Luận án Nghiên cứu ảnh hưởng của một số thông số công nghệ cơ bản đến quá trình tạo hình chi tiết phức tạp bằng phương pháp ép chảy ngang
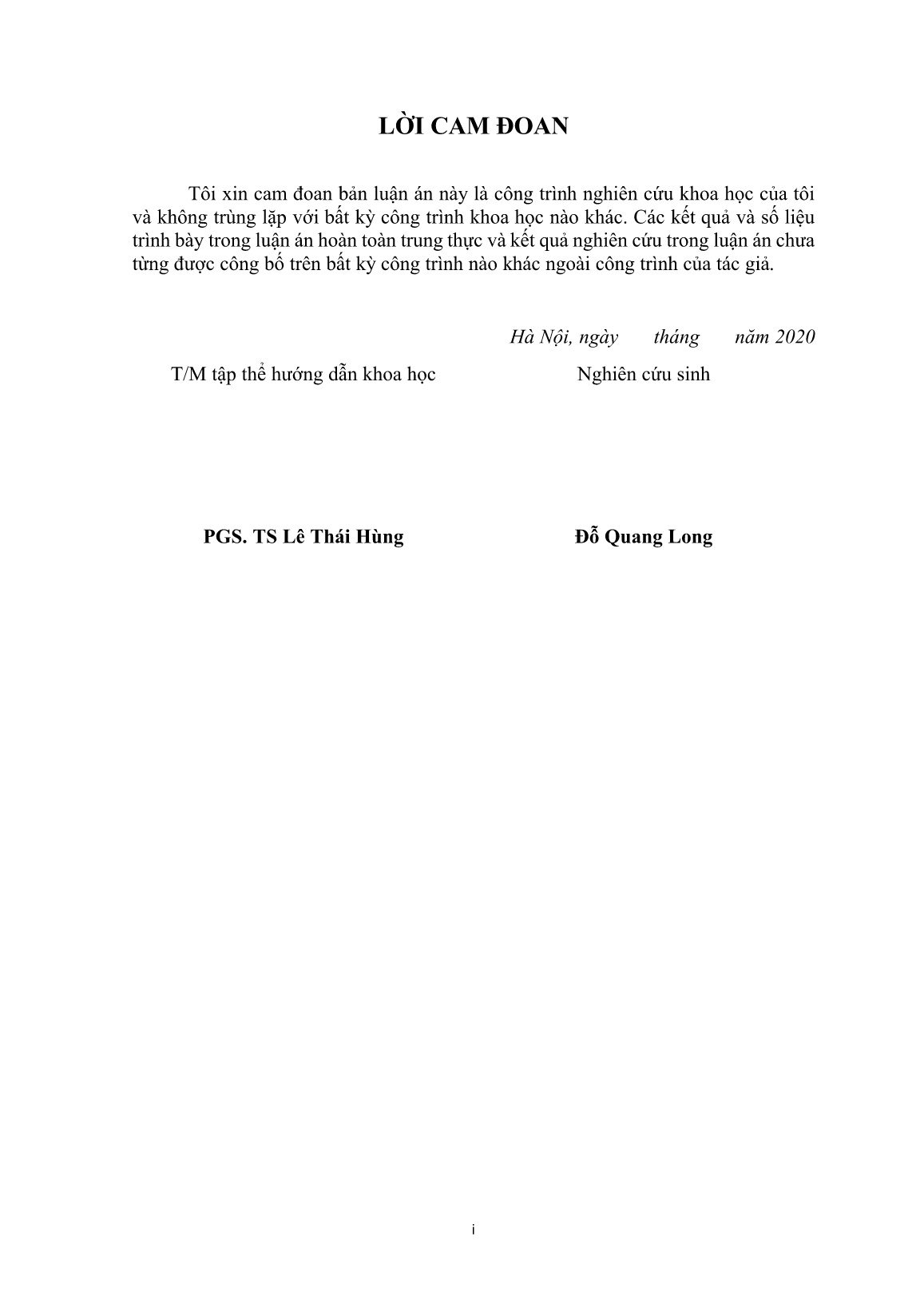
Trang 1
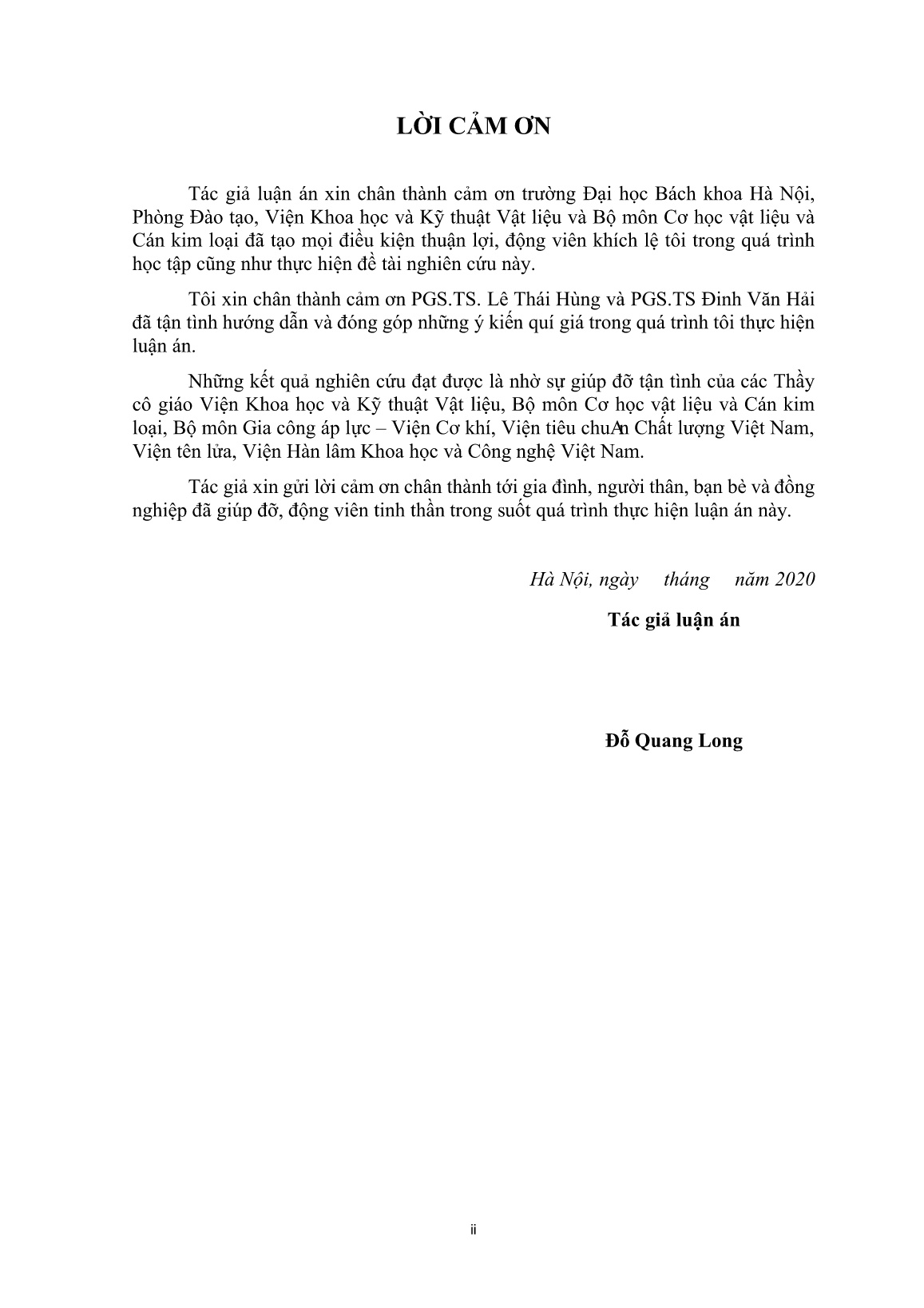
Trang 2
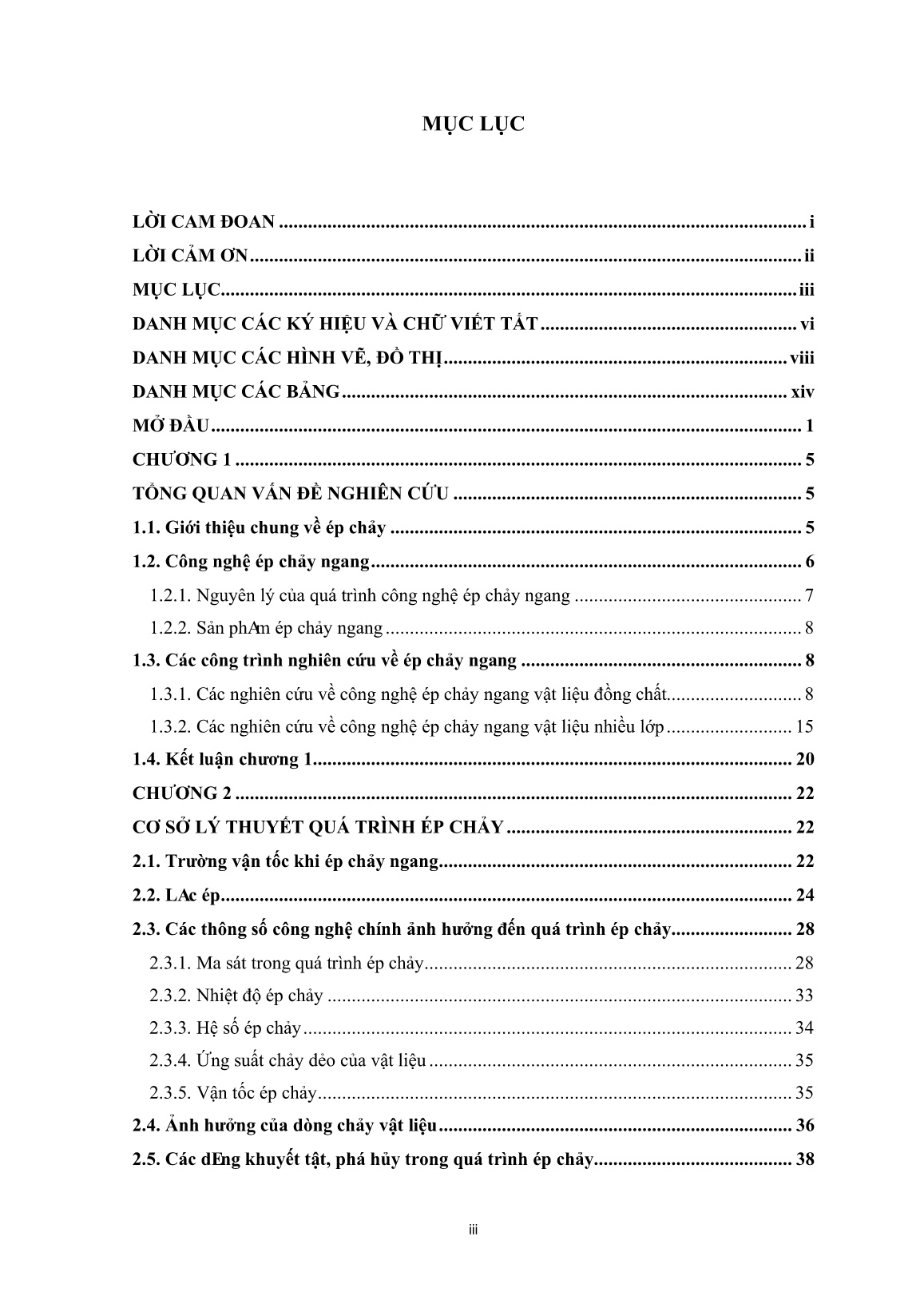
Trang 3

Trang 4
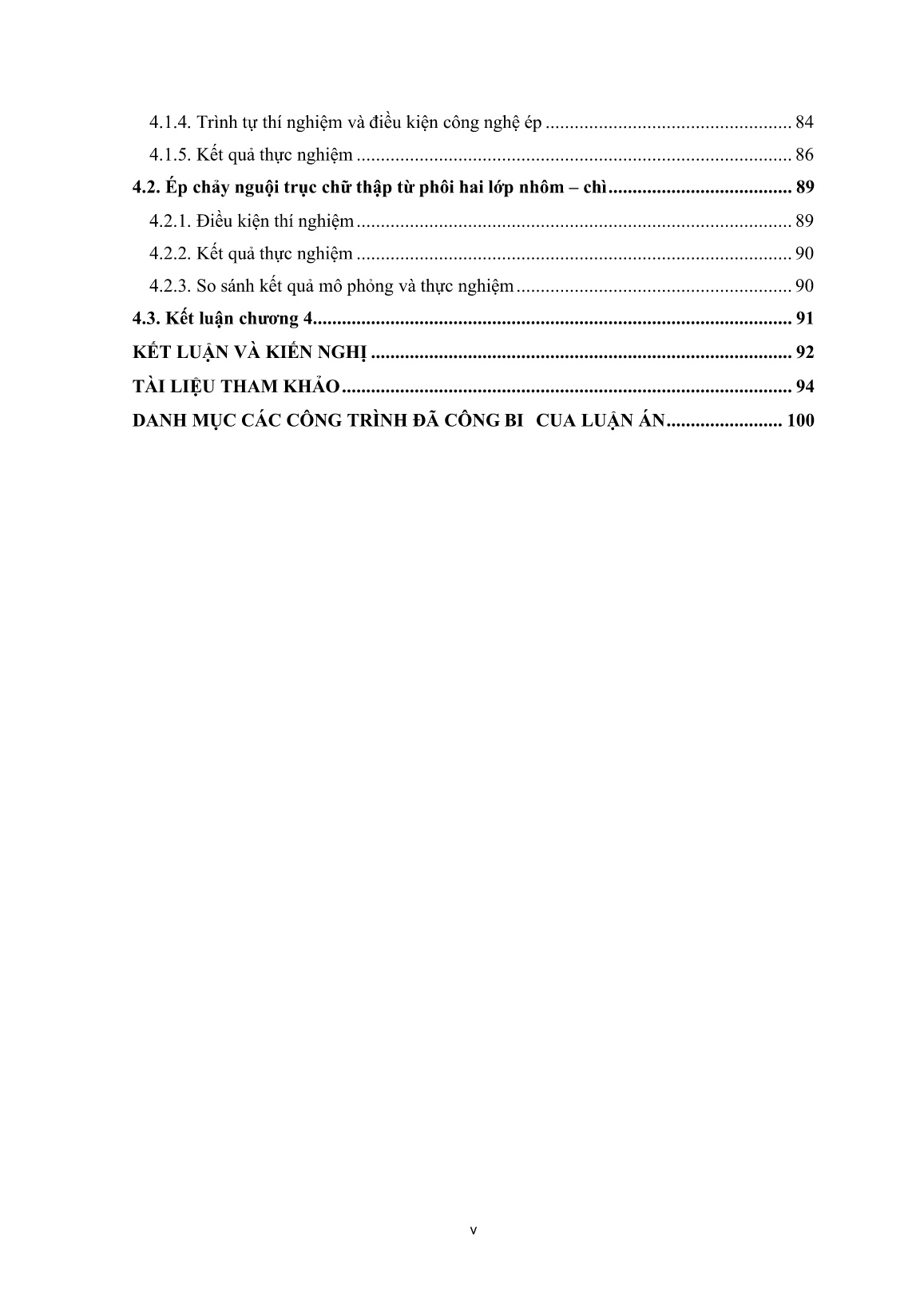
Trang 5
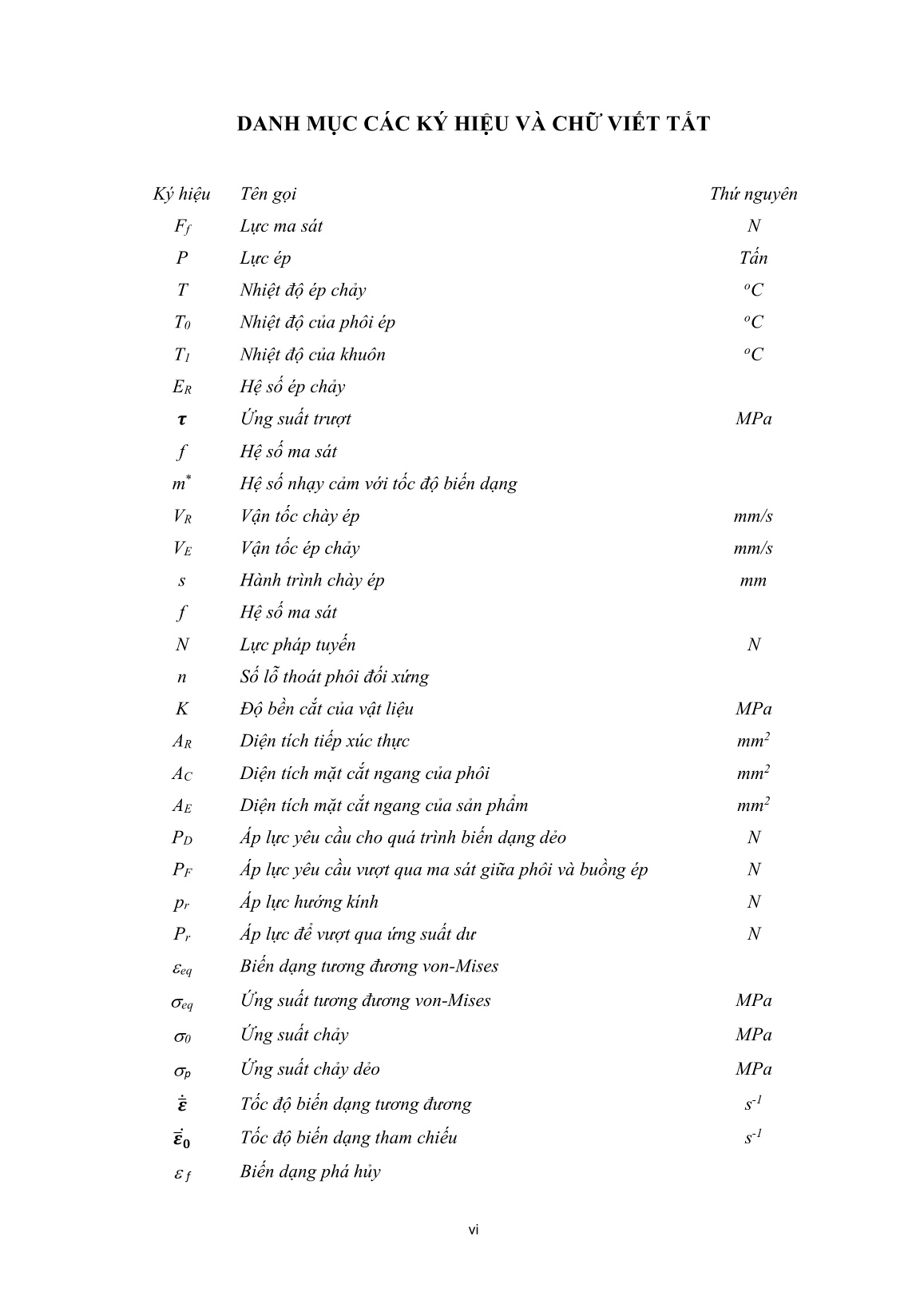
Trang 6
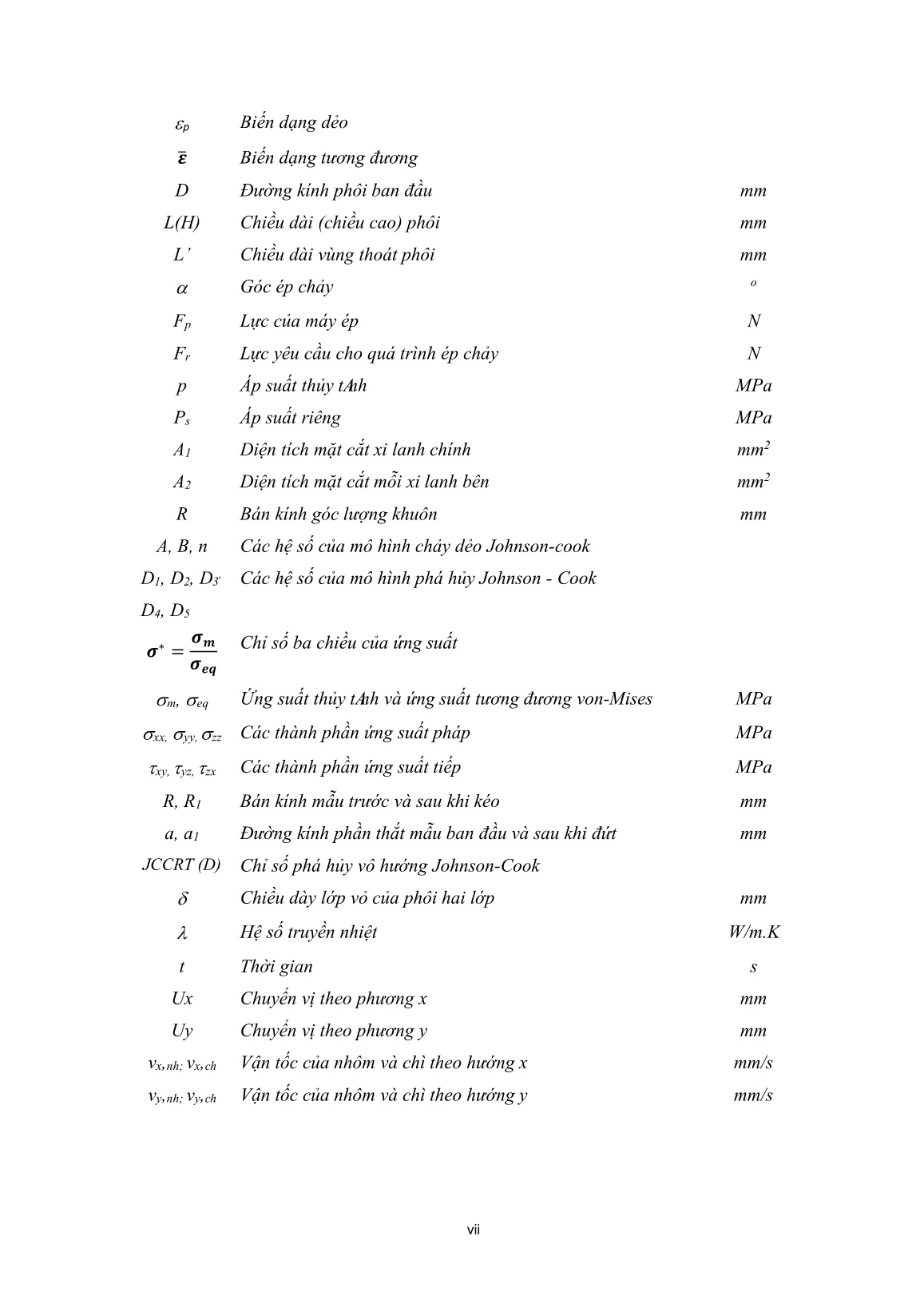
Trang 7
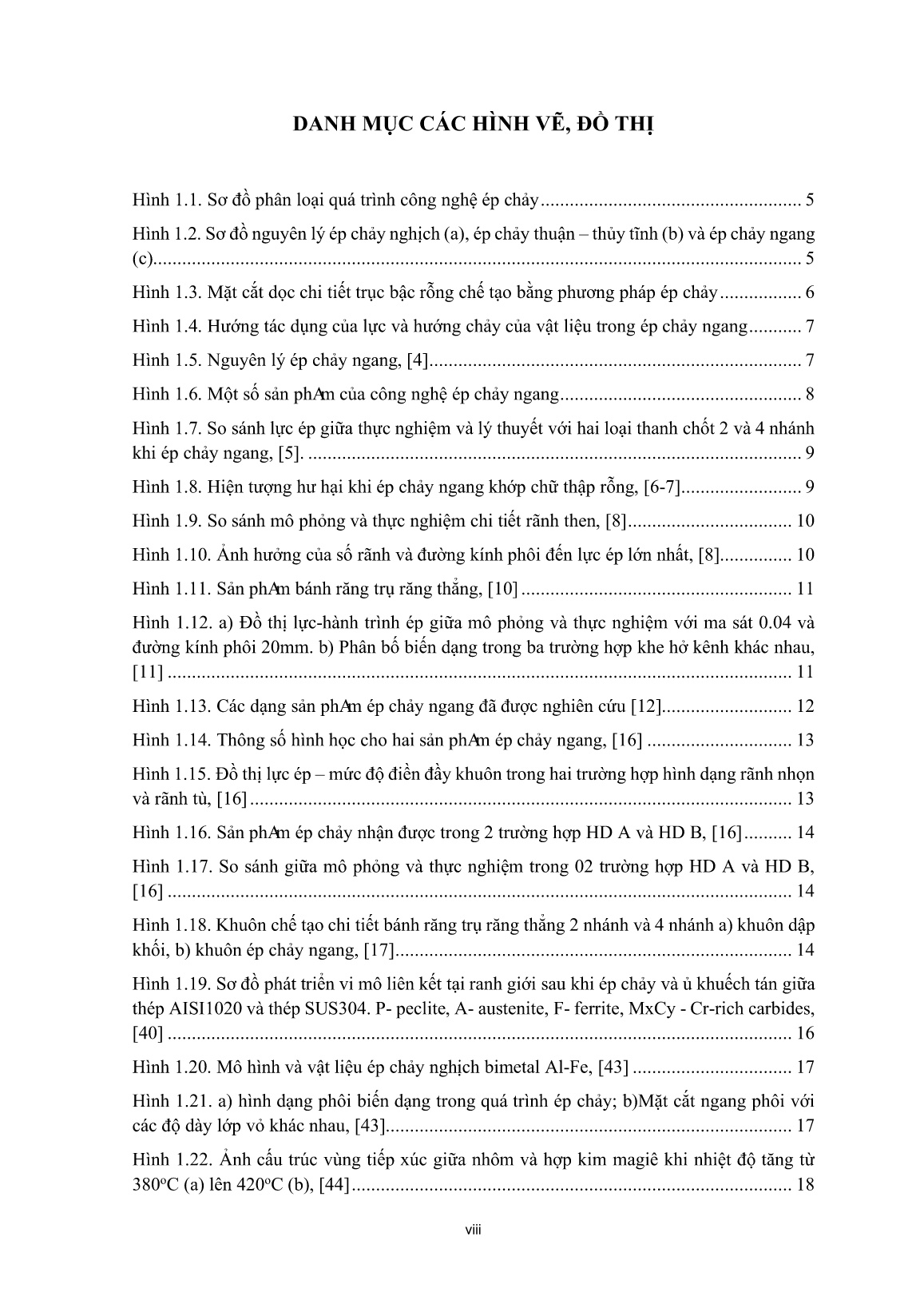
Trang 8
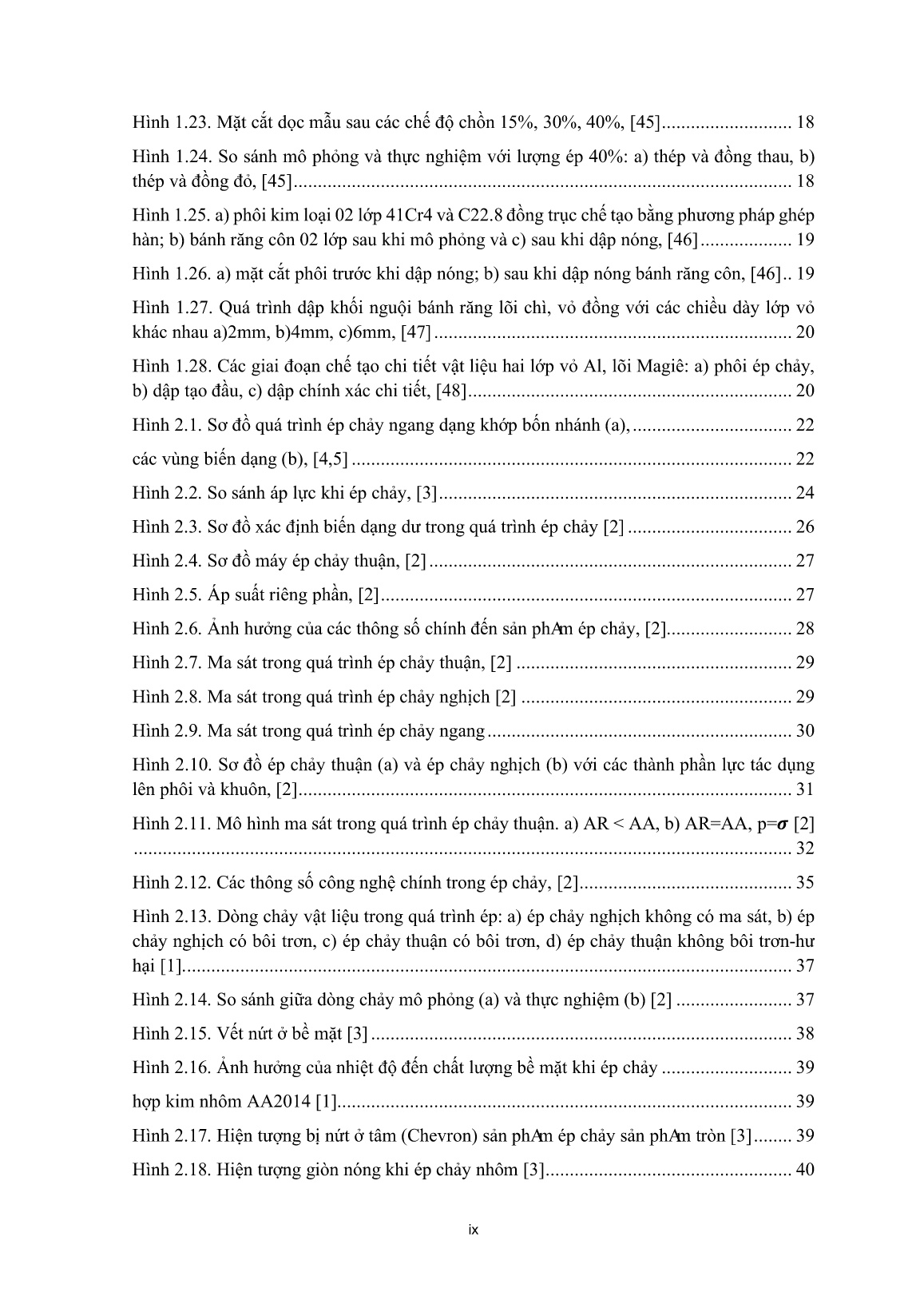
Trang 9
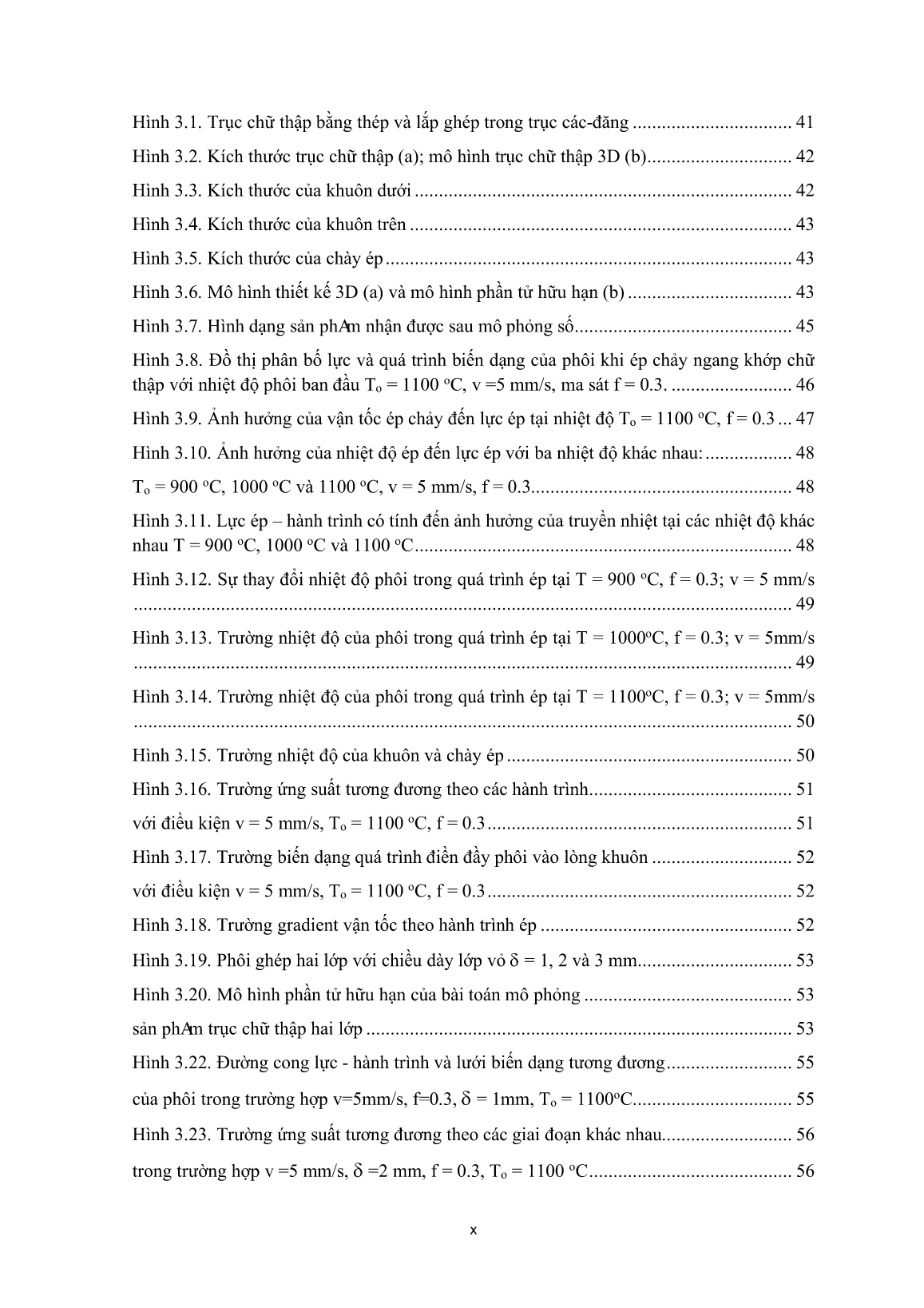
Trang 10
Tải về để xem bản đầy đủ
Bạn đang xem 10 trang mẫu của tài liệu "Luận án Nghiên cứu ảnh hưởng của một số thông số công nghệ cơ bản đến quá trình tạo hình chi tiết phức tạp bằng phương pháp ép chảy ngang", để tải tài liệu gốc về máy hãy click vào nút Download ở trên.
Tóm tắt nội dung tài liệu: Luận án Nghiên cứu ảnh hưởng của một số thông số công nghệ cơ bản đến quá trình tạo hình chi tiết phức tạp bằng phương pháp ép chảy ngang
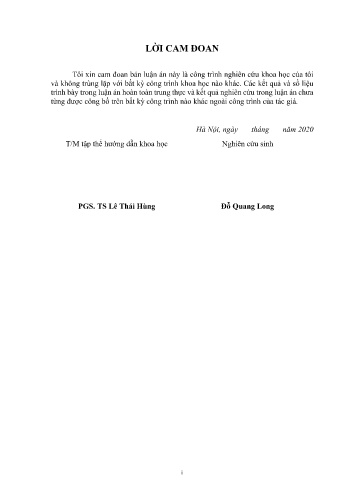
tăng với áp lực tiếp xúc như trên hình 2.11. Theo Bowden và Tabor [51], lực ma sát tỷ lệ thuận với diện tích bề mặt tiếp xúc thực. Trong trường hợp ép chảy thuận (áp suất tiếp xúc cao), diện tích tiếp xúc thực AR gần tương đương với diện tích tiếp xúc biểu kiến AA khi phôi bị chồn trong khuôn. Những xem xét quan trọng trong quá trình ép chảy thuận là lực ma sát gia tăng giữa phôi và buồng ép và tương tác ma sát giữa kim loại chảy và vùng tiếp xúc côn (vùng chết). Trong quá trình ép chảy thuận, áp lực lớn gia tăng đòi hỏi phôi phải được hỗ trợ bởi thành buồng ép. Từ quan điểm thực tế, có hai loại điều kiện ma sát: o Ma sát giữa buồng ép và phôi là ma sát dính; o Ma sát giữa hai bề mặt là ma sát trượt. Trong quá trình ép chảy, điều kiện ma sát tại bề mặt tương tác giữa phôi và buồng ép được xem xét như là ma sát dính khi lớp bề mặt phôi được tách ra từ thành buồng ép. Schey [52] đưa ra một giải pháp bằng việc sử dụng hệ số ma sát, f, trong các quá trình gia công áp lực mà ở đó áp lực tiếp xúc là rất cao. Mô hình ma sát này được xác định như sau: Ff = f kAR (2.21) 32 Trong đó: f- là hệ số ma sát; k- là độ bền cắt của vật liệu; AR- là diện tích tiếp xúc thực. Đối với mô hình này thì diện tích tiếp xúc thực tương đương tổng diện tích tiếp xúc. Ff – Lực ma sát Trong trường hợp ma sát dính thì f = 1, trong khi đối với các điều kiện bôi trơn lý tưởng thì f » 0. Do đó, ứng suất ma sát 𝜏\ cho bởi: 𝜏\ = 𝑘 = ]^√` (2.22) Trong đó: k là tương đương với 𝜎# √3⁄ theo điều kiện dẻo Von-Mises; 