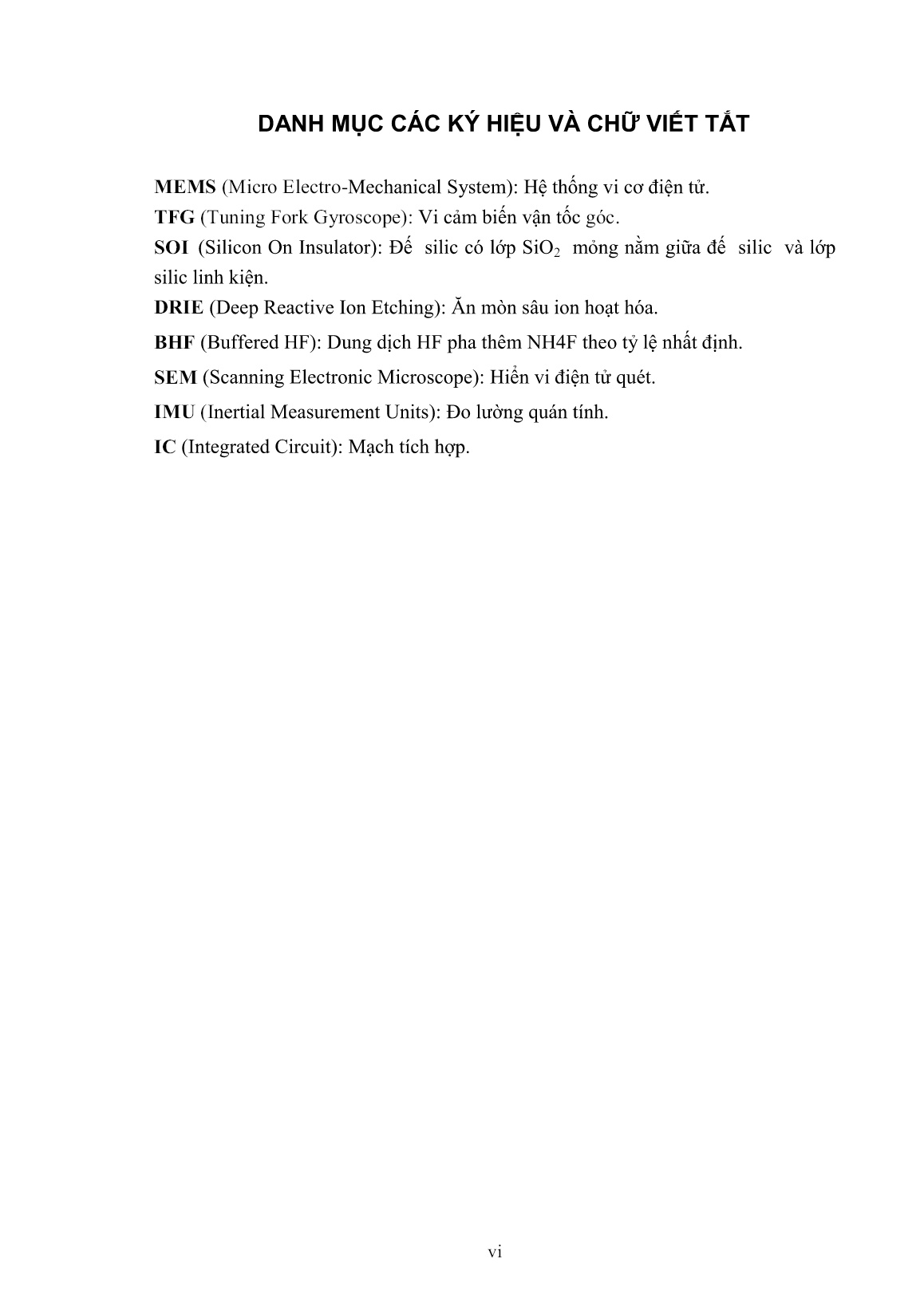
Trang 6
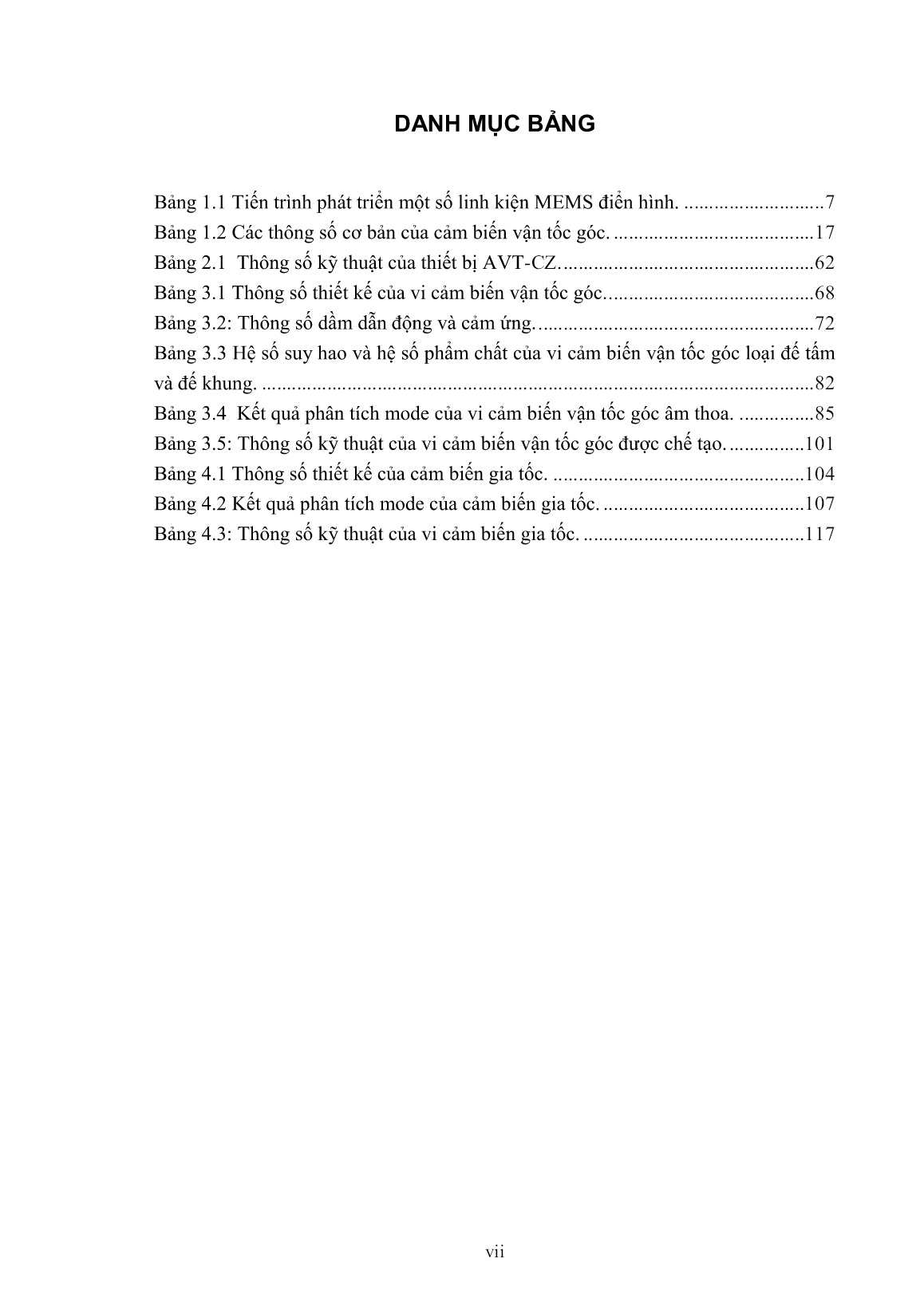
Trang 7
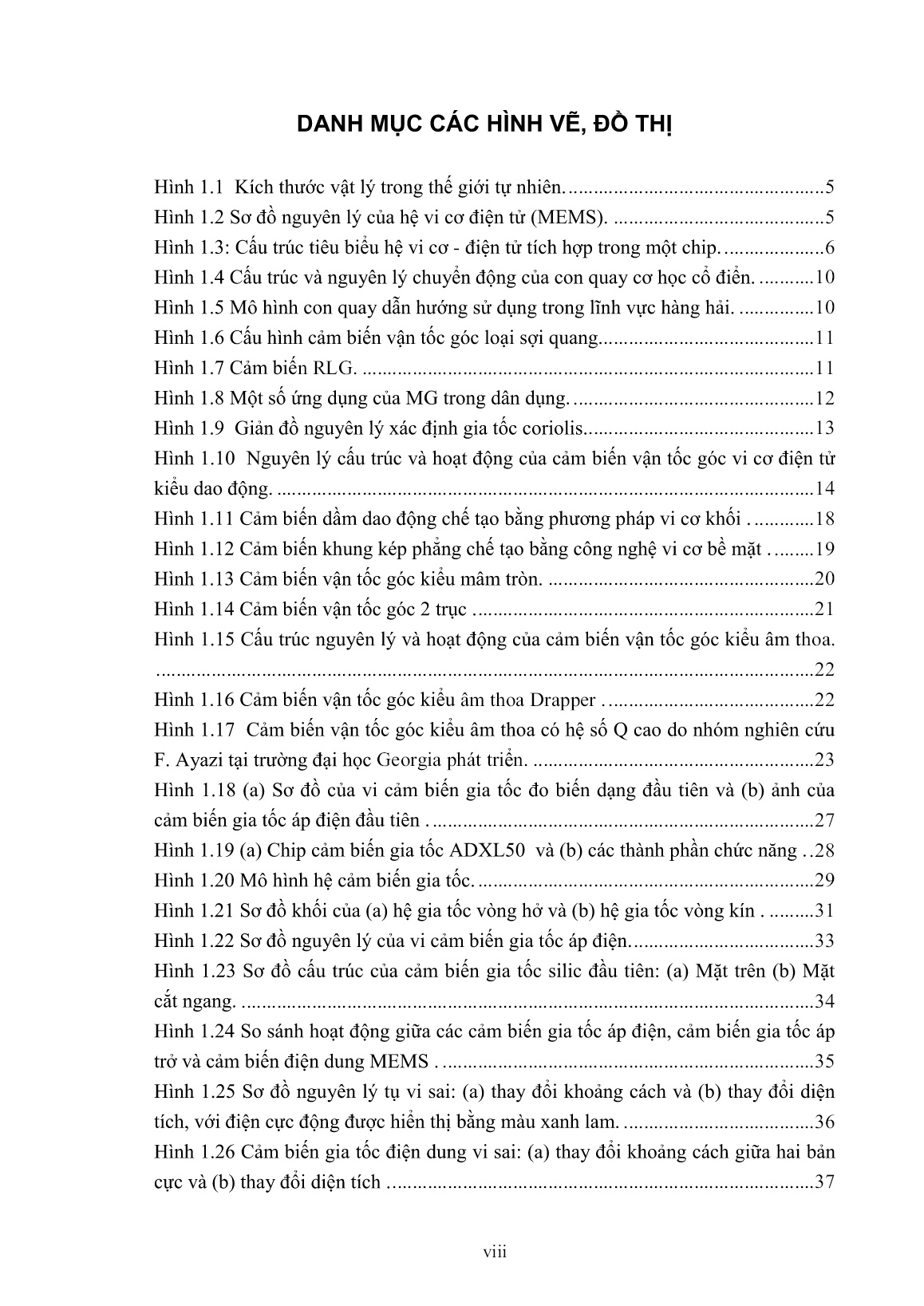
Trang 8
