Luận án Nghiên cứu ảnh hưởng của một số thông số hình học khuôn và thông số công nghệ đến chất lượng sản phẩm khi ép chảy hợp kim nhôm
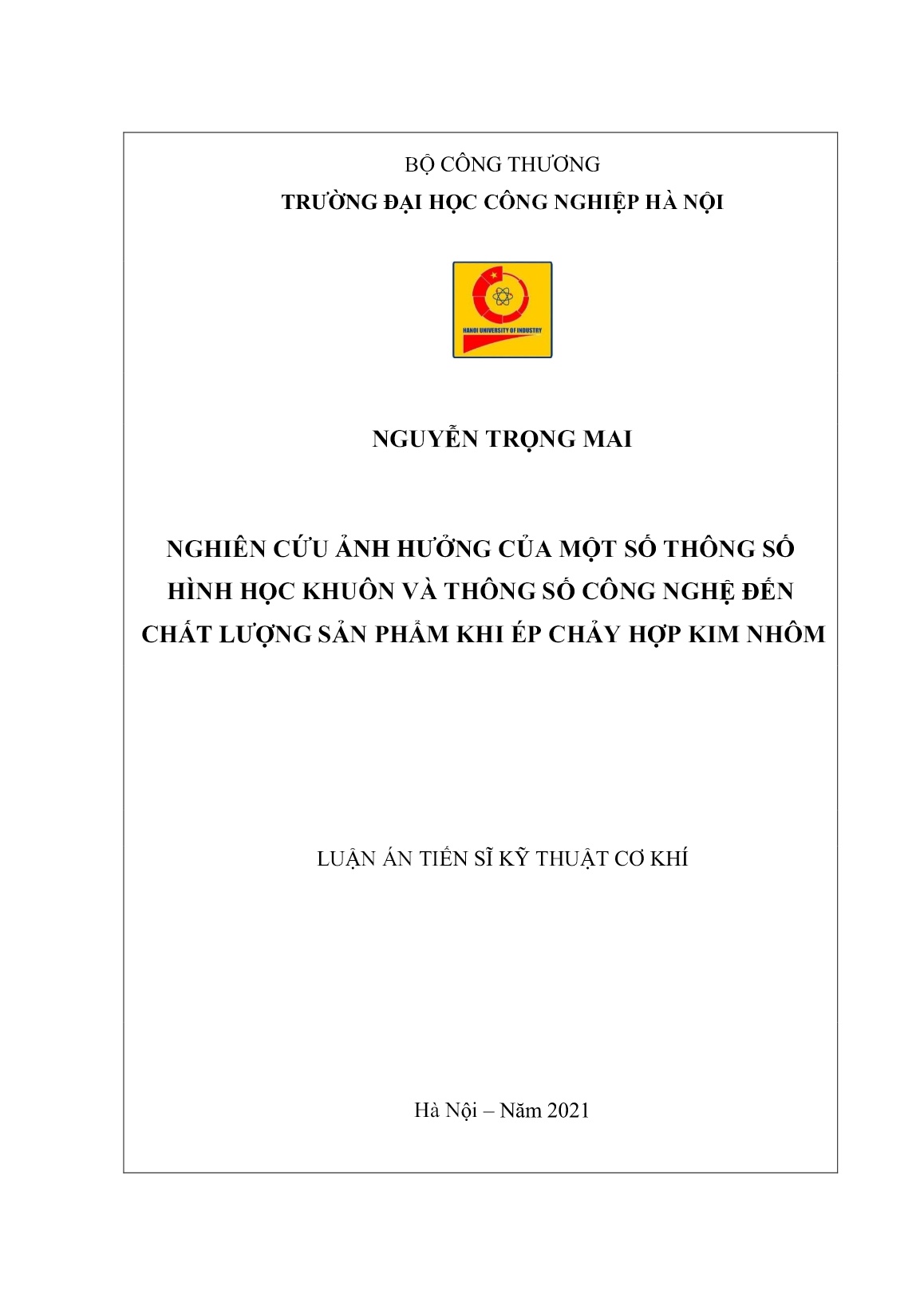
Trang 1
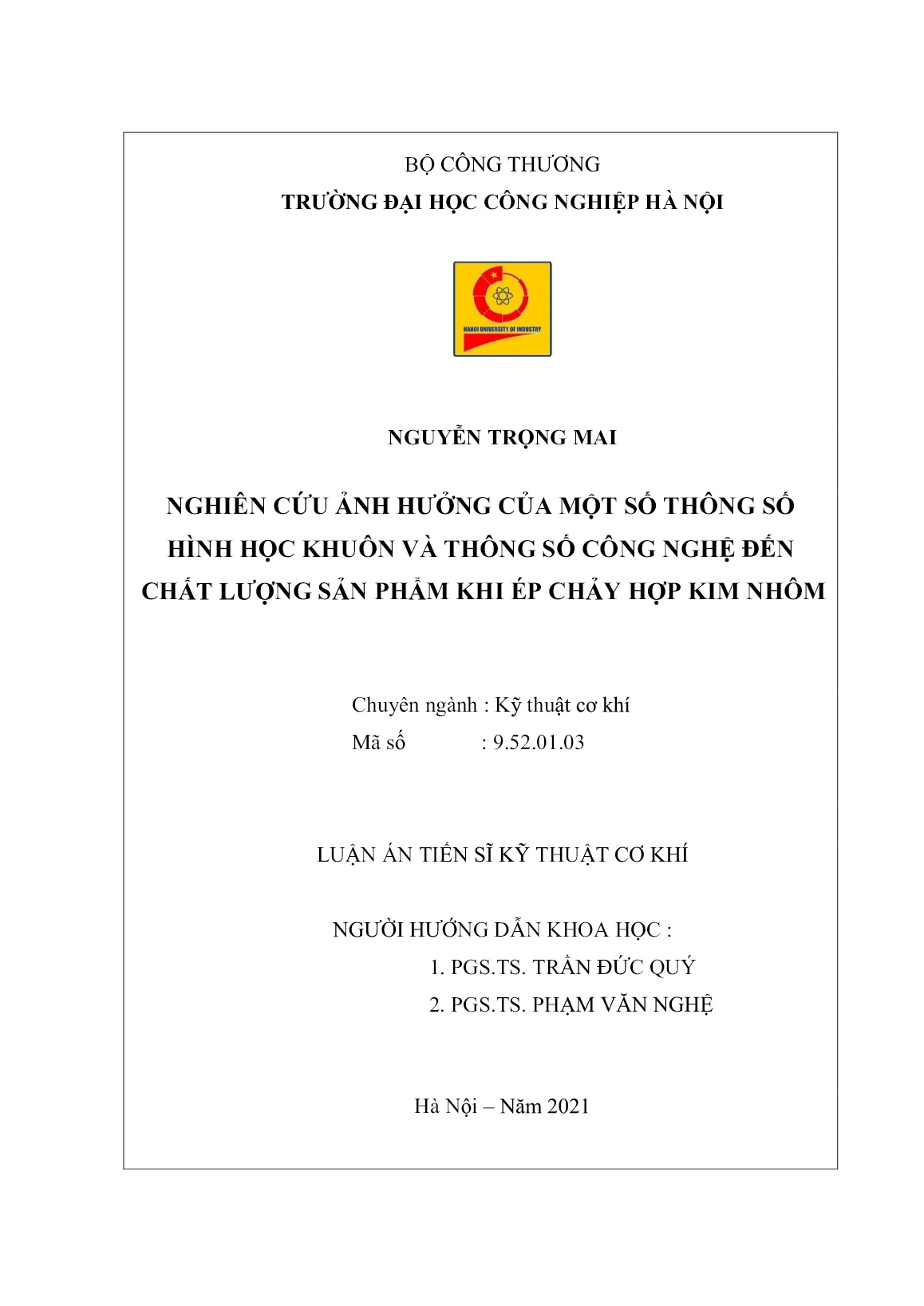
Trang 2
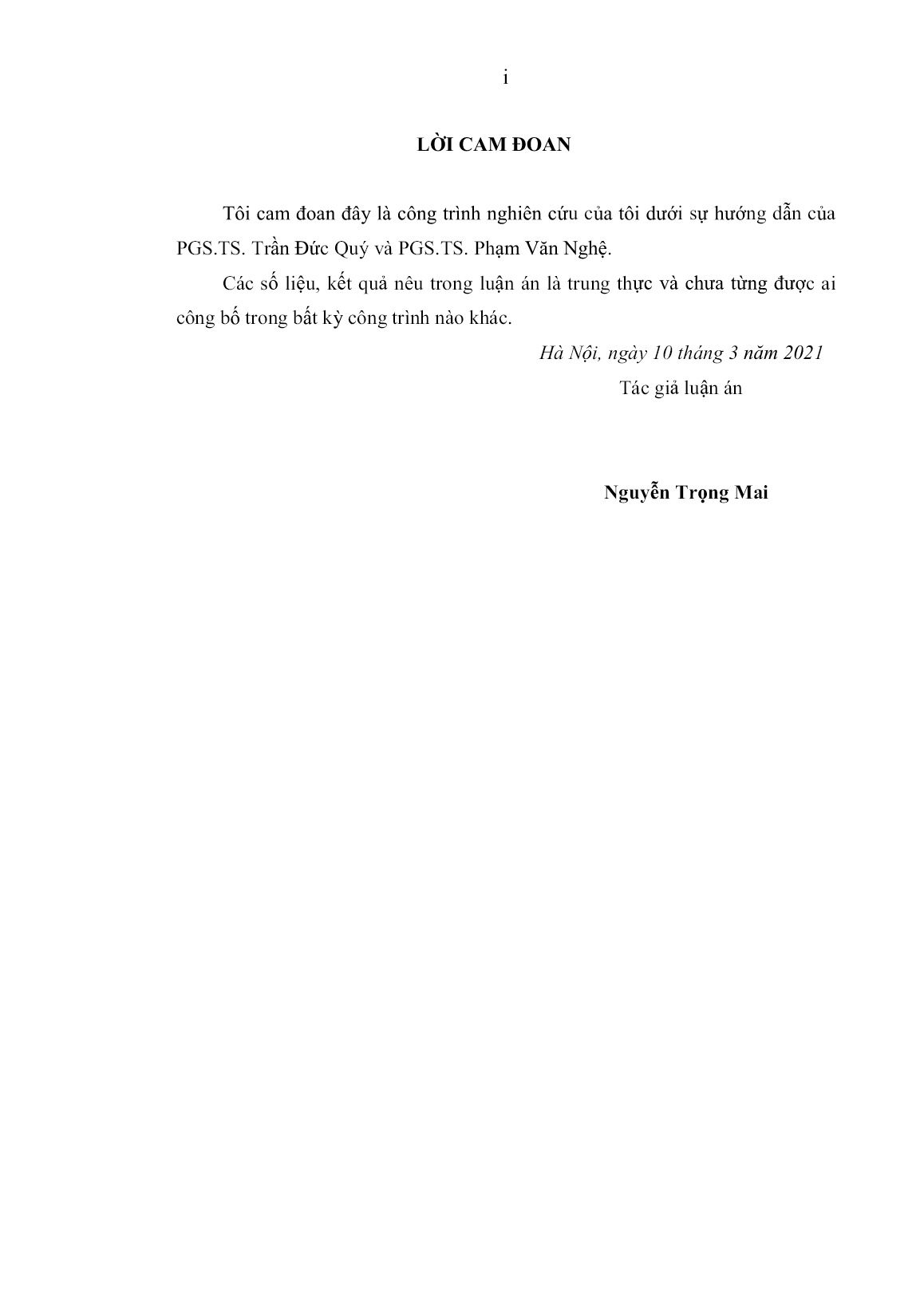
Trang 3
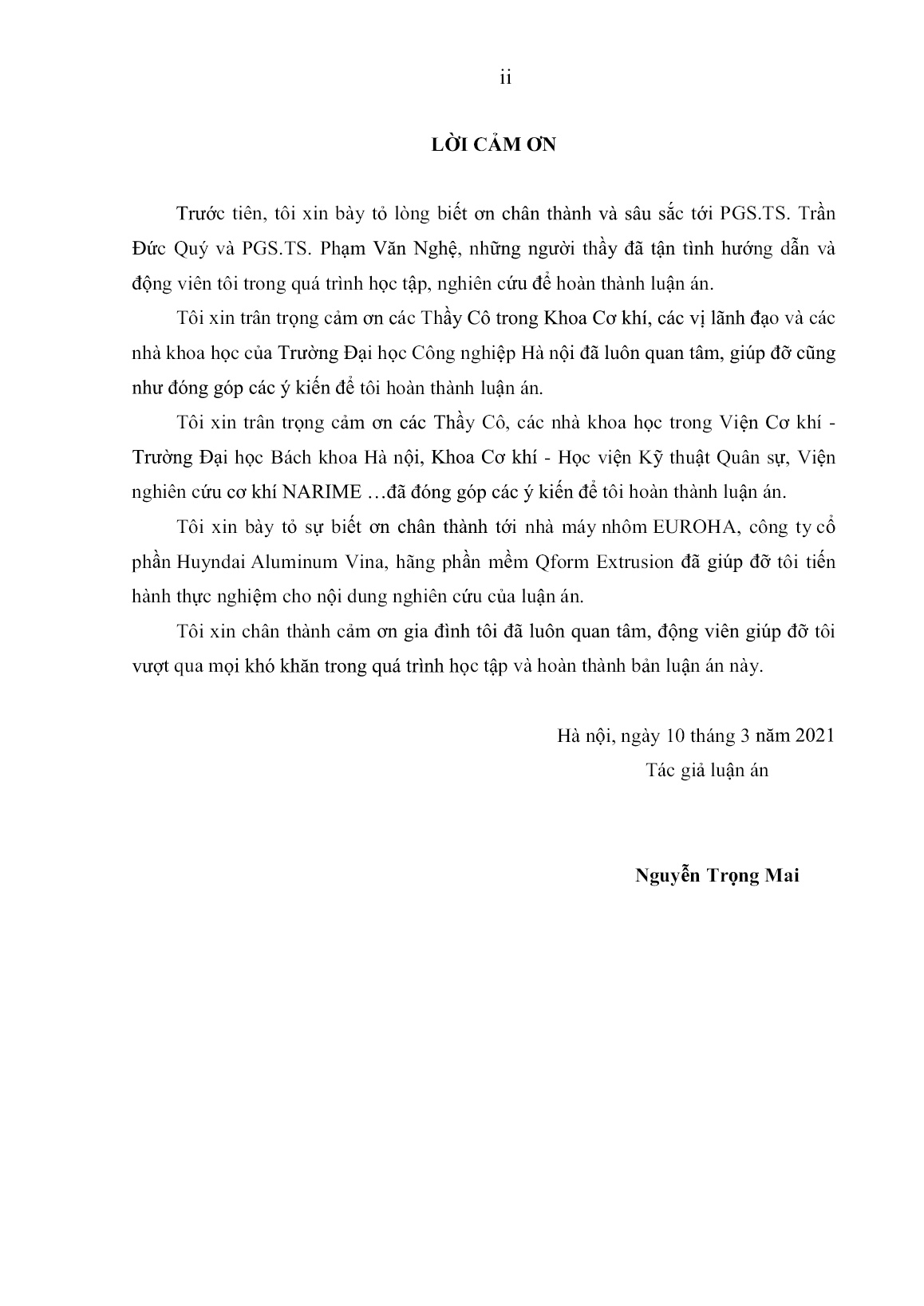
Trang 4
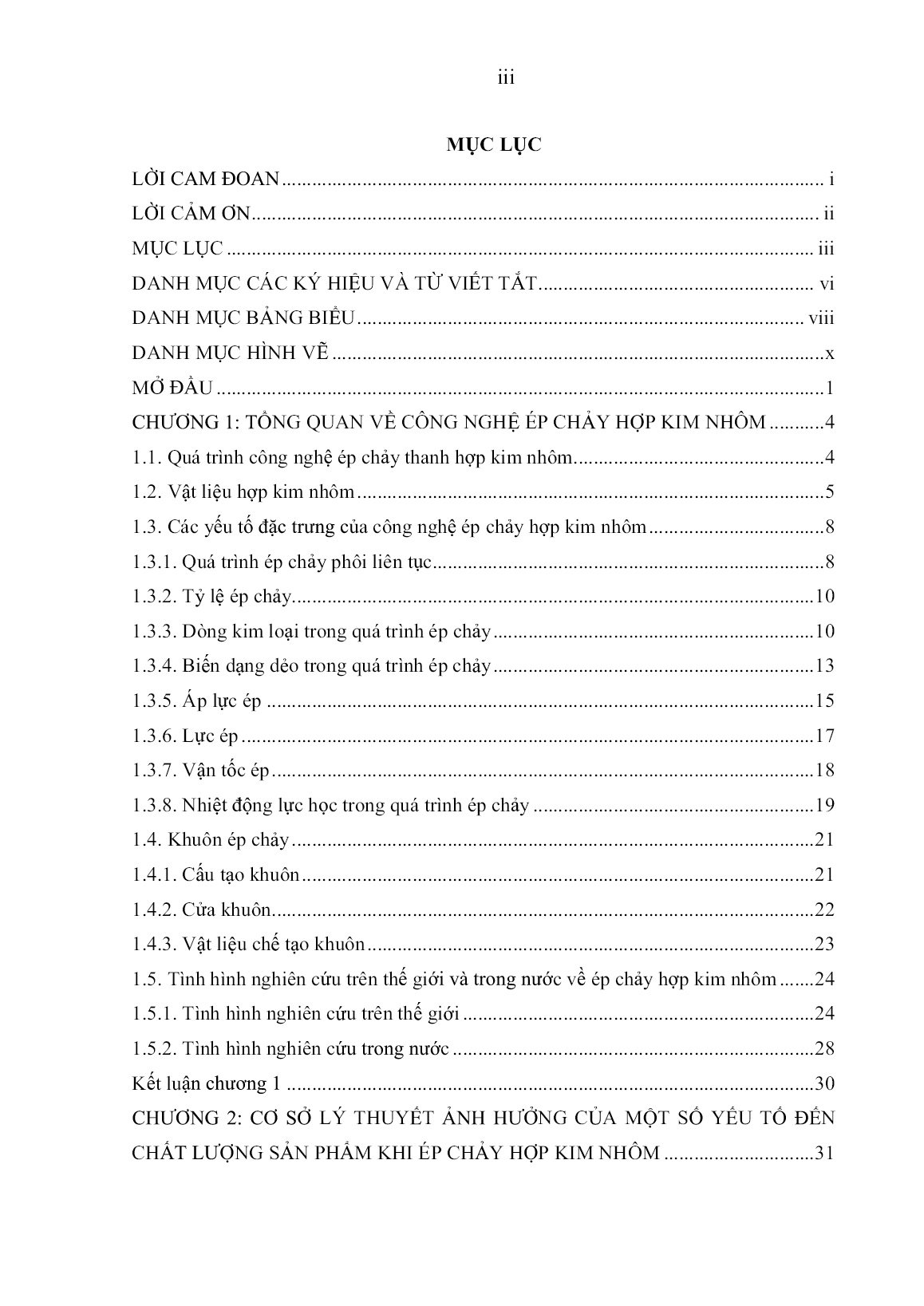
Trang 5
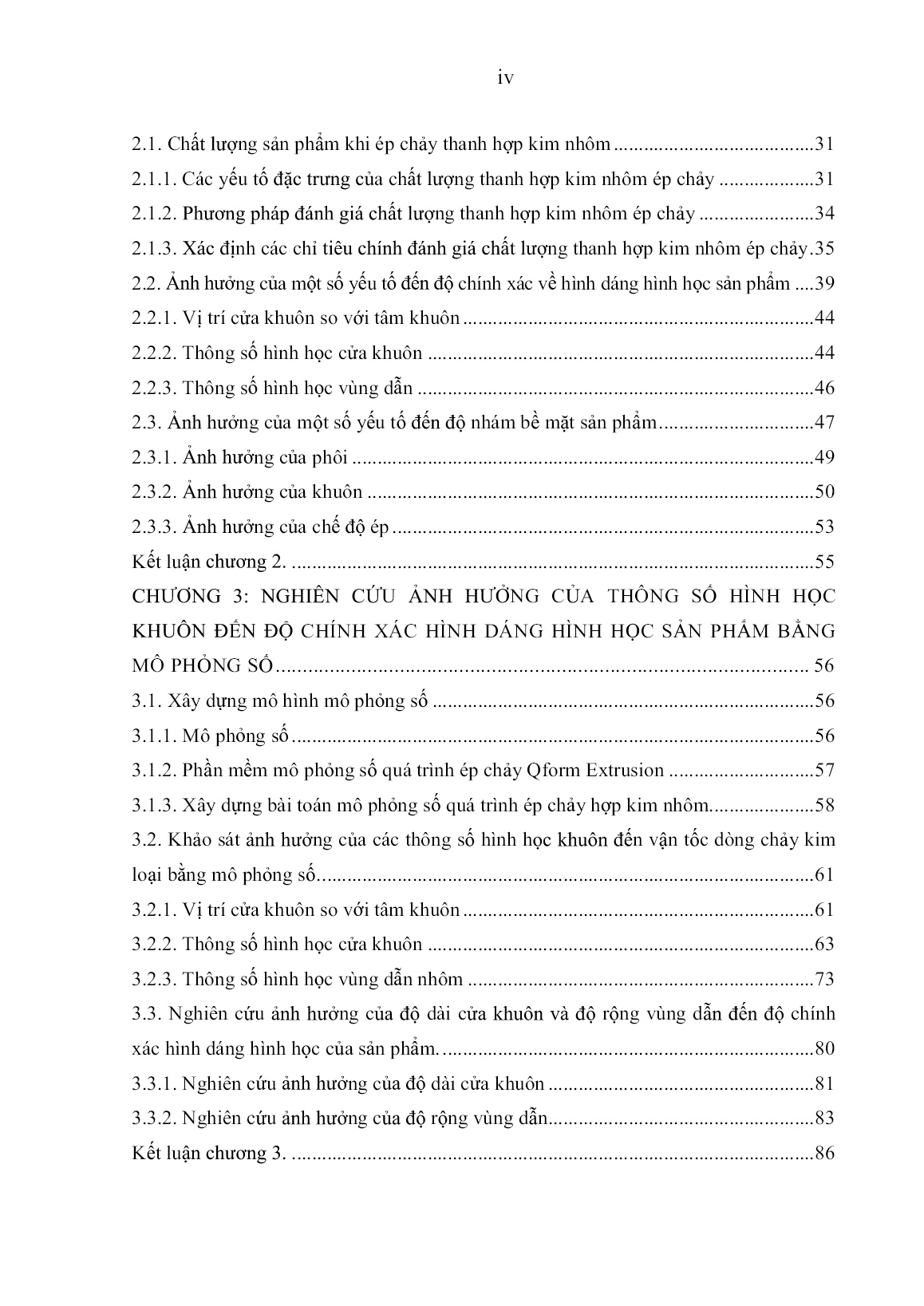
Trang 6
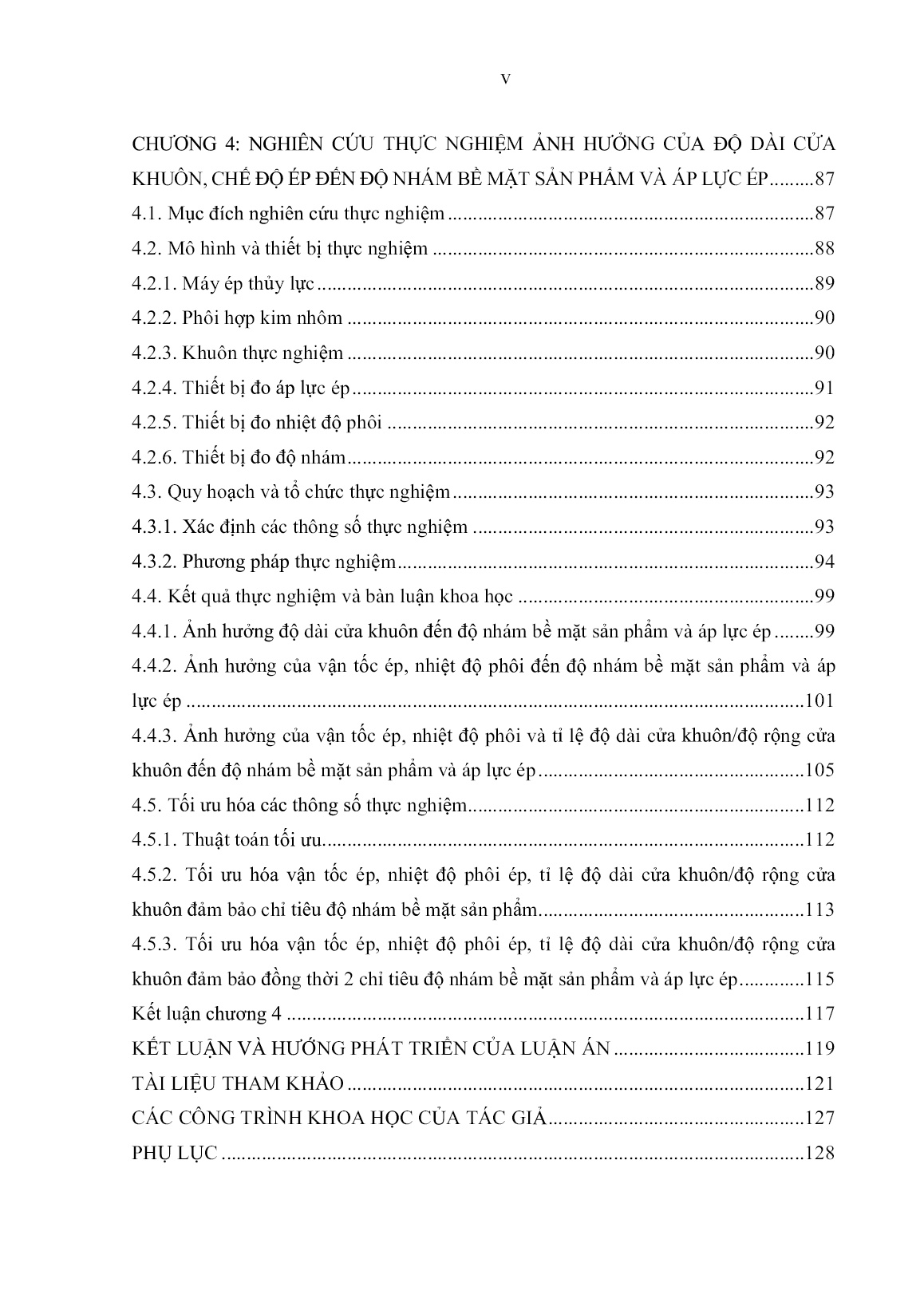
Trang 7
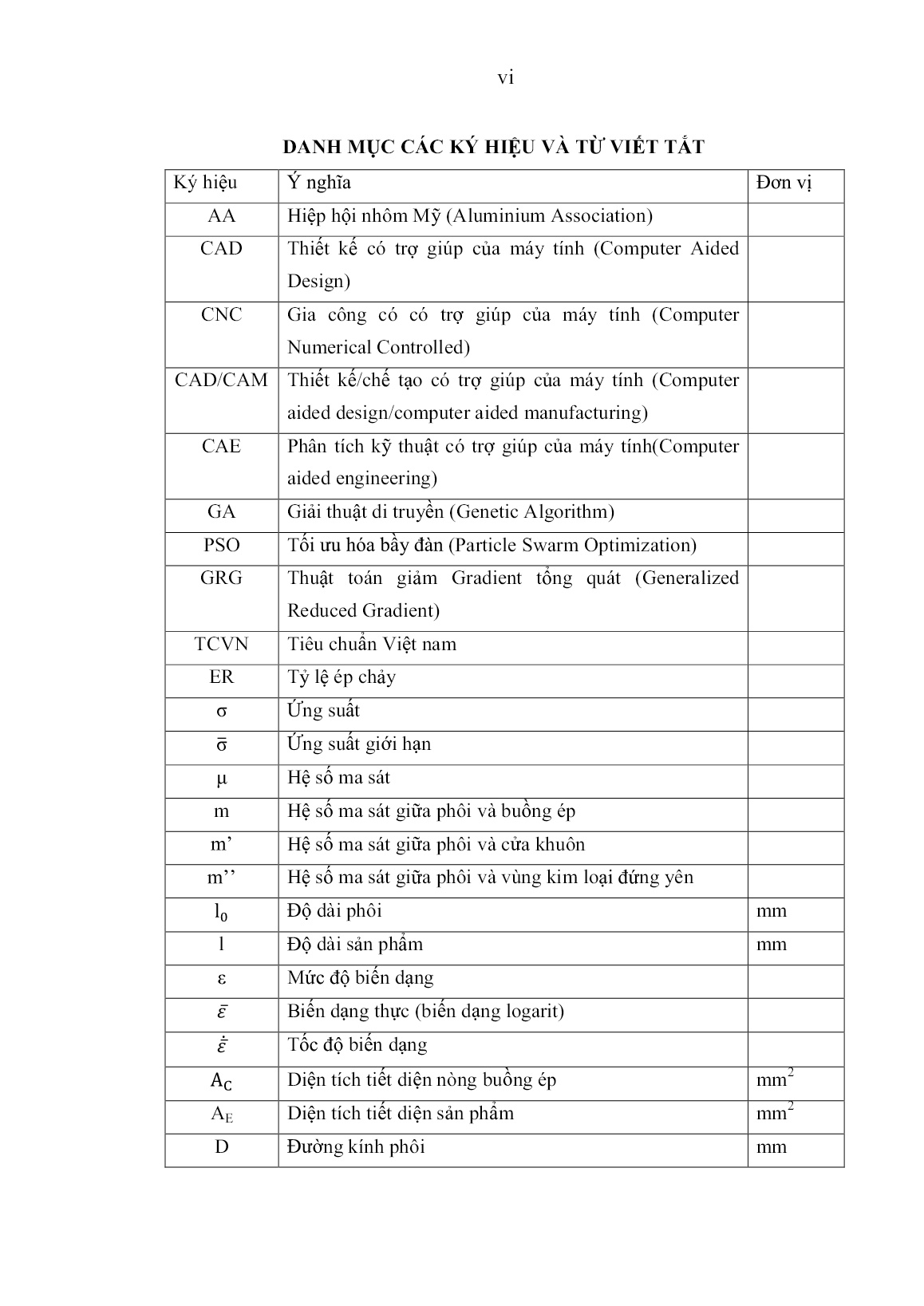
Trang 8
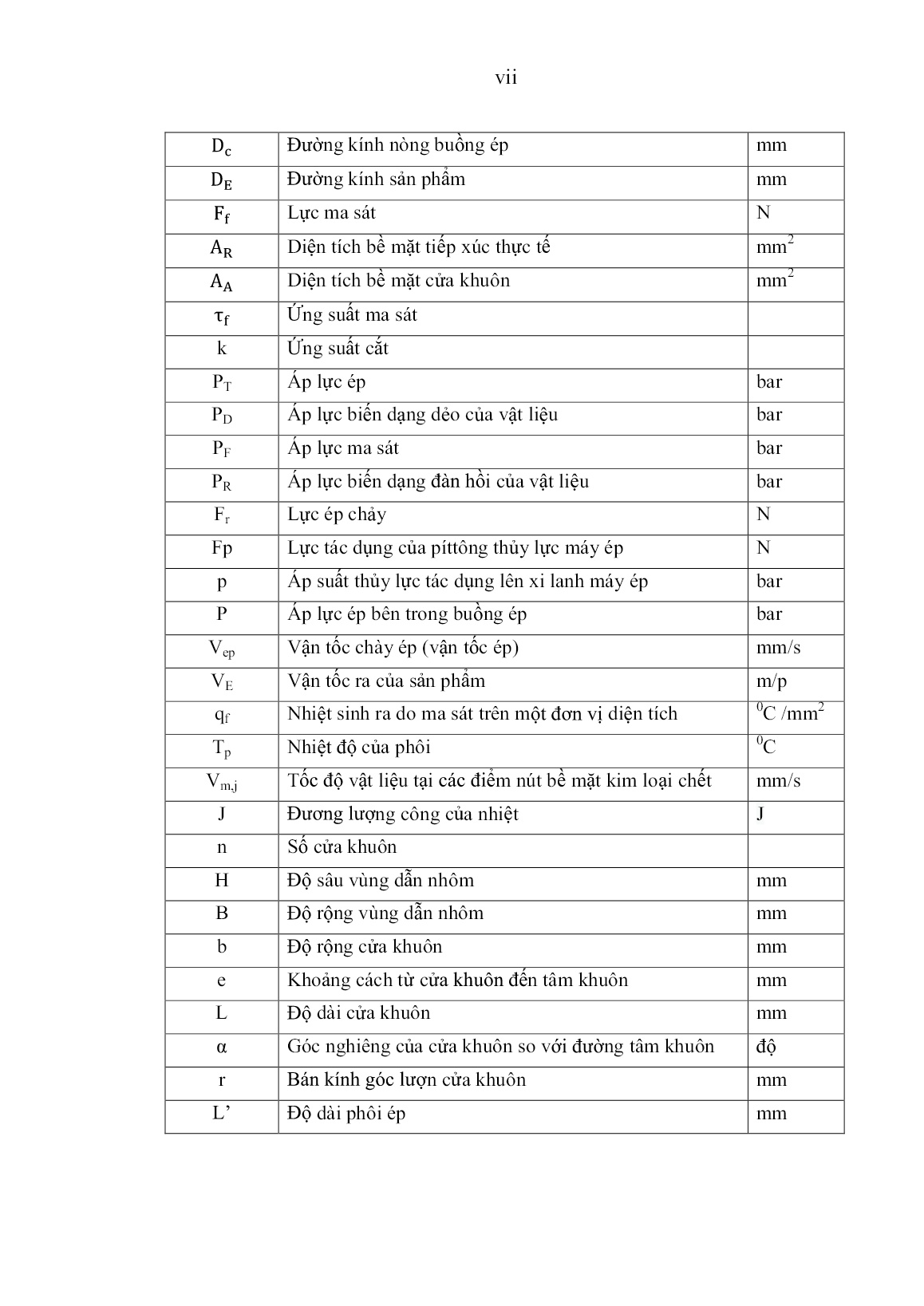
Trang 9
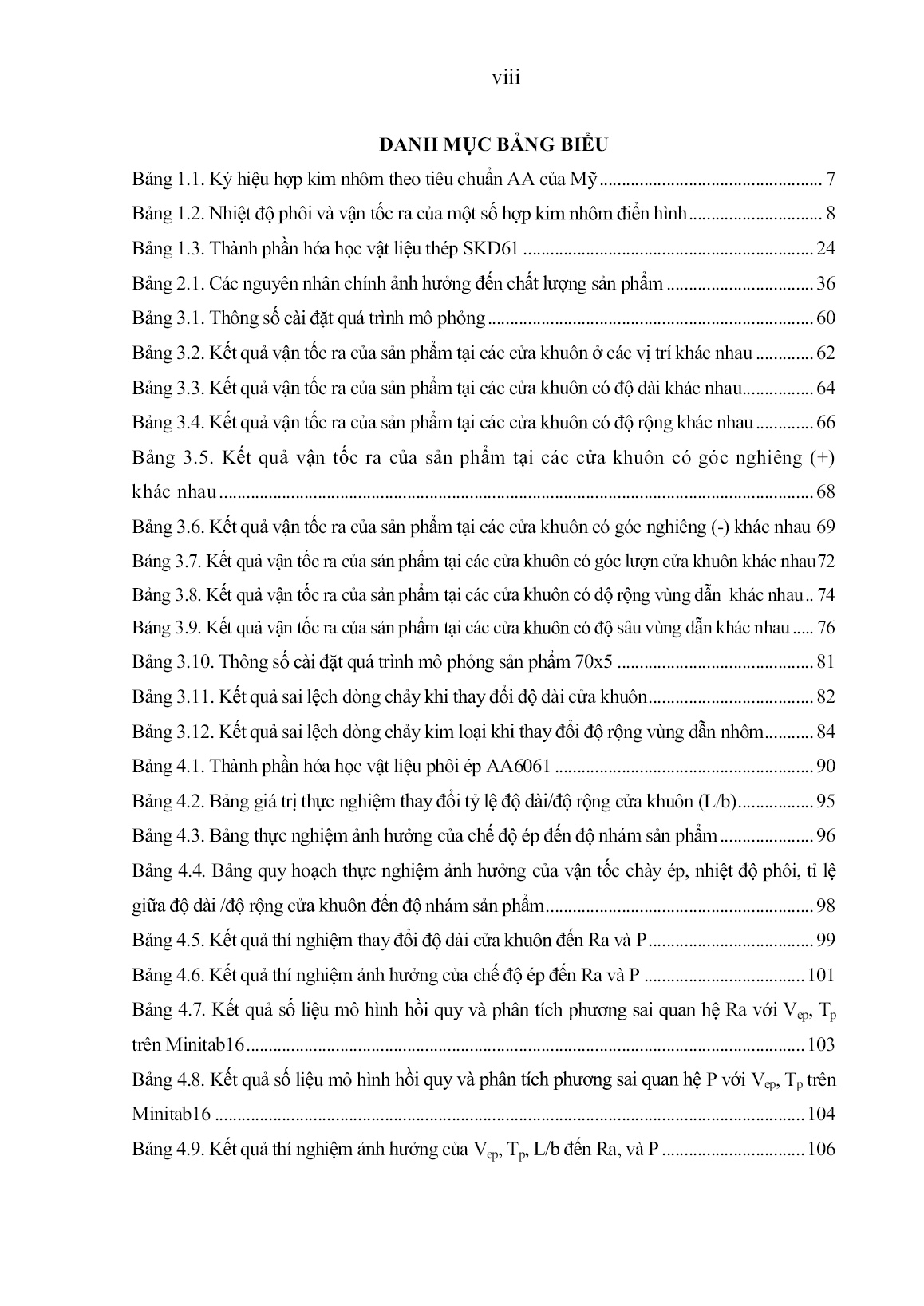
Trang 10
Tải về để xem bản đầy đủ
Bạn đang xem 10 trang mẫu của tài liệu "Luận án Nghiên cứu ảnh hưởng của một số thông số hình học khuôn và thông số công nghệ đến chất lượng sản phẩm khi ép chảy hợp kim nhôm", để tải tài liệu gốc về máy hãy click vào nút Download ở trên.
Tóm tắt nội dung tài liệu: Luận án Nghiên cứu ảnh hưởng của một số thông số hình học khuôn và thông số công nghệ đến chất lượng sản phẩm khi ép chảy hợp kim nhôm
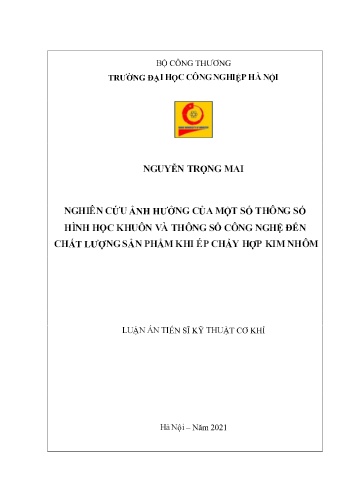
- Cửa khuôn: Độ dài của cửa khuôn L; độ rộng của cửa khuôn b; góc nghiêng của cửa khuôn hợp với phƣơng ép α. Dựa trên cơ sở lý thuyết trên có thể phân tích các thông số hình học khuôn có sự ảnh hƣởng đến tốc độ ra của sản phẩm, từ đó ảnh hƣởng đến sự cân bằng dòng chảy kim loại, độ chính xác về hình dáng hình học sản phẩm ép chảy nhƣ sau: 2.2.1. Vị trí cửa khuôn so với tâm khuôn Trong quá trình ép chảy thuận trên khuôn ép sản phẩm dạng thanh với trƣờng hợp độ dài cửa khuôn L không đổi, vận tốc ra của sản phẩm tại các vị trí khác nhau trên cửa khuôn là khác nhau. Vận tốc dòng chảy kim loại tại khu vực tâm khuôn có vận tốc cao hơn khu vực xa tâm khuôn do khu vực mặt trụ ngoài phôi có hiện tƣợng ma sát giữa phôi với thành buồng ép và với khu vực vùng kim loại chết [58]. 2.2.2. Thông số hình học cửa khuôn a) Độ dài cửa khuôn Tăng độ dài cửa khuôn L (hình 1.15) tại một vị trí nào đó trên cửa khuôn sẽ làm tăng diện tích tiếp xúc giữa dòng chảy với khuôn, từ đó làm tăng ma sát giữa dòng kim loại với bề mặt cửa khuôn. Do đó làm giảm vận tốc ra của sản phẩm và làm tăng áp lực ép. Vì vậy ngƣời ta thƣờng tăng độ dài cửa khuôn tại khu vực có vận tốc ra của sản phẩm nhanh hơn và ngƣợc lại để có thể cân bằng dòng chảy kim loại [58]. b) Độ rộng cửa khuôn Tại vị trí sản phẩm có độ rộng cửa khuôn b (hình 1.15) lớn sẽ giúp lƣu lƣợng kim loại chảy qua nhiều hơn làm cho vận tốc đi ra của dòng kim loại nhanh hơn và ngƣợc lại. Vì vậy cần phải có biện pháp để làm giảm vận tốc dòng chảy