𝜎# là ứng suất tương đương của vật liệu. Hình 2.11. Mô hình ma sát trong quá trình ép chảy thuận. a) AR < AA, b) AR=AA, p=𝜎# [2] • Tương tác giữa dòng chảy kim loại và vùng chết: Vùng chết thể hiện trong hình 2.7. Ta thấy, vật liệu ở các góc khuôn không tham gia vào dòng chảy và bị dính chặt vào khuôn tạo thành một mặt côn. Ma sát giữa kim loại trong và kim loại chảy bằng ứng suất phá hủy cắt. Ứng suất ma sát cũng được đưa ra bởi biểu thức 2.22. • Tương tác giữa vật liệu và khuôn: Trên cơ sở quan sát bề mặt khuôn sau nhiều chu kỳ ép, thấy rằng ma sát trong khuôn có thể thay đổi một cách phức tạp khi kim loại chảy qua lỗ khuôn. Một mô hình ma sát được phát triển bởi Abtahi [53] dựa trên cách đo độ trượt và bám dính. Mô hình này cho thấy ma sát gần như không đổi trong vùng dính, trong khi ở vùng trượt, ma sát thay đổi theo góc khuôn. Bảng 2.1 giới thiệu một số hệ số ma sát áp dụng trong quá trình tạo hình khi dùng dạng ma sát trượt Tresca, [54,55,67]. 33 Bảng 2.1. Một số hệ số ma sát trong tạo hình khi dùng ma sát trượt Quá trình gia công Hệ số ma sát Quá trình tạo hình nguội 0.08 – 0.12 Tạo hình ấm 0.2 Quá trình tạo hình nóng có bôi trơn 0.2 – 0.3 Tạo hình nóng không bôi trơn 0.7 – 0.9 2.3.2. Nhiệt độ ép chảy Ép chảy có thể thực hiện biến dạng vật liệu ở trạng thái gia công nguội và trạng thái gia công nóng. Trong đó, gia công nóng được biến dạng dẻo ở điều kiện nhiệt độ tại đó xem quá trình hồi phục xảy ra đồng thời với quá trình biến dạng. Ép chảy được thực hiện ở nhiệt độ cao (lớn hơn nhiệt độ kết tinh lại) đối với các kim loại và hợp kim khó biến dạng nhằm giảm trở kháng biến dạng (giảm lực ép) trong quá trình ép. Nhiệt độ là một trong những thông số quan trọng nhất trong quá trình ép chảy nóng. Ứng suất chảy giảm khi nhiệt độ tăng do đó quá trình biến dạng sẽ dễ dàng hơn. Những thay đổi trong quá trình ép chảy phụ thuộc vào nhiệt độ phôi, sự truyền nhiệt từ phôi đến khuôn ép và nhiệt sinh ra do biến dạng và ma sát. Trong thực tế quá trình ép chảy có sự thay đổi nhiệt rất phức tạp, ngay khi phôi nóng được nạp vào khuôn (khuôn thường được làm nóng trước để giảm sự truyền nhiệt vào khuôn) cho đến kết thúc quá trình ép chảy. Một số nghiên cứu đã chỉ ra ảnh hưởng của nhiệt độ đến quá trình ép chảy [56-63] và nêu ra một số lưu ý khi thực hiện quá trình ép chảy ở nhiệt độ cao: - Nhiệt độ làm việc phải thấp hơn nhiệt độ nóng chảy và nhiệt độ giòn nóng của vật liệu (ranh giới hạt đã nóng chảy) để tránh hiện tượng giòn nóng (bở nóng). - Nhiệt độ cao làm tăng khả năng oxi hóa bề mặt phôi dẫn đến chất lượng bề mặt sản phẩm