Luận án Nghiên cứu ảnh hưởng của gia nhiệt khuôn phun ép bằng khí nóng đến độ bền sản phẩm nhựa dạng thành mỏng
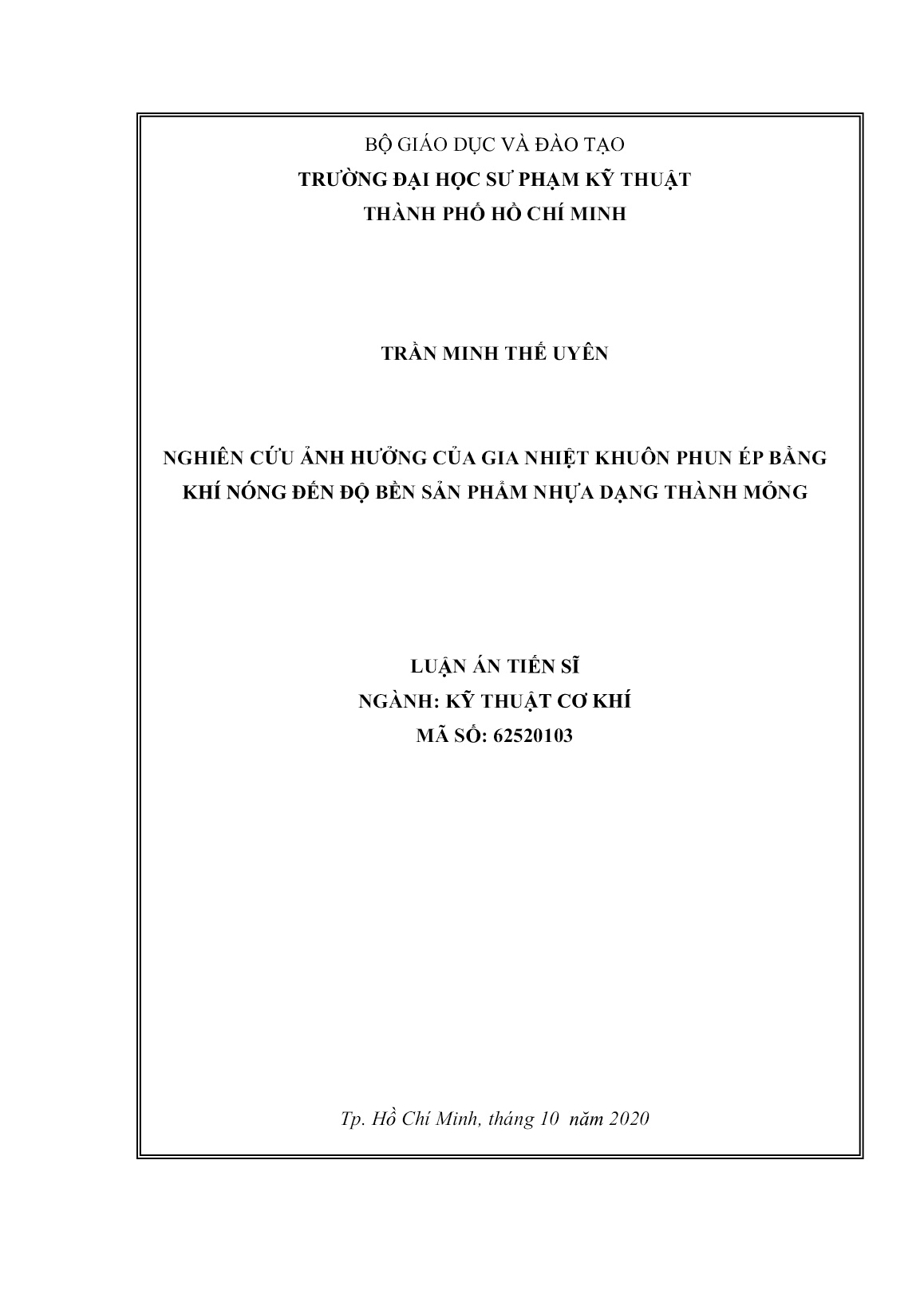
Trang 1
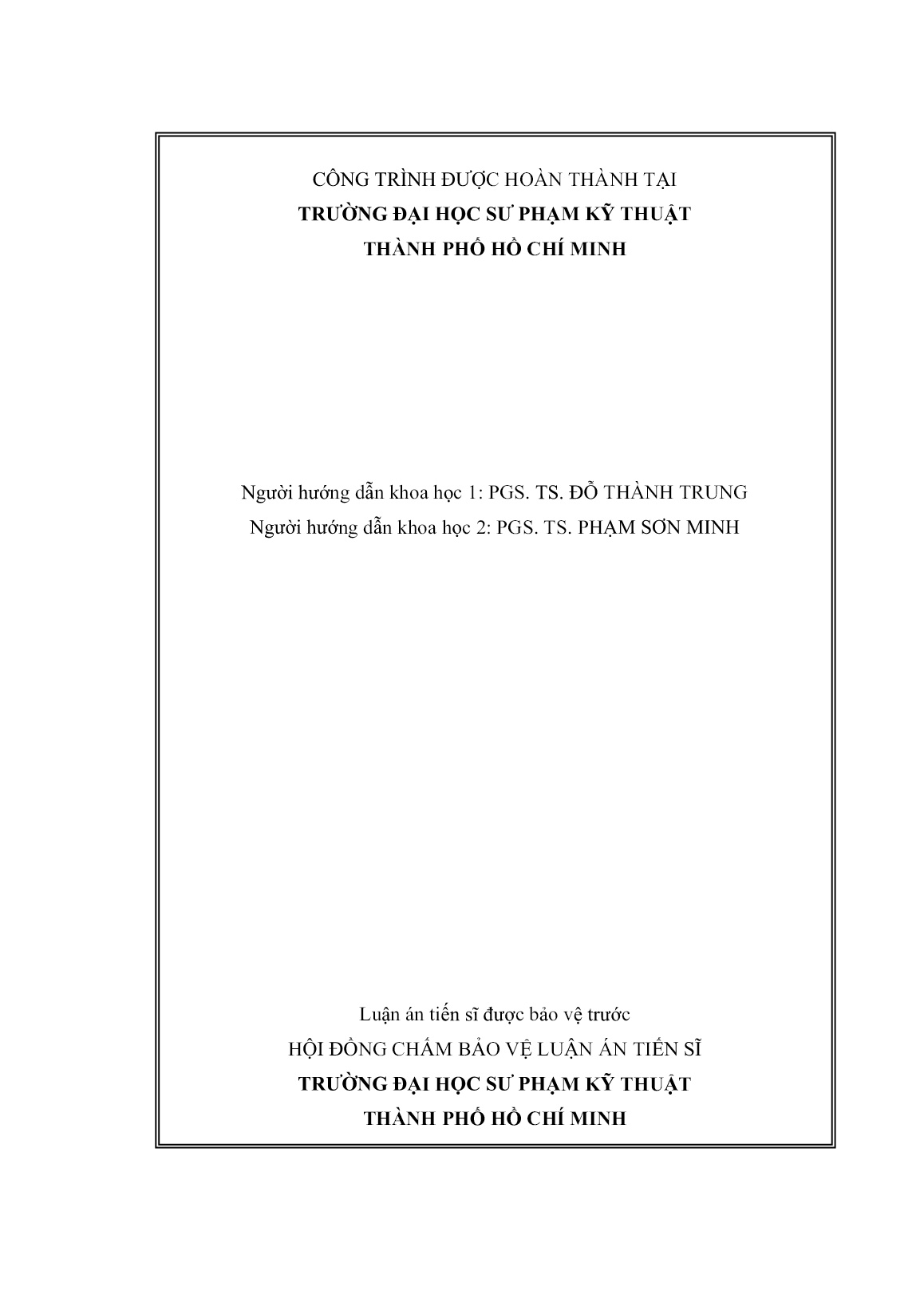
Trang 2
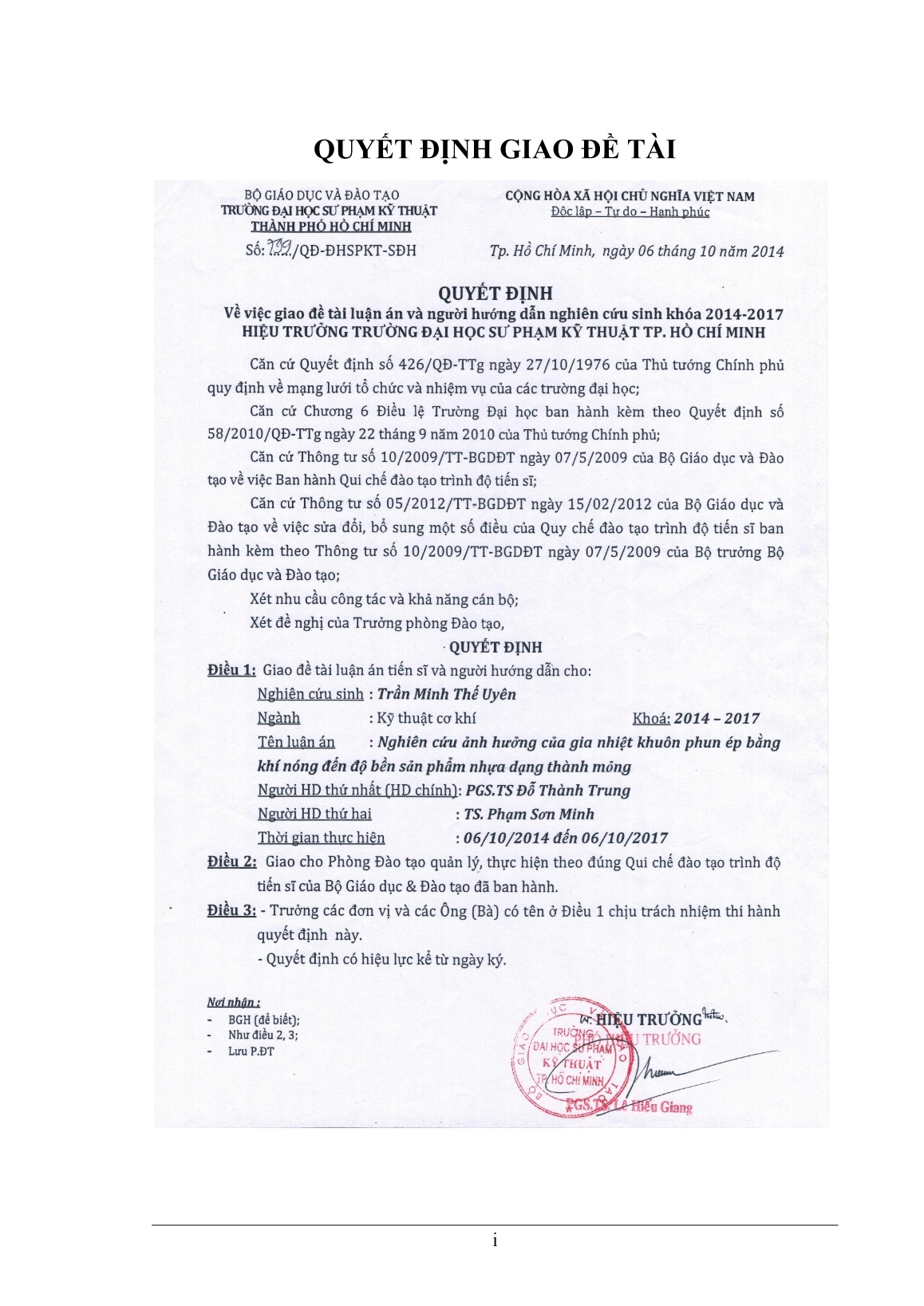
Trang 3
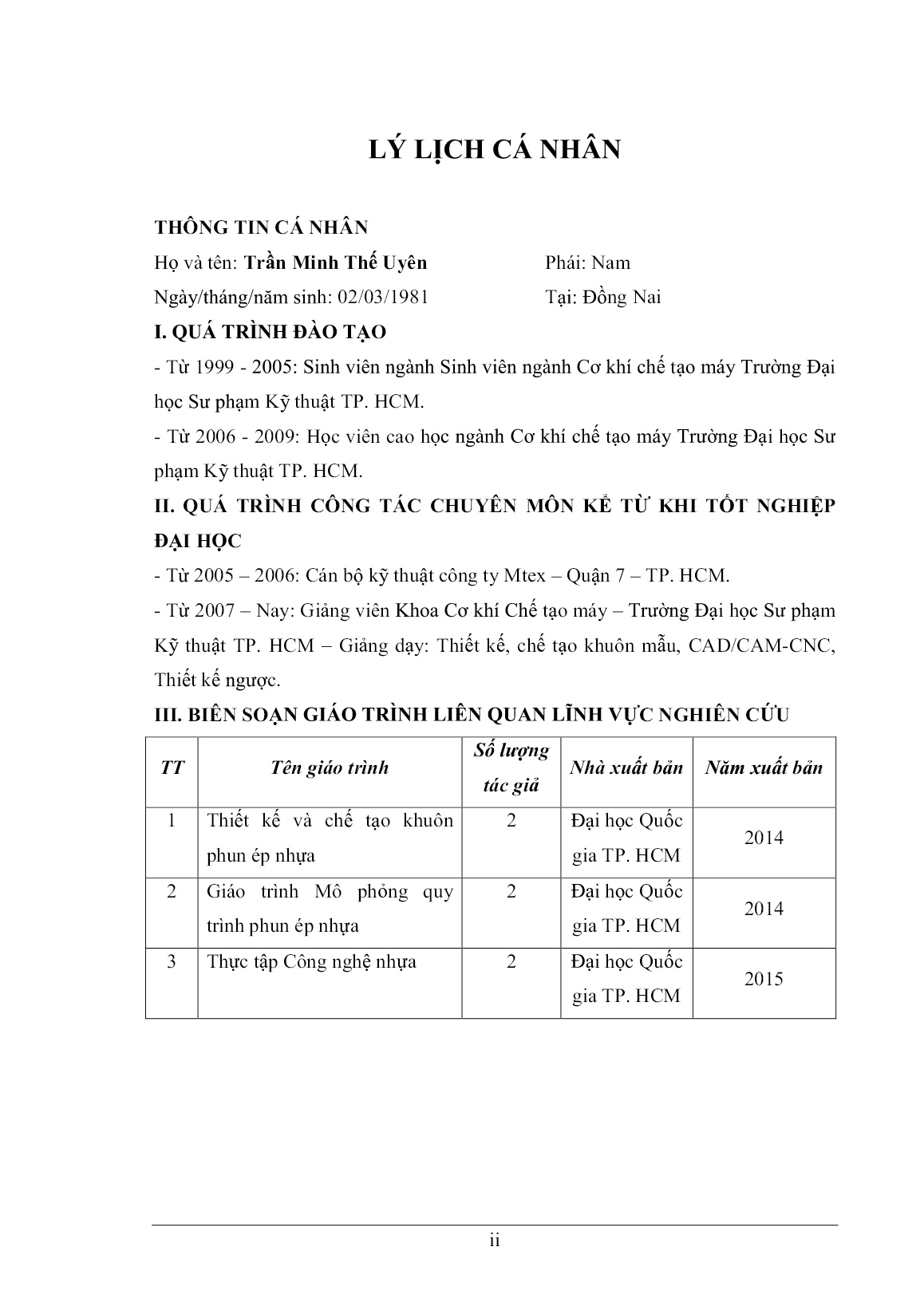
Trang 4
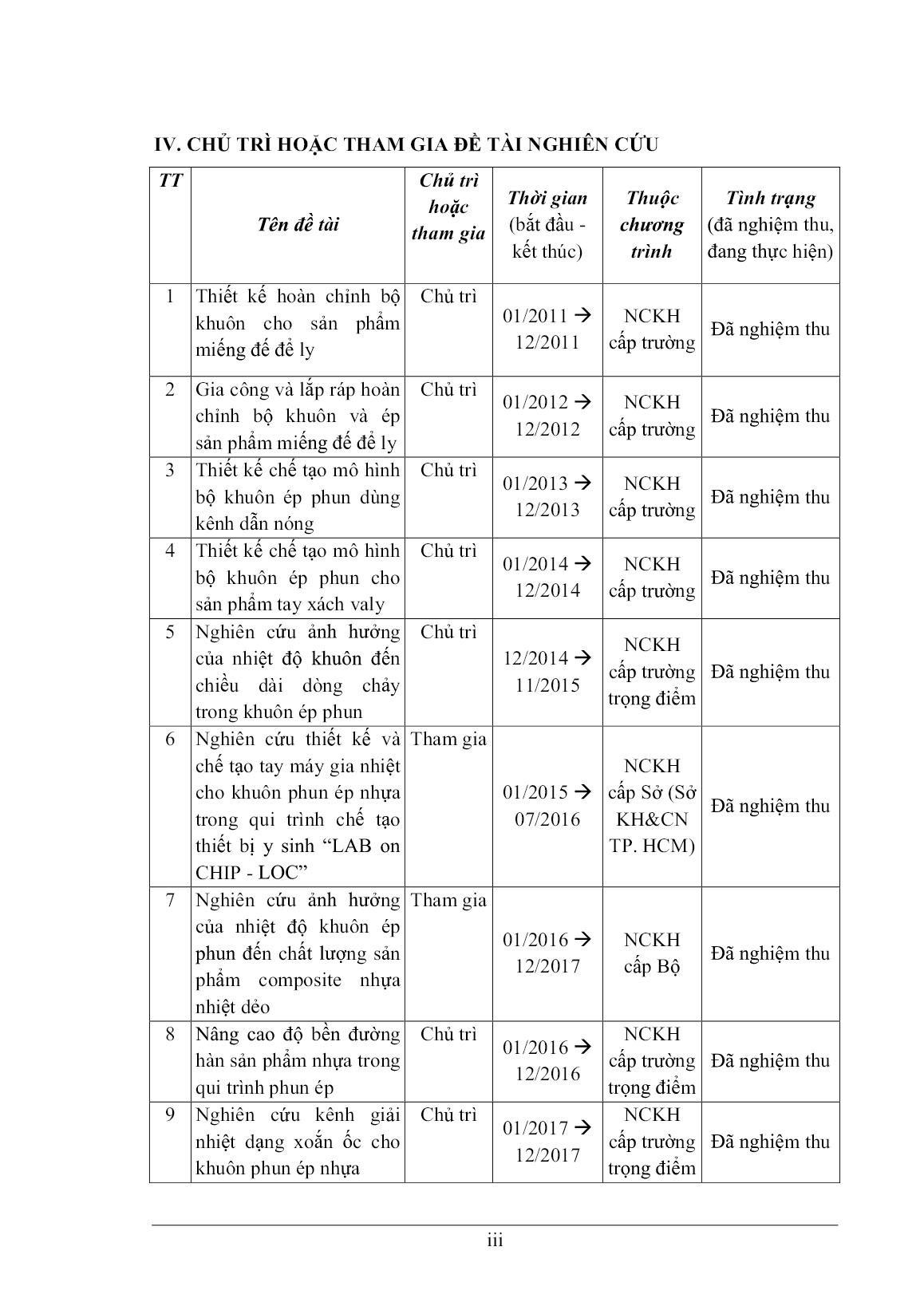
Trang 5
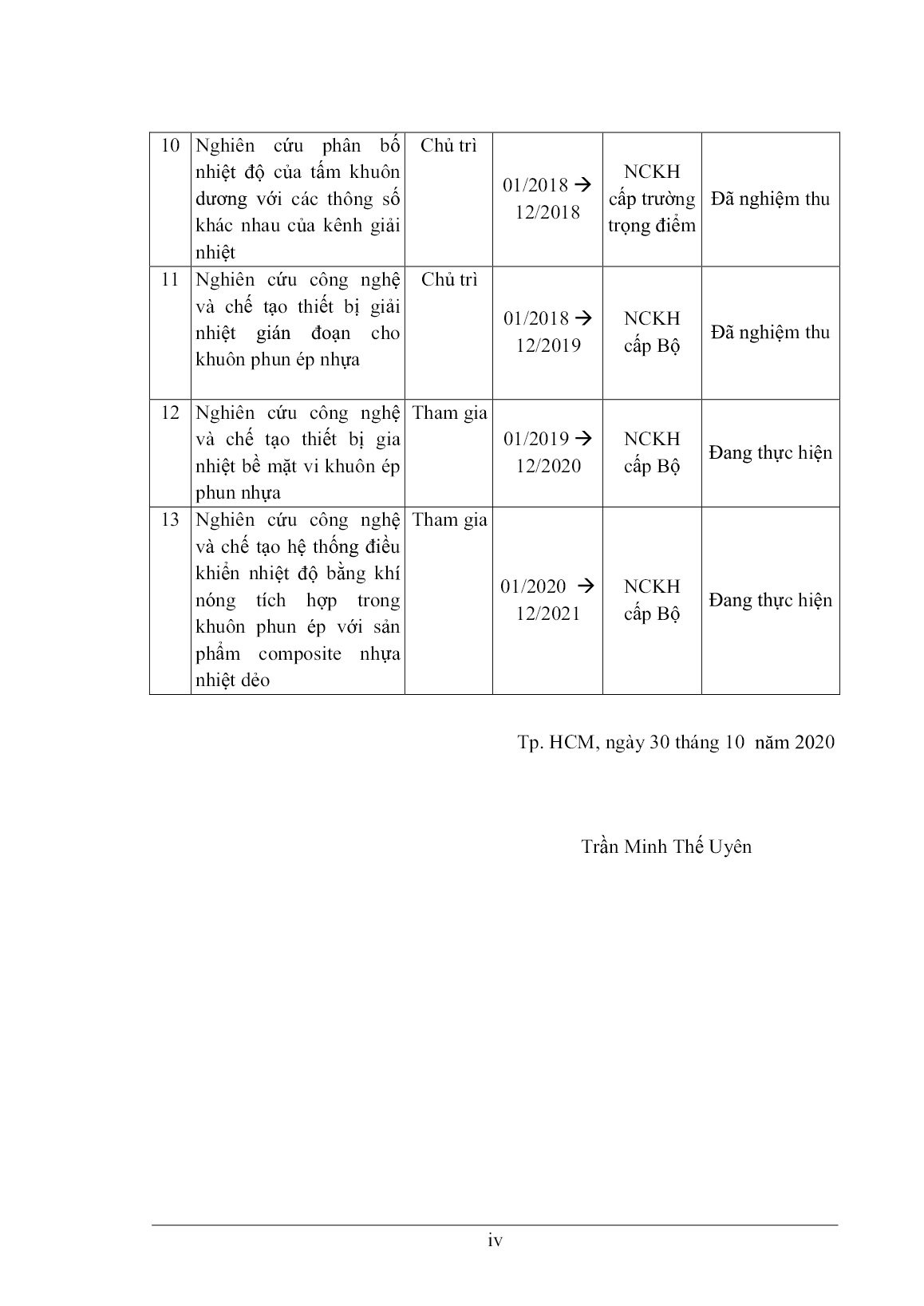
Trang 6
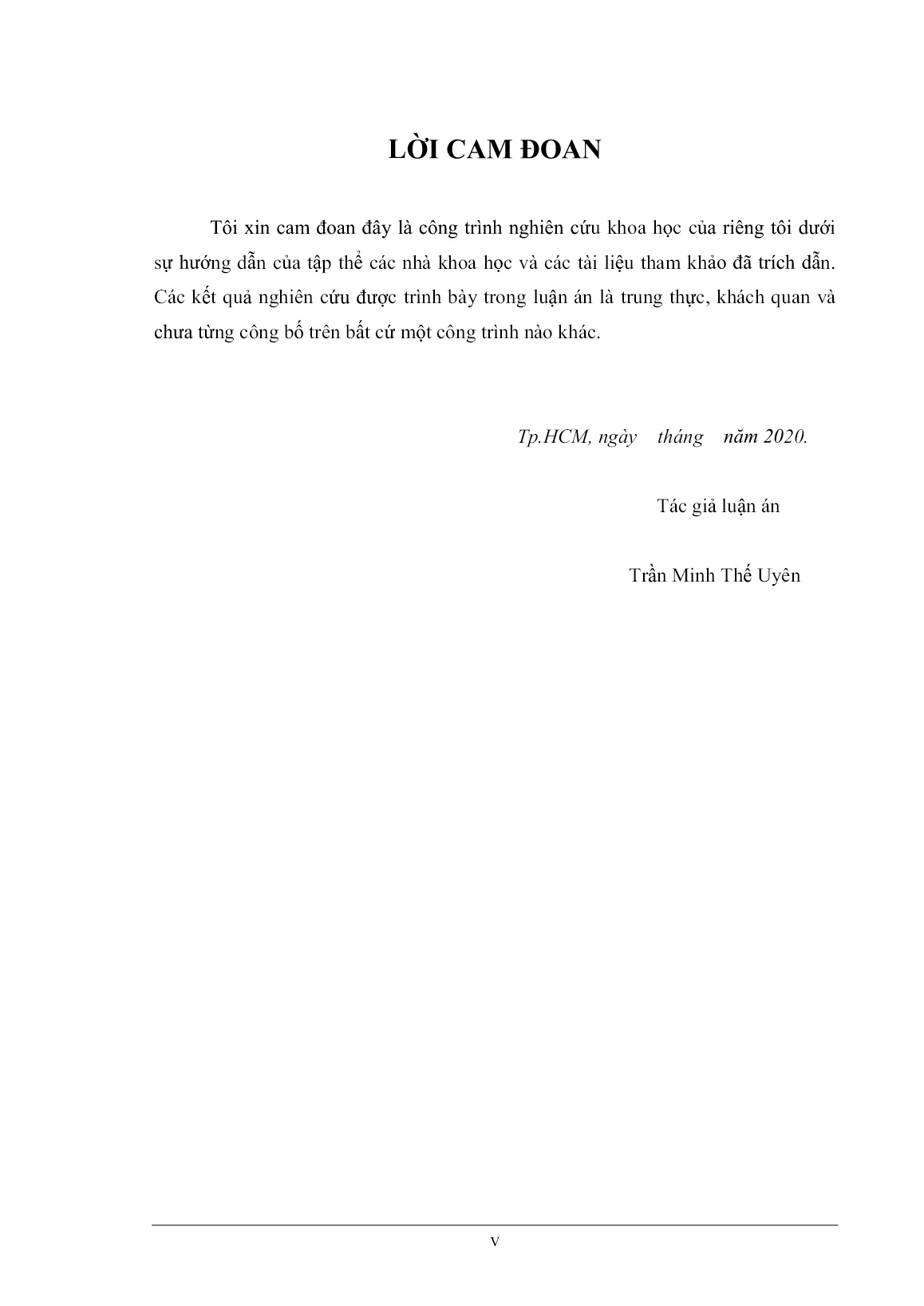
Trang 7
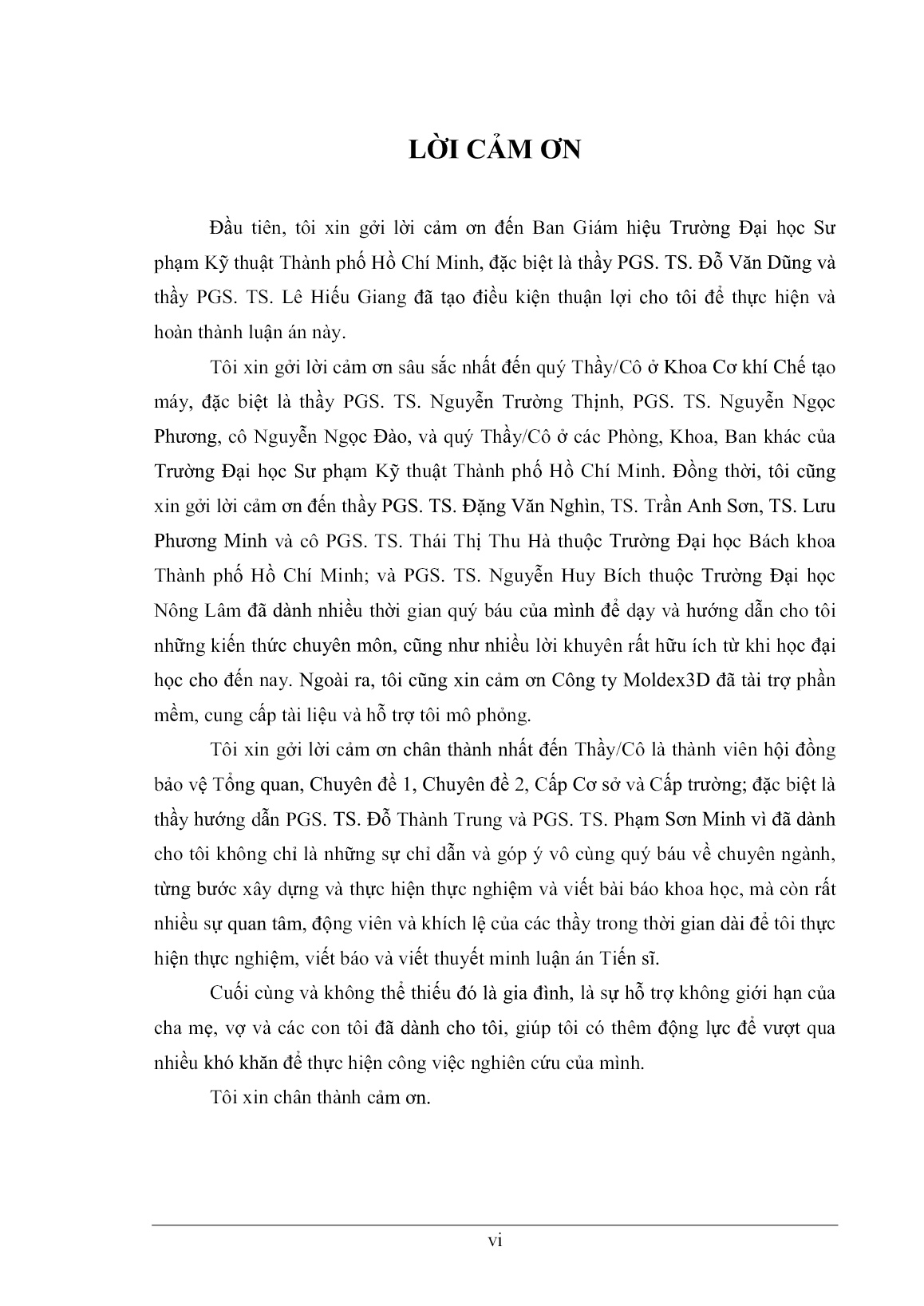
Trang 8
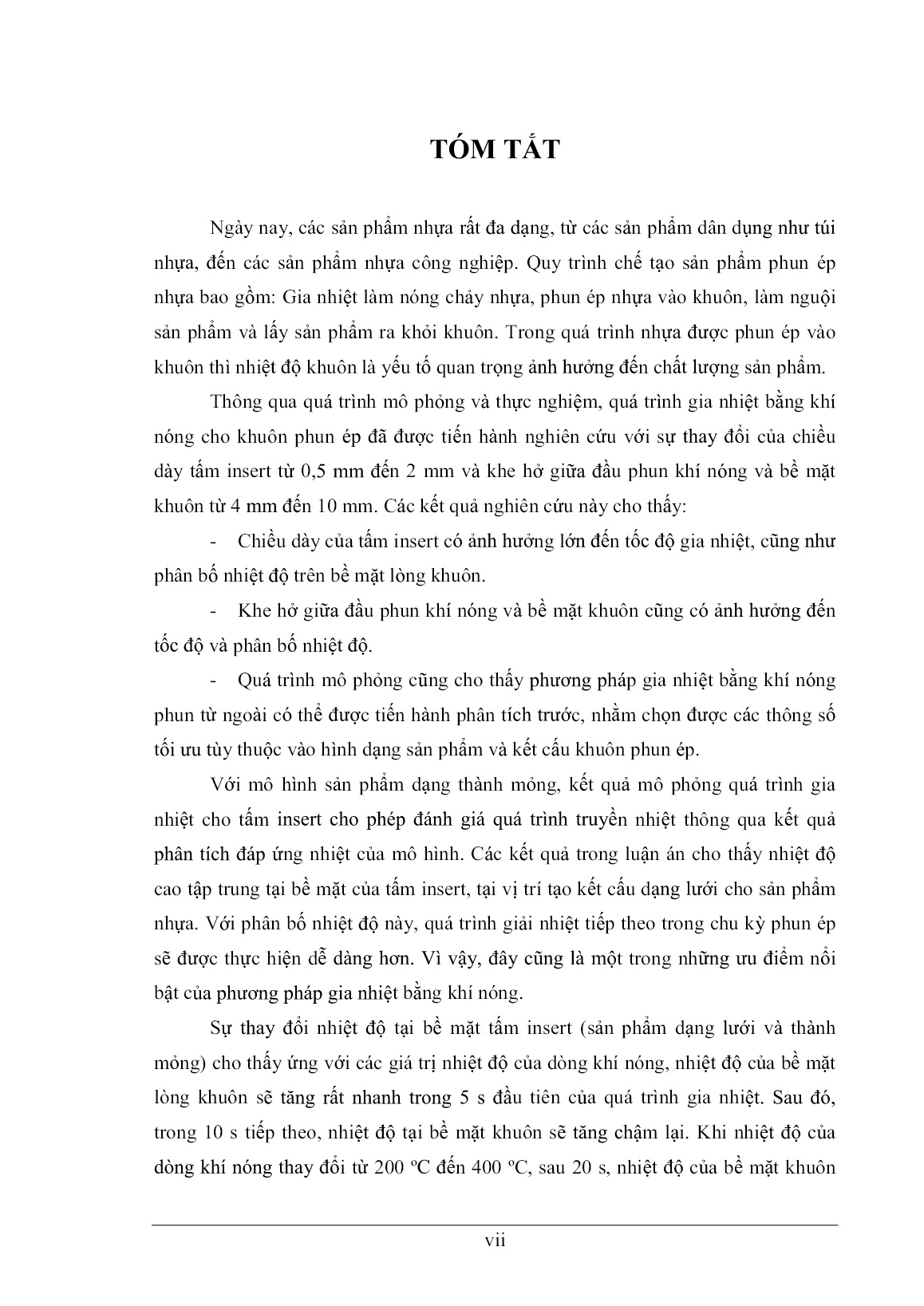
Trang 9
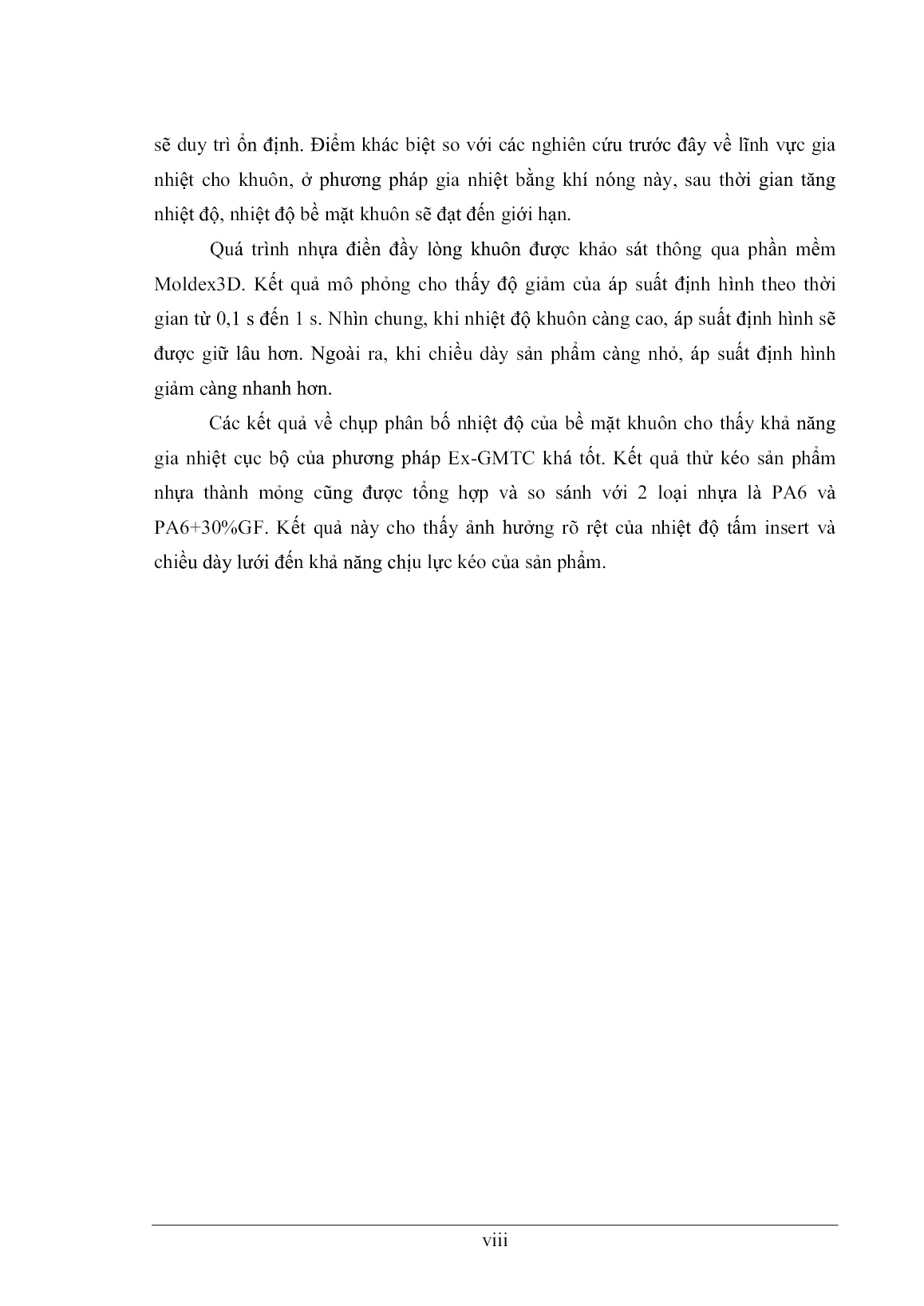
Trang 10
Tải về để xem bản đầy đủ
Bạn đang xem 10 trang mẫu của tài liệu "Luận án Nghiên cứu ảnh hưởng của gia nhiệt khuôn phun ép bằng khí nóng đến độ bền sản phẩm nhựa dạng thành mỏng", để tải tài liệu gốc về máy hãy click vào nút Download ở trên.
Tóm tắt nội dung tài liệu: Luận án Nghiên cứu ảnh hưởng của gia nhiệt khuôn phun ép bằng khí nóng đến độ bền sản phẩm nhựa dạng thành mỏng
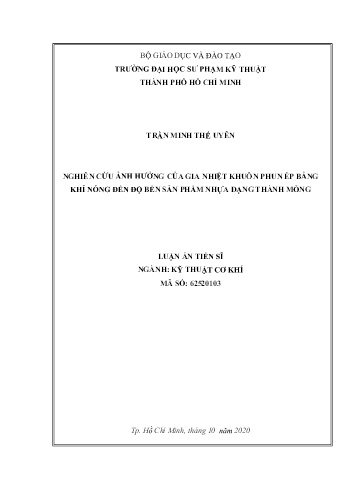
y nhựa sẽ bị mất nhiệt, giảm nhiệt độ [102]. Do đó, tại bề mặt tiếp xúc giữa nhựa và lòng khuôn sẽ hình thành lớp nguội (Frozen layer). Chính hiện tượng đông đặc nhanh này, dòng chảy nhựa sẽ có những đặc điểm không giống như dòng chảy thông thường. Trong lĩnh vực phun ép nhựa, dòng chảy nhựa trong lòng khuôn tuân thủ theo các tính chất của dòng chảy Fountain Flow với các đặc điểm như: Phần nhựa tại tâm dòng chảy sẽ chảy nhanh hơn phần nhựa gần với lòng khuôn. Trong đó, tại vị trí tiếp xúc với lòng khuôn, nhựa được xem như không chảy. Nhựa tại đầu dòng chảy được ép về phía trước và bị cuốn về phía lòng khuôn (hình 2.16). Kết quả của hiện tường này là: trong quá trình nhựa điền đầy lòng khuôn, phần nhựa được ép vào lòng khuôn trước tiên sẽ bị cuốn về phía lòng khuôn trước, hiện tượng này xảy ra liên tục đến khi nhựa đã điền đầy hoàn toàn lòng khuôn. Trong quá trình phát triển của ngành công nghệ khuôn mẫu, độ bền sản phẩm nhựa là một trong những vấn đề quan trọng, luôn được quan tâm trong sản xuất. 36 Tuy nhiên, các yếu tố ảnh hưởng đến chất lượng sản phẩm, đặc biệt với độ bền sản phẩm, vẫn chưa được nghiên cứu đầy đủ. Các nghiên cứu trước đây cho thấy độ bền sản phẩm nhựa sẽ được cải thiện nếu làm tốt các bước như: thiết kế sản phẩm, thiết kế khuôn, lựa chọn vật liệu, phun ép với các thông số phù hợp, [103]. Tuy nhiên, cho đến nay, việc tối ưu hóa các vấn đề này vẫn đang là một thách thức lớn trong lĩnh vực phun ép nhựa. Thành khuôn Lớp đông đặc Lớp Dòng lõi nhựa