Luận án Nghiên cứu ảnh hưởng của vật liệu stone mastic ASPhalt đến khả năng chống lún vệt bánh xe và chống nứt mặt đường bê tông ASPhalt trong điều kiện Việt Nam
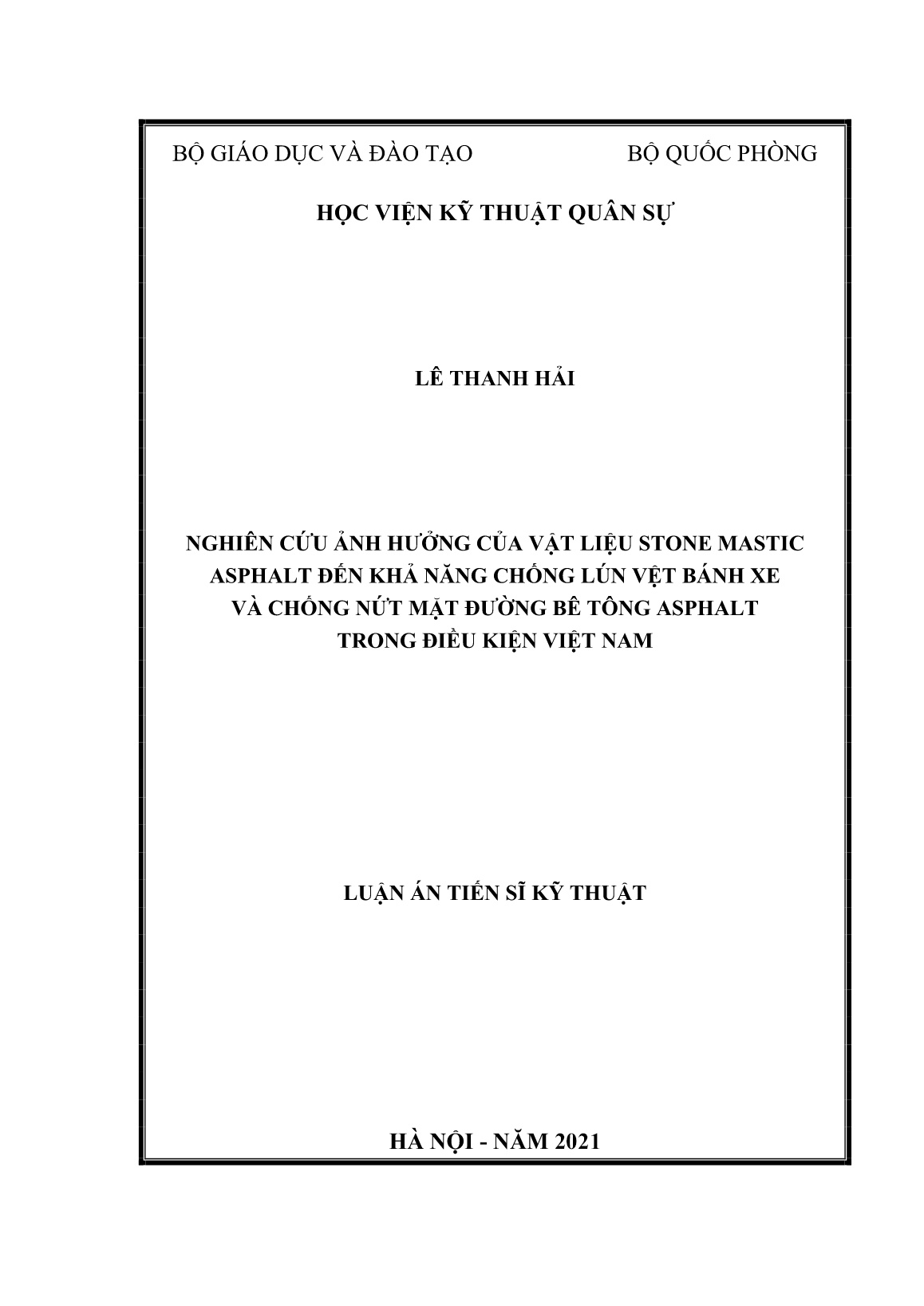
Trang 1
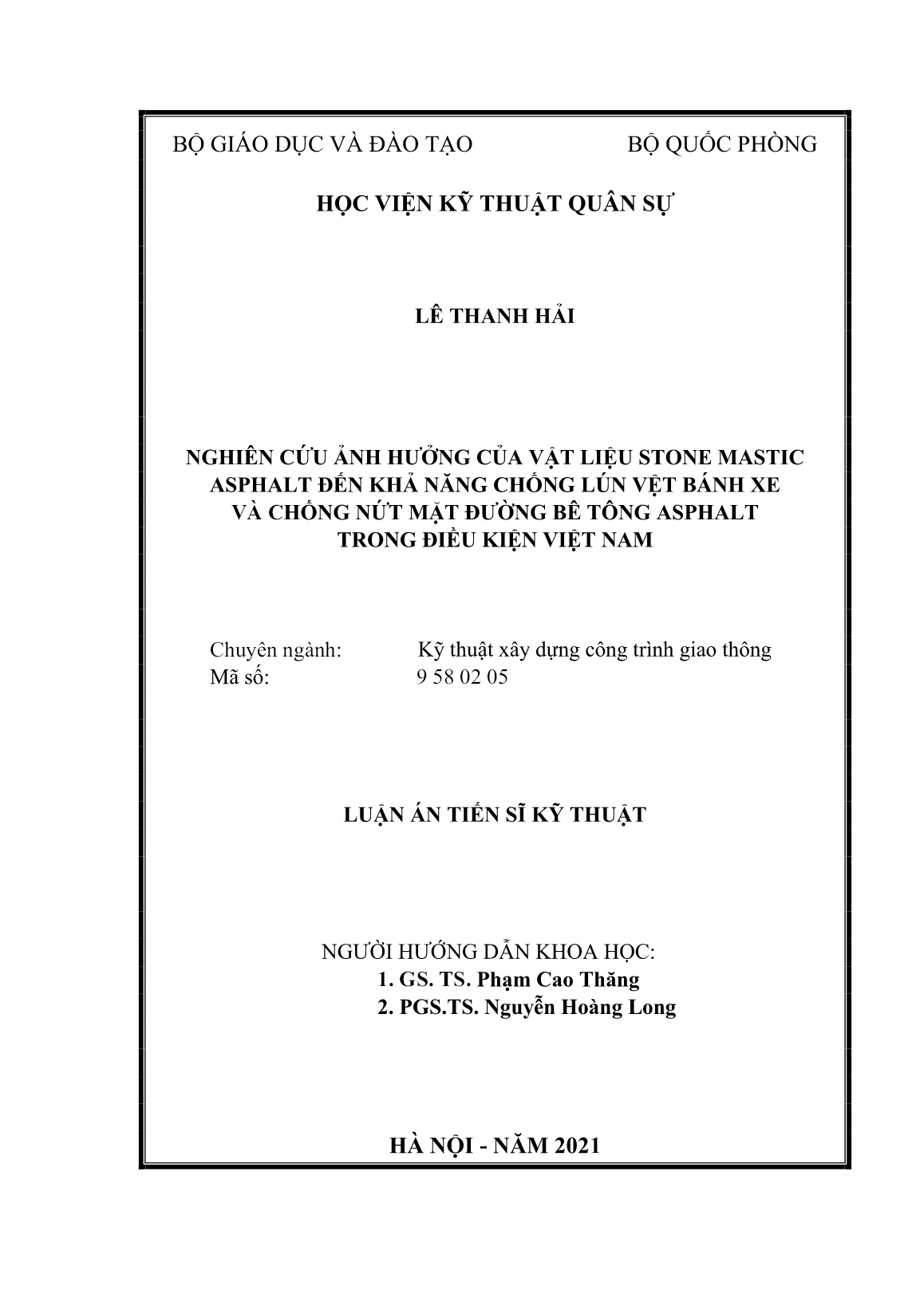
Trang 2
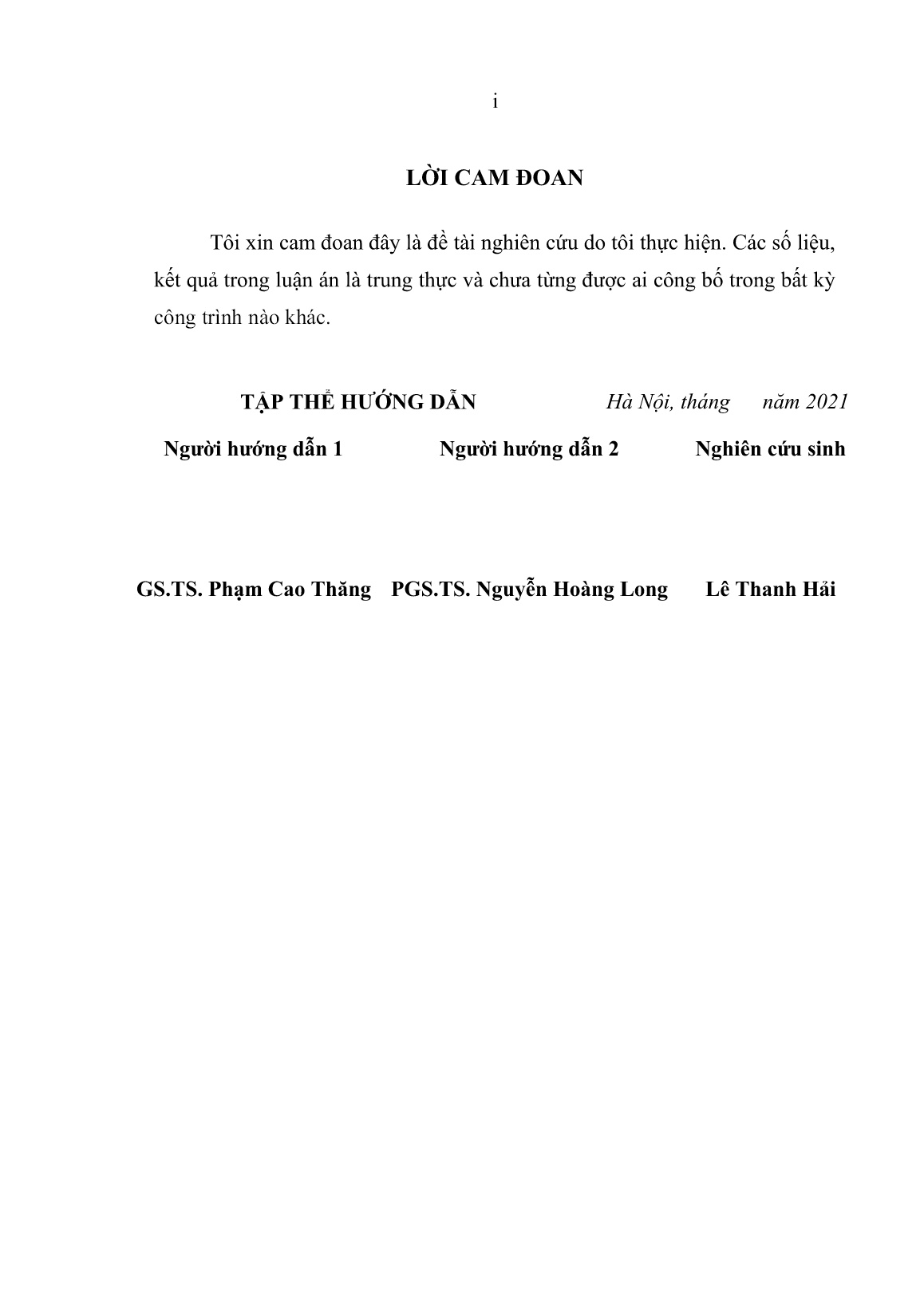
Trang 3
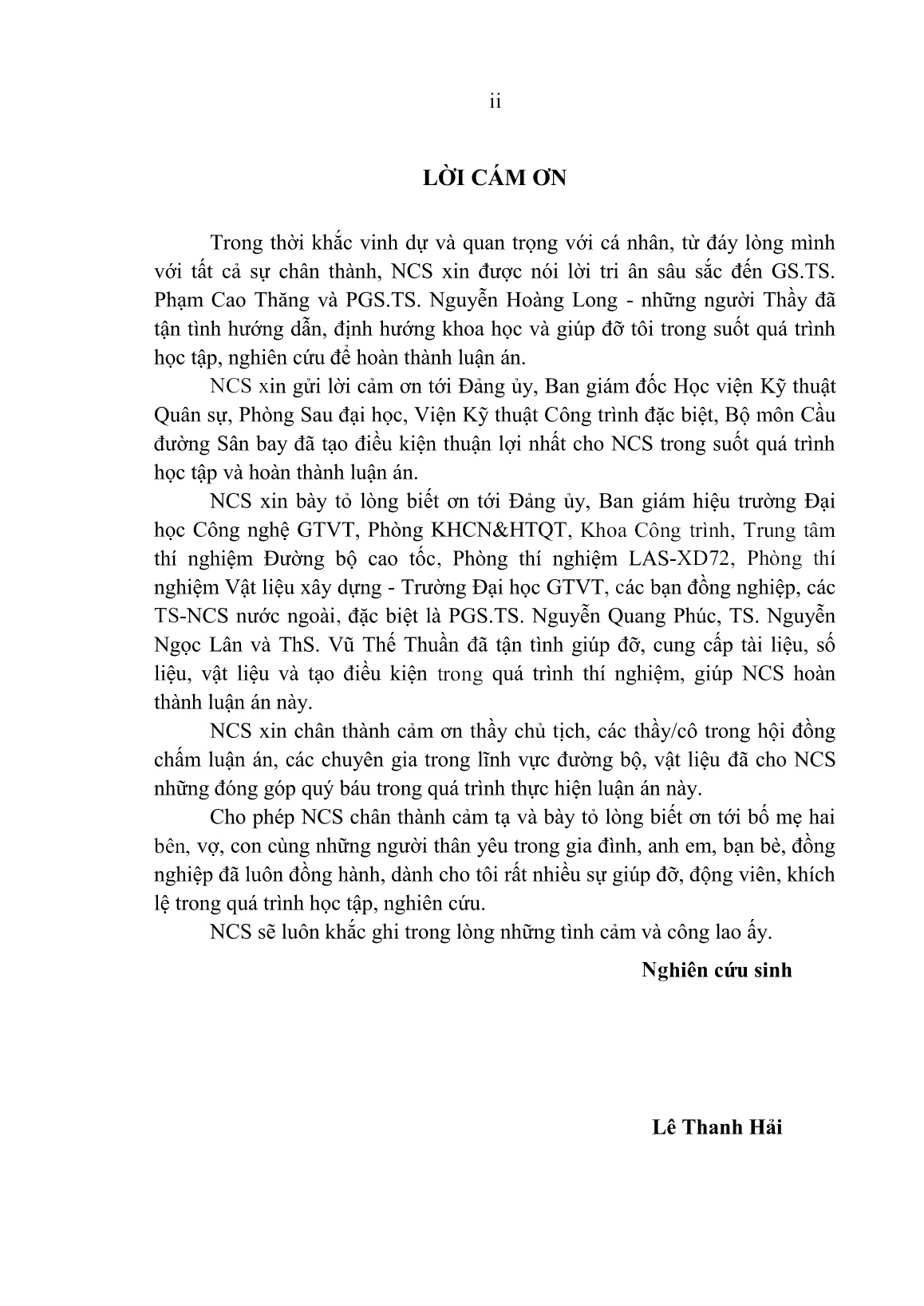
Trang 4
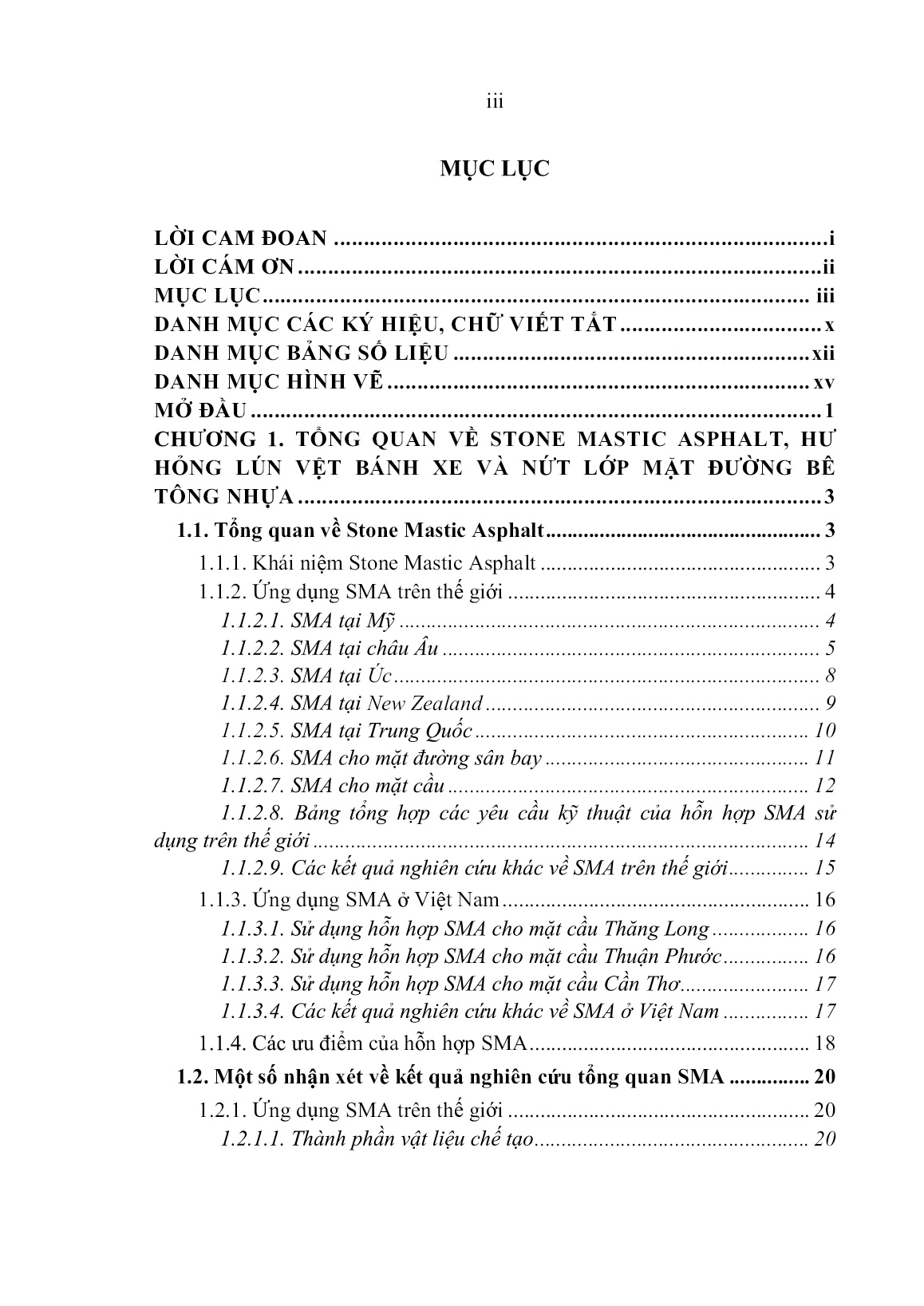
Trang 5
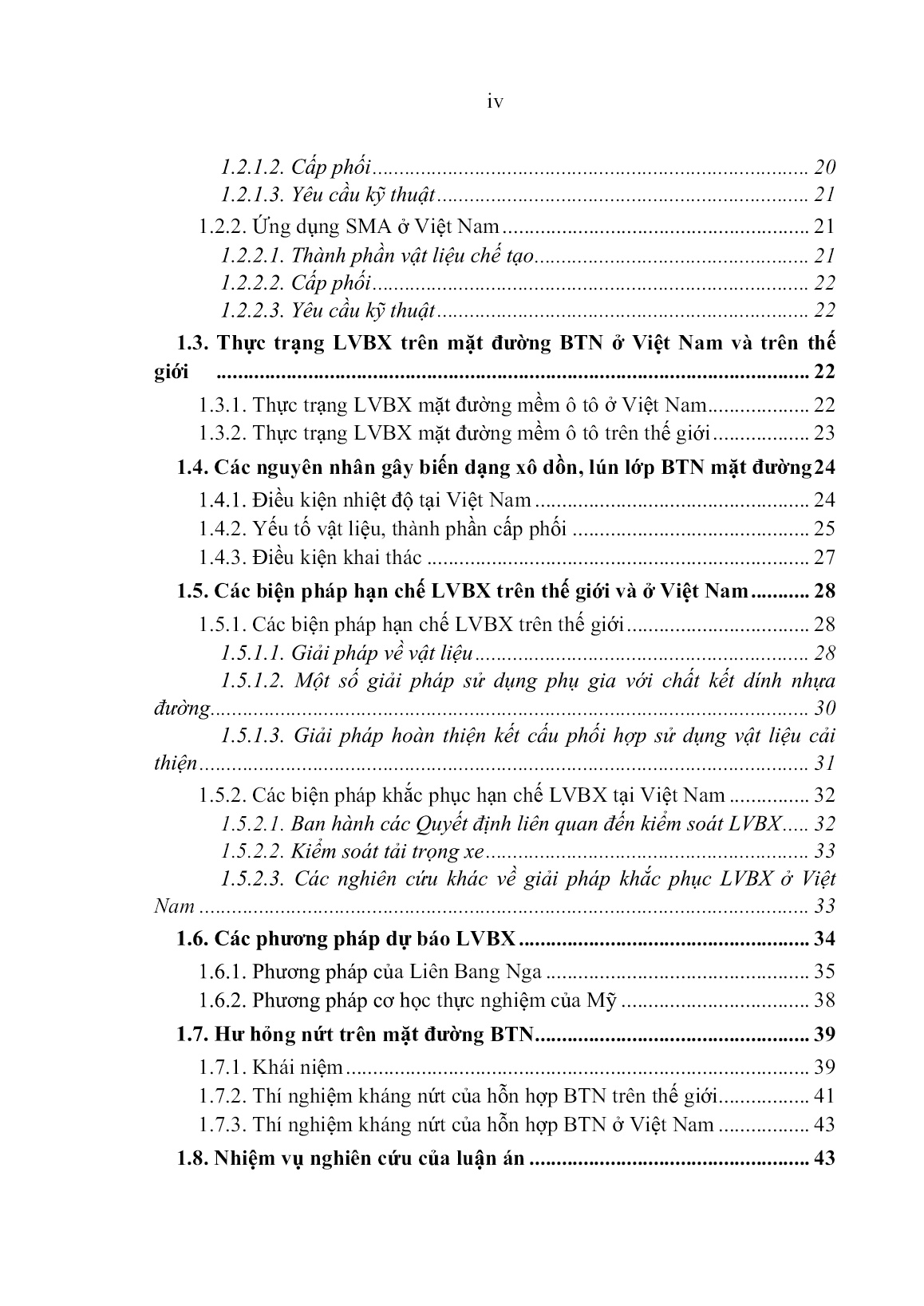
Trang 6
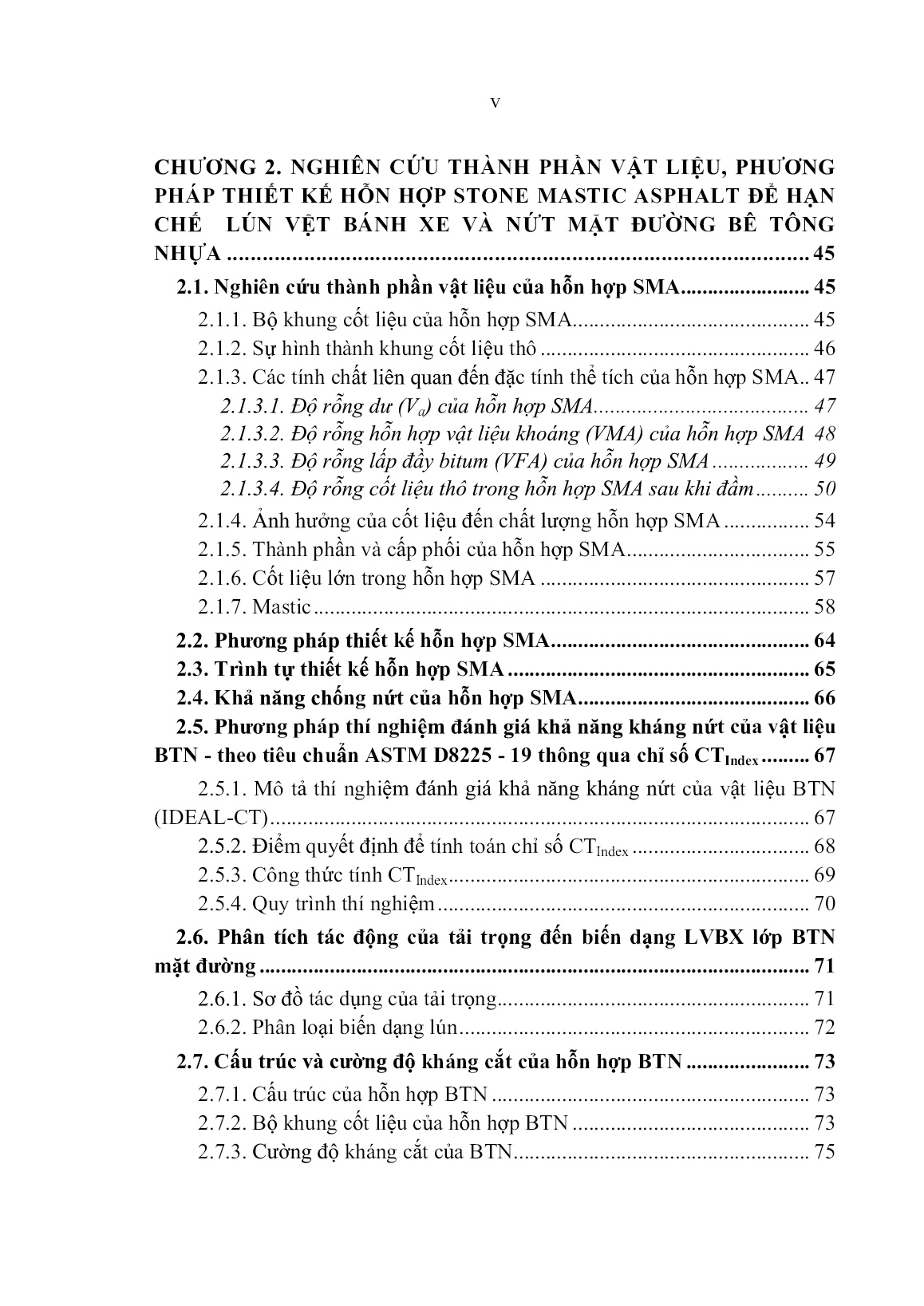
Trang 7
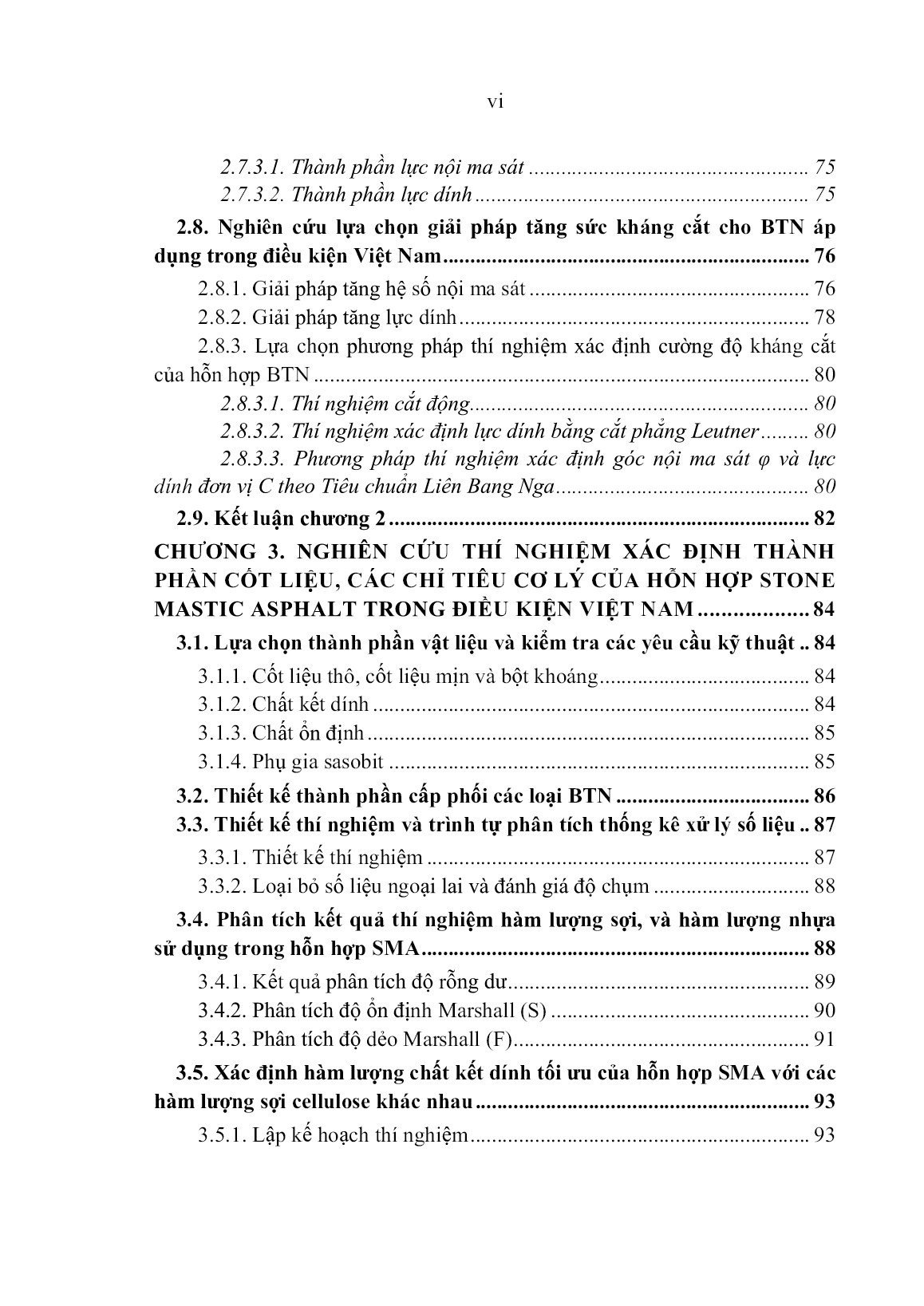
Trang 8
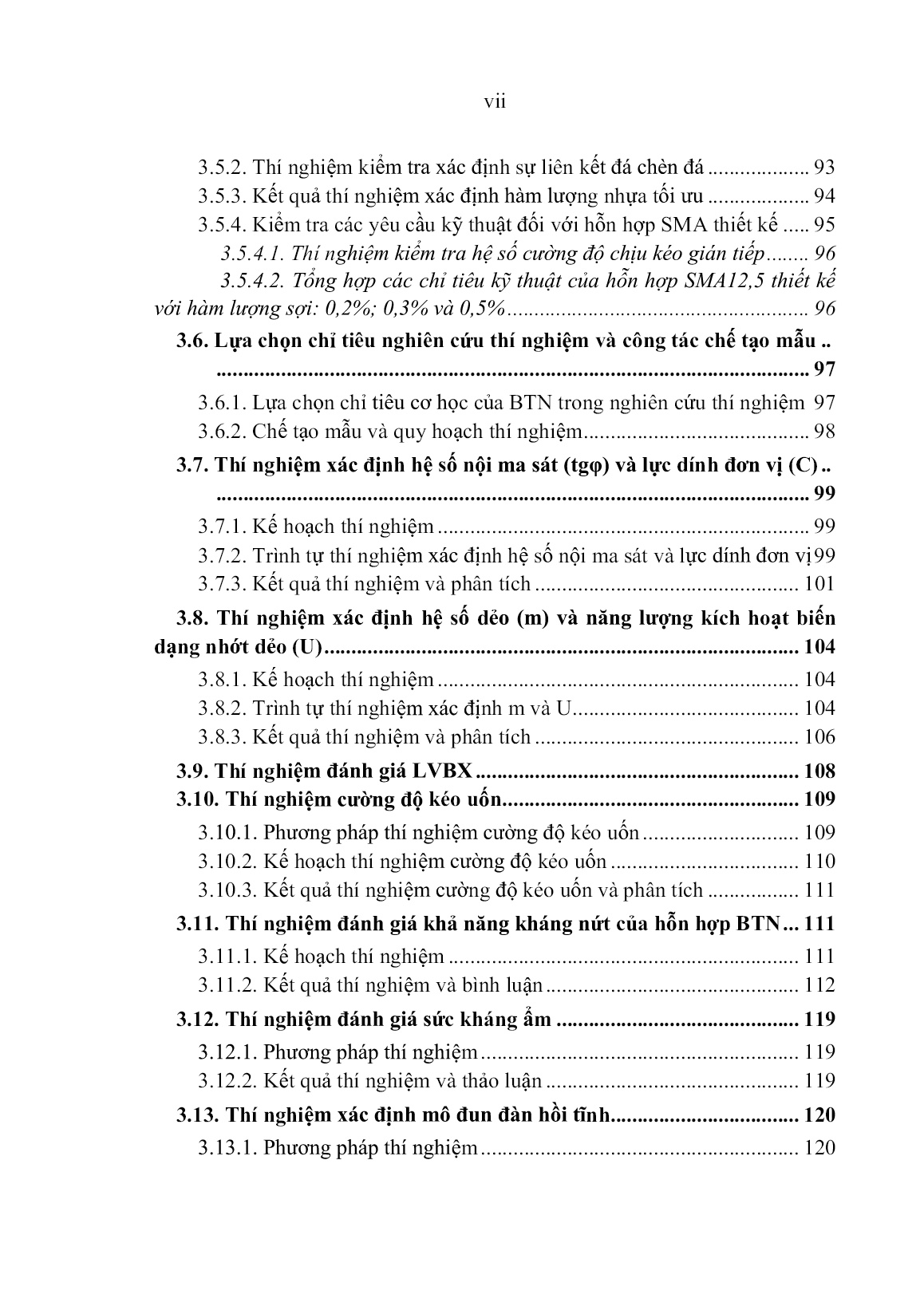
Trang 9
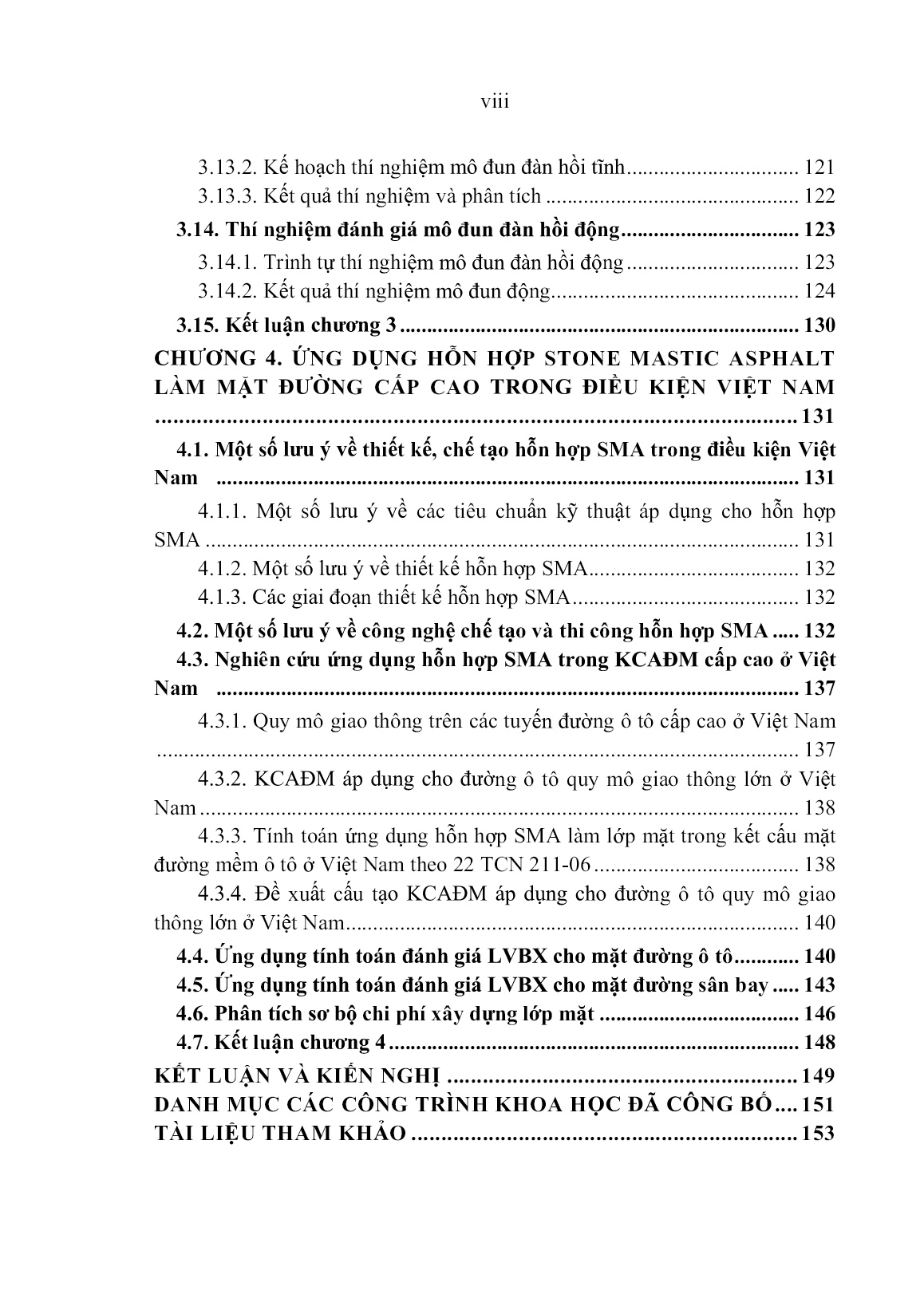
Trang 10
Tải về để xem bản đầy đủ
Bạn đang xem 10 trang mẫu của tài liệu "Luận án Nghiên cứu ảnh hưởng của vật liệu stone mastic ASPhalt đến khả năng chống lún vệt bánh xe và chống nứt mặt đường bê tông ASPhalt trong điều kiện Việt Nam", để tải tài liệu gốc về máy hãy click vào nút Download ở trên.
Tóm tắt nội dung tài liệu: Luận án Nghiên cứu ảnh hưởng của vật liệu stone mastic ASPhalt đến khả năng chống lún vệt bánh xe và chống nứt mặt đường bê tông ASPhalt trong điều kiện Việt Nam
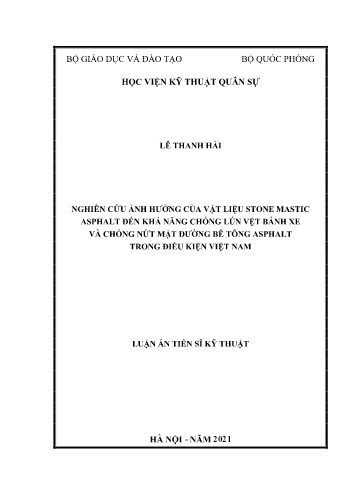
có độ hao mòn thấp, và phải kiểm soát hàm lượng hạt thoi dẹt. Các yêu cầu kỹ thuật cốt liệu thô của hỗn hợp SMA ở một số nước trên thế giới được thể hiện ở Bảng 2.4 [31,61]. Bảng 2.4. Một số yêu cầu kỹ thuật của cốt liệu thô Quốc gia/ Tiêu chuẩn Độ hao mòn Los Angeles, % Hàm lƣợng hạt thoi dẹt, % Hàm lƣợng hạt nghiền, % Mỹ/ AASHTO M325 Max 30 Max 20 (3 : 1) Max 5 (5 : 1) 1 mặt: 100 2 mặt: 90 Ấn Độ/ IRC SP 79 Max 25 Max 30 100 Cộng hòa Séc/ ČSN 73 6121 Max 25 - 100 Estonia/ EVS-EN 901-3 Max 15-20 Max 10-15 - CHLB Đức/ ZTV Asphalt - StB 07/1 Max 20 Max 20 100 Nauy Max 25 Max 25 100 Ba Lan/ WT-2 2014 CzęśćI Max 25 Max 20 100 Thụy Điển Max 25 Max 20 > 90 2.1.7. Mastic Mastic là thành phần lớn thứ hai của SMA. Mastic chiếm xấp xỉ 20-25% khối lượng hỗn hợp và 30-35% thể tích. Khoảng 35-40% thể tích cốt liệu thô sau khi đầm sẽ tạo thành thể tích rỗng, sau khi được lấp đầy bởi mastic, thì còn lại 3-5% thể tích rỗng. Sơ đồ minh họa được thể hiện ở Hình 2.12 [78]. Mastic bao gồm những thành phần sau: - Cốt liệu mịn (Fine aggregate); - Bột khoáng (Filler); - Chất ổn định (Stabilizer) hay chất chống chảy (là sợi hoặc các loại phụ gia khác); - Chất kết dính bitum (Bituminous binder). 