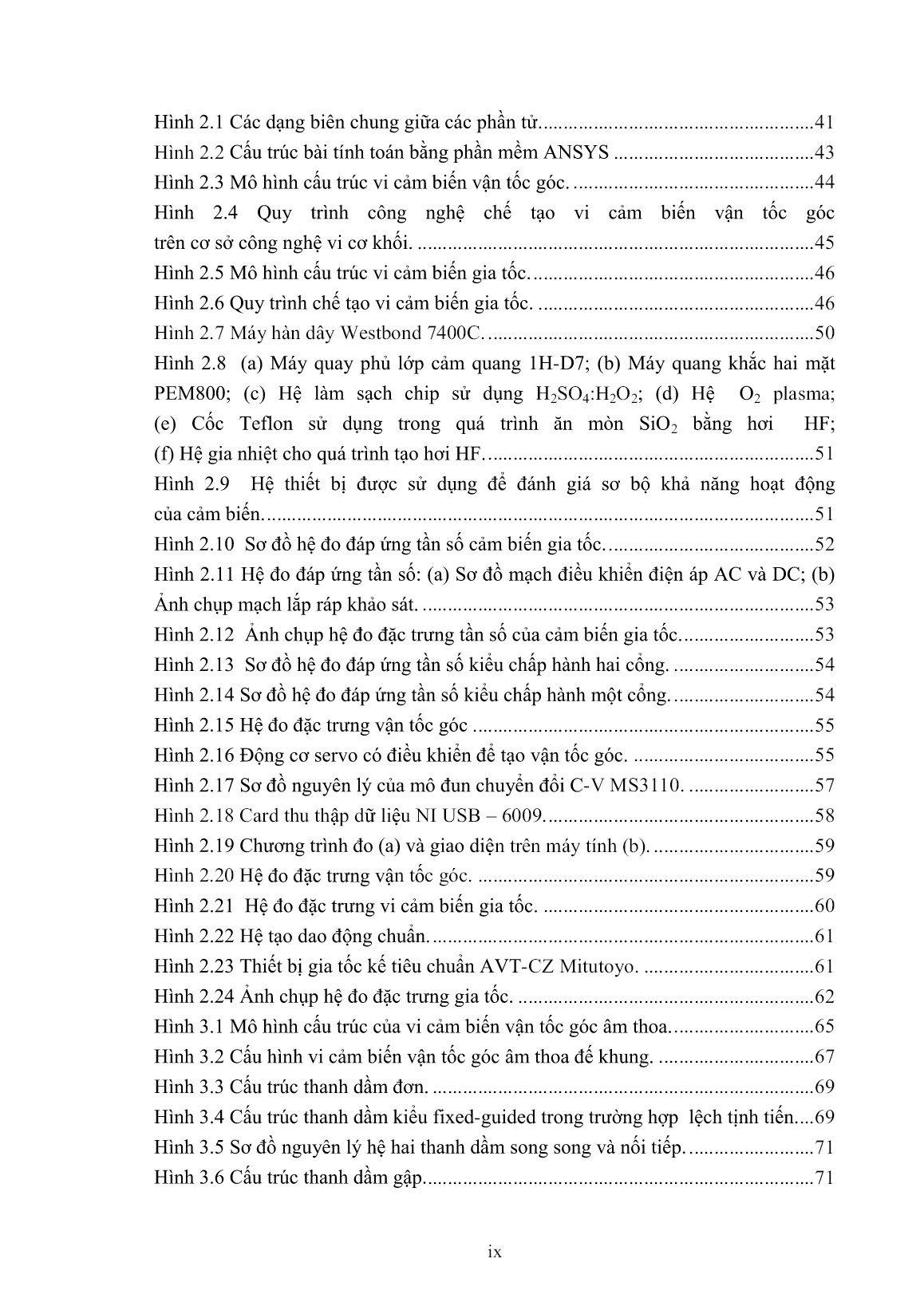
Trang 9
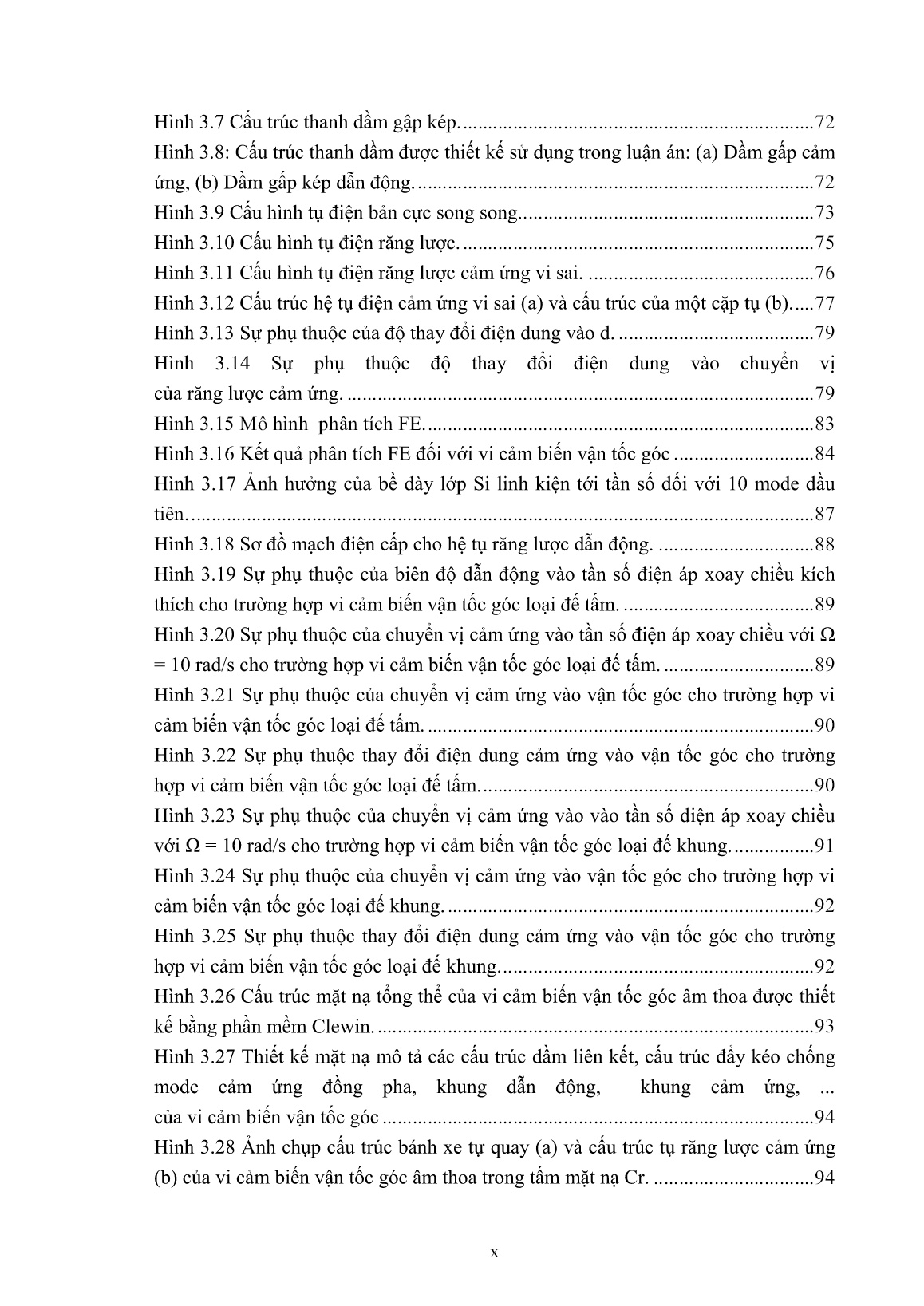
Trang 10
Tải về để xem bản đầy đủ
Bạn đang xem 10 trang mẫu của tài liệu "Luận án Nghiên cứu thiết kế chế tạo vi cảm biến vận tốc góc âm thoa và cảm biến gia tốc kiểu tụ", để tải tài liệu gốc về máy hãy click vào nút Download ở trên.