Thành khuôn Dòng chảy Fountain Lớp Bề mặt Thành khuôn đông đặc lõi ` b a Lớp lõi Lớp trượt Thành khuôn Dòng chảy Fountain Hình 2.14: Dòng chảy của nhựa trong khuôn [102] Qua các nghiên cứu trước đây, độ bền của sản phẩm nhựa được cải thiện rõ rệt với các trường hợp có chiều dày lớp bề mặt mỏng. Hiện tượng này được giải thích dựa trên ứng suất dư và độ giảm áp trong suốt quá trình điền đầy lòng khuôn. Trong quá trình này, nếu lớp bề mặt mỏng, tiết diện của dòng chảy nhựa sẽ lớn, do đó, nhựa sẽ dễ dàng chảy về phía trước, kết quả là ứng suất dư của sản phẩm sau khi được lấy ra khỏi lòng khuôn sẽ giảm rất nhiều [103]. Trong những năm gần đây, nhiều nghiên cứu đã tập trung nghiên cứu độ bền của sản phẩm nhựa thông qua yếu tố lớp bề mặt (Frozen layer). Kết quả cho thấy đặc điểm dòng chảy [103] và cấu trúc bên trong 37 của vật liệu là các yếu tố phức tạp, ảnh hưởng lớn đến độ bền sản phẩm. Ngoài ra, với cùng vật liệu nhựa, sự hình thành lớp bề mặt sẽ quyết định bởi đặc tính nhiệt tại bề mặt khuôn, trong đó, hệ số trao đổi nhiệt giữa nhựa và lòng khuôn là một trong những thông số quan trọng, đặc biệt với sản phẩm nhựa thành mỏng. Muốn giảm thất thoát nhiệt của dòng chảy nhựa (nhằm giảm chiều dày của lớp bề mặt), cách duy nhất là giảm chênh lệch nhiệt độ giữa nhựa và lòng khuôn. 2.5 Phương t ình dòng chảy nhựa và dòng kh 2.5.1 C c phương trình chính ❖ Đ i v i dòng nhựa [109]: Phương trình liên tục: + (u ) = 0 (2.7) t 1 1 1 Phương trình bảo toàn động lượng: ( u) + ( u u) = −p + g + (2.8) t 1 1 1 1 1 1 1 1 Phương trình bảo toàn năng lượng: 2 ( 1,11CTCTTHpp) + ( 1,111u − 11 ) = 11 + 1 (2.9) t Trong đó, t là thời gian, u1 là véc tơ vận tốc dòng nhựa, 1g là lực trọng trường, 1 là khối lượng riêng của nhựa,1 là ứng suất trượt của nhựa, p1 là áp suất của nhựa, C p,1 là nhiệt dung riêng của nhựa, 1 là độ nhớt của nhựa, 1 là tốc độ trượt của nhựa, 1 là hệ số truyền nhiệt của nhựa, T1 là nhiệt độ của nhựa và H1 là nguồn nhiệt ngoài. ❖ Đ i v i t m insert khuôn: Phương trình bảo toàn năng lượng: T CT2 + ( − ) = 0 (2.10) 2p2 ,2t 2 38 Trong đó, là thời gian, 2 là khối lượng riêng của vật liệu làm khuôn,C p,2 là nhiệt dung riêng của vật liệu làm khuôn, 2 là hệ số truyền nhiệt của vật liệu làm khuôn, T2 là nhiệt độ của khuôn. ❖ Đ i v i dòng khí: Phương trình liên tục: 3 + ( u ) = 0 (2.11) t 33 Phương trình bảo toàn động lượng: () 33u + () uu = −p + (2.12) t 3 3 3 3 3 Mối quan hệ giữa 3 ứng suất trượt và độ biến dạng: T 2 3= 3 u 3 +( u 3) − u 3 (2.13) 3 Phương trình bảo toàn năng lượng: 2 ( 3,33CTCTTHpp) + ( 3,333u − 33 ) = 33 + 3 (2.14) t Trong đó, là thời gian, u3 là véc tơ vận tốc dòng khí, 3 là khối t lượng riêng của khí, 3 là ứng suất trượt của khí, p3 là áp suất của khí,C p,3 là nhiệt dung riêng của khí, 3 là độ nhớt của khí, 3 là tốc độ trượt của khí, 3 là hệ số truyền nhiệt của khí, T3 là nhiệt độ của khí và H3 là nguồn nhiệt ngoài. 