Luận án Nghiên cứu tạo cấu trúc siêu mịn cho vật liệu AZ31 bằng kỹ thuật ép cưỡng bức trong khuôn rãnh chu kỳ
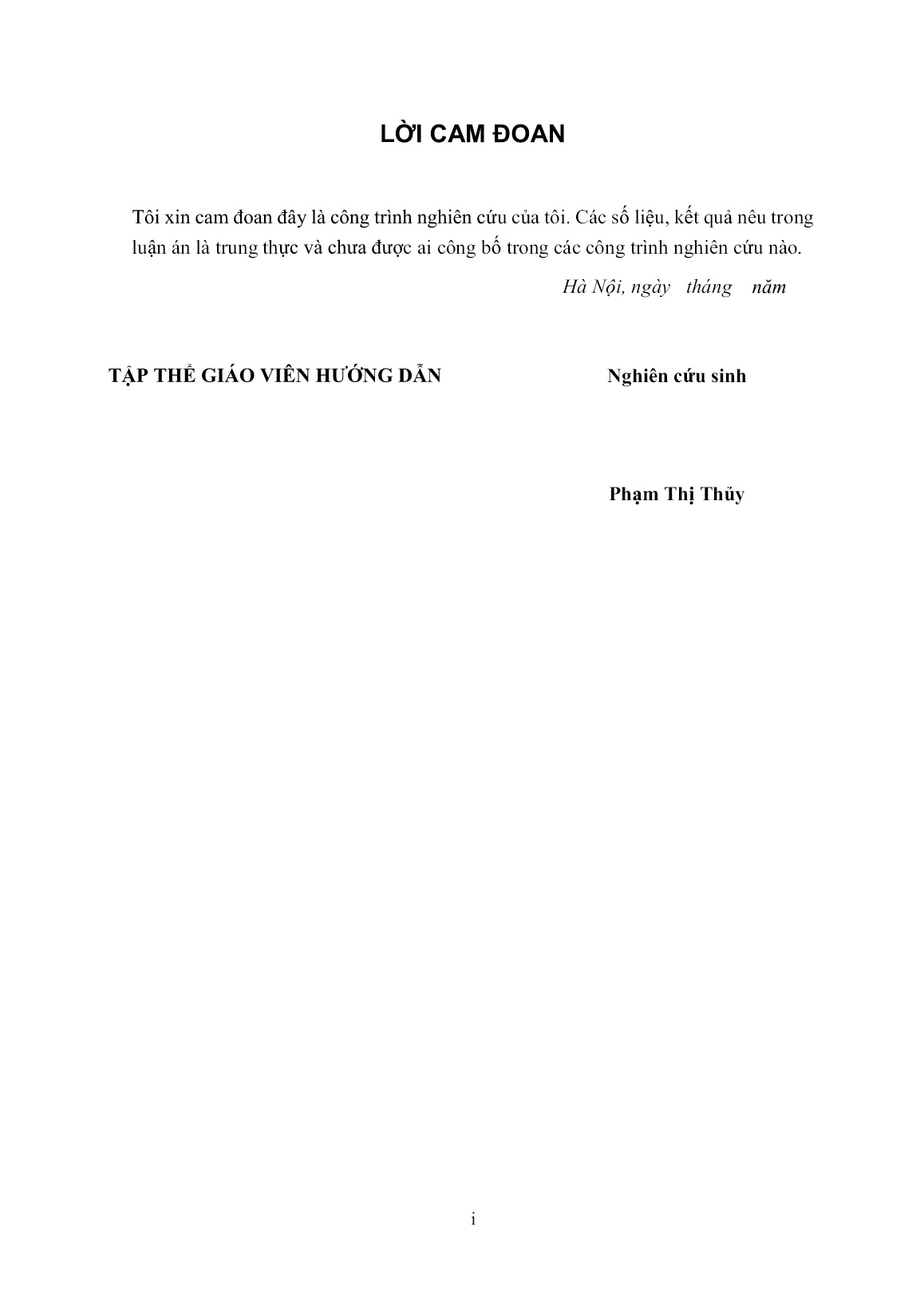
Trang 1
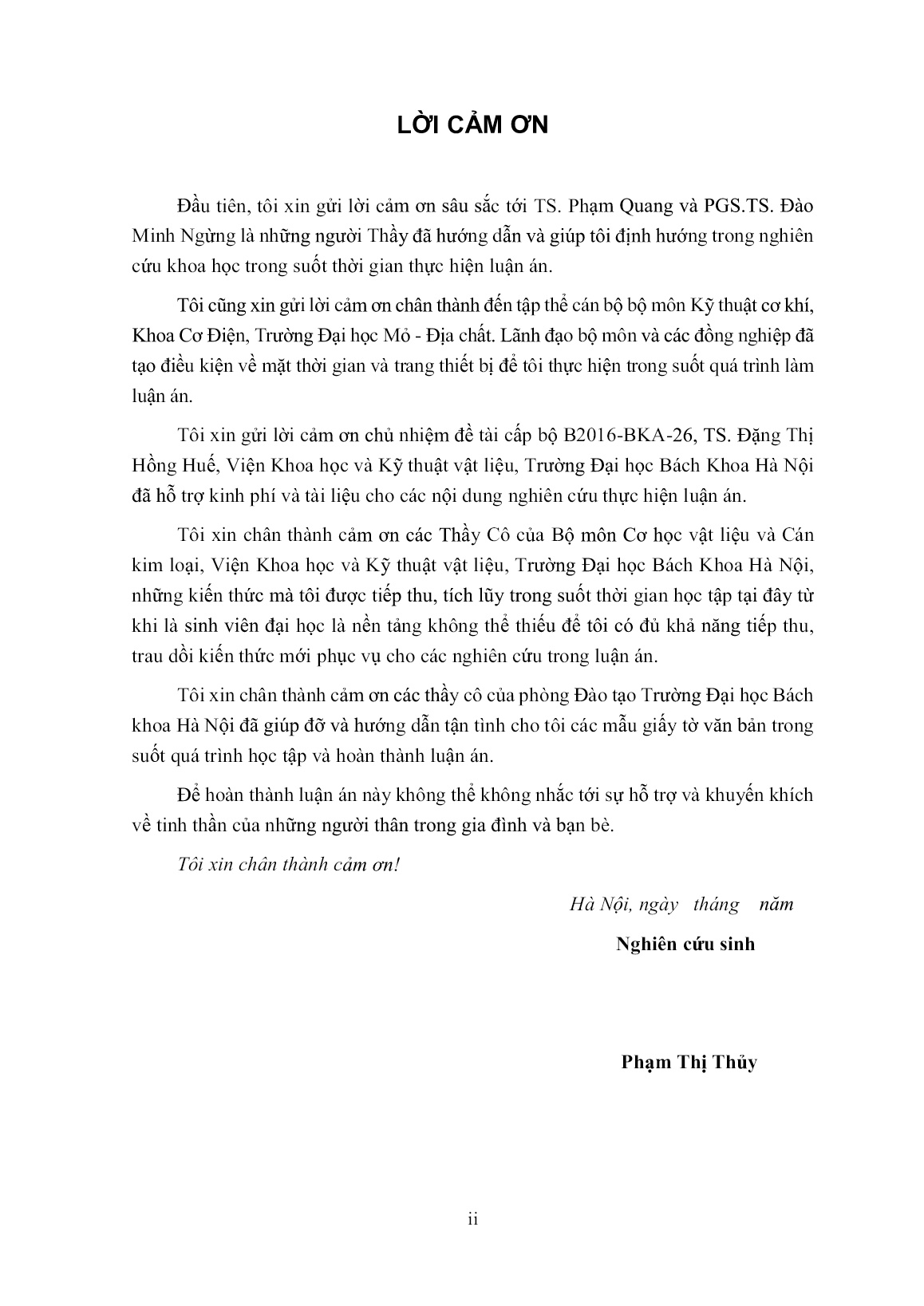
Trang 2
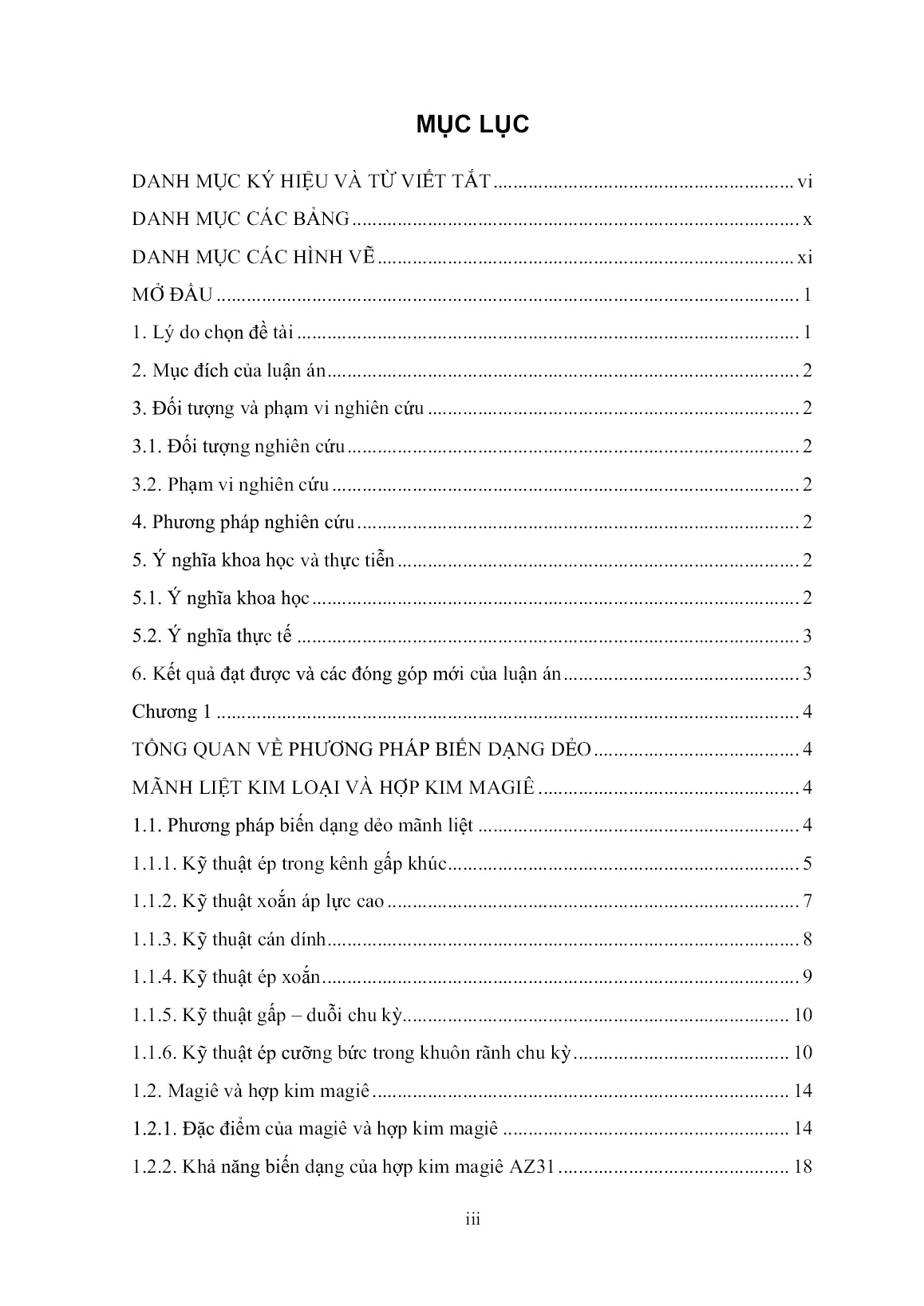
Trang 3
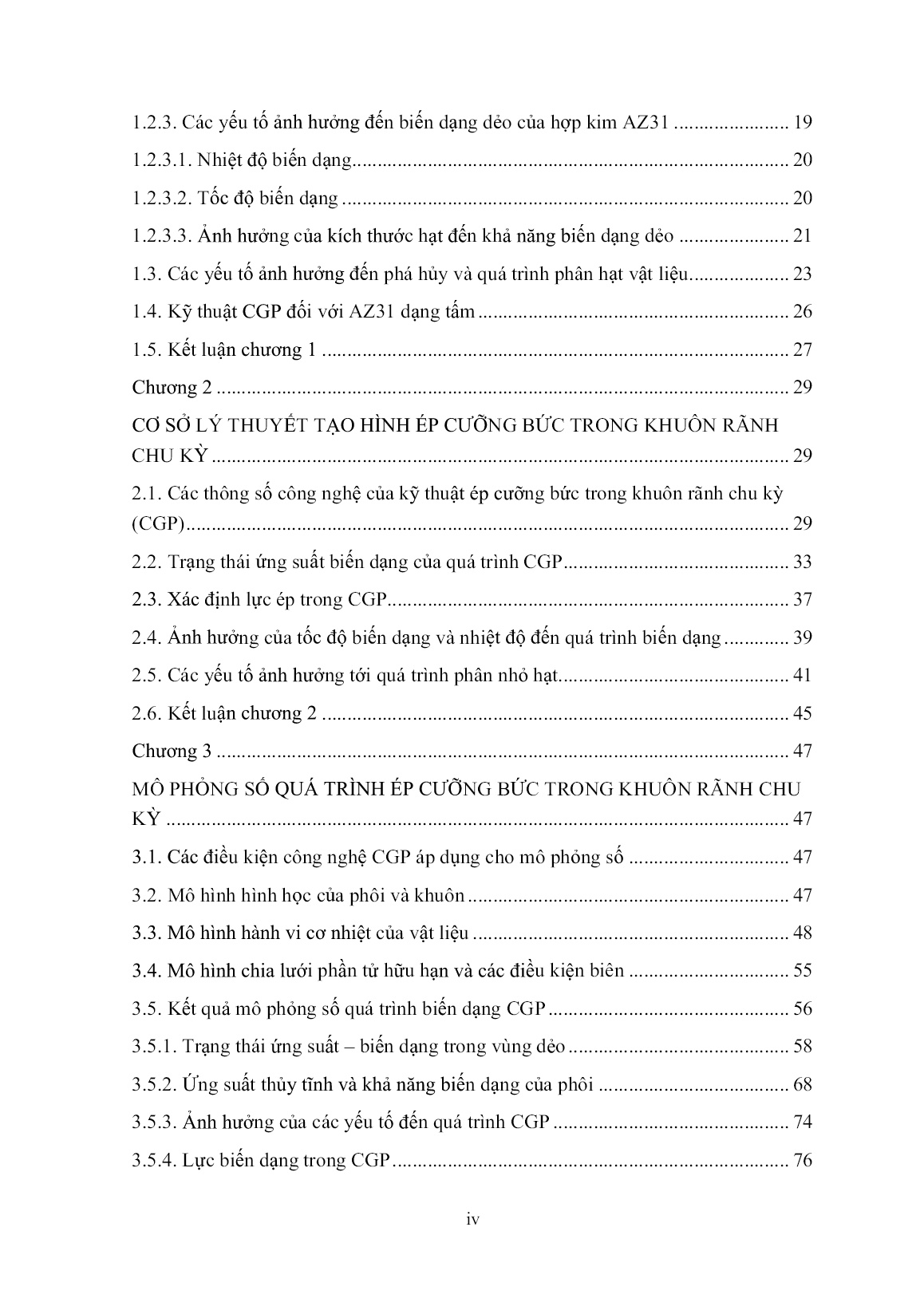
Trang 4
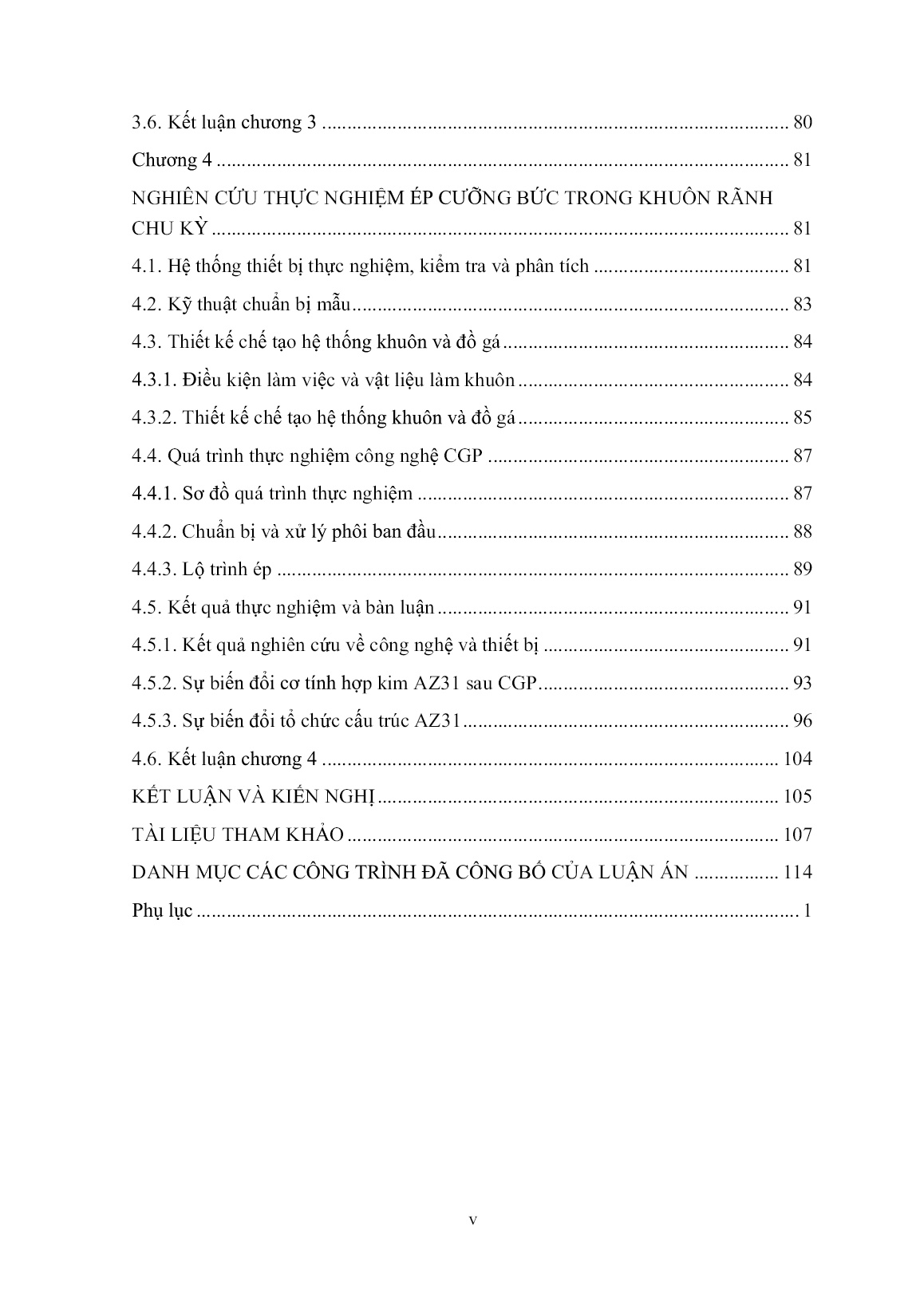
Trang 5
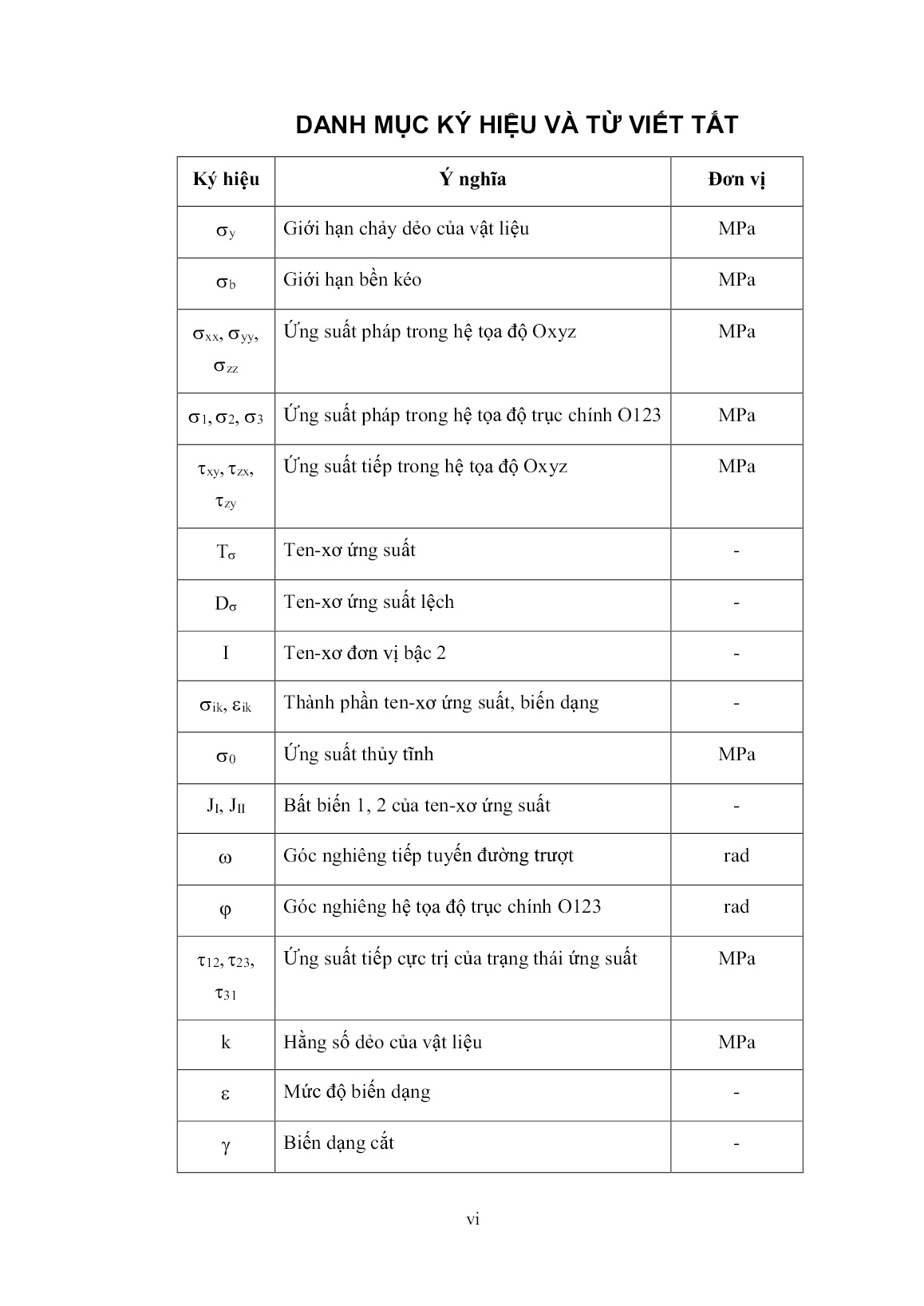
Trang 6
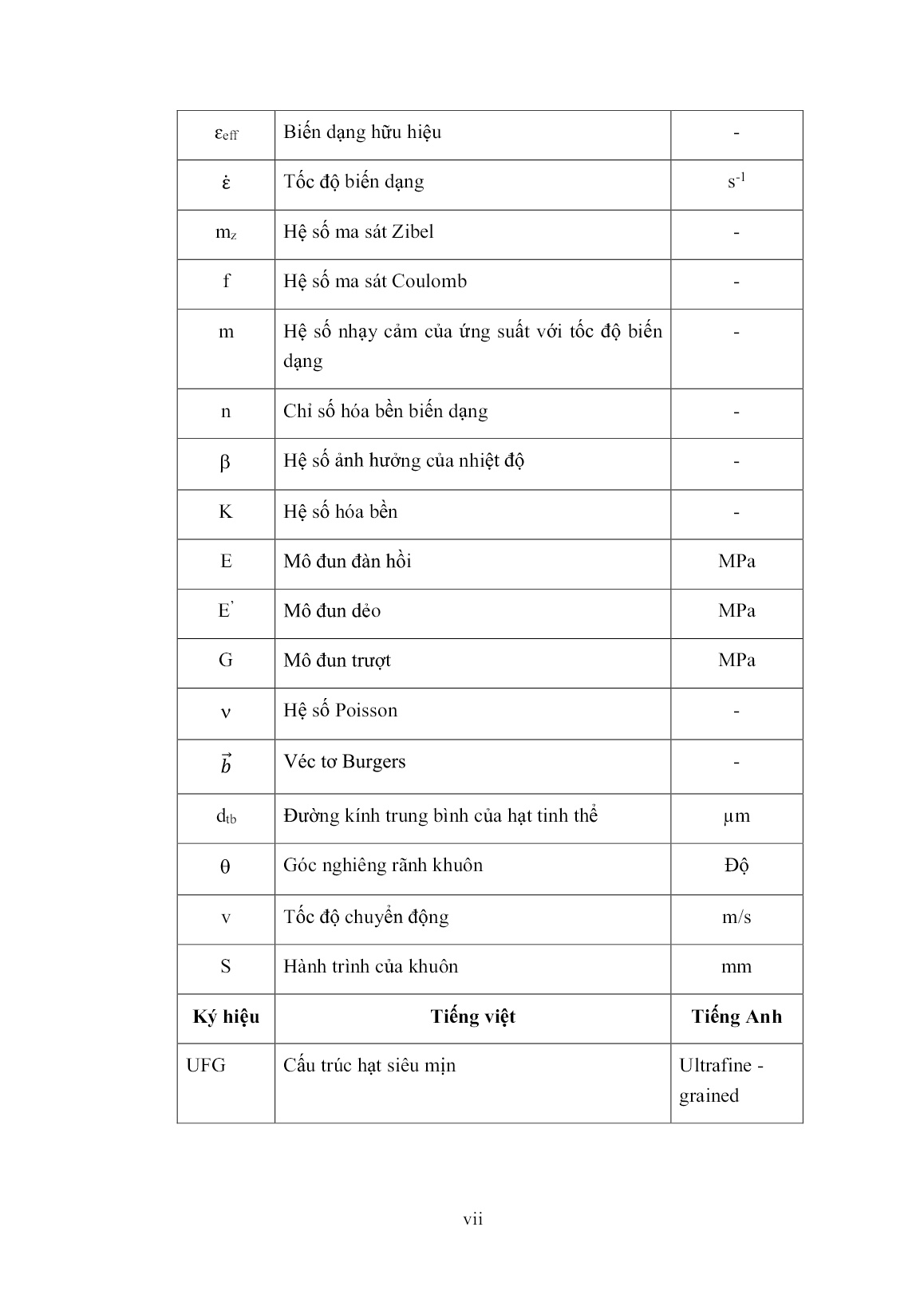
Trang 7
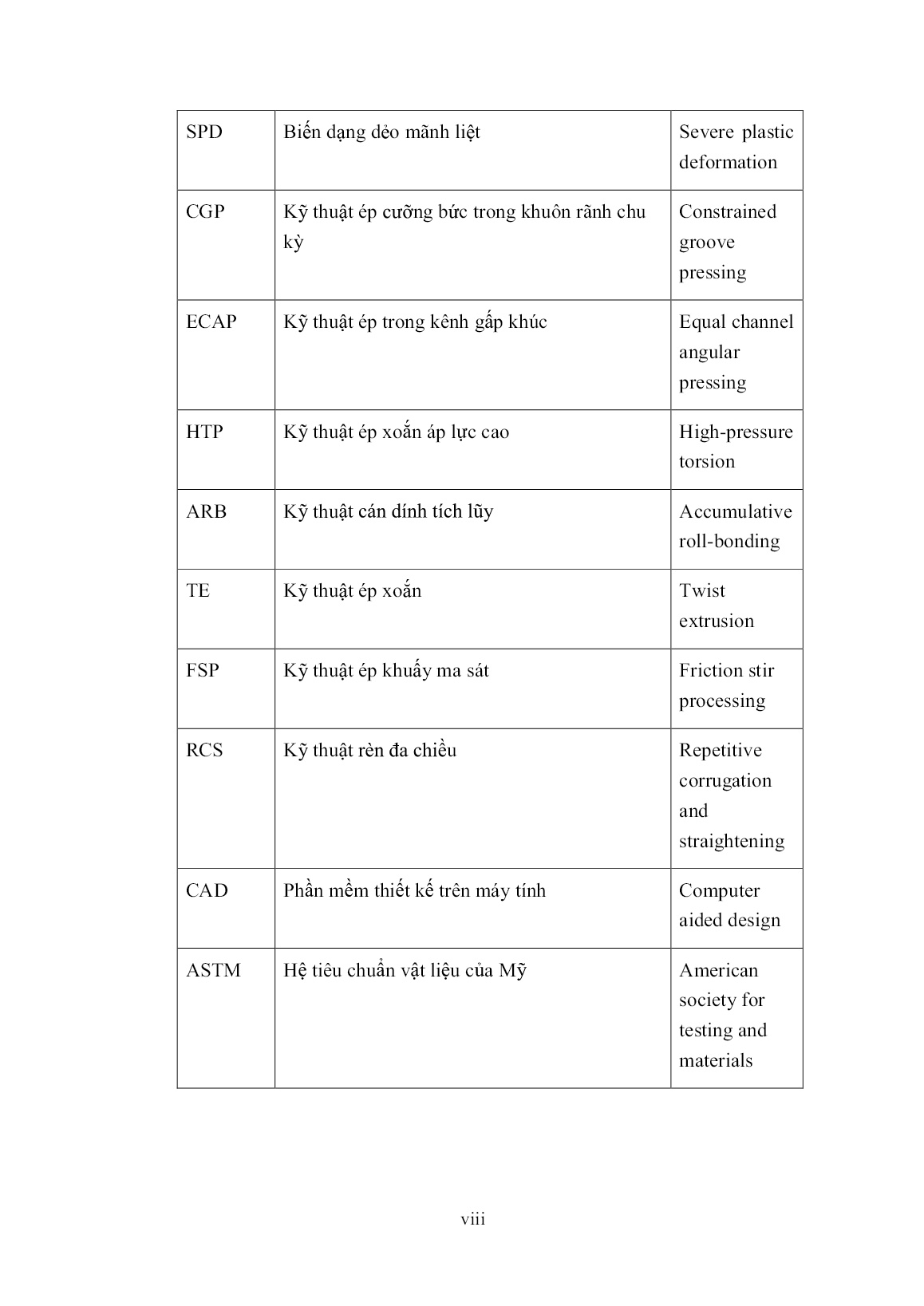
Trang 8
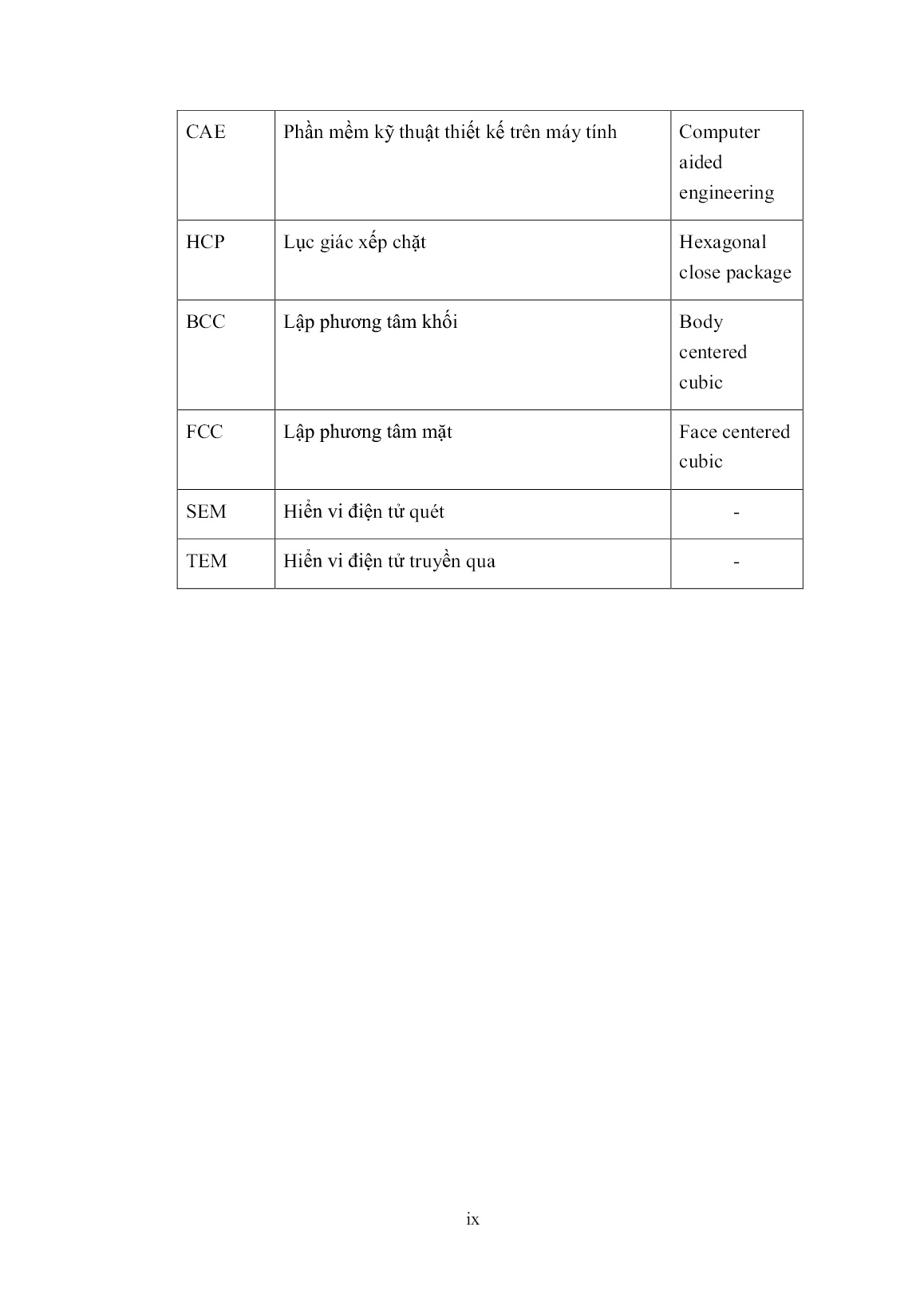
Trang 9
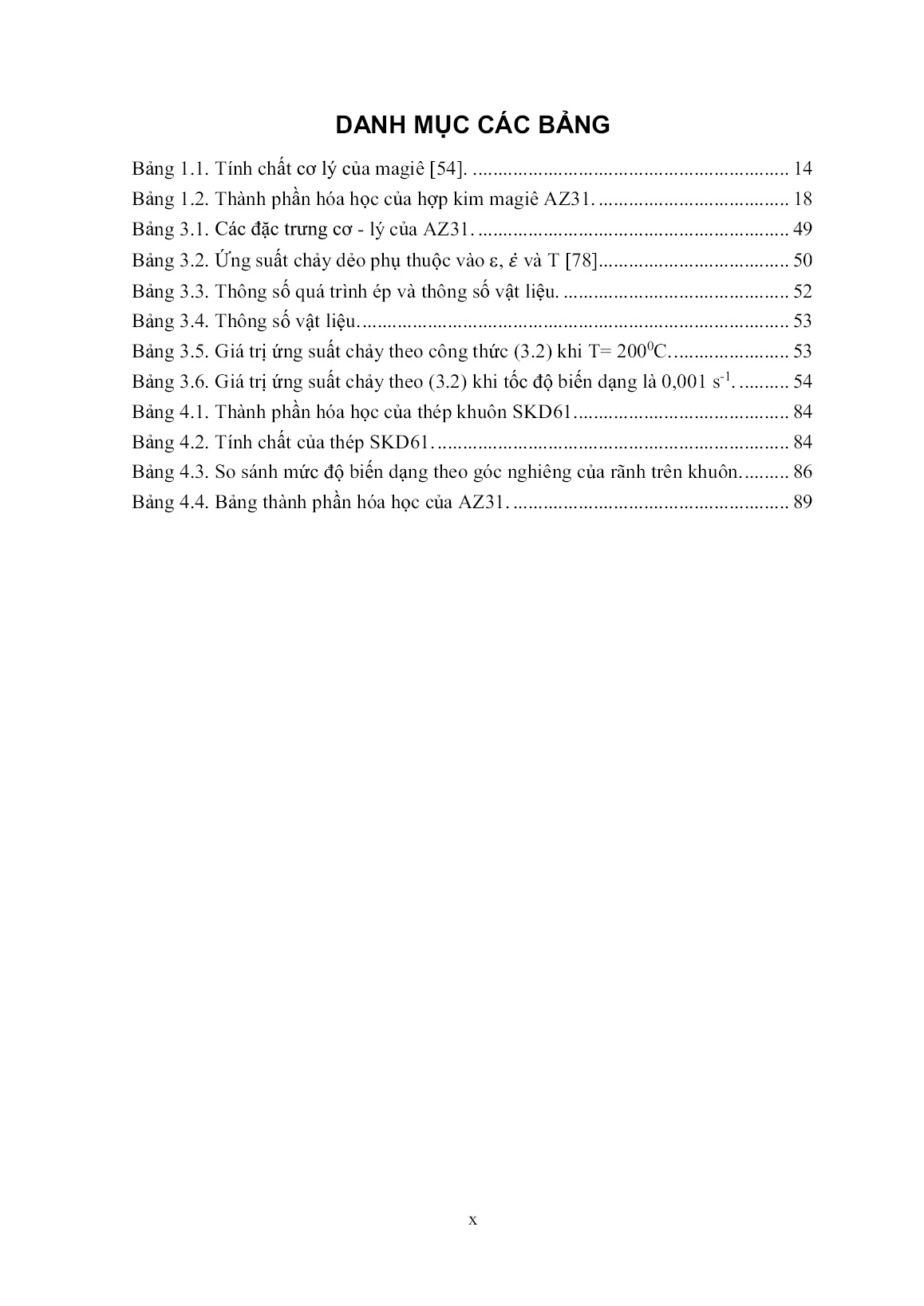
Trang 10
Tải về để xem bản đầy đủ
Bạn đang xem 10 trang mẫu của tài liệu "Luận án Nghiên cứu tạo cấu trúc siêu mịn cho vật liệu AZ31 bằng kỹ thuật ép cưỡng bức trong khuôn rãnh chu kỳ", để tải tài liệu gốc về máy hãy click vào nút Download ở trên.
Tóm tắt nội dung tài liệu: Luận án Nghiên cứu tạo cấu trúc siêu mịn cho vật liệu AZ31 bằng kỹ thuật ép cưỡng bức trong khuôn rãnh chu kỳ
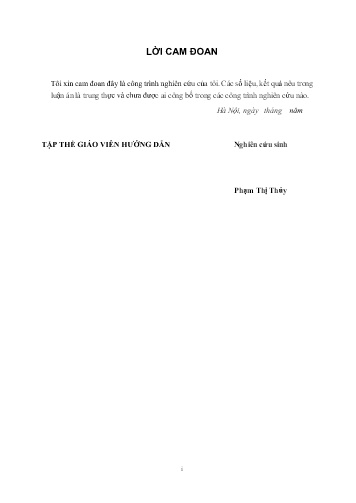
n hồi, dẻo và nhớt. Tính chất của vật liệu trên thực tế là sự kết hợp của 3 đặc tính đó. Ví dụ các vật liệu kỹ thuật có các đặc tính đàn hồi – nhớt, đàn hồi dẻo lý tưởng, đàn hồi dẻo hóa bền, Nếu đàn hồi lý tưởng và dẻo lý tưởng có tính tức thời thì tính nhớt của vật liệu thể hiện sự phụ thuộc của biến dạng vào thời gian khi có ứng suất tác dụng. Bản chất của nó được giải thích bằng quá trình khuếch tán trong thời gian có lực tác dụng. Thông thường ứng suất chảy của vật liệu phụ thuộc vào rất nhiều yếu tố trong đó có tổ chức cấu trúc, nhiệt độ T, mức độ biến dạng , tốc độ biến dạng ε̇. Trong quá trình biến dạng, sự phụ thuộc của các yếu tố trên được biểu thị bằng phương trình vi phân (2.19) [69]. dσ = ∂σ ∂T dT + ∂σ ∂ε dε + ∂σ ∂ε̇ dε̇ (2.19) 3.0 4.0 5.0 6.0 0.00 10.00 20.00 30.00 40.00 10 20 30 40 50 C h iề u d ày p h ô i, m m Lự c ép P , T ấn Góc nghiêng rãnh, độ 0.00-10.00 10.00-20.00 20.00-30.00 30.00-40.00 40 Với n gọi là lũy thừa hóa bền biến dạng và m là hệ số nhạy cảm của ứng suất chảy với tốc độ biến dạng, chúng được xác định từ thực nghiệm (giá trị 0 m, n 1), phụ thuộc vào tổ chức cấu trúc, các điều kiện cơ nhiệt và lịch sử của quá trình biến dạng, chúng được sử dụng trong các công thức xác định ứng suất chảy của vật liệu. Tác giả E. Xart đã sử dụng công thức (2.20) [55]. ∂σ/σ ∂ε/ε = n; ∂σ/σ ∂ε̇/ε̇ = m (2.20) Mô hình vật liệu trong trường hợp chung được xây dựng với nhiều công thức thực nghiệm khác nhau, với nhiều hằng số đặc trưng cho biến đổi tính chất vật liệu. Luận án áp dụng công thức (2.21) của V. A. Tretiacov như sau [24, 70]: 𝜎 = Kεnε̇meβ/T (2.21) Trong công nghệ tạo hình đẳng nhiệt, ứng suất chảy được tính thông qua n và m như công thức (2.22). 