Luận án Nghiên cứu khả năng cắt của đá mài xẻ rãnh nghiêng trên bề mặt đá mài chế tạo thử nghiệm tại Việt Nam khi mài phẳng vật liệu SKD11 nhiệt luyện
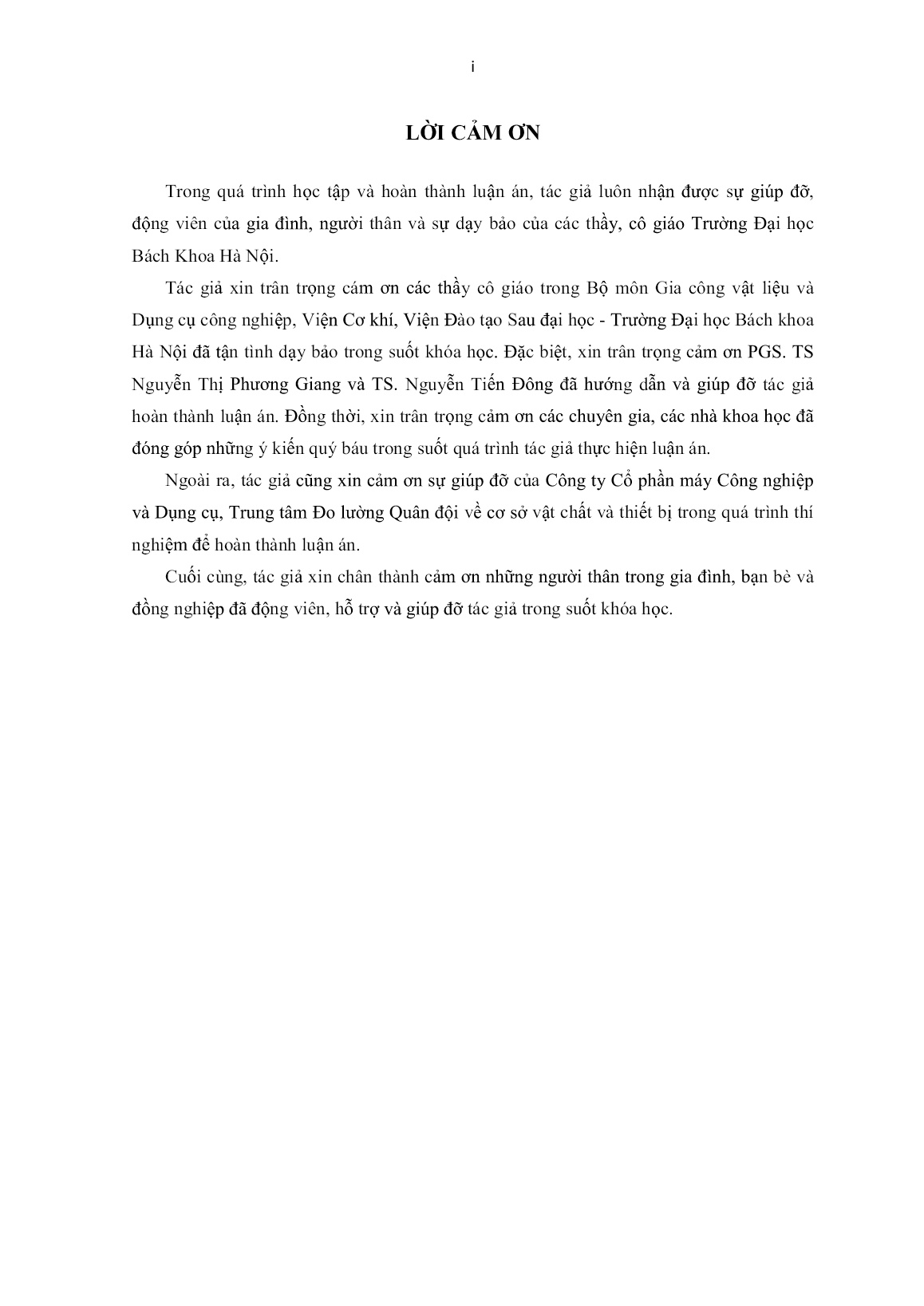
Trang 1
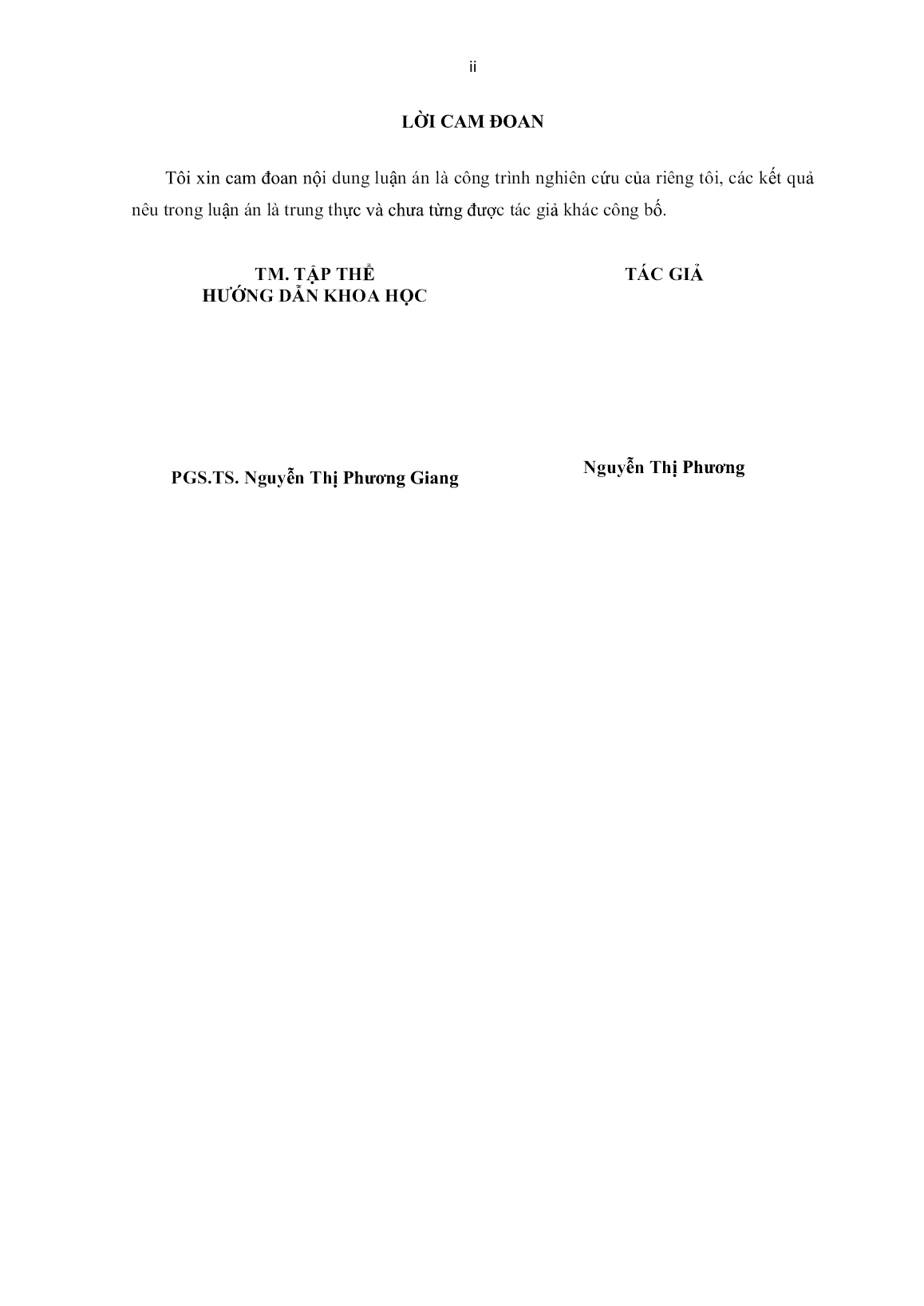
