Luận án Nghiên cứu ảnh hưởng của một số yếu tố công nghệ đến mòn đá và chất lượng bề mặt chi tiết khi mài định hình rãnh tròn xoay
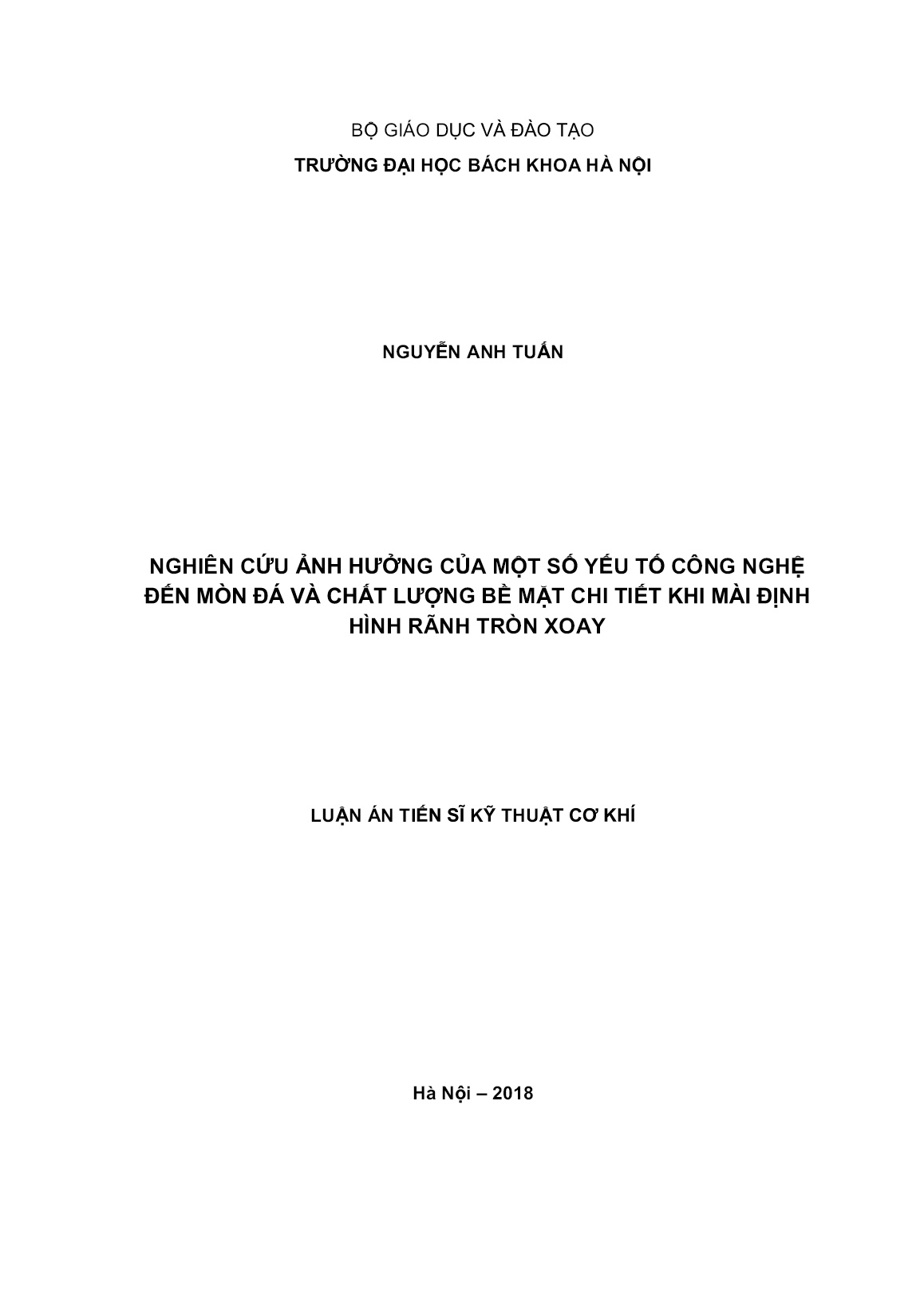
Trang 1
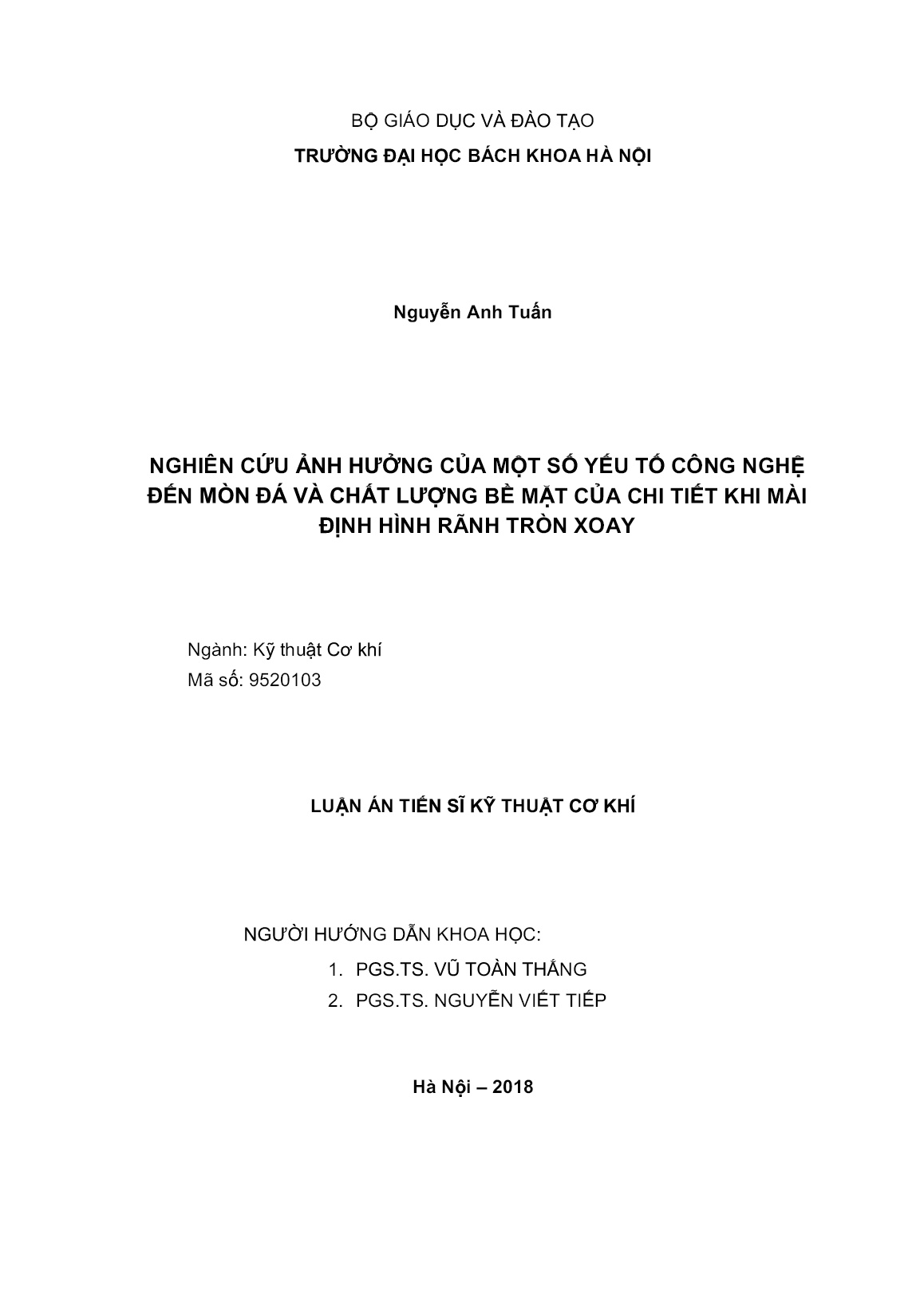
Trang 2
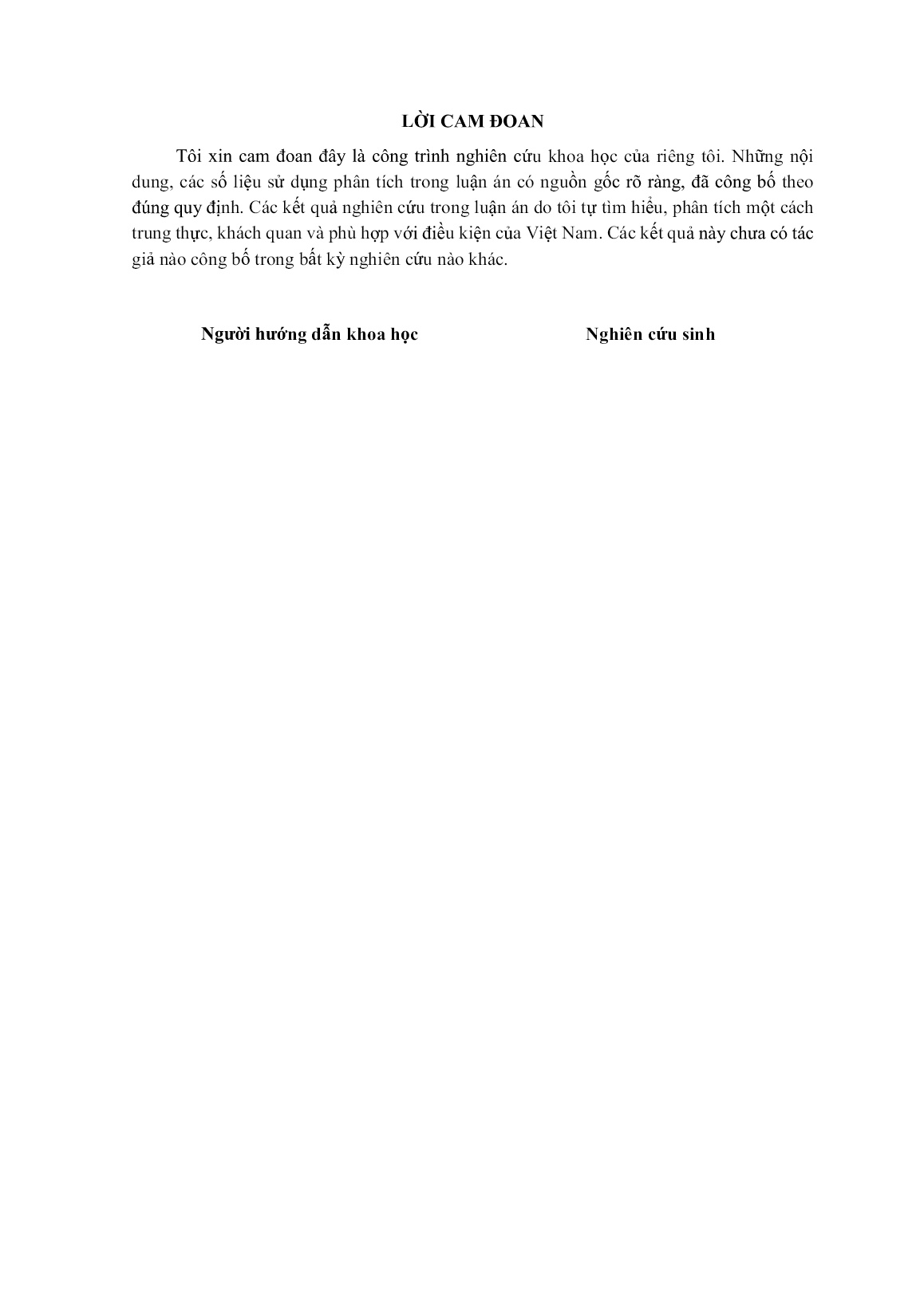
Trang 3
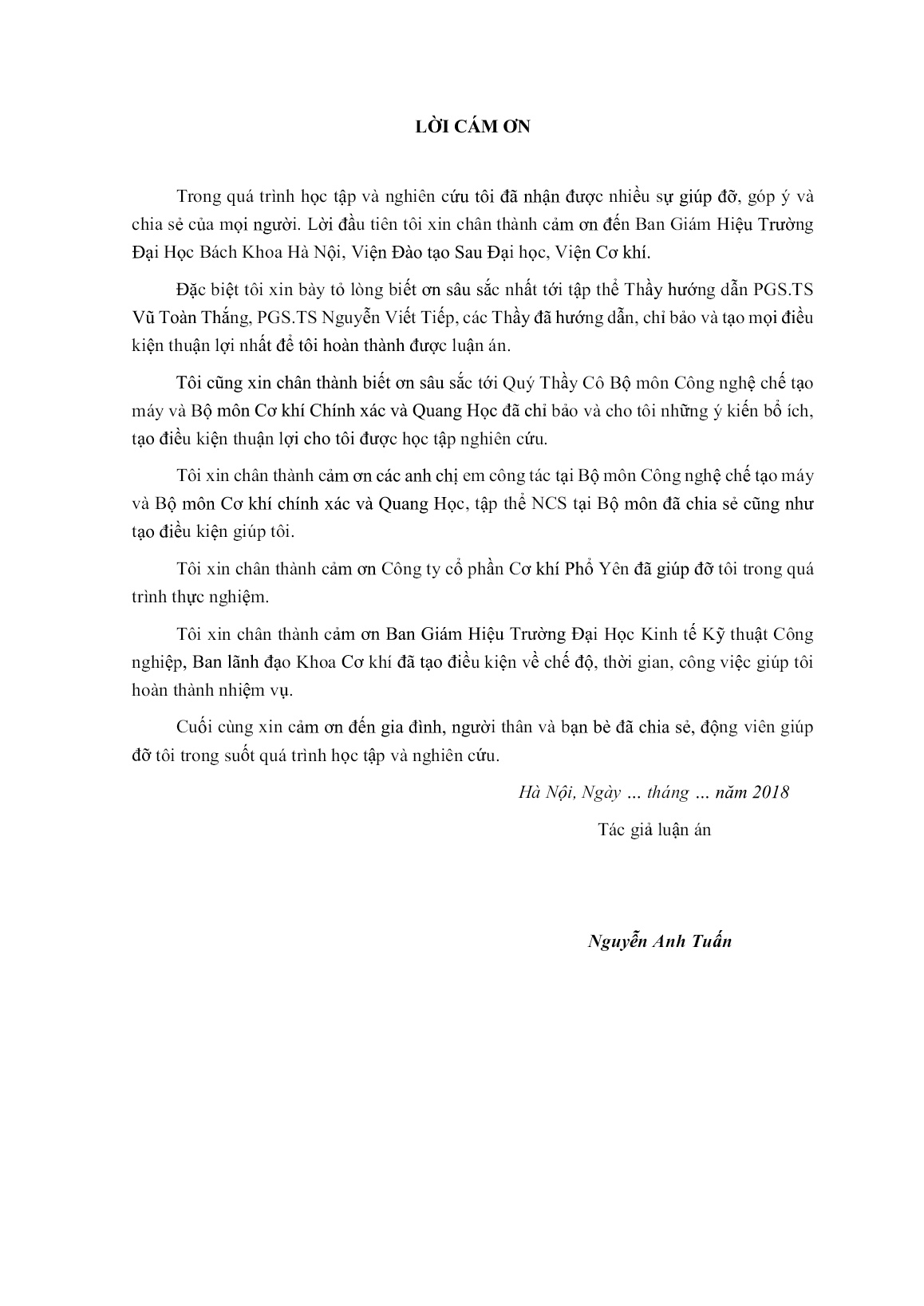
Trang 4
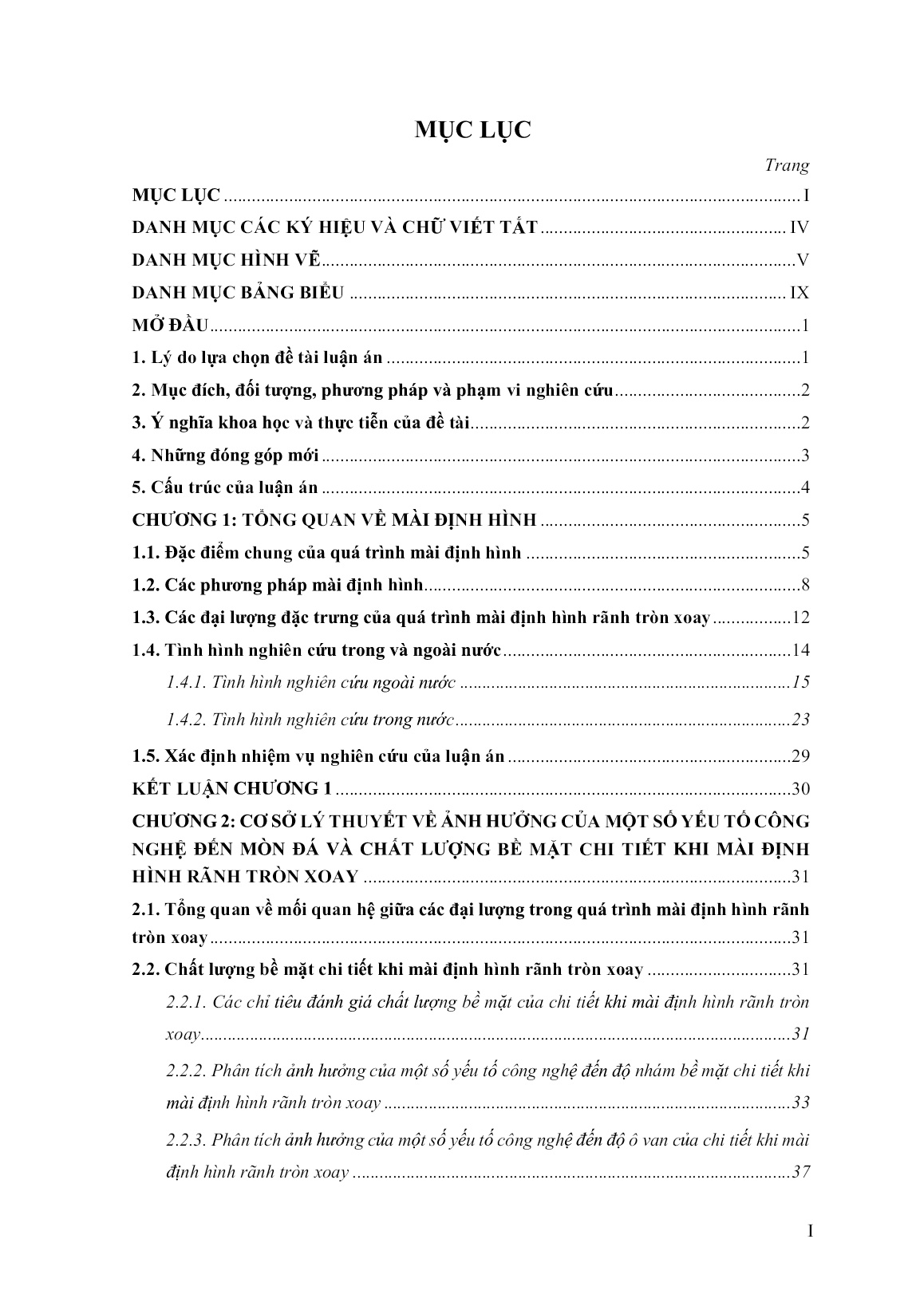
Trang 5
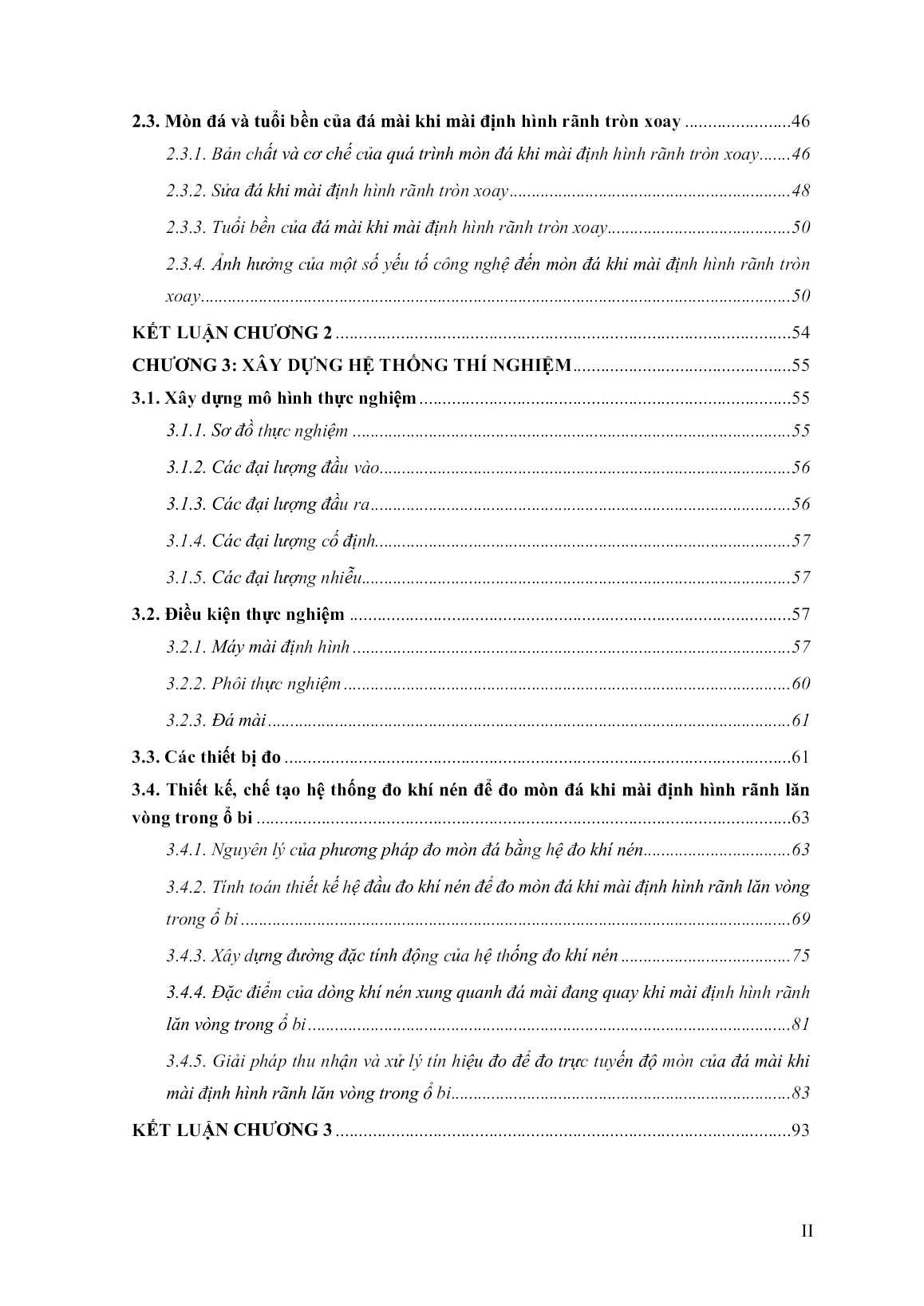
Trang 6
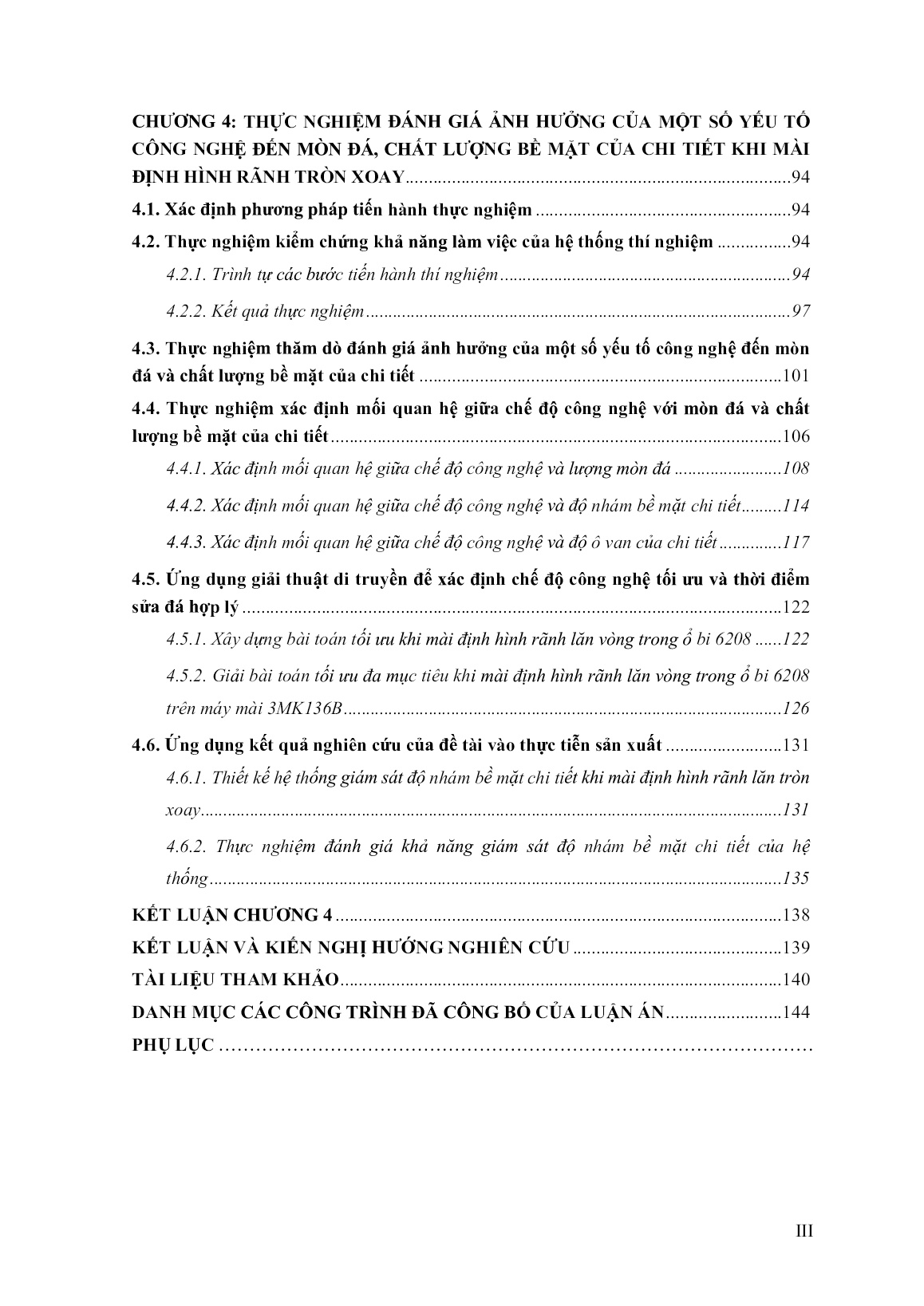
Trang 7
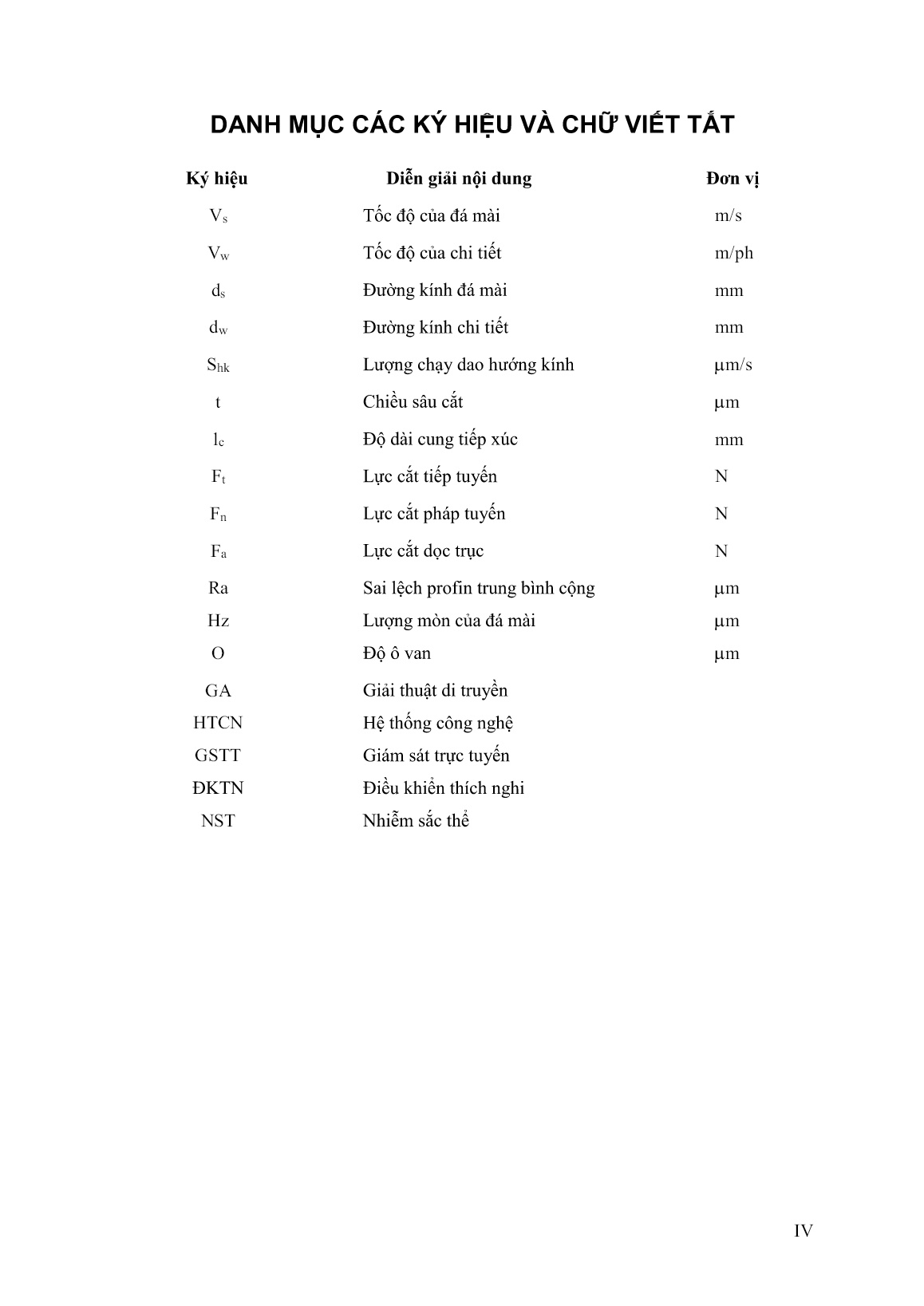
Trang 8
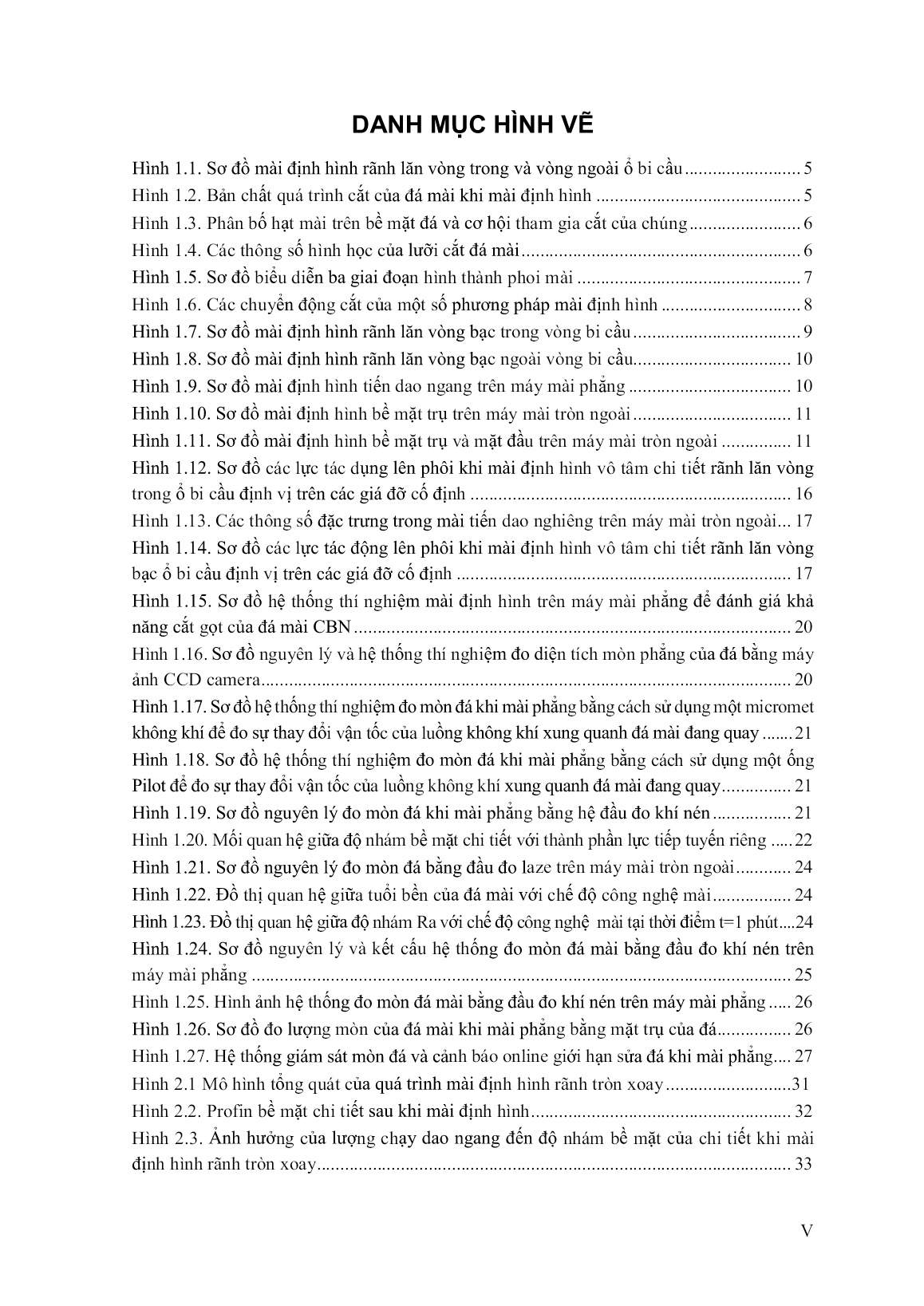
Trang 9
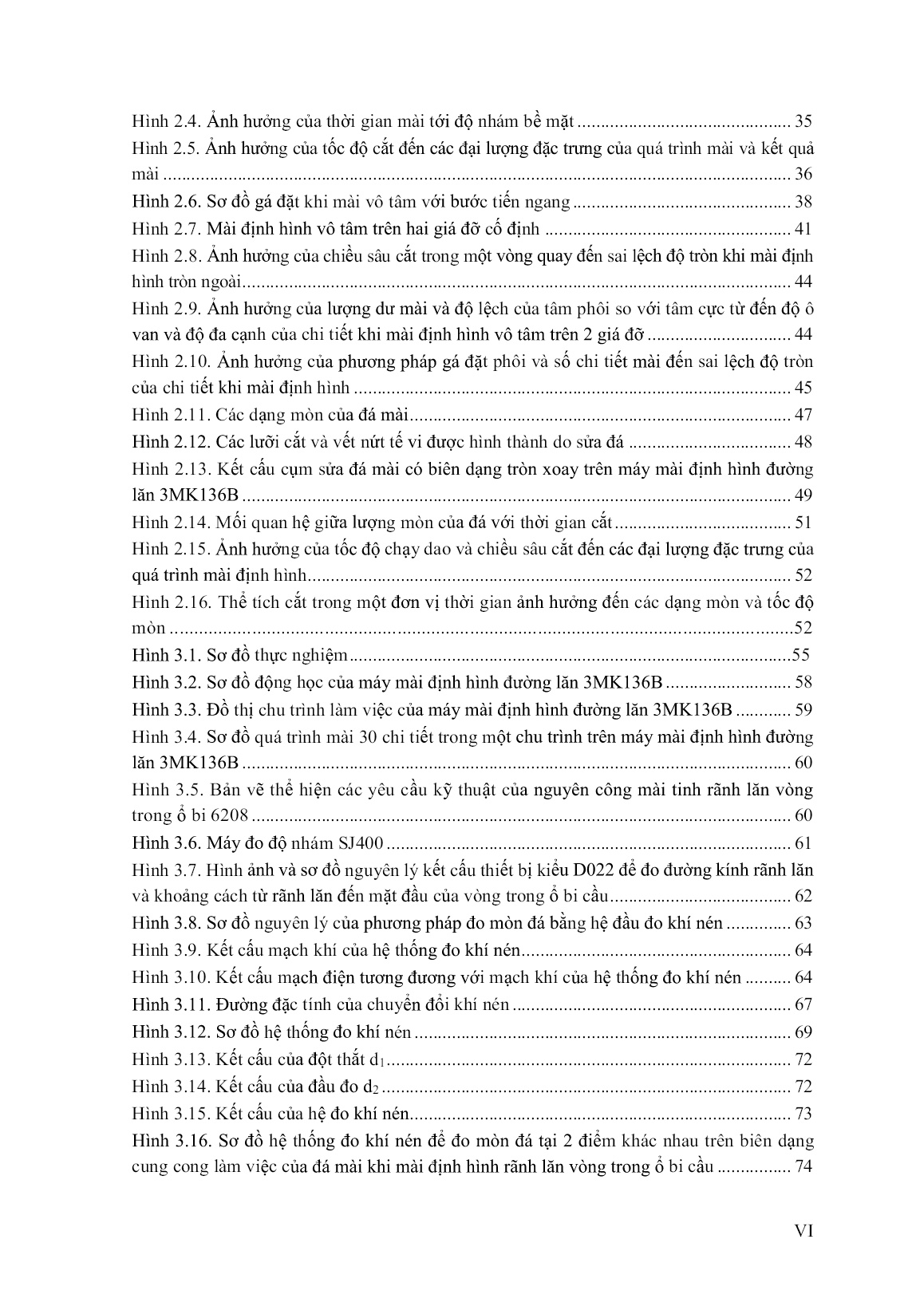
Trang 10
Tải về để xem bản đầy đủ
Bạn đang xem 10 trang mẫu của tài liệu "Luận án Nghiên cứu ảnh hưởng của một số yếu tố công nghệ đến mòn đá và chất lượng bề mặt chi tiết khi mài định hình rãnh tròn xoay", để tải tài liệu gốc về máy hãy click vào nút Download ở trên.
Tóm tắt nội dung tài liệu: Luận án Nghiên cứu ảnh hưởng của một số yếu tố công nghệ đến mòn đá và chất lượng bề mặt chi tiết khi mài định hình rãnh tròn xoay
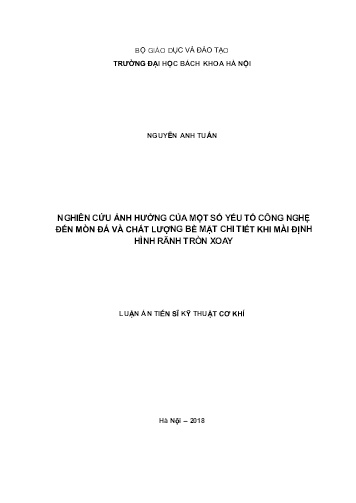
n chỉ đánh giá được lượng mòn tại một vùng diện tích rất nhỏ có thể coi như một điểm. Vì vậy, để Chú thích hình 3.15: đánh giá được lượng mòn của đá mài khi mài định 1. Panme 0:25 7. Đầu thổi d2 hình rãnh lăn tròn xoay vòng trong ổ bi 6208 cần 2. Chốt tỳ 8. Lò xo sử dụng hai hệ đo khí nén để đo mòn đồng thời 3. Bạc đỡ 9. Then tại hai điểm có lượng chênh lệnh mòn lớn nhất 4. Trục trung gian 10. Bulong M5 (tại điểm đỉnh biên dạng cung cong đá mài và tại 5. Đột thắt d1 11. Bạc bắt panme điểm mép biên dạng cung cong của đá mài) như 6. Bạc đỡ hệ đầu đo thể hiện trên hình 3.16. Xuất phát từ sơ đồ nguyên lý mài định hình rãnh lăn vòng trong ổ bi cầu nhận thấy biên dạng của đá mài phải giống với biên dạng của bề mặt rãnh lăn tròn xoay cần mài. Do đó, từ yêu cầu kích thước của bề mặt rãnh lăn cần gia công sẽ xác định được chiều cao và bán kính biên dạng cung cong làm việc của đá mài. Trên cơ sở đó, tâm biên dạng cung cong làm việc của đá mài sẽ dễ dàng được xác định. Vì vậy, căn cứ vào không gian thực tế của máy đặc biệt là không gian của hộp che đá trên máy sẽ xác định được vị trí gá đặt của từng hệ đầu đo cần gá đặt trên máy như hình 3.16. Ngoài ra, để xác định chính xác khoảng dịch chuyển của đầu đo d2 trong mỗi hệ đầu đo so với tâm biên dạng cung cong làm việc của đá 73 mài (khe hở z) thì ở đây sử dụng đuôi panme số 05 và đồng hồ so điện tử số 06. Trong đó đuôi panme số 05 dùng để điều chỉnh khoảng khe hở z, đồng hồ so số 06 dùng để xác định khoảng cách khe