59 Hình 2.12. Thể tích cốt liệu thô, mastic và lỗ rỗng của hỗn hợp SMA Chức năng của mastic: - Dính kết bộ khung cấu trúc cốt liệu thô; - Bôi trơn các hạt cốt liệu thô trong quá trình đầm và tạo một cấu trúc cốt liệu phù hợp trong quá trình đầm lớp mặt; - Làm kín các lớp hoặc lấp đầy lỗ rỗng trong quá trình đầm cấu trúc cốt liệu để tạo ra hỗn hợp có độ bền cao và khả năng chống lại các yếu tố bên ngoài khác như nước hoặc chất khử; - Chịu được các vấn đề do tải trọng và nhiệt độ. Hình 2.13 cho thấy sự chèn chặt của cốt liệu mịn (các hạt bị động) giữa các hạt cốt liệu thô (các hạt chủ động) [78]. (a) Sơ đồ nguyên lý; (b) Hình ảnh thực tế - mastic Hình 2.13. Lấp đầy khoảng trống giữa các hạt cốt liệu thô (hạt chủ động) bằng các hạt bị động a) Cốt liệu mịn Vai trò của cốt liệu mịn trong hỗn hợp SMA là lấp đầy các khoảng trống giữa các hạt cốt liệu lớn và làm cho cốt liệu lớn dễ dàng cài móc với nhau, mặc dù có khả năng được sắp xếp xung quanh nhưng cốt liệu mịn 60 không được làm gián đoạn sự cài móc lẫn nhau giữa các hạt cốt liệu lớn. Sự xáo trộn như vậy có thể được minh họa bằng ví dụ về cốt liệu tròn, không được nghiền (ví dụ, cát tự nhiên hoặc sỏi không nghiền) với bề mặt trơn nhẵn sẽ làm cho các cốt liệu thô dễ bị trượt. Việc đưa những “quả bóng cứng” như vậy vào hỗn hợp SMA gây ra vấn đề với sự ổn định (cài móc) của bộ khung cốt liệu. Đó là lý do ở nhiều quốc gia, việc sử dụng cốt liệu không được nghiền trong hỗn hợp SMA bị giới hạn chỉ sử dụng ở những đoạn đường có lưu lượng thấp hoặc việc sử dụng thường bị cấm [78]. Độ góc cạnh là một tính năng mô tả các thuộc tính của cốt liệu mịn và thường được xác định điển hình bằng thí nghiệm chảy, đây là một phương pháp gián tiếp để đo độ góc cạnh. Ở châu Âu, hệ số chảy (phương pháp EN 933-6) được ký hiệu là Ecs theo tiêu chuẩn Châu Âu EN 13043 và mô tả thời gian cần thiết để một lượng cốt liệu tiêu chuẩn chảy ra khỏi bình có hình dạng thông qua chỗ mở. Càng nhiều cốt liệu thô được nghiền với cấu trúc tốt thì thời gian chảy càng dài, nghĩa là cốt liệu thô hoặc góc cạnh có xu hướng khóa chúng với nhau và không chảy nhanh như với các hạt trơn nhẵn. Cốt liệu có Ecs ≥ 30-35 giây thì được xem là thích hợp với hỗn hợp SMA [61]. Cũng có những yêu cầu liên quan đến độ góc cạnh của cốt liệu nhỏ ở Mỹ. Thử nghiệm được thực hiện theo tiêu chuẩn AASHTO T304, Phương pháp A, giá trị độ góc cạnh cốt liệu nhỏ ≥ 45%. Độ góc cạnh cũng được đo theo tiêu chuẩn ASTM D3398 và cũng như phương pháp thử nghiệm của Hiệp hội cốt liệu quốc gia - Mỹ (NAA) [78]. Theo tiêu chuẩn kỹ thuật SMA của Ấn Độ (IRC SP 79), quy định đương lượng cát (SE) ≥ 50%. Cốt liệu mịn để chế tạo SMA chỉ dùng loại hạt lớn với mô đun độ lớn 2,5. Cốt liệu mịn được chế tạo từ đá gốc có cường độ không nhỏ hơn cường độ của đá dùng làm đá dăm [78]. Trong các tiêu chuẩn