không tốt, gây hiện tượng hóa mềm chày và khuôn. - Khó điều chỉnh bôi trơn thích hợp và chất bôi trơn đắt. - Nhiệt độ làm việc trong ép chảy thường cao hơn trong rèn, cán do ứng suất thủy tĩnh lớn và để giảm thiểu nguy cơ nứt vỡ phôi. Nhiệt độ của phôi phụ thuộc vào: - Nhiệt độ ban đầu của dụng cụ, bản chất của vật liệu. - Nhiệt phát sinh do biến dạng dẻo. - Nhiệt phát sinh do ma sát giữa phôi và khuôn. - Khả năng truyền nhiệt ra môi trường bên ngoài của phôi và khuôn. Nếu ta bỏ qua gradient nhiệt độ nghĩa là 𝑔𝑟𝑎𝑑mmmmmmmmmm⃗ 𝑇 = 0, thì xem như nhiệt độ đồng đều và bằng hằng số. 34 Nếu có xét đến quá trình truyền nhiệt giữa phôi và khuôn, khi đó nhiệt độ ép chảy được xác định như sau: 𝑇 = 𝑇p − (𝑇p − 𝑇R) exp uvlCwxyz (2.23) Trong đó: 𝑇p- là nhiệt độ phôi ban đầu; 𝑇R- là nhiệt độ của khuôn; l - là hệ số truyền nhiệt; 𝛿 - là chiều dày lớp vật liệu; 𝑝, 𝑐 - là hằng số vật liệu. Nếu nhiệt độ tăng do biến dạng và ma sát, thì nhiệt độ trung bình của vật liệu tại thời điểm 𝑡 là: 𝑇~ = 𝑇 + 𝑇A + 𝑇\ (2.24) Trong đó: 𝑇A - là nhiệt phát sinh do biến dạng; 𝑇\ - là nhiệt do ma sát. Trong trường hợp tổng quát, quá trình truyền nhiệt của phôi trong hệ tọa độ trụ được mô tả bởi phương trình sau, [63]: R1 1 ul 1z + 3 u𝑘 3z + 𝑞 = 𝜌𝐶w C (2.25) Trong đó: T - là nhiệt độ; t - là thời gian; k- là hệ số truyền nhiệt; r - là khối lượng riêng; Cp- là nhiệt dung riêng; q- là tốc độ sinh nhiệt. 2.3.3. Hệ số ép chảy Hệ số ép chảy của bộ khuôn nhiều lỗ thoát phôi có thể xác định bằng tỷ số giữa diện tích mặt cắt của phôi và diện tích mặt cắt của sản phẩm (hình 2.12): 𝐸L = >? (>@) (2.26) Trong đó: n - là số lỗ thoát phôi đối xứng; AC - là diện tích mặt cắt của phôi; AE - là diện tích mặt cắt của sản phẩm. Hệ số ép chảy là một chỉ số cho biết khả năng gia công để nhận được sản phẩm yêu cầu. Hiệu quả biến dạng là một hàm của tỷ số ép chảy hay nói cách khác là áp suất cần thiết để ép chảy là một hàm của biến dạng. Khi tỷ số ép chảy thấp thì mức độ biến dạng dẻo thấp. Năng lượng tiêu hao cho ép chảy cũng thấp. Nếu tỷ số ép chảy thấp thì cấu trúc kim loại nhận được không có biến đổi tích cực (tương tự như vật đúc có hạt thô). Về mặt cơ học sẽ không được cải thiện. Khi tỷ số ép chảy trong khoảng từ 1-10 không đảm bảo việc đáp ứng tính chất cơ lý mong muốn của sản phẩm. Ngược lại khi tỷ số ép chảy cao, lực ép hay năng lượng tạo hình sẽ cao nhưng tính chất cơ học của sản phẩm sẽ được cải thiện rõ rệt nhờ mức độ biến dạng lớn tăng khả năng 35 hóa bền. Thông thường đối với các hợp kim cao tỷ số ép chảy trong khoảng từ 10-35, còn các hợp kim thấp tỷ số ép chảy có