Luận án Nghiên cứu các đặc trưng kháng cắt của bê tông nhựa dùng làm tầng mặt cho kết cấu áo đường ô tô
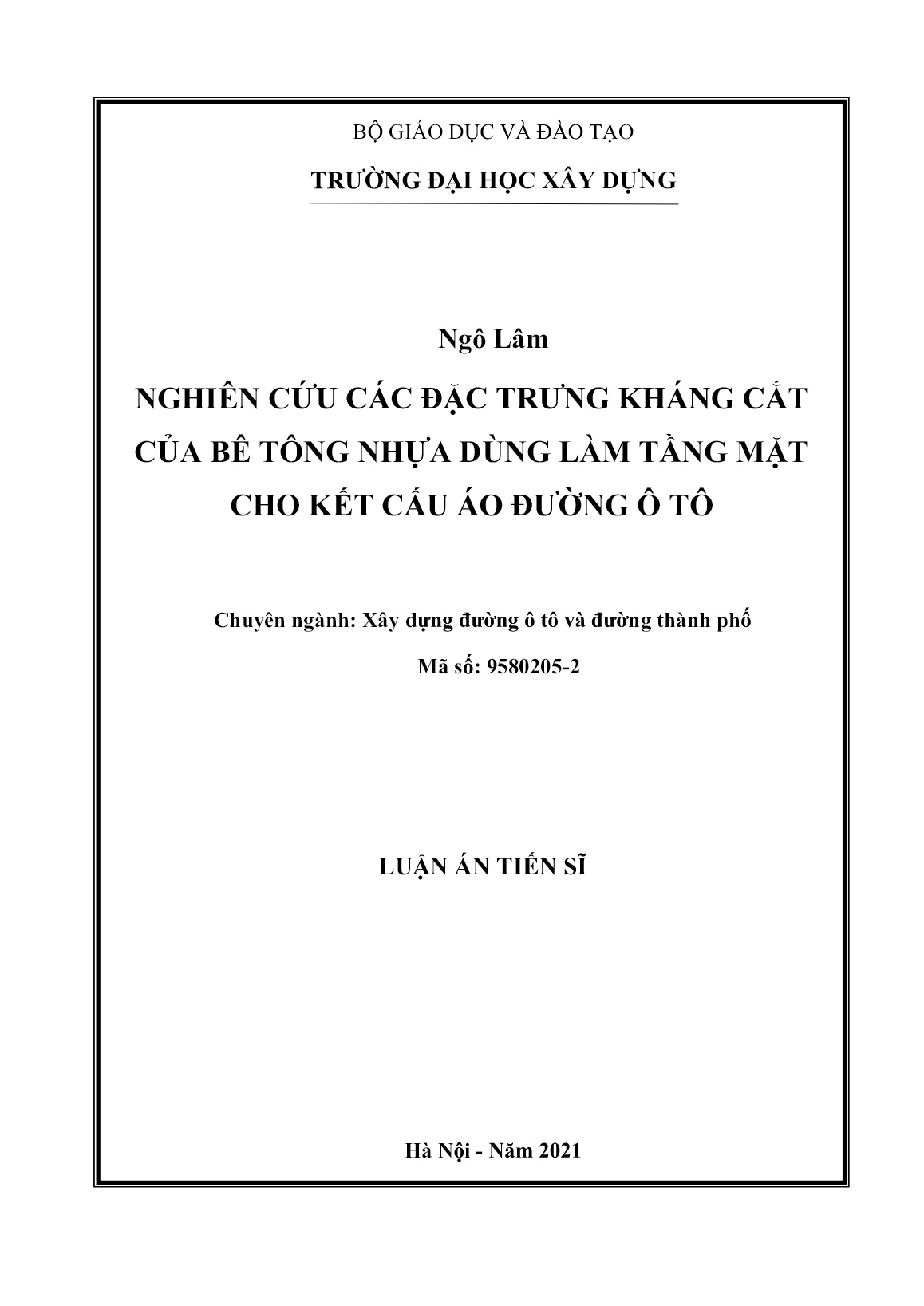
Trang 1
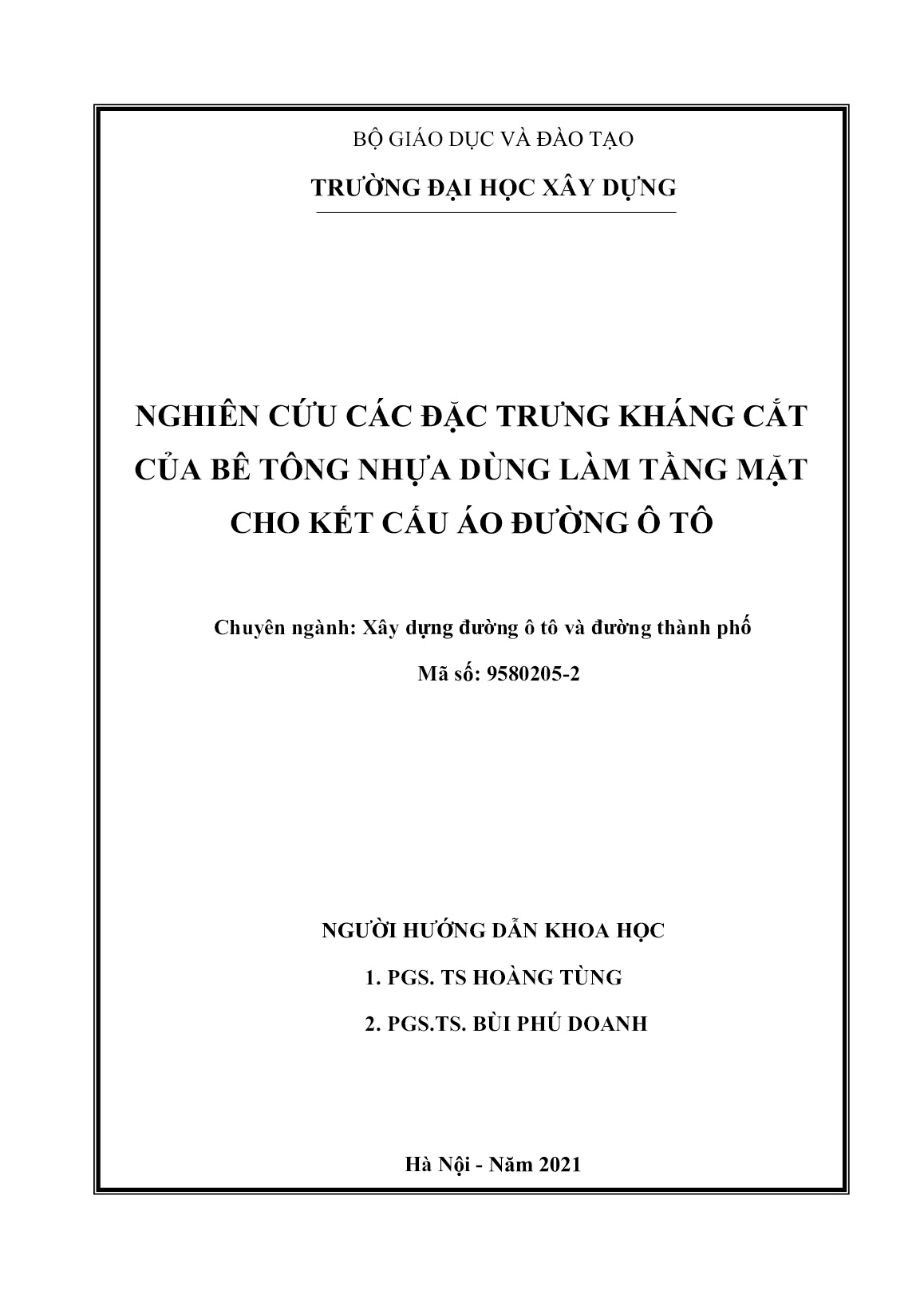
Trang 2
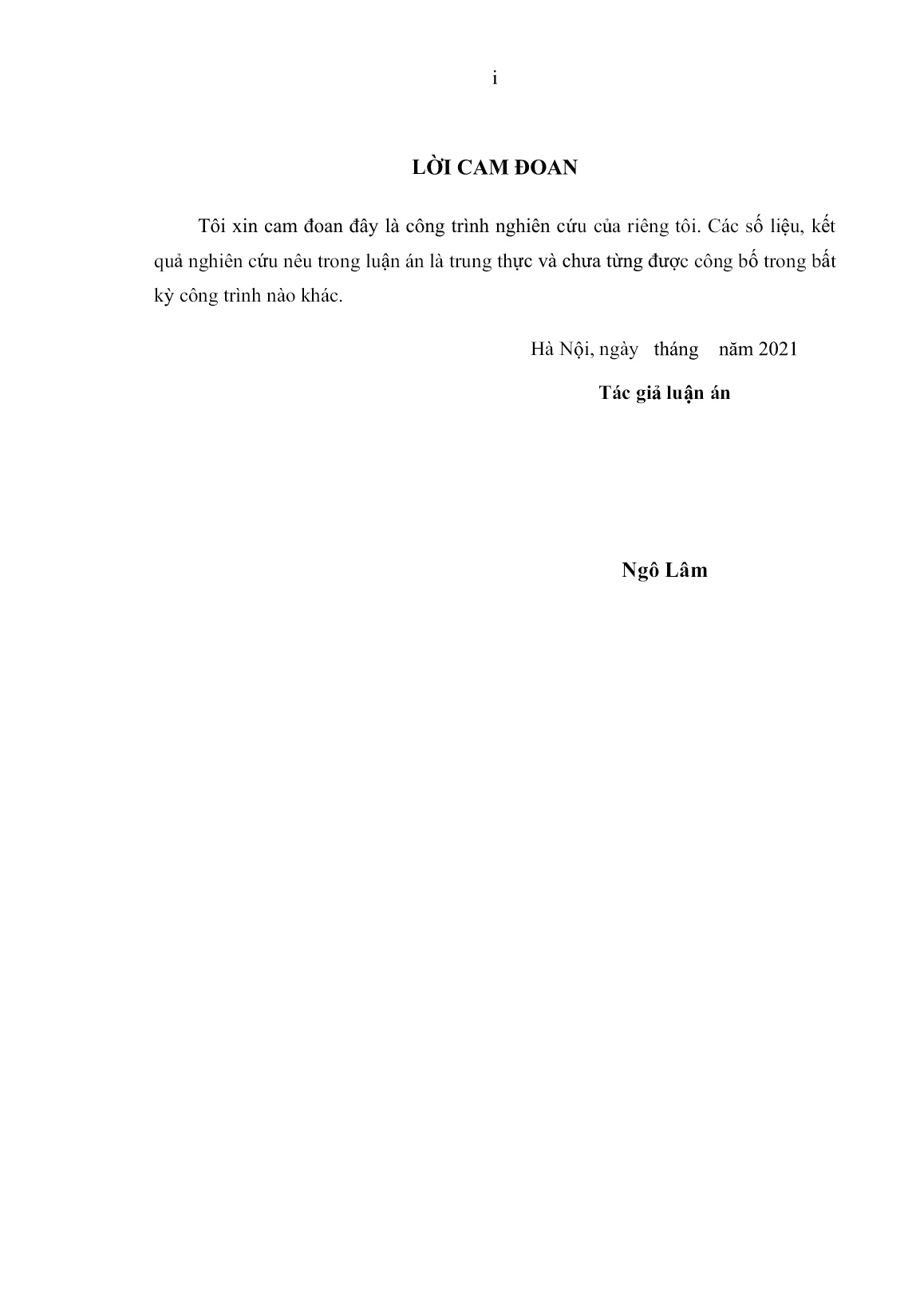
Trang 3
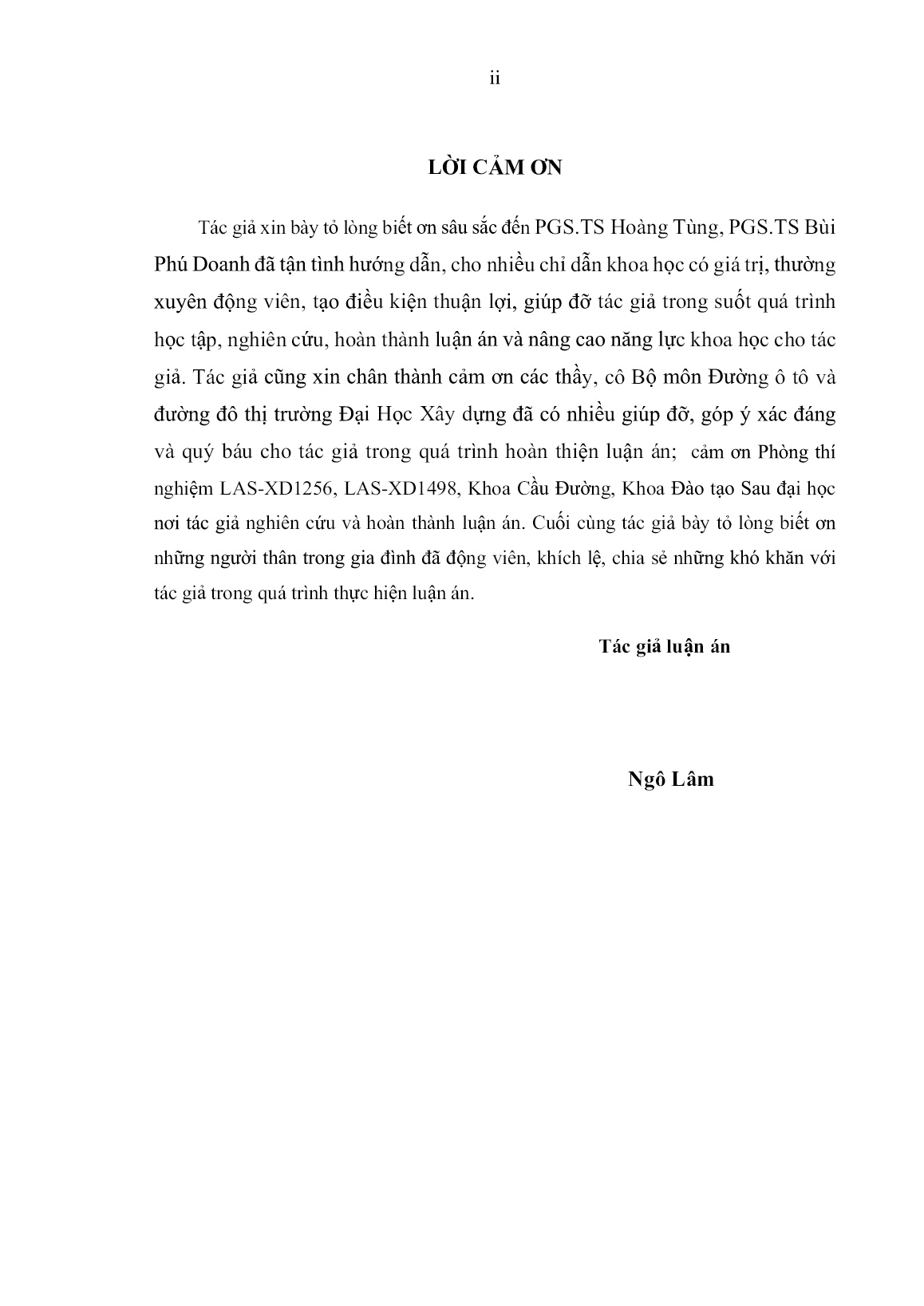
Trang 4
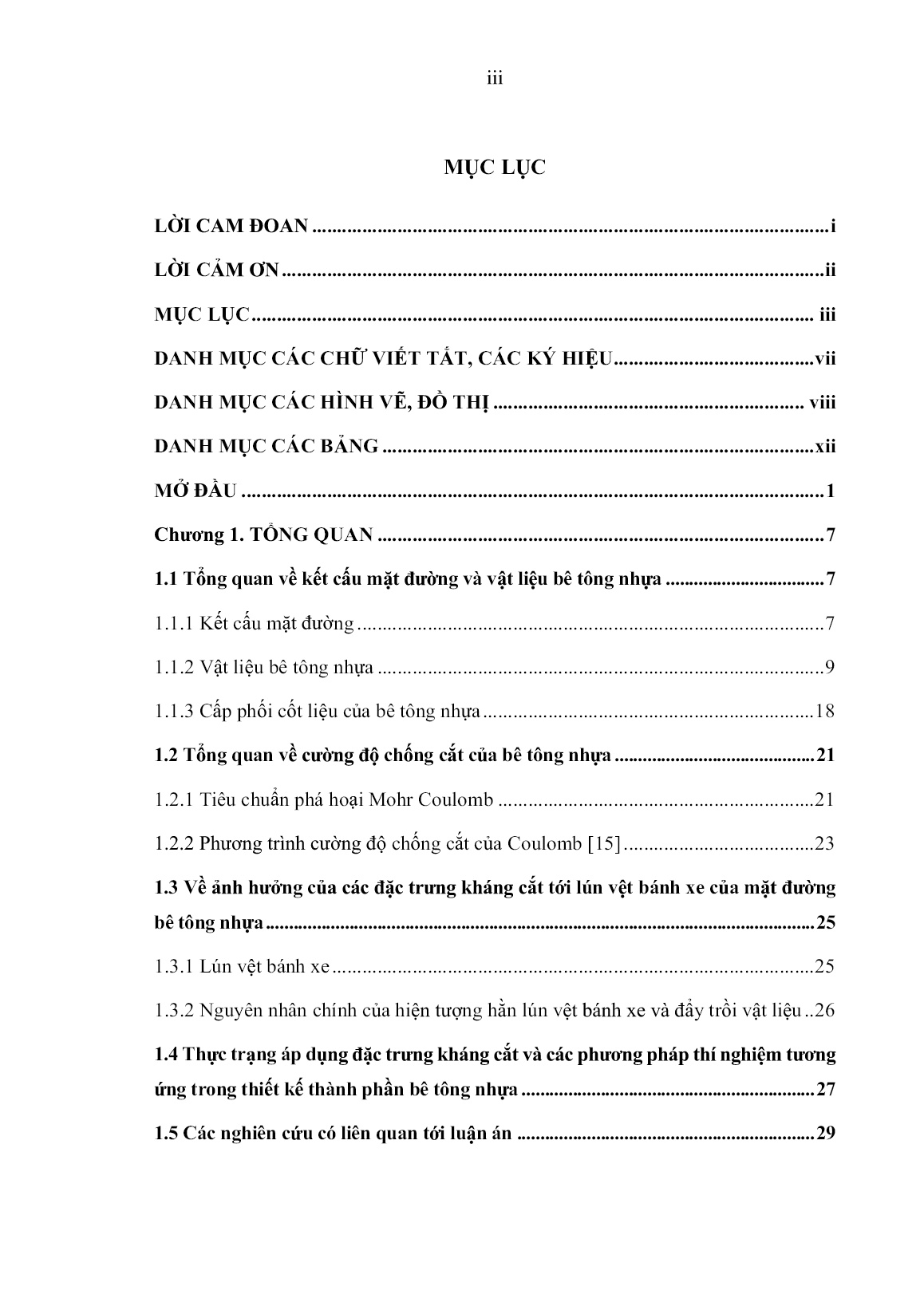
Trang 5
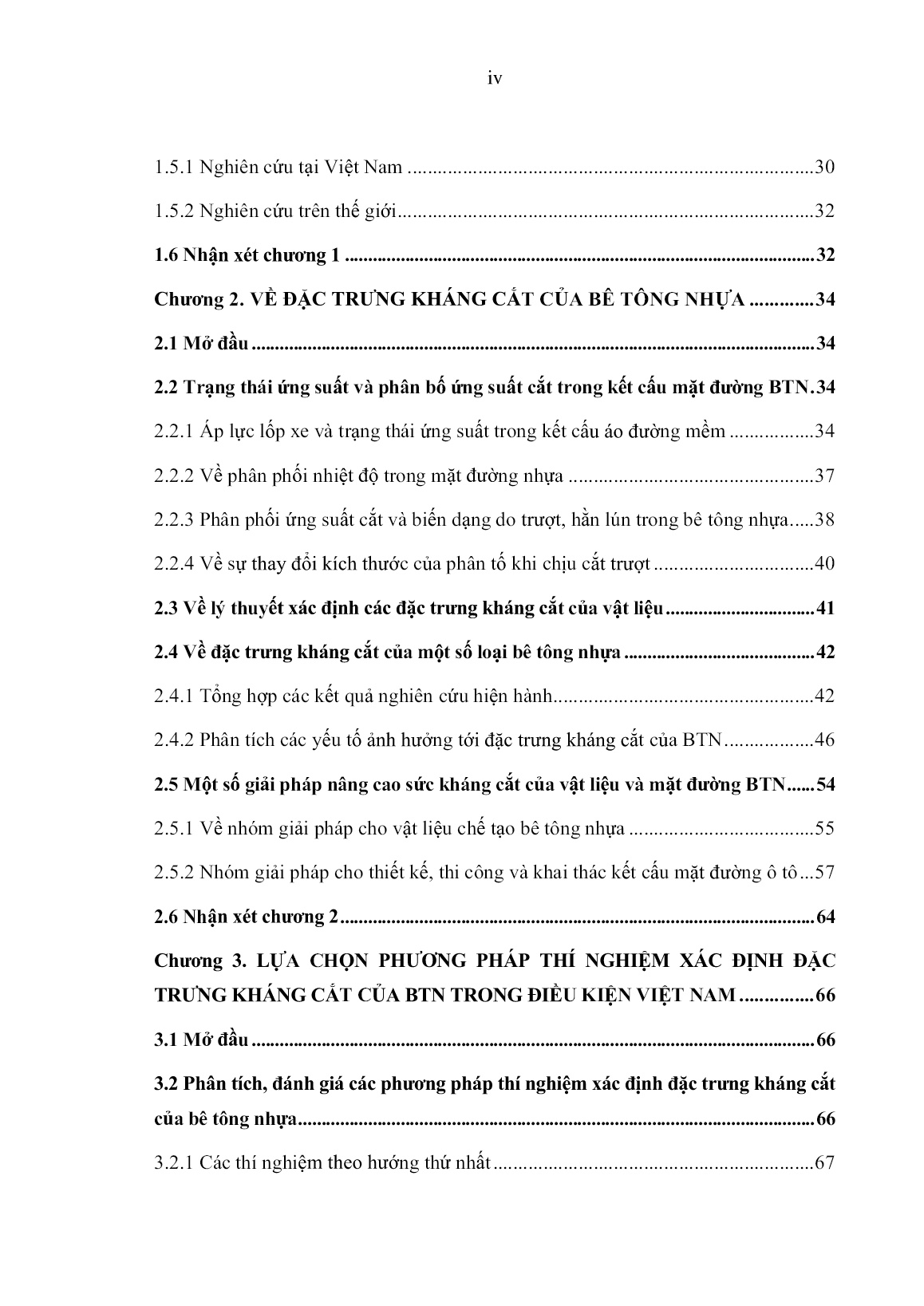
Trang 6
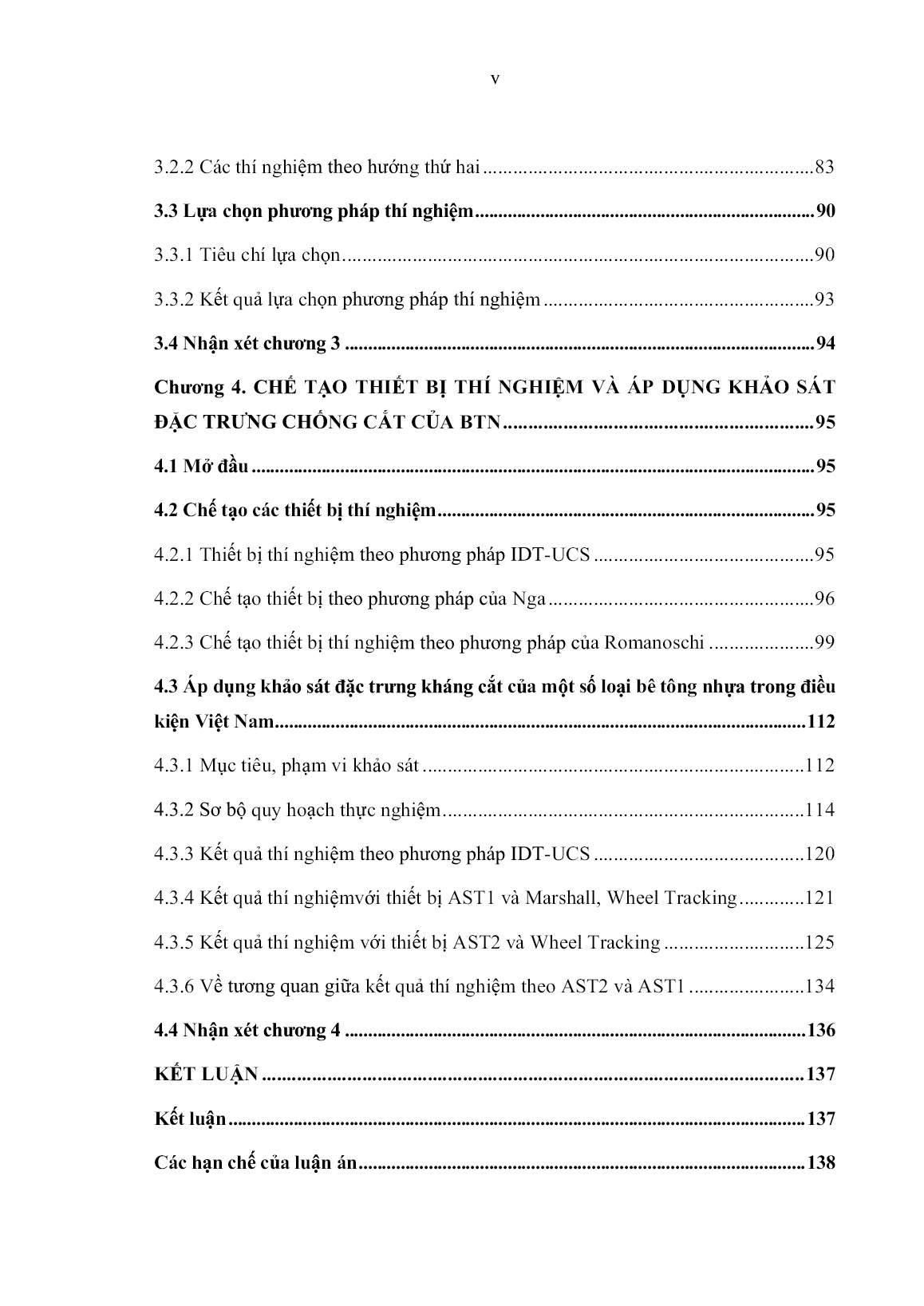
Trang 7
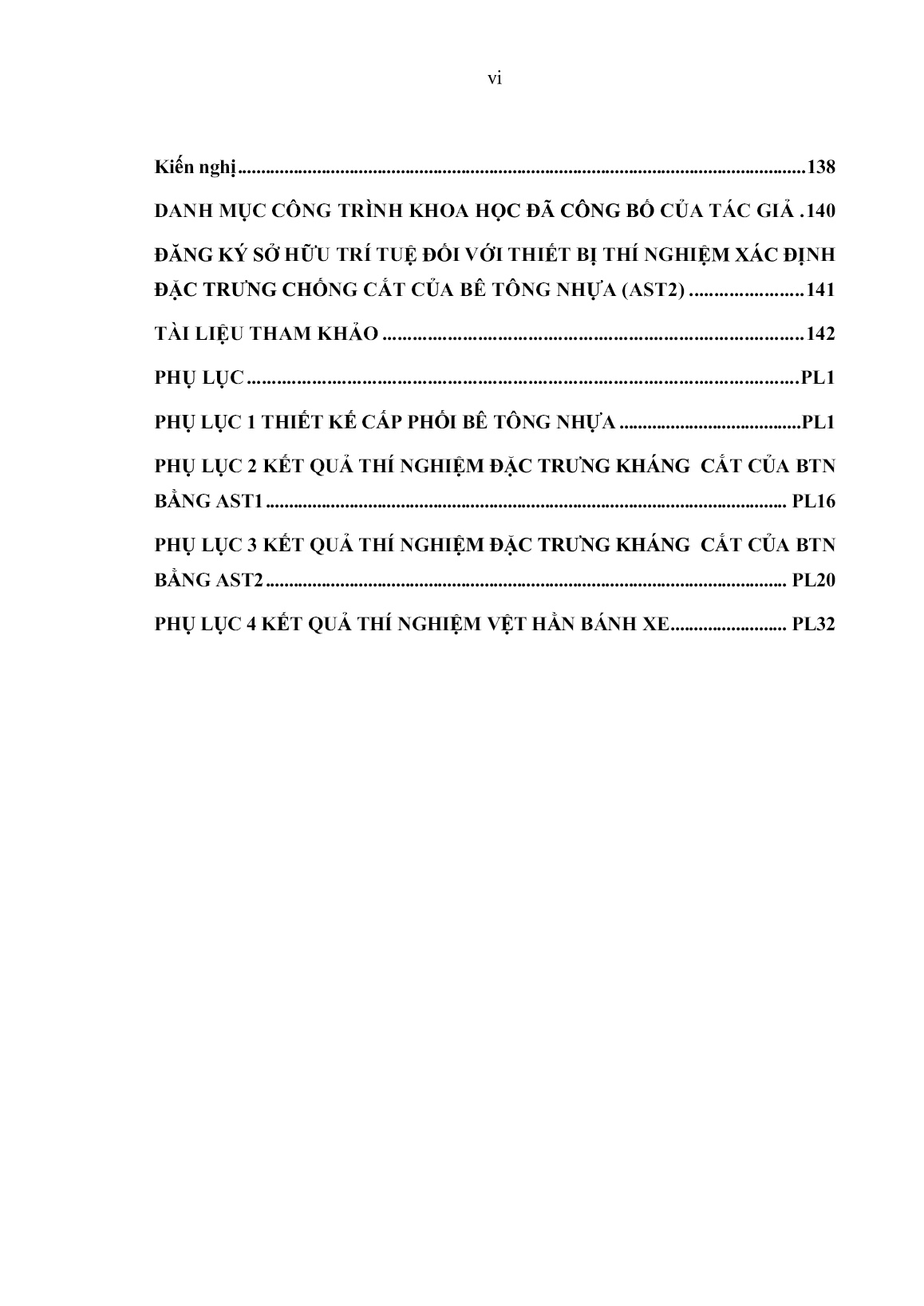
Trang 8
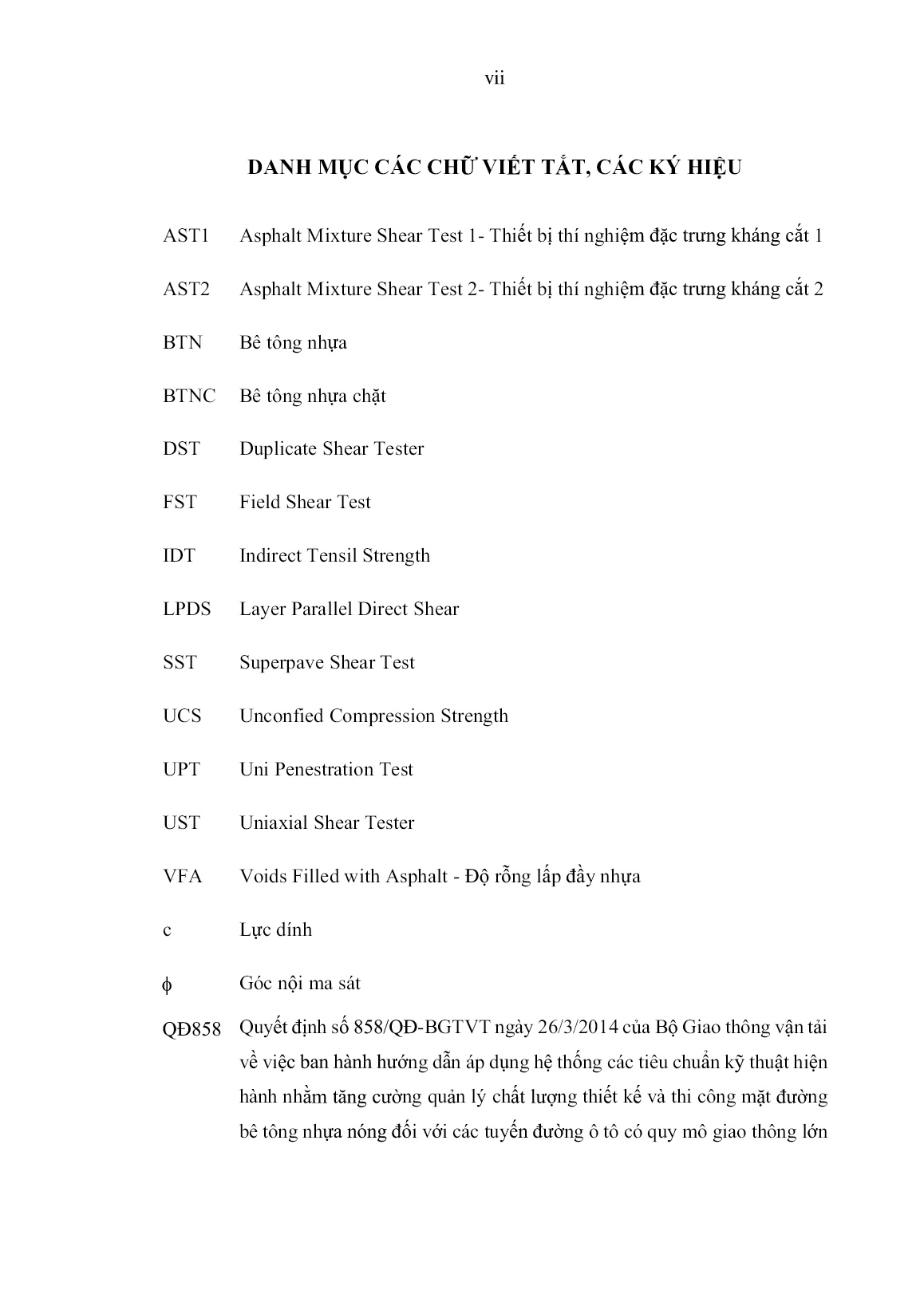
Trang 9
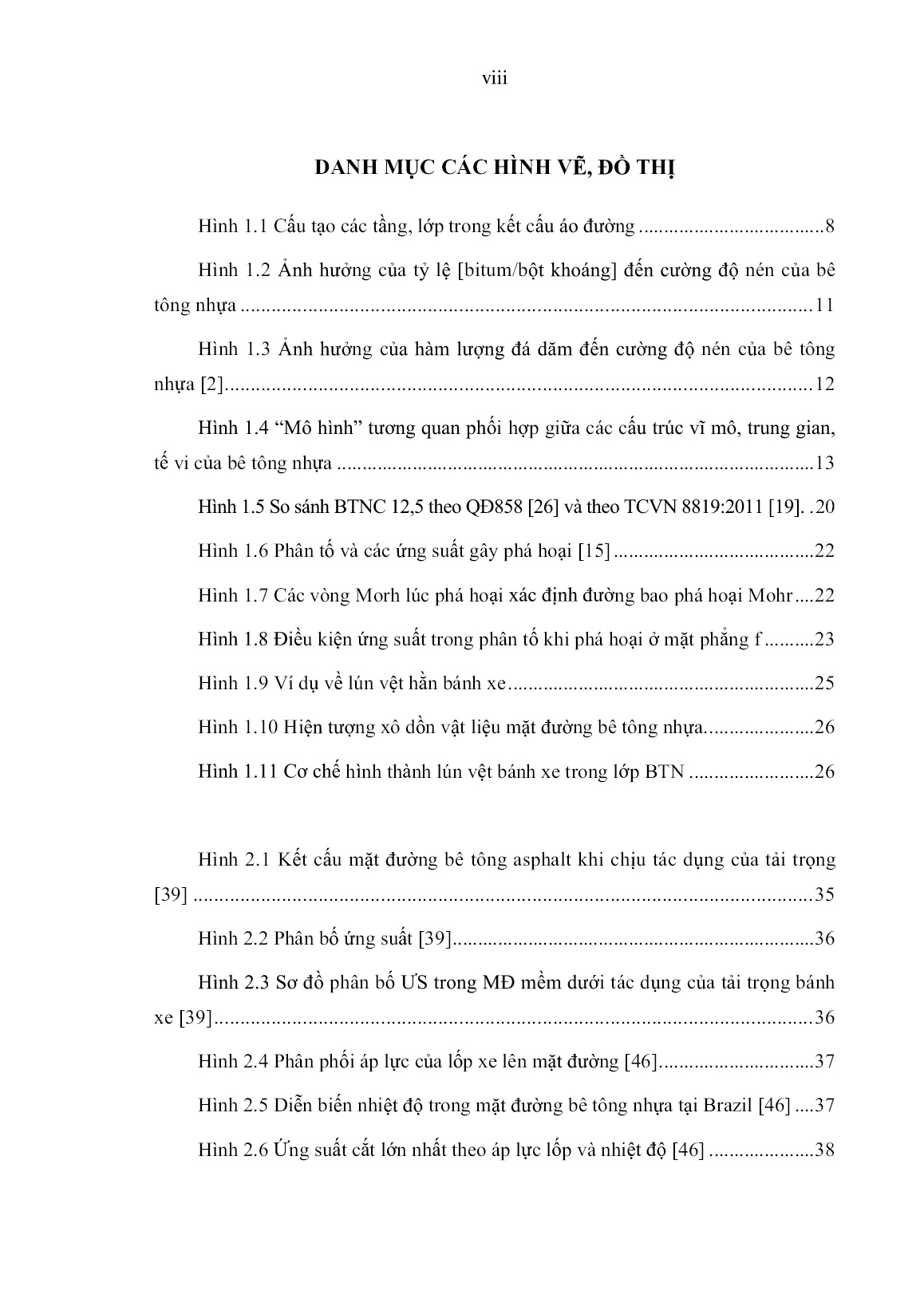
Trang 10
Tải về để xem bản đầy đủ
Bạn đang xem 10 trang mẫu của tài liệu "Luận án Nghiên cứu các đặc trưng kháng cắt của bê tông nhựa dùng làm tầng mặt cho kết cấu áo đường ô tô", để tải tài liệu gốc về máy hãy click vào nút Download ở trên.
Tóm tắt nội dung tài liệu: Luận án Nghiên cứu các đặc trưng kháng cắt của bê tông nhựa dùng làm tầng mặt cho kết cấu áo đường ô tô
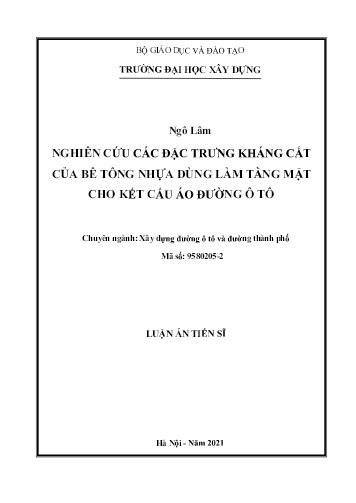
cập ở điều 3.3 bài viết này). Nếu nhiệt độ mặt đường nhựa (T50%max hoặc T98%max ) lớn hơn hoặc bằng 640C thì cần sử dụng mác nhựa 40/50. Cũng cần sử dụng mác 40/50 cho các trường hợp đường có quy mô giao thông lớn và đoạn đường xe đi chậm. 62 Trường hợp nhiệt độ mặt đường dự báo trong khoảng 62-640C nên dùng mác 40/50, nếu không có nhựa 40/50 thì có thể dùng mác 60/70 nhưng nên chọn nhựa 60/70 có các chỉ tiêu độ kim lún sát cận dưới. Nên dùng thiết bị DSR để kiểm tra mác nhựa dự kiến sử dụng xem mác nhựa (theo phân mác độ kim lún) đó là chịu được nhiệt độ Tmax nơi sẽ xây dựng đường không. Nếu chọn mác nhựa đường theo phân cấp PG (AASHTO M320: performance. Graded Asphalt Binder) thì về điều kiện nhiệt độ phải chọn mác PG tương ứng với Tmax (T50%max hoặc T98%max và Tmin > -100C). Nếu Tmax trong khoảng 58-640C thì phải chọn mác PG 64-10; nếu Tmax ≥ 640C thì phải chọn mác PG 70-10. Về điều kiện giao thông, nên tham khảo [5] để chọn mác nhựa theo quan điểm: quy mô giao thông càng lớn và tốc độ xe càng chậm (hoặc dừng đỗ) thì mác nhựa càng phải chọn cao lên một cấp (thậm chí là 2 cấp). 2.5.2.3 Sử dụng kết cấu áo đường với lớp BTN lớp mặt trên cũng có khả năng ổn định ở nhiệt độ cao (chống lún vệt bánh cao) và BTN lớp mặt dưới có khả năng chịu mỏi cao. Kết cấu này được đề cập ở “Chỉ dẫn thiết kế mặt đường mềm 2012” của Ấn Độ [38] với tầng mặt hỗn hợp BTN gồm 2 lớp (tổng bề dày tầng mặt không quá 20cm) trong đó lớp trên bằng BTNC chỉ dày 30-50mm (tùy theo quy mô giao thông tính bằng tổng số trục xe 8,2 tấn tích lũy). Phải sử dụng nhựa mác VG40 (tương