về SMA của Trung Quốc (JTG F40-2004), Ấn Độ (IRC SP 79), Châu Âu (EN 13108-5), Cộng Hòa Séc (ČSN 73 6121), CHLB Đức (ZTV Asphalt - StB 07/1), Nauy đều quy định 100% cốt liệu mịn phải được chế tạo từ đá nghiền [61]. Một số quốc gia cũng quy định cốt liệu nhỏ được tạo thành từ 50% cốt liệu nghiền/50% cốt liệu tự nhiên, hoặc 75% cốt liệu nghiền/25% cốt liệu tự nhiên (như tiêu chuẩn SMA của Úc - RMS R121, yêu cầu tối thiểu 50% cốt liệu mịn được làm từ đá nghiền). Hàm lượng cốt liệu nhỏ nghiền càng cao, sẽ tạo ra nội ma sát lớn, góp phần vào độ ổn định tổng thể của SMA. Hàm lượng cốt liệu mịn thông thường chiếm từ 12-17% theo khối lượng hỗn hợp vật liệu khoáng trong hỗn hợp SMA [61,78]. 61 b) Bột khoáng Bột khoáng là những hạt lọt qua sàng 0,075mm. Hàm lượng bột khoáng sử dụng trong hỗn hợp SMA thông thường chiếm từ 8-13%. Bột khoáng là thành phần quan trọng của hỗn hợp SMA, không những lấp đầy lỗ rỗng giữa các hạt cốt liệu lớn, làm tăng độ đặc của hỗn hợp mà còn làm tăng diện tích tiếp xúc, làm cho màng bitum trên bề mặt hạt vật liệu khoáng càng mỏng và như vậy lực tương tác giữa chúng tăng lên, cường độ và độ bền nước của SMA cũng tăng lên. Khi trộn với bitum trong hỗn hợp SMA, bột khoáng cần tạo nên một lớp hoạt tính, ổn định nước. Mối quan hệ vật lý, hoá học giữa bề mặt hạt bột khoáng và bitum làm tăng cường độ của SMA, nhưng cũng làm tăng tính giòn của nó. Vì vậy, lượng bột khoáng trong SMA chỉ được dùng trong một giới hạn nhất định để tránh làm tăng tốc độ hoá già của bitum trong hỗn hợp. Bột khoáng để chế tạo SMA thường sử dụng các loại bột mịn từ đá vôi và đá đôlômit. Cường độ chịu nén của đá không nhỏ hơn 200 daN/cm2. Vật liệu chế tạo bột khoáng cần sạch, không chứa các chất bẩn và sét quá 4%. Bột khoáng cần phải khô khi trộn với bitum, không được vón cục và có khả năng hút bitum tốt [50]. Các yêu cầu kỹ thuật của bột khoáng được quy định theo tiêu chuẩn AASHTO M17 - Mỹ [32]. Để hiểu rõ hơn quá trình làm việc của bột khoáng đã đầm trong hỗn hợp SMA, xem xét khái niệm độ rỗng trong bột khoáng đã đầm. Khi đầm cốt liệu sẽ tạo ra hỗn hợp với thể tích của hỗn hợp bao gồm thể tích các hạt (thể tích đặc) và khoảng không gian trống giữa chúng (lỗ rỗng). Trong hỗn hợp vữa nhựa thông thường (là hỗn hợp phối trộn giữa bột khoáng và bitum), lỗ rỗng này sẽ bị chiếm chỗ bởi bitum. Phần còn lại sẽ là một phần bitum còn lại và bột khoáng dư thừa còn lại. Bitum có trong vữa nhựa có thể được chia thành hai loại sau (Hình 2.14) [78]: (i) - Bitum cố định - là bitum bên trong các lỗ rỗng (lấp đầy lỗ rỗng giữa các các hạt bột khoáng đã đầm); (ii) - Bitum