Luận án Trường nhiệt độ và trường ẩm trong khuôn tươi
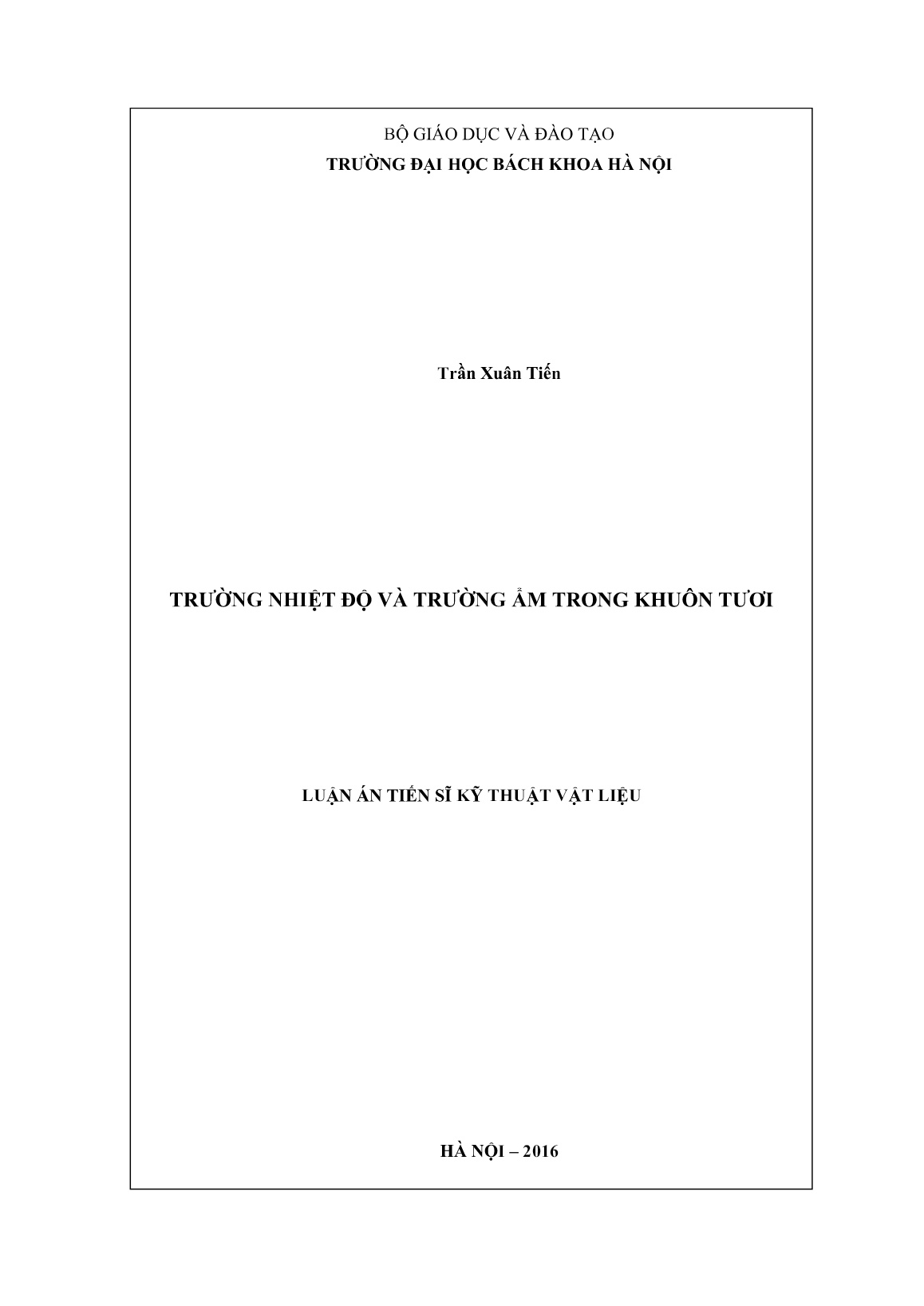
Trang 1
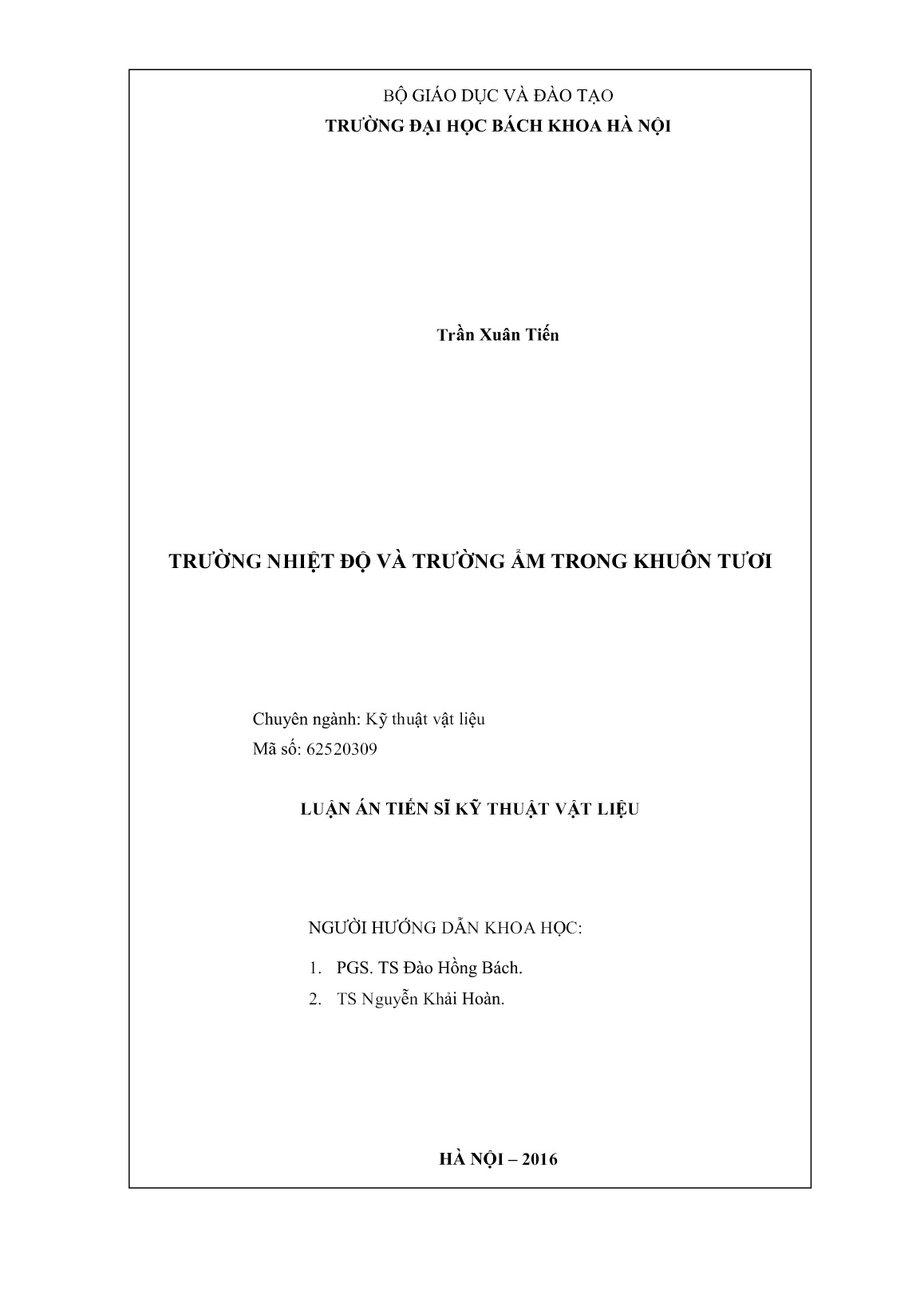
Trang 2
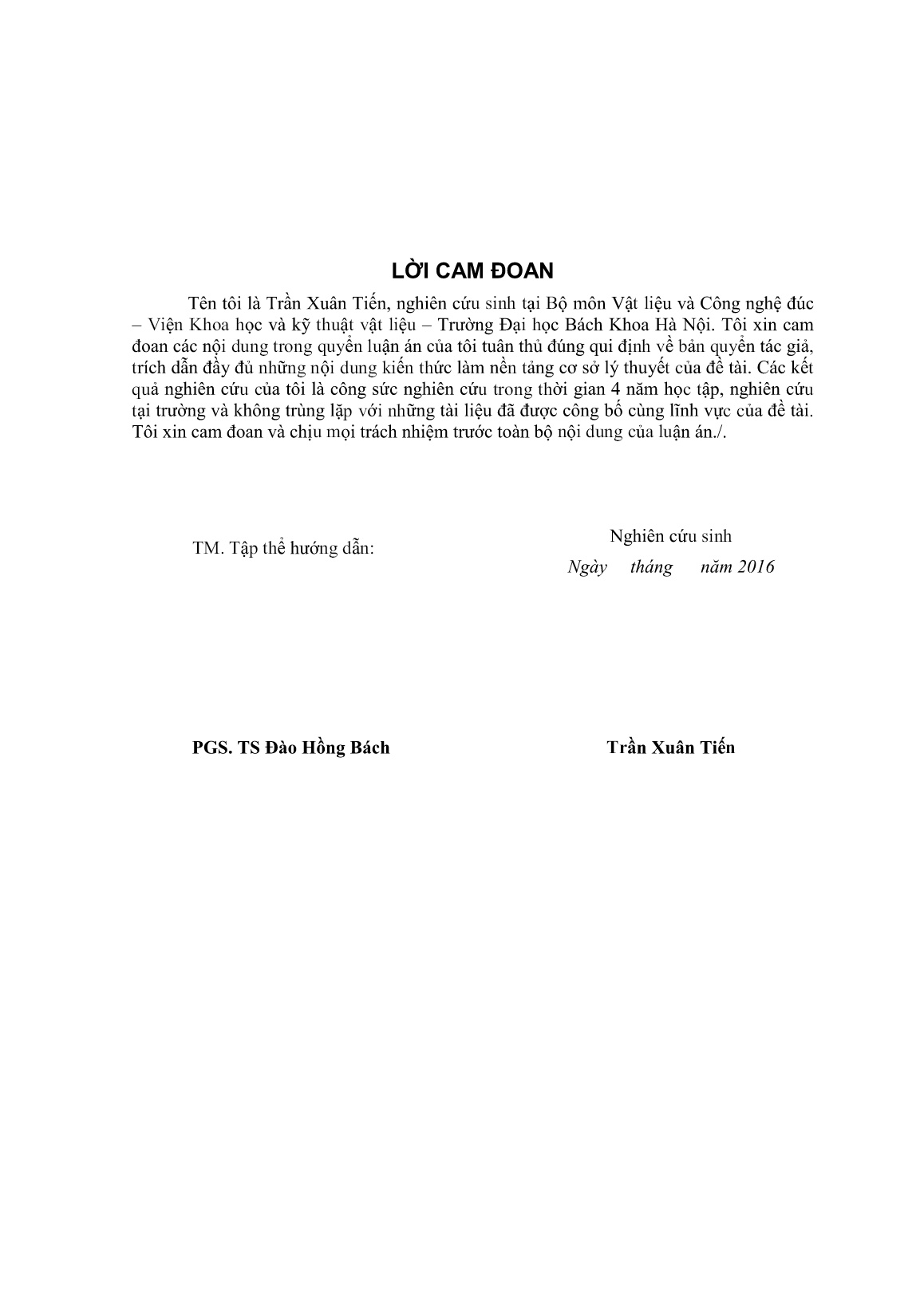
Trang 3
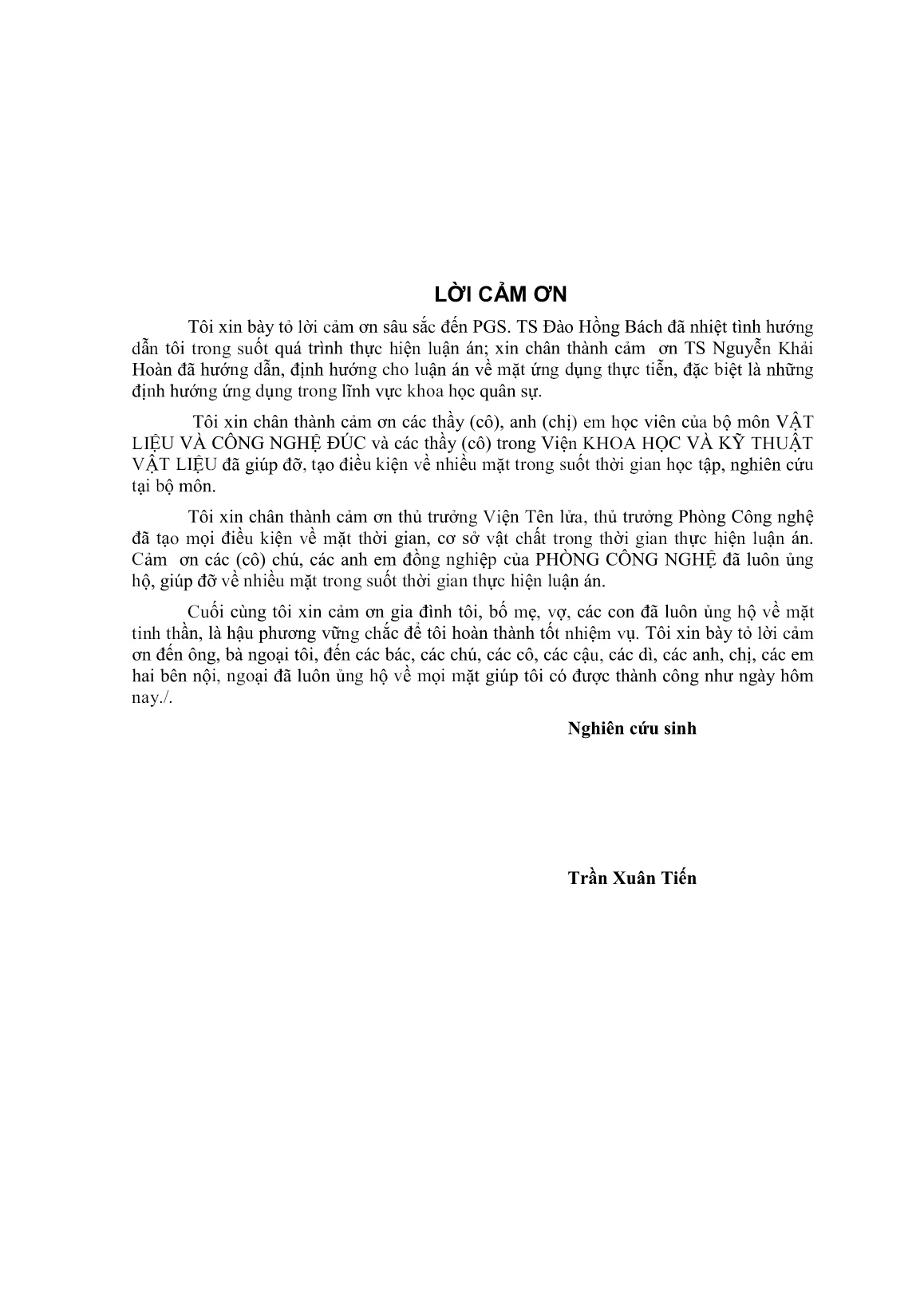
Trang 4
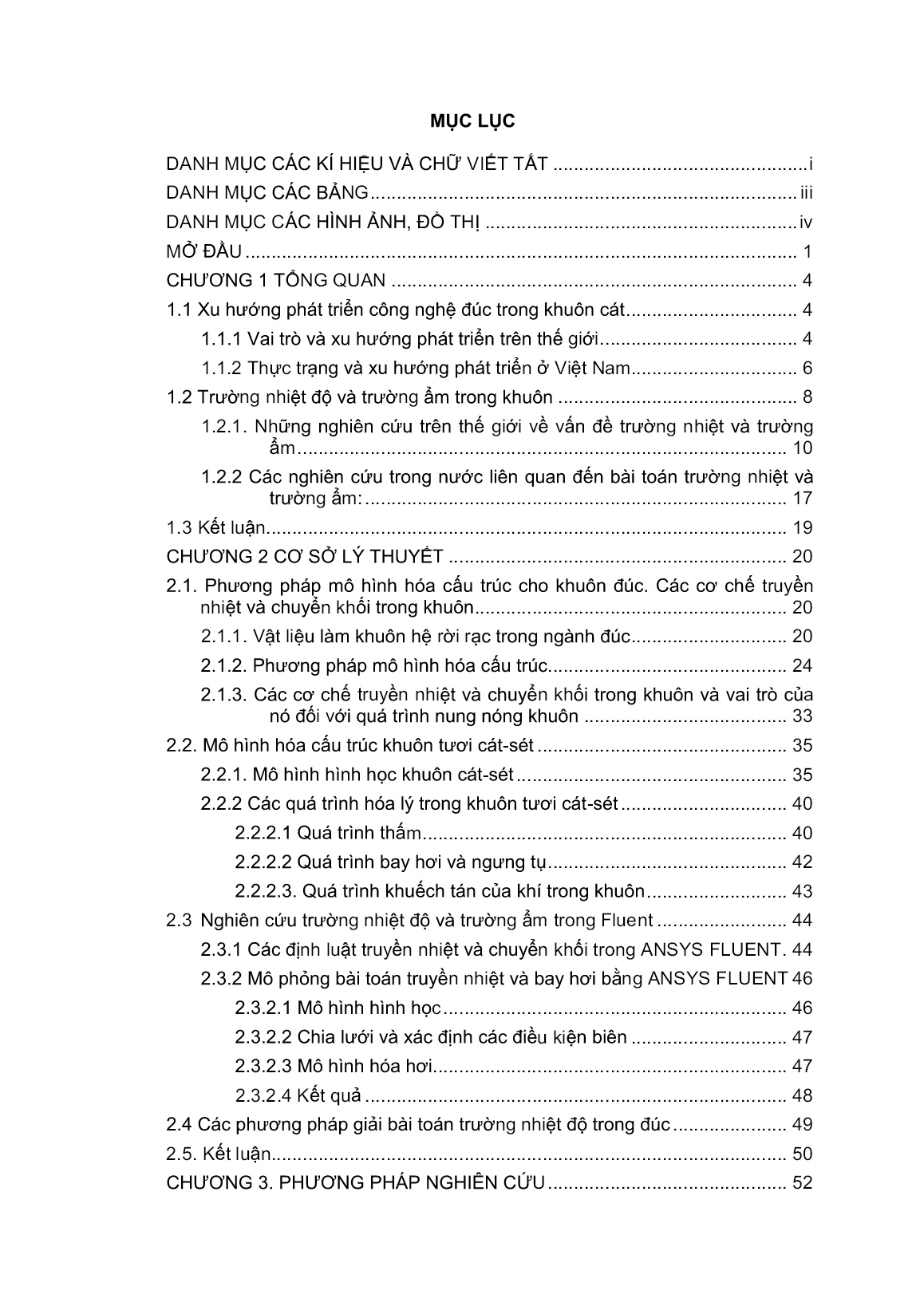
Trang 5
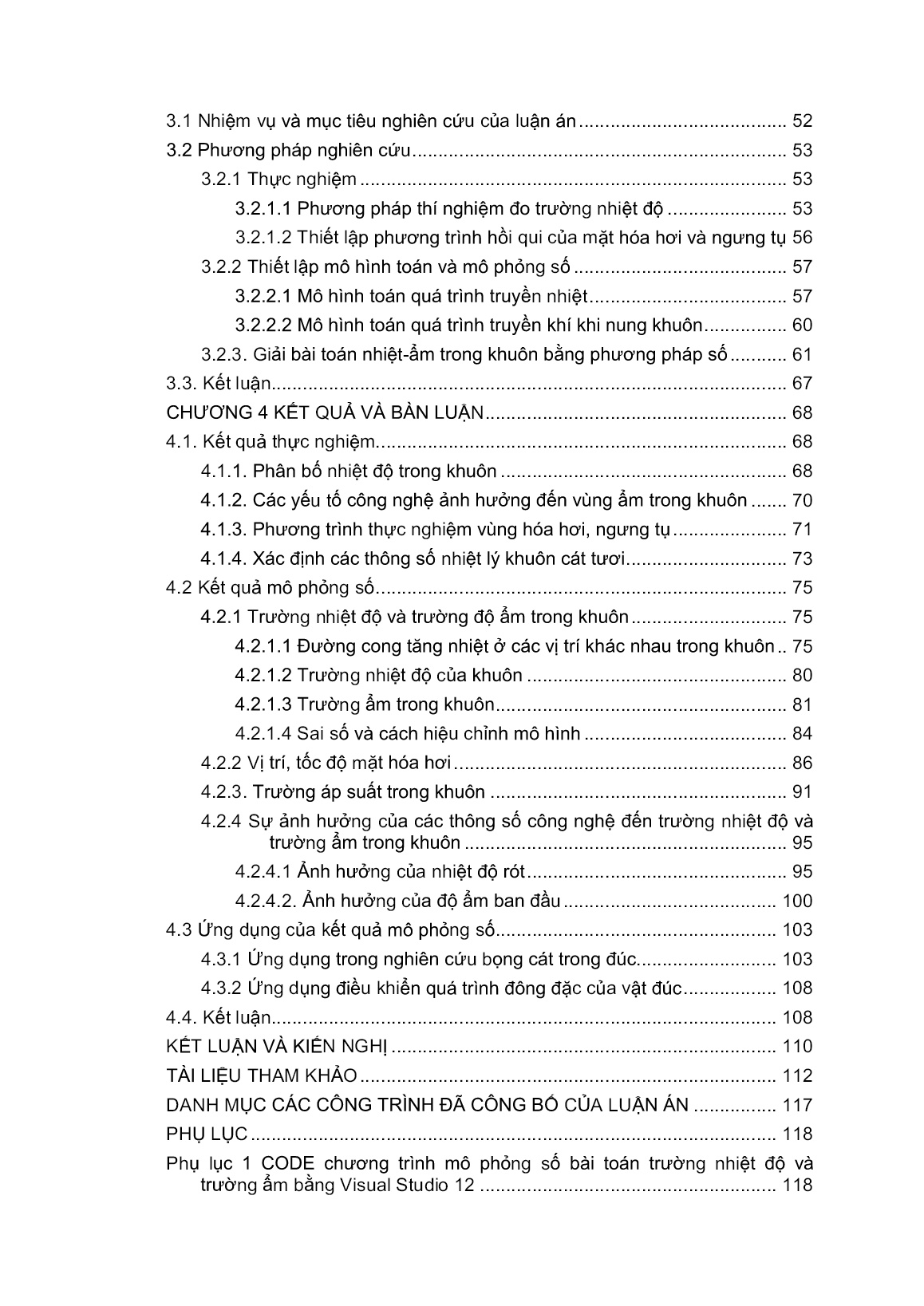
Trang 6
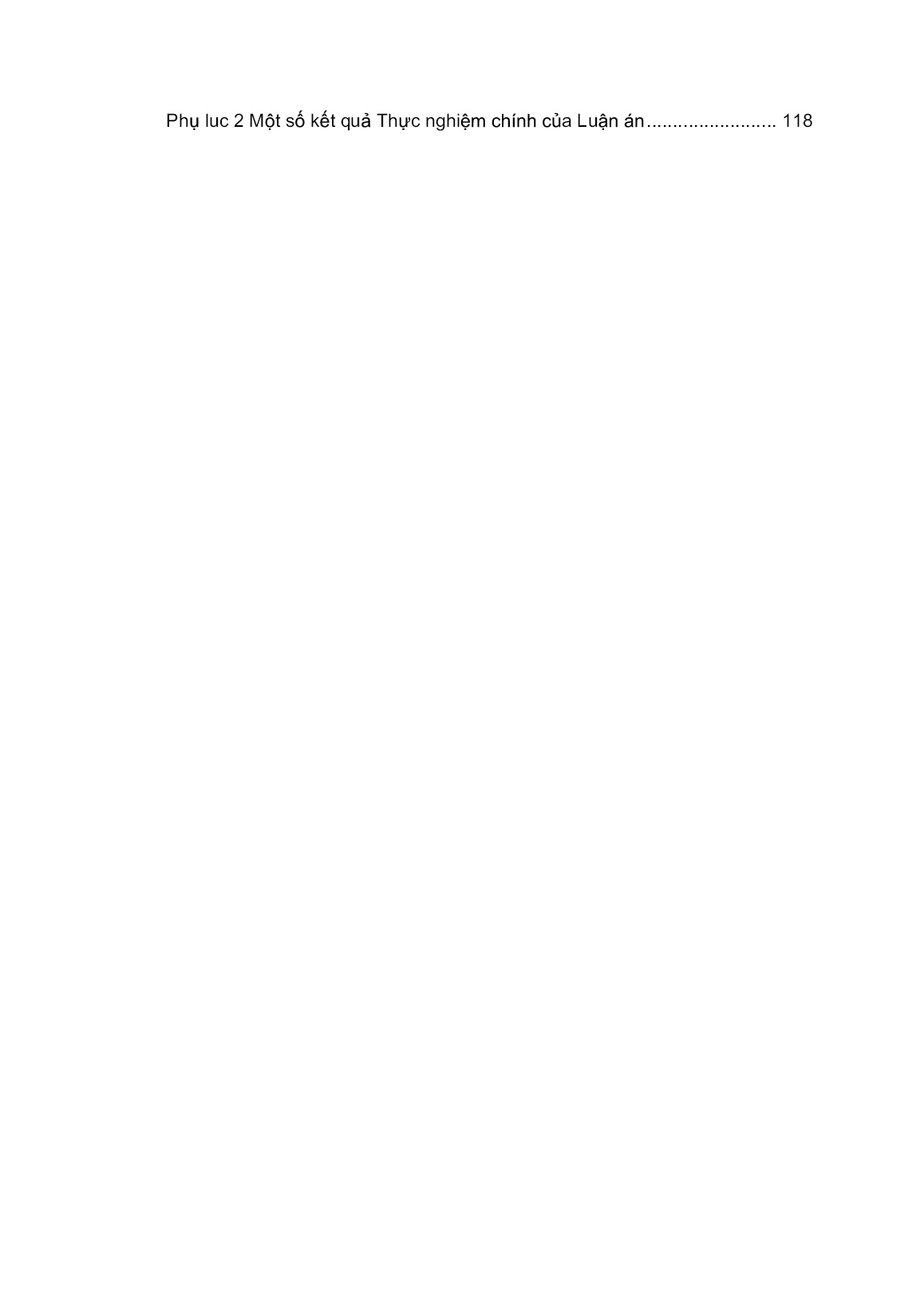
Trang 7
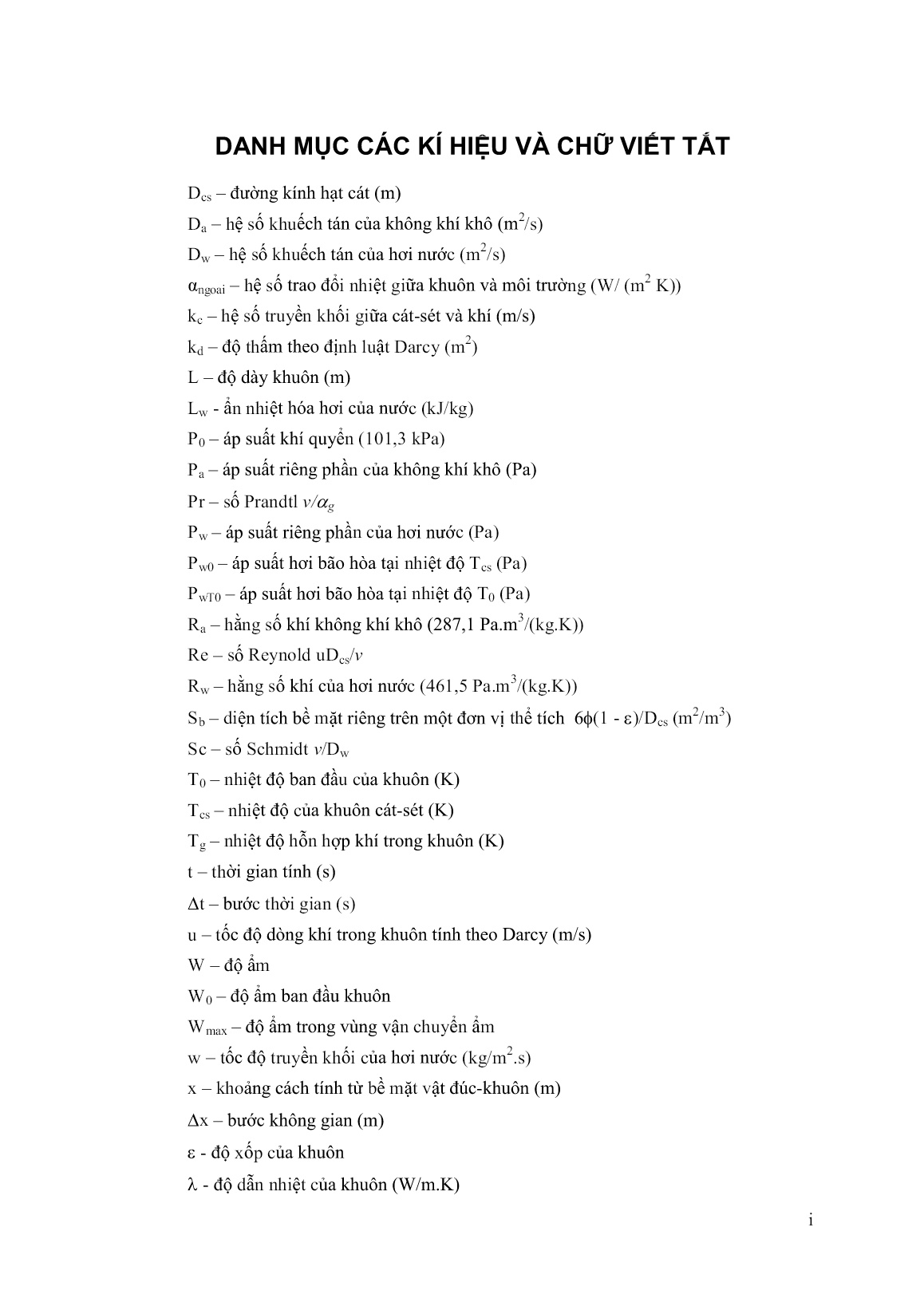
Trang 8
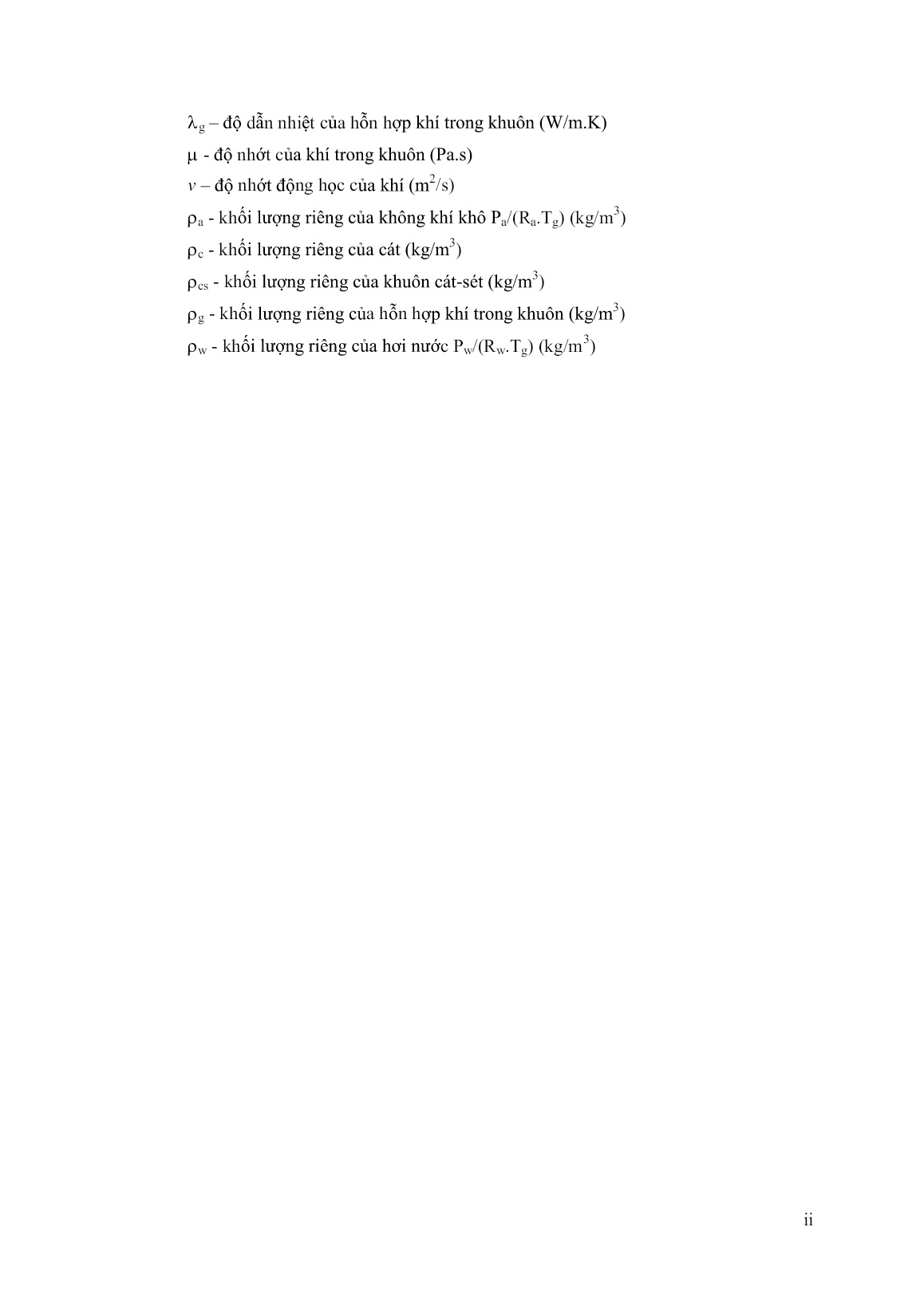
Trang 9
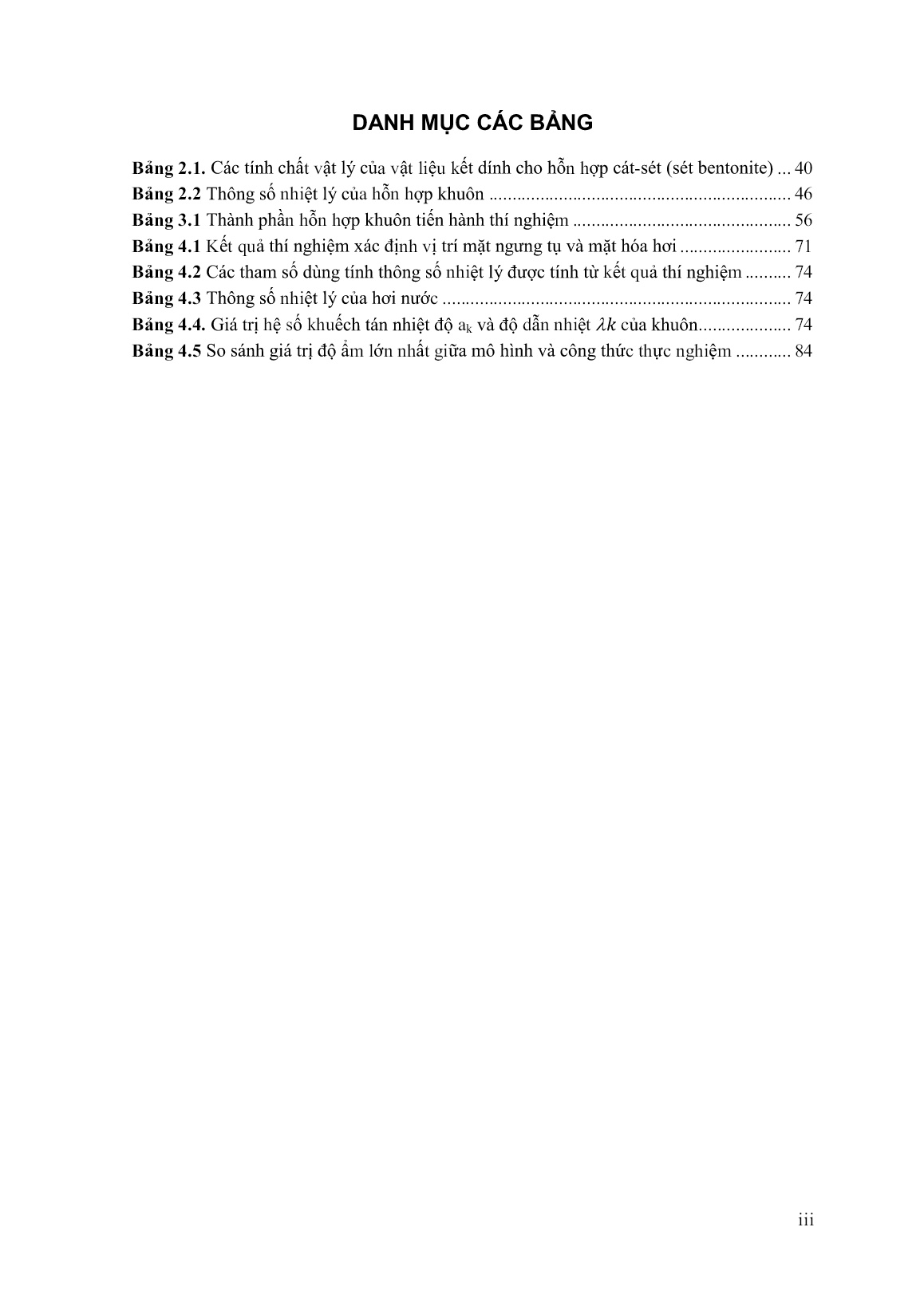
Trang 10
Tải về để xem bản đầy đủ
Bạn đang xem 10 trang mẫu của tài liệu "Luận án Trường nhiệt độ và trường ẩm trong khuôn tươi", để tải tài liệu gốc về máy hãy click vào nút Download ở trên.
Tóm tắt nội dung tài liệu: Luận án Trường nhiệt độ và trường ẩm trong khuôn tươi
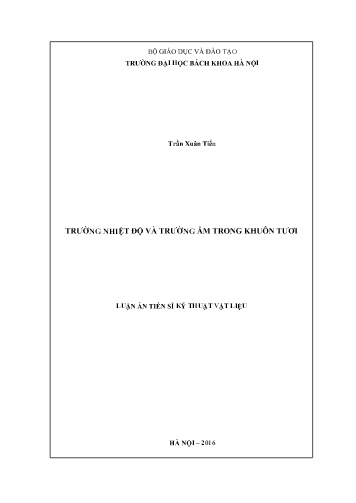
cát-sét 2.2.1. Mô hình hình học khuôn cát-sét Trên cơ sở phân tích những mô hình cấu trúc với hệ phân tán, trên cơ sở những nghiên cứu trong các công trình [75, 77, 86] với vật liệu làm khuôn thì hỗn hợp khuôn cát sét có thể đƣợc biểu diễn dƣới dạng tổ hợp của các thành phần sau – các hạt nền (cát SiO2) có đƣờng kính d đƣợc bao trong vỏ chất kết kính (sét bentonite) có chiều dày 0 (hình 2.16): Hình 2.16 Mô hình cấu trúc hỗn hợp làm khuôn cát-sét (a) và các thành phần của nó (b) Với mô hình này khoảng trống giữa các hạt cát đƣợc điền đầy không khí, khi đó ta coi cát và sét là một phần tử, không khí trong khuôn là hỗn hợp của không khí khô và hơi nƣớc. Khi đó độ xốp sẽ đƣợc thông qua khối lƣợng riêng của cát-sét cs, khối lƣợng riêng của khí kho, và khối lƣợng riêng hiệu dụng của khuôn hd tính theo công thức sau: (2.17) Tuy nhiên mô hình này chỉ dùng để nghiên cứu quá trình nhiệt trong trƣờng hợp không dầm chặt hỗn hợp làm khuôn vì nó không phản ánh đƣợc sự phân bố không đều của lớp chất dính sau khi đã dầm chặt; ở trạng thái không dầm chặt thì diện tích mặt tiếp xúc giữa các hạt cát-sét là rất nhỏ, khác xa so với ở trạng thái dầm chặt. Hình 2.17 Hình dạng của phần tử hỗn hợp làm khuôn ở nhưng giai đoạn hình thành khác nhau: a – hỗn hợp chưa dầm chặt; b – hỗn hơp sau khi dầm chặt. 36 Để nghiên cứu một cách tốt hơn quá trình nhiệt trong hệ khuôn cát-sét có dầm khuôn ta nghiên cứu cấu trúc của khuôn gồm hai giai đoạn cấu thành nhƣ sau [64]: 1. quá trình hình thành hỗn hợp không dầm chặt khi mà các hạt đƣợc phủ kín bởi một lớp chất kết dính có chiều dày 0 đƣợc phân bố đồng đều trên toàn bộ hạt có hình dạng cầu (hình 2.17 a); 2. quá trình tạo