đương với mác nhựa 40/60 theo độ kim lún) để có khả năng chống lún vệt bánh và đủ sức chịu cắt trượt (ổn định ở nhiệt độ cao) và lớp dưới bằng hỗn hợp đá dăm nhựa chặt DBM (Dense bituminous macadam, tương tự ATB trong tiêu chuẩn JTGF40.2004 của Trung Quốc) dầy từ 6-15cm tùy quy mô giao thông. Lớp DBM của Ấn Độ có 2 loại cỡ hạt lớn nhất danh định là 26,5mm và 37,5mm. Lớp này nên sử dụng mác nhựa VG40 (tương đương mác 40/60 theo độ kim lún) và nếu nằm dưới mặt đường 8-10cm thì có thể dùng mác nhựa VG30 (tương đương mác nhựa 50/70 theo độ kim lún) nhưng đều phải thiết kế hỗn hợp có độ rỗng dư sau khi 63 đầm nén bằng 3% và thể tích nhựa đến 13% (tức là hàm lượng nhựa theo khối lượng hỗn hợp khoảng 4,5% - cao hơn hàm lượng nhựa tối ưu xác định theo phương pháp Marshall 0,5-0,6%) với độ rỗng dư nhỏ và hàm lượng nhựa lớn lớp này sẽ có khả năng chịu mỏi cao đồng thời chống thấm nước tốt (theo [38], hỗn hợp BTN có độ rỗng dư ≤4% có thể xem là không thấm nước trên thực tế). Với những tuyến đường đòi hỏi tuổi thọ dài còn có thể thiết kế hỗn hợp DBM với độ rỗng dư 2%. Theo [38] việc dùng nhựa mác VG40 sẽ giảm được 50% vệt bánh xe so với việc dùng mác VG30. Ở các nước này có nhiệt độ không khí cao nhất lớn hơn 40oC và quy mô xe tải ≥2000 xe/ngày đêm thì cả lớp DBM cũng nên dùng nhựa mác VG40 (mác 40/60 theo độ kim lún). Việc dùng mác nhựa VG40 cho cả lớp DBM cũng hạn chế được hằn lún khi dùng lu nặng đầm nén hỗn hợp DBM. Ngoài việc sử dụng mác nhựa có độ cứng cao, lớp mặt trên bằng BTNC nên bằng hỗn hợp có độ rỗng dư 4-6% với cấp phối cốt liệu thô (khống chế ở cỡ hạt 2,36mm) để tăng khả năng ổn định cắt trượt; do vậy đương nhiên là khả năng chịu mỏi của lớp này sẽ thấp. Nhưng nếu bảo đảm được dính bám tốt giữa lớp BTNC này với lớp DBM ở dưới thì ứng suất kéo – uốn do tải trọng bánh xe gây ra sẽ truyền cả xuống đáy lớp DBM được thiết kế để có khả năng chịu mỏi cao như trên đã đề cập. Do vậy giải pháp bố trí kết cấu với 2 lớp hỗn hợp nhựa có chức năng khác nhau này sẽ càng có hiệu quả nếu giữa chúng càng dính bám chặt với nhau. 2.5.2.4 Bố trí kết cấu nền mặt đường để giảm ứng suất cắt trượt đồng thời giảm được biến dạng kéo (uốn) lớn nhất mà lớp BTN phải chịu. Như đã phân tích ở trên, tuổi thọ mỏi của lớp BTN mặt đường sẽ tăng lên nếu εt do tải trọng trục xe gây ra càng nhỏ. Ngoài việc phụ thuộc vào tải trọng trục lớn hay nhỏ, trị số εt hay ứng suất kéo uốn σku do tải trọng trục gây ra ở đáy lớp BTN còn phụ thuộc vào tỷ số AC ch.m E E (EAC: Mô đun đàn hồi của lớp BTN; Ech.m: Mô đun đàn hồi chung của các lớp phía dưới bao gồm cả nền