Luận án Nghiên cứu điều khiển hệ thống lái điện trên ô tô con
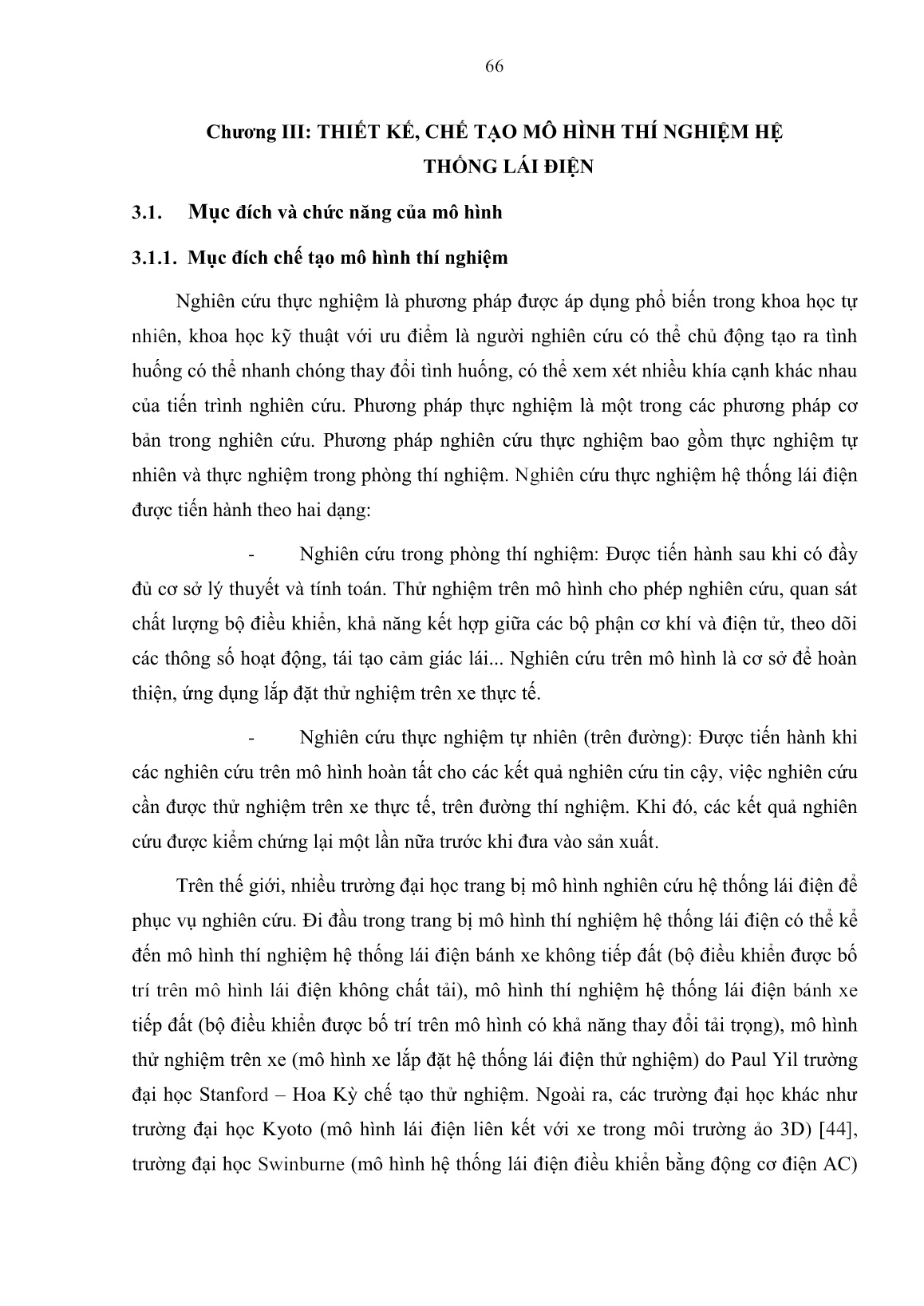
Trang 1

Trang 2
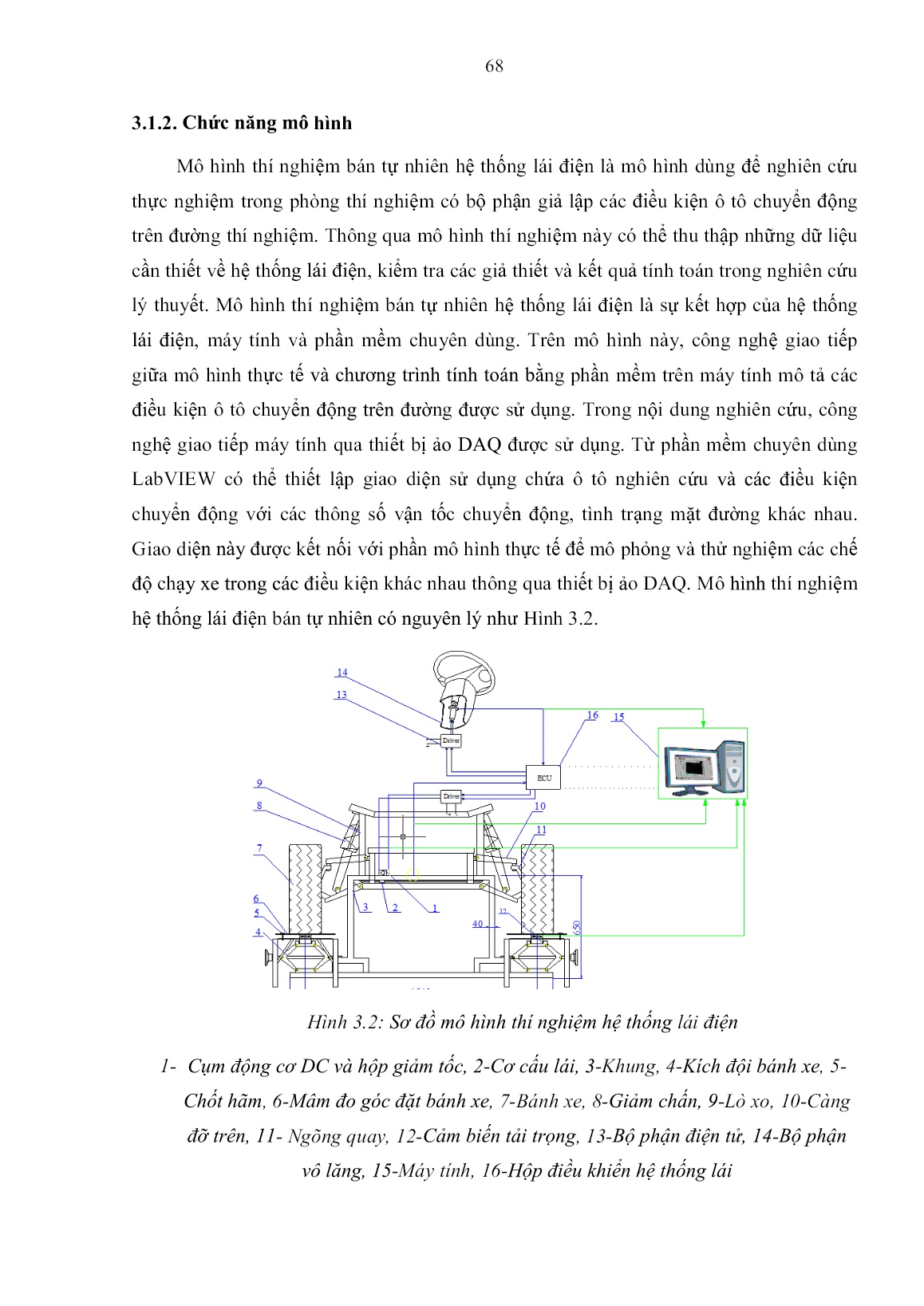
Trang 3
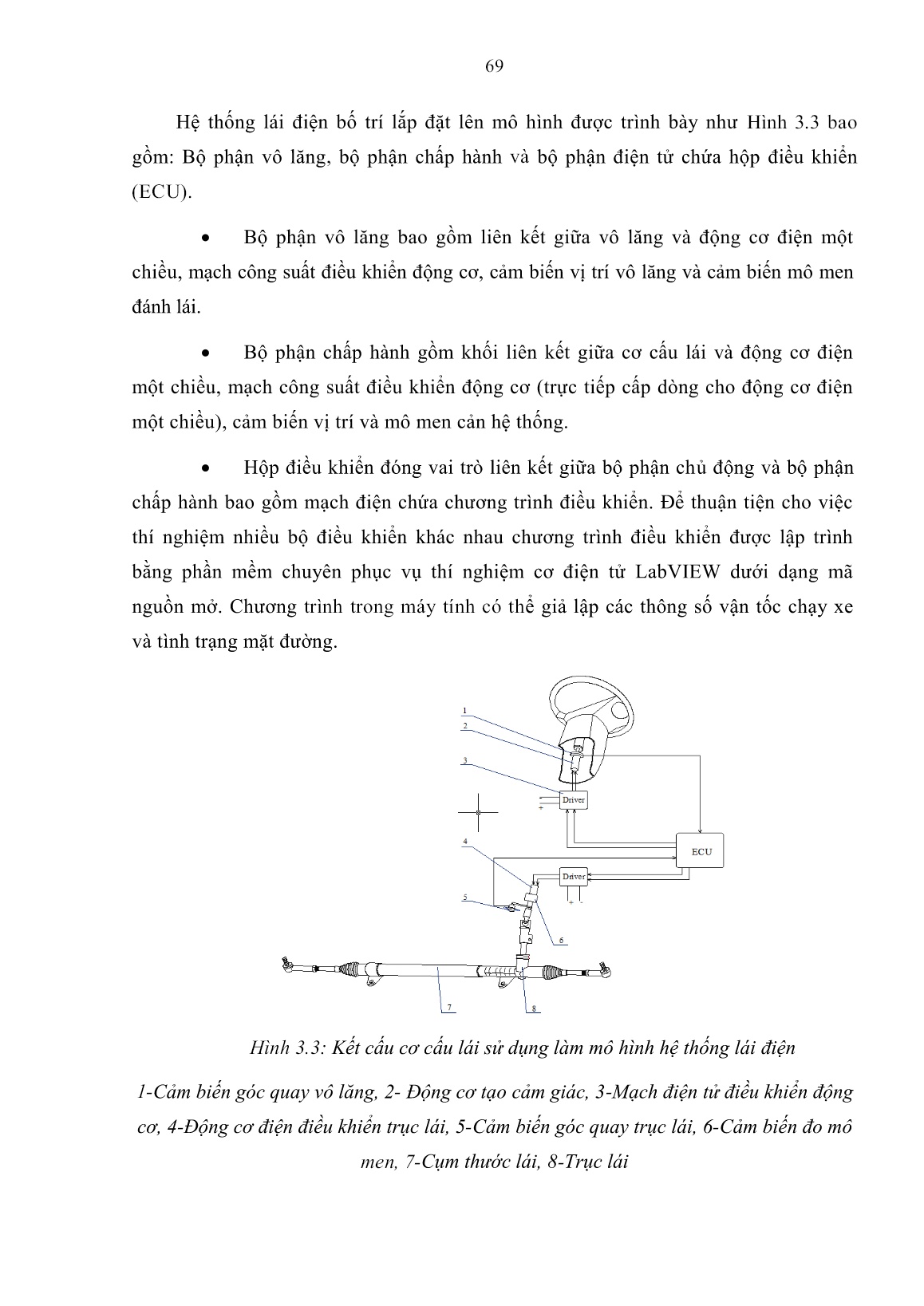
Trang 4
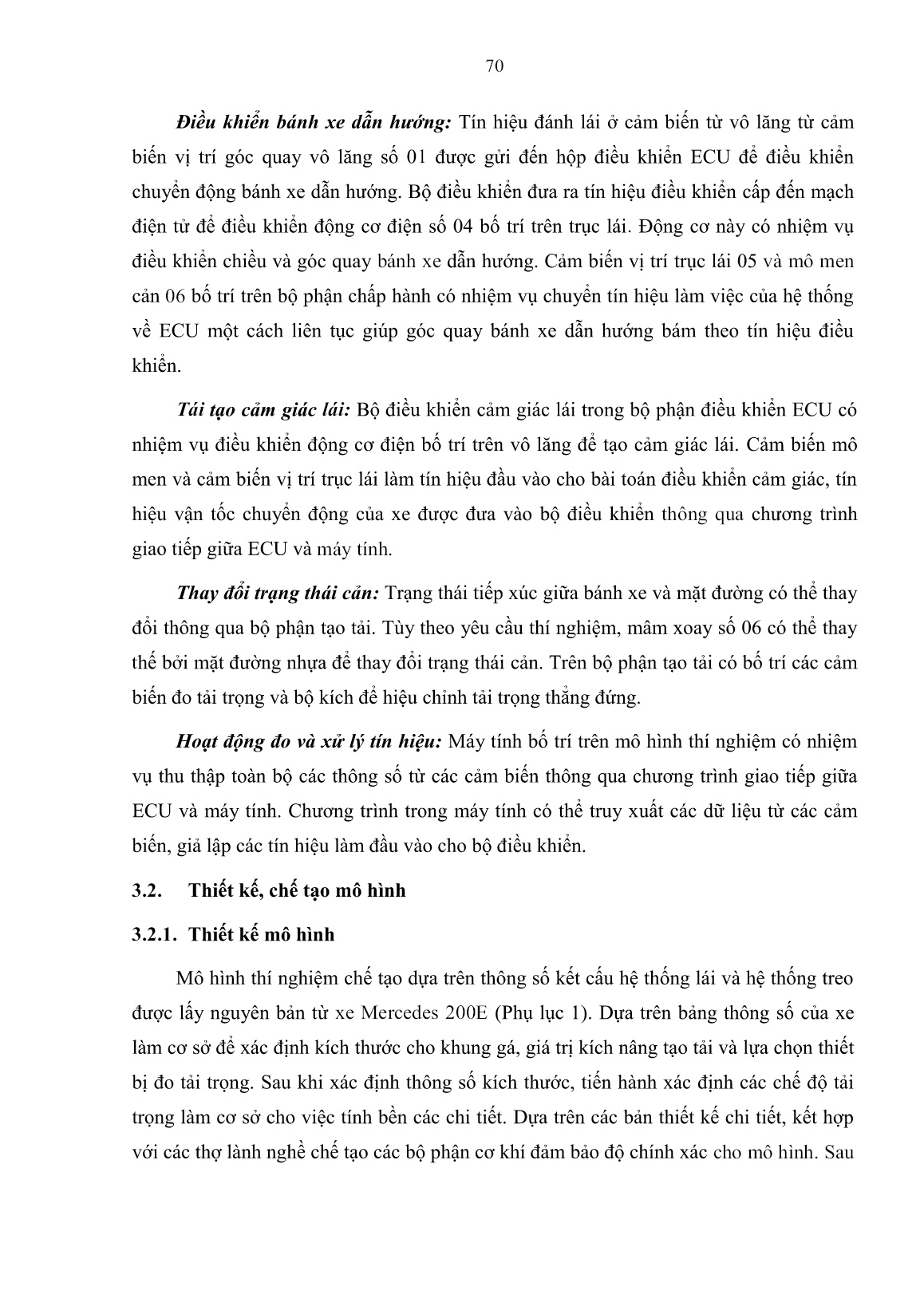
Trang 5
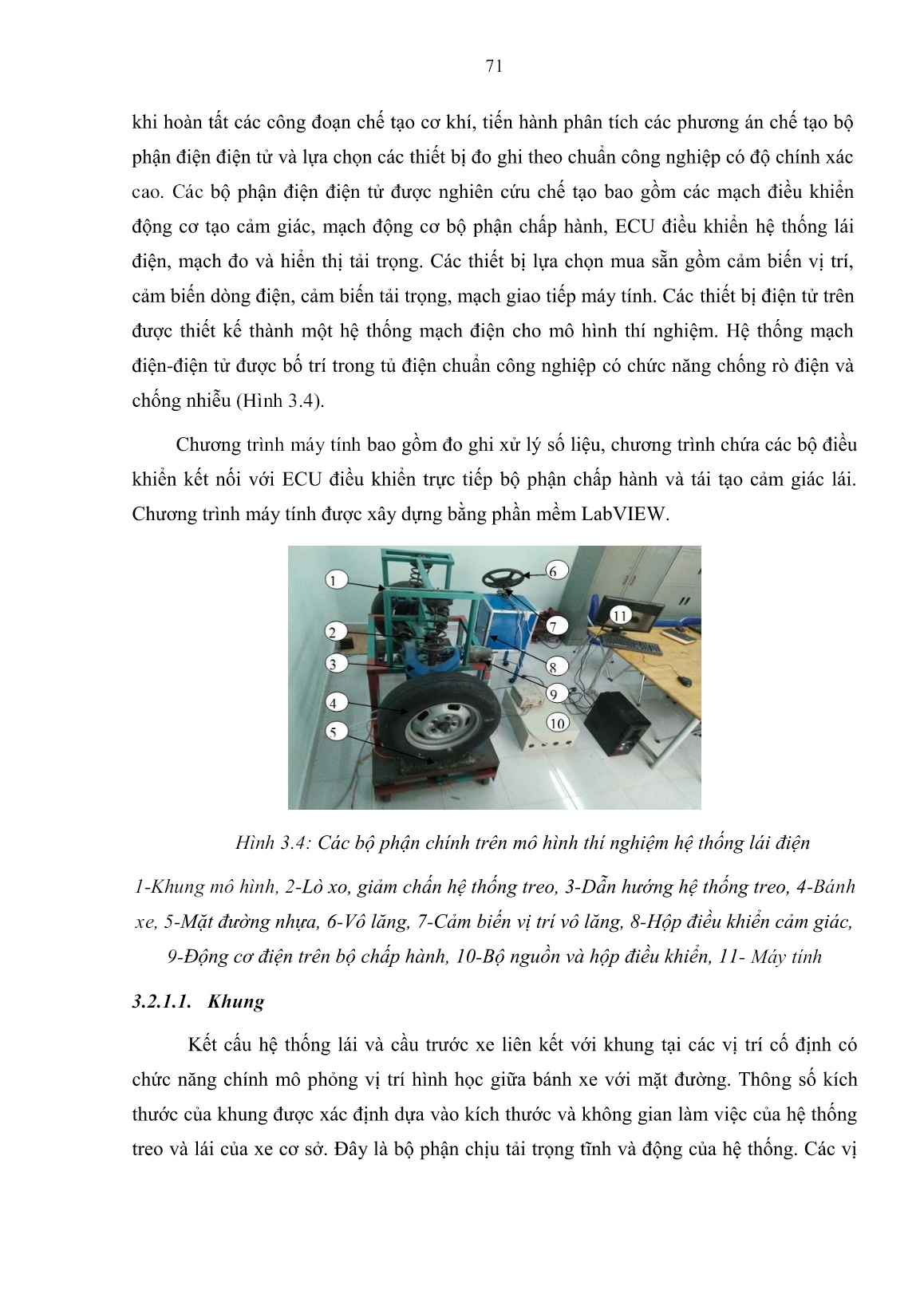
Trang 6
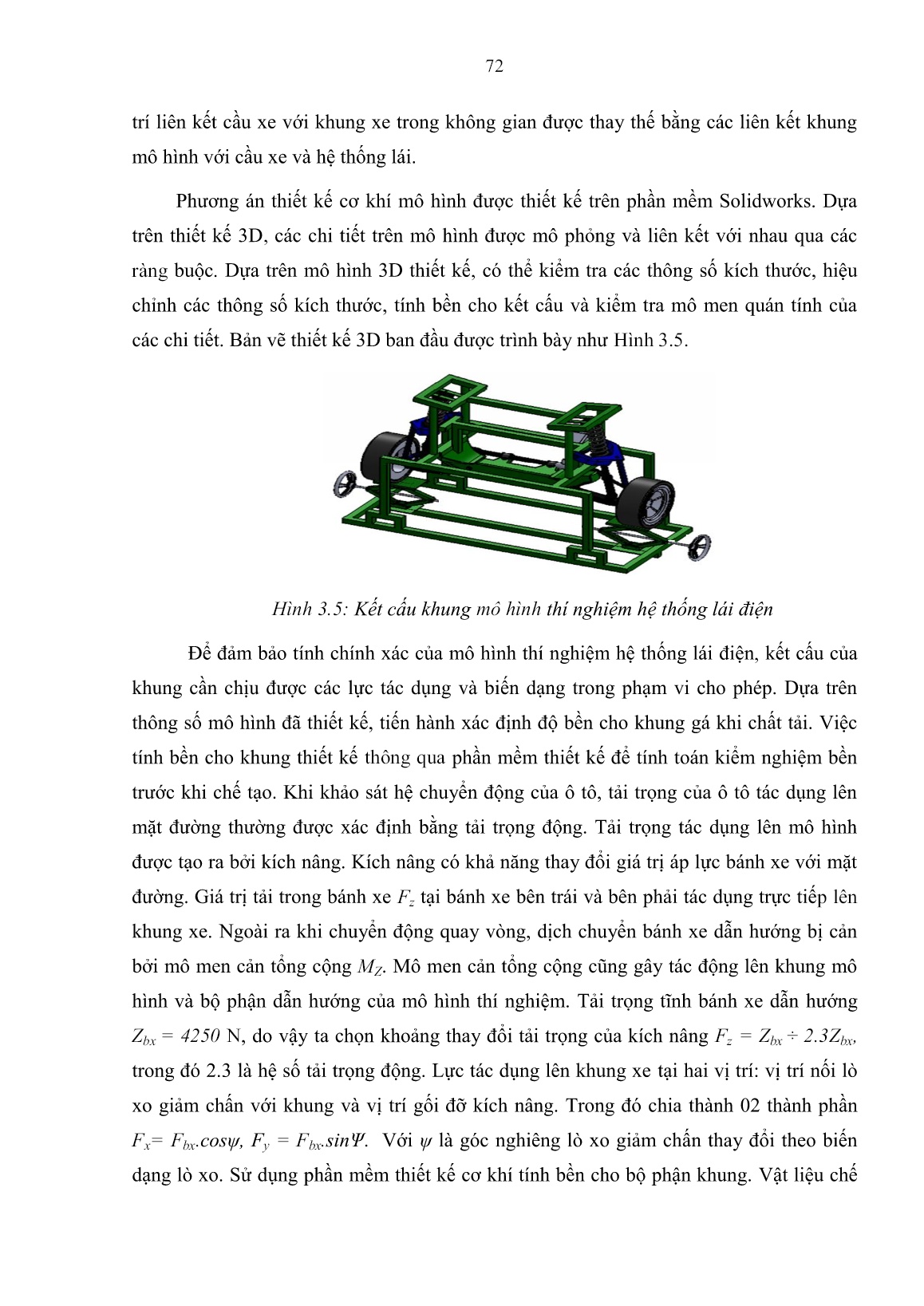
Trang 7
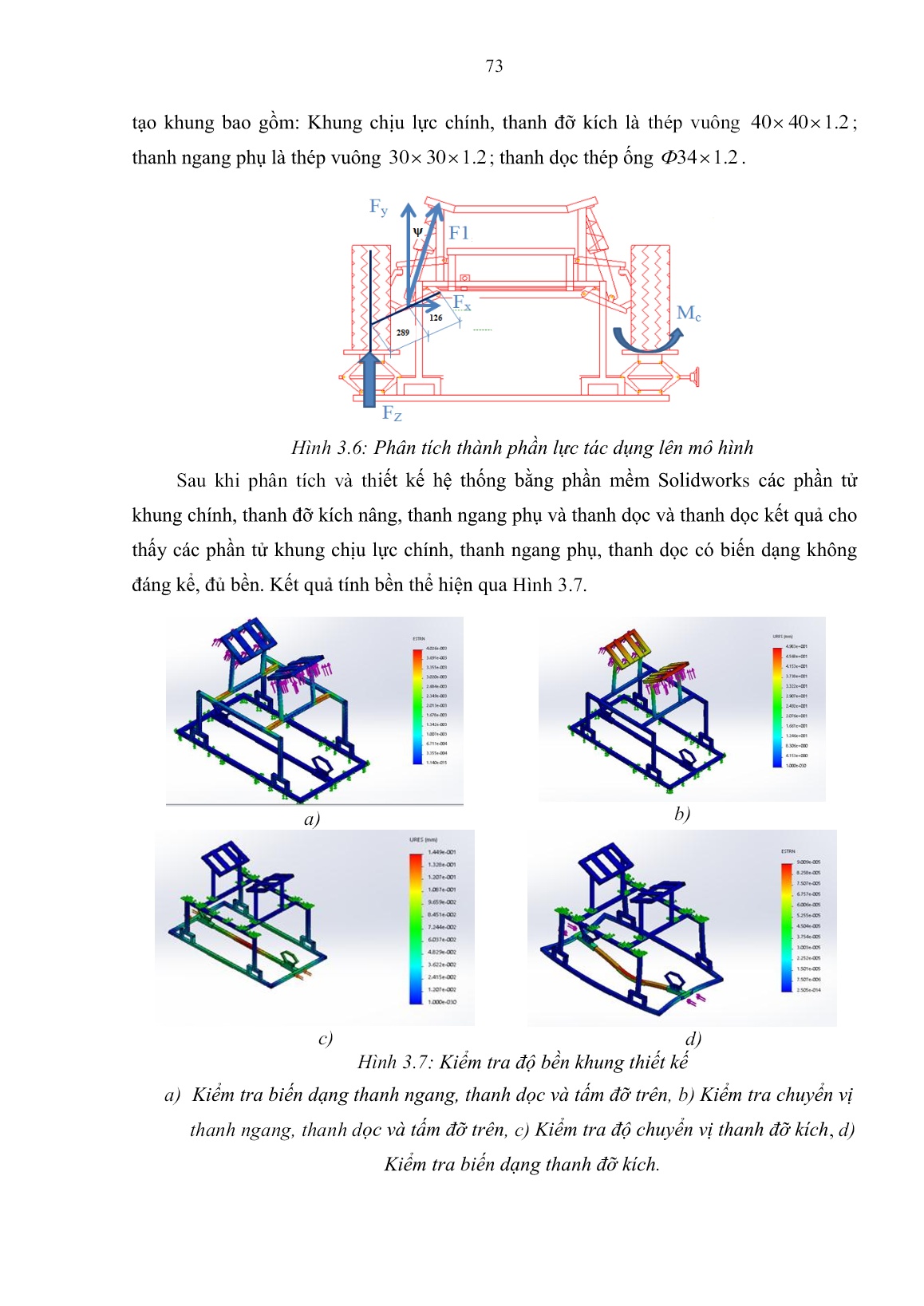
Trang 8
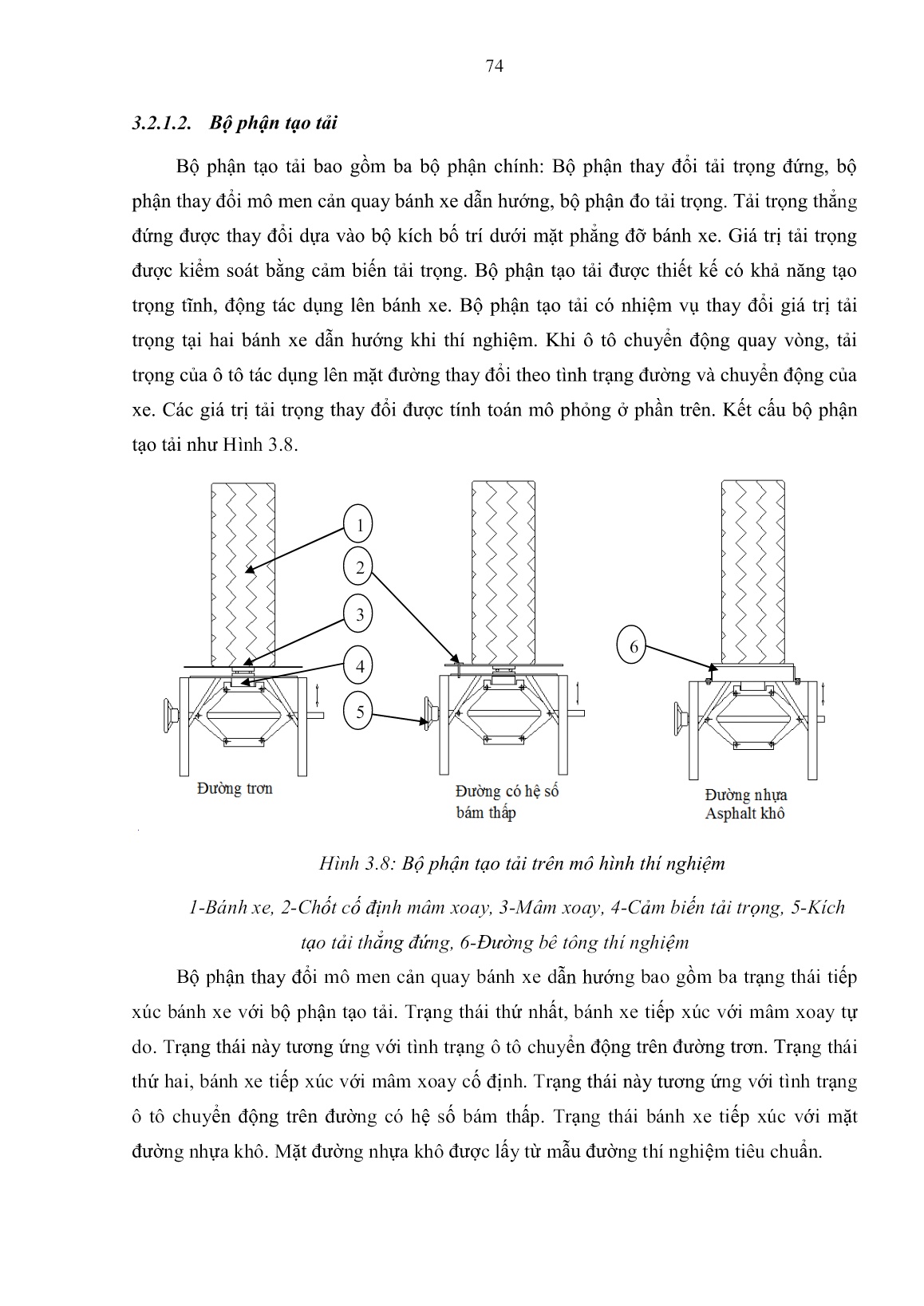
Trang 9
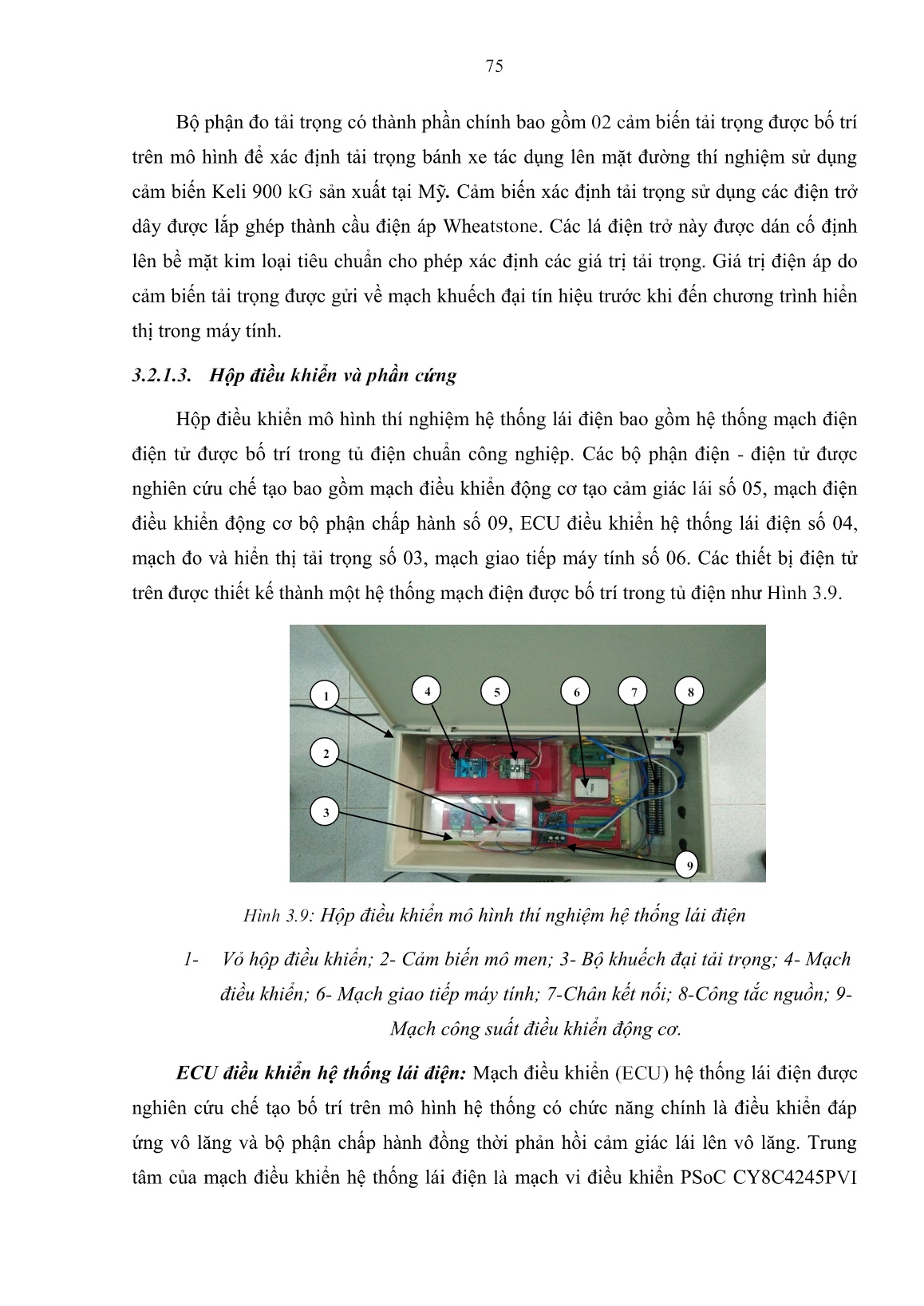
Trang 10
Tải về để xem bản đầy đủ
Bạn đang xem 10 trang mẫu của tài liệu "Luận án Nghiên cứu điều khiển hệ thống lái điện trên ô tô con", để tải tài liệu gốc về máy hãy click vào nút Download ở trên.
Tóm tắt nội dung tài liệu: Luận án Nghiên cứu điều khiển hệ thống lái điện trên ô tô con
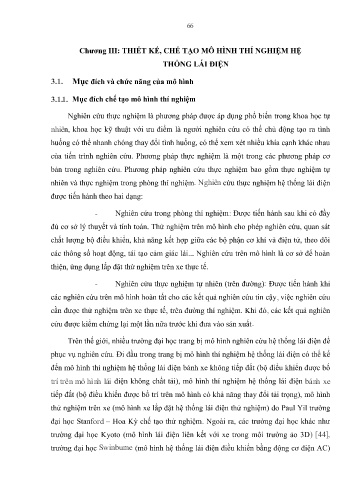
hệ thống treo, 3-Dẫn hướng hệ thống treo, 4-Bánh xe, 5-Mặt đường nhựa, 6-Vô lăng, 7-Cảm biến vị trí vô lăng, 8-Hộp điều khiển cảm giác, 9-Động cơ điện trên bộ chấp hành, 10-Bộ nguồn và hộp điều khiển, 11- Máy tính 3.2.1.1. Khung Kết cấu hệ thống lái và cầu trước xe liên kết với khung tại các vị trí cố định có chức năng chính mô phỏng vị trí hình học giữa bánh xe với mặt đường. Thông số kích thước của khung được xác định dựa vào kích thước và không gian làm việc của hệ thống treo và lái của xe cơ sở. Đây là bộ phận chịu tải trọng tĩnh và động của hệ thống. Các vị 72 trí liên kết cầu xe với khung xe trong không gian được thay thế bằng các liên kết khung mô hình với cầu xe và hệ thống lái. Phương án thiết kế cơ khí mô hình được thiết kế trên phần mềm Solidworks. Dựa trên thiết kế 3D, các chi tiết trên mô hình được mô phỏng và liên kết với nhau qua các ràng buộc. Dựa trên mô hình 3D thiết kế, có thể kiểm tra các thông số kích thước, hiệu chỉnh các thông số kích thước, tính bền cho kết cấu và kiểm tra mô men quán tính của các chi tiết. Bản vẽ thiết kế 3D ban đầu được trình bày như Hình 3.5. Hình 3.5: Kết cấu khung mô hình thí nghiệm hệ thống lái điện Để đảm bảo tính chính xác của mô hình thí nghiệm hệ thống lái điện, kết cấu của khung cần chịu được các lực tác dụng và biến dạng trong phạm vi cho phép. Dựa trên thông số mô hình đã thiết kế, tiến hành xác định độ bền cho khung gá khi chất tải. Việc tính bền cho khung thiết kế thông qua phần mềm thiết kế để tính toán kiểm nghiệm bền trước khi chế tạo. Khi khảo sát hệ chuyển động của ô tô, tải trọng của ô tô tác dụng lên mặt đường thường được xác định bằng tải trọng động. Tải trọng tác dụng lên mô hình được tạo ra bởi kích nâng. Kích nâng có