Trang 2
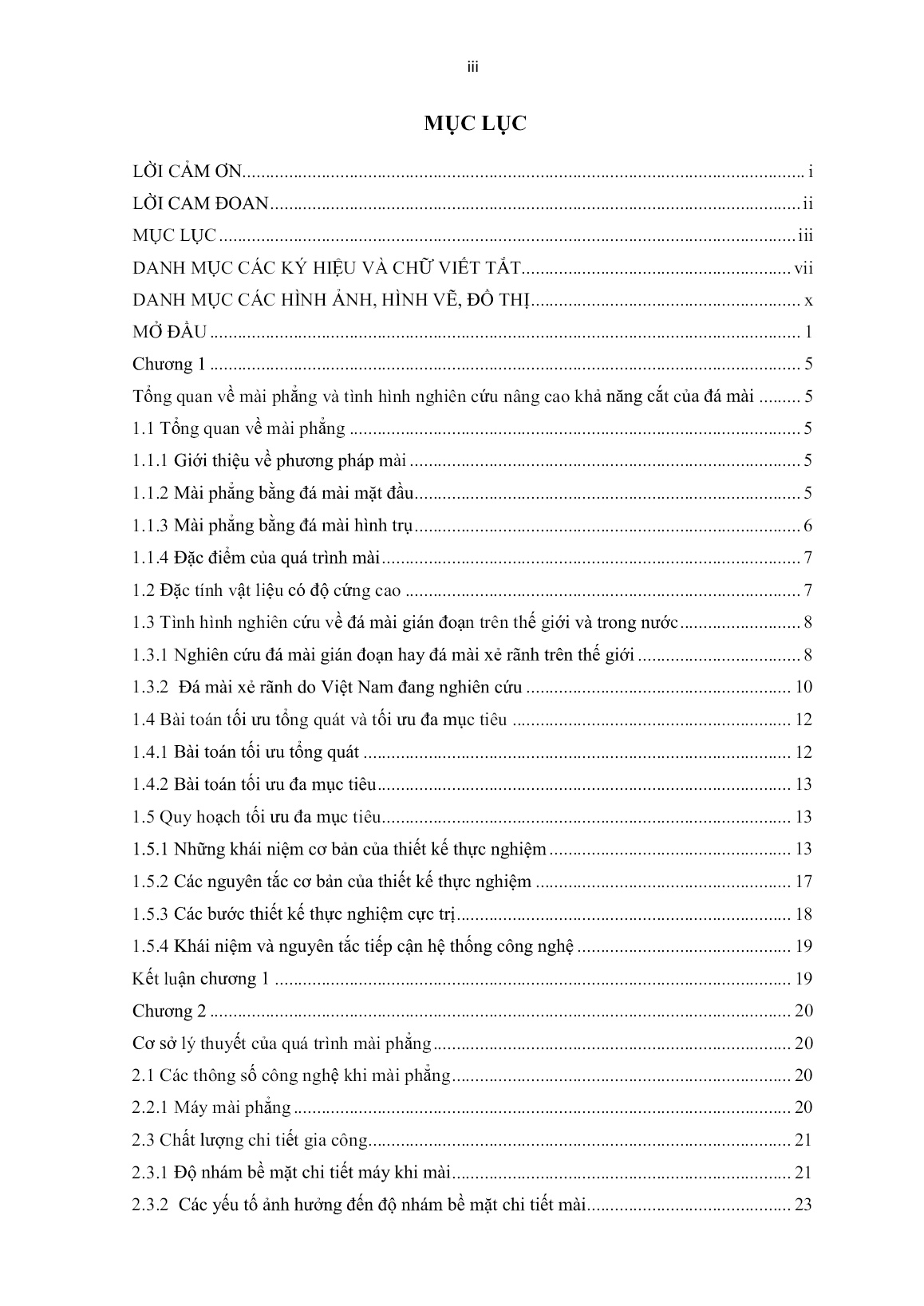
Trang 3
