Luận án Nghiên cứu mòn biên dạng điện cực và chất lượng bề mặt gia công bằng phương pháp xung tia lửa điện
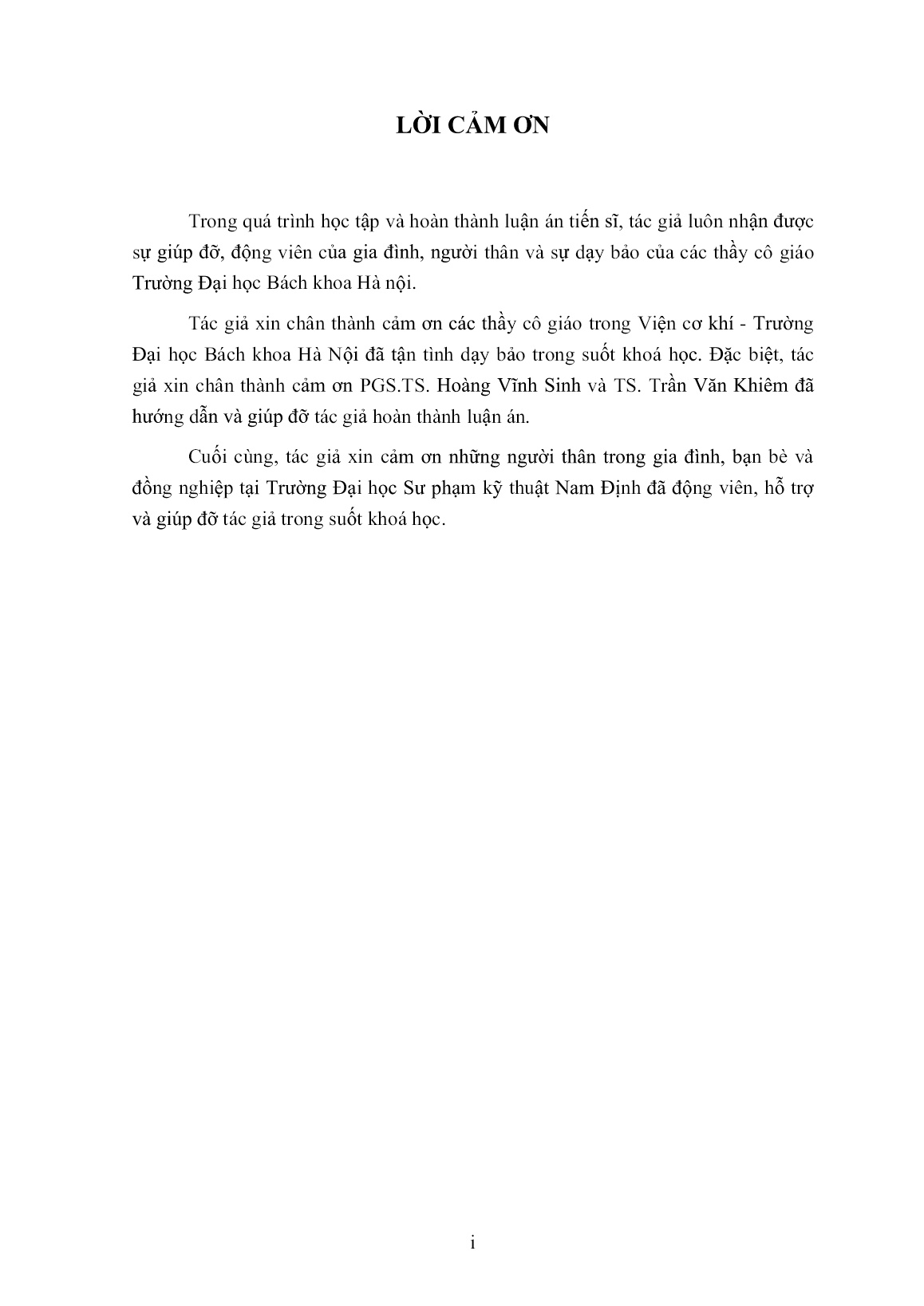
Trang 1
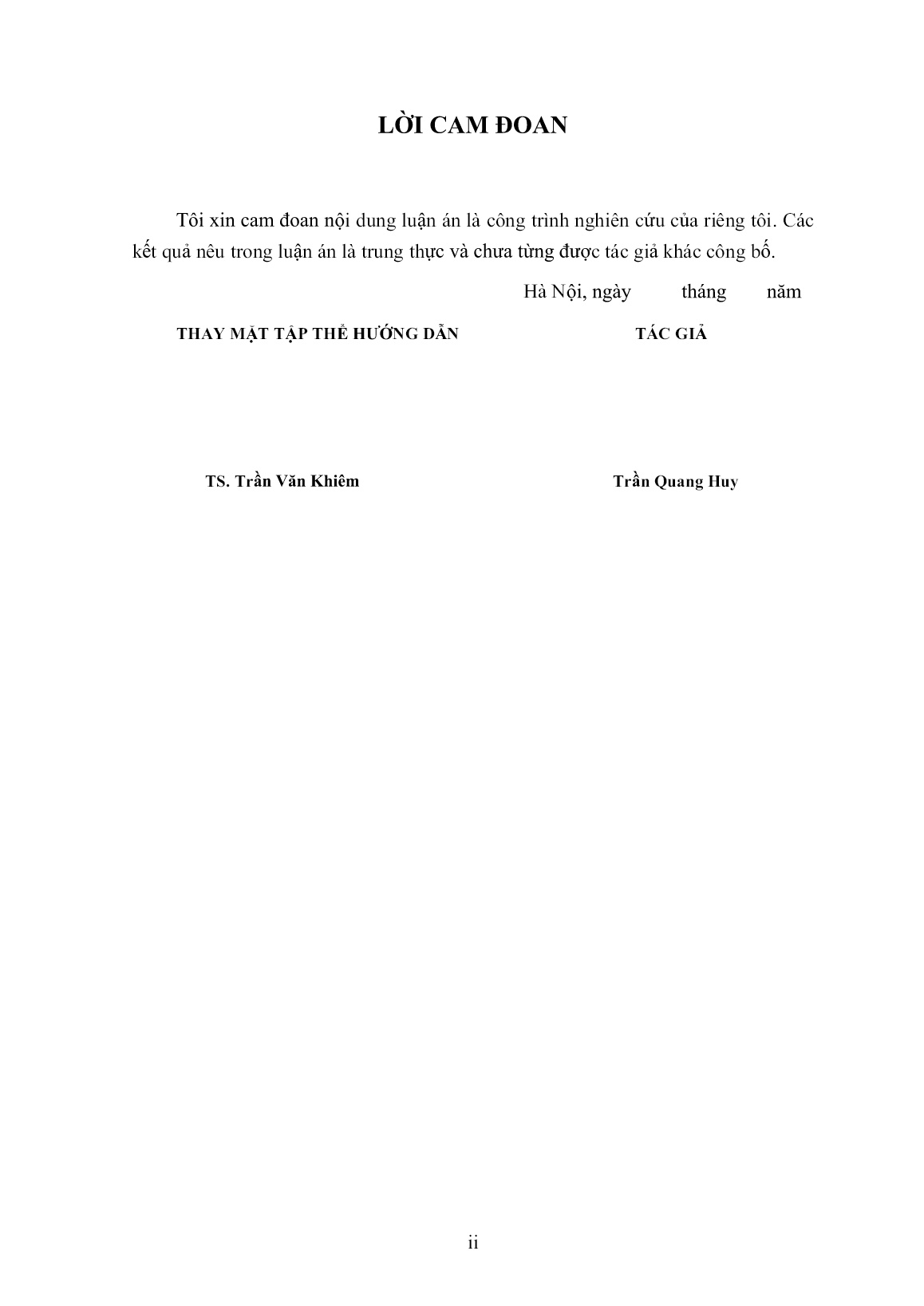
Trang 2
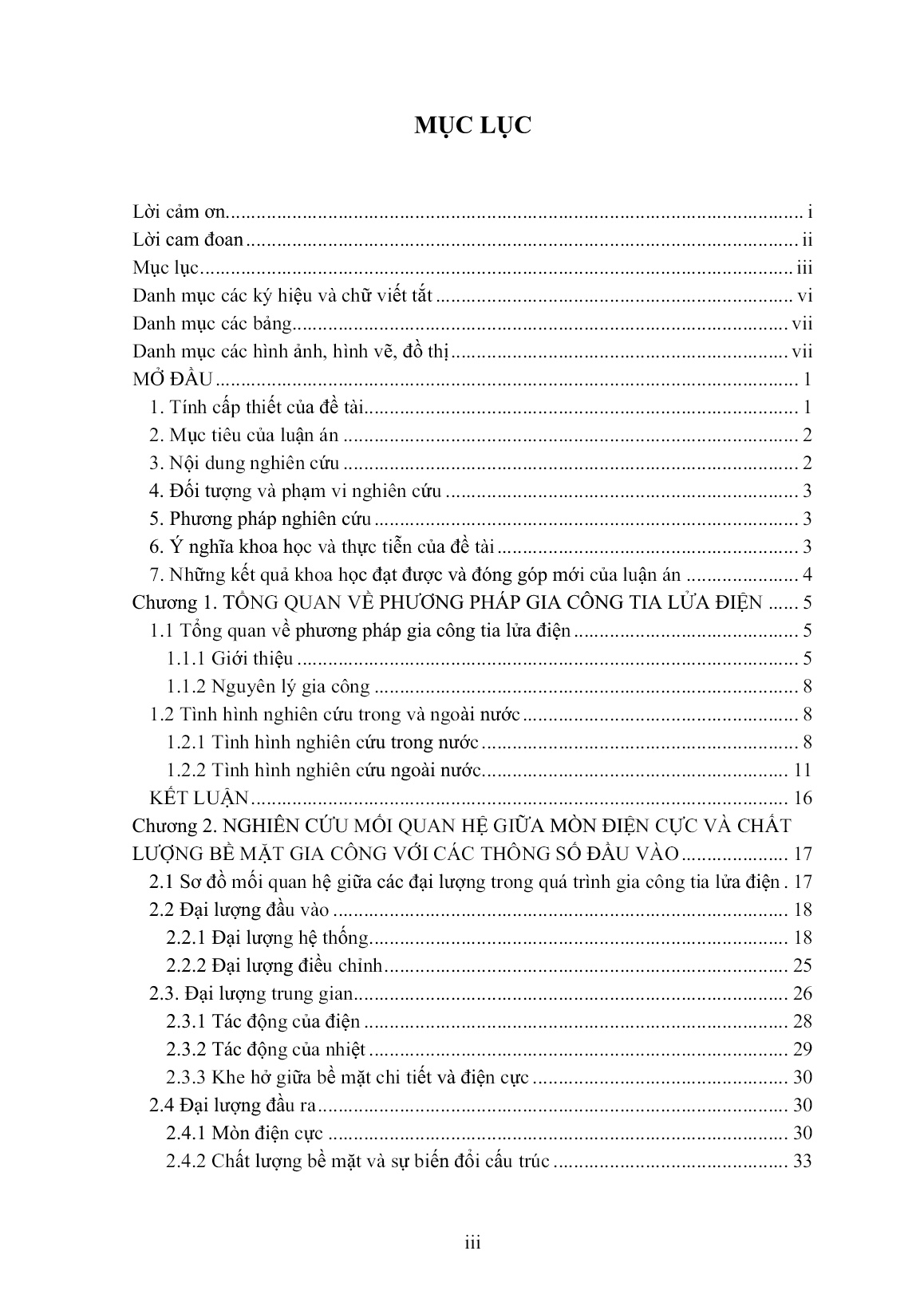
Trang 3
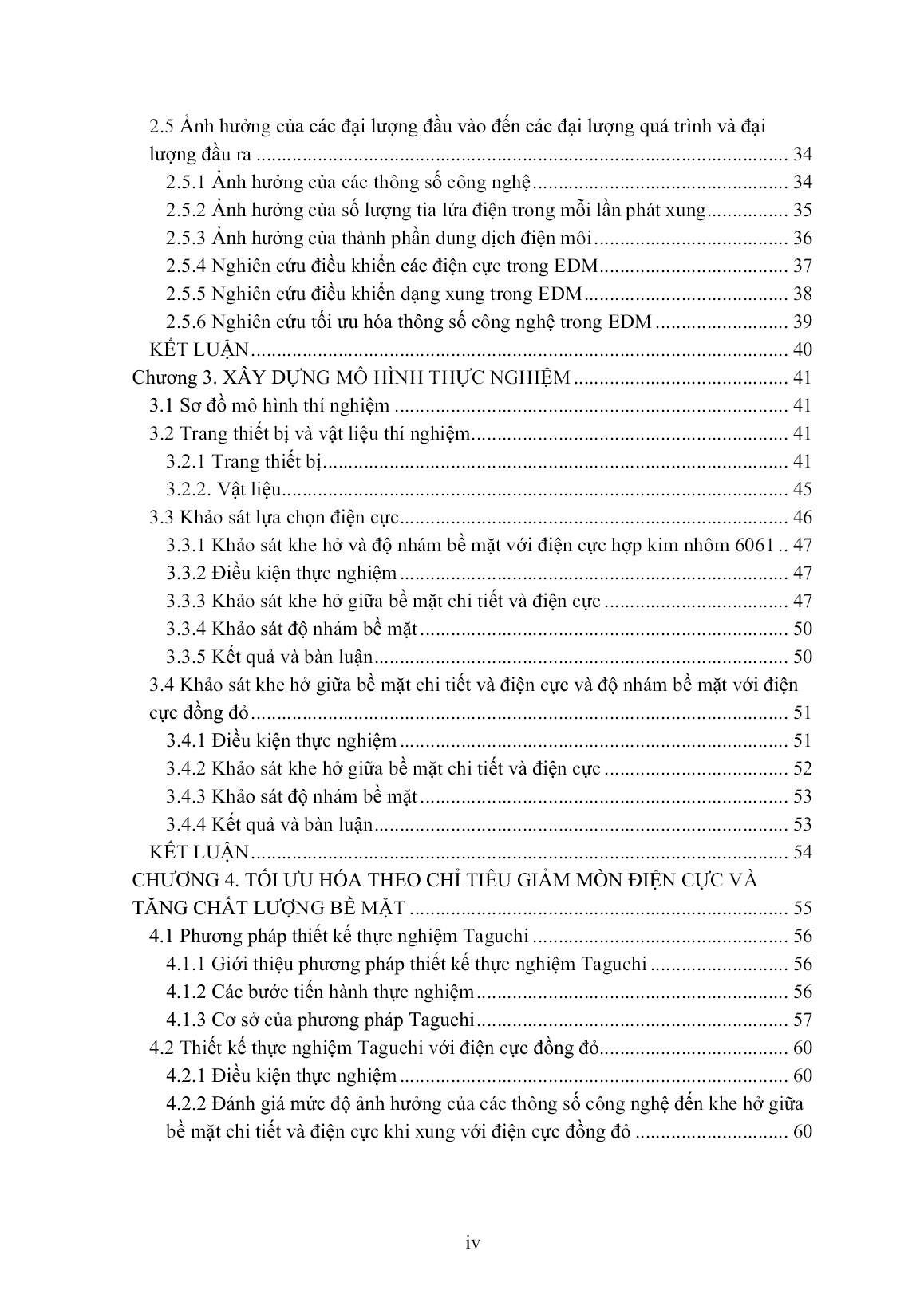
Trang 4
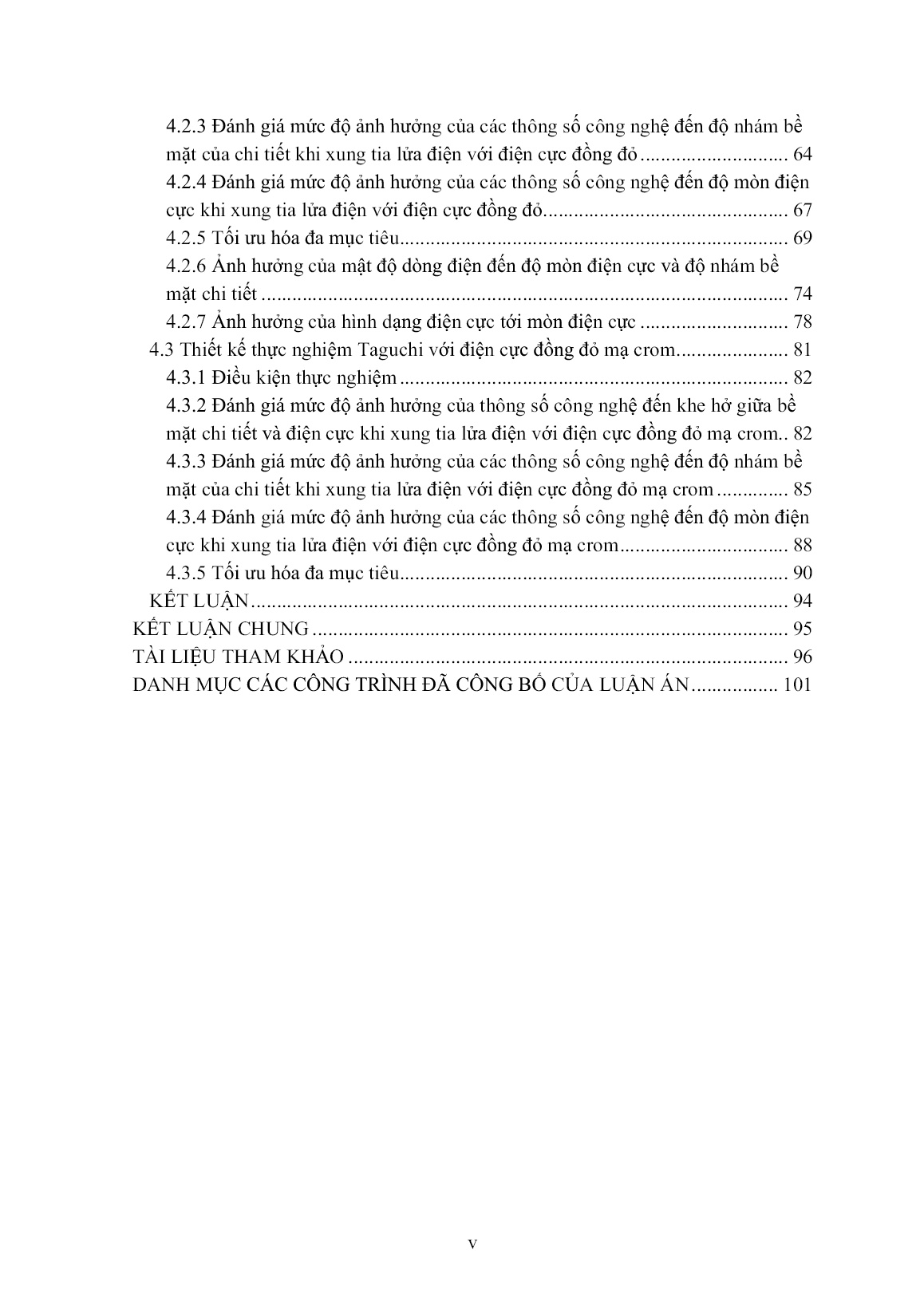
Trang 5
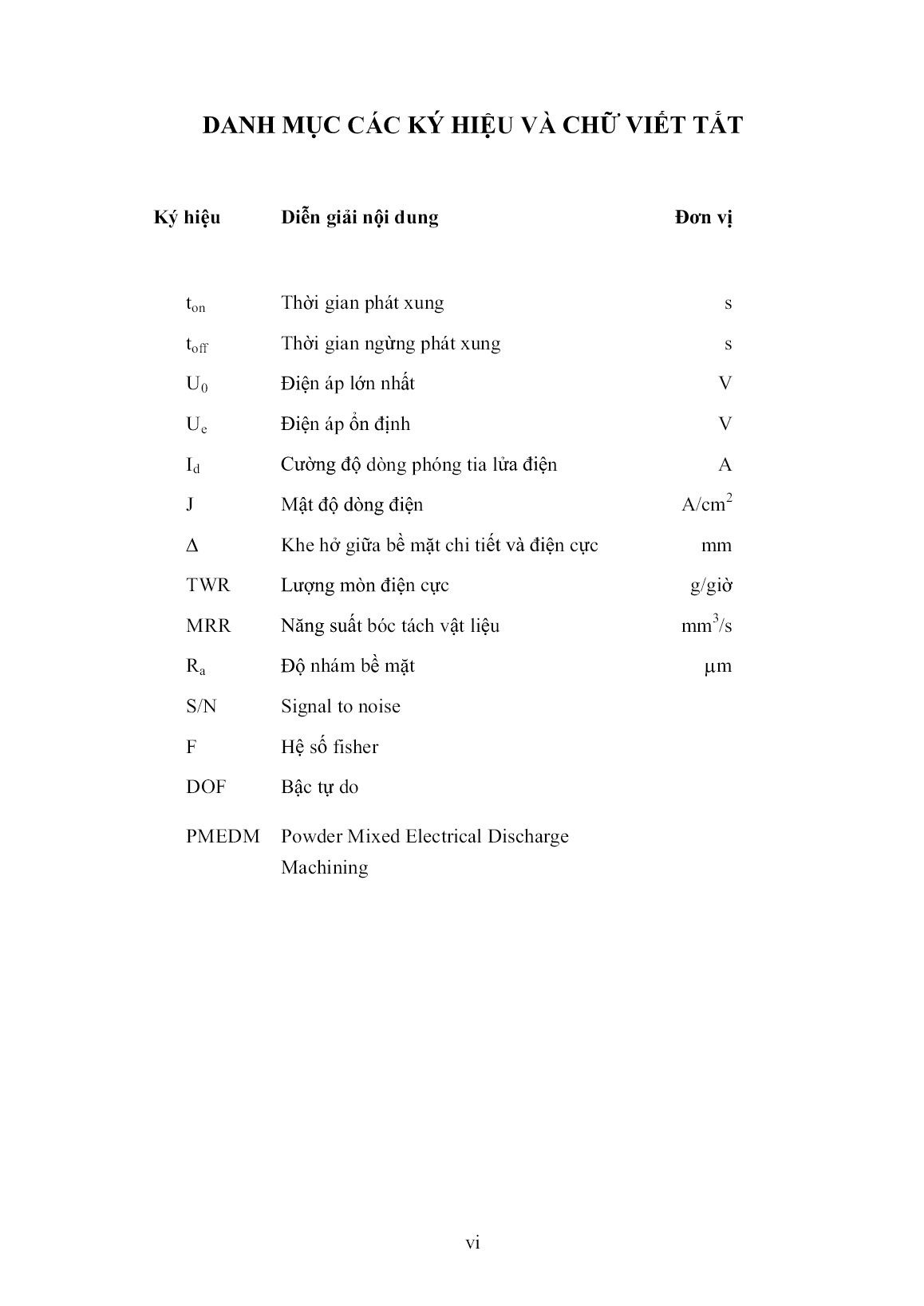
Trang 6
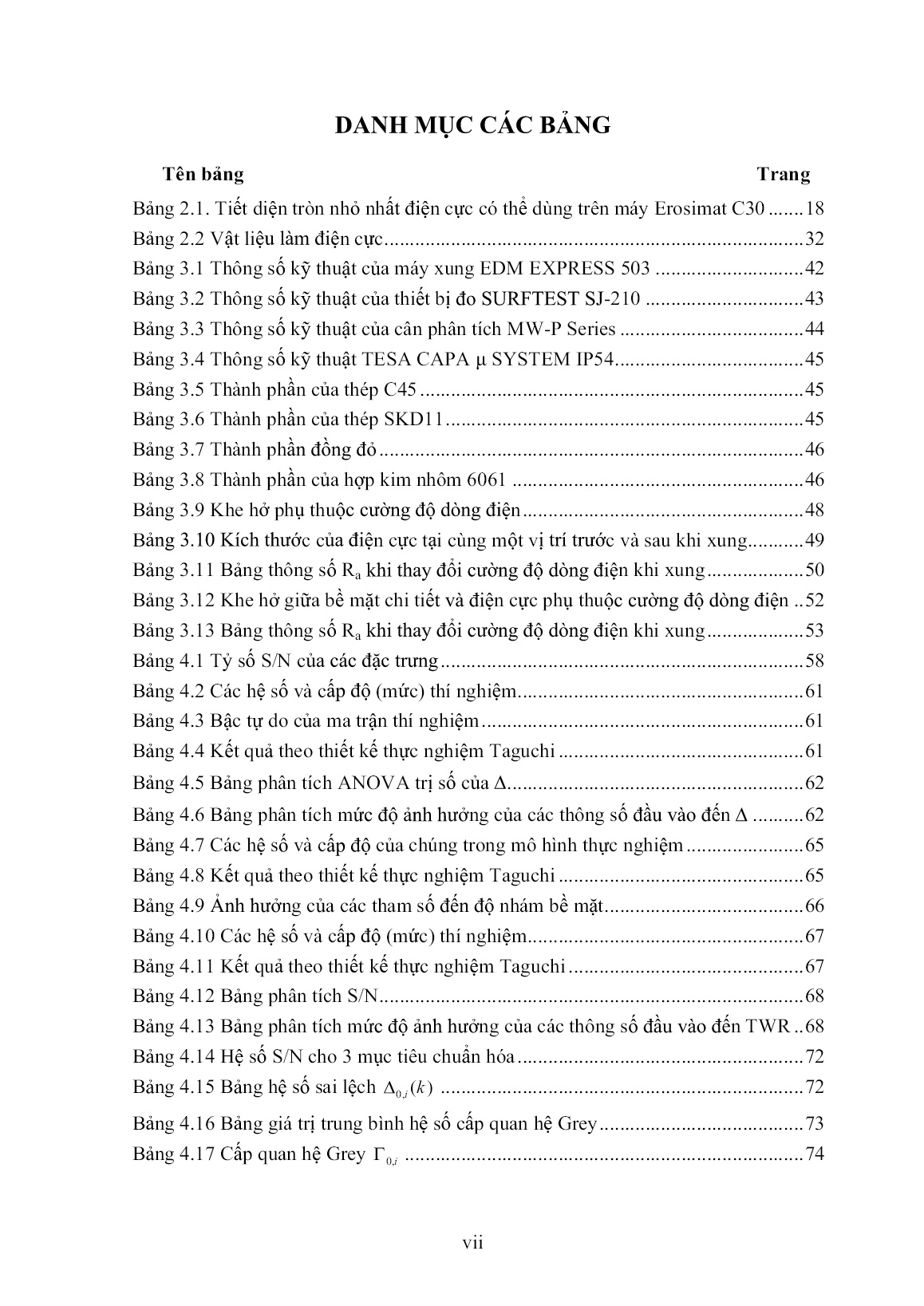
Trang 7
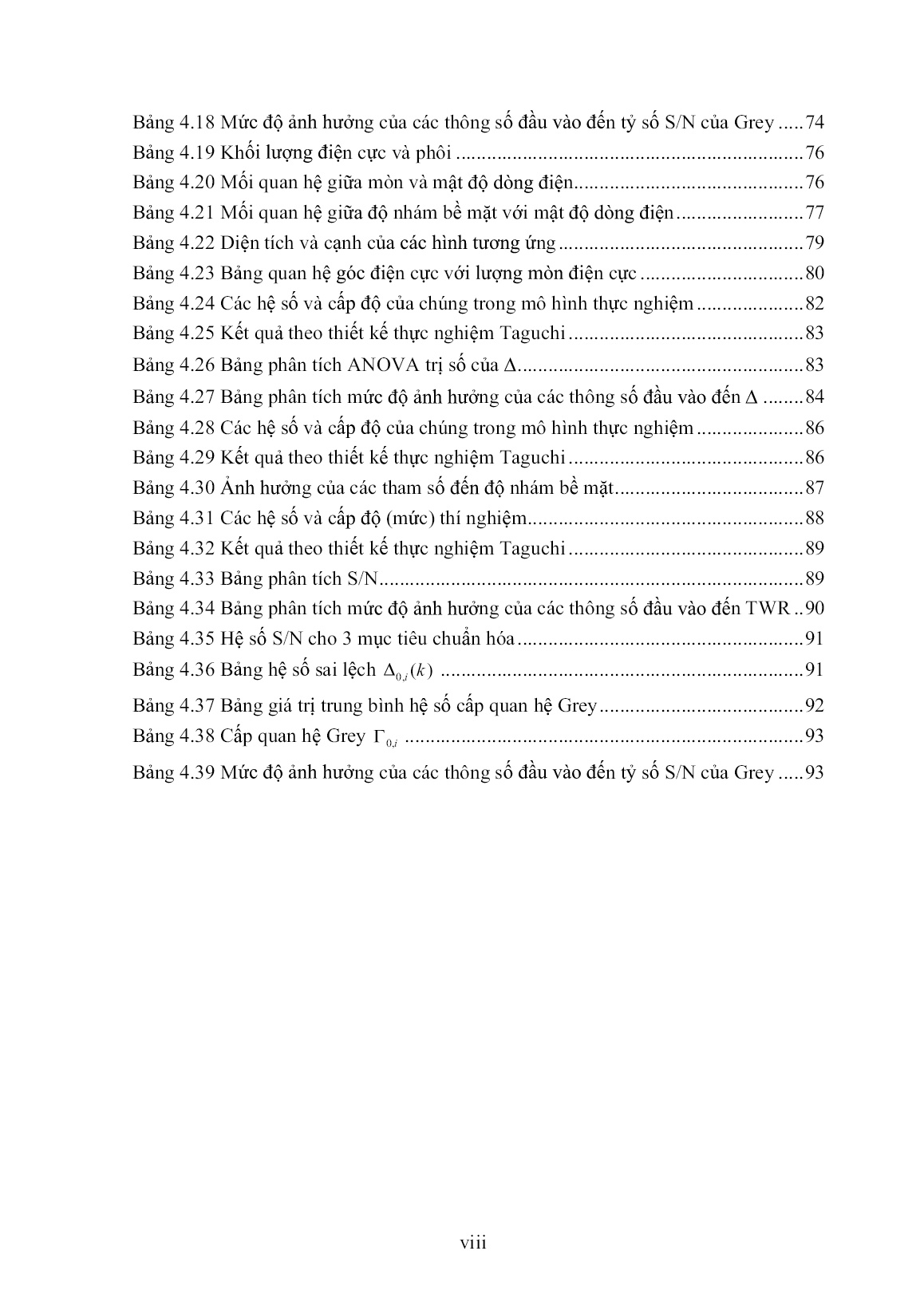
Trang 8
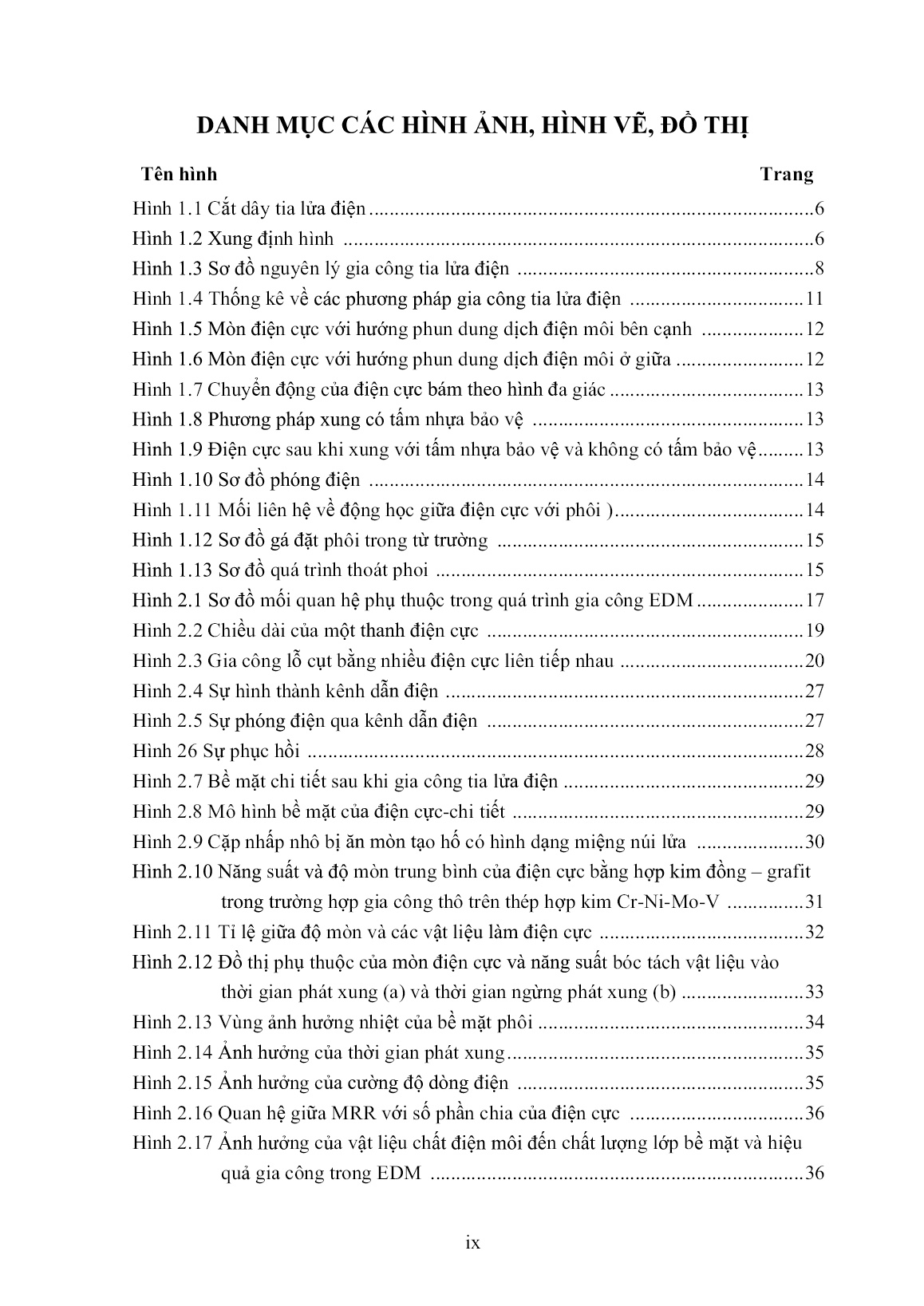
Trang 9
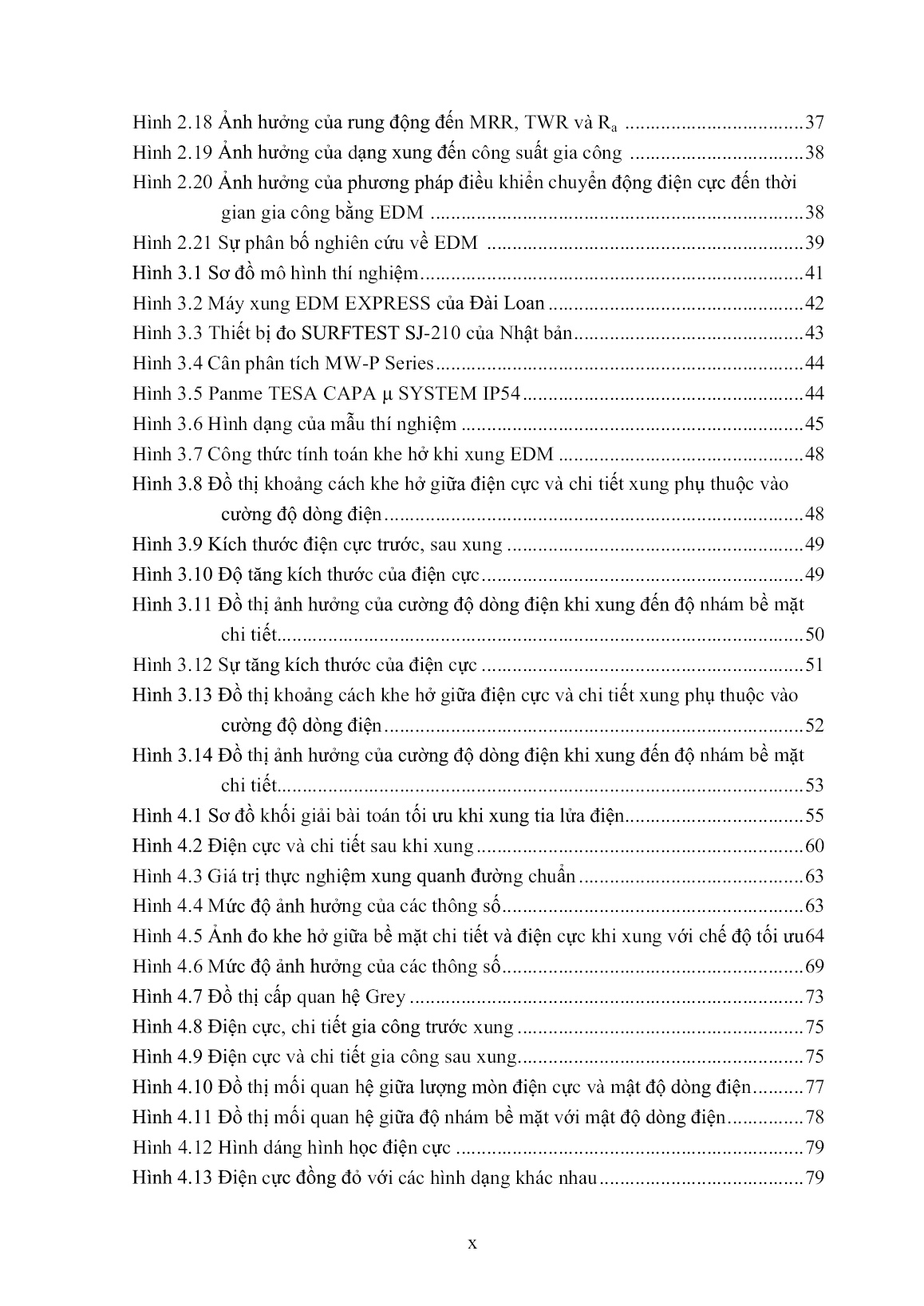
Trang 10
Tải về để xem bản đầy đủ
Bạn đang xem 10 trang mẫu của tài liệu "Luận án Nghiên cứu mòn biên dạng điện cực và chất lượng bề mặt gia công bằng phương pháp xung tia lửa điện", để tải tài liệu gốc về máy hãy click vào nút Download ở trên.
Tóm tắt nội dung tài liệu: Luận án Nghiên cứu mòn biên dạng điện cực và chất lượng bề mặt gia công bằng phương pháp xung tia lửa điện
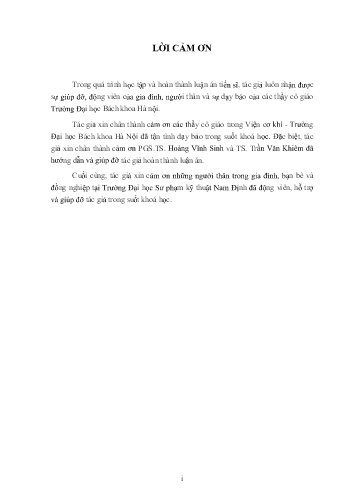
liệu của các điện cực tại nơi tiếp giáp với kênh dẫn điện bị bốc hơi. Bề mặt của chi tiết sau khi bị ăn mòn bằng tia lửa điện có hình dạng những hố nhỏ giống miệng núi lửa: Hình 2.7 Bề mặt chi tiết sau khi gia công tia lửa điện (Nguồn:[9]) Bề mặt của các điện cực luôn có những nhấp nhô (nhám). Khi đƣa chúng đến gần nhau, sẽ luôn có 1 cặp nhấp nhô đối diện có khoảng cách nhỏ nhất (trên hình 2.8 là điểm A). Tại đó, mật độ cƣờng độ điện trƣờng là lớn nhất (do khe hở là bé nhất) dẫn đến tia lửa điện sẽ xuất hiện và ăn mòn cặp nhấp nhô này (hình 2.9) Hình 2.8 Mô hình bề mặt của điện cực-chi tiết (Nguồn:[9]) 29 Hình 2.9 Cặp nhấp nhô bị ăn mòn tạo hố có hình dạng miệng núi lửa (Nguồn:[9]) Cặp nhấp nhô A biến mất sau 1 xung. Ở xung kế tiếp, cặp nhấp nhô B lại trở thành cặp nhấp nhô gần nhất. Tia lửa điện sẽ xuất hiện ở đó và "miệng núi lửa" thứ 2 đƣợc tạo ra. Hệ thống điều khiển có nhiệm vụ đƣa dần cặp điện cực đến gần nhau để bù lƣợng vật liệu đã bị ăn mòn tại các điểm A, B,.... Cứ nhƣ vậy, tia lửa điện sẽ đƣợc xuất hiện tại từng điểm và sẽ lan dần trên toàn bộ bề mặt đối diện nhau của cặp điện cực. Kết quả sẽ đƣợc bề mặt chi tiết nhƣ hình 2.7. Việc mòn của vật liệu điện cực là không mong muốn. Mục đích chính của các nghiên cứu về quá trình gia công EDM là tìm cách tăng lƣợng ăn mòn chi tiết, giảm lƣợng mòn của điện cực [9]. 