khả năng thay đổi giá trị áp lực bánh xe với mặt đường. Giá trị tải trong bánh xe Fz tại bánh xe bên trái và bên phải tác dụng trực tiếp lên khung xe. Ngoài ra khi chuyển động quay vòng, dịch chuyển bánh xe dẫn hướng bị cản bởi mô men cản tổng cộng MZ. Mô men cản tổng cộng cũng gây tác động lên khung mô hình và bộ phận dẫn hướng của mô hình thí nghiệm. Tải trọng tĩnh bánh xe dẫn hướng Zbx = 4250 N, do vậy ta chọn khoảng thay đổi tải trọng của kích nâng Fz = Zbx ÷ 2.3Zbx, trong đó 2.3 là hệ số tải trọng động. Lực tác dụng lên khung xe tại hai vị trí: vị trí nối lò xo giảm chấn với khung và vị trí gối đỡ kích nâng. Trong đó chia thành 02 thành phần Fx= Fbx.cosψ, Fy = Fbx.sinΨ. Với ψ là góc nghiêng lò xo giảm chấn thay đổi theo biến dạng lò xo. Sử dụng phần mềm thiết kế cơ khí tính bền cho bộ phận khung. Vật liệu chế 73 tạo khung bao gồm: Khung chịu lực chính, thanh đỡ kích là thép vuông 40 40 1.2 ; thanh ngang phụ là thép vuông 30 30 1.2; thanh dọc thép ống Ф34 1.2. Hình 3.6: Phân tích thành phần lực tác dụng lên mô hình Sau khi phân tích và thiết kế hệ thống bằng phần mềm Solidworks các phần tử khung chính, thanh đỡ kích nâng, thanh ngang phụ và thanh dọc và thanh dọc kết quả cho thấy các phần tử khung chịu lực chính, thanh ngang phụ, thanh dọc có biến dạng không đáng kể, đủ bền. Kết quả tính bền thể hiện qua Hình 3.7. a) b) c) d) Hình 3.7: Kiểm tra độ bền khung thiết kế a) Kiểm tra biến dạng thanh ngang, thanh dọc và tấm đỡ trên, b) Kiểm tra chuyển vị thanh ngang, thanh dọc và tấm đỡ trên, c) Kiểm tra độ chuyển vị thanh đỡ kích, d) Kiểm tra biến dạng thanh đỡ kích. 74 3.2.1.2. ộ ph n tạo tải Bộ phận tạo tải bao gồm ba bộ phận chính: Bộ phận thay đổi tải trọng đứng, bộ phận thay đổi mô men cản quay bánh xe dẫn hướng, bộ phận đo tải trọng. Tải trọng thẳng đứng được thay đổi dựa vào bộ kích bố trí dưới mặt phẳng đỡ bánh xe. Giá trị tải trọng được kiểm soát bằng cảm biến tải trọng. Bộ phận tạo tải được thiết kế có khả năng tạo trọng tĩnh, động tác dụng lên bánh xe. Bộ phận tạo tải có nhiệm vụ thay đổi giá trị tải trọng tại hai bánh xe dẫn hướng khi thí nghiệm. Khi ô tô chuyển động quay vòng, tải trọng của ô tô tác dụng lên mặt đường thay đổi theo tình trạng đường và chuyển động của xe. Các giá trị tải trọng thay đổi được tính toán mô phỏng ở phần trên. Kết cấu bộ phận tạo tải như Hình 3.8. 