Luận án Nghiên cứu chất lượng mối hàn kết cấu thép bằng hàn hồ quang tự động dưới lớp trợ dung gốm aluminate-rutile chế tạo trong nước
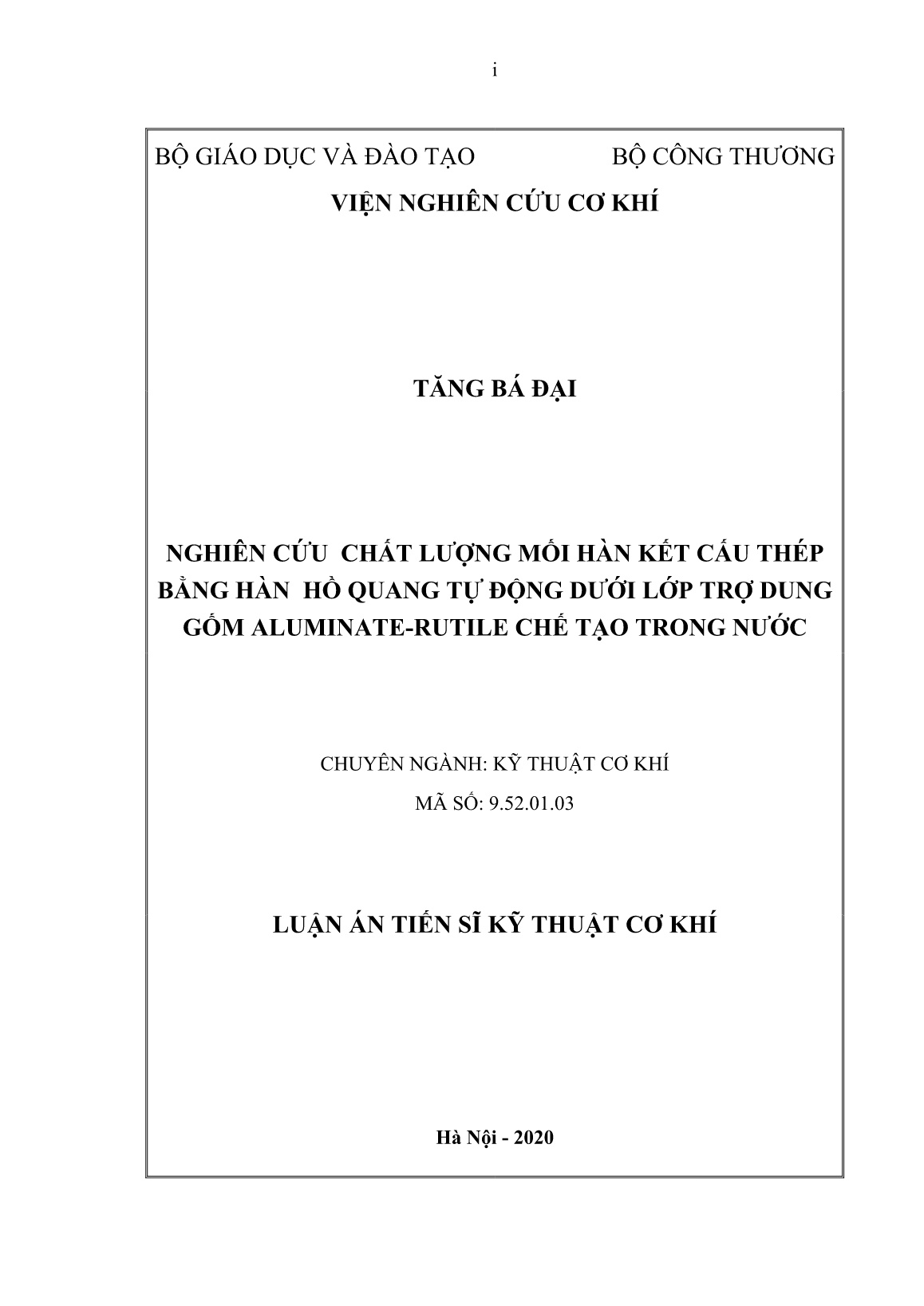
Trang 1
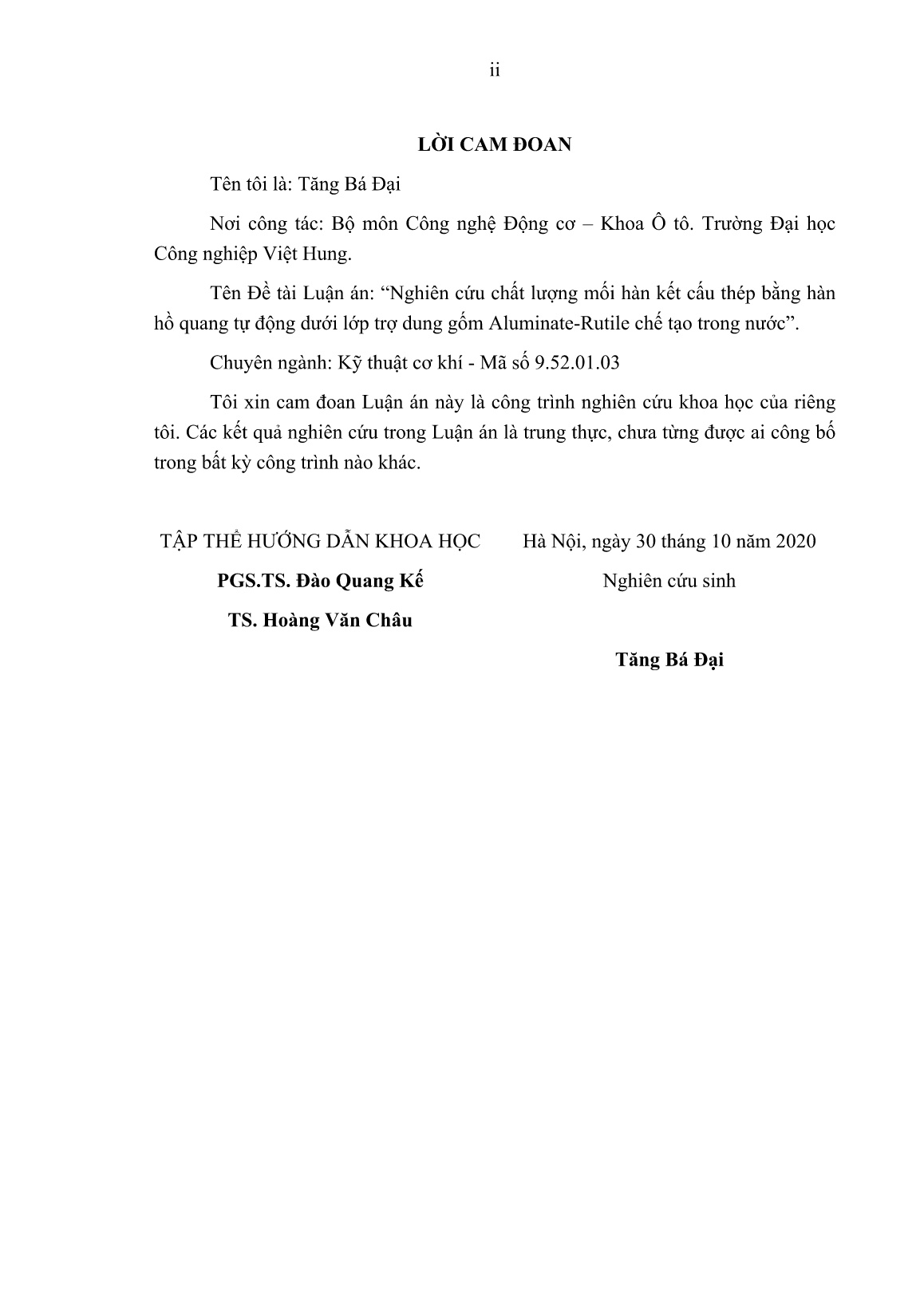
Trang 2
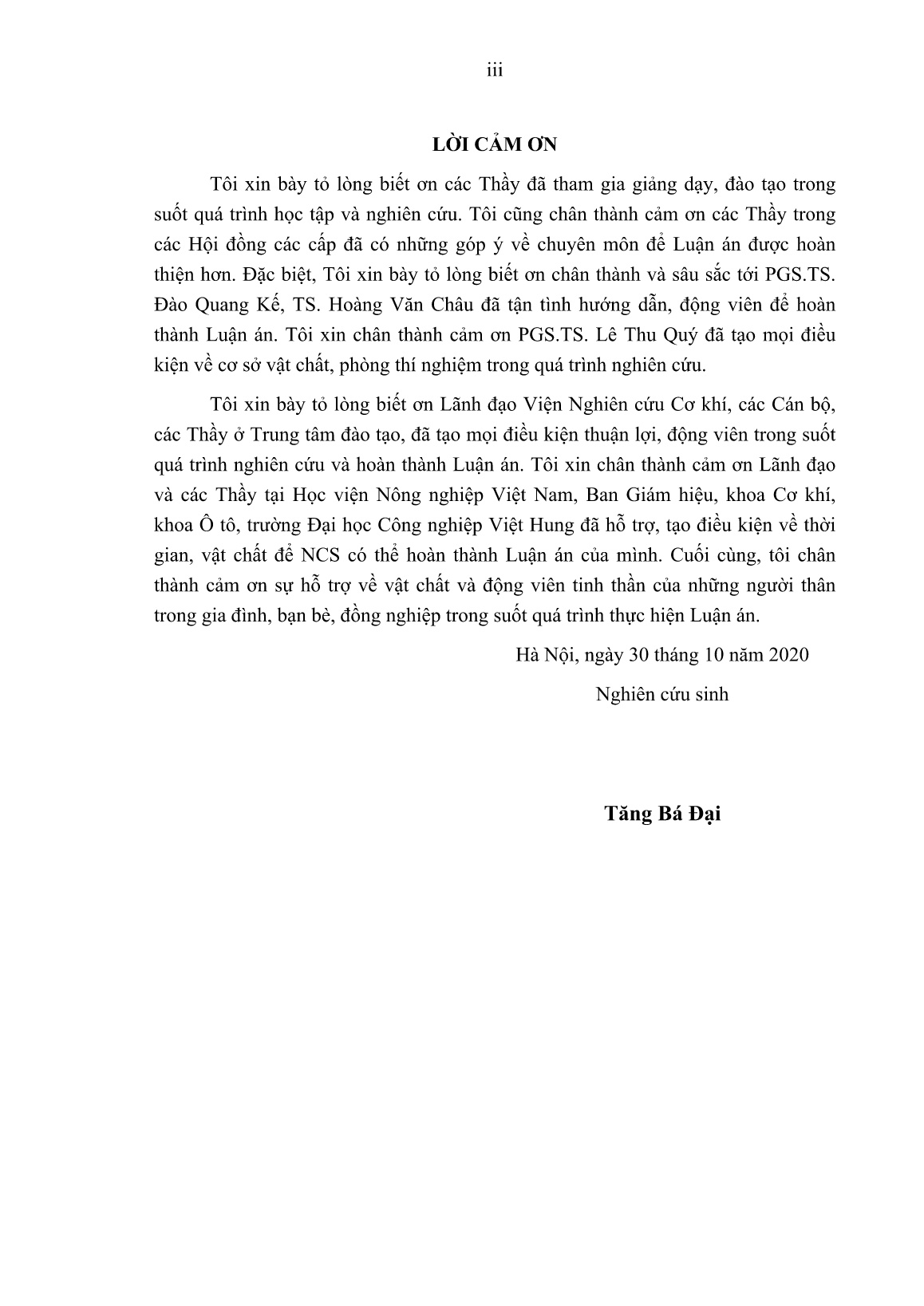
Trang 3
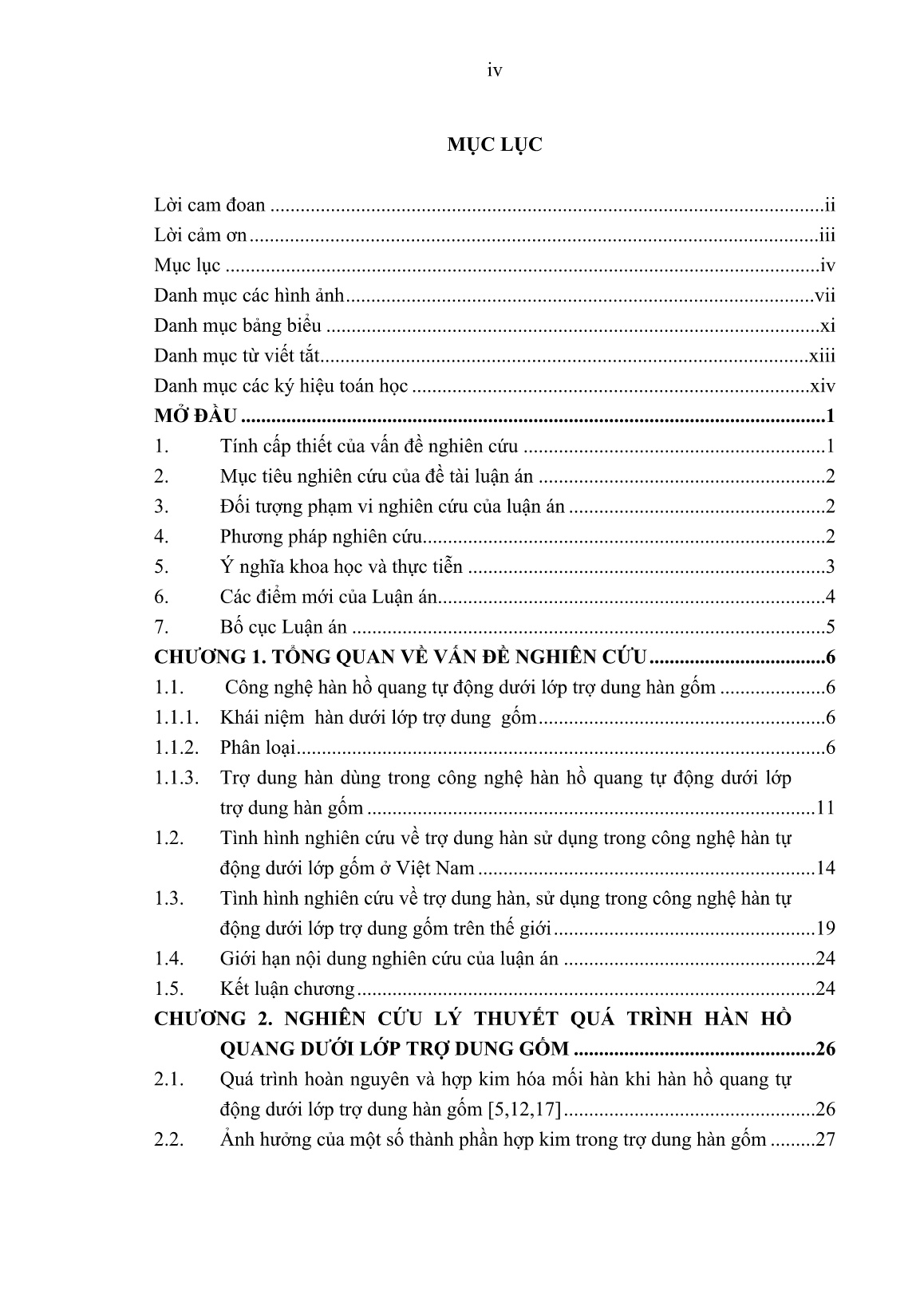
Trang 4
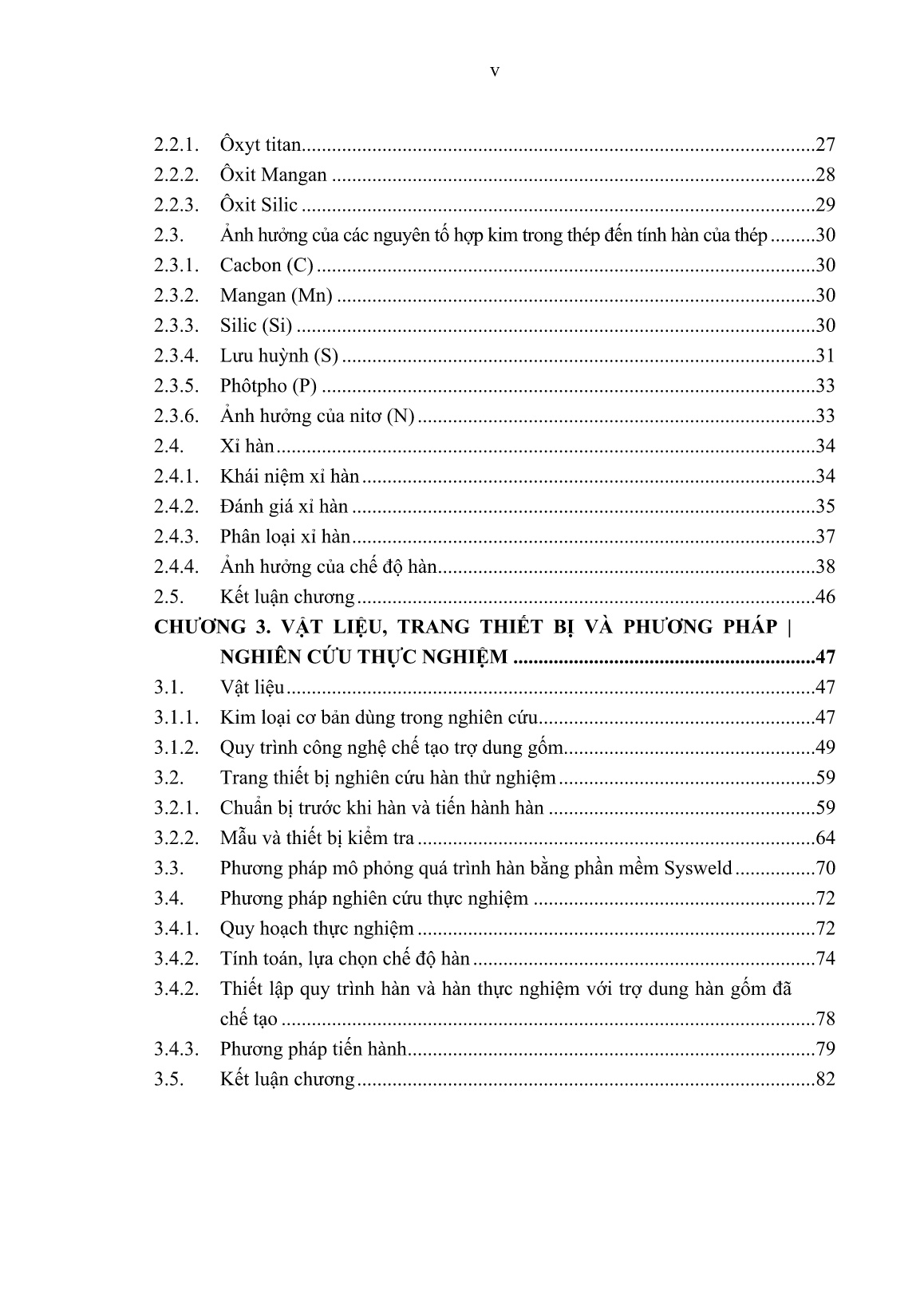
Trang 5
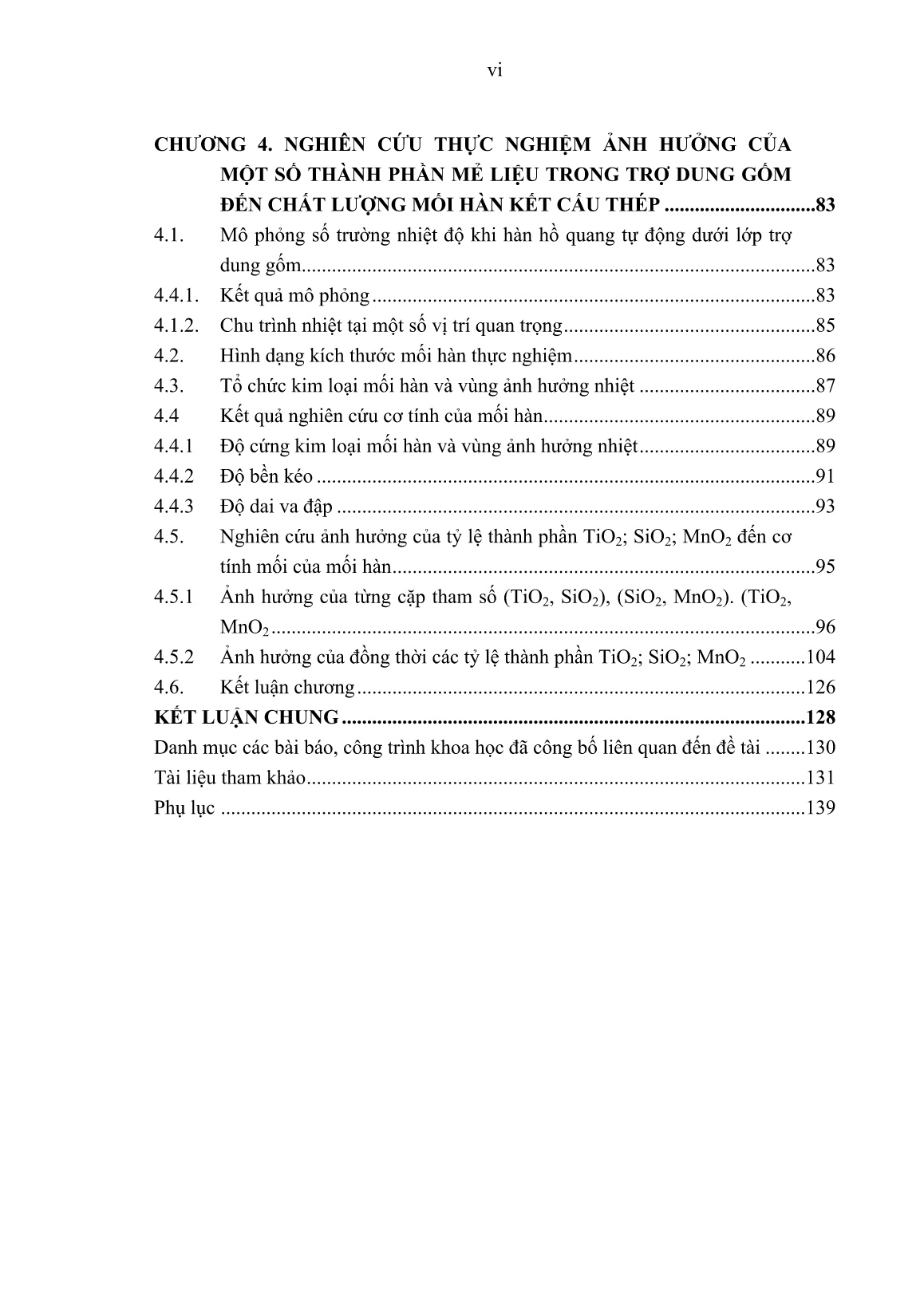
Trang 6
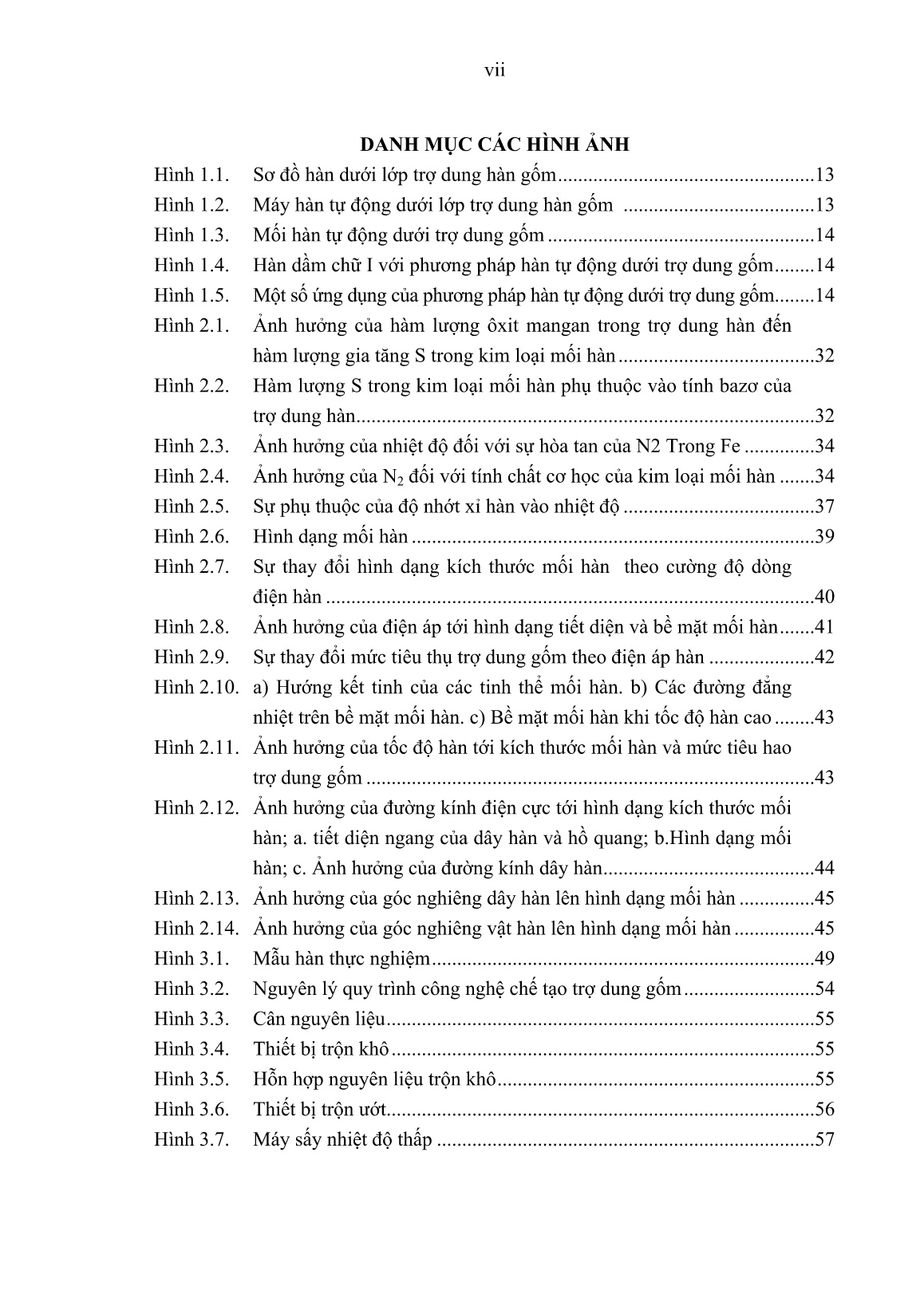
Trang 7
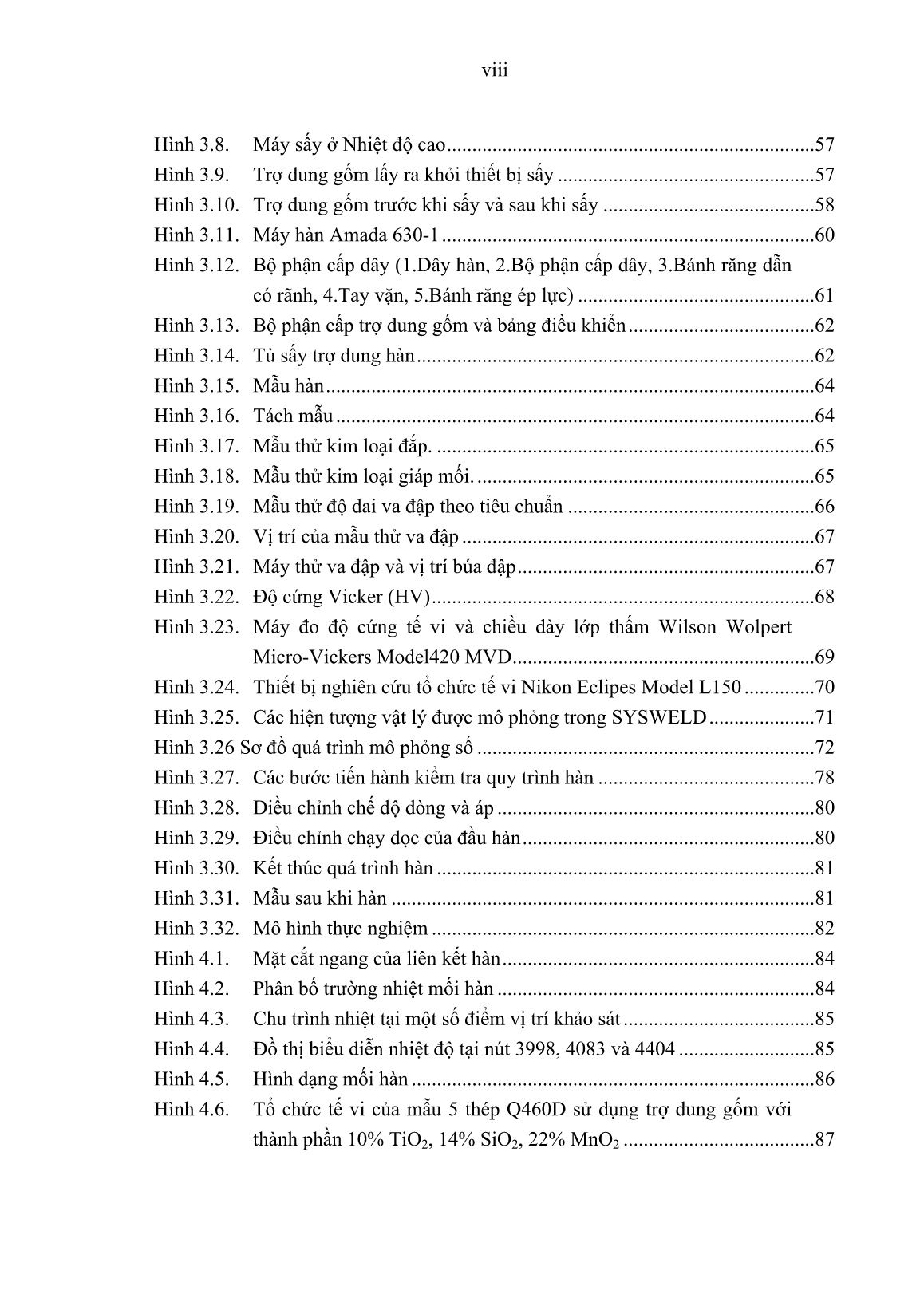
Trang 8
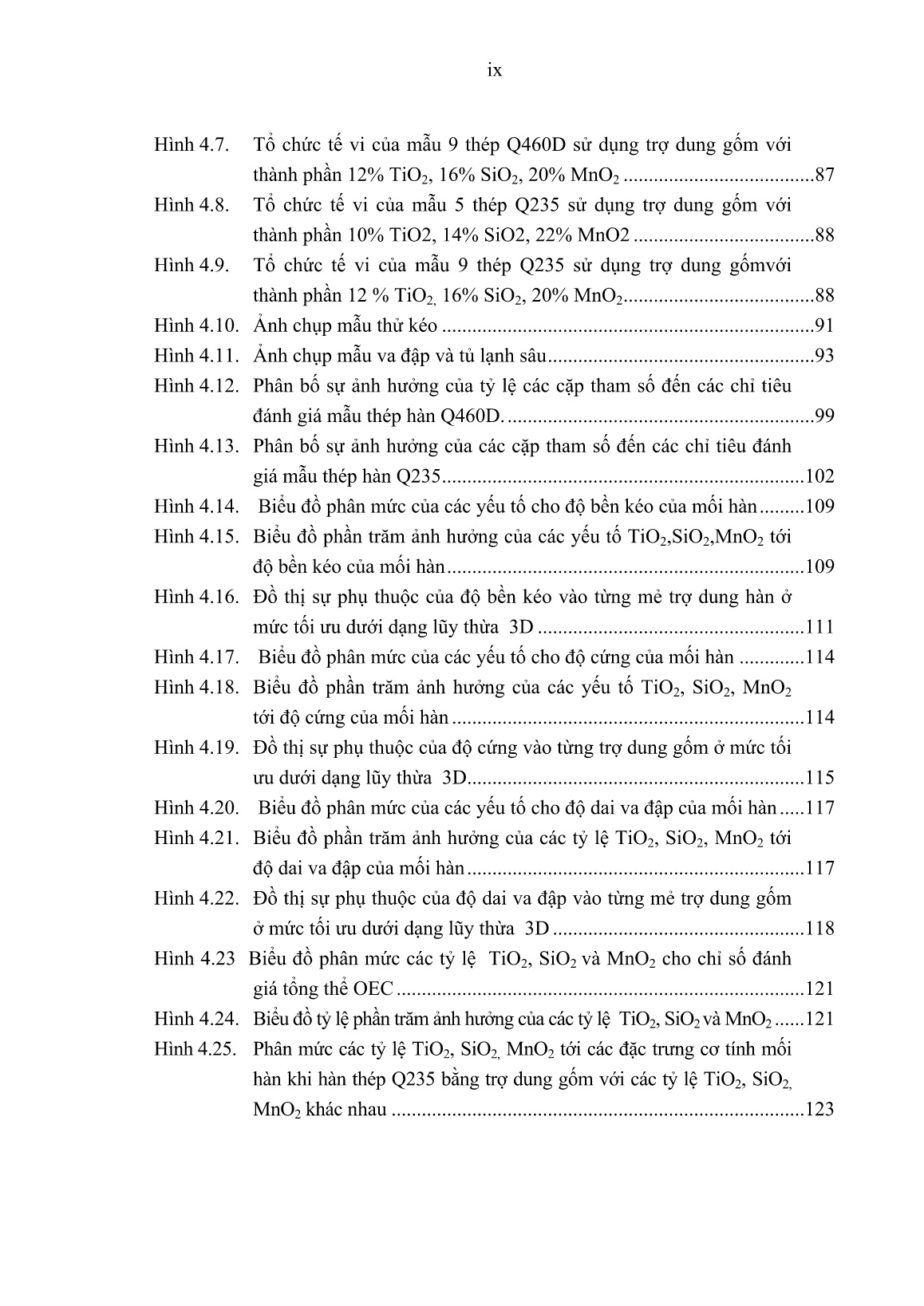
Trang 9
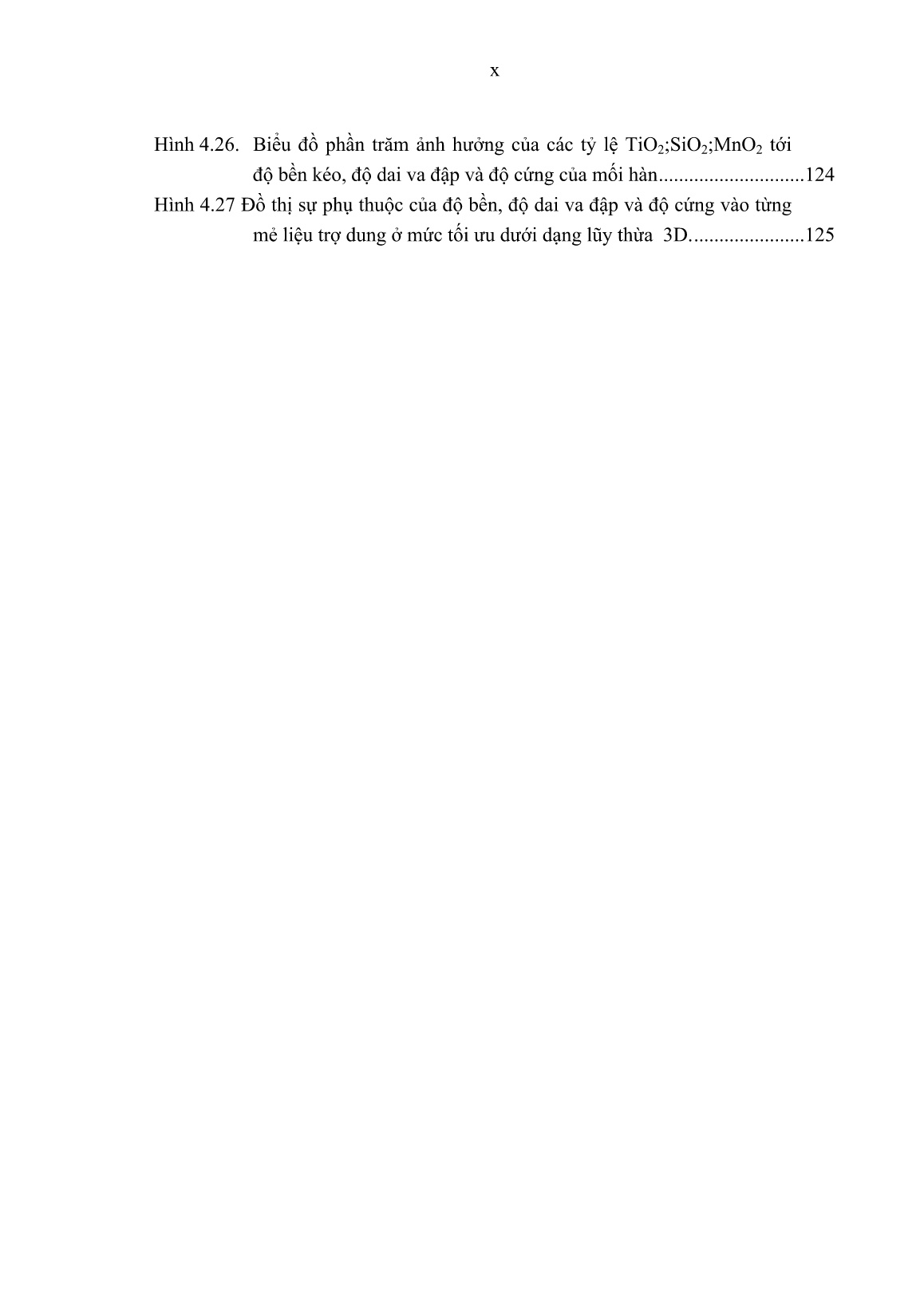
Trang 10
Tải về để xem bản đầy đủ
Bạn đang xem 10 trang mẫu của tài liệu "Luận án Nghiên cứu chất lượng mối hàn kết cấu thép bằng hàn hồ quang tự động dưới lớp trợ dung gốm aluminate-rutile chế tạo trong nước", để tải tài liệu gốc về máy hãy click vào nút Download ở trên.
Tóm tắt nội dung tài liệu: Luận án Nghiên cứu chất lượng mối hàn kết cấu thép bằng hàn hồ quang tự động dưới lớp trợ dung gốm aluminate-rutile chế tạo trong nước

bản, a - chiều rộng khe hàn, b - bề rộng mối hàn; c - chiều cao mối hàn, 3.1.2. Quy trình công nghệ chế tạo trợ dung gốm. 3.1.2.1. Tính toán bài phối liệu cho trợ dung gốm Để tính toán bài phối liệu cho trợ dung gốm, áp dụng phương pháp quy hoạch thực nghiệm toàn phần, nội dung của phương pháp như sau: - Lựa chọn các yếu tố đầu vào, ở đây là thành phần các chất trong mẻ phối liệu trợ dung gốm loại Aluminate - Rutile. Căn cứ vào các yếu tố đầu vào sau đó tham khảo ý kiến chuyên gia để đánh giá mức độ quan trọng của các yếu tố đến hàm mục tiêu, thực hiện các thí nghiệm thăm dò với mục đích tìm ra những yếu tố ảnh hưởng nhất tới giá trị của hàm mục tiêu và giá trị của chúng. Gọi đó là giá trị ở tâm, khi tối ưu hoá nhận giá trị 0. - Xây dựng ma trận quy hoạch thực nghiệm. - Tổ chức các thí nghiệm và lấy mẫu thống kê. - Từ số liệu thu được xây dựng mô hình thống kê thực nghiệm để mô tả quá trình, tức là xác định hàm mục tiêu. - Kiểm định các hệ số của phương trình hồi quy có nghĩa không (theo tiêu chuẩn Student) - Từ phương trình hồi quy phân tích sự tương tác giữa các yếu tố ảnh hưởng đến mục tiêu đầu ra. Để quy hoạch thực nghiệm toàn phần tác giả đã tiến hành bố trí thí nghiệm thay đổi đồng thời các yếu tố. Mỗi yếu tố được tiến hành ở 3 mức: mức trên, mức dưới và mức cơ sở sẽ là mức ở tâm. Theo tiêu chuẩn ISO 14174-2012 về thành phần trợ dung gốm hệ Aluminate – Rutile ta có bảng sau: Bảng 3.4. Thành phần trợ dung gốm hệ Aluminate – Rutile Dựa vào tiêu chuẩn ISO 14174 – 2012 về thành phần trợ dung gốm hệ Aluminate– Rutile để nghiên cứu ảnh hưởng của 3 yếu tố