2.5.2 Điều kiện iên ❖ Tại bề mặt chuyển tiếp nhựa – t m insert khuôn: n ()() 2 TTT =Pf w − ,1 (2.15) Trong đó, vế trái tượng trưng cho thông lượng nhiệt từ bên trong khuôn truyền đến bề mặt dòng nhựa thông qua quá trình dẫn nhiệt, vế phải tượng trưng cho thông lượng nhiệt từ dòng nhựa nóng truyền đến bề mặt lòng khuôn thông qua quá trình đối lưu; n là vec tơ pháp tuyến bề mặt lòng khuôn, P là hệ số tỏa nhiệt của nhựa, Tw là nhiệt độ bề mặt lòng khuôn, Tf ,1 là nhiệt độ nhựa. 39 Điều kiện không trượt: uu= w (2.16) Vận tốc của các phân tử nhựa tại bề mặt tấm insert lòng khuôn bằng với vận tốc của tấm insert khuôn, trong trường hợp này, do tấm insert khuôn đứng yên trong quá trình nhựa điền đầy lòng khuôn nên: u = 0 (2.17) ❖ Tại bề mặt dòng khí - t m insert khuôn: n ()() 2 TTT =Gf w − ,3 (2.18) Trong đó, vế trái tượng trưng cho thông lượng nhiệt từ bên trong khuôn truyền đến bề mặt lòng khuôn thông qua quá trình dẫn nhiệt, vế phải tượng trưng cho thông lượng nhiệt từ dòng khí nóng truyền đến bề mặt lòng khuôn thông qua quá trình đối lưu. Điều kiện không trượt: uu= w (2.19) Vận tốc của các phân tử khí tại bề mặt tấm insert lòng khuôn bằng với vận tốc của tấm insert khuôn, trong trường hợp này, do tấm insert khuôn đứng yên trong quá trình phun khí nóng nên: u = 0 (2.20) Trong đó, G là hệ số tỏa nhiệt của khí, Tf ,3 là là nhiệt độ khí. ❖ Tại đầu phun khí: T = TK (2.21) (Trong nghiên cứu này, TK là nhiệt độ của dòng khí ứng với các giá trị nghiên cứu là 200 ºC, 250 ºC, 300 ºC, 350 ºC, 400 ºC; nhiệt độ tấm insert khuôn ban đầu là 30 ºC và nhiệt độ không khí ban đầu là 30 ºC). 2.5.3 Mô hình t ong ô ph ng Trong nghiên cứu này, các phương trình vi phân chính và điều kiện biên của quá trình gia nhiệt khuôn được giải bằng phần mềm Ansys dựa trên phương pháp thể tích hữu hạn (FVM) cho dòng khí. Trong kỹ thuật này, vùng quan tâm được chia thành các vùng nhỏ, được gọi là thể tích kiểm soát [106]. Các phương trình được rời 40 rạc và giải quyết lặp đi lặp lại cho mỗi thể tích kiểm soát. Kết quả thu được là giá trị gần đúng của từng biến số tại các điểm cụ thể trên toàn miền. Theo cách này, ta sẽ thu được một bức tranh đầy đủ về hành vi của