tự do - là chất kết dính dư thừa còn lại sau khi các lỗ rỗng được lấp đầy. Hình 2.14. Khái niệm về bitum cố định và bitum tự do 62 Trên thực tế, số lượng bitum tự do rất quan trọng, vì các tính chất của mastic phụ thuộc vào số lượng bitum tự do. Hàm lượng bitum tự do trong vữa nhựa càng thấp thì tốc độ tăng độ cứng càng nhanh [69]. Các hạt bột khoáng khi đầm khô tối đa Hỗn hợp bitum-bột khoáng khi bitum không đủ lấp đầy các lỗ rỗng Hỗn hợp bitum-bột khoáng khi bitum đủ để lấp đầy các lỗ rỗng Hỗn hợp bitum-bột khoáng lấp đầy rỗ rỗng và bitum bị thừa quá mức Hình 2.15. Lấp đầy các lỗ trỗng trong bột khoáng Hình 2.15 minh họa quá trình lấp đầy các khoảng trống trong bột khoáng được đầm; Bitum về cơ bản đóng hai vai trò: là chất bôi trơn làm cho các hạt di chuyển dễ dàng hơn và là chất lỏng mà các hạt lơ lửng trong đó [78]. Với hàm lượng bitum không đổi trong hỗn hợp BTN, số lượng bitum tự do phụ thuộc vào các lỗ rỗng trong bột khoáng được đầm. Với tỷ lệ cố định của các thành phần trong hỗn hợp BTN, số lượng bitum tự do có thể được tăng lên bằng cách thay đổi thành phần bột khoáng có hàm lượng lỗ rỗng thấp hơn. c) Chất kết dính Các loại chất kết dính khác nhau cho hỗn hợp SMA được sử dụng ở nhiều nước. Ở Australia, bitum cấp 320 được sử dụng phổ biến, bitum cấp 170 được sử dụng để tăng cường độ bền cho các công trình có lưu lượng giao thông thấp. Hầu hết các công trình đường bộ ở New Zealand đều sử dụng bitum 60/70 [73]. Trước đây ở Châu Âu, chất kết dính thông thường cũng được sử dụng để chế tạo hỗn hợp SMA. Bitum 50/70 được sử dụng phổ biến ở CHLB Đức cho các tuyến đường có lưu lượng xe thấp hoặc bitum 70/100 được sử dụng ở Hà Lan. Thế nhưng với sự thay đổi các phương tiện giao thông và lưu lượng giao thông tăng nhanh thì bitum cải tiến đã được sử dụng. Những nghiên cứu của các nhà khoa học ở Đức đã cho thấy sử dụng bitum cải tiến (như PMB 25/55-55) cho hỗn hợp SMA giúp tăng khả năng kháng LVBX lên gấp nhiều lần so với bitum thông thường [78]. 63 Bitum polime cải tiến (PMB) thường được sử dụng để tăng độ dính bám với hỗn hợp vật liệu khoáng. Nghiên cứu của ER.Brown [55] chỉ ra rằng hỗn hợp SMA sử dụng PMB có khả năng chống LVBX và độ ổn định cao hơn so với hỗn hợp SMA sử dụng chất kết dính thông thường. Nếu lượng chất kết dính quá nhiều, sẽ đẩy những hạt cốt liệu thô ra xa, ngược lại nếu lượng vữa asphalt quá ít sẽ dẫn đến độ rỗng dư cao làm giảm độ bền của hỗn hợp SMA [81]. Hỗn hợp SMA có cấp phối gián đoạn và hàm lượng bitum tương đối lớn (hàm lượng bitum tối thiểu của hỗn hợp SMA tại CHLB Đức và Cộng hòa Séc là 6,5%, Ba Lan là 