tại các vị trí này. c) Góc nghiêng cửa khuôn Góc của cửa khuôn hợp với phƣơng ép chảy ( ) cũng có tác dụng thay đổi vận tốc thoát của sản phẩm. Các dạng cửa khuôn nhƣ thể hiện trên nhƣ hình 1.17. Cửa khuôn (+) (hình 1.17.b) sẽ làm chậm vận tốc ra so với cửa khuôn dạng song song (hình 1.17.a), do diện tích tiếp xúc giữa dòng kim loại với cửa khuôn tăng làm tăng lực ma sát. Cửa khuôn dạng (-) (hình 1.17.c) sẽ làm vận tốc ra trở nên nhanh hơn so với dạng cửa khuôn song song (hình 1.17.a) do diện tích tiếp xúc giữa dòng 45 kim loại với cửa khuôn giảm làm giảm lực ma sát. Thay đổi góc của cửa khuôn đƣợc sử dụng khi việc thay đổi độ dài cửa khuôn không đáp ứng đƣợc trong việc kiểm soát vận tốc ra không đổi của dòng chảy. Thay đổi góc cửa khuôn cũng đƣợc sử dụng trong quá trình sửa khuôn vì chỉ cần gia công một lƣợng nhỏ kim loại đã có thể thay đổi đƣợc vận tốc ra của sản phẩm. Ảnh hƣởng của góc cửa khuôn đến vận tốc dòng chảy của sản phẩm đƣợc sử dụng trong việc dự đoán vận tốc ra của sản phẩm khi khuôn bị biến dạng dƣới tác dụng của lực ép, làm cho góc cửa khuôn thay đổi trong quá trình ép chảy nhƣ trên hình 2.12. Trong thực tế ngƣời ta thƣờng thiết kế cửa khuôn dạng song song. Tuy nhiên do quá trình chế tạo khuôn có sai số và do khuôn có thể bị biến dạng đàn hồi (võng giữa) trong quá trình làm việc dẫn tới vận tốc ra tại cửa khuôn là khác nhau, việc này là rất khó dự đoán trƣớc. a) Cửa khuôn dạng thắt b) Cửa khuôn dạng loe Hình 2.12. Dòng chảy kim loại tại cửa khuôn [58] Vì vậy, nếu muốn sử dụng góc cửa khuôn để kiểm soát dòng chảy thì góc cửa khuôn dạng (+) hay song song nên đƣợc sử dụng vì chúng có thể hiệu chỉnh vận tốc dòng chảy. Cửa khuôn dạng (-) cho áp lực ép chảy thấp, tuy nhiên chúng không thể hiệu chỉnh đƣợc vận tốc dòng chảy. Thƣờng chỉ sử dụng loại cửa khuôn dạng (-) trong trƣờng hợp nó không ảnh gì đến vận tốc thoát tại các điểm khác nhau trên cửa khuôn nhƣ sản phẩm dạng đối xứng hay trong trƣờng hợp vấn đề cân bằng dòng chảy không bị ảnh hƣởng bởi góc nghiêng cửa khuôn. d) Bán kính góc lƣợn cửa khuôn Bán kính góc lƣợn cửa khuôn r khác nhau sẽ ảnh hƣởng đến diện tích tiếp xúc của dòng chảy kim loại với bề mặt cửa khuôn khác nhau. Từ đó làm thay đổi lực ma 46 sát, do đó ảnh hƣởng đến vận tốc ra của sản phẩm. 2.2.3. Thông số hình học vùng dẫn a) Độ rộng vùng dẫn Độ rộng vùng dẫn B (hình 1.15) tăng sẽ làm tăng lƣu lƣợng dòng kim loại, từ đó làm tăng vận tốc dòng chảy ra tại cửa khuôn. Vì vậy để cân bằng dòng chảy, độ rộng vùng dẫn nhôm ở khu vực tâm khuôn phải nhỏ hơn ở khu vực xa tâm khuôn. Độ rộng vùng dẫn nhôm ở khu vực có