đất). Qua toán đồ tính toán ứng suất σku ở đáy lớp mặt BTN trong [24] xuất phát từ lời giải của bài toán phân tích hệ số đàn 64 hồi nhiều lớp, ta có thể thấy: nếu cùng lớp BTN được đặt trên các lớp dưới có Ech.m càng lớn (tức là tỷ số AC ch.m E E càng nhỏ) thì ứng suất kéo – uốn đơn vị càng nhỏ và tuổi thọ mỏi của lớp BTN đó sẽ tăng lên. Về ứng suất cắt trượt, theo toán đồ tính ứng suất cắt trượt ở tiêu chuẩn 22TCN- 211-06 [24] cũng cho thấy điều tương tự: tỷ số AC ch.m E E càng nhỏ, tức là Ech.m càng lớn thì ứng suất cắt trượt do tải trọng trục xe gây ra trong lớp BTN mặt đường cũng nhỏ đi. Các nhận xét nói trên cho thấy, nếu lớp mặt BTN được đặt trên các lớp móng cứng (có mô đun đàn hồi cao) thì sẽ có lợi cả về mặt chịu mỏi và chịu cắt trượt. 2.6 Nhận xét chương 2 Dưới tác dụng của tải trọng bánh xe, bê tông nhựa thuộc tầng mặt chịu đồng thời lực tác dụng theo hai phương thẳng đứng và theo phương ngang. Do đó, mỗi phân tố trong kết cấu mặt đường đều xuất hiện trạng thái ứng suất với đầy đủ thành phần ứng suất tiếp và ứng suất pháp. Khi tải trọng nặng tăng lên, kết hợp với nhiệt độ cao, bê tông nhựa thuộc tầng mặt có thể bị phá hoại ở trạng thái chịu cắt. Về mặt vĩ mô, toàn bộ kết cấu có thể xuất hiện các tình trạng điển hình như xô dồn vật liệu, vệt hằn bánh xe. Xét riêng cho từng phân tố bê tông nhựa, sẽ xuất hiện hiện tượng phá hoại do cắt trượt. Trên mặt phá hoại, theo lý thuyết đã trình bày ở chương 1 (Mohr-Coulomb), trên mặt phá hoại sẽ hình thành các ứng suất cắt ff và ứng suất pháp ff, quan hệ với nhau theo phương trình (2-1) 𝜏𝑓𝑓 = 𝜎𝑓𝑓𝑡𝜑 + 𝑐 Từ đó, nhiều học giả trên thế giới đã và đang đi theo hướng nghiên cứu về các đặc trưng kháng cắt c, tg để phục vụ cho việc thiết kế được loại bê tông nhựa có sức kháng cắt cao, chống được hằn lún bánh xe. 65 Do vậy, việc nghiên cứu xác định góc nội ma sát và lực dính của bê tông nhựa là cần thiết và là một hướng đi có tính khoa học, tính thực tiễn. Trong điều kiện của Việt Nam, trước hết, cần phải tìm được một phương pháp thí nghiệm phù hợp để xác định được hai đặc trưng này, là cơ sở để triển khai các nghiên cứu khác liên quan tới mục đích chế tạo được loại bê tông nhựa có sức kháng cắt cao. Nội dung về phương pháp thí nghiệm sẽ được trình bày ở chương 3 của luận án. 66 Chương 3. LỰA CHỌN PHƯƠNG PHÁP THÍ NGHIỆM XÁC ĐỊNH ĐẶC TRƯNG KHÁNG CẮT CỦA BTN TRONG ĐIỀU KIỆN VIỆT NAM 3.1 Mở đầu Sự cần thiết phải nghiên cứu, xác định các đặc trưng kháng cắt (lực dính c, góc nội ma sát ) của bê tông nhựa đã được trình bày ở chương 1, 2. Tuy nhiên, trong điều kiện hiện nay của Việt