𝜎 = Kεnε̇m (2.22) Nếu n = 0 - đặc trưng của quá trình dẻo nhớt lý tưởng ta có: 𝜎 = Kε̇m (2.23) Khi đó, độ nhạy cảm của ứng suất với tốc độ biến dạng m được xác định như công thức (2.24) [71]. m = ∂lnσ ∂lnℰ̇ (2.24) Ảnh hưởng của tốc độ biến dạng đến ứng suất chảy dẻo được thể hiện qua rất nhiều mô hình khác nhau. Nếu tốc độ biến dạng rất thấp, có thể không cần xét đến ảnh hưởng của tốc độ biến dạng, khi đó m = 0. Mô hình chảy dẻo của vật liệu cho thấy, ứng suất chảy dẻo trong điều kiện cơ nhiệt nhất định là hàm của hệ số hóa bền K, lũy thừa hóa bền biến dạng n, hệ số nhạy cảm của ứng suất chảy với tốc độ biến dạng m và hệ số ảnh hưởng của nhiệt độ . Các hằng số này có tập hợp các giá trị riêng, đặc trưng cho từng loại kim loại và hợp kim. Hệ số K phản ánh ảnh hưởng của tổ chức cấu trúc, nếu vật liệu có độ bền cao thì K sẽ có giá trị lớn và ngược lại vật liệu dẻo hơn thì K có giá trị nhỏ. Lũy thừa hóa 41 bền biến dạng n càng lớn thì độ gia tăng của ứng suất chảy xảy ra càng mạnh khi mức độ biến dạng tăng. Tương tự như vậy, với hệ số nhạy cảm của ứng suất chảy với tốc độ biến dạng, ứng suất tăng khi tốc độ biến dạng tăng, tuy nhiên chúng sẽ tăng mạnh hơn khi m lớn. Việc lựa chọn nhiệt độ biến dạng phải phù hợp sao cho một mặt không làm trở lực biến dạng tăng, mặt khác không dẫn đến phát triển kích thước hạt bởi quá trình kết tinh lại xảy ra (trừ trường hợp kết tinh động làm kích thước hạt giảm). Quá trình SPD, làm mật độ xốp tăng mạnh do hư hại nên phải duy trì áp lực thủy tĩnh đủ cao. Vấn đề này được thể hiện rất hiệu quả trong kỹ thuật ép kênh gấp khúc (ECAP). Tuy nhiên, trong kỹ thuật CGP sẽ khó xảy ra, vì trong công nghệ này phôi có diện tích bề mặt tự do lớn. Với vật liệu cấu trúc mạng tinh thể kiểu HCP khó biến dạng nên cần phải có tác động của yếu tố nhiệt độ. Các nghiên cứu cho thấy [54], với titan (cấu trúc HCP) khi tăng nhiệt độ đến 3000C thì giới hạn chảy giảm đi 1/3 lần. Rưbin [72] đã chỉ rõ, ở nhiệt độ 2000C quá trình trượt đã xảy ra trên các hệ trượt phụ (hệ lăng trụ và hệ tháp). Như vậy, đối với các vật liệu khác có kiểu cấu trúc mạng HCP đều có thể áp dụng phương pháp SPD nếu lựa chọn được nhiệt độ phù hợp. Các yếu tố ảnh hưởng đến biến dạng ở trên, cần được xác định bằng thực nghiệm để xây dựng mô hình vật liệu ứng dụng trong phương pháp mô hình hóa và mô phỏng số bằng phần tử hữu hạn. Đã có nhiều tài liệu nghiên cứu về vấn đề này, đường cong ứng