độ rộng cửa khuôn lớn phải nhỏ hơn độ rộng vùng dẫn nhôm ở khu vực có độ rộng cửa khuôn nhỏ. b) Độ sâu vùng dẫn Khi tăng độ sâu vùng dẫn nhôm H (hình 1.15) tại một vị trí nào đó sẽ làm tăng quãng đƣờng di chuyển của dòng chảy kim loại từ mặt đầu khuôn đến cửa khuôn ở vị trí đó, dẫn tới vận tốc dòng chảy kim loại ra tại vị trí đó chậm hơn so với các vị trí khác. Tuy nhiên việc thay đổi độ sâu vùng dẫn nhôm tại các vị trí khác nhau trên cửa khuôn sẽ gây khó khăn trong quá trình chế tạo khuôn. Vì vậy cần hạn chế thiết kế khuôn có sự thay đổi độ sâu vùng dẫn nhôm tại các vị trí khác nhau. Như vậy, qua phân tích trên cho ta thấy vận tốc ra của dòng chảy kim loại phụ thuộc vào các thông số hình học của khuôn. Để đảm bảo độ chính xác về hình dáng hình học của sản phẩm thì dòng chảy kim loại ra khỏi cửa khuôn phải đƣợc cân bằng (vận tốc dòng chảy kim loại tại các vị trí trên cửa khuôn phải bằng nhau). Hiện nay cân bằng dòng chảy của sản phẩm vẫn dựa chủ yếu vào kinh nghiệm của ngƣời thiết khuôn và chế tạo khuôn. Mỗi bộ khuôn thƣờng phải chỉnh sửa thiết kế sau một vài lần thử khuôn mới đạt đƣợc sự cân bằng dòng chảy. Do đó chi phí cho chế tạo khuôn trong quá trình ép thƣờng cao. Nhƣng với việc ứng dụng các phần mềm chuyên dụng mô phỏng số vào quá trình ép chảy sẽ tìm ra quy luật xác định đƣợc vận tốc dòng chảy ra tại các vị trí khảo sát trên cửa khuôn trong các trƣờng hợp biên dạng cụ thể. Căn cứ vào kết quả mô phỏng số, ngƣời thiết kế khuôn có thể hiệu chỉnh các thông số hình học của khuôn để đạt đƣợc sự cân bằng dòng chảy kim loại thoát ra khỏi cửa khuôn. 47 Vì vậy cần thiết phải ứng dụng phần mềm mô phỏng số để tìm ra kết cấu khuôn hợp lý cho mỗi biện dạng sản phẩm khác nhau đảm bảo cân bằng dòng chảy kim loại. Từ đó đảm bảo độ chính xác về hình dáng hình học của sản phẩm. 2.3. Ảnh hƣởng của một số yếu tố đến độ nhám bề mặt sản phẩm * Cơ sở lý thuyết: Độ nhám bề mặt là một chỉ tiêu đánh giá chất lƣợng sản phẩm ép chảy về mặt thẩm mỹ cũng nhƣ khả năng xử lý nhiệt hay mạ của sản phẩm thanh hợp kim nhôm [58,67]. Độ nhám sản phẩm ép chảy có thể đƣợc phân loại thành các độ nhám vĩ mô và vi mô. Độ nhám vĩ mô đƣợc hình thành bên trong các khu vực quá trình ép chảy và liên quan chặt chẽ đến độ nhám của bề mặt cửa khuôn, độ nhám vi mô nhỏ hơn do sự liên kết tuyến tính của xâm thực xen kẽ với các kết tủa pha kim loại. Độ nhám bề mặt gây ra bởi nguyên nhân chủ yếu là hiện tƣợng bám dính hợp kim nhôm vào bề mặt cửa khuôn nhƣ trên hình 2.13 [50]. Lớp bám dính này không bằng phẳng, do vậy nó sẽ in dập hình dạng của nó lên bề mặt sản phẩm thanh hợp kim nhôm