hở z. 05 06 07 Mitutoyo 0.001 04 08 09 10 Mitutoyo 0.001 03 Z 02 R d 01 Hình 3.16. Sơ đồ hệ thống đo khí nén để đo mòn đá tại 2 điểm khác nhau trên biên dạng cung cong làm việc của đá mài khi mài định hình rãnh lăn vòng trong ổ bi cầu Chú thích hình 3.16: 1: Đá mài 2: Đầu đo d2 3: Đột thắt d1 4: Hệ đầu đo thứ nhất (đầu đo thẳng) 5: Đuôi panme 6: Đồng hồ so điện tử của Mitutoyo 7: Hệ đầu đo thứ hai (Đầu đo nghiêng) 8: Tấm bắt đồng hồ so 9: Thanh đo 10: Tấm bắt thanh đo Từ đó nhận thấy cần thiết kế được bộ đồ gá chuyên dùng để gá lắp dễ dàng hệ đầu đo lên máy mài đảm bảo được độ cứng vững của hệ đo trong quá trình máy mài đang làm việc. Đồng thời, bộ đồ gá này cũng cần đảm bảo việc điều chỉnh dễ dàng để đường tâm của đầu đo d2 đi qua tâm biên dạng cung cong làm việc của đá mài để khí nén thổi ra từ đầu đo d2 theo phương vuông góc với bề mặt cần đo. 74 Xuất phát từ các yêu cầu trên nhận thấy với mỗi hệ đầu đo khí nén đo mòn ở đỉnh và ở mép biên dạng cung cong làm việc của đá mài cần có các cơ cấu dịch chuyển theo phương dọc và phương ngang như thể hiện trên hình 3.17, hình 3.18. Trong đó, để thực hiện dịch chuyển tịnh tiến các hệ đầu đo theo một phương nhất định ở đây lựa chọn sử dụng cơ cấu điều chỉnh bằng mang cá. Nguyên nhân là vì kết cấu của cơ cấu điều chỉnh này đơn giản, dễ chế tạo mà vẫn đảm bảo được độ chính xác yêu cầu. Kết cấu của cơ cấu điều chỉnh bằng mang cá gồm 4 chi tiết chính: Mang cá tĩnh, mang cá động, tấm căn điều chỉnh và trục vítme. Để xác định được các thông số kích thước của từng chi tiết trong các cụm mang cá điều chỉnh ở trên cần căn cứ vào không gian làm việc thực tế của máy mài định hình đường lăn 3MK136B, đặc biệt là không gian của hộp che đá và kết hợp với việc tra sổ tay công nghệ chế tạo máy. 3.4.3. Xây dựng đường đặc tính động của hệ thống đo khí nén Căn cứ vào cơ sở lý thuyết và nguyên lý của phương pháp đo mòn đá bằng hệ thống đo khí nén nhận thấy: Trong quá trình đo mòn đá bằng hệ đo khí nén, từ giá trị áp suất của buồng đo xác định được nhờ cảm biến áp suất muốn tìm ra được khoảng cách khe hở z thì cần căn cứ vào tỷ số truyền hay độ nhạy của hệ đầu đo. Do đó, sau khi đã tính toán được các thông số của hệ đầu đo và thiết kế được hệ đầu đo thì một trong những yêu cầu quan trọng đặt ra để đảm bảo độ chính xác của phép đo là cần xác định được chính xác độ nhạy hay tỷ số truyền thực tế của hệ đầu đo. Vì vậy cần phải xây dựng được phương trình và đường đặc tính của hệ đầu đo. Như phân tích ở phần trước nhận thấy khi tính toán các thông số của hệ đo khí nén thì tỷ số truyền lý thuyết của