dòng chảy. Tấm insert khuôn được chia theo lưới hex dominent do cấu tạo đơn giản của tấm insert khuôn; trong khi, khối khí được chia lưới terahedrons do cấu trúc phức tạp, cho phép tăng số lượng phần tử tại các vùng đòi hỏi độ chính xác mô phỏng cao. Dòng khí nghiên cứu trong luận án này có hệ số nhớt động lực khoảng 1.83e-5 kg/ms nên có hệ số Re rất lớn và là dòng chảy rối. Do đó, ôm hình sử dụng cho mô phỏng là mô hình k- ε tiêu chuẩn [106], là một trong những mô hình chảy rối phổ biến nhất, là một mô hình hai phương trình, gồm có thêm 2 phương trình đối lưu để mô tả tính rối của dòng chảy. Biến đối lưu đầu tiên là động năng chảy rối k, biến đối lưu thứ 2 trong trường hợp này là tiêu tán rối ε là biến xác định quy mô chảy rối, và biến k xác định năng lượng chảy rối cho dòng khí. 2.6 Kiể t a độ ền kéo 2.6.1 Tiêu chuẩn độ ền kéo ASTM D638 Tiêu chuẩn ASTM D638 là tiêu chuẩn phổ biến để xác định cơ tính của vật liệu nhựa nhiệt dẻo dưới tác dụng của lực kéo. Quá trình thử nghiệm theo tiêu chuẩn này được thực hiện bằng cách tác dụng lực kéo lên mẫu thử và xác định các đặc tính khác nhau của mẫu thử khi chịu ứng suất kéo. Trong đó, một số đặc tính phổ biến có thể được xác định như sau: • Độ bền kéo: Là khả năng chịu lực lớn nhất của mẫu thử. • Mô đun đàn hồi: Là khả năng chống biến dạng đàn hồi của mẫu thử. • Độ giãn dài: Là phần trăm dài ra của mẫu thử khi chịu tác dụng của lực kéo. Độ giãn dài lớn hơn cho thấy độ dẻo cao hơn. • Hệ số Poisson: Là tỉ số giữa biến dạng ngang tương đối và biến dạng dọc tương đối (theo phương tác dụng lực). Có rất nhiều phương pháp thử nghiệm khác nhau cho mẫu thử được chế tạo từ vật liệu nhựa nhiệt dẻo. Trong đó, tiêu chuẩn ASTM D638 được ưu tiên sử dụng cho các mẫu thử có dạng thành mỏng. 41 2.6.2 Công thức t nh độ ền kéo Độ bền kéo là đặc tính chịu kéo lớn nhất của mẫu thử và được xác định theo công thức sau: (2.22) Trong đó, t là độ bền kéo cần tìm, Fmax là lực kéo lớn nhất, A là diện tích mặt cắt ngang ban đầu của mẫu thử. 2.6.3 C ch tiến hành thử nghiệ Mẫu thử được chế tạo bằng công nghệ phun ép như hình 2.15. Quá trình thử nghiệm độ bền kéo được thực hiện trên máy thử kéo, mẫu thử được đặt ở tâm ngàm kẹp để lực có thể truyền từ máy qua mẫu thử đến vùng thử bền kéo mà không có lực ngang tác dụng. Tốc độ kéo đối với mẫu thử thành mỏng theo tiêu chuẩn ASTM D638 có thể chọn 5 mm/phút cùng với điều kiện thử nghiệm ở nhiệt độ phòng. Đồng thời, số lượng lần thử nghiệm là ít nhất 5 mẫu cho mỗi mẫu trong 1 trường hợp. Kết quả đo được là giá trị