tạo ra nhám bề mặt sản phẩm. Hình 2.13. Bám dính hợp kim nhôm trên bề mặt cửa khuôn [50] 48 Sự phát triển của một lớp bám dính trên bề mặt cửa khuôn phụ thuộc vào nhiều yếu tố: nhiệt độ ở cửa khuôn, vận tốc ra, độ dài cửa khuôn, độ nhám của bề mặt cửa khuôn, vật liệu chế tạo khuôn, vật liệu hợp kim nhôm [58]. Bên cạnh hiện tƣợng bám dính lớp oxit nhôm trên bề mặt cửa khuôn, còn xuất hiện quá trình hình thành các hạt bám dính cào xƣớc lên bề mặt sản phẩm thanh hợp kim nhôm gây ra độ nhám bề mặt sản phẩm [67]. Sự hình thành hạt bám dính phụ thuộc vào các yếu tố chính: Nhiệt độ ép, vận tốc ép, áp lực ép và lớp mặt bám dính tại cửa khuôn [67]. Quá trình hình thành hạt bám dính đƣợc chia làm 4 giai đoạn (hình 2.14) [67] Hình 2.14. Cơ chế hình thành các hạt bám dính [67] (a) giai đoạn khởi đầu; (b) tăng trưởng; (c) tách rời; (d) giai đoạn bám dính 1. Giai đoạn khởi đầu. Lớp Oxit nhôm ở trạng thái chảy dẻo dƣới nhiệt độ và áp lực ép chúng bắt đầu bám dính vào bề mặt thép trên cửa khuôn tạo thành các hạt bám dính nhỏ đƣợc thể hiện trên hình 2.14a. 2. Giai đoạn tăng trƣởng. Tiếp sau đó các lớp kim loại liên tiếp bám dính vào hạt đã hình thành ở giai đoạn thứ nhất, các lớp bám dính kết tinh lại, bề mặt của hạt bị ôxi hóa khá nhanh. Một số hạt có thể sớm bị tách ra khỏi bề mặt cửa khuôn và tan chảy vào 49 sản phẩm khi chúng còn nhỏ. Một số hạt tiếp tục lớn lên có thể đạt hàng trăm μm ở cuối giai đoạn này nhƣ thể hiện trên hình 2.14b. 3. Tách mảng. Khi một số hạt bám dính lớn dần trên bề mặt cửa khuôn đạt chiều cao khoảng 10†30μm, chúng bắt đầu tách ra khỏi bề mặt cửa khuôn, khi đó nó cào xƣớc vào bề mặt sản phẩm, tạo ra vệt nhám trên bề mặt sản phẩm sâu khoảng 1†5 μm. Có hiện tƣợng tăng dần về kích thƣớc từ khi nó bắt đầu tách đến khi chúng tách rời bề mặt cửa khuôn nhƣ thể hiện trên hình 2.14c. 4. Giai đoạn bám dính vào bề mặt sản phẩm. Sau khi tách khỏi bề mặt cửa khuôn, các hạt bám dính chìm một phần vào bề mặt sản phẩm ở cuối mỗi vệt cào xƣớc và một phần nhô lên khỏi bề mặt sản phẩm thanh hợp kim nhôm đƣợc thể hiện nhƣ trên hình 2.14d. Kích thƣớc độ rộng của đầu hạt bám dính thƣờng là 100 ~ 200 μm; độ cao của đầu hạt bám dính là 30 ~ 140 μm và độ cao của phần thấp của hạt thƣờng dƣới 30 μm. Các hạt bám dính bề mặt này ảnh hƣởng xấu đến thẩm mỹ cũng nhƣ chất lƣợng bề mặt của sản phẩm. Các nghiên cứu đã chỉ ra rằng sự gia tăng giá trị độ nhám bề mặt sản phẩm trong quá trình ép chảy có liên quan đến số lƣợng các hạt bám dính bề mặt và chất lƣợng bề mặt cửa khuôn [67]. Nhƣ vậy, qua phân tích trên có thể thấy rằng độ nhám bề mặt sản phẩm ép chảy