2.3.3 Khe hở giữa bề mặt chi tiết và điện cực Điện cực đƣợc điều khiển chạy tự động để điều chỉnh khe hở giữa bề mặt chi tiết và điện cực không thay đổi ứng với mỗi điều kiện gia công xác định. Hệ thống điều chỉnh chuyển động điện cực phải đảm bảo các yêu cầu: Điều chỉnh kích thƣớc khe hở ổn định và tốc độ thích nghi nhanh để đáp ứng với sự ngắn mạch hoặc kích thƣớc khe hở. Độ rộng của khe hở không thể đo lƣờng trực tiếp nhƣng có thể đƣợc suy ra bởi điện áp trung bình tại khe hở [13]. 2.4 Đại lƣợng đầu ra 2.4.1 Mòn điện cực Việc lựa chọn hợp lý vật liệu điện cực là một yếu tố quan trọng. Điều này không những chỉ ảnh hƣởng đến độ chính xác gia công, mà còn ảnh hƣởng đến tính kinh tế thông qua năng suất và độ hao mòn điện cực. Trong quá trình gia công, chính điện cực cũng bị hớt đi một lớp mỏng vật liệu của nó, tuy rất nhỏ so với lƣợng hớt vật liệu của phôi, nhƣng lại ảnh hƣởng nhiều đến khả năng công nghệ. Sự hớt vật liệu từ điện cực này là không mong muốn 30 vì nó gây ra sự mòn điện cực [54]. Nguyên nhân là do mật độ điện từ tập trung ở bề mặt phôi (cực dƣơng) cao hơn nhiều lần so với mật độ ion dƣơng tập trung tới bề mặt dụng cụ (cực âm) trong khi mức độ tăng của dòng điện lại rất lớn. Đặc biệt là dòng ion chỉ đạt cực (+) trong những s đầu tiên. Để có thể giữ cho độ mòn điện cực là nhỏ nhất bằng cách chọn vật liệu điện cực phù hợp với phôi. Việc chọn các tham số ăn mòn điện cực cũng tác động lên độ mòn điện cực. Chính do sự mòn điện cực là nó gây ta sự không chính xác khi gia công. Độ mòn tƣơng đối của điện cực đƣợc xác định theo công thức [14]: V E .100% (2.4) VW Trong đó: VE là thể tích vật liệu bị mất đi ở điện cực VW là thể tích vật liệu phôi đƣợc lấy đi. Ảnh hƣởng lên độ mòn tƣơng đối của điện cực bao gồm các yếu tố sau: + Sự phối hợp điện cực/phôi + Dòng điện Ie hay bƣớc dòng điện + Độ kéo dài xung + Sự đấu cực. Có thể thấy năng suất và độ mòn trung bình của điện cực bằng hợp kim đồng – grafite trong trƣờng hợp gia công thô trên thép hợp kim Cr-Ni-Mo-V. Những trị số này chỉ là những chỉ số hƣớng dẫn, vì thông scí của máy cũng có ảnh hƣởng rất lớn. Hình 2.10 Năng suất và độ mòn trung bình của điện cực bằng hợp kim đồng – grafit trong trường hợp gia công thô trên thép hợp kim Cr-Ni-Mo-V (Nguồn: [2]) Trong trƣờng hợp gia công hợp kim cứng thì độ mòn sẽ lớn hơn, có thể thấy trên đồ thị hình 2.11. Trên thực tế, không có vật liệu nào có thể thỏa mãn đầy đủ những yêu cầu đặt ra cho vật liệu làm điện cực, do đó cần phải có sự lựa chọn khác nhau tùy vào 31 phƣơng pháp gia công. Thông thƣờng khi gia công thô và gia công tinh, ngƣời ta dùng các vật liệu điện cực khác nhau. Khi gia công thô, phổ biến nhất là dùng điện cực đồng thau và zamak, với tiết nhỏ thì dùng đồng và wolfram, ở máy