1 2 3 6 4 5 Hình 3.8: Bộ phận tạo tải trên mô hình thí nghiệm 1-Bánh xe, 2-Chốt cố định mâm xoay, 3-Mâm xoay, 4-Cảm biến tải trọng, 5-Kích tạo tải thẳng đứng, 6-Đường bê tông thí nghiệm Bộ phận thay đổi mô men cản quay bánh xe dẫn hướng bao gồm ba trạng thái tiếp xúc bánh xe với bộ phận tạo tải. Trạng thái thứ nhất, bánh xe tiếp xúc với mâm xoay tự do. Trạng thái này tương ứng với tình trạng ô tô chuyển động trên đường trơn. Trạng thái thứ hai, bánh xe tiếp xúc với mâm xoay cố định. Trạng thái này tương ứng với tình trạng ô tô chuyển động trên đường có hệ số bám thấp. Trạng thái bánh xe tiếp xúc với mặt đường nhựa khô. Mặt đường nhựa khô được lấy từ mẫu đường thí nghiệm tiêu chuẩn. 75 Bộ phận đo tải trọng có thành phần chính bao gồm 02 cảm biến tải trọng được bố trí trên mô hình để xác định tải trọng bánh xe tác dụng lên mặt đường thí nghiệm sử dụng cảm biến Keli 900 kG sản xuất tại Mỹ. Cảm biến xác định tải trọng sử dụng các điện trở dây được lắp ghép thành cầu điện áp Wheatstone. Các lá điện trở này được dán cố định lên bề mặt kim loại tiêu chuẩn cho phép xác định các giá trị tải trọng. Giá trị điện áp do cảm biến tải trọng được gửi về mạch khuếch đại tín hiệu trước khi đến chương trình hiển thị trong máy tính. 3.2.1.3. Hộp điều khiển và phần cứng Hộp điều khiển mô hình thí nghiệm hệ thống lái điện bao gồm hệ thống mạch điện điện tử được bố trí trong tủ điện chuẩn công nghiệp. Các bộ phận điện - điện tử được nghiên cứu chế tạo bao gồm mạch điều khiển động cơ tạo cảm giác lái số 05, mạch điện điều khiển động cơ bộ phận chấp hành số 09, ECU điều khiển hệ thống lái điện số 04, mạch đo và hiển thị tải trọng số 03, mạch giao tiếp máy tính số 06. Các thiết bị điện tử trên được thiết kế thành một hệ thống mạch điện được bố trí trong tủ điện như Hình 3.9. 1 4 5 6 7 8 2 3 9 Hình 3.9: Hộp điều khiển mô hình thí nghiệm hệ thống lái điện 1- Vỏ hộp điều khiển; 2- Cảm biến mô men; 3- Bộ khuếch đại tải trọng; 4- Mạch điều khiển; 6- Mạch giao tiếp máy tính; 7-Chân kết nối; 8-Công tắc nguồn; 9- Mạch công suất điều khiển động cơ. ECU điều khiển hệ thống lái điện: Mạch điều khiển (ECU) hệ thống lái điện được nghiên cứu chế tạo bố trí trên mô hình hệ thống có chức năng chính là điều khiển đáp ứng vô lăng và bộ phận chấp hành đồng thời phản hồi cảm giác lái lên vô lăng. Trung tâm của mạch điều khiển hệ thống lái điện là mạch vi điều khiển PSoC CY8C4245PVI 76 cho phép điều khiển lập trình các thuật toán nhận các tín hiệu từ cảm biến phân tích, từ đó đưa tín hiệu điều khiển cơ cấu chấp hành phù hợp theo yêu cầu. Các chương trình điều khiển khi hoàn thiện sẽ được lập trình đưa vào mạch vi điều khiển PsoC. Vi điều khiển PSoC là một trong những vi điều khiển thông minh có khả năng tái cấu hình (cài đặt các chân theo người lập trình). Bên cạnh