suất chảy dẻo đã công bố có thể được áp dụng cho các mục đích nghiên cứu khác. Nhờ yếu tố nhiệt độ thích hợp, quá trình phục hồi và quá trình kết tinh động một phần có thể kết hợp với quá trình SPD để làm giảm hiệu ứng hóa bền. Biến dạng ở nhiệt độ ấm còn ảnh hưởng rất nhiều đến các quá trình chuyển biến, hòa tan và tiết pha trong vật liệu. 2.5. Các yếu tố ảnh hưởng tới quá trình phân nhỏ hạt Quá trình phân nhỏ hạt phụ thuộc nhiều vào nhiệt độ, mức độ biến dạng và tốc độ biến dạng. Trong điều kiện nhiệt độ và tốc độ biến dạng không đổi, cụ thể khi biến dạng nguội người ta đã xây dựng các mô hình, trong đó đường kính trung bình của hạt là một hàm của biến dạng d = f () [56, 73], mô hình cũng cho thấy mật độ xốp là một hàm của mức độ biến dạng và áp lực thủy tĩnh. Quá trình biến dạng dẻo, mật độ lệch phát triển rất mạnh từ = 106 khi ủ đến = 1010 và cao hơn nữa, song song với nó là sự gia tăng của mật độ lỗ xốp. Kích thước các lỗ xốp có thể tăng hay giảm, sát nhập lại hoặc triệt tiêu hoàn toàn phụ thuộc vào ứng suất thủy tĩnh và ảnh hưởng trực tiếp đến tính dẻo của vật liệu. Nếu ứng suất thủy tĩnh nhỏ hoặc dương thì tính dẻo 42 kém, nghĩa là mật độ, kích thước lỗ xốp tăng, dẫn đến phá hủy. Khi ứng suất thủy tĩnh âm, có giá trị tuyệt đối lớn thì tính dẻo cao, tức là mức độ biến dạng phá hủy (f) tăng. Thông số chính dùng để đánh giá quá trình phân nhỏ hạt là mức độ biến dạng. Trong các điều kiện nhiệt độ và tốc độ nhất định, ta có thể xác định sự thay đổi đường kính hạt phụ thuộc vào mức độ biến dạng. Tuy nhiên, sự phụ thuộc thông qua biến trung gian chủ yếu là mật độ lệch. Mật độ lệch ( ) phụ thuộc vào hằng số hóa bền (h), hằng số phục hồi (r), mức độ biến dạng (), tốc độ biến dạng (ε̇) và nhiệt độ được thể hiện như công thức sau theo mô hình Laasraoni – Jonas dρ = (h − rρ)dε − ρ. dε h = h0 ( ε̇ ε0 ) m1 exp ( m1Q RT ) ; r = r0 ( ε̇ ε0 ) −m1 exp ( −m1Q RT ) trong đó h0, r0, m1, là các hằng số thực nghiệm; Q là hoạt năng; R là hằng số khí; T là nhiệt độ. Như đã biết, biến dạng nguội được sử dụng với mục đích hóa bền, do hiệu ứng giảm kích thước hạt, tăng tổng biên hạt và tăng mật độ lệch. Nếu điều kiện biến dạng xảy ra dưới nhiệt độ kết tinh lại thì các quá trình hóa bền có thể không thuận nghịch (vì có thể xảy ra quá trình hồi phục). Khi kích thước hạt giảm và đạt một giới hạn nào đó, tính năng sử dụng của vật liệu như độ bền, độ dai va đập và độ bền mỏi đều tăng vượt trội, trong khi tính công nghệ của vật liệu vẫn đảm bảo. Mối liên hệ giữa ứng suất trượt τ với đường kính hạt d được thể hiện trong công thức Hall – Petch có dạng: 𝜏 = 𝜏0 + 𝐾𝑑 −𝑛 (2.25) trong đó: τ0 là ứng suất ma sát trượt ban đầu; K – hệ số hóa bền vật liệu; n – chỉ số hóa bền. Quá trình làm nhỏ hạt nhờ biến dạng dẻo theo cơ chế song tinh và cơ chế trượt, trên cơ sở chuyển động của lệch mạng và trong điều kiện nhất định có trượt của biên hạt. Các đường biên hạt trong biến dạng song tinh sẽ rất mảnh và thẳng. 