TiO2, SiO2 và MnO2 trong trợ dung gốm tới chất lượng mối hàn. Việc thay đổi 3 thành phần trên để đánh giá chất lượng kim loại mối hàn, trong trợ dung gốm hệ Aluminate– Rutile có thành phần hóa học chủ yếu là: Al2O3 (39-41%), TiO2 (9-11%), SiO2 (13-15%), MnO2 (19-21%) chiếm hàm lượng rất lớn, bên cạnh đó các thành phần như Si, Mn, trong thép Q460D cũng có hàm lượng tương đối cao. Nên khi thay đổi hàm lượng của các thành phần đó sẽ làm cho cơ tính của kim loại mối hàn thay đổi một cách rõ rệt. Từ đó ta có thể dễ dàng đánh giá được sự thay đổi cơ tính của kim loại mối hàn. Theo tiêu chuẩn ISO 14174-2012 về thành phần trợ dung gốm, tác giả đã tiến hành nhiều thí nghiệm thăm dò chế tạo trợ dung gốm với các bài phối liệu khác nhau (đầu vào), tương ứng nhận được là các kết quả chất lượng (đầu ra) khác nhau, sau đó khoanh vùng sơ bộ thành phần phối liệu, xác định một số nguyên liệu có ảnh hưởng đáng kể đến chất lượng mối hàn. Từ đó có bài phối liệu trợ dung gốm Aluminate – Rutile (bảng 3.4). - Chọn các yếu tố trên cơ sở của nền tạo xỉ là: MnO2 - TiO2 - SiO2 - Tác giả chọn các biến Z1: MnO2, Z2: TiO2, Z3: SiO2 Qua nghiên cứu thăm dò như đã đề cập ở trên, tác giả chọn miền khảo sát của các yếu tố là: % MnO2: 18 ÷ 22 % TiO2: 8 ÷ 12 % SiO2: 12 ÷ 16 Từ đó xây dựng điều kiện thí nghiệm (bảng 3.5). Bảng 3.5. Mã hóa ma trận thí nghiệm Trong đó: Z1, Z2, Z3 là miền khảo sát (Đầu vào), lần lượt X0, X1, X2, X3,.. (thông số ảnh hưởng đến quá trình). Dựa vào các kết quả thực nghiệm đã xác định được các tham số X0, X1, X2, X3 ...gọi là nhận dạng mô hình thống kê. Phương trình nhận được gọi là phương trình hồi quy thực nghiệm của hệ thống tương ứng với bộ thí nghiệm đã cho. Bảng 3.6. Các mức của biến đầu vào Các yếu tố biến thiên % MnO2 Z1 % TiO2 Z 2 % SiO2 Z 3 Mức trên (Z i = + 1) 22 12 16 Mức cơ sở (Z i = 0) 20 10 14 Mức dưới (Z i = - 1) 18 8 12 Khoảng biến thiên (∆) 2 2 2 Từ bài phối liệu đã tính toán khối lượng từng chất để sản xuất 100kg trợ dung hàn gốm như sau: Do các chất trong thành phần mẻ liệu trợ dung gốm không phải nguyên chất, ngoài hàm lượng chủ yếu còn có hàm lượng các chất khác trong thành phần mẻ liệu trợ dung hàn (Bảng 3.7) cho ta thấy hàm lượng chính và hàm lượng tạp chất có trong các nguyên liệu. Bảng 3.7. Hàm lượng chính và hàm lượng tạp chất có trong từng trong nguyên liệu Danh mục quặng sa khoáng, fero hợp kim và các thành phần khác theo đơn trợ dung được lựa chọn đảm bảo các yêu cầu kỹ thuật cần thiết (thành phần chính, hàm lượng tạp chất chứa P, S nằm trong giới hạn cho phép). Ta điều chỉnh các thành phần của TiO2, SiO2, MnO2 nằm ngoài khoảng cho phép của tiêu chuẩn ISO 14174 – 2012 và