đó, mạch điều khiển có thiết kế chức năng giao tiếp máy tính được thông qua cổng USB cho phép nạp chương trình điều khiển từ máy tính. Mạch điều khiển trên bao gồm các khối mạch thành phần: khối mạch nguồn 5V (POWER) nhiệm vụ chính cấp nguồn cho vi điều khiển, khối mạch giao tiếp máy tính với vi điều khiển qua cổng USB (USB-UART) cho phép nhận các chương trình từ máy tính, khối mạch vi điều khiển trung tâm PSoC chứa các chương trình lập trình sẵn. Sơ đồ nguyên lý của mạch điện điều khiển trình bày trong Hình 3.10. Hình 3.10: Nguyên lý mạch điều khiển hệ thống lái điện Mạch điều khiển động cơ: Tín hiệu mạch điều khiển không trực tiếp điều khiển động cơ bộ phận chấp hành và động cơ tạo cảm giác mà gửi đến mạch điện công suất điều khiển động cơ (Driver). Mạch công suất trực tiếp tiếp nhận dòng điện điều khiển từ nguồn chính 12V và tín hiệu điều khiển từ mạch điều khiển. Chương trình chính trong mạch điều khiển sẽ quyết định chiều quay, vận tốc, mô men động cơ. Mạch công suất thiết kế cho mô hình sử dụng Mosfet có công suất 360 W bố trí dạng cầu có các bộ phận 77 đảm bảo khả năng giải nhiệt khi làm việc ở cường độ cao. Mạch công suất trong luận án sử dụng trên mô hình sử dụng 04 MOSFET IRF3205 và 02 IC IR2110 giao tiếp với vi điều khiển (Hình 3.11). Hình 3.11: Nguyên lý Driver điều khiển động cơ DC sử dụng cầu H 3.2.1.4. Thiết bị đo ghi và chương trình hiển thị, xử lý số liệu Mạch giao tiếp máy tính: Chức năng chính của bộ phận này là ghi lại các thông số kỹ thuật khi mô hình hoạt động ở các chế độ tải trọng khác nhau. Thông số từ cảm biến được hiển thị trên màn hình máy tính sau khi đi qua mạch điện giao tiếp máy tính. Để đảm bảo tính chính xác thông số đo, trong chương trình thí nghiệm sử dụng thiết bị giao tiếp máy tính của các hãng National Instruments, có độ chính xác cao (Hình 3.12). Thông số kỹ thuật Card giao tiếp trình bày trong phần Phụ lục 2. Hình 3.12: Mạch giao tiếp máy tính NI 6009 78 Cảm biến đo dòng: Cảm biến dòng được bố trí trên mô hình hệ thống để đo cường độ dòng điện cấp cho động cơ điều khiển hệ thống lái điện. Cảm biến dòng điện được sử dụng là cảm biến Allegro ACS712 được sản xuất tại Mỹ. Cảm biến ACS712 sử dụng hiệu ứng Hall để xác định cường độ dòng điện, cường độ dòng điện qua cuộn dây Stator động cơ điều khiển được cảm nhận bởi IC Hall chuyển thành tín hiệu điện áp. Đặc tính điện áp và mạch điện bố trí cảm biến dòng được thể hiện trong Hình 3.13. Hình 3.13: Khối mạch điện cảm biến dòng và đặc tính Cảm biến đo vị trí (encoder): Cảm biến xác định vị trí được bố trí trên vô lăng và