chủ yếu gây ra bởi lớp bám dính và sự hình thành các hạt bám dính trên bề mặt cửa khuôn. Cả 2 yếu tố này phụ thuộc vào các yếu tố chính nhƣ nhiệt độ ép, vận tốc ép, áp lực ép, bề mặt cửa khuôn và vật liệu hợp kim nhôm. Dựa trên các cơ sở lý thuyết trên có thể phân tích các yếu tố ảnh hƣởng đến độ nhám bề mặt sản phẩm ép chảy nhƣ sau: 2.3.1. Ảnh hƣởng của phôi * Vật liệu phôi Các vật liệu phôi khác nhau cũng ảnh hƣởng đến quá trình hình thành lớp bám dính và các hạt bám dính trên bề mặt cửa khuôn khác nhau. Từ đó ảnh hƣởng đến độ nhám bề mặt của sản phẩm đƣợc thể hiện trên hình 2.15. 50 Theo nhƣ đồ thị ta thấy khi các vật liệu đƣợc bổ sung các nguyên tố Mg, Si, Fe đều làm gia tăng độ nhám bề mặt của sản phẩm. Nguyên tố Si làm tăng độ nhám bề mặt của sản phẩm lớn hơn so với nguyên tố Mg. Đặc biệt vật liệu đƣợc bổ sung nguyên tố Fe làm tăng độ nhám bề mặt của sản phẩm lớn hơn nhiều so với các vật liệu bổ sung nguyên tố Mg, Si [33]. Hình 2.15. Ảnh hưởng của vật liệu phôi đến độ nhám bề mặt sản phẩm [33] 2.3.2. Ảnh hƣởng của khuôn * Độ dài cửa khuôn Độ dài cửa khuôn tăng làm tăng ma sát giữa dòng chảy kim loại với bề mặt cửa khuôn, dẫn tới làm tăng độ dài lớp bám dính và làm tăng nhiệt độ tại cửa khuôn, đồng thời làm thay đổi quá trình hình thành các hạt bám dính, do đó làm thay đổi độ nhám bề mặt sản phẩm. Khi độ dài cửa khuôn giảm gần bằng 0 (khi bề mặt cửa khuôn nghiêng (-)) thì toàn bộ sai số về hình dáng hình học tế vi của bề mặt cửa khuôn sẽ tác động trực tiếp vào bề mặt sản phẩm và làm tăng độ nhám bề mặt sản phẩm [58]. Tuy nhiên, mức độ ảnh hƣởng cụ thể của độ dài cửa khuôn đến độ nhám bề mặt của sản phẩm vẫn ít đƣợc công bố. Do vậy cần thiết phải tiến hành nghiên cứu thực nghiệm thực tế để đánh giá ảnh hƣởng của độ dài cửa khuôn đến độ nhám bề mặt của sản phẩm. 51 * Góc nghiêng cửa khuôn Góc nghiêng cửa khuôn có ảnh hƣởng đến độ nhám bề mặt. Ximao [67] thử nghiệm với góc nghiêng cửa khuôn nhỏ hơn 00 (dạng cửa khuôn (-)), khi đó độ dài cửa khuôn gần bằng 0, đã nhận thấy sự gia tăng nhanh số lƣợng các hạt bám dính trên bề mặt sản phẩm và đồng thời độ nhám bề mặt sản phẩm cũng tăng nhanh. * Độ nhám bề mặt cửa khuôn Độ nhám bề mặt cửa khuôn ảnh hƣởng đến sự hình thành lớp bám dính trên bề mặt cửa khuôn, cũng nhƣ quá trình hình thành các hạt bám dính bề mặt. Độ nhám bề mặt cửa khuôn lớn sẽ làm tăng độ nhám bề mặt sản phẩm khi mới ép ra khỏi cửa khuôn. Sau đó, do hình thành lớp oxit bám dính trên bề mặt cửa khuôn làm cho độ nhám bề mặt sản phẩm ít bị ảnh hƣởng bởi độ nhám ban đầu của cửa khuôn. Ảnh hƣởng của độ nhám bề mặt cửa khuôn