lớn thì dùng dura. Khi gia công tinh thì có thể dùng điện cực đồng; cũng có trƣờng hợp dùng điện cực thép, đặc biệt khi làm dao cắt. Gia công hợp kim cứng thì thƣờng dùng điện cực đồng, đồng thau, đồng wolfram. Ở một số nƣớc thì dùng điện cực bằng đồng ép với bột silic-carbit. Gần đây nhất thì chủ yếu dùng điện cực grafite để gia công tinh các hốc, lỗ kín. Hình 2.11 Tỉ lệ giữa độ mòn và các vật liệu làm điện cực [Nguồn: [2]) Bảng 2.2 Vật liệu làm điện cực Loại Bột Vật Đồng Hộp gia Đồng Zamak Thép Gang Dura Grafite kim liệu đỏ thép công loại Thô Thép + + 0 - 0 + + + - HKC + - + - 0 - + + 0 Bán Thép + + + + + + 0 + - tinh HKC - - + + + - 0 + 0 Tinh Thép - - + + + - - + - HKC - - + + + - - + 0 Chú thích ký hiệu: (+) : Nên dùng (-) : Không nên dùng (0) : Chỉ nên dùng trong trƣờng hợp đặc biệt. 32 Độ chính xác gia công và nhám bề mặt khi gia công xung điện phụ thuộc vào nhiều yếu tố trong đó có vật liệu điện cực. Do đó việc chọn vật liệu điện cực thích hợp nhất đóng vai trò quan trọng trong quá trình lập quy trình công nghệ gia công xung điện. Ngoài ra, mòn điện cực và năng suất bóc tách vật liệu phụ thuộc nhiều vào thời gian phát xung và thời gian ngừng phát xung [17,36] nhƣ hình 2.12. a) b) Hình 2.12 Đồ thị phụ thuộc của mòn điện cực và năng suất bóc tách vật liệu vào thời gian phát xung (a) và thời gian ngừng phát xung (b)(Nguồn: [17]) 2.4.2 Chất lƣợng bề mặt và sự biến đổi cấu trúc Trong gia công xung định hình, điện cực đóng vai trò cực kì quan trọng vì chất lƣợng bề mặt gia công phụ thuộc vào độ chính xác của điện cực. Việc lựa chọn hợp lý vật liệu điện cực là một yếu tố quan trọng. Điều này không những ảnh hƣởng đến chất lƣợng bề mặt gia công, mà còn ảnh hƣởng đến tính kinh tế thông qua năng suất và độ hao mòn điện cực trung bình. Trong quá trình gia công, do phóng điện mà một lƣợng vật liệu trên bề mặt chi tiết gia công bị bóc đi, để lại trên bề mặt những vết nhỏ li ti chồng mép lên nhau. Kích thƣớc của các vết này phụ thuộc chủ yếu vào năng lƣợng sinh ra trong một lần phóng. Chất lƣợng bề mặt gia công mà đặc trƣng là độ nhám phụ thuộc vào năng lƣợng của một lần phóng điện. Một phần diện tích của tụ tạo nên vết lõm nên thể tích của vết lõm tỉ lệ với năng lƣợng phóng ra của tụ. Ngoài ra độ nhám còn phụ thuộc vào cƣờng độ dòng điện và tần số dòng điện. Ngoài những yếu tố trên còn có những yếu tố khác cũng có ảnh hƣởng đến độ nhám nhƣ: vật liệu điện cực, chất lƣợng của dung dịch điện môi v.v. Bề mặt gia công bằng EDM đƣợc đặc trƣng bởi hình dạng, thành phần hóa học, cấu trúc tổ chức tế vi và cơ lý tính của nó. Độ nhám bề mặt tăng khi năng lƣợng xung tăng. Nhiệt của các tia lửa điện sẽ tạo ra lớp bề mặt phôi bao gồm nhiều lớp: Lớp trắng, lớp tôi cứng, lớp ảnh hƣởng nhiệt và lớp không ảnh hƣởng (hình 2.13). 