trục cơ cấu lái. Cảm biến vị trí bố trí trên vô lăng, trục lái làm tín hiệu điều khiển chuyển động và phản hồi hệ thống. Trên mô hình sử dụng encoder của hãng Omron được sử dụng để xác định vị trí và chiều quay trục. Encoder có cấu tạo chính gồm bộ phận phát từ và đĩa quang như Hình 3.14. Đĩa quang được sử dụng trong encorder bố trí trên mô hình được khắc 500 vạch nhỏ tương ứng với 500 xung/vòng. Ánh sáng đi qua khe hở đĩa quang được cảm nhận và đưa vào bộ khuếch đại. Để tránh sai số cũng như xác định được chiều quay trên mỗi encoder được bố trí 02 bộ phận cảm nhận kênh A và kênh B. Hai kênh này kết hợp với chương trình đọc Encoder sẽ hiển thị chính xác vị trí trục. Hình 3.14: Nguyên lý và kết cấu cảm biến đo vị trí encoder Chương trình giao tiếp máy tính và xử lý số liệu thí nghiệm: Chương trình giao tiếp máy tính phục vụ thí nghiệm được xây dựng bằng phần mềm LabVIEW liên kết với 79 thiết bị ảo (DAQ). Thiết bị ảo DAQ là một công cụ liên kết giữa thiết bị phần cứng và phần mềm trong các thiết bị đo lường. Thiết bị này được tạo ra bởi người sử dụng theo các tiêu chuẩn của máy tính. Thiết bị DAQ cho phép biến đổi tín hiệu thành tín hiệu số và gửi tới máy tính (tới phần mềm bên trong máy tính). Phương pháp này có tính mềm dẻo cao vì có thể sử dụng một thiết bị phần cứng cho nhiều chương trình thí nghiệm khác nhau. Để nghiên cứu mô hình hệ thống lái điện bằng DAQ, cần trang bị máy tính có thể truy xuất trực tiếp bộ nhớ DMA (Direct memory access), giao tiếp cổng USB và có cấu hình cao để đảm bảo tốc độ khi truyền dữ liệu. Chương trình giao tiếp máy tính sử dụng các khối điều khiển, hiển thị, và xử lý số liệu cho chương trình thí nghiệm điều khiển mô hình hệ thống lái điện. Kết quả thí nghiệm được hiển thị trực tiếp qua giao diện màn hình. Bên cạnh đó các dữ liệu thí nghiệm có thể lưu lại dưới dạng bảng thông qua việc kết nối cơ sở dữ liệu trên phần mềm LabVIEW với phần mềm Excel. Chương trình chính cho phép hiển thị các thông số hoạt động hệ thống cũng như tạo ra các tín hiệu điều khiển tương ứng với các chế độ chạy xe. Giao diện này được cài đặt trong máy tính và dễ dàng sử dụng. Giao diện kết nối máy tính phục vụ thí nghiệm như Hình 3.15. Hình 3.15: Giao diện kết nối máy tính phục vụ thí nghiệm hệ thống lái điện 3.2.2. Thiết kế chƣơng trình điều khiển bám Chương trình điều khiển bám được xây dựng bằng phần mềm LabVIEW, chương trình có cấu trúc gồm hai bộ thiết bị ảo DAQ1, DAQ2, hàm thuộc biến đầu vào là tải 80 trọng và sai số, ba biến đầu ra là KP, KI, KD , biểu đồ hiển thị trực tiếp khả năng bám góc quay