đƣợc thể hiện hình 2.16 với hai trƣờng hợp độ nhám cửa khuôn Ra = 0,5†0,75μm và Ra =1,5÷1,75 [33]. Hình 2.16. Ảnh hưởng của độ nhám bề mặt cửa khuôn đến độ nhám bề mặt sản phẩm[33]. Nhìn vào đồ thị hình 2.16 cho thấy độ nhám bề mặt cửa khuôn chỉ ảnh hƣởng đến độ nhám đoạn đầu của sản phẩm. Nhƣng sau đó mức độ ảnh hƣởng của độ nhám bề mặt cửa khuôn đến độ nhám bề mặt sản phẩm là rất nhỏ. * Hƣớng nhám bề mặt cửa khuôn Phƣơng pháp gia công tinh ảnh hƣởng đến hƣớng nhám bề mặt cửa khuôn, từ đó ảnh hƣởng đến sự hình thành lớp bám dính trên bề mặt cửa khuôn, cũng nhƣ quá trình hình thành các hạt bám dính bề mặt, dẫn đến ảnh hƣởng đến độ nhám bề mặt của sản 52 phẩm nhƣ thể hiện trên hình 2.17 với ba trƣờng hợp: bề mặt cửa khuôn đƣợc đánh bóng, bề mặt cửa khuôn đƣợc mài theo phƣơng ngang và theo phƣơng dọc với hƣớng ra của sản phẩm [33]. Nhìn vào hình 2.17 cho thấy đánh bóng bề mặt cửa khuôn dọc theo hƣớng dòng chảy làm tăng chiều dài lớp bám dính, từ đó làm tăng độ nhám bề mặt sản phẩm. Ngƣợc lại đánh đánh bóng bề mặt cửa khuôn theo hƣớng ngang với dòng chảy giúp giảm chiều dài lớp bám dính từ đó giúp làm giảm độ nhám bề mặt sản phẩm. Hình 2.17. Ảnh hưởng của phương pháp gia công tinh bề mặt cửa khuôn đến độ nhám bề mặt sản phẩm ép chảy [33]. * Vật liệu phủ bề mặt cửa khuôn Hình 2.18. Ảnh hưởng của lớp phủ bề mặt cửa khuôn đến độ nhám bề mặt sản phẩm 53 Đặc tính lớp phủ bề mặt cũng ảnh hƣởng lớn đến độ nhám bề mặt sản phẩm khi ép chảy thanh hợp kim nhôm nhƣ đƣợc thể hiện trên hình 2.18 [33] với hai trƣờng hợp: bề mặt cửa khuôn không có lớp phủ và bề mặt cửa khuôn đƣợc phủ lớp thấm nitơ. Các vật liệu phủ lớp bề mặt cửa khuôn khác nhau sẽ ảnh hƣởng đến ma sát giữa bề mặt sản phẩm với bề mặt cửa khuôn, đồng thời cũng ảnh hƣởng đến lớp bám dính oxit trên bề mặt cửa khuôn. Từ đó ảnh hƣởng đến độ nhám bề mặt sản phẩm. Bề mặt đƣợc phủ sẽ giúp làm giảm ma sát, tăng khả năng chống mài mòn cửa khuôn. Hình 2.18 cho thấy bề mặt cửa khuôn đƣợc thấm nitơ sẽ làm giảm sự bám dính trên mặt cửa khuôn so với bề mặt cửa khuôn thông thƣờng, do đó làm giảm độ nhám bề mặt sản phẩm. 2.3.3. Ảnh hƣởng của chế độ ép * Nhiệt độ phôi Khi thay đổi nhiệt độ phôi ép là một thông số quan trọng làm thay đổi lực ma sát cũng nhƣ áp lực ép lên bề mặt cửa khuôn, làm ảnh hƣởng đến quá trình hình thành lớp bám dính bề mặt cũng nhƣ các hạt bám dính bề mặt. Vì vậy độ nhám bề mặt sản phẩm thay đổi [58,67]. Tuy nhiên, do sự ảnh hƣởng phức tạp của nhiệt độ lên quá trình hình thành lớp bám dính trên mặt cửa khuôn cũng nhƣ sự hình thành hạt bám dính. Do vậy, cần thiết phải tiến hành các