thành hỗn hợp làm khuôn đƣợc dầm chặt, nó xảy ra khi có sự biến dạng chất kết dính bao xung quanh hạt cát, chính vì vậy nó làm cho bán kính hiệu dụng r của phần tử cát-sét giảm đi một lƣợng và lƣợng dƣ của chất kết dính bị ép tràn ra vùng tiếp xúc gần đó (hình 2.17 b); mức độ biến dạng trên toàn bộ mặt tiếp xúc là nhƣ nhau. Để tính tham số 0 (chiều dày lớp kết dính ở giai đoạn đầu) đƣợc thực hiện bằng việc tính phƣơng trình cân bằng khối lƣợng đối với hỗn hợp và chất nền (cát) với chất kết dính. Gọi Xs là tỷ lệ thành phần của sét trong hỗn hợp, mc là khối lƣợng của cát, ms là khối lƣợng của sét trong hỗn hợp chƣa dầm chặt, khi đó Xs đƣợc tính nhƣ sau: (2.18) có thể đƣợc viết ở dạng: (2.19) trong đó Vs, s và Vc, c – tƣơng ứng là thể tích và khối lƣợng riêng của chất kết dính (sét) và chất nền (cát). Với giả thiết về sự phân bố hoàn toàn và đồng đều của chất kết dính giữa các hạt nền và hạt dạng cầu (hình 2.17 a), ta tính lại thể tích chất kết dính trên một hạt nhƣ sau: ( ) ( ) (2.20) Mặt khác đối với lớp vỏ chất kết dính của hình cầu thể tích của nó đƣợc tính nhƣ sau: (( ) ) (2.21) Từ hai biểu thức trên biến đổi cuối cùng ta có công thức tính chiều dày chất kết dính nhƣ sau: (√ ( ) ) (2.22) Khi dầm chặt hỗn hợp làm khuôn (giai đoạn thứ hai) các phần tử bị biến dạng (hình 2.17 b). Giá trị biến dạng tuyến tính của toàn bộ phần tử khi đó là , giá trị biến dạng củ phần tử là - k=/r. Từ đó ta thấy rằng khi ứng dụng thiết bị gia lực ép trong ngành đúc phải đảm bảo không làm biến dạng và phá hủy hạt cát, biến dạng tuyến tính tối đa của thiết bị có thể đạt giá trị 0, trong trƣờng hợp đó chất kết dính tiếp xúc trực tiếp với hạt nền (cát). Khi có sự biến dạng của phần tử thì phần thừa của chất kết dính sẽ tràn ra từ vùng tiếp xúc với của các phần tử sang vùng lỗ trống xung quanh, do đó làm giảm độ xốp và tăng diện tích tiếp xúc của hỗn hợp. Để thuận tiện cho việc mô tả sự biến dạng của chất dính trong vùng tiếp xúc ta đƣa vào tham số biến dạng tƣơng đối của lớp màng chất dính s, có tính đến sự thay đổi của nó từ 0 (hỗn hợp không dầm chặt) đến 1 (phần tử bị nén đến 37 tiếp xúc với chất nền-hạt cát), có thể đƣợc tính theo công thức sau: . Chiều dày nhỏ nhất của lớp màng chất dính ở phần giữa của vùng tiếp xúc bằng: ( ) (2.23) Với phần cạnh vùng tiếp xúc chiều dày lớp màng chất dính tăng dần cho đến khi đạt giá trị lớn nhất max, cao hơn hẳn chiều dày ban đầu 0. Để mô tả cấu trúc và quy luật phân bố nhiệt trong vật liệu làm khuôn dạng hạt có chất kết dính khi sử dụng giải pháp của