Nam, chưa có một phương pháp và thiết bị chính thức cho phép xác định được các đặc trưng trên. Do vậy, phần tiếp theo của luận án sẽ được xây dựng với mục đích sau: - Phân tích, tổng hợp các phương pháp thí nghiệm xác định sức kháng cắt/đặc trưng kháng cắt của bê tông nhựa trên thế giới; - Đề xuất lựa chọn phương pháp phù hợp với điều kiện Việt Nam; - Chế tạo, hoàn chỉnh và xác định điều kiện áp dụng của thiết bị thí nghiệm theo phương pháp đã lựa chọn. 3.2 Phân tích, đánh giá các phương pháp thí nghiệm xác định đặc trưng kháng cắt của bê tông nhựa Qua tổng quan các nghiên cứu trên thế giới về phương pháp thí nghiệm xác định các đặc trưng kháng cắt của bê tông nhựa, các phương pháp, thiết bị thí nghiệm hiện hành có thể xếp vào hai nhómchính: - Hướng thứ nhất: Xác định trực tiếp sức chống cắt thông qua thí nghiệm cắt và nén đồng thời, trong đó có cả thí nghiệm nén ba trục. - Hướng thứ 2: Tiến hành riêng rẽ các thí nghiệm nén theo phương dọc trục và theo đường sinh của mẫu hình trụ. Sau đó, dựa trên một số giả thuyết về bảo toàn năng lượng (công), xác định góc nội ma sát và lực dính c. 67 3.2.1 Các thí nghiệm theo hướng thứ nhất 3.2.1.1 Thí nghiệm cắt SST- Superpave Shear Test Thí nghiệm này được quy định tại tiêu chuẩn AASHTO T320-07 (2016) [28],[32][50] thực hiện theo sơ đồ và hệ thống thiết bị như hình 3.1. Hình 3.1 Sơ đồ và thiết bị thí nghiệm SST [32] Mẫu thí nghiệm hình trụ có đường kính từ 100 đến 150 mm (không nhỏ hơn 3 lần chiều cao mẫu), chiều cao 38mm hoặc 50mm được gắn chặt vào hai đĩa thép 1 (thuộc cơ cấu ra lực thẳng đứng) và 2 (thuộc cơ cấu ra lực ngang). Trong thí nghiệm SST này, mẫu bê tông nhựa hình trụ được chế tạo theo phương pháp Superpave và được cắt theo sơ đồ hình 3.2 bằng tải trọng lặp để xác định ra mô đun cắt động G*, góc trễ pha và biến dạng cắt lớn nhất max xuất hiện trong mẫu bê tông nhựa. Hình 3.2 Sơ đồ cắt bê tông nhựa theo SST [32] 68 Theo [32] khi chịu lực cắt theo sơ đồ hình 3.2, trong hỗn hợp bê tông nhựa, các thành phần hạt có hiện tượng trượt lên nhau, làm tăng kích thước (theo phương vuông góc với phương tác dụng lực) của hỗn hợp như đã trình bày ở mục 2.2.4. Đó chính là lý do trong thí nghiệm SST, đã bổ sung thêm lực nén lên mẫu theo phương thẳng đứng nhằm mục đích chính là hạn chế sự thay đổi của chiều cao mẫu. Đây là một nội dung rất quan trọng. Từ chuyển vị thẳng đứng của mẫu đo được, máy sẽ tự động điều chỉnh lực nén để đảm bảo mẫu vẫn giữ được chiều cao không đổi so với ban đầu. Yêu cầu này đòi hỏi cơ cấu đo đạc chuyển vị liên kết được với hệ thống thiết bị nén, rất phức tạp, đắt