6,6%, Hungary và Estonia là 6,2% [61]), do vậy trong quá trình trộn, vận chuyển, rải và đầm nén chỉ một phần bitum bám vào cốt liệu, phần còn lại sẽ tách khỏi hỗn hợp và chảy ra ngoài. Để khắc phục hiện tượng trên, các loại chất ổn định như sợi cellulose hoặc sợi khoáng đã được thêm vào hỗn hợp. d) Chất ổn định Chất ổn định được sử dụng cho hỗn hợp SMA có thể là sợi cellulose, sợi khoáng hoặc sợi tổng hợp. Chất ổn định dạng sợi sẽ kết hợp với bitum, lấp đầy các lỗ rỗng trong hỗn hợp cốt liệu. Chất ổn định được đưa vào hỗn hợp trong quá trình trộn khô để ngăn hiện tượng bitum chảy ra trong quá trình trộn, vận chuyển, đầm nén và khai thác. Hiện nay ở CHLB Đức, chất ổn định được sử dụng trên 90% là sợi cellulose. Mặc dù chất ổn định chiếm một tỉ lệ rất nhỏ trong hỗn hợp SMA, khoảng 3 đến 15 phần ngàn, nhưng là thành phần không thể thiếu của SMA. Chất ổn định khi được trộn với bitum sẽ làm bitum giảm độ nhớt, trở nên quánh hơn nhờ tính chất hút - thấm nhựa của chúng và vì vậy sẽ ngăn được hiện tượng chảy nhựa [23]. Hai dạng sợi cellulose phổ biến đang sử dụng hiện nay là dạng xốp và dạng viên. Phụ gia dạng sợi Viatop được nghiên cứu và phát triển bởi Tập đoàn J.Rettenmaier & Sohne (CHLB Đức). Các loại phụ gia Viatop có hàm lượng sợi cellulose sử dụng cho SMA như: Viatop Premium, Viatop 66, Viatop plus AD10, Viatop plus C25.... Tại Liên Bang Nga, các loại phụ gia dạng hạt phổ biến nhất là phụ gia Nanobit-SD (Нанобит-СД) và phụ gia Chryzotop (Хризотоп). Phụ gia Chryzotop được nghiên cứu, phát triển, sản xuất bởi Công ty Stilobit (Стилобит) - Liên Bang Nga. Tại Mỹ, khuyến cáo sử dụng sợi cellulose cho hỗn hợp SMA với tỷ lệ 0,3% theo khối lượng hỗn hợp, sợi khoáng tỷ lệ là 0,4%). Ấn Độ, Trung Quốc và một số nước ở Châu Âu quy định sử dụng sợi cellulose cho hỗn hợp SMA 64 với hàm lượng tối thiểu là 0,3% theo khối lượng hỗn hợp. Độ chảy nhựa được xác định theo tiêu chuẩn AASHTO T305 (Mỹ) hoặc TCVN 8860-6:2011 - Bê tông nhựa - phương pháp thử - phần 6: Xác định độ chảy nhựa (Việt Nam). Hình ảnh thí nghiệm xác định độ chảy nhựa được thể hiện ở Hình 2.16. Hình 2.16. Thí nghiệm xác định độ chảy nhựa của hỗn hợp SMA 2.2. Phƣơng pháp thiết kế hỗn hợp SMA SMA được thiết kế theo các chỉ tiêu về đặc tính thể tích như độ rỗng dư, độ rỗng cốt liệu và sự hình thành liên kết đá chèn đá [55,78]. Tiêu chuẩn kỹ thuật cho hỗn hợp SMA ở Mỹ trước đây là AASHTO MP8 và AASHTO PP 41-02. Hiện nay đã được thay thế bằng tiêu chuẩn AASHTO M325-08 và AASHTO R46-08. Điểm khác biệt lớn nhất giữa hai tiêu chuẩn là AASHTO M325 yêu cầu sử dụng đầm xoay (SGC), trong khi đó AASHTO