33 Lớp trắng là lớp kết tinh lại với các vết nứt tế vi do ứng suất dƣ vì nóng, lạnh đột ngột lặp đi lặp lại. Độ kéo dài thời gian xung càng lớn thì lớp này càng dày. Lớp bị tôi cứng, với cấu trúc tròn, lớp này có độ cứng tăng vọt so với kim loại nền. Lớp bị ảnh hƣởng nhiệt, do nhiệt độ ở đây đã vƣợt quá nhiệt độ Austenite trong một thời gian ngắn. Độ cứng này giảm so với lớp tôi cứng. Lớp không bị ảnh hƣởng nhiệt: có độ cứng bình thƣờng so với vật liệu nền [1]. Hình 2.13 Vùng ảnh hưởng nhiệt của bề mặt phôi (Nguồn: [1]) Bề mặt chi tiết đƣợc gia công EDM có thể đạt Ra = 0,63µm khi gia công thô và Ra = 0,16µm khi gia công tinh. Thông thƣờng độ chính xác gia công vào khoảng 0,01mm. Ở các máy khoan tọa độ EDM độ chính xác gia công đạt đến 0,0025mm. 2.5 Ảnh hƣởng của các đại lƣợng đầu vào đến các đại lƣợng quá trình và đại lƣợng đầu ra 2.5.1 Ảnh hƣởng của các thông số công nghệ Khả năng công nghệ của EDM không chỉ bị ràng buộc bởi công suất của máy mà còn phụ thuộc rất nhiều vào các thông số công nghệ. Công suất tiêu thụ, chất lƣợng bề mặt và năng suất bóc tách vật liệu của EDM chịu ảnh hƣởng bởi rất nhiều thông số công nghệ nhƣ: Điện áp phóng tia lửa điện, cƣờng độ dòng điện, khe hở giữa bề mặt chi tiết và điện cực, thời gian phát xung, thời gian ngừng phát xung, sự phân cực điện cực, dòng và đặc trƣng của dung dịch điện môi, độ dẫn điện của điện cực - phôi, diện tích gia công v.v [15,31, 34]. Các kết quả khảo sát với điện cực Cu và vật liệu gia công là thép SKD61 đã cho thấy: Khi tăng cƣờng độ dòng điện đã làm năng suất bóc tách vật liệu (MRR), Lƣợng mòn điện cực (TWR) và độ nhám bề mặt (Ra) tăng nhanh, nhƣng khi thời gian phát xung tăng dẫn đến MRR và Ra tăng còn TWR giảm (hình 2.14 và 2.15). 34 Và ảnh hƣởng của cƣờng độ dòng điện đến các chỉ tiêu đánh giá là mạnh hơn so với thời gian phát xung [52, 56]. Hình 2.14 Ảnh hưởng của thời gian phát xung (Nguồn: [52]) Hình 2.15 Ảnh hưởng của cường độ dòng điện (Nguồn: [52]) 2.5.2 Ảnh hƣởng của số lƣợng tia lửa điện trong mỗi lần phát xung Thông thƣờng trong EDM chỉ tạo ra một tia lửa điện cho mỗi lần phát xung. Để tạo ra nhiều tia lửa điện trong mỗi lần phát xung thì điện cực sẽ đƣợc chia thành hai hoặc nhiều phần điện cực nhỏ [27, 31]. Các phần điện cực nhỏ này sẽ đƣợc cách điện giữa chúng và đƣợc kết nối với bộ phận phát xung để tạo ra nhiều