thể dao động trong khoảng từ 10-100. Tuy nhiên, tỷ số ép chảy cao hay thấp không phải là giá trị tuyệt đối mà còn tùy thuộc vào hình dạng hình học của sản phẩm ép chảy. Hình 2.12. Các thông số công nghệ chính trong ép chảy, [2] 2.3.4. Ứng suất chảy dẻo của vật liệu Đường cong ứng suất – biến dạng mô tả ứng xử cơ học của một vật liệu, nhận được khi thực hiện thí nghiệm kéo hoặc nén dưới các điều kiện khác nhau. Ứng suất chảy (trở kháng biến dạng) của vật liệu là rất quan trọng chịu ảnh hưởng của các yếu tố sau: • Thành phần hóa học và cấu trúc của vật liệu (A). • Nhiệt độ biến dạng (T), mức độ biến dạng (e) và tốc độ biến dạng (𝜀)̇. Do đó, ứng suất chảy có thể biểu diễn dưới dạng hàm như sau: 𝜎 = 𝑓(𝜀, 𝜀̇, 𝑇, 𝐴) (2.27) Mối quan hệ giữa ứng suất chảy và tốc độ biến dạng đã được sử dụng trong mô phỏng số để xác định ảnh hưởng của mức độ biến dạng dẻo và tốc độ biến dạng đến nhiệt độ trong ép chảy nhôm 6063 [64, 65]. Bởi vì độ chính xác của việc phân tích này phụ thuộc rất nhiều vào ứng suất chảy của vật liệu. Mối quan hệ giữa ứng suất chảy và tốc độ biến dạng cho bởi: s = 𝜎p u ḂḂz~∗ (2.28) Trong đó: 𝜎p - là ứng suất chảy tại tốc độ biến dạng tham chiếu đã biết 𝜀ṗ, m* - là hệ số nhạy cảm với tốc độ biến dạng. 2.3.5. Vận tốc ép chảy Ứng xử của của kim loại đối với các quá trình ép chảy có thể chịu ảnh hưởng của tốc độ biến dạng. Tăng vận tốc chày dẫn đến sự gia tăng lực ép. Nhiệt độ trong quá trình ép chảy gia tăng với sự tăng của vận tốc chày ép. Sự gia tăng này thực tế là do tốc độ biến dạng tăng tỷ lệ thuận với vận tốc chày ép và nhiệt sinh ra tỷ lệ thuận với tốc độ biến dạng. 𝐸L = 𝐴𝐴 36 Mối quan hệ giữa vận tốc chày ép và vận tốc ép chảy của phôi được trình bày trong tài liệu [2]. Phần này giải thích cách tính vận tốc ép chảy theo vận tốc của chày ép bằng cách sử dụng các quan hệ toán học đơn giản. Vận tốc ép chảy có thể được tính toán bằng cách sử dụng định luật bảo toàn thể tích, có nghĩa là thể tích kim loại phôi bằng với thể tích kim loại ép chảy ra khỏi lòng khuôn với giả thiết không có sự tiêu hao kim loại do cháy hay các khuyết tật đúc. Các thông số như trên hình 2.12, áp dụng định luật bảo toàn thể tích ta có: VRAC = VEAE (2.29) Trong đó: VR- là vận tốc của chày ép AC- là diện tích mặt cắt ngang của phôi VE- là vận tốc ép chảy AE – là diện tích mặt cắt ngang của sản phẩm Nếu khuôn có nhiều lỗ khuôn ép chảy mối quan hệ này sẽ thay đổi theo số lỗ khuôn ép chảy. VRAC = VE (nAE) (2.30) Trong đó: n là số lỗ khuôn ép chảy đối xứng Khi đó, vận tốc ép chảy của phôi là: 𝑉 = 𝑉L >? (>@) hay 𝑉 = 𝑉L. 