đầu đo đã được xác định. Tuy nhiên, khi thực hiện gia công chế tạo đột thắt d1 và đầu thổi d2 luôn có sai số. Ngoài ra, khi gá lắp hệ đo khí nén lên máy mài để đo mòn đá do ảnh hưởng của các yếu tố xuất hiện trong quá trình mài như ảnh hưởng của phoi mài, ảnh hưởng của dung dịch trơn nguội, ảnh hưởng sự nhấp nhô của bề mặt làm việc đá mài, ảnh hưởng độ cong bề mặt làm việc của đá mài định hình, ảnh hưởng sự chuyển động của đá trong quá trình mài sẽ làm cho đường đặc tính động của hệ đầu đo có thể sẽ khác so với đường đặc tính lý thuyết của hệ đầu đo [32]. Vì vậy, việc xác định đường đặc tính động của hệ đầu đo bằng thực nghiệm sau khi chế tạo và gá lắp hệ đầu đo lên máy mài là một khâu vô cùng quan trọng trong việc thiết kế chế tạo hệ đo khí nén. Điều này sẽ quyết định đến độ chính xác của phép đo độ mòn. Do đó, cần tiến hành thực nghiệm để xây dựng mối quan hệ giữa khe hở z với áp suất p sau khi đã chế tạo, gá đặt hệ đầu đo lên máy và điều chỉnh máy để đá mài ở trạng thái quay với vận tốc như khi mài, đồng thời đã thực hiện tưới dung dịch trơn nguội. Muốn vậy, trước tiên cần phải xác định được sơ đồ hệ thống đo và trang thiết bị trong hệ thống đo khí nén để đo mòn đá khi mài định hình rãnh lăn vòng trong ổ bi 6208 trên máy mài định hình đường lăn vòng bạc ổ bi 3MK136B. 3.4.3.1. Sơ đồ hệ thống đo khí nén khi mài định hình rãnh lăn vòng trong ổ bi Để xây dựng đường đặc tính động hệ đo khí nén, một máy mài định hình đường lăn 3MK136B được sử dụng trong thí nghiệm. Hình 3.17 thể hiện hình ảnh thực tế của hệ đầu 75 đo sau khi được gá lắp lên máy mài. Hình 3.18 thể hiện sơ đồ và đồ họa 3D của hệ thống thí nghiệm. Dòng khí nén đi vào Dòng khí nén từ buồng 27 29 28 09 29 28 trong hệ đầu đo đo ra cảm biến áp suất 07 19 08 a) b) 03 02 23 01 24 c) 0 d) 8 08 26 Hộp che đá 06 08 20 25 Hình 3.17. Hình ảnh thực tế của hệ thống đo khí nén sau khi được gá lắp lên trên máy mài định hình đường lăn 3MK136B a) Hình ảnh nhìn từ phía đằng trước b) Hình ảnh nhìn cận cảnh hai đầu thổi d2 c) Hình ảnh nhìn cận cảnh hai đầu đo d) Hình ảnh nhìn từ phía đằng sau 76 30 Máy Air nén compressorkhí 29 28 27 Air supply Air 01 23 26 02 Mitutoyo 25 0.001 03 04 22 24 21 Mitutoyo 0.001 05 06 Z 07 R d 20 08 19 11 09 10 12 AC-220V CPressureảm biến CPressureảm biến ápSensor suất ápSensor suất DC-12V a) Hình 3.18. Sơ đồ và đồ họa 3D của hệ thống thí nghiệm đo mòn đá khi mài định hình rãnh lăn vòng trong ổ bi 6208 a) Sơ đồ của hệ thống thí nghiệm b) Đồ họa 3D của hệ thống thí nghiệm Chú thích hình 3.17 và hình 3.18: 1. Đuôi panme của đầu đo thẳng; 2. Bộ mang cá để điều chỉnh đầu đo thẳng dịch chuyển theo phương dọc; 3. Bộ mang cá để điều chỉnh đầu thẳng dịch chuyển theo phương ngang; 4. Lò xo; 5. Đột thắt d1; 6. Hệ đầu đo đo mòn ở đỉnh biên dạng cung cong của đá mài (đầu đo thẳng hay đầu đo thứ nhất); 7. Đầu đo d2 của hệ đầu đo thẳng; 8. Đá mài định hình tròn xoay; 9. Cảm biến áp suất đo áp suất buồng đo của đầu đo thẳng; 10. Bộ đổi nguồn Adapter DC-12V để cấp nguồn điện một chiều cho cảm biến áp suất; 11. Nguồn điện 220 V; 12. Cảm biến áp suất đo áp suất buồng đo của đầu đo nghiêng; 19. Đầu đo d2 của hệ đầu đo nghiêng; 20. Hệ đầu đo đo mòn ở mép biên dạng cung cong của đá mài (đầu đo nghiêng hay đầu đo thứ hai); 21. Tấm bắt thanh đo; 22. Thanh đo; 23. Đồng hồ so điện tử của Mitutoyo; 24. Đĩa phân độ đầu đo nghiêng; 25. Đuôi panme của đầu đo nghiêng; 26. Bộ mang cá đầu đo nghiêng để điều chỉnh đầu đo theo phương hướng kính. 27. Cảm biến áp suất đo áp suất nguồn khí nén đầu vào; 28. Van điều áp chính xác; 29. Bộ lọc khí; 30. Máy nén khí. 77 3.4.3.2. Trang thiết bị trong hệ thống đo khí nén để đo mòn đá khi mài định hình rãnh lăn vòng trong ổ bi - Cảm biến áp suất SEU-31-N của hãng Pisco với các thông số kỹ thuật như thể hiện trong bảng 3.4. - Đá mài 500x8x203WA100xLV60. Các đặc tính kỹ thuật của đá mài được thể hiện như trong bảng 3.5. Bảng 3.4. Các đặc tính kỹ thuật của cảm biến Bảng 3.5. Các thông số thể hiện đặc tính kỹ áp suất SEU-31-N [50] thuật của đá mài Phạm vi đo 0÷10 bar Ký hiệu đá: 500x8x203WA100xLV60 Độ phân giải 0,01 bar Vật liệu hạt mài: Coranh đông trắng Độ hạt : 100 Chất dính kết: Gốm Độ cứng của đá mài: Mềm (MV2) Kích thước đá: 500x8x203 Tốc độ đá : 60 m/s - Máy mài: Thí nghiệm được thực hiện trên máy mài định hình đường lăn vòng trong ổ bi 3MK136B. Các thông số kỹ thuật chính của máy như trong bảng 3.1. 3.4.3.3. Các bước xây dựng đường đặc tính động của hệ thống đo khí nén Việc xây dựng đường đặc tính động của hệ thống đo khí nén được thực hiện theo trình tự các bước như sau: - Bước 1: Lần lượt thực hiện gá lắp hệ đầu đo ở đỉnh biên dạng cung cong đá mài và gá lắp hệ đầu đo ở mép biên dạng cung cong đá mài lên trên máy mài định hình đường lăn vòng trong ổ bi như thể hiện trên hình 3.17 và hình 3.18. Đầu tiên, thực hiện điều chỉnh để áp suất nguồn P = 4 bar. Sau đó, thực hiện điều chỉnh máy để đá mài quay với vận tốc (60 m/s) và thực hiện tưới dung dịch trơn nguội để điều kiện thí nghiệm xây dựng đường đặc tính động giống như khi đang mài. Tiếp theo, tiến hành sửa đá. Việc thực hiện sửa đá ở đây rất quan trọng vì điều này sẽ tạo cho viên đá tròn và