lực tương ứng với giá trị giãn dài của mẫu thử cho đến khi phá hủy. Sau đó, căn cứ vào công thức (2.22) để xác định độ bền kéo của mẫu thử. Loại I, II, III và V Loại IV Hình 2.15: Mẫu thử kéo theo tiêu chuẩn ASTM D638 [108] 42 Bảng 2.1: Thông số kích thước mẫu thử [108] Thông s k ch thư c mẫu thử tương ứng v i các bề dày (đơn vị mm) Bề dày 7 mm Bề dày 7 đến 14mm Bề dày ≤ 4 mm Loại I Loại II Loại III Loại IV Loại V Dung sai W 13 6 19 6 3.18 ±0.5 (WC) L 57 57 57 33 9.53 ±0.5 WO 19 19 29 19 +6.4 LO 165 183 246 115 63.5 Không giới hạn trên G 50 50 50 7.62 ±0.25 D 115 135 115 65 25.4 ±5 R 76 76 76 14 12.7 ±1 RO 25 ±1 43 Chương 3 MÔ TẢ MÔ PHỎNG VÀ THỰC NGHIỆM Trong chương này, qui trình gia nhiệt khuôn bằng khí nóng bên ngoài khuôn, mô hình mô phỏng, mô hình thực nghiệm và các thiết bị sử dụng trong thực nghiệm sẽ được mô tả cụ thể. Trong đó, phân bố nhiệt độ và phân bố áp suất trong lòng khuôn sẽ được phân tích thông qua mô phỏng bằng phần mềm Ansys và Moldex3D. Ngoài ra, quá trình gia nhiệt khuôn, phun ép và đánh giá mẫu thử cũng được thực hiện với vật liệu PA6 và PA6+30%GF. 3.1. Qui t ình gia nhiệt khuôn ằng kh nóng ngoài khuôn Trong quá trình nhựa điền vào khuôn với sản phẩm thành mỏng, những lớp nhựa tiếp xúc với thành của khuôn (bề mặt khuôn ở nhiệt độ thấp) sẽ đông đặc nhanh. Quá trình đông lại ở bề mặt tiếp xúc với khuôn sẽ làm giảm áp lực của dòng nhựa và gây khó khăn cho quá trình chảy của nhựa lỏng vào lòng khuôn. Đây cũng là một trong những nguyên nhân chính làm giảm chất lượng về độ bền của sản phẩm nhựa. Để khắc phục được tình trạng đó, một trong những phương pháp hiệu quả nhất hiện nay là tăng nhiệt độ bề mặt lòng khuôn tiếp xúc với nhựa đến giá trị nhiệt độ tối ưu, qua đó, quá trình đông đặc lớp nhựa tiếp xúc với khuôn sẽ giảm và không làm cho quá trình giải nhiệt sau quá trình ép tăng lên. Các bước cơ bản của quy trình phun ép nhựa có hỗ trợ gia nhiệt khuôn bằng khí nóng bên ngoài khuôn được trình bày như hình 3.2. Trong qui trình này, nhằm tăng khả năng chảy của dòng nhựa trong bước điền đầy khuôn, phương pháp gia nhiệt cho bề mặt khuôn đã được đề xuất. Trong luận án này, phương pháp gia nhiệt cho lòng khuôn bằng khí nóng phun từ ngoài (Gas-assisted mold temperature control – Ex-GMTC) là một trong những công nghệ mới được nghiên cứu trong qui trình phun ép nhựa. Phương pháp này giúp gia nhiệt và giải nhiệt cho lòng khuôn nhanh. Hệ thống công nghệ phục vụ cho Ex-GMTC được chuẩn bị gồm các thiết bị chính như: Hệ thống điều khiển GMTC, hệ thống cấp khí nóng (gồm máy nén khí, khối gia nhiệt cho khí, hệ thống điều khiển lưu lượng khí) và hệ thống giải nhiệt cho khuôn, các cụm thiết bị này được mô tả như hình 3.1. 