𝐸L (2.31) Trong đó: ER chính là hệ số ép chảy 2.4. Ảnh hưởng của dòng chảy vật liệu Dòng chảy của kim loại là cơ sở để xác định trường hợp phân bố ứng suất, biến dạng, các thông số về lực và công biến dạng. Ngoài ra, dựa vào dòng chảy của kim loại ta có thể rút ra kết luận về sự xuất hiện của khuyết tật trên sản phẩm ép. Để nghiên cứu dòng chảy của kim loại có thể áp dụng nhiều phương pháp khác nhau, ví dụ phương pháp thí nghiệm trên mô hình vật liệu sáp và nhựa dẻo, thí nghiệm ép những kim loại dễ biến dạng như chì, thiếc... ở nhiệt độ phòng, thí nghiệm ép trong điều kiện sản xuất. Một kỹ thuật phổ biến để nghiên cứu mô hình dòng chảy là cắt một phôi tròn thành hai nửa và đánh dấu một mặt bằng lưới vuông. Hai nửa sau đó được đặt cùng nhau trong buồng chứa (chúng cũng có thể được gắn chặt với nhau) và ép chảy thành một sản phẩm. Sau đó chúng được tách ra và quan sát sự biến dạng của đường lưới. Những nhân tố ảnh hưởng quan trọng nhất đến dòng chảy của kim loại phải kể đến ma sát giữa vật liệu biến dạng và thành buồng ép, cối và chày ép cũng như thuộc tính ứng xử của vật liệu. Đặc biệt sự phân bố tính dẻo không đồng đều trên tiết diện cũng như chiều dài của phôi ép gây nên bởi tổ chức thớ trong phôi (dạng thiên tích nhánh cây đối với phôi đúc và thớ dọc đối với phôi cán) cũng như bởi sự phân bố nhiệt độ khác nhau giữa các vùng sẽ làm ảnh hưởng đến sự chảy của kim loại trong quá trình biến dạng. Tất cả sự tác động của những yếu tố ảnh hưởng đó đã dẫn đến 37 sự xuất hiện của các dạng dòng chảy khác nhau. Hình 2.13 biểu diễn các dạng dòng chảy khác nhau theo Pearson và Parkin [66]. Có thể nhận thấy khi phôi đi qua vùng biến dạng của khuôn là lúc dòng chảy kim loại bị biến dạng mãnh liệt nhất. Hình 2.13a dòng chảy của vật liệu gần như đồng nhất là do ma sát giữa thành khuôn và phôi là không đáng kể khi ép chảy nghịch. Bề mặt của phôi nhận được do đó cũng có chất lượng tốt. Vùng chết gần khu vực thoát phôi gần như không tồn tại. Cùng với quá trình ép chảy nghịch nhưng có sự xuất hiện ma sát giữa phôi và miệng khuôn, do đó tồn tại một vùng chết tại cửa khuôn như hình 2.13b. Kim loại ở tâm phôi có tốc độ di chuyển nhanh hơn so với phần kim loại còn lại. Vật liệu ở gần khu vực cửa khuôn tồn tại và gần vùng chết tồn tại biến dạng cắt trên bề mặt. Tuy nhiên nhìn chung quá trình ép chảy thuận cho dòng chảy đồng nhất nếu khả năng bôi trơn tốt. Trong trường hợp ép chảy thuận có bôi trơn thì vùng chết và biến dạng cắt đều cao hơn so với quá trình ép chảy thuận như trên hình 2.13c. Tính chất sản phẩm nhận được sẽ không đồng nhất và cho chất lượng bề mặt không