MP8 sử dụng thiết bị đầm theo phương pháp Marshall (2×50 chày/1 mặt; độ ổn định Marshall ≥ 6,2kN và độ dẻo Marshall từ 2-4mm). Nghiên cứu của Scherocman [99] đã chứng minh rằng khi chế tạo mẫu SMA theo phương pháp Marshall chỉ sử dụng 50 chày/1 mặt, không dùng 75 chày/1 mặt vì sẽ gây ra hiện tượng vỡ cốt liệu khi đầm. Hầu hết tiêu chuẩn hỗn hợp SMA ở các nước Châu Âu, Ấn Độ, Trung Quốc, New Zealand thiết kế theo phương pháp Marshall với 2×50 chày/1 mặt. Tại New Zealand cho phép sử dụng một trong hai phương pháp đầm theo Marshall hoặc đầm xoay. Thiết bị đầm xoay - là thiết bị có giá thành khá cao (so với thiết bị Marshall), yêu cầu người sử dụng phải có tay nghề và kinh nghiệm tốt. Hiện nay ở Việt Nam, số lượng các đơn vị có thiết bị đầm xoay chưa nhiều, do vậy, trong nghiên cứu, phương pháp Marshall được lựa chọn để thiết kế hỗn hợp SMA. Đây là phương pháp phổ biến, thiết bị đầm theo phương pháp Marshall có hầu hết ở các phòng thí nghiệm xây dựng công trình giao thông tại Việt Nam, vận hành thiết bị đơn giản. 65 2.3. Trình tự thiết kế hỗn hợp SMA Tham khảo các tài liệu [31,33,55,78], trình tự thiết kế hỗn hợp SMA được tiến hành như sau: ① Lựa chọn thành phần vật liệu SMA; ② Lựa chọn cấp phối tốt nhất: Đề xuất 3 đường cấp phối trong đường bao theo tiêu chuẩn AASHTO M325, trong đó 1 đường cấp phối bám sát cận trên, 1 đường đi giữa, và 1 đường bám sát cận dưới trong giới hạn đường bao; ③ Xác định khối lượng thể tích bằng thí nghiệm AASHTO T19 [35] (đầm bằng dùi chọc khô - dry-rodded test) cho mỗi cấp phối. Xác định độ rỗng cốt liệu thô ở trạng thái chưa đầm nén VCADRC; ④ Xác định một hàm lượng nhựa hợp lý ban đầu bằng kinh nghiệm, sau đó trộn hỗn hợp đủ khối lượng cho tối thiểu 3 mẫu Marshall/1 đường cấp phối. Đúc mẫu sử dụng máy đầm Marshall với công đầm nén: 2×50 chày/mặt mẫu; ⑤ Thí nghiệm xác định tỷ trọng lớn nhất Gmm của hỗn hợp SMA theo TCVN 8860-4 (AASHTO T209); ⑥ Tháo khuôn mẫu đã được đầm nén, thí nghiệm xác định tỷ trọng khối Gmb của các mẫu theo TCVN 8860-5 (AASHTO T166). Tính các đặc trưng thể tích của mẫu: Độ rỗng dư Va; Độ rỗng cốt liệu VMA; Độ rỗng cốt liệu thô đã đầm nén VCAMIX; ⑦ Lựa chọn đường cấp phối thỏa mãn chỉ tiêu VMA ≥ 17% và tồn tại bộ khung cốt liệu thô theo nguyên lý tiếp xúc đá chèn đá VCAMIX ≤ VCADRC. Nếu có nhiều hơn 1 đường cấp phối thỏa mãn thì chọn đường cấp phối có VMA lớn nhất; cấp phối đi giữa đường bao giới hạn; cấp phối có tỷ lệ cốt liệu thô ít hơn; cấp phối dễ trộn và kiểm soát khi thi công hơn; Nếu đã có kinh nghiệm thiết kế hỗn hợp SMA cho các dự án tương tự thì chỉ cần chọn ngay cấp phối tốt nhất