Tóm tắt nội dung tài liệu: Luận án Nghiên cứu thiết kế chế tạo vi cảm biến vận tốc góc âm thoa và cảm biến gia tốc kiểu tụ
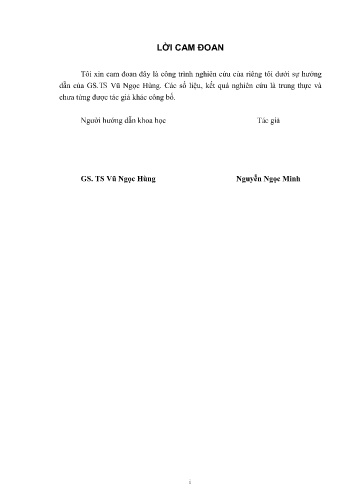
à đã thu được nhiều kết quả ở Berkeley trong những năm 1960 trong ngành xây dựng. Phương pháp này được cung cấp nền tảng toán học chặt chẽ vào năm 1973 với việc tổng kết trong cuốn An Analysis of The Finite element Method và kể từ đó PPPTHH được tổng quát hóa thành một ngành của toán ứng dụng, một mô hình số học cho các hệ thống tự nhiên, được ứng dụng rộng rãi trong kĩ thuật, ví dụ như điện từ học và động lực học chất lỏng. Những năm gần đây, nhờ sự phát triển của các công cụ toán cùng với sự phát triển của máy tính điện tử, đã thiết lập và dần dần hoàn thiện các phần mềm công nghiệp, sử dụng để giải các bài toán cơ học vật rắn, cơ học thuỷ khí, các bài toán động, bài toán tường minh và không tường minh, các bài toán tuyến tính và phi tuyến, các bài toán về trường điện từ, bài toán tương tác đa trường vật lý. ANSYS (Analysis Systems) là một gói phần mềm phân tích phần tử hữu hạn (Finite Element Analysis - FEA) hoàn chỉnh dùng để mô phỏng, tính toán thiết kế công nghiệp, đã và đang được sử dụng trên thế giới trong hầu hết các lĩnh vực kỹ thuật: kết cấu, nhiệt, dòng chảy, điện, điện từ, tương tác giữa các môi trường, giữa các hệ vật lý. ANSYS được đưa ra từ năm 1970, do nhóm nghiên cứu của giáo sư Dr. Jonh 42 Swanson dựa trên việc đưa ra hệ thống tính toán Swanson. Trong hệ thống này, bài toán cơ học kĩ thuật được giải quyết bằng phương pháp lấy chuyển vị làm gốc. Trong tính toán thiết kế cơ khí, phần mềm ANSYS có thể liên kết với các phần mềm thiết kế mô hình hình học 2D và 3D để phân tích trường ứng suất, biến dạng, trường nhiệt độ, tốc độ dòng chảy, có thể xác định được độ mòn, mỏi và phá huỷ của chi tiết. Nhờ việc xác định đó, có thể tìm các thông số tối ưu cho công nghệ chế tạo. ANSYS còn cung cấp phương pháp giải các bài toán cơ với nhiều dạng mô hình vật liệu khác nhau: đàn hồi tuyến tính, đàn hồi phi tuyến, đàn dẻo, đàn nhớt, dẻo, dẻo nhớt, chảy dẻo, vật liệu siêu đàn hồi, siêu dẻo, các chất lỏng và chất khí. Hình 2.2 cho ta cái nhìn tổng quát cấu trúc cơ bản của một bài tính trong ANSYS, gồm 3 phần chính: tạo mô hình tính (preprocessor), tính toán (solution) và xử lý kết quả (postprocessor). Ngoài 3 bước chính trên, quá trình phân tích bài toán trong ANSYS còn phải kể đến quá trình chuẩn bị (preferences) là quá trình định hướng cho bài tính. Trong quá trình này ta cần định hướng xem bài toán ta sắp giải dùng kiểu phân tích nào (kết cấu, nhiệt hay điện từ), mô hình hóa như thế nào (đối xứng trục hay đối xứng quay, hay mô hình 3 chiều đầy đủ), dùng kiểu phần tử nào. Hiểu được các bước phân tích này trong ANSYS sẽ giúp ta dễ dàng hơn trong việc giải bài toán của mình. Vấn đề đặt ra là làm sao để thể hiện những ý tưởng này trong ANSYS. ANSYS cung cấp 2 cách để giao tiếp với người dùng (Graphic User Interface, GUI), công cụ trực quan dùng menu với các thao tác click chuột hoặc viết mã lệnh trong một file văn bản rồi đọc vào từ File/Read input from (ta cũng có thể dùng kết hợp 2 cách này một cách linh hoạt: dùng lệnh tạo cấu trúc, rồi dùng menu khai thác kết quả). Bài toán phân tích cơ của cấu trúc là bài toán phân tích tĩnh được thực hiện trên phần mềm ANSYS thông qua kiểu bài toán phân tích mode. Kết quả nhận được là tần số dao động riêng và dạng mode dao động của cảm biến. Phương trình chuyển động trong trường hợp này được cho như sau: 0uKuM (2.1) Trong đó, {M} là ma trận khối lượng cấu trúc; {K} là ma trận độ cứng cấu trúc; u là chuyển vị. Đây là phương trình vi phân dao động tự do, trong đó không có thành phần giảm chấn (D). Phương trình này cho lời giải là các tần số dao động riêng ứng với các mode dao động riêng tương ứng. Đối với các hệ tuyến tính, dao động tự do có dạng dao động điều hoà, được mô tả bằng phương trình: tcosu ii (2.2) 43 Trong đó, i là trị riêng biểu diễn dạng