bằng như quá trình ép chảy nghịch. Điều này cũng phản ánh lực ép tăng cao hơn trong trường hợp ép chảy thuận như trên hình 2.2. Hình 2.13c xảy ra hiện tượng hư hại khi bôi trơn không đảm bảo, vật liệu ép chảy không đồng nhất, vận tốc ép chảy quá lớn hoặc nhiệt độ không đồng nhất trên phôi. Khi đó tồn tại một vùng chết (không di chuyển) lớn và biến dạng cắt xảy ra mãnh liệt. a) b) c) d) Hình 2.13. Dòng chảy vật liệu trong quá trình ép: a) ép chảy nghịch không có ma sát, b) ép chảy nghịch có bôi trơn, c) ép chảy thuận có bôi trơn, d) ép chảy thuận không bôi trơn-hư hại [1]. Hình 2.14 là kết quả của quá tình ép chảy thuận giữa mô phỏng và thực nghiệm. Lưới biến dạng tương đồng nhau và tồn tại một vùng chết. a) b) Hình 2.14. So sánh giữa dòng chảy mô phỏng (a) và thực nghiệm (b) [2] 38 2.5. Các dạng khuyết tật, phá hủy trong quá trình ép chảy 2.5.1. Nứt bề mặt sản phẩm Trong một số trường hợp, sản phẩm sau khi ép chảy xuất hiện các vết nứt có dạng hình sóng ngang hoặc các vết xước dọc theo chiều dài của sản phẩm. Theo nhiều nghiên cứu chỉ ra rằng, nguyên nhân của hiện tượng này là do các yếu tố sau đây: - Ma sát giữa vật liệu phôi và khuôn lớn, đặc biệt tại vùng cửa thoát phôi - Vận tốc ép chảy cao (tốc độ thoát cao) - Nhiệt độ ép quá cao (đến ngưỡng vùng giòn nóng) Hai nguyên nhân đầu đều do tương thích biến dạng dẫn đến lớp ngoài chịu ứng suất kéo. Cụ thể, lớp bên trong thoát qua lỗ khuôn nhanh hơn nhiều so với lớp bề mặt sản phẩm, lớp kim loại tiếp xúc với khuôn thoát chậm do ma sát với khuôn lớn dẫn đến bị lớp trong kéo theo nên gây ra ứng suất kéo. Ở vùng nhiệt độ thấp có thể gây hiện tượng dính khuôn hoặc thay đổi đột ngột lực ép cũng gây ra hiện tượng nứt ngang, đứt đoạn trên bề mặt. Hình 2.15 là mô tả hiện tượng vết nứt ngang xuất hiện trên bề mặt của sản phẩm sau khi ép. Hình 2.15. Vết nứt ở bề mặt [3] Nếu nhiệt độ ép chảy, ma sát hoặc vận tốc quá cao, nhiệt độ bề mặt có thể tăng lên đáng kể, điều này có thể gây nứt và rách bề mặt. Những vết nứt này là giữa các hạt (nghĩa là dọc theo ranh giới hạt và gây ra bởi hiện tượng giòn nóng). Những khuyết tật này xảy ra đặc biệt là trong các hợp kim nhôm, magiê và kẽm và cũng có thể xảy ra trong các hợp kim khác ở nhiệt độ cao. Trường hợp này có thể tránh bằng cách làm giảm nhiệt độ phôi và vận tốc ép chảy thấp hơn. Rạn nứt bề mặt cũng có thể xảy ra ở nhiệt độ thấp hơn, nguyên nhân là do bị dính chu kỳ của sản phẩm ép chảy dọc theo vùng chết của cửa khuôn. Khi đó bề mặt trên sản phẩm bị các vết xước dạng hình các mắt của thân tre, người ta còn gọi là khuyết tật thân