có biên dạng giống với biên dạng định hình của chi tiết cần mài. Cuối cùng, lần lượt thực hiện điều chỉnh đầu đo d2 ở từng hệ đầu đo sao cho nguồn khí nén có áp suất không đổi thổi liên tục theo phương vuông góc với bề mặt làm việc của đá mài, đường tâm của đầu đo d2 phải có phương đi qua tâm biên dạng cung cong làm việc của đá mài như đã trình bày ở phần trước. - Bước 2: Lần lượt thực hiện điều chỉnh để đầu đo d2 ăn dao hướng kính vào bề mặt làm việc của đá mài đối với từng hệ đầu đo. Ví dụ, với hệ đầu đo thẳng thì tiến hành vặn đuôi panme số 1 từ từ và đều tay theo chiều kim đồng hồ, làm chi tiết chốt tì và trục di động cùng với toàn bộ hệ đầu đo gồm đột thắt d1 số 5, đầu đo d2 số 7 sẽ dịch chuyển tịnh tiến từ từ xuống phía dưới để đầu đo d2 số 7 từ từ tiến theo phương hướng kính cắt vào bề mặt đá mài nhằm mục đích tạo ra ở mặt đầu của đầu thổi d2 một mặt cong có biên dạng giống với biên dạng làm việc của đá mài định hình để khi hệ đầu đo làm việc thì khí thổi ra từ đầu đo d2 sẽ được chảy tập trung trên một bề mặt có biên dạng giống với biên dạng bề mặt làm việc 78 của đá mài định hình trong một khoảng khe hở z rất nhỏ giữa mặt đầu của đầu đo d2 và bề mặt làm việc của đá mài. Điều này sẽ giúp cho hệ đầu đo làm việc được tốt hơn, đầu đo sẽ phát hiện được những thay đổi rất nhỏ ở các đỉnh lưỡi cắt của hạt mài khi các đỉnh lưỡi cắt của hạt mài bị cùn đi hoặc khi các hạt mài bị vỡ ra thành các mảnh nhỏ hoặc khi cả hạt mài bị bật ra khỏi chất dính kết do ma sát hoặc lực cắt gây ra trong quá trình mài. Sau đó, xoay đầu Panme để điều chỉnh đầu đo d2 ở mỗi hệ đầu đo cách xa khỏi bề mặt đá. - Bước 3: Lần lượt xoay đầu Panme để thực hiện điều chỉnh vị trí của đầu đo d2 ở từng hệ đầu đo tiếp xúc với bề mặt làm việc của đá mài (ứng với vị trí khe hở z = 0). Khi đó quan sát sẽ thấy có hoa lửa xuất hiện và nếu tiếp tục điều chỉnh đầu đo d2 tiến dao hướng kính vào bề mặt đá thì trị số áp suất p của buồng đo cũng sẽ không thay đổi vì lúc này mặt đầu của đầu đo d2 sẽ áp sát vào biên dạng cung cong làm việc của đá mài. Thời điểm này thực hiện ghi lại trị số áp suất buồng đo ở từng hệ đầu đo. Nhận thấy, đây chính là áp suất buồng đo ứng với khe hở z = 0. - Bước 4: Tiếp đó bằng cách vặn đầu Panme để có thể điều chỉnh được vị trí của đầu đo so với bề mặt làm việc của đá mài đi từng khoảng nhỏ một ở từng hệ đầu đo. Với giới hạn của điều kiện thí nghiệm, độ phân giải của panme ở đây chỉ là 0,01 mm nên để đảm bảo độ dịch chuyển chính xác của đầu đo đến từng micromet thì ở đây sẽ gá lắp lên mỗi hệ đầu đo một đồng hồ so điện tử Mitutoyo