G.N.Dulnhev cho việc phân chia phần tử liên kết trong cấu trúc hỗn độn của vật liệu dạng hạt [25] bằng việc hoàn thiện mô hình cấu trúc ô cơ sở, trong đó hạt cơ bản (hạt nền có đƣờng kính rc có lớp vỏ chất dính có chiều dày từ max đến (hình 2.18, a) và chứa đầy không khí trong các lỗ trống. Hình 2.18 Mô hình cấu trúc ô cơ sở của vật liệu làm khuôn qua dầm chặt: a – cấu trúc ô cơ sở; b – sơ đồ liên kết của trở nhiệt Ta đƣa vào một hệ kí hiệu mới để biểu diễn các thông số cấu trúc của bƣớc tạo khuôn thứ nhất nhƣ sau: ta sẽ kí hiệu thêm chỉ số phía trên là ―0‖, khi đó các tham số cấu trúc có dạng sau , ; các tham số cấu trúc của giai đoạn 2 sẽ đƣợc biểu diễn mà không có chỉ số trên. Nk – là số tọa độ; m22 – độ xốp cấu trúc bậc 2. Với các tham số đƣợc kí hiệu mới đó ta có thể viết các công thức tính tham số cho hệ khuôn nhƣ sau [25]: √( ) ; (2.24) √ √ . (2.25) Với giả thiết rằng khi biến dạng không làm thay đổi số tọa độ, khi đó ta có . Với hệ biến dạng thì bán kính tƣơng đối y4 của mô hình giảm dân so với giá trị ban đầu nhƣ sau: ( ). (2.26) Khi đánh giá thể tích bị ép ra khi biến dạng chất kết dính (dạng cầu) và thể tích của khối trụ có bán kính r2 và chiều cao √ (hình 2.18, a), là nhƣ nhau, ở dạng đó là vùng gần vùng tiếp xúc có dạng sau [28]: 38 √ ( ) √ . (2.27) Có tính đến htr nhƣ sau: √ . (2.28) Ta xét kích thƣớc bất kỳ của các tham số tiếp xúc yi tuyến tính theo quan hệ . Trong tài liệu [25] đã chỉ ra rằng độ xốp cuối cùng của hệ biến dạng m2 sẽ đƣợc biểu diễn qua giá trị k và sự thay đổi tƣơng đối của kích thƣớc bên ngoài của toàn bộ hệ - biến dạng hoàn toàn c (giả thiết rằng biến dạng xảy ra đồng thời với phần tử thuộc khung cốt và với chính khung cốt, và chúng tỷ lệ thuận với c). Vì sau khi nén ép vạt liệu làm khuôn giá trị m2 là một đại lƣợng chƣa biết, thuận lợi hơn khi biểu diễn độ xốp phụ thuộc vào giá trị k hoặc c. Việc xác định c đối với vật liệu làm khuôn không quá phức tạp và có thể nhận đƣợc giá trị khi ta đo các kích thƣớc tuyến tính trƣớc và sau khi dầm nén. Đối với m2, với độ xốp khung cốt ở trạng thái biến dạng m2k, với độ xốp cấu trúc bậc hai m22 và với c ta nhận có: ( √ √ ) ; (2.29) √ √ ; (2.30) ( ) ; (2.31) ( ) . (2.32) Độ dẫn nhiệt của cấu trúc ô cơ sở, áp dụng dƣới dạng hình trụ có bán kính r4 (hình 2.18, a) đƣợc xác định bằng cách sử dụng phƣơng pháp phân chia nó thành các mặt đoạn nhiệt và đẳng nhiệt cùng với việc tìm các trở nhiệt riêng sau đó (hình 2.18, b). Dòng nhiệt đi vào nền dƣới của phần tử, vƣợt qua trở nhiệt lớp chất kết dính R1, tiếp đó