tre. Khi sản phẩm bị ép chảy dính vào vùng chết của cửa khuôn thì lực ép tăng nhanh và nó được giải phóng khi ra khỏi cửa khuôn, điều đó làm xuất hiện các vết nứt trên bề mặt có tính chu kỳ. Hình 2.16 là chất lượng bề mặt của sản phẩm khi ép chảy hợp kim nhôm AA5456. Nhận thấy, khi nhiệt độ gia tăng từ 350 oC lên 480 oC chất lượng bề mặt giảm rõ rệt. Các vết nứt trên bề mặt xuất hiện nhiều tại nhiệt độ 480 oC. 39 Hình 2.16. Ảnh hưởng của nhiệt độ đến chất lượng bề mặt khi ép chảy hợp kim nhôm AA2014 [1] 2.5.2. Nứt ở tâm Tại tâm của sản phẩm ép chảy có thể phát triển các vết nứt, được gọi là nứt trung tâm (Chevron), vỡ trung tâm, vỡ dạng mũi tên. Hiện tượng nứt ở tâm cũng là do tương thích biến dạng. Cụ thể, lớp biên chịu nén, còn lõi chịu ứng suất kéo. Nguyên nhân là do hệ số ép chảy nhỏ, chỉ có lớp biên biến dạng, lõi không biến dạng (hoặc biến dạng ít) dẫn đến lớp biên giãn dài nhiều (thoát nhanh) còn lõi giãn dài ít (thoát chậm hơn). Những vết nứt này cũng đã được quan sát thấy trong quá trình đùn ống và trong kéo sợi, ống. Hình 2.17a là hiện tượng sản phẩm ép chảy bị nứt ở tâm phát hiện nhờ cắt mẫu làm hai nửa và quan sát hoặc người ta có thể kiểm tra bằng siêu âm. Hiện tượng nứt tại tâm gia tăng khi hai phía của vùng biến dạng không tiếp xúc với nhau trên hình 2.17b. Trường hợp này muốn mở rộng vùng biến dạng, người ta có thể giảm góc khuôn, tăng hệ số ép chảy hoặc cả hai trường hợp đồng thời. Hình 2.17. Hiện tượng bị nứt ở tâm (Chevron) sản phẩm ép chảy sản phẩm tròn [3] Nứt ở tâm hoặc ngoài bề mặt sản phẩm (center burst or chevron cracking) có thể xảy ra ở điều kiện hệ số ép chảy thấp do điều kiện ma sát thấp ở vùng biến dạng trong khuôn ép chảy. 40 2.5.3. Hiện tượng giòn nóng Hình 2.18. Hiện tượng giòn nóng khi ép chảy nhôm [3] Hình 2.18 là hình ảnh sản phẩm ép chảy bị chày dạng vảy cá khi nhiệt độ ép chảy quá cao đồng thời ma sát làm phát sinh nhiệt làm xuất hiện nóng chảy cục bộ trên bề mặt gây ra phá hủy bề mặt sản phẩm. Đây cũng chính là nguyên nhân gây hư hỏng sản phẩm khi ép nóng, tuy lực ép nóng có giảm nhưng yêu cầu phải điều chỉnh chế độ nhiệt rất khắc khe. 2.6. Kết luận chương 2 - Trên cơ sở tổng hợp cơ sở lý thuyết vùng biến dạng khi ép chảy ngang để xem xét trường vận tốc dòng chảy từ đó xác định được lực ép ngang bằng phương pháp định trị trên. - Phân tích các yếu tố ảnh hưởng đến quá trình ép chảy ngang như: nhiệt độ, ma sát, tỷ số ép chảy, ảnh hưởng của dòng chảy vật liệu, cấu trúc trong quá trình ép chảy đến chất lượng sản phẩm, nhận thấy, các yếu tố này không những ảnh hưởng trực tiếp đến quá trình