sau đó đánh giá các đặc trưng thể tích mà không cần phải làm với cả 3 đường cấp phối; ⑧ Lựa chọn hàm lượng nhựa tối ưu; ⑨ Thí nghiệm các chỉ tiêu hỗn hợp SMA tại hàm lượng nhựa tối ưu như: thí nghiệm xác định các đặc trưng thể tích, thí nghiệm độ chảy nhựa (AASHTO T305). Nếu một số các yêu cầu kỹ thuật của hỗn hợp SMA không đạt, thì có thể điều chỉnh thiết kế cấp phối, cụ thể như sau: - Độ rỗng dƣ Va: có thể được kiểm soát bằng cách thay đổi hàm lượng nhựa. Tuy nhiên, có một số trường hợp độ rỗng dư thấp hơn yêu cầu mặc dù hàm lượng nhựa đã ở mức thấp nhất theo quy định, việc giảm hàm lượng nhựa trong trường hợp này sẽ giúp tăng độ rỗng dư Va nhưng lại vi phạm quy 66 định. Vì vậy, cần phải thay đổi cấp phối để tăng độ rỗng vật liệu khoáng VMA thay vì giảm hàm lượng nhựa. - Độ rỗng vật liệu khoáng VMA: Khi giá trị VMA không đạt theo yêu cầu, có thể điều chỉnh bằng cách tăng hàm lượng cốt liệu thô trong hỗn hợp. Việc thay đổi nguồn vật liệu cũng có thể thay đổi VMA. - Độ rỗng cốt liệu thô VCAMIX: nếu VCAMIX > VCADRC thì cần phải thay đổi thành phần cấp phối để đảm bảo sự hình thành cấu trúc đá chèn đá. Thông thường sẽ thay đổi bằng cách tăng thành phần cốt liệu thô. - Độ chảy nhựa: Vấn đề chảy nhựa có thể được khắc phục bằng cách thay đổi hàm lượng hoặc thay đổi loại chất ổn định. 2.4. Khả năng chống nứt của hỗn hợp SMA Hỗn hợp SMA sử dụng chất ổn định là phụ gia dạng sợi không những giúp hạn chế hiện tượng chảy nhựa mà còn có tác dụng tăng mật độ màng bitum trên bề mặt hạt cốt liệu, tăng độ ổn định tổng thể cho hỗn hợp. Năm 2016, Đ.V.Thanh [12] đã chế tạo hỗn hợp SMA16 theo tiêu chuẩn JTG F40-2004 (Trung Quốc), sử dụng 3 loại sợi là sợi hữu cơ, sợi khoáng và sợi tổng hợp. Sau đó dùng kính hiển vi điện tử độ phân giải cao (Quanta 200) phân tích vi quan các mẫu bị phá hoại nứt khi không dùng và dùng ba loại sợi khác nhau, thu được các kết quả như sau: - Trong hỗn hợp SMA cả ba loại sợi đều có khả năng đan chéo dọc ngang, hình thành kết cấu mạng không gian, kiểu kết cấu này có tác dụng truyền lực đồng thời ngăn cản sự trơn trượt giữa các hạt, liên kết tổng thể hỗn hợp, cản trở và làm chậm sự hình thành và phát triển vết nứt”; - Sợi phân bố đan chéo trong các lỗ rỗng nhỏ, vì vậy giúp ngăn cản sự mở rộng của các vết nứt và lỗ rỗng. Tuy nhiên, khi hàm lượng sợi sử dụng thấp, chưa đạt đến giá trị tối ưu, kết cấu mạng lưới không gian sẽ chưa đủ để hình thành, liên kết giữa sợi với sợi kém. Khi hàm lượng sợi quá nhiều sẽ gây ra hiện tượng sợi kết bó, dồn đống, sợi phân bố không đồng đều, nhiều sợi ở trạng thái rời rạc, không phát huy được tác dụng