dao động với tần số dao động riêng thứ i; i là tần số góc riêng thứ i có đơn vị là (rad/s); t là thời gian. Hình 2.2 Cấu trúc bài tính toán bằng phần mềm ANSYS Thay (2.2) vào (2.1), thu được: 02 ii KM (2.3) Đẳng thức này thoã mãn khi i =0 hoặc KMi 2 =0. Điều kiện thứ nhất là điều kiện tầm thường, vì vậy có thể bỏ qua. Điều kiện thứ hai cho lời giải: 44 02 MK (2.4) Đây là bài toán trị riêng, trong đó lời giải sẽ là n giá trị 2 tương ứng n trị riêng i , trong đó, n là số bậc tự do (DOF- Degree Of Freedom). Từ các giá trị 2 thu được có thể tính được tần số do động riêng theo hệ thức: 2 i if (2.5) Trên đây là cơ sở lý thuyết của bài toán phân tích mode. Tiếp theo, phương pháp này được áp dụng để thu được các giá trị tần số dao động riêng tương ứng với từng dạng dao động tự do (mode shape). Từ đó chúng ta có thể tìm cách tối ưu các thông số hình học của cấu trúc như chiều dài, độ rộng của dầm, hay kích thước của khối gia trọng. Trên cơ sở tích hợp phần đồ họa máy tính (CAD), ANSYS cho phép tái hiện được các mô hình thiết kế cảm biến với kích thước đúng như thực tế trong phần tiền xử lý PREP7. II.2 Công nghệ chế tạo vi cảm biến vận tốc góc và cảm biến gia tốc II.2.1 Quy trình công nghệ chế tạo vi cảm biến vận tốc góc Vi cảm biến vận tốc góc kiểu âm thoa có cấu hình được mô tả như trên hình 2.3. Về nguyên lý, cảm biến gồm hai khối gia trọng được gắn với khung cố định bởi các dầm treo đàn hồi và được liên kết với nhau qua hệ dầm ghép nối đàn hồi. Hình 2.3 Mô hình cấu trúc vi cảm biến vận tốc góc. Vi cảm biến vận tốc góc kiểu âm thoa được chế tạo trên cơ sở công nghệ vi cơ khối sử dụng đế SOI (Silicon On Insulator). Quy trình chế tạo vi cảm biến vận tốc góc với các bước công nghệ chính như quang khắc, ăn mòn khô sâu, phún xạ được trình bày trên hình 2.4. Để chế tạo vi cảm biến vận tốc góc kiểu âm thoa, 45 phiến SOI kích thước (2 cm x 2 cm) đã được sử dụng, trong đó lớp Si tạo linh kiện có bề dày 30 m, lớp SiO2 đệm có bề dày 2 m lớp Si đế có bề dày 500 m. Lớp mỏng SiO2 được phủ lên bề mặt đế bằng phương pháp ôxy hóa nhiệt. Quá trình quang khắc và ăn mòn lớp ôxít được thực hiện để đưa ảnh cấu hình của linh kiện lên bề mặt đế. Sau đó, quá trình khắc khô sâu hoạt hóa DRIE được thực hiện nhằm định hình cấu trúc của vi cảm biến vận tốc góc trong lớp Si tạo linh kiện. Sau quá trình ăn mòn khô, điện cực Au được chế tạo bằng kỹ thuật phún xạ. Để tạo ra cấu hình treo trên đế khung, quá trình ăn mòn khô từ mặt dưới của đế được thực hiện. Cuối cùng, bước ăn mòn mẫu trong hơi HF được thực hiện để loại bỏ lớp ôxít SiO2 đệm nằm dưới lớp linh kiện nhằm tách các cấu trúc như điện cực động, thanh dầm treo và khối gia trọng khỏi đế. (a ) Phiến SOI (b ) Quang khắc (c ) Ăn mòn SiO2 (d ) Ăn mòn khô sâu (e ) Phún xạ điện cực (f ) Ăn mòn khô sâu (g ) Ăn mòn SiO2 đệm Lớp SiO2 nhiệt Lớp Si đế Lớp Si linh kiện Lớp SiO2 đệm Pt Lớp cảm quang Hình 2.4 Quy trình công nghệ chế tạo vi cảm biến vận tốc góc trên cơ sở công nghệ vi cơ khối. II.2.2 Quy trình công nghệ chế tạo vi cảm biến gia tốc Vi cảm biến gia tốc kiểu điện dung có cấu hình được mô tả như trên hình 2.5 và cũng được chế tạo trên cơ sở công nghệ vi cơ khối. Sơ đồ ở hình 2.6 mô tả các bước chính trong quy trình chế tạo. 46 Hình 2.5 Mô hình cấu trúc vi cảm biến gia tốc. (a) Phiến Si Lớp SiO2 nhiệt Lớp SiO2 đệm Lớp Si linh kiện Lớp Si đế (b) Quang khắc (d) Ăn mòn khô sâu (f) Ăn mòn lớp SiO2 đệm (c) Ăn mòn SiO2 (e) Phún xạ điện cực Lớp Au Lớp cảm quang Hình 2.6 Quy trình chế tạo vi cảm biến gia tốc. 47 Để chế tạo cảm biến gia tốc, phiến SOI kích thước (2 cm x 2 cm), trong đó lớp Si tạo linh kiện có bề dày 30 m, lớp SiO2 đệm có bề dày 2 m lớp Si đế có bề dày 500 m cũng đã được sử dụng. Quy trình chế tạo vi cảm biến vận tốc góc với các bước công nghệ chính như quang khắc, ăn mòn khô sâu, phún xạ,... đã được xây dựng với các điều kiện kỹ thuật tương tự như đối với quy trình công nghệ chế tạo vi cảm biến vận tốc góc. Như vậy, trong