tia lửa điện đồng thời trong một lần phát xung làm tăng năng suất bóc tách vật liệu. Thông qua thực nghiệm khảo sát ảnh hƣởng của số phần chia điện cực Cu đến MRR trong gia công thép dụng cụ, tác giả Yang X. (2016) đã đề xuất giải pháp mới làm tăng số lƣợng các tia lửa điện [58]. Kết quả đã chỉ ra rằng, số lƣợng các tia lửa điện sẽ phụ thuộc vào số lƣợng các phần nhỏ của điện cực và khi số phần chia của điện cực tăng lên dẫn đến năng suất bóc tách vật liệu tăng theo (hình 2.16). Số lƣợng các tia lửa điện sẽ phụ thuộc vào số lƣợng các phần nhỏ của điện cực. Điện năng tiêu thụ của EDM thông thƣờng với EDM có điện cực đƣợc chia nhỏ tƣơng tự nhau, nhƣng công suất của tia lửa điện trong EDM có điện cực chia nhỏ sẽ bằng “n” lần so với EDM thông thƣờng trong một lần phát xung [18]. Do vậy, chất lƣợng bề mặt và MRR của EDM có điện cực chia nhỏ cao hơn so với EDM thông thƣờng nhƣng công suất tiêu 35 thụ lại nhỏ hơn. Tuy nhiên, việc chia nhỏ điện cực và đảm bảo sự cách điện giữa chúng là rất khó, nhất là bề mặt điện cực phức tạp hoặc kích thƣớc nhỏ. Hình 2.16 Quan hệ giữa MRR với số phần chia của điện cực (Nguồn: [58]) 2.5.3 Ảnh hƣởng của thành phần dung dịch điện môi Dung dịch điện môi sử dụng trong EDM có thể ở các dạng: lỏng, khí hoặc hỗn hợp lỏng và khí. Vật liệu dung dịch điện môi là các loại dầu cách điện, nƣớc khử ion và khí ga. Sự ảnh hƣởng của vật liệu dung dịch điện môi đến MRR và chất lƣợng bề mặt của thép làm khuôn 8407 trong EDM đã đƣợc Zhen L. et al. (2014) nghiên cứu tại [61]. Kết quả đã cho thấy: Vật liệu dung dịch điện môi có ảnh hƣởng mạnh đến hiệu quả gia công bằng EDM, dầu hỏa cho MRR thấp nhất trong 3 dung dịch điện môi đƣợc nghiên cứu và chất điện môi lỏng cho hiệu quả cao hơn chất khí (hình 2.17). Dung dịch điện môi có ảnh hƣởng rất lớn đến năng suất, chất lƣợng và độ ổn định quá trình gia công. Hình 2.17 Ảnh hưởng của vật liệu chất điện môi đến chất lượng lớp bề mặt và hiệu quả gia công trong EDM (Nguồn: [61]) 36 2.5.4 Nghiên cứu điều khiển các điện cực trong EDM Điều khiển chuyển động của các điện cực là điều khiển quan trọng nhất quyết định đến quá trình gia công bằng EDM. Hiện nay, điều khiển servo đƣợc sử dụng để điều khiển chuyển động của các điện cực nhờ đó điều khiển chính xác kích thƣớc khe hở giữa bề mặt chi tiết và điện cực, hiệu quả gia công và độ ổn định trong EDM. Trong thực tế không nhất thiết tia lửa điện có cƣờng độ tốt nhƣ nhau với hai lần phát xung liên tục khi khe hở giữa bề mặt chi tiết và điện cực không đổi. Điều này là do đỉnh và đáy của các nhấp nhô trên bề