theo bảng ma trận quy hoạch thực nghiệm (Bảng 3.8) Bảng 3.8. Phối liệu với các mẻ trợ dung hàn gốm Aluminate – Rutile Thành phần TiO2(%) Al2O3(%) SiO2 (%) MnO2 (%) Các chất còn lại % Mẻ 1 8 39 12 18 - Mẻ 2 8 39 12 22 - Mẻ 3 12 39 12 18 - Mẻ 4 12 39 12 22 - Mẻ 5 8 39 16 18 - Mẻ 6 8 39 16 22 - Mẻ 7 12 39 16 18 - Mẻ 8 12 39 16 22 - Mẻ 9 10 40 14 20 - Bảng 3.9. Thành phần % về khối lượng cho từng chất khi chưa tính đến khối lượng các tạp chất có trong 100kg trợ dung gốm Nguyên liệu Rutin Nhôm ôxit Cao lanh Quặng mangan Các chất còn lại (%) (%) (%) (%) (%) Mẻ 1 8,7 75 23,07 36 - Mẻ 2 8,7 75 23,07 44 - Mẻ 3 13,04 75 23,07 36 - Mẻ 4 13,04 75 23,07 44 - Mẻ 5 8,7 75 30,7 36 - Mẻ 6 8,7 75 30,7 44 - Mẻ 7 13,04 75 30,7 36 - Mẻ 8 13,04 75 30,7 44 - Mẻ 9 10,86 76,9 26,9 40 - Bảng 3.10. Khối lượng nguyên chất có trong 100kg trợ dung gốm Nguyên liệu Rutin(g) Nhôm ôxit(g) Cao lanh(g) Quặng mangan (g) Các chất còn lại (g) Mẻ 1 5256 39780 11717 21780 - Mẻ 2 5256 39780 11717 26620 - Mẻ 3 7884 39780 11717 21780 - Mẻ 4 7884 39780 11717 26620 - Mẻ 5 5256 39780 15623 21780 - Mẻ 6 5256 39780 15623 26620 - Mẻ 7 7884 39780 15623 21780 - Mẻ 8 7884 39780 15623 26620 - Mẻ 9 6570 40800 13670 24200 - 3.1.2.2. Cân đong nguyên liệu khô Trợ dung gốm được chế tạo theo ba bước chính: Chuẩn bị và pha trộn nguyên liệu, tạo hạt. Tất cả các hợp chất dạng bột trộn lẫn với nhau theo trọng lượng khác nhau [62 - 68], các nguyên liệu dạng khoáng chất được chọn lựa theo đúng chủng loại, thành phần đạt chất lượng rồi được nghiền nhỏ, chúng được sàng để loại bỏ hạt quá cỡ (0,3mm). Nguyên liệu phải khô, độ ẩm không quá 1%. Từng thành phần cân đúng theo tỷ lệ có mặt của chúng trong công thức pha trộn đã chọn, tất cả các phần nguyên liệu cân xong được cho chung vào thiết bị trộn, đầu tiên chúng được trộn khô cho đến khi các thành phần trộn lẫn đều với nhau sau đấy chúng được chuyển sang chế độ trộn ướt bằng cách rót thêm dần nước thủy tinh vào trong quá trình trộn. Khi phối liệu đã ướt đều thì được chế biến tạo thành từng hạt trợ dung, các hạt trợ dung được tiếp tục vê tròn có dạng hình cầu để tạo nên độ sít chặt, sau đấy trợ dung gốm được sấy. Hình 3.2. Nguyên lý quy trình công nghệ chế tạo trợ dung gốm Dựa vào quy trình công nghệ hình 3.2 tác giả đưa ra dây chuyền thiết bị thích hợp để phục vụ việc thực hiện công nghệ. Dây chuyền thiết bị gồm các thiết bị chính sau: Thiết bị trộn và tạo hạt, thiết bị vê tròn hạt và lò sấy nhiệt độ cao. Ngoài ra còn một số thiết bị phụ trợ khác như: Băng tải, gầu nâng, cân, sàng, máy nghiền, máy đóng bao, máy khâu bao Hình 3.3. Cân nguyên liệu 3.1.2.3. Trộn khô Tất cả các nguyên liệu cân xong được trộn