trục lái và tín hiệu điều khiển, luật hợp thành mờ sử dụng luật Mamdani. Giao diện điều khiển bám sử dụng bộ điều khiển Fuzzy-PID được trình bày trong Hình 3.16. Hình 3.16: Giao diện điều khiển bám Mô men cản quay (load) được xác định bằng cảm biến đo mô men được gửi về DAQ1. Sai lệch giữa góc quay vô lăng và góc quay trục lái được xác định bằng cảm biến vị trí được tổng hợp từ hai cảm biến vị trí vô lăng và vị trí trục lái chuyển về DAQ2 . Các hàm quan hệ giá trị ngôn ngữ biến vào và ra bộ điều khiển mờ. Hàm thuộc được tính toán xác định trong chương 2 được đưa vào chương trình điều khiển bám được trình bày từ Hình 3.17 đến Hình 3.21. Hình 3.17: Hàm thuộc tải trọng thay đổi trong chương trình máy tính 81 Hình 3.18: Hàm thuộc sai số thay đổi trong chương trình máy tính Hình 3.19: Hàm thuộc biến KP trong chương trình máy tính Hình 3.20: Hàm thuộc biến KI trong chương trình máy tính Hình 3.21: Hàm thuộc biến KD trong chương trình máy tính 82 Luật điều khiển được xây dựng gồm 49 luật thể hiện được đưa vào chương trình máy tính như Hình 3.22. Hình 3.22: Bảng luật hợp thành điều khiển mờ trong chương trình máy tính Quan hệ truyền đạt bộ điều khiển mờ: Lựa chọn nguyên lý giải mờ theo phương pháp đường phân đôi diện tích ta xây dựng được quan hệ truyền đạt bộ điều khiển mờ. Biểu diễn mối quan hệ giữa tín hiệu vào, tín hiệu đầu ra và thông số bộ điều khiển PID thể hiện qua Hình 3.23, 3.24, 3.25. Hình 3.23: Đáp ứng hệ số KP theo tải trọng, sai số trong chương trình máy tính Hình 3.24: Đáp ứng hệ số KI theo tải trọng, sai số trong chương trình máy tính 83 Hình 3.25: Đáp ứng hệ số KD theo tải trọng, sai số trong chương trình máy tính Thiết kế bộ điều khiển Fuzzy-PID trong môi trường LabVIEW: Dựa trên các thiết kế bộ điều khiển Fuzzy-PID trong chương 2, tiến hành lập trình bộ điều khiển bằng phần mềm LabVIEW. Chương trình điều khiển bám trình bày như Hình 3.26, 3.27. Hình 3.26: Chương trình điều khiển bám sử dụng bộ điều khiển PID Hình 3.27: Chương trình điều khiển bám sử dụng bộ điều khiển Fuzzy-PID Mô hình hoàn thiện sau khi thiết kế chế tạo như Hình 3.28. 84 Hình 3.28: Mô hình thí nghiệm hệ thống lái điện hoàn chỉnh 3.3. Thử nghiệm mô hình Sau khi hoàn thành công đoạn chế tạo, lắp ráp, hiệu chỉnh cần tiến hành chạy thử nghiệm để đánh giá khả năng làm việc của mô hình. Việc thử nghiệm trên bệ thử với trạng thái tiếp xúc trực tiếp với mâm xoay tự do nhằm kiểm tra hoạt động điều khiển lái thông thường, khả năng đáp ứng của hệ thống điện điện tử (độ đáp ứng cơ cấu vành lái và bộ phận chấp hành). Mâm xoay ở trạng