mặt phôi, hạt tạp chất trong dung môi đã làm thay đổi đặc trƣng dẫn điện trong khe hở giữa bề mặt chi tiết và điện cực. Hệ thống điều khiển thích nghi dùng để duy trì kích thƣớc khe hở mong muốn tạo ra tia lửa điện tốt, ngăn ngừa hiện tƣợng phóng hồ quang và ngắn mạch [18]. Một số kỹ thuật đã đƣợc ứng dụng để điều khiển thích nghi chuyển động EDM nhƣ: Tích hợp rung động, điều khiển mờ, thiết bị tạo xung và hệ thống điều khiển servo chuyển động điện cực [49]. Tác giả Ghiculescu D. et al. đã nghiên cứu tích hợp rung siêu âm trong điều khiển servo chuyển động điện cực Cu nhằm nâng cao năng suất và chất lƣợng quá trình gia công xung thép dụng cụ X210Cr12 [25]. Kết quả đã cho thấy: Tích hợp rung động trong EDM đã làm MRR tăng, TWR và Ra giảm (hình 2.18). Nghiên cứu các hệ thống điều khiển tối ƣu chuyển động servo của điện cực không chỉ giúp phát hiện những lỗi không mong muốn xuất hiện trong quá trình gia công mà còn tạo ra sự thay đổi thích nghi trƣớc khi các hiện tƣợng này xảy ra [51]. Tuy nhiên, đây là vấn đề rất phức tạp và cần tiếp tục nghiên cứu trong tƣơng lai. Hình 2.18 Ảnh hưởng của rung động đến MRR, TWR và Ra (Nguồn: [30]) 37 2.5.5 Nghiên cứu điều khiển dạng xung trong EDM Xung trong EDM thƣờng đƣợc phân thành các dạng: Xung hở, xung tia lửa điện, xung ngắn mạch, xung hồ quang và xung trễ [48]. Các dạng xung khác nhau sẽ có công suất gia công khác nhau (hình 2.19). Để có thể thực hiện gia công cần tạo ra xung tia lửa điện theo yêu cầu chất lƣợng bề mặt tốt hơn các xung khác. Các xung hồ quang và xung ngắn mạch cho bề mặt gia công có chất lƣợng thấp, quá trình gia công lại không ổn định do sự xuất hiện của các hạt dẫn điện tồn tại trong khe hở phóng điện và điều này đã ảnh hƣởng không có lợi cho quá trình gia công [49]. Trong những trƣờng hợp này, ngƣời vận hành máy cần thiết phải có những thao tác thích hợp để ổn định quá trình làm việc của máy. Chuyển động của điện cực đƣợc điều khiển thích nghi đã làm năng suất gia công đƣợc cải thiện đáng kể (tăng 57,5% với tốc độ chuyển động 0,5 m/s và 54,95% với 1 m/s) so với EDM đƣợc điều khiển servo (hình 2.20). Việc hình thành các dạng xung trong EDM chịu ảnh hƣởng của rất nhiều yếu tố trong đó một số yếu tố hiện nay vẫn đƣợc coi là nhiễu. Vì vậy, nghiên cứu nhằm tạo ra bộ điều khiển thích nghi trực tiếp để hạn chế sự xuất hiện các dạng xung không mong muốn nhằm ổn định quá trình hoạt động của máy cần đƣợc quan tâm. Hình 2.19 Ảnh hưởng của dạng xung đến công suất gia công (Nguồn: [48]) Hình 2.20 Ảnh hưởng của phương pháp điều khiển chuyển động điện cực đến thời gian gia công bằng EDM (Nguồn: [48]) 38 2.5.6 Nghiên cứu tối ƣu hóa thông số công nghệ trong EDM Các thông số công nghệ trong EDM thƣờng đƣợc xác định thông qua kinh nghiệm hoặc sổ tay công nghệ. Tuy nhiên, việc lựa chọn này sẽ không đảm bảo chắc chắn đƣợc kết quả gia công sẽ tối ƣu hoặc xấp xỉ trị số tối ƣu. Để khắc phục vấn đề này, hiện nay hầu hết ảnh hƣởng của các thông số công nghệ đều đƣợc tối ƣu theo các chỉ tiêu TWR nhỏ hơn, chất lƣợng bề mặt tốt hơn và năng suất bóc tách vật liệu cao hơn [29,47]. Phƣơng pháp đƣợc sử dụng trong các nghiên cứu là thực nghiệm nghiên cứu với sự kết hợp của nhiều cặp vật liệu điện cực - phôi khác nhau [33]. Tác giả Sanghani C. R. et al. (2014) đã giới thiệu một số phƣơng pháp và công cụ đƣợc sử dụng để giải quyết các bài toán tối ƣu hóa các mối quan hệ giữa thông số công nghệ và chỉ tiêu đánh giá chất lƣợng trong EDM [51]. Các mô hình đƣợc thực hiện thực nghiệm kiểm chứng và đã dự đoán đƣợc các đặc trƣng chất lƣợng mong muốn [49]. Nghiên cứu tối ƣu hóa các thông số công nghệ trong EDM rất phức tạp, kết quả nghiên cứu phụ thuộc rất nhiều vào vật liệu điện cực, phôi và máy gia công. EDM đã đƣợc ứng dụng khá phổ biến trong sản xuất, tuy nhiên nhiều vấn đề thuộc nguyên lý gia công của phƣơng pháp này vẫn chƣa đƣợc sáng tỏ nhƣ: Thời gian gia công thực tế, kích thƣớc chính xác của khe hở phóng điện v.v. Việc ứng dụng các hệ thống điều khiển tự động (CAD/CAM, CIM v.v) trong tự động hóa vận hành máy EDM chƣa nhiều [49]. Để có thể sử dụng tối đa hiệu quả kinh tế - kỹ thuật của EDM thì nghiên cứu làm rõ nguyên lý gia công và tự động hóa trong EDM cũng đang rất đƣợc quan tâm. Thống kê từ năm 1981 ÷ 2015 về nghiên cứu đã công bố trong EDM đƣợc trình bày trên hình 2.21. Hình 2.21 Sự phân bố nghiên cứu về EDM (Nguồn: [49]) 39 KẾT LUẬN Đã phân tích mối quan hệ giữa các đại lƣợng đầu vào, đại lƣợng trung gian, đại lƣợng đầu ra và lựa chọn đƣợc các thông số sau để nghiên cứu: - Đại lƣợng đầu vào bao gồm biên dạng và vật liệu điện cực cùng các thông số công nghệ của quá trình gia công là cƣờng độ phóng điện, thời gian phát xung và thời gian ngừng phát xung. - Đại lƣợng trung gian đặc trƣng là khe hở giữa bề mặt chi tiết và điện cực tạo ra trong quá trình lấy vật liệu dƣới tác động của điện và nhiệt. - Đại lƣợng đầu ra bao gồm mòn biên dạng điện cực và chất lƣợng bề mặt của chi tiết sau gia công. 40 Chƣơng 3. XÂY DỰNG MÔ HÌNH THỰC NGHIỆM 3.1 Sơ đồ mô hình thí nghiệm Trên cơ sở lý thuyết đã phân tích, phạm vi nghiên cứu của đề tài tập trung nghiên cứu về mòn điện