43 Hình 2.10. Mô hình phân chia hạt do chuyển động của lệch [74]. Với cơ chế trượt, phụ thuộc vào mức độ biến dạng, trình tự phân hạt sẽ là: 1) tăng mật độ lệch; 2) lệch tích tụ và sắp xếp lại hình thành các vách lệch (hình 2.10); 3) với hiệu ứng tương tác của tập hợp lệch tập trung trên biên giới siêu hạt làm xuất hiện hiện tượng “lệch chêm” (disclination) không hoàn chỉnh và hoàn chỉnh làm lệch hướng tinh thể liền kề, tạo dần lên biên hạt góc xoay khi ứng suất tác động lớn và nhiệt độ cao [75, 76]. Mỗi hạt gồm nhiều siêu hạt có biên giới hạt góc nhỏ và khi chúng thay đổi định hướng như xoay thành biên hạt góc lớn có mức độ khác nhau tùy thuộc vào trạng thái ứng suất, biến dạng tại từng vị trí, thời điểm. Ở giai đoạn biến dạng đầu, hóa bền phụ thuộc vào mật độ lệch và tổng đường biên hạt tăng. Khi đường kính hạt nhỏ tới một giá trị nhất định thì mật độ lệch lại giảm, tính dẻo khi đó được giải thích bằng cơ chế biến dạng xoay hạt. Hình 2.11. Mô hình giải thích lệch chêm do hiệu ứng tác dụng của tập hợp lệch. Để đạt được cấp hạt nhỏ mịn, phải duy trì mức độ biến dạng trượt rất lớn cùng với ứng suất thủy tĩnh phải cao nhưng điều này ảnh hưởng rất nhiều đến việc thiết kế thiết bị và lựa chọn các thông số công nghệ. Quá trình phân chia hạt chủ yếu do chuyển động của lệch chêm. Lệch chêm cũng là một dạng khuyết tật của mạng tinh thể đã được đề cập đến nhiều. Như mô tả trên hình 2.11, mặt ABCD là một phần biên hạt gián đoạn chưa hoàn chỉnh, xuất hiện bởi tác dụng của tập hợp vô số lệch. Cũng như lệch thông thường, đây là một dạng 44 khuyết tật đường. Đường AB có trường ứng suất đàn hồi rất phức tạp gọi là đường lệch chêm 𝜉 . Nghiên cứu các đường biên gián đoạn, đã chỉ ra rằng sự thay đổi hướng tinh thể xung quanh lệch chêm khác không, tức là tạo nên một góc xoay rất nhỏ Ω⃗⃗ . Tùy theo trường ứng suất tác dụng hoặc ứng suất dư cấp III, góc xoay có thể quanh trục Ox, Oy hoặc Oz là Ω⃗⃗ x, Ω⃗⃗ y và Ω⃗⃗ z. Gọi N⃗⃗ là véc tơ đơn vị của mặt ABCD, ta có 3 trường hợp lệch chêm như sau: 1) góc xoay quanh trục Ox thì ξ ⃗ Ω⃗⃗ & N⃗⃗ Ω⃗⃗ ; 2) góc xoay quanh trục Oy thì ξ ⃗ ∥ Ω⃗⃗ & N⃗⃗ Ω⃗⃗ ; 3) góc xoay quanh trục Oz thì ξ ⃗ Ω⃗⃗ & N⃗⃗ ∥ Ω⃗⃗ . Ứng suất giữa các phần của vật