có độ chính xác 0,001 mm như thể hiện trên hình 3.17 và hình 3.18. Chân của đồng hồ so điện tử sẽ luôn luôn tiếp xúc và dịch chuyển cùng với một thanh đo (Ví dụ với hệ đầu đo thẳng thì đó là chi tiết thanh đo 22). Thanh đo này được gắn cứng với phần dịch chuyển đầu đo d2 của hệ đầu đo bằng một tấm bắt thanh đo (Ví dụ với hệ đầu đo thẳng thì đó là chi tiết tấm bắt thanh đo 21). Vì vậy khi xoay đầu panme thì sẽ làm cho đầu đo d2 của hệ đầu đo cùng với thanh đo dịch chuyển. Đầu đo d2 của hệ đầu đo dịch chuyển một lượng bao nhiêu thì thanh đo cũng dịch chuyển một lượng bấy nhiêu, cho nên trị số hiển thị trên đồng hồ so gắn vào hệ đầu đo cũng sẽ thay đổi một lượng như vậy tức hiển thị đúng lượng dịch chuyển của đầu đo d2. Ban đầu điều chỉnh để khe hở z = 0 như ở bước 3, tại vị trí này để đồng hồ so điện tử hiển thị giá trị bằng 0. Khi đó bằng cách vặn đuôi panme và đọc trị số trên đồng hồ so điện tử sẽ có thể thực hiện điều chỉnh vị trí của đầu đo d2 ở từng hệ đầu đo đi từng micromet một so với bề mặt làm việc của đá mài. Vì vậy, tại mỗi vị trí dịch chỉnh đi từng micromet một của đầu đo d2 ở từng hệ đầu đo sẽ ghi nhận được giá trị áp suất p tương ứng hiển thị trên sensor áp suất của buồng đo, từ đó sẽ xây dựng được một bảng kết quả thực nghiệm về mối tương quan giữa áp suất p của buồng đo và khe hở z ở từng hệ đầu đo như trong bảng kết quả thực nghiệm ở phụ lục 1. Trong quá trình thực nghiệm luôn luôn phải giữ áp suất nguồn không đổi P = 4 bar bằng điều áp chính xác. 3.4.3.4. Kết quả đo và xây dựng đường đặc tính động của hệ thống đo khí nén Từ bảng kết quả thực nghiệm xây dựng được về mối tương quan giữa áp suất p của buồng đo với khe hở z ở phần trước, áp dụng phương pháp quy hoạch thực nghiệm bình phương cực tiểu với dạng phương trình mối quan hệ đã xây dựng được ở phần trước là: P p 1 az22 79 Từ đó, ứng dụng phần mềm Matlab sử dụng chương trình trong phụ lục 13 sẽ xây dựng được một hàm toán học và đồ thị biểu diễn mối quan hệ giữa áp suất p và khe hở z, tức là xây dựng được đường đặc tính động của mỗi hệ thống đầu đo như hình 3.19, hình 3.20. Đường đặc tính động của hệ đầu đo khí nén đo mòn ở đỉnh biên dạng cung cong làm việc của đá mài Đường đặc tính động của hệ đầu đo khí nén đo mòn t p (bar) ấ ở mép biên dạng cung cong làm việc của đá mài Áp su Khe hở z (m) Hình 3.19. Đường đặc tính động của hệ đo khí nén trên toàn miền từ 0÷4 bar sau khi được gắn lên trên máy mài đo mòn tại điểm đỉnh và điểm mép của biên dạng cung cong đá mài Đường đặc tính động của hệ đầu đo khí nén đo mòn ở đỉnh biên dạng cung cong làm việc