ép chảy mà còn ảnh hưởng tương tác lẫn nhau. - Nghiên cứu lựa chọn các thông số công nghệ chính là: vận tốc ép chảy, nhiệt độ và quá trình truyền nhiệt của phôi vào khuôn để xem xét ảnh hưởng của các thông số này đến lực ép và quá trình ép chảy ngang trục chữ thập bằng phần mềm mô phỏng số từ đó phân tích trạng thái ứng suất-biến dạng trên phôi. - Các hiện tượng hư hại, phá hủy gặp phải khi ép chảy như hiện tượng nứt trên bề mặt và tại tâm phôi. Đặc biệt hiện tượng tách lớp, phá hủy giữa các lớp khi ép chảy vật liệu nhiều lớp và hiện tượng phá hủy mỏi của chi tiết sau nhiều chu kỳ làm việc. Từ các nghiên cứu đó luận án lựa chọn sản phẩm trục chữ thập để ép chảy ngang bằng vật liệu hai lớp và xem xét hiện tượng phá hủy khi ép chảy vật liệu hai lớp. 41 CHƯƠNG 3 NGHIÊN CỨU QUÁ TRÌNH ÉP CHẢY NGANG TRỤC CHỮ THẬP BẰNG MÔ PHỎNG SỐ 3.1. Giới thiệu khớp chữ thập Khớp chữ thập có cấu tạo khá đơn giản, nhưng sử dụng hiệu quả trong các bộ truyền động và ứng dụng nhiều trong công nghiệp ô tô, máy công trình Khớp chữ thập cơ bản gồm 2 phần chính, là trục chữ thập và bốn cốc bi lắp vào đầu của bốn đỉnh của thân chữ thập. Bên trong cốc chữ thập gồm các viên bi đũa nhỏ và dài xếp khít nhau sao cho vừa với lòng trong của cốc để tạo nên một con lăn tròn ôm khít lấy đỉnh thân chữ thập. Trục chữ thập thường được làm từ loại thép các bon trung bình hoặc thép hợp kim kết hợp với các quá trình xử lý nhiệt để chi tiết có độ bền cao và có thể làm việc trong điều kiện chịu mỏi. Ngoài ra, cũng có những loại trục chữ thập được làm bằng các hợp kim màu của nhôm và đồng sử dụng trong các dẫn động không chịu tải lớn, chịu ăn mòn và chống oxy hóa. Hình 3.1 là trục chữ thập bằng thép và khớp chữ thập. - Công dụng của trục chữ thập: là cơ cấu nối và truyền mômen xoắn. Nó được sử dụng để truyền mômen giữa các cụm không cố định trên cùng một đường trục và các cụm này có thể bị thay đổi vị trí tương đối trong quá trình làm việc. Ngoài ra, trục chữ thập còn có tác dụng như điều chỉnh vận tốc, ngăn ngừa quá tải hay đóng mở các cơ cấu cơ khí, v.vVí dụ trong hệ thống truyền lực của ôtô các khớp nối được dùng để nối giữa các trục các đăng, khớp trượt tới hộp số với cầu chủ động hoặc để nối giữa cầu chủ động với bánh xe ở hệ thống treo độc lập. a) Trục chữ thập (đã lắp bi) b) Khớp chữ thập Hình 3.1. Trục chữ thập bằng thép và khớp chữ thập - Yêu cầu kỹ thuật: do trục chữ thập
File đính kèm:
luan_an_nghien_cuu_anh_huong_cua_mot_so_thong_so_cong_nghe_c.pdf
Thông tin đưa lên trang web-in.docx
Tóm tắt luận án_Đỗ Quang Long-14-11-2020-in.pdf
TRÍCH YẾU LUẬN ÁN.pdf