liệu là ứng suất cấp I; ứng suất giữa các hạt của vật liệu là ứng suất cấp II và ứng suất trong phạm vi một hạt của tinh thể là ứng suất cấp III. Dưới tác dụng của các mô men theo bất kỳ hướng trục nào thì hướng chuyển động của lệch chêm sẽ vuông góc với chính nó. Độ bền và tính dẻo của kim loại và hợp kim là tính chất cơ học của vật liệu rất nhạy cảm với tính chất của các tinh thể và sự liên kết của chúng trong tổ chức cấu trúc, trong các điều kiện khác như nhau thì hoàn toàn được xác định bởi số lượng, chủng loại và sự bố trí trong không gian của các loại khuyết tật trong mạng tinh thể. Tính chất của mạng tinh thể lý tưởng (tính đối xứng, các thông số ô cơ sở, qui luật tương tác các phân tử, ) chỉ quyết định đến giá trị tới hạn hoặc thể hiện như những hằng số liên quan đến đặc tính tổ chức cấu trúc lẫn khuyết tật của vật liệu. Độ bền trượt của tinh thể ở các nhiệt độ khác nhau phụ thuộc vào chuyển động của lệch, chính vì vậy quá trình biến dạng và phân chia hạt gắn liền với sự phân tích mật độ lệch. Phụ thuộc vào mức độ biến dạng, tiến trình biến đổi kích thước hạt cũng phụ thuộc vào tiến trình chuyển động của lệch, thay đổi mật độ và ở giai đoạn SPD chịu ảnh hưởng của hiệu ứng tác động tập hợp lệch. Biến dạng của tinh thể kiểu mạng HCP có đặc thù riêng, tuy nhiên cũng tuân theo những qui luật chung như sau: 1/ Khi biến dạng còn nhỏ sự gia tăng mật độ lệch và phân bố của chúng từ 106/cm2 ở trạng thái ủ ban đầu đến 108/cm2. 2/ Giai đoạn biến dạng tiếp theo, mật độ lệch tăng mạnh 108/cm2 ÷ 1010/cm2. Xuất hiện các khu vực lệch tập trung, tích tụ. 3/ Khi mức độ biến dạng tăng hơn, mật độ lệch tăng đến 1011/cm2 ÷ 1012/cm2. Đặc điểm của giai đoạn này là lệch tập trung, làm xuất hiện độ lệch hướng các tinh thể siêu hạt liền kề nên hình thành biên siêu hạt. Đối với tinh thể kiểu lục giác xếp chặt ít phát hiện ra độ lệch hướng của các siêu hạt tinh thể liền kề như các loại tinh thể kiểu BCC và FCC. Điều này được giải thích do HCP có số hệ trượt nhỏ. Tuy nhiên, có thể phân tích và quan sát sự tồn tại của vô số các đường được tạo nên bởi cơ chế biến dạng song tinh theo các hệ trượt 45 {101̅2}〈1̅011〉. Quá trình này xuất hiện bởi tác động của trường lực đàn hồi ngay từ khi mức độ biến dạng dẻo nhỏ. Khi biến dạng mãnh liệt đạt đến mức độ cao, do hiệu ứng tác động của tập hợp lệch, các khuyết tật đường dạng lệch chêm xuất hiện. Tại thời điểm này, xuất hiện hai khả năng. Khả năng thứ nhất, lệch chêm chuyển động qua hạt thì hạt được phân đôi với các hướng tinh thể hai hạt liền kề có độ sai lệch bởi góc xoay ∆�⃗� . Nếu trong