của đá mài Đường đặc tính động của hệ đầu đo khí nén đo mòn ở mép biên dạng cung cong làm việc của đá mài t p (bar) ấ Áp su Khe hở z (m) Hình 3.20. Đường đặc tính động của hệ đo khí nén trên miền làm việc thực của đầu đo sau khi được gắn lên trên máy mài đo mòn tại điểm đỉnh và điểm mép của biên dạng cung cong đá mài Nhận xét: Đường đặc tính động của hệ đo sau khi được gắn lên máy mài sẽ khác so với đường đặc tính lý thuyết. Nguyên nhân đó là do có sai số trong quá trình chế tạo đột thắt d1 và đầu đo d2. Một nguyên nhân khác đó là do ảnh hưởng của dung dịch trơn nguội, bề mặt đá mài và độ cứng vững của hệ thống công nghệ khi gá lắp hệ đầu đo lên máy mài ... Trong đó, hệ đo khí nén đo mòn ở đỉnh biên dạng cung cong của đá mài có phạm vi đo là 200 μm (từ 50 μm đến 250 μm tương ứng với áp suất buồng đo từ 0,79 bar đến 3,10 bar), tỷ số truyền của đầu đo imax = 0,02 bar/μm và phương trình đường đặc tính động (hàm truyền) là: 3,54 p (3.21) 1 5,4613 10 04 z 2 80 2 Với sai số trung bình là tb = 0,0006%, độ phân tán sai số là = 0,00008. Trong khi, hệ đo khí nén đo mòn ở mép biên dạng cung cong của đá mài có phạm vi đo là 140 μm (từ 20 μm đến 160 μm tương ứng với áp suất buồng đo từ 0,61 bar đến 3,26 bar), tỷ số truyền imax = 0,03 bar/μm và phương trình đường đặc tính động (hàm truyền) là: 3,54 p (3.22) 1 1,8655 10 04 z2 2 Với sai số trung bình là tb = 0,006 %, độ phân tán sai số là = 0,0029. Như vậy, mỗi hệ đo ở trên có một hàm truyền và khoảng làm việc khác nhau. Do đó, để đảm bảo độ chính xác của phép đo thì trước khi thực hiện quá trình đo mòn phải tiến hành điều chỉnh vị trí của mỗi hệ đo khí nén sao cho khoảng khe hở (z) giữa đầu đo và bề mặt cung cong làm việc của đá mài nằm trong phạm vi đo đã xác định ở trên. Tuy nhiên, ở đây trong quá trình thực nghiệm để dễ dàng điều chỉnh hệ đo vào trong miền đo có thể thực hiện điều chỉnh khe hở z thông qua trị số áp suất (p) trong buồng đo xác định được nhờ cảm biến áp suất buồng đo. Ngoài ra, trong quá trình đo do đá bị mòn nên khoảng cách khe hở z sẽ tăng. Khi đó, nếu trị số khoảng cách khe hở z vượt quá giới hạn trên của khoảng làm việc của hệ đo thì cần thực hiện điều chỉnh lại vị trí của hệ đo bằng cách vặn đuôi panme số 1 và đuôi panme số 25 ở mỗi hệ đo để luôn luôn đảm bảo chỉ thực hiện phép đo khi đầu đo nằm trong miền làm việc của hệ đo. 3.4.4. Đặc điểm của dòng khí nén xung quanh đá mài đang quay khi mài định hình rãnh lăn vòng trong ổ bi Qua thực nghiệm khảo sát đo mòn đá bằng đầu đo khí nén khi mài định hình rãnh lăn vòng trong ổ bi 6208 trên máy mài định hình