đi qua hạt nền (cát) và chảy dọc theo nền, khi đó nó vƣợt qua trở nhiệt R2. Song song với điều đó dòng nhiệt đi vào vƣợt qua trở nhiệt R3 của lỗ trống không khí dạng cầu có phần tiếp giáp với phần tử nằm trên đƣờng đẳng nhiệt AB và hạn chế từ bên phải bởi đƣờng đoạn nhiệt CB (hình 2.18, a). Sau khi đi qua phần có trở nhiệt R3 thì dòng nhiệt đƣợc phân bố trên hạt nền (cát) có trở nhiệt R4 và song song với nó là lớp vỏ chất kết dính trở nhiệt (R5).Song song với toàn bộ cách phân bố dòng nhiệt đƣợc mô tả ở trên thì sự dẫn nhiệt còn xảy ra trong các lỗ trống xuyên suốt có trở nhiệt R6. Đối với tổng trở nhiệt R của tất cả phần tử liên kết, ta biểu diễn nó thông qua độ dẫn nhiệt hiệu dụng của khung cốt k, đƣợc viết nhƣ sau: ( ) . (2.33) 39 Giả thiết rằng chiều dầy chất kết dính tăng tuyến tính từ giá trị đến max, khi đó R1 có thể đƣợc viết ở dạng sau: ( ) , (2.34) trong đó s – là độ dẫn nhiệt của chất kết dính (sét). Với R2 ta có: , (2.35) trong đó c – là độ dẫn nhiệt của hạt nền (cát); - là hàm dòng phân tán của dòng nhiệt, trong trƣờng hợp này ta có thể lấy gần đúng bằng giá trị sau: . (2.36) Với trở nhiệt R3 khi sử dụng lý thuyết đƣợc trình bày trong tài liệu [57], với điều kiện ta chỉ tính trở nhiệt lớn nhất của lớp không khí, khi đó ta có thể viết nhƣ sau: ( )(√ √ √ √ ) , (2.37) trong đó hệ số tổ hợp đƣợc tính theo công thức (2.8), hệ số dẫn nhiệt hiệu dụng của khí trong khe hở dạng cầu kc, có tính đến sự dẫn nhiệt phân tử và dẫn nhiệt bức xạ, đƣợc tính theo công thức sau: ( ) ̅̅ ̅̅ ̅̅ ̅̅ ( ). (2.38) Với R4, R5 và R6 đƣợc tính theo công thức sau: √ ( ) ( ) ; (2.39) √ ( ) (( ) ( ) ) (2.40) ( ) (2.41) trong đó hệ số dẫn nhiệt hiệu dụng trong lỗ trống suốt 2cn tìm đƣợc bằng cách tƣơng tự nhƣ với kc. Dựa vào sơ đồ liên kết của các trở nhiệt (hình 2.18, b) và từ công thức (2.33) dùng cho k ta có: ( )( ) . (2.42) Nhiệt dung riêng của cát-sét đƣợc tính nhƣ sau: ( ) (2.43) trong đó cs và cc – tƣơng ứng là nhiệt dung riêng của chất kết dính (sét) và chất nền (cát). 40 Bảng 2.1. Các tính chất vật lý của vật liệu kết dính cho hỗn hợp cát-sét (sét bentonite) Tên gọi thông số Kí hiệu Giá trị hoặc công thức tính Đơn vị tính Tài liệu Độ dẫn nhiệt s 49,239- 0,061T+2,015.10 5 T 2 W/(mK) [2] Khối lƣơng riêng s 2600 kg/m 3 [10] Các hệ số trong phƣơng trình (c=a+bT-cT -2) dùng cho nhiệt dung riêng a b c 40,79 4,763.10 -3 9,928.10 5 -------- [88] 2.2.2 Các quá trình hóa lý trong khuôn tƣơi cát-sét 2.2.2.1 Quá trình thấm Nƣớc có trong khuôn (hàm lƣợng <15%) tồn tại ở dạng riêng biệt, không