trường hợp do ảnh hưởng của yếu tố nào đó mà xảy ra quá trình nới (ứng suất giảm) nghĩa là xuất hiện các lỗ xốp trên trục lệch chêm [77]. Để duy trì quá trình phân hạt và hạn chế phát triển lỗ xốp thì áp lực thủy tĩnh phải đủ cao. Hình 2.12. So sánh khuyết tật đường (a) & chuyển động: của lệch (b, c, d) & lệch chêm (e, f, g). Lệch chêm cũng là một dạng khuyết tật đường mà chuyển động của chúng dẫn đến phân chia hạt với độ sai lệch hướng tinh thể liền kề. Đây là sự khác biệt so với sự chuyển động của lệch như thể hiện trên hình 2.12. 2.6. Kết luận chương 2 Quá trình SPD trong CGP được phân tích trong điều kiện lý tưởng (không có ma sát và vật liệu dẻo lý tưởng) và điều kiện thực tế (ma sát, hóa bền), nghiên cứu 46 ảnh hưởng của các thông số khác nhau đã làm rõ bản chất quá trình gồm các giai đoạn biến dạng uốn, biến dạng kéo và biến dạng ép, nhưng phần lớn chủ yếu là quá trình biến dạng trượt, với lượng biến dạng sau mỗi chu kỳ đạt eff = 116%. Phôi tấm dễ hồi phục lại hình dạng và kích thước ban đầu để thực hiện các bước biến dạng tiếp theo. Tiết diện mặt phôi lớn nên lực ma sát giữa phôi và khuôn đủ lớn làm tăng ứng suất thủy tĩnh, duy trì quá trình biến dạng dẻo không phá hủy. Quá trình biến dạng theo sơ đồ uốn, kéo và nén nên thuận lợi cho cơ chế biến dạng khác nhau. Tuy nhiên, quá trình biến dạng hợp kim AZ31 cần được thực hiện ở các nhiệt độ khác nhau vì hai lý do: 1) cấu trúc lục giác xếp chặt ít hệ trượt, khó biến dạng nên cần có nhiệt độ tăng cường các hệ trượt phụ (loại lăng trụ và loại hình tháp) tham gia quá trình biến dạng; 2) hòa tan các hạt tiết pha của hợp kim Mg vốn làm ngăn cản chuyển động của lệch. Cấu trúc kiểu lục giác xếp chặt (HCP) biến dạng khó hơn so với kiểu BCC và FCC nhưng hiệu ứng phân chia hạt cao hơn. Khi biến dạng ở chế độ nhiệt của hợp kim Mg, việc kết hợp với hiệu ứng kết tinh động một phần, phục hồi động và tiết pha trước, trong và sau quá trình SPD sẽ tạo nên tổ chức cấu trúc hạt đa tinh thể nhỏ mịn, chứa các hạt tiết pha phân bố đều sẽ làm tăng mạnh các tính chất cơ học vật liệu, cụ thể tăng độ cứng, giới hạn chảy, giới hạn bền và độ dẻo dai. 47 Chương 3 MÔ PHỎNG SỐ QUÁ TRÌNH ÉP CƯỠNG BỨC TRONG KHUÔN RÃNH CHU KỲ 3.1. Các điều kiện công nghệ CGP áp dụng cho mô phỏng số Mô phỏng số là phương pháp hữu hiệu được nghiên cứu để tối ưu hóa các quá trình công nghệ. Thay đổi kết quả mô phỏng bằng việc thay đổi các điều kiện biên, có thể lựa chọn các phương án thông số công nghệ tối ưu, giảm thiểu thời gian chỉnh sửa thiết kế sản phẩm, giảm chi phí chế tạo thử. Phương pháp mô phỏng số