44 Trong hệ thống Ex-GMTC, khối gia nhiệt cho khí làm nhiệm vụ cung cấp khí nóng với nhiệt độ khí có thể thay đổi từ 200 oC đến 400 oC. Khí nóng này sẽ được phun trực tiếp vào lòng khuôn nhằm gia nhiệt cục bộ cho lòng khuôn. Ngược lại, hệ thống giải nhiệt cho khuôn bằng nước sẽ làm nhiệm vụ giữ nhiệt độ khuôn ở giá trị cho trước. Trong quá trình hoạt động, bộ phận điều khiển GMTC sẽ nhận tín hiệu đóng/mở của khuôn, từ đó sẽ điều khiển van khí cấp cho bộ gia nhiệt cho khí để gia nhiệt cho khuôn. Hệ thống điều Tín hiều điều khiển khiển Ex-GMTC van khí mở / khiển khuôn Đóng Khí vào Tínhiềuđiều Nguồn khínóng nước dương Khuôn Khuôn âm Hệ thống Hệ điều khiển nhiệt khiển độ Hình 3.1: Hệ thống Ex-GMTC Trong nghiên cứu này, khí nóng sẽ được sử dụng như nguồn nhiệt nhằm nâng nhiệt độ tại bề mặt khuôn. Hình 3.2 trình bày các bước gia nhiệt cho khuôn bằng khí nóng phun từ ngoài. Trong quá trình gia nhiệt cục bộ này, sau khi hai nửa khuôn mở ra để lấy sản phẩm ra khỏi lòng khuôn, nửa khuôn di động sẽ di chuyển đến vị trí gia nhiệt (hình 3.2 – Bước 1). Sau đó, khối gia nhiệt cho khí sẽ di chuyển đến vị trí gia nhiệt cho khuôn (hình 3.2 - Bước 2). Tại vị trí này, khí nóng từ khối gia nhiệt sẽ phun vào lòng khuôn. Thông qua quá trình truyền nhiệt đối lưu giữa khí nóng và lòng khuôn, nhiệt độ bề mặt lòng khuôn sẽ tăng lên. Khi nhiệt độ lòng khuôn đạt đến giá trị cần thiết, khối gia nhiệt sẽ được di chuyển ra khỏi khu vực 45 phun ép (hình 3.2 – Bước 3), sau đó, hai nửa lòng khuôn sẽ đóng lại, chu kỳ phu ép sẽ được tiếp tục. Khối gia gia Khối gia Khối nhiệt chokhí nhiệt chokhí nhiệt Lòng khuôn Lòng khuôn Lòng khuôn cần gia nhiệt cần gia nhiệt cần gia nhiệt Khối gia Khối nhiệt chokhí nhiệt Bước 1: Khuôn mở ra Bước 2: Khí nóng phun vào lòng Bước 3: Khuôn đóng lại, khuôn chuẩn bị cho nhựa vào lòng khuôn Hình 3.2: Các bước gia nhiệt bề mặt khuôn khi sử dụng hệ thống Ex-GMTC 3.2. Mô hình ô ph ng và thực nghiệ Nhằm đánh giá khả năng gia nhiệt bằng khí nóng phun từ ngoài, mô hình như hình 3.3 và hình 3.4 được sử dụng. Vùng gia nhiệt trên khuôn được thiết kế với chi tiết tấm insert có kích thước 100 mm x 50 mm. Để đánh giá khả năng gia nhiệt của phương pháp Ex-GMTC, 5 cảm biến nhiệt được lắp tại bề mặt khuôn để thu thập các giá trị nhiệt độ thay đổi trong suốt quá trình gia nhiệt. Trong các nghiên cứu trước đây về lĩnh vực gia nhiệt bề mặt khuôn [96 – 99], thiết kế khuôn với tấm insert thường được sử dụng nhằm tăng hiệu suất của quá trình gia nhiệt. Các nghiên cứu này cho thấy chiều dày của tấm insert là một trong những thông số quan trọng, có ảnh hưởng lớn đến kết quả gia nhiệt cho khuôn. Vị trí tương đối của khuôn, tấm insert, đầu phun khí nóng và các cảm biến được trình bày như hình 3.3 và hình 3.4. 