đường lăn 3MK136B nhận thấy áp suất trong buồng đo của mỗi hệ đầu đo luôn thay đổi trong suốt quá trình mài một chi tiết theo chuyển động chạy dao hướng kính của bàn máy mang phôi. Vì vậy, một vấn đề đặt ra là cần xác định được nguyên nhân dẫn đến sự thay đổi của áp suất trong buồng đo. Theo tài liệu [31, 33] thì một viên đá mài khi đang quay ở tốc độ cao sẽ mang theo một lớp không khí trên bề mặt do ma sát của bề mặt đá mài với lớp không khí như thể hiện trên hình 3.21. Đồng thời, luồng không khí này sẽ hướng ra phía ngoài bởi lực ly tâm. Sự thay đổi của dòng khí gây ra bởi chuyển động quay của đá mài dẫn đến sự thay đổi diện tích chảy của dòng khí thổi từ đầu đo d2 của hệ đầu đo vào bề mặt làm việc của đá mài ra môi trường xung quanh. Do đó, điều này làm thay đổi áp suất trong buồng đo. Hình 3.22 thể hiện sự thay đổi của áp suất buồng đo trong quá Hình 3.21. Hình ảnh mô tả dòng khí chảy trình mài một chi tiết vòng trong ổ bi 6208 trên xung quanh một viên đá mài đang quay [33] 81 máy mài định hình 3MK136B ứng với mỗi giai đoạn chuyển động chạy dao hướng kính của bàn ụ vật. ng đo (bar) ồ t bu ấ Áp su Áp Chuyển động chạy dao hướng kính Thời gian gia công (s) Hình 3.22. Sự thay đổi áp suất của buồng đo trong quá trình mài một chi tiết Phía bên phải hình 3.22 thể hiện nguyên lý làm việc của máy mài định hình rãnh lăn vòng trong ổ bi 3MK136B: Đá mài và phôi thực hiện chuyển động quay xung quanh đường tâm. Đồng thời, bàn ụ vật thực hiện chuyển động chạy dao hướng kính. Đặc biệt, như thể hiện trên hình 3.3 về sơ đồ chu trình làm việc của máy thì chuyển động chạy dao hướng kính của bàn máy mang phôi ở đây được chia thành 8 giai đoạn. Ở phía bên trái của hình 3.22 thể hiện sự thay đổi áp suất của buồng đo theo thời gian trong quá trình mài một chi tiết. Từ biểu đồ này và căn cứ vào thời gian cài đặt thực tế trên máy cho các chuyển động tiến vào và lùi ra của bàn máy mang phôi, nhận thấy rằng: Áp suất của buồng đo tăng rất nhanh khi bàn máy mang phôi thực hiện chuyển động chạy dao nhanh (ứng với giai đoạn 1). Sau đó áp suất buồng đo cũng tăng lên nhưng ở tốc độ chậm hơn khi bàn máy mang phôi thực hiện chuyển động tiến tiếp cận (ứng với giai đoạn 2). Tiếp theo, khi bàn máy mang phôi thực hiện chuyển động tiến mài thô và tiến mài tinh (ứng với giai đoạn 3 và 5), thì áp suất buồng đo cũng tăng nhưng ở tốc độ chậm hơn nhiều. Sau
File đính kèm:
luan_an_nghien_cuu_anh_huong_cua_mot_so_yeu_to_cong_nghe_den.pdf
2. bìa quyen tom tat.pdf
3. Tom tat luan an.pdf
4. thong tin tom tat luan an (TV).pdf
5. Thong tin tom tat luan an (TA).pdf