thực nghiệm thực tế để đánh giá đƣợc quy luật ảnh hƣởng của nhiệt độ ép đến độ nhám bề mặt sản phẩm. * Vận tốc ép Tăng vận tốc ép làm tăng nhiệt dòng chảy đƣợc thể hiện nhƣ trên hình 2.19 dẫn đến làm thay đổi lực ma sát cũng nhƣ áp lực ép lên bề mặt cửa khuôn, làm ảnh hƣởng đến quá trình hình thành lớp bám dính bề mặt cũng nhƣ các hạt bám dính bề mặt nhƣ phân tích ở trên. Đồng thời thay đổi vận tốc ép làm thay đổi đến quá trình hình thành lớp bám dính bề mặt cũng nhƣ các hạt bám dính bề mặt. Từ đó làm thay đổi độ nhám bề mặt sản phẩm. Đây là quá trình phức tạp, cần thiết phải tiến hành các thực nghiệm thực tế để đánh giá đƣợc quy luật ảnh hƣởng của vận tốc ép đến độ nhám bề mặt sản phẩm. 54 Hình 2.19. Ảnh hưởng của vận tốc ép đến nhiệt độ bề mặt sản phẩm [58] Như vậy qua những phân tích trên cho ta thấy được mức độ ảnh hưởng khác nhau của các yếu tố đến độ nhám bề mặt sản phẩm của quá trình ép: Đối với phôi trong quá trình ép: vật liệu phôi thƣờng đƣợc lựa chọn theo yêu cầu kỹ thuật của sản phẩm do đó phải chấp nhận mức độ ảnh hƣởng của vật liệu phôi đến độ nhám bề mặt sản phẩm. Độ dài phôi đƣợc xác định theo độ dài sản phẩm và giới hạn của độ dài buồng ép của máy ép, do vậy sự thay đổi độ dài phôi trong sản xuất thực tế là rất ít. Đƣờng kính phôi phụ thuộc vào các kích thƣớc đƣờng kính tiêu chuẩn của nhà máy sản xuất phôi và đƣờng kính buồng ép, do vậy thực tế ngƣời ta ít thay đổi đƣờng kính phôi trong quá trình ép. Vì vậy tác giả không đi sâu nghiên cứu về ảnh hƣởng của phôi đến độ nhám bề mặt sản phẩm. Đối với khuôn ép: góc nghiêng cửa khuôn trong quá trình chế tạo khuôn thực tế thƣờng là góc 0o để dễ chế tạo trong quá trình cắt dây tia lửa điện cửa khuôn và đảm bảo vấn đề có thể sửa khuôn khi có sai số trong quá trình chế tạo nhằm cân bằng dòng chảy kim loại. Quá trình chế tạo khuôn thực tế, bề mặt cửa khuôn chủ yếu phải đánh bóng với độ nhám bề mặt rất nhỏ, do đó độ nhám bề mặt cửa khuôn và hƣớng độ nhám bề mặt cửa khuôn ít thay đổi. Sử dụng các vật liệu phủ bề mặt cửa khuôn khác nhau sẽ ảnh hƣởng đến độ nhám bề mặt sản phẩm khác nhau, nhƣng giá thành chế tạo khuôn cũng khác nhau. Nhà sản xuất phải cân nhắc lựa chọn vật liệu phủ đảm bảo giá thành với chất lƣợng bề mặt sản phẩm. 55 Thông số độ dài cửa khuôn là dễ thay đổi khi thiết kế và chế tạo khuôn, do vậy cần đi sâu nghiên cứu thực nghiệm sự ảnh hƣởng độ dài cửa khuôn đến độ nhám bề mặt sản phẩm để xác định đƣợc độ dài cửa khuôn hợp lý. Đối với chế độ ép: Cả 2 thông số nhiệt độ phôi ép, vận tốc ép đều có thể thay đổi trong quá trình ép, do vậy cần phải đi sâu nghiên cứu thực