46 Tấm insert Hệ thống làm nguội Hình 3.3: Vị trí cảm biến, tấm insert so với khuôn G: Khe hở giữa đầu phun khí và bề mặt tấm insert h: Bề dày tấm insert Đầu phun khí nóng G Bề mặt gia nhiệt Hệ thống làm nguội Đơn vị: mm Hình 3.4: Vị trí gia nhiệt của đầu phun Sau khi đánh giá khả năng gia nhiệt cho khuôn với qui trình mới này, cho thấy khả năng áp dụng được của quá trình này trong thực tế. 47 Tiếp theo, chọn mẫu mô phỏng và thực nghiệm trong nghiên cứu này là mẫu thử độ bền kéo theo tiêu chuẩn ASTM D638 với hình dạng và kích thước như hình 3.5. Trong đó, chiều dày của mẫu thử tại vùng phá hủy sẽ được thay đổi lần lượt là 0,4 mm, 0,6 mm và 0,8 mm, đồng thời, vùng gia nhiệt được thiết kế dạng lưới như vùng A, để cho thấy ảnh hưởng của nhiệt độ khuôn và chiều dày mẫu thử đến độ bền kéo được thể hiện rõ rệt hơn. Hình 3.5: Hình dạng và kích thước của mẫu mô phỏng và thực nghiệm [104] 3.3. Mô ph ng 3.3.1 Mô ph ng quá trình gia nhiệt bằng khí nóng ngoài khuôn Trong luận án này, mô hình mô phỏng quá trình gia nhiệt được xây dựng nhằm quan sát phân bố nhiệt độ tại vùng gia nhiệt. Trong quá trình lắp ráp, giữa tấm insert và khuôn luôn tồn tại khe hở. Trong quá trình gia nhiệt, khe hở này đóng vai trò như một lớp cách nhiệt giữa tấm insert và khuôn. Vì vậy, tương tự như các nghiên cứu trước đây [21, 22], mô hình mô phỏng (hình 3.4) trong luận án này chỉ 48 bao gồm hai phần chính: thể tích tấm insert và thể tích không khí. Các điều kiện ban đầu được trình bày như hình 3.6 và các thông số mô phỏng, đặc tính vật liệu được trình bày như bảng 3.1. Trong quá trình chia lưới, phần thể tích tấm insert được chia lưới hex dominant với 7 lớp theo chiều dày, còn lại, với thể tích không khí, phần tử lưới dạng tetra được sử dụng, trong đó, các phần tử gần miệng phun khí nóng được chia với kích thước lưới nhỏ hơn. Phương pháp mô phỏng được tiến hành với phần mềm ANSYS thông qua các thông số như quá trình thực nghiệm. Bảng 3.1: Đặc tính vật liệu mô phỏng quá trình gia nhiệt bề mặt khuôn V t liệu Tên Đơn vị Giá trị Khối lượng phân tử kg/kmol 28.96 Khối lượng riêng kg/m3 1.185 Khí Nhiệt dung riêng J/kgK 1004.4 Độ nhớt động lực học kg/ms 