tiền. Cùng với sơ đồ trên, thí nghiệm SST có thể tiến hành theo các cách phổ biến sau: Thí nghiệm cắt đơn giản với chiều cao không đổi (SSCH). Thí nghiệm này theo nguyên lý tác dụng lên mẫu một ứng suất cắt có độ lớn 7 kPa với số chu kỳ là 100. Sau đó tăng ứng suất cắt tác dụng lên mẫu với tốc độ là 70 kPa/giây và giữ trong khoảng thời gian 10 giây. Sau 10 giây, giảm ứng suất cắt xuống còn 0 với tốc độ 21 kPa/giây. Tiếp tục ghi số liệu thêm 30 giây nữa sau khi tải trọng đã về 0. Thí nghiệm được thực hiện ở các nhiệt độ 4oC, 20oC và 40oC. Kết quả thí nghiệm thu được là ứng suất dọc trục, ứng suất cắt và biến dạng cắt. Thí nghiệm cắt tải trọng lặp với chiều cao không đổi (RSCH). Theo thí nghiệm này, một ứng suất cắt có dạng nửa hình sin với số chu kỳ là 100, thời gian tác dụng 0.1 giây, nghỉ 0,6 giây với ứng suất tác dụng dọc trục không vượt quá 7 kPa được tác dụng lên mẫu. Tiếp theo, tác dụng lên mẫu một ứng suất cắt có dạng nửa hình sin có độ lớn 70 kPa với số chu kỳ là 5000, thời gian tác dụng 0.1 giây, nghỉ 0.6 giây. Nhiệt độ thí nghiệm là nhiệt độ trung bình của 7 ngày trong năm đo ở độ sâu 50,8 mm ở kết cấu mặt đường. Kết quả thí nghiệm thu được là ứng suất dọc trục, ứng suất cắt và biến dạng cắt. Thí nghiệm cắt tải trọng lặp với tỷ lệ ứng suất không đổi (RSCSR). Tiến hành tác dụng lên mẫu đồng thời một ứng suất dọc trục và ứng suất cắt có dạng nửa hình sin có độ lớn sao cho tỷ lệ giữa ứng suất dọc trục và ứng suất cắt là không đổi và bằng 69 từ 1,1 đến 1,5 lần. Nhiệt độ chọn để thí nghiệm là nhiệt độ trung bình của 7 ngày trong năm đo ở độ sâu mặt đường là 50,8 mm. Nhận xét: - Việc áp dụng một lực nén dọc trục lên mẫu thí nghiệm xác định sức chống cắt của Bê tông nhựa là rất cần thiết, để đảm bảo cho thí nghiệm được sát với trạng thái chịu cắt của bê tông nhựa ở ngoài thực tế; - Lực nén dọc trục vừa nêu cũng giúp cho sơ đồ thí nghiệm gần với lý thuyết của Mohr – Culomb; - Mẫu và kết quả thí nghiệm (mô đun cắt động G*, góc trễ pha và ứng suất cắt lớn nhất max ) tuân thủ theo phương pháp Superpave, phù hợp với điều kiện của Hoa Kỳ, nhưng lại chưa có trong hệ thống tiêu chuẩn Việt Nam hiện hành (cho bê tông nhựa); Thí nghiệm không cho phép xác định các đặc trưng kháng cắt (lực dính c, góc nội ma sát ) của bê tông nhựa. - Việc xác định giá trị lực nén theo chiều cao mẫu ở đây rất phức tạp, đòi hỏi cơ cấu thủy lực và sen sen sơ hiện đại, đắt tiền. - Hệ thống thiết bị sử dụng trong thí nghiệm này rất đắt tiền, hiện chưa phổ cập tại Việt Nam; 3.2.1.2 Thí nghiệm DST (Duplicate Shear Tester) Như trình bày ở trên, với ngay các