quy trình công nghệ chế tạo cảm biến gia tốc, các bước a e được thực hiện tương tự như trong quy trình công nghệ chế tạo vi cảm biến vận tốc góc. Bước f trong quy trình này liên quan tới quá trình ăn mòn mẫu trong hơi HF để loại bỏ lớp ôxít SiO2 đệm nằm dưới lớp linh kiện nhằm tách các cấu trúc như điện cực động, thanh dầm treo và khối gia trọng khỏi đế. Hai loại cảm biến đã được chế tạo trên cơ sở sử dụng các hóa chất, khí chuyên dụng,.. tại phòng sạch Viện ITIMS. II.2.3 Thông tin kỹ thuật đối với các bước công nghệ chế tạo cảm biến a. Xử lý đế Đế SOI 2x2 cm2 đã được sử dụng để chế tạo vi cảm biến vận tốc góc và vi cảm biến gia tốc có các thông số kỹ thuật: lớp Si bề mặt/linh kiện với độ dày 30 m tương ứng với bề dày của linh kiện, lớp ôxít Si 2 m và lớp đế Si dày 500 m. Đế SOI đầu tiên được làm sạch bằng acetone và sau đó được xử lý trong dung dịch “Piranha” là hỗn hợp axit sunfuric đậm đặc H2SO4 và hydrogen peroxide H2O2 theo tỷ lệ 4:1 để loại bỏ tất cả chất hữu cơ trên bề mặt đế. Mẫu được ngâm trong dung dịch trên ở nhiệt độ 90 0C trong khoảng thời gian 4 h sau đó được làm sạch trong nước khử ion và sấy khô. b. Ô xi hóa Để tạo lớp SiO2 trên bề mặt mẫu, quá trình ô xi hóa nhiệt đã được thực hiện. Dòng khí O2 với lưu lượng 5,12 lít/phút đã được sử dụng. Quá trình ô xi hóa được thực hiện ở nhiệt độ 1100 oC trong khoảng thời gian 30 phút. Bề dày của lớp SiO2 có giá trị cỡ 0,3 m. c. Quang khắc Các bước kỹ thuật trong qui trình quang khắc bao gồm: - Tạo lớp bám dính xử dụng dung dịch primer OAP bằng kỹ thuật quay phủ (spin coating) với tốc độ 2000 vòng/phút trong khoảng thời gian 30 s lên đế silic . - Phủ dung dịch cảm quang lên bề mặt đế bằng kỹ thuật quay phủ. Dung dịch cảm quang dương OFPR 800-20 cp đã được sử dụng. Quá trình quay phủ lớp cảm quang được thực hiện đầu tiên ở tốc độ 1000 vòng/phút trong thời gian 5 s để 48 dàn đều vật liệu cảm quang trên bề mặt đế, sau đó ở tốc độ 3000 vòng /phút để đạt bề dày cỡ 1 µm. - Xử lý nhiệt ủ sơ bộ để loại bỏ dung môi cũng như ứng suất dư trong lớp cảm quang ở nhiệt độ 110 oC trong khoảng thời gian 90 s. - Hiệu chỉnh mặt nạ quang (kỹ thuật so Mask) và thực hiện chiếu ánh sáng UV trên cơ sở sử dụng thiết bị quang khắc (mask agliner). Bước chiếu sáng cho phép tạo ảnh ẩn trong lớp cảm quang tương ứng với ảnh topo của cấu trúc linh kiện trên mặt nạ quang. Liều chiếu sáng có giá trị cỡ 14 mJ/cm2. - Xử lý ủ nhiệt ở nhiệt độ 90 oC trong khoảng thời gian 120 s. - Tiến hành hiện hình bằng cách ngâm mẫu trong dung dịch hiện hình NMD- 3 trong khoảng thời gian 15-20 s. - Xử lý nhiệt ủ đóng rắn ở nhiệt độ 130 oC trong khoảng thời gian 30 phút. d. Ăn mòn SiO2 Lớp ôxit SiO2 được ăn mòn trong dung dịch BHF. Dung dịch này là hỗn hợp của dung dịch NH4F và dung dịch HF với tỷ lệ tương ứng là 5 : 1. Các phản ứng hóa học liên quan được mô tả như sau: SiO2 + 6HF SiF6+ H2+ 2H2O NH4F NH3 + HF Tốc độ ăn mòn lớp SiO2 trong dung dịch BHF ở nhiệt độ phòng là khoảng 100 nm/phút. e. Ăn mòn khô sâu DRIE (Deep Reactive Ion Etching) Về cơ bản, ăn mòn khô có nguyên lý dựa trên sự kết hợp của quá trình bắn phá ion (quá trình ăn mòn vật lý) và các phản ứng hóa học giữa các ion hoạt hóa hình thành trong trong môi trường plasma có chân không cao với các nguyên tử bề mặt vật liệu tạo ra các sản phẩm ở pha hơi (quá trình ăn mòn hóa học) dẫn đến kết quả khối vật liệu (Si) được tẩy bỏ, tạo ra cấu trúc cần thiết. Để tạo ra các cấu trúc MEMS có tỷ số cạnh cao, cấu trúc có vách thẳng đứng được ăn mòn sâu vào trong đế silic, quá trình ăn mòn cần có tính dị hướng cao. Để đáp ứng yêu cầu trên, kỹ thuật ăn mòn khô sâu trên cơ sở quy trình Bosch đã được ứng dụng trong chế tạo vi cảm biến vận tốc góc và cảm biến gia tốc. Quy trình này gồm hai bước: (i). Ăn mòn Si bằng phương pháp ăn mòn ion hoạt hóa (RIE); (ii). Phủ lớp bảo vệ trên cơ sở quá trình polime hóa. Hai bước trên được lặp lại nhiều lần cho đến khi độ sâu hốc khắc đạt giá trị như thiết kế. Quá trình