liên kết thành cụm với nhau, nƣớc trong khuôn không chảy đƣợc, nó chỉ có thể chuyển động khi ở trạng thái hơi [63], nói một cách khác là không khí và hơi nƣớc tạo thành hơi nhiệt động trong khuôn. Vì vậy theo [67, 80] quá trình có vai trò quan trọng đối với hệ vật đúc – khuôn chính là lý thuyết thấm. Sự thấm là sự chuyển động của chất lỏng, khí hoặc chất lỏng khí hóa trong môi trƣờng xốp. Môi trƣờng xốp hoặc vật thể xốp là pha rắn, bị đâm xuyên bởi một số lƣợng lớn các lỗ trống liền nhau. Vật thể đó thuộc nhóm cấu trúc biểu hiển rõ cấu trúc dị pha. Sự chuyển động của chất lỏng, khí hoặc chất lỏng dạng hơi (từ đây về sau chỉ gọi đơn giản là khí) trong không gian xốp của vật xốp là đặc biệt phức tạp. Đặc trƣng ngẫu nhiên về hình dạng và sự phân bố của tƣng lỗ xốp đã loại bỏ khả năng mô tả một cách chặt chẽ chuyển động của khí trong nó. Nghiệm thủy khí chính xác của bài toán cũng không thể tìm đƣợc thậm chí với hệ đƣợc hình thành bởi các phần tử dạng cầu đƣợc sắp xếp theo hệ thống có kích thƣớc nhƣ nhau (còn gọi là vật thể phân tán đơn). Tốc độ thấm tại điểm cho trƣớc của vật thể đƣợc xác định nhƣ là tỷ lệ của sự tiêu hao thể tích tích thực của khí trên diện tích mà thông qua nó quá trình thấm diễn ra, (2.44) Phƣơng trình liên tục biểu diễn định luật bảo toàn khối lƣợng trong ngành thủy động lực học. Nghiên cứu hình hộp chữ nhật vô cùng nhỏ từ vật liệu xốp, sự phân bố của hình hộp trong hệ tọa độ nhƣ đã chỉ ra trên hình 2.19 [98]. Giả thiết rằng, trong thể tích dV=dxdydz của vật thể đƣợc xét đến có tác động của nguồn khối lƣợng có cƣờng độ . Nếu qua mặt bên trái của hình hộp có dòng vật chất di chuyển qua q(x,t) thì qua bề mặt nằm cách khoảng dx sẽ có dòng ra q(x+ x, t). Khai triển hàm q(x+ x, t) theo dãy Taylor và giới hạn bởi hai số hạng đầu tiên, khi đó ta có: ( ) ( ) ( ) . (2.45) 41 Hình 2.19 Mô hình chuyển khối xét trong một phần tử dạng hình hộp chữ nhật Sự thay đổi khối lƣợng vật chất trong thể tích dV sau khoảng thời gian dt ( ) * ( ) ( ) + . (2.46) Sự thay đổi khối lƣợng của chất thấm trong thể tích dV sẽ gây ra một gia lƣơng tƣơng ứng của mật độ. Theo đó , (2.47) trong đó - là mật độ; - là độ xốp. Từ biểu thức (2.46) và (2.47) suy ra . (2.48) Phƣơng trình (2.48) nhận đƣợc là phƣơng trình liên tục của dòng thấm trong trƣờng hợp một chiều. Nếu nhƣ quá trình thấm cũng xảy ra trong hƣớng y và z thì lập luận tƣơng tự sẽ đƣa đến phƣơng trình sau cùng nhƣ sau . (2.49) Trong trƣờng hợp tổng quát thì ( ), phƣơng trình (2.49) trong thủy động học có vai trò nhƣ phƣơng trình