đơn vị nghiên cứu tại Mỹ thì hệ thống thí nghiệm SST vẫn chưa được áp dụng rộng rãi vì các lý do: chi phí cao, phức tạp trong chế tạo mẫu và vận hành thí nghiệm [28],[29][51]. Do vậy, Đại học Texas đã phát triển phương pháp thí nghiệm DST đơn giản hơn, có khả năng áp dụng rộng rãi hơn SST [29] nhưng vẫn cho phép xác định các đặc trưng chống cắt như SST. Cơ cấu thí nghiệm được trình bày trên hình 3.3. Các điểm thay đổi cơ bản so với thí nghiệm SST là: - Việc cắt mẫu được tiến hành cho 2 mẫu cùng một lúc. 70 - Để hạn chế sự thay đổi chiều cao của mẫu khi cắt, hai mẫu được gắn vào hệ thống khung và đĩa kim loại như hình 3.3. Hệ thống các đĩa thép và khung cứng có tác dụng hạn chế các mẫu bị thay đổi chiều cao. Đĩa hợp kim nhôm ở giữa có vai trò truyền lực cắt từ bộ phận gia tải lên mẫu. Hình 3.3 Sơ đồ thí nghiệm DST [29] Các điều kiện khác về chế tạo mẫu, nhiệt độ thí nghiệm, lực tác dụng đều giống như thí nghiệm SST, để cho ra kết quả cuối cùng là mô đun cắt động G*, góc trễ pha và biến dạng cắt lớn nhất max Nhận xét: Về cơ bản, phương pháp thí nghiệm này vẫn có những đặc điểm giống như đối với thí nghiệm SST, trong đó vẫn giữ được lực nén tác dụng lên mẫu thông qua cơ cấu khung cứng. Điểm khác cơ bản là sử dụng 2 mẫu một lúc, và chỉ sử dụng hệ thống khung cứng để hạn chế sự phát triển chiều cao của mẫu. Về hệ thống thiết bị, vẫn đòi hỏi phải sử dụng các thiết bị đắt tiền, theo hệ thống superpave, chưa có ở Việt Nam. 3.2.1.3 Thí nghiệm FST (Field Shear Test) Thí nghiệm này được phát triển trong chương trình nghiên cứu NCHRP (dự án 9-18) [52]. Theo đó, mẫu thí nghiệm và các điều kiện thí nghiệm (lực, nhiệt độ) cũng tương tự phương pháp SST, với “chiều cao” mẫu theo phương đường kính 71 không đổi (nhờ hệ thống khung cứng) . Điểm khác biệt là mẫu hình trụ được cắt theo phương đường kính (hình 3.4a), với hệ thống thiết bị như ở hình 3.4b. a. Vị trí cắt mẫu b. Khuôn cắt mẫu theo FST Hình 3.4 Nguyên lý và khuôn cắt mẫu trong thí nghiệm cắt theo FST [52] Các kết quả thí nghiệm theo phương pháp này đã chỉ ra rằng, mô đun cắt động G*, góc trễ pha và ứng suất cắt lớn nhất max có giá trị phân tán, ít tập trung, do diễn biến ứng suất trên mặt cắt đi qua đường sinh tương đối phức tạp. Nhận xét: - Về hệ thống thiết bị, vẫn đòi hỏi phải sử dụng các thiết bị đắt tiền, theo hệ thống superpave, chưa có ở Việt Nam. - Do mẫu cắt theo đường sinh nên kết quả thí nghiệm phụ thuộc không những vào đường kính mà còn theo chiều cao mẫu. Do vậy, khi áp dụng với mẫu khoan ngoài hiện trường (có chiều dày thay đổi) thì cần phải xây dựng hệ thống các