ăn mòn khô sâu được thực hiện trên cơ sở thiết bị RIE-400iPB, trong đó plasma được tạo bởi kỹ thuật plasma ghép cảm ứng (Inductively Coupled Plasma –ICP). Trong trường hợp này, plasma được tạo trong từ trường của cuộn dây sẽ có mật độ lớn dẫn tới làm tăng tốc 49 độ ăn mòn vật liệu. Công suất nguồn RF cung cấp cho cuộn dây tạo plasma (Coil power) có giá trị cỡ 600 W. Trong bước ăn mòn Si bằng phương pháp ăn mòn ion hoạt hóa (RIE), khí phản ứng SF6 với lưu lượng 130 sccm đã được sử dụng. Quá trình ăn mòn được thực hiện trên cơ sở phản ứng Si + 4F SiF4 trong điều kiện áp suất 20 mTorr và khoảng thời gian 9 s. Công suất nguồn RF cấp cho điện cực chứa đế cần ăn mòn (Platen power) là 15 W. Đối với bước phủ lớp bảo vệ trên cơ sở quá trình polime hóa, khí C4F8 với lưu lượng 85 sccm đã được sử dụng. Quá trình polime hóa được mô tả qua phản ứng nCF2 (CF2)n. Quá trình này được thực hiện trong điều kiện áp suất 20 mTorr khoảng thời gian 7 s. Tốc độ ăn mòn Si trong ăn mòn khô sâu đạt giá trị cỡ 2,5 µm/phút. f. Phún xạ tạo điện cực Để tạo điện cực vàng của linh kiện, phương pháp phún xạ ca tốt đã được sử dụng. Ưu điểm của phương pháp này là có thể chế tạo màng mỏng có độ kết dính tốt với đế, có đồng đều và được khống chế nhờ điều khiển công suất phún xạ. Để tăng độ bám dính của điện cực vàng, lớp lót Cr cần được phún xạ phủ lên bề mặt đế. Quá trình phún xạ được thực hiện trên cơ sở sử dụng khí Ar với lưu lượng 30 sccm và áp suất 10-5 mmHg. Màng Cr với bề dày 15 nm đã được phún xạ ở điều kiện công suất nguồn cao áp DC cỡ 80 W trong khoảng thời gian 3 phút. Đối với màng Au, để đạt được bề dày 100 nm, công suất nguồn cao áp DC và thời gian phún xạ có giá trị tương ứng là 80 W và 5 phút. g. Cắt mẫu tạo chip cảm biến Để cắt mẫu tạo chip cảm biến, mẫu chứa linh kiện được phủ lớp cảm quang bằng máy quay phủ nhằm bảo vệ các chi tiết linh kiện trong quá trình cắt mẫu. Sau đó, các mẫu được cắt thành từng bộ cảm biến trên cơ sở thiết bị cắt mẫu. Tiếp theo, lớp cảm quang trên chip linh kiện được loại bỏ và mẫu được làm sạch trong dung dịch piranha và nước khử ion (DI). Cuối cùng, các chip này sẽ được sấy khô ở nhiệt độ 120°C trong 20 phút. h. Ăn mòn lớp SiO2 đệm trong hơi HF Quá trình ăn mòn trong môi trường hơi HF đã được thực hiện để ăn mòn lớp SiO2 đệm nằm bên dưới lớp linh kiện nhằm giải phóng các điện cực động, dầm treo và các khối gia trọng. Kỹ thuật ăn mòn trong môi trường hơi HF sẽ giúp khắc phục vấn đề dính ướt, hiệu ứng có thể làm đứt gẫy các cấu trúc của cảm biến, đặc biệt là đối với điện cực răng lược. Tốc độ ăn mòn của SiO2 bởi hơi HF với nồng độ 46% ở 50 40°C có giá trị khoảng 0,2 m/phút. Sau khi ăn mòn trong hơi HF, các chip được sấy khô ở 120°C trong 10 phút. i. Đóng gói cảm biến Sau quá trình chế tạo, các chip cảm biến sẽ được đóng gói. Chip cảm biến được dán lên một bo mạch trên cơ sở sử dụng epoxy hai thành phần. Bo mạch làm bằng nhựa cứng có các chân điện cực kim loại. Sau đó, quá trình hàn dây được thực hiện nhằm tạo dây điện cực kết nối giữa các điện cực của chip cảm biến với chân điện cực tương ứng của bo mạch. Quá trình hàn dây được thực hiện trên cơ sở hệ thiết bị hàn siêu âm Westbond 7400C (hình 2.7). Hình 2.7 Máy hàn dây Westbond 7400C, Model 7400C-79C Hình 2.8 trình bày một số hình ảnh liên quan đến một số thiết bị được sử dụng trong chế tạo cảm biến: a) b) c) d) e) f) 51 Hình 2.8 (a) Máy quay phủ lớp cảm quang 1H-D7; (b) Máy quang khắc hai mặt PEM800; (c) Hệ làm sạch chip sử dụng H2SO4:H2O2; (d) Hệ O2 plasma; (e) Cốc Teflon sử dụng trong quá trình ăn mòn SiO2 bằng hơi HF; (f) Hệ gia nhiệt cho quá trình tạo hơi HF. Các thiết bị sử dụng tại trong phòng sạch viện ITIMS. j. Kiểm tra sơ bộ khả năng hoạt động của cảm biến Cảm biến sau khi chế tạo đã được đánh giá sơ bộ về khả năng hoạt động trên cơ sở kiểm tra trạng thái tách cấu trúc và kiểm tra ngắn mạch giữa các điện cực. Để đánh giá trạng thái tách cấu trúc, mẫu được quan sát bằng kính hiển vi (hình 2.9). Đầu dò được sử dụng để tác động trực tiếp lên phần cấu trúc cơ di động như dầm treo và khối gia trọng. Độ lệch được quan sát thấy ở các thanh dầm lò xo cho thấy cấu trúc được tách khỏi đế. Bước kiểm tra này cho phép xác định khả năng loại bỏ hoàn toàn các lớp ôxít đệm và sự gắn giữ cấu trúc neo trên đế. Để kiểm tra ngắn mạch, đồng hồ vạn năng đã được sử dụng nhằm xác định sự ngắn mạch giữa điện cực cảm ứng hoặc điện cực kích thích. Nếu phát hiện ngắn mạch, các cảm biến cần được ăn mòn thêm nữa để loại bỏ các phần kết nối. Hình 2.9 Hệ thiết bị được sử dụng để đánh giá sơ bộ khả năng hoạt động của cảm biến. II.3 Phương pháp đo đáp ứng tần số của vi cảm biến II.3.1 Phương pháp đo đáp ứng tần số của vi cảm biến gia tốc Sơ đồ hệ đo đáp ứng tần số đối với vi cảm biến gia tốc được trình bày trên hình 2.10. Cảm biến được kích thích bởi một tín hiệu điện áp xoay chiều AC với tần số khác nhau cấp vào một đầu của điện cực cảm ứng. Tín hiệu đầu ra được lấy 52 từ đầu kia của điện cực và được khuếch đại. Trên cơ sở đặc trưng đáp ứng tần số, tần số cộng hưởng của cảm biến sẽ được xác định. Để khuếch đại tín hiệu, bộ khuếch đại sử dụng các chip OP37 IC đã được lắp đặt ở đầu ra. Khi khối gia trọng được kích thích bởi điện áp AC, nó sẽ làm dịch chuyển các điện cực cảm ứng. Do điện dung điện cực cảm ứng thay đổi bởi dịch chuyển, điện tích trong điện cực cảm ứng sẽ thay đổi tùy thuộc tần số dao động của khối gia trọng dẫn tới xuất hiện dòng điện ở mạch ngoài. Để tăng cường biên độ dịch chuyển của điện cực cảm ứng, ngoài điện áp xoay chiều AC, điện áp một chiều DC đã được cấp bổ sung cho cảm biến. Chip OP37 là một loại IC OPAMP được sử dụng để khuếch đại và chuyển đổi dòng điện trên thành điện áp. Hình 2.10 Sơ đồ hệ đo đáp ứng tần số cảm biến gia tốc. Trong kết cấu hệ đo, mạch điều khiển độ lớn, tần số của điện áp AC và DC cấp cho bộ cảm biến đã được xây dựng (hình 2.11). Hình 2.12 trình bày hệ đo đặc trưng tần của vi cảm biến gia tốc trong thực tế. (a) 53 (b) Hình 2.11 Hệ đo đáp ứng tần số: (a) Sơ đồ mạch điều khiển điện áp AC và DC; (b) Ảnh chụp mạch lắp ráp khảo sát. Hình 2.12 Ảnh chụp hệ đo đặc trưng tần số của cảm biến gia tốc. II.3.2 Phương pháp đo đáp ứng tần số của vi cảm biến vận tốc góc Hai cấu hình mạch điện tử đã được sử dụng để khảo sát đặc trưng đáp ứng tần số nhằm xác định tần số cộng hưởng tự nhiên của vi cảm biến vận tốc góc: cấu hình hai cổng chấp hành và cấu hình chấp hành một cổng. Trong cấu hình hệ đo chấp hành hai cổng, điện áp xoay chiều VAC được lấy từ máy phân tích mạng (Network Analyzer) và cấp cho phần điện cực cố định của hệ kích thích răng lược. Trong khi đó, điện áp một chiều DC được đưa vào khối gia trọng. Điện áp DC được sử dụng để tăng cường lực tĩnh điện giữa các răng lược. Tín hiệu đầu ra từ phần điện cực động của hệ kích thích răng lược được khuếch đại bởi một bộ khuếch đại trở kháng và kết nối đến đầu vào máy phân tích mạng để quan sát đặc tính như 54 trong hình 2.13. Biên độ dao động cực đại được xác định trên cơ sở đặc trưng điện dung - tần số. Hình 2.13 Sơ đồ hệ đo đáp ứng tần số kiểu chấp hành hai cổng. Trong cấu hình chấp hành một cổng, điện áp xoay chiều AC với tần số biến đổi lấy từ máy phân tích mạng được sử dụng để kích thích cảm biến (Hình 2.14). Điện áp xoay chiều được kết hợp với điện áp một chiều DC cấp cho khối gia trọng cảm biến. Tín hiệu đầu ra được lấy từ phần điện cực cố định của hệ kích thích răng lược và được khuếch đại bởi một bộ khuếch đại trở kháng và kết nối đến đầu vào máy phân tích mạng. Hình 2.14 Sơ đồ hệ đo đáp ứng tần số kiểu chấp hành một cổng. II.4 Xây dựng hệ đo vận tốc góc Trong phần này, chúng tôi sẽ trình bày kết quả xây dựng hệ đo vận tốc góc của cảm biến. Sơ đồ khối và sơ đồ lắp ráp của hệ đo đặc trưng cảm biến được trình bày tương ứng trên hình
File đính kèm:
luan_an_nghien_cuu_thiet_ke_che_tao_vi_cam_bien_van_toc_goc.pdf
Thong tin Web - TA.pdf
Thong tin Web - TV.pdf
TomTat LA.pdf