Fourie trong dẫn nhiệt: nhờ nó trƣờng vật lý của thế năng tƣơng ứng đƣợc mô tả. Phƣơng trình Darcy có thể đƣợc biểu diễn ở dạng: . (2.50) trong đó - trọng lƣợng riêng của chất thấm (N/m3); K - hệ số thấm (m/s); l – độ dài chênh áp. Tỷ lệ г đƣợc gọi là hệ số thẩm thấu theo chất tƣơng ứng (ví dụ khi thấm khí – hệ số thông khí, khi thấm nƣớc – hệ số thấm nƣớc). Tuy nhiên tính chất thấm của môi trƣờng xốp có đặc trƣng không phụ thuộc vào dạng chất lỏng. Với mục tiêu đó ngƣời ta thƣờng sử dụng quan hệ sau [88, 98]: , (2.51) hoặc г , (2.52 trong đó K – hệ số thấm (m4/(N.s)); г – hệ số thấm khí (độ thông khí), m/s; – độ nhớt động học (N.s/m2). Hệ số г đƣợc sử dụng phổ biến trong ngành đúc: giá trị của г đƣợc tính bằng cách thí nghiệm theo tiêu chuẩn cho hỗn hợp làm khuôn về độ thông khí. Việc chuyển từ đơn vị thông khí trong đúc dang đơn vị thông khí theo hệ SI đƣợc thực hiện theo quan hệ: 1 đv=0,017.10-6 m4/(N.s). 42 Bằng việc tính biểu thức (2.51) và (2.52) trong nghiên cứu lý thuyết phƣơng trình định luật Darcy thƣờng cho ta công thức sau: г ( ) , (2.53) hoặc ( ) , (2.54) trong đó ( ) – là gradient áp suất theo hƣớng pháp tuyến với bề mặt đẳng áp. Dƣới tác động của sai khác nhiệt độ lớp biên với vật đúc thì khí sẽ chuyển động đến điểm cuối của vùng nóng, còn ở lớp giữa thì chất khí chuyển đến điểm cuối vùng lạnh mao dẫn (hình 2.20) [70]. Sự luân chuyển khí này làm tăng áp suất ở vùng nóng của khuôn và phân chia hỗn hợp khí thành các phần riêng biệt. Hình 2.20 Quá trình chuyển động khí trong khuôn Khi đó các chất khí nhẹ sẽ bị tích tụ lại ở vùng nóng, còn các khí năng hơn ở vùng lạnh, điều này có nghĩa trong hỗn hợp không khí với hơi nƣớc thì vùng nóng của khuôn sẽ giàu hơi nƣớc hơn, còn vùng lạnh thì giàu không khí hơn (khối lƣợng nguyên tử của nƣớc là 18, không khí là 29). Hình 2.21 Áp suất riêng phần của hơi nước trong quá trình bay hơi và ngưng tụ 2.2.2.2 Quá trình bay hơi và ngƣng tụ Trong khuôn cát tƣơi có nƣớc với vai trò là chất kết dính của hỗn hợp làm khuôn, nó tồn tại trong khuôn ở dạng riêng biệt, cho nên quá trình luân chuyển khí rõ ràng phức tạp hơn vì trong quá trình thấm do nhiệt còn có quá trình bay hơi của nƣớc ở vùng nóng và ngƣng tụ hơi nƣớc ở vùng lạnh, quá trình khuếch tánKhi đó giá trị quan trọng lúc này là 43 độ ẩm tuyệt đối của khuôn W (tỷ lệ giữa lƣợng nƣớc chứa trong vật ẩm với khối lƣợng vật thể khô). Trong vùng nóng của khuôn áp suất của hơi nƣớc bão hòa cao hơn so với trong vùng lạnh. Khi luân chuyển theo vòng tròn thì ở lớp dọc trục đƣa một