tham số điều chỉnh (như chúng ta đang làm với thí nghiệm Marshall ở Việt Nam). Việc này rất công phu và tốn kém. 72 3.2.1.4 Thí nghiệm cắt phẳng Leutner Thí nghiệm cắt phẳng Leutner (Leutner test) được phát triển ở Đức vào cuối những năm 1970, hình 3.5. Hiện nay, mô hình thí nghiệm cắt phẳng Leutner được sử dụng phổ biến trong các tiêu chuẩn ở các nước Đức, Anh, Thụy Sĩ, Australia và phần lớn các nước châu Âu khác. Hình 3.5 Mô hình và thiết bị Leutner [40],[52][55][58] Đây là một thiết bị đơn giản để thí nghiệm cắt trực tiếp nhằm xác định lực dính giữa hai lớp bê tông nhựa. Thí nghiệm được thực hiện với mẫu thử hình trụ đường kính 150 mm hoặc 101,6 mm được tạo thành từ ít nhất hai lớp bê tông nhựa. Mẫu thử có thể được khoan từ hiện trường hoặc được chế bị trong phòng thí nghiệm. Cơ chế của phương pháp này là tác dụng một lực cắt tập trung không đổi để tạo ra một tốc độ chuyển vị cắt không đổi tại mặt tiếp xúc giữa hai lớp bê tông nhựa. Tốc độ chuyển vị cắt không đổi theo tiêu chuẩn là 50,8 mm/phút. Vì vậy, thiết bị thí nghiệm Marshall hoặc thiết bị thí nghiệm CBR có thể được sử dụng cho mô hình thí nghiệm cắt Leutner. So với thí nghiệm SST thì thiết bị thí nghiệm Leutner đơn giản hơn. Tuy nhiên, nhược điểm của phương pháp này là ứng suất cắt không đồng nhất trong quá trình cắt [40],[52][58], chưa xét đến áp lực dọc trục tác dụng lên mẫu thử. Thí nghiệm được thực hiện ở các nhiệt độ khác nhau từ 10oC-60oC. 73 Nhận xét: Đặc điểm của thí nghiệm này là chỉ xét đến cắt phẳng, chưa xét được thành phần ứng suất nén dọc trục, chiều cao mẫu vẫn thay đổi. Do vậy, kết quả thu được chủ yếu liên quan đến lực dính. 3.2.1.5 Thí nghiệm cắt NCAT Các phương pháp thí nghiệm cắt phẳng Leutner chỉ tiến hành thí nghiệm cắt phẳng mà chưa xét đến tác dụng của lực nén dọc trục do ảnh hưởng của áp lực thẳng đứng của bánh xe cũng như ma sát mặt đường gây ra. Để cải tiến các thí nghiệm nêu trên, Trung tâm công nghệ nhựa quốc gia (NCAT) Mỹ đã chế tạo bộ thiết bị thí nghiệm cường độ cắt NCAT có bổ sung bộ phận gia tải dọc trục nêu trên (hình 3.6) [57]. Bộ thiết bị này cũng được gá lắp vào các thiết bị nén truyền thống phù hợp hoặc thiết bị Marshall. Lực dọc trục thường được áp dụng ba mức, ở 0, 69, và 138 kPa. Hình 3.6 Thiết bị cắt NCAT [55][56][57] Nhiệt độ thí nghiệm mẫu thử thường ở ba chế độ 10 oC, 25 oC và 60oC. Tốc độ cắt duy trì ở 50,8mm/phút. Công thức tính cường độ chịu cắt cũng tương tự như phương pháp Leutner. Nhận xét: - Thí nghiệm này không đề cập tới giá trị lực dính c và góc nội ma sát ; 74 - So với các thí nghiệm cắt phẳng, thì thí nghiệm