giải quyết được các bài toán phi tuyến mà phương pháp giải tích chưa thực hiện được. Độ chính xác của kết quả mô phỏng số cũng phụ thuộc vào nhiều yếu tố: độ chính xác của mô hình hành vi cơ nhiệt, độ chính xác của kết quả nhận dạng mô hình ứng xử của vật liệu, độ chính xác của thuật toán khi giải và độ chính xác của các điều kiện biên. Trạng thái ứng suất, biến dạng, phân bố nhiệt độ, tính dẻo của vật liệu là các thông số tác động trực tiếp đến sự thay đổi tổ chức cấu trúc tế vi của sản phẩm ép định hướng trên rãnh chu kỳ. Tất cả các yếu tố này có thể được phân tích trên cơ sở lực ép, trường ứng suất, trường biến dạng, trường tốc độ biến dạng và các nguy cơ mất ổn định chảy dẻo cũng như phá hủy nhận được từ mô phỏng số. Căn cứ vào nghiên cứu tổng quan, quá trình mô phỏng số được thực hiện trong các điều kiện nhiệt độ 2500C, 2000C và 1500C, tốc độ biến dạng trong phạm vi 0,1 ÷ 0,0001s-1 nhằm lựa chọn chế độ tối ưu cho các quá trình thực nghiệm. Mô phỏng được tiến hành với bốn chu kỳ ép. Ở giữa mỗi chu kỳ ép, phôi được xoay một góc z = 1800, sau cuối mỗi chu kỳ ép phôi xoay một góc z = 900. Để đánh giá sơ bộ các yếu tố ảnh hưởng, số lượng phần tử hữu hạn lấy ở mức trung bình cao. Với bộ các thông số được lựa chọn, quá trình mô phỏng được tiến hành với số lượng phân tử ở mức độ chính xác cao để phân tích trạng thái ứng suất – biến dạng. 3.2. Mô hình hình học của phôi và khuôn Phôi có kích thước (60 x 60 x 3) mm, hai bộ khuôn gồm bộ khuôn ép định hướng trên rãnh chu kỳ và bộ khuôn ép phẳng. Trên cơ sở kích thước chi tiết phôi ép, tính toán kích thước khuôn dập phẳng, khuôn ép rãnh và các bộ phận chi tiết bên trong khuôn ép để phục vụ cho mô phỏng số quá trình ép tạo hình và ép phẳng theo chu kỳ chi tiết phôi. 48 Sau khi hoàn thành lắp ghép khuôn trên và khuôn dưới với phôi, bộ khuôn được ghép xếp chồng với nhau như hình 3.1. Hình 3.1. Sơ đồ lắp ghép khuôn: (1) nửa khuôn trên; (2) phôi; (3) nửa khuôn dưới và (4) áo khuôn. Khuôn ép được giả thuyết là cứng tuyệt đối. Mô hình hình học của khuôn và phôi phục vụ cho mô phỏng số được xây dựng trên cơ sở các bản vẽ thiết kế khuôn phục vụ cho thực nghiệm kiểm chứng và chế tạo thử nghiệm vật liệu. 3.3. Mô hình hành vi cơ nhiệt của vật liệu Vật liệu phôi sử dụng trong mô phỏng số là vật liệu tiêu chuẩn được giả thiết liên tục, đồng nhất và đẳng hướng. Vật liệu chế tạo khuôn được chọn là SKD61 trong mô phỏng số được giả thiết cứng tuyệt đối. Trong quá trình mô phỏng, nhiệt độ được giả thiết là hằng số (ép đẳng nhiệt), để phù hợp với thực tế có gia nhiệt khuôn bằng nhiệt độ của phôi. Các đặc trưng cơ - lý của vật liệu AZ31 theo tiêu chuẩn Mỹ (ASTM) được trình bày trong bảng 3.1. 49 Bảng 3.1. Các đặc trưng cơ - lý của AZ31. Đặc tính Giá trị Khối lượng riêng 1,77 g/cm3 Độ bền kéo tới hạn 275 MPa Độ bền kéo chảy 190 MPa Mô đun đàn hồi 45 GPa Độ bền cắt tới hạn 495 MPa Hệ số Poisson 0,35 Độ bền cắt 190 MPa Nhiệt dung riêng 960 J/kg.K Độ dẫn nhiệt 26 K-1 Hệ số dẫn nhiệt 96 Wm-1K-1 Điểm chảy 565 ÷ 635oC Trong gia công tạo hình vật liệu, mức độ biến dạng là một trong những thông số quan trọng nhất, với mục đích nghiên cứu ảnh hưởng của biến dạng đến quá trình phân chia hạt nên luận án hạn chế tối đa các ảnh hưởng của những thông số khác như nhiệt độ và tốc độ biến dạng. Để giảm ảnh hưởng của tốc độ và nhiệt độ, quá trình ép có thể được thực hiện trên máy ép thủy lực với tốc độ rất chậm và trong điều kiện đẳng nhiệt. Thực tế tổng quan tài liệu cho thấy, nghiên cứu ảnh hưởng của cả ba yếu tố là rất phức tạp nên việc hạn chế ảnh hưởng của một vài thông số trong điều kiện là cần thiết. Trong điều kiện ép đẳng nhiệt (T = const). Để loại trừ ảnh hưởng của yếu tố nhiệt độ bằng cách lấy = 0 và các thông số K, m, n được xác định bằng thực nghiệm cũng ở nhiệt độ không đổi đó. Để đơn giản hóa mô hình lưu biến vật liệu và quá trình mô phỏng, đường cong ứng suất - biến dạng = Kεn được xác định trong từng điều kiện nhiệt độ T = 1500C; 50 2000C và 2500C và tốc độ biến dạng ε̇ = 0,0001; 0,001 và 0,01 s-1 thì các hệ số vật liệu = 0, m = 0. Hệ số K và n được xác định dựa vào đường cong thực nghiệm chảy dẻo khi thử kéo vật liệu AZ31 của Yong QiCheng [78] ở cùng các điều kiện phạm vi nhiệt độ và tốc độ biến dạng của luận án. Tài liệu đã công bố đầy đủ các số liệu và điều kiện thực nghiệm có thể thu thập và xử lý kết quả như bảng 3.2. Bảng 3.2. Ứng suất chảy dẻo phụ thuộc vào , �̇� và T [78]. TT , MPa �̇�, s-1 T, K TT , MPa �̇�, s-1 T, K 1 75 0,05 0,0001 523 26 150 0,05 0,01 473 2 78 0,1 0,0001 523 27 175 0,1 0,01 473 3 80 0,15 0,0001 523 28 180 0,15 0,01 473 4 81 0,2 0,0001 523 29 185 0,2 0,01 473 5 75 0,05 0,001 523 30 200 0,25 0,01 473 6 80 0,1 0,001 523 31 202 0,3 0,01 473 7 87 0,15 0,001 523 32 205 0,35 0,01 473 8 100 0,2 0,001 523 33 160 0,05 0,0001 423 9 103 0,25 0,001 523 34 175 0,1 0,0001 423 10 110 0,05 0,01 523 35 179 0,15 0,0001 423 11 125 0,1 0,01 523 36 180 0,2 0,0001 423 12 132 0,15 0,01 523 37 165 0,05 0,001 423 13 145 0,2 0,01 523 38 19
File đính kèm:
luan_an_nghien_cuu_tao_cau_truc_sieu_min_cho_vat_lieu_az31_b.pdf
bìa quyển.pdf
bìa tóm tắt .docx.pdf
Mẫu 2_trích yếu luận án.pdf
quyển tóm tắt.pdf