cách liên tục khí có lƣợng ẩm tăng từ vùng nóng sang vùng lạnh, còn ở lớp biên đƣa khí có lƣợng ẩm thấp từ vùng lạnh sang vùng nóng. Nhƣ vậy trong vùng nóng hơi nƣớc có áp suất nhỏ hơn áp suất bão hòa, còn trong vùng lạnh thì có áp suất lớn hơn áp suất hơi bão hòa (hình 2.21), khi đó nƣớc bay hơi trong vùng nóng và ngƣng tụ trong vùng lạnh. Tỷ phần bay hơi và ngƣng tụ đƣợc tính theo công thức sau [51, 54, 59]: (2.55) trong đó Pw0, Pw tƣơng ứng là áp suất hơi bão hòa và áp suất riêng phần hơi nƣớc nhiệt độ T (Pa); kc là hệ số truyền khối của hơi nƣớc ứng với điều kiện bay hơi và ngƣng tụ (m/s); Rw – là hằng số khí hơi nƣớc 461,5 Pa.m 3 / (kg.K). Hệ số truyền khối kc đƣợc tính theo bài toán dòng thông qua các chỉ số Reynolds và Schmidt nhƣ sau: ( ) (2.56) ( ) , (2.57) trong đó Dw – hệ số khuếch tán của hơi nƣớc (m 2 /s); Sc – số Schmidt; Re – chỉ số Reynold; - độ xốp; Dcs – đƣờng kính hạt cát-sét. 2.2.2.3. Quá trình khuếch tán của khí trong khuôn Sự bay hơi của nƣớc trong quá trình nung nóng khuôn làm cho hơi nƣớc bị đẩy (khuếch tán) vào các lớp sâu bên trong khuôn do áp suất dƣ trong vùng ngƣng tụ và tạo thành vùng ngƣng tụ trong khuôn. Lƣợng hơi nƣớc trong vùng ngƣng tụ đạt 90 99%, còn ở bề mặt tiếp xúc vật đúc gần nhƣ bằng 0. Hỗn hợp khí trong khuôn (hơi nƣớc+không khí) ngoài việc tuân theo định luật thấm, thì còn di chuyển trong khuôn bằng cơ chế khuếch tán [68, 69]. ( ) ( ) ( ) (2.58) trong đó C nồng độ hơi nƣớc trong khuôn (kg.mol/m3); D – hệ số khuếch tán hơi nƣớc (m 2 /s), hệ số khuếch tán của hơi nƣớc đƣợc xác định ( ) . Nồng độ hơi nƣớc phụ thuộc áp suất riêng phần của hơi nƣớc theo công thức sau: (2.59) thay phƣơng trình (2.59) vào phƣơng trình (2.58) ta đƣợc: ( ) ( ) ( ) (2.60) Qua nghiên cứu, phân tích cơ sở lý thuyết nhận thấy rằng, việc mô hình hóa cấu trúc có vai trò quan trọng trong quá trình mô phỏng quá trình đúc trong khuôn hệ rời rạc, đặc biệt đối với hệ khuôn cát-sét (có chất dính sét, liên quan đến độ dầm chặt khuôn). Dựa trên mô hình cấu trúc cho phép ta xác định đƣợc các thông số nhiệt lý của khuôn, các quá trình truyền nhiệt chuyển khối diễn ra trong khuôn. 44 Đối với khuôn tƣơi cát-sét, các quá trình hóa-lý xảy ra trong khuôn gồm quá trình truyền nhiệt dẫn nhiệt, đối lƣu; các quá trình bay hơi và ngƣng tụ của nƣớc trong khuôn; quá trình di chuyển của khí trong khuôn dƣới tác động của trƣờng nhiệt độ khuôn. Đây chính là nội dung quan trọng trong quá trình thiết lập mô hình toán cho bài toán trƣờng nhiệt độ và trƣờng ẩm trong khuôn 2.3 Nghiên cứu