cực và chất lƣợng bề mặt (đại diện là độ nhám bề mặt và chiều sâu lớp tôi cứng) dƣới tác dụng của các đại lƣợng đầu vào nhƣ máy xung EDM, dung dịch điện môi, vật liệu, hình dạng điện cực cũng nhƣ chế độ công nghệ ta xây dựng đƣợc sơ đồ mô hình thí nghiệm nhƣ sau: Máy xung EDM Dung dịch điện môi Vật liệu Vật liệu Chi tiết gia Điện cực công Chế độ công Biên dạng nghệ Đo độ nhám Đo chiều sâu Đo khe hở giữa Đo mòn điện bề mặt lớp tôi cứng bề mặt chi tiết cực và điện cực Mô hình hóa số liệu thí nghiệm Tối ƣu hóa thông số công nghệ Hình 3.1 Sơ đồ mô hình thí nghiệm 3.2 Trang thiết bị và vật liệu thí nghiệm 3.2.1 Trang thiết bị a) Máy thí nghiệm Máy thí nghiệm sử dụng trong công trình này là máy xung tia lửa điện EDM EPRESS của Đài Loan. 41 Hình 3.2 Máy xung EDM EXPRESS của Đài Loan Bảng 3.1 Thông số kỹ thuật của máy xung EDM EXPRESS 503 TT Tên thông số kỹ thuật Đơn vị Giá trị 350(+50) 1 Hành trình XYZ mm 200(+50) 150(+100) 2 Cƣờng độ phóng điện lớn nhất A 15 3 Hệ thống bơm dung dịch điện môi Có 4 Vỏ bao che máy có 1200 5 Kích thƣớc máy (kích thƣớc chung) mm 1000 dài x rộng x cao 1800 6 Kích thƣớc phôi tối đa theo X mm 400 7 Kích thƣớc phôi tối đa theo Y mm 300 8 Kích thƣớc phôi tối đa theo Z mm 100 9 Tải trọng phôi tối đa Kg 150 42 b) Thiết bị đo - Thiết bị đo độ nhám: Sử dụng thiết bị đo độ nhám SURFTEST SJ-210 của Nhật bản với các thông số kỹ thuật nhƣ bảng 3.2. Bảng 3.2 Thông số kỹ thuật của thiết bị đo SURFTEST SJ-210 TT Đặc tính Thông số Trục X 5,6 mm 1 Điều kiện làm việc Trục Z 360 m Sai số 0,02 m 2 Tốc độ đo 0,25mm/s 3 Lực tối đa 400mN Chuẩn làm việc JIS’82, JIS’94, JIS’01, 4 ISO’ 97, ANSI, VDA 5 Chuẩn đo Ra, Rz 6 Kích thƣớc WxDxH 52,1x65,8x160 7 Khối lƣợng 500g Hình 3.3 Thiết bị đo SURFTEST SJ-210 của Nhật bản 43 - Thiết bị đo mòn: Sử dụng cân phân tích MW-P Series độ chính xác 1/1000 Hình 3.4 Cân phân tích MW-P Series Bảng 3.3 Thông số kỹ thuật của cân phân tích MW-P Series TT Đặc tính Thông số 1 Tải trọng 150 x 0,005 g 2 Đơn vị đo g, ct, lb, oz, GN, ozt, dwt, tl, T 3 Kích thƣớc 200x250x80 mm3 4 Trọng lƣợng tối đa 1,1 kg 5 Chức năng Cân, đếm, tính phần trăm - Thiết bị đo kích thước: Sử dụng Panme TESA CAPA μ SYSTEM IP54 Hình 3.5 Panme TESA CAPA μ SYSTEM IP54 44 Bảng 3.4 Thông số kỹ thuật TESA CAPA μ SYSTEM IP54 Mã IP54 Đơn vị Khoảng đo lớn nhất 30 mm Sai số 0,001 mm 3.2.2. Vật liệu a) Vật liệu chi tiết Trong công trình nghiên cứ
File đính kèm:
luan_an_nghien_cuu_mon_bien_dang_dien_cuc_va_chat_luong_be_m.pdf
Thong tin tom tat ve luan an NCS Trần Quang Huy.pdf
tom tat LA NCS Trần Quang Huy.pdf