nghiệm ảnh hƣởng của 2 thống số này đến độ nhám bề mặt sản phẩm để từ đó lựa chọn đƣợc chế độ ép hợp lý của quá trình ép. Cả 3 thông số nhiệt độ phôi, vận tốc ép và độ dài cửa khuôn đều có sự hảnh hƣởng đến lực ma sát dòng chảy với bề mặt cửa khuôn, từ đó ảnh hƣởng đến áp lực ép. Áp lực ép lên bề mặt cửa khuôn là một yếu tố ảnh hƣởng đến quá trình hình thành lớp bám dính và hạt bám dính bề mặt [67], do đó có sự ảnh hƣởng đến độ nhám bề mặt sản phẩm ép chảy. Mặt khác áp lực ép cũng gây ra biến dạng cửa khuôn [50], làm ảnh hƣởng đến tuổi bền của khuôn, lực ép của máy ép, độ chính xác tiết diện sản phẩm. Do vậy cần thiết phải tiến hành nghiên cứu ảnh hƣởng của 3 thống số này đến áp lực ép. Kết luận chƣơng 2. Qua phân tích nội dung chƣơng 2 rút ra một số kết luận sau: 1. Độ chính xác về hình dáng hình học và độ nhám bề mặt là những chỉ tiêu quan trọng đánh giá chất lƣợng thanh hợp kim nhôm ép chảy. 2. Các thông số hình học của khuôn có sự ảnh hƣởng đến tốc độ ra của sản phẩm. Do đó cần tiến hành nghiên cứu ứng dụng mô phỏng số để đánh giá đƣợc mức độ ảnh hƣởng của từng thông số hình học khuôn đến vận tốc dòng chảy kim loại, làm cơ sở để cân bằng dòng chảy khi thiết kế khuôn cho sản phẩm hợp kim nhôm cụ thể (tiết diện 70x5 mm, vật liệu 6061) đảm bảo độ chính xác về hình dáng hình học sản phẩm. Đây là bƣớc cần thiết trƣớc khi tiến hành chế tạo khuôn để thực hiện các nghiên cứu tiếp theo trong quá trình ép chảy sản phẩm thực tế. Nội dung này đƣợc trình bày trong chƣơng 3 của luận án. 3. Có 3 thông số ảnh hƣởng lớn đến độ nhám bề mặt sản phẩm thanh hợp kim nhôm và áp lực ép. Do vậy cần tiến hành nghiên cứu thực nghiệm ảnh hƣởng của 3 thông số này đến độ nhám bề mặt sản phẩm ép và áp lực ép để xác định chế độ ép và chiều dài cửa khuôn hợp lý nhằm đảm bảo độ nhám bề mặt sản phẩm và hiệu quả sử dụng thiết bị. Nội dung này đƣợc trình bày trong chƣơng 4 của luận án. 56 CHƢƠNG 3: NGHIÊN CỨU ẢNH HƢỞNG CỦA THÔNG SỐ HÌNH HỌC KHUÔN ĐẾN ĐỘ CHÍNH XÁC HÌNH DÁNG HÌNH HỌC SẢN PHẨM BẰNG MÔ PHỎNG SỐ 3.1. Xây dựng mô hình mô phỏng số 3.1.1. Mô phỏng số Mô phỏng số là quá trình giải mô hình cơ lý của bài toán đƣợc biểu diễn dƣới các phƣơng trình vi phân toán học kết hợp với các điều kiện biên cụ thể bằng các phƣơng pháp số (phƣơng pháp phần tử hữu hạn). Mục đích của phƣơng pháp là nhà t
File đính kèm:
luan_an_nghien_cuu_anh_huong_cua_mot_so_thong_so_hinh_hoc_kh.pdf
Thông tin luận án - tiếng anh.doc
Thông tin luận án - tiếng anh.pdf
Thông tin luận án - tiếng việt.doc
Thông tin luận án - tiếng việt.pdf
Tóm tắt luận án (Tiếng Anh).pdf
Tóm tắt luận án (Tiếng Việt).pdf