tay từ 5 ÷ 10 phút. Nguyên liệu trộn tay xong được trộn đều trong máy trộn chuyên dụng (máy trộn bi) khoảng 15÷20 phút. Hình 3.4. Thiết bị trộn khô Hình 3.5. Hỗn hợp nguyên liệu trộn khô 3.1.2.4. Trộn ướt Quá trình trộn ướt bằng cách rót dần nước thủy tinh vào quá trình trộn. Nước thủy tinh có thành phần chủ yếu là KNaSiO3.nH2O, có tác dụng tạo lên sự dính kết các hạt phối liệu, khi khô tạo nên sự kết dính các hạt. Trong quá trình hàn, nước thủy tinh phân hủy tạo ra các chất K2O và Na2O là các chất làm ổn định hồ quang. Trộn bằng máy trục xoắn vít đơn hoặc kép, hoặc máy trộn kiểu hành tinh. Làm cho trợ dung hàn được trộn nhuyễn, đồng đều và đảm bảo độ dẻo cần thiết. Hình 3.6. Thiết bị trộn ướt Công đoạn trộn ướt cần chú ý đảm bảo độ dẻo, nhuyễn của trợ dung, nếu trợ dung gốm quá nhão hoặc quá khô đều không tốt cho công đoạn ve viên tạo hạt, sẽ ảnh hưởng tới năng suất cũng như chất lượng sản phẩm. 3.1.2.5. Vê viên tạo hạt Khi phối liệu đã ướt đều thì được chế biến tạo thành từng hạt trợ dung gốm. Các hạt trợ dung gốm được tiếp tục vê tròn có dạng hình cầu và tạo nên độ sít chặt thì trong quá trình bảo quản, vận chuyển, sử dụng hạt trợ dung gốm khó bị vỡ nhỏ ra. Hạt trợ dung gốm được tạo theo phương pháp ép rồi cắt hoặc vê viên. 3.1.2.6. Sấy trợ dung gốm Việc sấy trợ dung được chia làm 2 giai đoạn, sấy sơ bộ và sấy nhiệt độ cao, trong giai đoạn đầu nhiệt độ được nâng dần lên 100oC, trong giai đoạn 2, nhiệt độ được nâng dần lên đến nhiệt độ nung cần thiết của loại trợ dung gốm. Việc chia làm hai giai đoạn sấy để đảm bảo hạt trợ dung gốm khô đều và có độ ẩm thấp nhất. Khi tăng nhiệt độ nung thì tính háo nước của trợ dung gốm giảm rõ rệt, còn các tính chất công nghệ được cải thiện. Tuy nhiên việc tăng nhiệt độ nung có giới hạn vì nhiệt độ cao có thể gây ra các phản ứng bất lợi cho trợ dung gốm, làm oxy hóa các nguyên tố hợp kim và phân hủy các oxit kim loại và muối, nếu trợ dung dùng cho hàn đắp tạo lên bề mặt kim loại cứng thì nhiệt độ sấy chỉ khoảng đến 450oC, còn nếu là các loại trợ dung hàn kết cấu thép thì nhiệt độ sấy có thể lên đến 750oC. Trong điều kiện khí hậu Việt Nam và diện tích mặt bằng cho phép có thể tiến hành sấy giai đoạn 1 bằng hong khô ở nhiệt độ sấy 100oC và giữ nhiệt trong 30 phút, giai đoạn sấy khô kiệt nhiệt độ cao nhất có thể lên đến 750oC và giữ nhiệt độ trong khoảng 1 giờ. Sấy xong, trợ dung gốm được làm nguội xuống nhiệt độ phòng. Hình 3.7. Máy sấy nhiệt độ thấp Hình 3.8. Máy sấy ở Nhiệt độ cao Hình 3.9. Trợ dung gốm lấy ra khỏi thiết bị sấy Hình 3.10. Trợ dung gốm trước khi sấy và sau khi sấy 3.1.2.7. Phân loại trợ dung gốm Sau khi sấy, trợ dung gốm được sàng lọc (kích thước mắt sàng từ nhỏ nhất 0,5 và to nhất đến 1,5mm) hạt to quá và hạt nhỏ quá không đạt yêu cầu đều phải loại ra qua hai lần sàng, các hạt quá to thì được nghiền lại, các hạt quá nhỏ thì đưa trở lại công đoạn trộn nguyên liệu nhằm tạo ra những hạt trợ dung gốm tương đối đồng đều nhau. 3.1.2.8. Bao gói, kiểm tra thành phẩm và nhập kho Trợ dung gốm sau khi sấy khô sẽ được kiểm tra chất lượng bảo quản và cất giữ trong túi ni lông kín, các túi trợ dung phải được đặt trong thùng nhựa hoặc thùng sắt kín nếu cất giữ lâu dài. Khi vận chuyển tránh gây va đập. Trước khi hàn phải sấy lại trợ dung ở nhiệt độ 200 – 250oC, trong 1 giờ đồng hồ. Trợ dung hàn khi dùng xong có thể sàng sẩy để loại bỏ xỉ, sau đó có thể dùng lại bằng cách bổ sung thêm trợ dung gốm mới. Trợ dung hàn khi cháy sản sinh ra một lượng lớn các chất khí, vì vậy nơi làm việc phải thông thoáng. 3.1.2.9. Nguyên liệu trong nước sử dụng chế tạo trợ dung hàn gốm Qua tìm hiểu cho thấy các nguyên liệu được dùng để chế tạo trợ dung hàn gốm, phần lớn là sản xuất trong nước cho chất lượng tốt và ổn định, các nguyên liệu này có mặt ở nhiều nơi nước ta [1]. Boxit có rất nhiều ở Tây Nguyên, tuy nhiên chưa khai thác hiện tại vẫn phải nhập khẩu và Fero mangan sản xuất trong nước có tỷ lệ cacbon cao (khoảng 7%) , không dùng chế tạo trợ dung hàn gốm được nguyên liệu này cũng phải nhập khẩu. Bảng 3.11. Thành phần hóa học của vật liệu trong nước dùng để sản xuất trợ dung hàn [1] 3.2. Trang thiết bị nghiên cứu hàn thử nghiệm Trợ dung hàn sau khi chế tạo xong cần được thử nghiệm thông qua hàn để đánh giá chất lượng và khả năng ứng dụng. 3.2.1. Chuẩn bị trước khi hàn và tiến hành hàn Công việc chuẩn bị mẫu gồm: - Máy hàn kèm theo bộ phận cấp dây và trợ dung gốm, bộ phận điều chỉnh di chuyển dọc, ngang của đầu hàn. - Trợ dung gốm. - Đồ gá hàn. - Mẫu để hàn. - Bảo hộ lao động. - Tiến hành hàn. 3.2.1.1. Máy hàn Sử dụng máy hàn Amada 630-1 để hàn thử nghiệm (địa chỉ: Khoa Cơ-Điện - Học viện Nông nghiệp Việt Nam, Trâu Quỳ - Gia Lâm - Hà Nội). Đây là loại máy hàn điều khiển bằng công nghệ thyristor sản xuất tại Trung Quốc. Hình 3.11. Máy hàn Amada 630-1 Tính năng: - Điện áp ba pha, có bốn bánh xe cho di chuyển - Điều chỉnh thuận tiện, thích hợp cho nhiều vị trí hàn khác nhau. - Động cơ servo điều chỉnh cho quá trình cấp dây và hệ thống bước. - Lý tưởng để hàn tự động trong lĩnh vực công nghiệp và công nghiệp nặng. - Dòng hàn ổn định, mối hàn thẩm mỹ. - Hiệu suất cao mà tiêu thụ năng lượng thấp, giảm tối đa chi phí sản xuất. - Cấu tạo máy đơn giản dễ vận hành và bảo dưỡng Dưới đây là thông số kỹ thuật cơ bản của máy: Bảng 3.12. Thông số kĩ thuật máy hàn