thái xoay tự do khi chốt mở, khi đó tình trạng làm việc của hệ thống tương ứng với trạng thái bánh xe di chuyển trên đường trơn trượt (Hình 3.29). Hình 3.29: Bánh xe tiếp xúc với mâm xoay Mô hình thí nghiệm bán tự nhiên được cài đặt các thông số chạy xe như vận tốc, sự thay đổi của tải trọng, tình trạng mặt đường. Ứng với mỗi trường hợp trên, bộ điều khiển PID và Fuzzy-PID được cài đặt cho phần cứng hệ thống lái, tiến hành đánh lái với góc đánh lái thay đổi từ 0 – 900. Tải trọng tác dụng bánh xe lên nền đường được thay đổi theo vận tốc chuyển động, thử nghiệm được thực hiện ở ba giá trị vận tốc 0 km/h, 40 km/h, 60 85 km/h. Kết quả là khả năng đáp ứng giữa vô lăng lái và trục lái được xác định thông qua chương trình đo ghi trên máy tính. 3.3.1. Thử nghiệm so sánh hệ thống lái điện và hệ thống lái cơ khí truyền thống Để kết quả thí nghiệm chất lượng hệ thống lái được chính xác ban đầu phải so sánh khả năng làm việc của hệ thống lái điện với hệ thống lái truyền thống bao gồm tỷ số truyền và khả năng làm việc của hình thang lái. Tỷ số truyền và khả năng làm việc của hình thang lái được xác định thông qua cảm biến góc quay vô lăng và thiết bị đo góc đặt bánh xe. Tiến hành đánh lái với góc quay vô lăng thay đổi từ vị trí trung hòa đến vị trí cuối cùng 7200 khi cho bánh xe tiếp xúc mới mâm xoay, bộ điều khiển cài đặt cho hệ thống lái điện là bộ điều khiển PID, tải trọng bánh xe dẫn hướng ở chế độ tải trọng tĩnh giá trị 4250 N. ảng 3.1: Kết quả thử nghiệm đánh lái bên phải Góc quay bánh Góc quay bánh Góc quay bánh Góc quay vô xe bên phải xe bên trái xe bên trái lý Tỷ số truyền lăng (độ) (độ) thực tế (độ) thuyết (độ) thực tế 0 0 0 0 20 5.1 4.9 4.74 99 19.8 10 9.6 9.29 195 19.9 15.5 14.1 13.61 290 19.6 20.1 17.8 17.79 378 19.9 25.3 22.2 21.89 471 19.8 30.2 25.8 26.01 557 19.9 35.4 31.4 30.17 674 20.2 38.1 33.1 32.95 714 20.1 Khả năng làm việc hình thang lái khi đánh lái sang phải được thể hiện bằng đồ thị quan hệ giữa góc quay bánh xe dẫn bên phải và trái như Hình 3.30. Hình 3.30: Quan hệ góc quay bánh xe dẫn hướng khi đánh lái sang phải 86 ảng 3.2: Kết quả thử nghiệm đánh lái bên trái Góc quay bánh Góc quay bánh Góc quay bánh Góc quay vô xe bên phải xe bên phải lý xe bên trái (độ) lăng(độ) thực tế (độ) thuyết (độ) Tỷ số truyền 0 0 0 0 20 5.1 4.9 4.75 99 19.8 10.1 9.6 9.29 196 19.9 15.3 14.2 13.6 290 19.7 20.2 17.9 17.79 379 19.9 25.3 22.3 21.89 471 19.8 30.3 26.1 26.01 557 19.8 34.8 31 30.1 675 20.5 37.9 33.2 32.95 714 20.1 Khả năng làm việc hình thang lái khi đánh lái sang trái được thể hiện bằng đồ thị quan hệ giữa góc quay bánh xe dẫn bên phải và trái như Hình 3.31. Hình 3.31: Quan hệ góc quay bánh xe dẫn hướng khi đánh lái sang trái Kết quả trên cho thấy hoạt động của hệ thống lái điện cho thông số phù hợp với tiêu chuẩn đánh giá các hệ thống lái truyền thống (sai số giữa lý thuyết và thực tế do hoạt động của hình thang lái và sai số cơ cấu cơ khí nhỏ hơn 10). Dựa vào kết quả thí nghiệm trên có thể thấy rằng khả năng làm việc của hệ thống đảm bảo tin cậy để thực hiện các nghiên cứu tiếp theo. 3.3.2. Thử nghiệm động lực học hệ thống lái lắp đặt hệ thống lái điện ở tình trạng bánh xe tiếp xúc với mâm xoay Khả năng đáp ứng của hệ thống (độ đáp ứng cơ cấu vành lái và bộ phận chấp hành) đặc trưng cho quan hệ động học hệ thống lái lắp đặt hệ thống lái điện. Để quan sát và phân tích một cách chính xác khả năng đáp ứng của hệ thống cần tiến hành thí nghiệm và 87 ghi lại các thông số làm việc hệ thống ở các trạng thái tải khác nhau. Khả năng đáp ứng của hệ thống phụ thuộc vào trạng thái cản hệ thống, bộ phận điều khiển (chương trình điều khiển hệ thống lái điện), kết cấu phần cứng hệ thống lái điện. Chương trình thí nghiệm quan sát độ trễ kết hợp với các chương trình đo mô men cản, vị trí góc quay bánh xe cho kết quả trực quan về khả năng đáp ứng hệ thống. các vị trí trung hòa và vị trí góc đánh lái cực đại khi thay đổi chiều đánh lái quán tính hệ thống thay đổi chiều đột ngột khả năng đáp ứng hệ thống cần quan sát kỹ lưỡng. a) Trạng thái mâm xoay tự do Tiến hành cài đặt bộ điều khiển PID cho hệ thống lái điện với các thông số KP =10, KI = 1.7, KD = 0.15, hiệu chỉnh tải trọng bánh xe 4250 N, tiến hành đánh lái từ vị trí trung hòa sang bên phải sau đó đảo chiều. Hiệu chỉnh tải trọng theo vận tốc đánh lái 40km/h, 60 km/h. Quan sát kết quả thí nghiệm từ thời gian thực hiển thị trực tiếp như Hình 3.32 đến Hình 3.34. Hình 3.32: Kết quả điều khiển bám sử dụng bộ điều khiển PID ở vận tốc 0 km/h Hình 3.33: Kết quả điều khiển bám sử dụng bộ điều khiển PID ở vận tốc 40 km/h 88 Hình 3.34: Kết quả điều khiển bám sử dụng bộ điều khiển PID ở vận tốc 60 km/h b) Trạng thái mâm xoay cố định Khi cài đặt bộ điều khiển PID cho hệ thống lái điện với các thông số Kp =10, KI = 1.7, KD= 0.15, hiệu chỉnh tải trọng hai bánh xe dẫn hướng 4250 N, tiến hành đánh lái từ vị
File đính kèm:
luan_an_nghien_cuu_dieu_khien_he_thong_lai_dien_tren_o_to_co.pdf
bìa tóm tắt tiếng anh.pdf
bìa tóm tắt.pdf
chuong1.pdf
chuong2.pdf
chuong4.pdf
muc luc.pdf
phuluc11.pdf
Thông tin luận án (Trần Văn Lợi).docx
tóm tắt luận án.pdf
tóm tắt tieng anh.pdf
trang bia.pdf