trƣờng nhiệt độ và trƣờng ẩm trong Fluent ANSYS FLUENT cung cấp mô hình tổng quát có khả năng giải quyết hàng loạt các vấn đề của dòng không nén đƣợc và nén đƣợc, dòng chảy tầng và chảy rối. Việc phân tích trạng thái ổn định hoặc tạm thời đều có thể thực hiện đƣợc. Trong ANSYS FLUENT, có nhiều mô hình toán học cho hiện tƣợng vận chuyển (nhƣ sự truyền nhiệt và các phản ứng hóa học) đƣợc tổ hợp với khả năng để mô hình hóa các mô hình hình học phức tạp. Fluent cho phép mô hình hóa dòng chảy và các bài toán liên quan đến hiện tƣợng vận chuyển trong các thiết bị công nghiệp và các quá trình công nghệ, các tính năng có ích khác nhau đều đƣợc cung cấp. Chúng bao hàm cả môi trƣờng xốp, các tham số chung (cánh quạt và bộ trao đổi nhiệt), dòng chảy xói-chu kỳ và sự truyền nhiệt, xoáy, và các mô hình của hệ tham chiếu chuẩn di động. Họ các hệ qui chiếu chuẩn di động của các mô hình bao hàm khả năng để mô hình hóa hệ qui chiếu chuẩn đơn pha hoặc đa pha. Phƣơng pháp chia lƣới theo trƣợt thời gian-chính xác, có ích để mô hình hóa bài toán đa pha ứng dụng trong máy tuabin, cũng cung cấp, mô hình cho mặt pha trộn để tính toán theo thời gian trung bình trong lĩnh vực dòng chảy. Một nhóm mô hình khác rất có ích trong ANSYS FLUENT là hệ thống các mặt tự do và các mô hình cho dòng đa pha. Chúng có thể đƣợc sử dụng để phân tích dòng khí- lỏng, khí-rắn, lỏng-rắn và khí-lỏng-rắn. Đối với các dạng vấn đề này, ANSYS FLUENT cung cấp các mô hình khác nhau nhƣ mô hình dòng khối (VOF), pha trộn và mô hình Ơ-le, cũng nhƣ cả mô hình pha rời rạc (DPM). Mô hình DPM sử dụng thuật toán Lagrange để tính cho pha phân tán (dạng hạt, giọt hay dạng bọt), bao gồm cả sự liên kết với các pha liên tục. 2.3.1 Các định luật truyền nhiệt và chuyển khối trong ANSYS FLUENT a) Quá trình nung nóng hoặc nguội (định luật 1 và 6) Sự nguội sẽ đƣợc hiểu là khi nhiệt độ phần tử nhỏ hơn nhiệt độ bay hơi theo định nghĩa, Tvap, và tỷ phần fv,0 của phần tử bị bay hơi. Các điều kiện này có thể đƣợc viết dƣới dạng [53, 59]: Định luật 1: Tp< Tvap (2.61) Định luật 6: mp ≤ (1-fv,0)mp,0 (2.62) trong đó Tp là nhiệt độ phần tử, mp,0 là khối lƣợng ban đầu của phần tử, và mp là khối lƣợng hiện tại. Khi đó cân bằng nhiệt độ liên quan đến nhiệt độ phần tử gồm có sự truyền nhiệt bằng đối lƣu và
File đính kèm:
luan_an_truong_nhiet_do_va_truong_am_trong_khuon_tuoi.pdf
1.1 Phu luc 1_ Code chuong trinh.pdf
1.2 Phu luc 2_So lieu TN.pdf
2. QUYEN TOM TAT LATS.pdf
3. Bia TOM TAT.pdf
4. INFORMATION ON NEW CONCLUSIONS.pdf
4. Thong tin ket luan moi LA.pdf