Amada 630-1 Đặc trưng kỹ thuật Đơn vị Auto Tractor-630-1 Nguồn hàn Armada-630K Nguồn cung cấp V 380 Dòng hàn A 630 Đường kính dây mm 2 – 6 Tốc độ cấp dây m/phút 0.3-3 Tốc độ hàn m/giờ Oct 85 Điều chỉnh độ cao mm 100 Điều chỉnh đầu hàn mm 4100x100x70 Góc xoay của đầu độ 90 Trọng lượng máy kg 65 Kích thước bên ngoài máy mm 1020 ×480 ×740 3.2.1.2. Bộ phận cấp dây, cấp trợ dung gốm Bộ phận cấp dây Bộ phận cấp dây (Hình 3.12) đóng vai trò điều chỉnh tốc độ đưa dây, tốc độ đưa dây được tự động điều chỉnh theo cường độ và điện áp hàn được đặt trước. Nó được điều khiển thông qua hệ thống bảng điều khiển. Hình 3.12. Bộ phận cấp dây (1.Dây hàn, 2.Bộ phận cấp dây, 3.Bánh răng dẫn có rãnh, 4.Tay vặn, 5.Bánh răng ép lực) Bộ phận cấp trợ dung hàn và bảng điều khiển Quá trình cấp thông số kĩ thuật máy hàn Amada 630-1 gốm cho quá trình hàn được thực hiện bằng phương pháp tự động. trợ dung hàn được đưa vào phễu cấp liệu có sàng lọc (loại bỏ sỉ, những hạt trợ dung có kích thước lớn, các vật chất khác như sỏi đá, rác,..). Được dẫn đến vị trí hàn bằng 1 ống dẫn, trên ống dẫn có van đóng mở để đóng ngắt việc cấp thuốc hàn. Trợ dung hàn dưới tác dụng của trọng lực sẽ rơi xuống vị trí hàn để phủ kín mối hàn và tham gia vào quá trình hàn. Hình 3.13. Bộ phận cấp trợ dung gốm và bảng điều khiển Bộ phận điều khiển quá trình hàn gồm có: 1. Công tắc nguồn, 2. Nút ấn bất đầu quá trình hàn, 3. Bảng chỉ thông số hàn, 4. Nút điều chỉnh dòng hàn, 5. Nút điều chỉnh dòng hàn kết thúc, 6. Nút điều chỉnh tốc độ hàn, 7. Nút điều chỉnh hiệu điện thế, 8. Nút điều chỉnh hiệu điện thế hàn kết thúc, 9. Điều chỉnh, 10. Nút dừng máy hàn, 11. Nút điều chỉnh dây hàn đi xuống, 12. Nút điều chỉnh dây hàn lên, 13. Nút xoay chọn đường kính dây hàn, 14. Công tắc điều chỉnh hướng di chuyển của xe hàn, 15. Công tác điều chỉnh thông số hàn, 16. Công tắc cài đặt hàn sẵn, 17. Nút xoay điều chỉnh xe hàn. 3.2.1.3. Chuẩn bị dây hàn và trợ dung gốm Trợ dung hàn dùng trong nghiên cứu này do tác giả phối liệu. Trước khi hàn trợ dung hàn phải được sấy khô, độ ẩm tối đa cho phép không quá 0,1%, nhiệt độ sấy 200- 250oC. Hình 3.14. Tủ sấy trợ dung hàn Hai loại dây hàn cho thép hợp kim thấp W49-VD và thép cacbon thấp H08A-VD của Công ty cổ phần Que hàn điện Việt - Đức, địa chỉ: Thường Tín - Hà Nội - Việt Nam, điện thoại: (024) 33853653 được sử dụng để hàn thực nghiệm trong luận án này. Dây hàn Việt Đức W49-VD (ER70S-6) tương đương tiêu chuẩn: ASME/AWS A5.18 ER70S – 6; EN 440GrSi1; JIS: YGW12; Quy chuẩn Việt Nam: 2: 2010/BGTVT SW52, là loại dây hàn có hàm lượng cacbon thấp, hàm lượng mangan và silic cao, tạp chất như lưu huỳnh, phôtpho rất ít sẽ tạo ra mối hàn