của sợi. Năm 2017, Shenghua Wu [102] đã công bố nghiên cứu về đánh giá tính năng dài hạn của mặt đường SMA12,5 và BTNC12,5 ở tuyến đường phía đông Bang Washington, Mỹ. Tính năng hiện trường được đánh giá dựa trên dữ liệu hệ thống quản lý mặt đường và khảo sát thực địa. Các mẫu khoan rút lõi hiện trường từ mặt đường SMA và BTNC được dùng để tiến hành các chỉ tiêu thí nghiệm trong phòng như: (i) mô đun đàn hồi kéo gián tiếp (IDT); (ii) biến dạng từ biến; (iii) độ bền mài mòn của lốp xe và (iv) thí nghiệm phá hủy IDT ở nhiệt độ thấp và trung bình. Các kết quả thí nghiệm đã chỉ ra rằng, tại 67 hiện trường, mặt đường SMA12,5 có các tính năng vượt trội hơn mặt đường BTNC12,5 về khả năng chống LVBX và nứt. Kết quả các thử nghiệm trong phòng với mẫu khoan rút lõi hiện trường đã chứng minh rằng hỗn hợp SMA có hiệu năng tốt hơn hỗn hợp BTNC về khả năng kháng nứt từ trên xuống, kháng nứt từ dưới lên và khả năng kháng nứt do nhiệt. Kết quả của thử nghiệm nhựa đường thu hồi cho thấy hỗn hợp SMA (với hàm lượng nhựa 6,8%) ít bị lão hóa hơn so với hỗn hợp BTNC (với hàm lượng nhựa 5,44%) và nhựa đường SMA thu hồi có khả năng kháng LVBX, kháng nứt do mỏi và nứt do nhiệt tốt hơn so với nhựa đường BTNC. Bài báo đã kết luận rằng mặt đường SMA, khi được thiết kế và thi công theo đúng kỹ thuật, là một giải pháp khả thi để kéo dài tuổi thọ của mặt đường BTN. Như vậy, hỗn hợp SMA có khả năng kháng nứt tốt so với BTNC thông thường do 2 nguyên nhân: (i) – Hỗn hợp SMA có hàm lượng bitum lớn (6,0-7,5%) so với các loại BTNC thông thường, do vậy, làm tăng tính linh hoạt và khả năng kháng nứt của hỗn hợp; (ii) – Sợi phân tán trong hỗn hợp SMA không những có tác dụng chống chảy nhựa mà còn có khả năng đan chéo dọc ngang, làm chậm sự hình thành và phát triển vết nứt. 2.5. Phƣơng pháp thí nghiệm đánh giá khả năng kháng nứt của vật liệu BTN - theo tiêu chuẩn ASTM D8225 - 19 thông qua chỉ số CTIndex 2.5.1. Mô tả thí nghiệm đánh giá khả năng kháng nứt của vật liệu BTN (IDEAL-CT) Năm 2019, phương pháp thí nghiệm IDEAL-CT đã được chuẩn hóa và được Mỹ ban hành thành tiêu chuẩn thí nghiệm ASTM D8225-19 [43]. Thí nghiệm IDEAL-CT tương tự như thí nghiệm độ bền kéo gián tiếp truyền thống, được tiến hành ở nhiệt độ phòng với các mẫu hình trụ với tốc độ gia tải 50mm/phút. Bất kỳ kích thước của mẫu hình trụ với đường kính khác nhau (100mm hoặc 150mm) và độ dày (38, 50, 62, 75mm, v.v.) đều có thể được dùng để thí nghiệm. Đối với
File đính kèm:
luan_an_nghien_cuu_anh_huong_cua_vat_lieu_stone_mastic_aspha.pdf
3.Tom tat nhung dong gop moi cua LATS.docx
2.Tom tat LATS - Le Thanh Hai.pdf