1.831e-5 Hệ số dẫn nhiệt W/mK 0.0261 Khối lượng phân tử kg/kmol 55.85 Khối lượng riêng kg/m3 7854 Thép Nhiệt dung riêng J/kg K 434 Hệ số dẫn nhiệt W/mK 60.5 49 Khí ra Nhiệt độ khí: 30 oC Áp suất khí quyển: 0,1 MPa Khí vào Nhiệt độ khí: 300 oC Áp suất khí: 7 MPa Hướng dòng khí: vuông góc bề mặt cần gia nhiệt Thể t ch kh Thể t ch gia nhiệt Điều kiện ban đầu: Nhiệt độ ban đầu: 30 oC • Nhiệt độ khí: 30 oC • Áp suất khí quyển: 0,1 MPa • Vận tốc khí: 0 m/s Hình 3.6: Điều kiện ban đầu của quá trình mô phỏng Áp suất dòng khí dùng để thực nghiệm là 7 MPa vì đây là áp suất phổ biến đưuọc sử dụng trong các nhà máy (xưởng cơ khí) và các thiết bị tạo ra nguồn khí có áp suất này rất phổ biến. 3.3.2 Mô ph ng quá trình nhựa điền đầy lòng khuôn Hiện nay, với qui trình phun ép thông thường, việc lựa chọn bộ thông số phun ép thích hợp cho từng loại sản phẩm hiện nay vẫn thường được thực hiện thông qua kinh nghiệm người đứng máy. Tuy nhiên, khi sử dụng bước gia nhiệt cho bề mặt lòng khuôn cho qui trình phun ép nhựa, việc lựa chọn bộ thông số thích hợp sẽ là một trong những thách thức cho người vận hành máy phun ép nhựa. Do đó, nhằm giúp người vận hành máy có thể lựa chọn bộ thông số thích hợp, luận án này sẽ nghiên cứu và đưa ra qui trình mô phỏng quá trình phun ép có sử dụng bước gia nhiệt cho lòng khuôn. 50 Tiền xử lý Phân tích Kết quả Moldex3D Moldex3D Moldex3D Designer Project Project Xây dựng hệ thống Nhập thuộc tính vật Phân tích kết quả kênh dẫn nhựa liệu nhựa điền đầy Xây dựng hệ thống Nhập thông số ép Phân tích kết quả kênh làm mát bão áp Phân tích kết quả Tạo lưới dạng khối Tiến hành phân tích làm mát Phân tích kết quả cong vênh Hình 3.7: Lưu đồ thực hiện quá trình mô phỏng [105] Với lưu đồ như hình 3.7, qui trình mô phỏng quá trình phun ép có sự hỗ trợ của bước gia nhiệt bằng khí nóng cho bề mặt khuôn được tiến hành với phần mềm Moldex3D thông qua ba giai đoạn như sau: - Giai đoạn 1 - Tiền xử lý Tại giai đoạn này, mô hình 3D của mẫu thực nghiệm đã được thiết kế từ trước trên các phần mềm CAD để xây dựng mô hình 3D. Mô hình này được nhập vào mô đun Moldex3D Designer. Trong môi trường Moldex3D Designer, hệ thống khuôn sẽ được thiết lập. Tại đây, các bước “Tiền xử lý” sẽ được tiến hành như hình 3.7
File đính kèm:
luan_an_nghien_cuu_anh_huong_cua_gia_nhiet_khuon_phun_ep_ban.pdf
TOM TAT Luan An tieng Anh THE UYEN 30_10_2020.pdf
TOM TAT Luan An tieng Viet THE UYEN 30_10_2020.pdf
Trang thong tin LA tieng Anh THE UYEN 30_10_2020.docx
Trang thong tin LA tieng Viet THE UYEN 30_10_2020.docx