có độ bền và độ dẻo dai cao. Tương tự, dây hàn Việt Đức H08A-VD tương đương tiêu chuẩn áp dụng ASME/AWS A5.17 EL12,ASME/AWS A5.17 EL8 được sử dụng để hàn thép cacbon thấp. 3.2.1.4. Điều kiện thí nghiệm Tiến hành thử nghiệm trên cùng mẫu thép Q460D và thép Q235 với các thông số và lượng vật liệu khác nhau (bảng 3.13). Bảng 3.13. Các điều kiện thí nghiệm TT Ký hiệu mẫu Chế độ hàn thực nghiệm Ghi chú 1 N01 Mẫu thép nền, mẻ trợ dung hàn Phối liệu 1 Thép Q235 Thép Q460D 2 N02 Mẫu thép nền, mẻ trợ dung hàn Phối liệu 2 3 N03 Mẫu thép nền, mẻ trợ dung hàn Phối liệu 3 4 N04 Mẫu thép nền, mẻ trợ dung hàn Phối liệu 4 5 N05 Mẫu thép nền, mẻ trợ dung hàn Phối liệu 5 6 N06 Mẫu thép nền, mẻ trợ dung hàn Phối liệu 6 7 N07 Mẫu thép nền, mẻ trợ dung hàn Phối liệu 7 8 N08 Mẫu thép nền, mẻ trợ dung hàn Phối liệu 8 9 N09 Mẫu thép nền, mẻ trợ dung hàn Phối liệu 9 3.2.1.5. Chuẩn bị mẫu để hàn Mẫu để hàn thép Q 235 và Q 460D có kích thước 350x250x25 mm và 350x250x20 (Hình 3.15), làm sạch bề mặt và rãnh của mẫu bằng máy mài hoặc giấy nhám trước khi hàn. Tiến hành hàn thử nghiệm trên cùng mẫu thép Q460D và thép Q235 với mẻ trợ dung hàn phối liệu khác nhau thể hiện như trong Bảng 3.20. Hình 3.15. Mẫu hàn 3.2.2. Mẫu và thiết bị kiểm tra 3.2.2.1. Thử cơ tính Thử cơ tính để xác định độ bền và độ tin cậy khi làm việc của kết cấu hàn, qua đó xem xét lại vật liệu hàn hoặc chế độ hàn. Mặt khác cơ tính cho phép đánh giá bậc thợ để chọn thợ phù hợp với yêu cầu. Thử cơ tính bao gồm thử tĩnh và thử va đập ở nhiệt độ thường, một số trường hợp thử ở nhiệt độ rất cao hoặc nhiệt độ âm. Đối với liên kết hàn của các kết cấu chịu nhiệt, làm việc ở nhiệt độ thấp hoặc tải trọng rung động thì phải tiến hành thử bổ sung độ dai va đập và độ bền mỏi. 3.2.2.2. Thử tĩnh Có thể tiến hành thử: (i) kéo các phần khác nhau của liên kết cùng kim loại nóng chảy; (ii) kéo liên kết hàn; (iii) uốn liên kết hàn. Tiến hành trên mẫu thử được cắt ra từ chính kết cấu cần kiểm tra hoặc các liên kết đặc biệt được hàn tương ứng với các điều kiện kỹ thuật xác định. Việc tách mẫu được tiến hành cẩn thận để tránh thay đổi kích thước và thay đổi trạng thái mẫu. Không lấy mẫu ở chỗ bắt đầu hàn và kết thúc mối hàn (50mm). Những mẫu có độ võng f trên chiều dài 200m không được vượt quá 10% chiều dày tấm không quá 4mm. Độ lệch hai mép hàn giáp mối hay hàn đắp h (Hình 3.18) không vượt quá 15% chiều dày tấm và không quá 4mm. Hình 3.16. Tách mẫu Nhiệt độ kiểm tra trong phòng thường lấy 200C. Số mẫu thử dùng để kéo không ít hơn hai, đối với các phương pháp khác không ít hơn ba. Thử kéo kim loại mối hàn Mục đích thử dùng trong trường hợp để phê chuẩn quy trình hàn cho