này đã đưa được vào áp lực dọc trục. Tuy nhiên, các giá trị áp lực này là cố định. Trong khi đó, theo phương trình của lý thuyết Mohr Culomb thì các giá trị 𝜎, 𝜏 ứng với thời điểm mẫu bị phá hoại. Với các mẫu khác nhau, bê tông nhựa khác nhau, thì hai thành phần ứng suất này có thể thay đổi khác nhau. 3.2.1.6 Thí nghiệm cắt LPDS (Layer Parallel Direct Shear) [40] Trên cơ sở nguyên lý của thiết bị thí nghiệm Leutner, bộ thiết bị Leutner được hiệu chỉnh thành thiết bị cắt trực tiếp lớp song song (cắt phẳng trực tiếp) LPDS. Nhờ đó, thiết bị LPDS được gá lắp dễ dàng vào thiết bị thí nghiệm Marshall để thí nghiệm (hình 3.7) [63, 64]. Bộ thiết bị LPDS đã trở thành thiết bị thí nghiệm tiêu chuẩn của Thụy Sĩ. Khi mẫu thử bị phá hoại do cắt, giá trị lực cắt Pmax (N) được nghi lại. Sau đó, cường độ cắt SB (MPa) được tính toán theo công thức sau: max B 2 4P S = πD (3-1) Trong đó: D – Là đường kính mẫu thử, mm Hình 3.7 Sơ đồ và nguyên lý của thiết bị LPDS [40] 75 Phương pháp này cũng tương tự như phương pháp cắt phẳng Leuner, là chỉ áp dụng được lực cắt, thiếu lực nén dọc trục. 3.2.1.7 Phương pháp cắt động (Ronmanoschi) Để xác định sức chống cắt của lớp dính bám giữa các lớp bê tông nhựa, Romanoschi và Metcalf đã chế tạo thiết bị thí nghiệm như hình 3.8 [48][59] Hình 3.8 Mô hình thí nghiệm cắt lớp dính bám giữa các lớp bê tông nhựa [48][59] Về nguyên lý hoạt động của thí nghiệm, mẫu bê tông nhựa sẽ chịu cắt theo sơ đồ trên hình 3.9. Trên mặt phẳng AB, mẫu bê tông nhựa chịu lực tác dụng theo hai phương, với các lực thành phần Hình 3.9 Sơ đồ cắt mẫu bê tông nhựa theo Romanoschi [48][59] 76 (3-2) Lực Px gây ra ứng suất cắt, lực Py gây ra ứng suất nén . Theo lý thuyết về cường độMohr-Coulomb, ở trạng thái phá hoại theo phương AB, ứng suất cắt ff trên mặt AB có quan hệ như sau ff=ff tg+c (3-3) Với , c lần lượt là góc nội ma sát và lực dính của hỗn hợp bê tông nhựa. Với mỗi góc cắt α khác nhau của thiết bị thí nghiệm, ta có được một phương trình tương quan ứng với trạng thái ứng suất tương ứng. Do đó, nếu sử dụng hai góc cắt khác nhau, ta sẽ thu được hai phương trình tương ứng với hai trạng thái ứng suất. Từ đó thiết lập được hệ phương trình: ff1 =ff1 tg+c (3-4) ff2 =ff2 tg+c Từ đó, có thể tìm ra được , c là nghiệm của hệ phương trình trên: { 𝑡𝑔 = 𝑡𝑓𝑓2−𝑡𝑓𝑓1 𝜎𝑓𝑓2−𝜎𝑓𝑓1 𝑐 = 𝑡𝑓𝑓1 − 𝜎𝑓𝑓1 𝑡𝑓𝑓2−𝑡𝑓𝑓1 𝜎𝑓𝑓2−𝜎�
File đính kèm:
luan_an_nghien_cuu_cac_dac_trung_khang_cat_cua_be_tong_nhua.pdf
Ngô LâmTrích yếu luận án.PDF
Ngô Lâm Tom tat luan an.pdf
Ngô Lâm tóm tắt luận án tiếng Anh.pdf
Ngô Lâm New contribution.PDF
Ngô Lâm đóng góp mới của luận án.PDF