một số ứng dụng. Việc thử không chỉ đo độ bền kéo, mà còn đo giới hạn chảy và độ giãn dài tương đối. Nhà sản xuất vật liệu hàn đôi khi thực hiện thử kéo nhằm xác định dây hàn, thuốc hàn, đắp ứng các cơ tính và tiêu chuẩn quy định để cấp chứng chỉ hợp cách cho kim loại hàn đó. Mẫu kiểm tra được gia công từ kim loại mối hàn hướng song song với trục của mối hàn và vuông góc với trục mối hàn (Hình 3.17) theo TCVN 6259-6 tương đương với GB/T13298[45, 87]. Vật thử kim loại đắp b) Mẫu thử kéo kim loại đắp Hình 3.17. Mẫu thử kim loại đắp. Vật thử kim loại hàn giáp mép b) Mẫu thử kéo kim hàn giáp mối Hình 3.18. Mẫu thử kim loại giáp mối. Nhờ các chỉ tiêu phản ánh độ bền của kim loại và hợp kim mà ta đánh giá được khả năng sử dụng của kim loại và hợp kim đó. 3.2.2.3. Thử độ dai va đập Độ dai va đập (ak) là khả năng vật liệu chịu tải trọng động mà không bị phá hủy giòn. Các giá trị độ dai va đập được quy định trong nhiều tiêu chuẩn, do nhiều vật liệu có thể bị phá hủy giòn, kể cả khi độ bền kéo đạt yêu cầu, sự phá hủy này là đặc biệt nghiêm trọng khi vật liệu có rãnh hoặc vết khía trên bề mặt. Độ dai va đập của kim loại trong vùng liên kết bằng tỷ số giữa năng lượng hấp thu bị phá hủy (công phá hủy) mẫu với tiết diện ngang tại chỗ rãnh khía. Cũng cần chú ý rằng giá trị độ dai va đập (ak, kJ/m2) chỉ để tham chiếu chứ nó không có trong các phép tính sức bền. Để thử độ dai va đập người ta thực hiện trên máy thử va đập bằng lực đập của búa với độ cao h để phá hủy mẫu kim loại. Có hai loại mẫu được sử dụng để xác định độ dai va đập: - Mẫu Charpy có kích thước 10x10x55mm, khi thử phải ngàm hai đầu trên máy. - Mẫu Izod có kích thước 10x10x75 mm, xẻ rãnh chữ V sâu 2 mm cách một đầu 28mm và ngàm tại đầu này trên máy. Quả búa con lắc của máy đập vào mặt đối diện chỗ xẻ rãnh, đồng hồ của máy chỉ giá trị công phá hủy mẫu. Thử Charpy-V được dùng nhiều do dễ kiểm tra mẫu thử với khoảng nhiệt độ rộng. Phương pháp này là đo năng lượng phát sinh và lan truyền, tạo thành nứt từ rãng khía tại các mẫu chuẩn bằng tác động tải trọng va đập. Hình 3.19. Mẫu thử độ dai va đập theo tiêu chuẩn Phép thử được thực hiện trên mẫu theo tiêu chuẩn quốc tế. Có thể các mẫu tiêu chuẩn hóa với kích thước nhỏ hơn 10mm × 7,5 mm và 10mm × 5mm. Tuỳ thuộc vào mục đích thử mà rãnh khía được bào (hoặc cưa) ở các vị trí khác nhau ở đường tâm mối hàn, vùng nóng chảy hay vùng ảnh hưởng nhiệt. Ngoài ra hướng trục c
File đính kèm:
luan_an_nghien_cuu_chat_luong_moi_han_ket_cau_thep_bang_han.docx
1. TRICH YEU LUAN AN TIENG VIET.docx
3. TÓm tẮt LA tieng Anh.docx
4. TÓm tẮt tieng viet.docx
5. Thong tin LA tieng Anh.docx
6. Thong tin LA tieng viet.docx