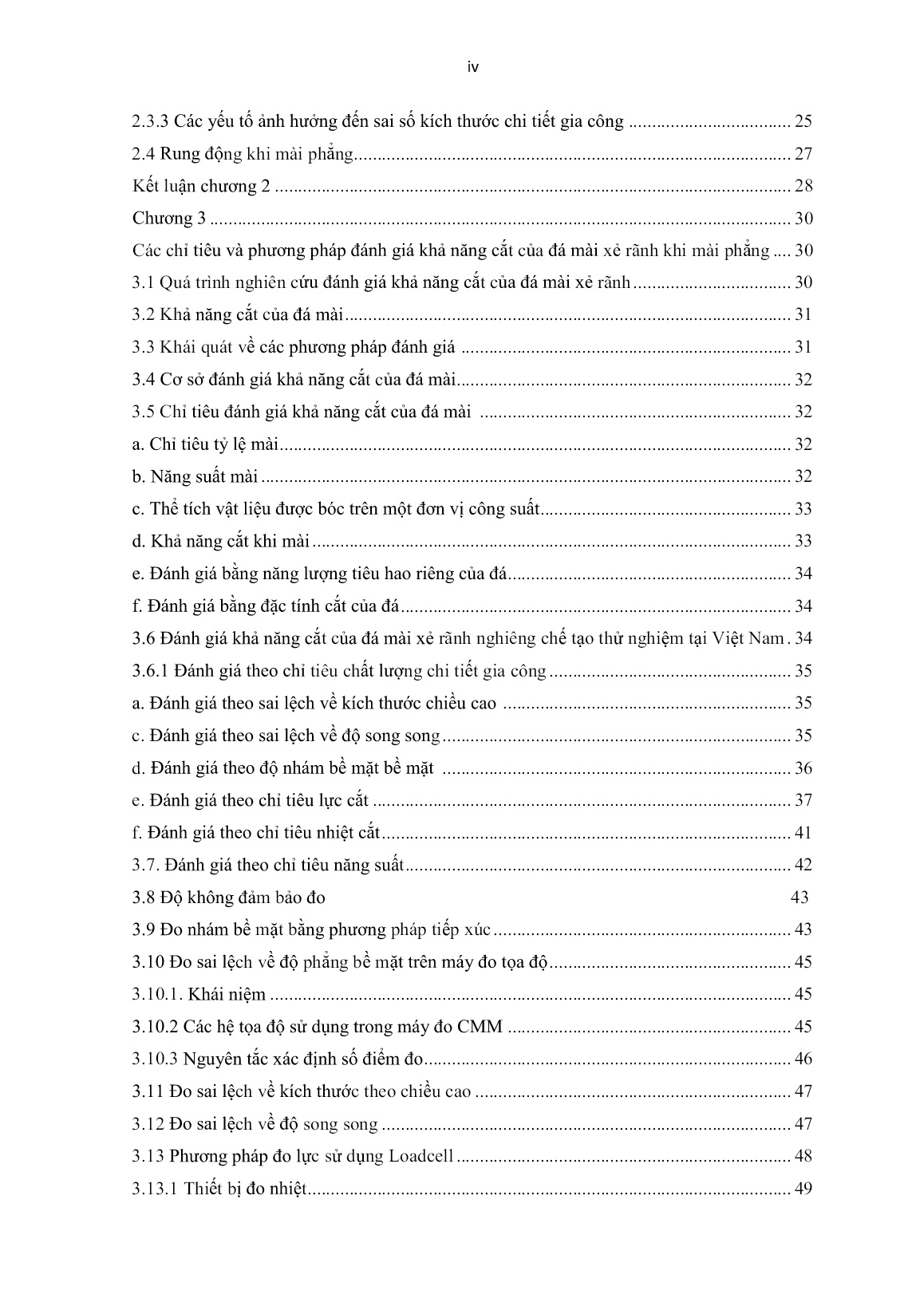
Trang 4
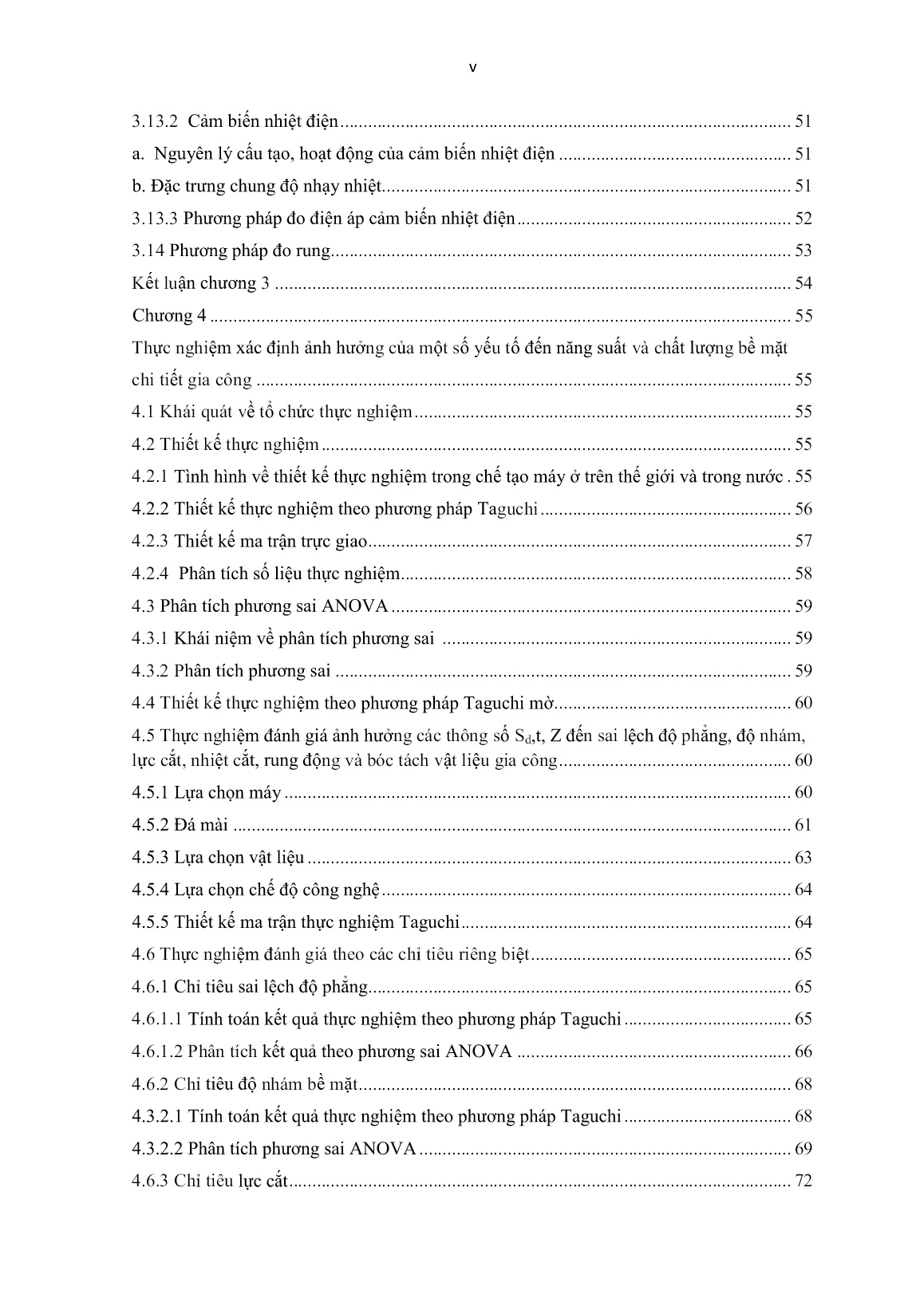
Trang 5
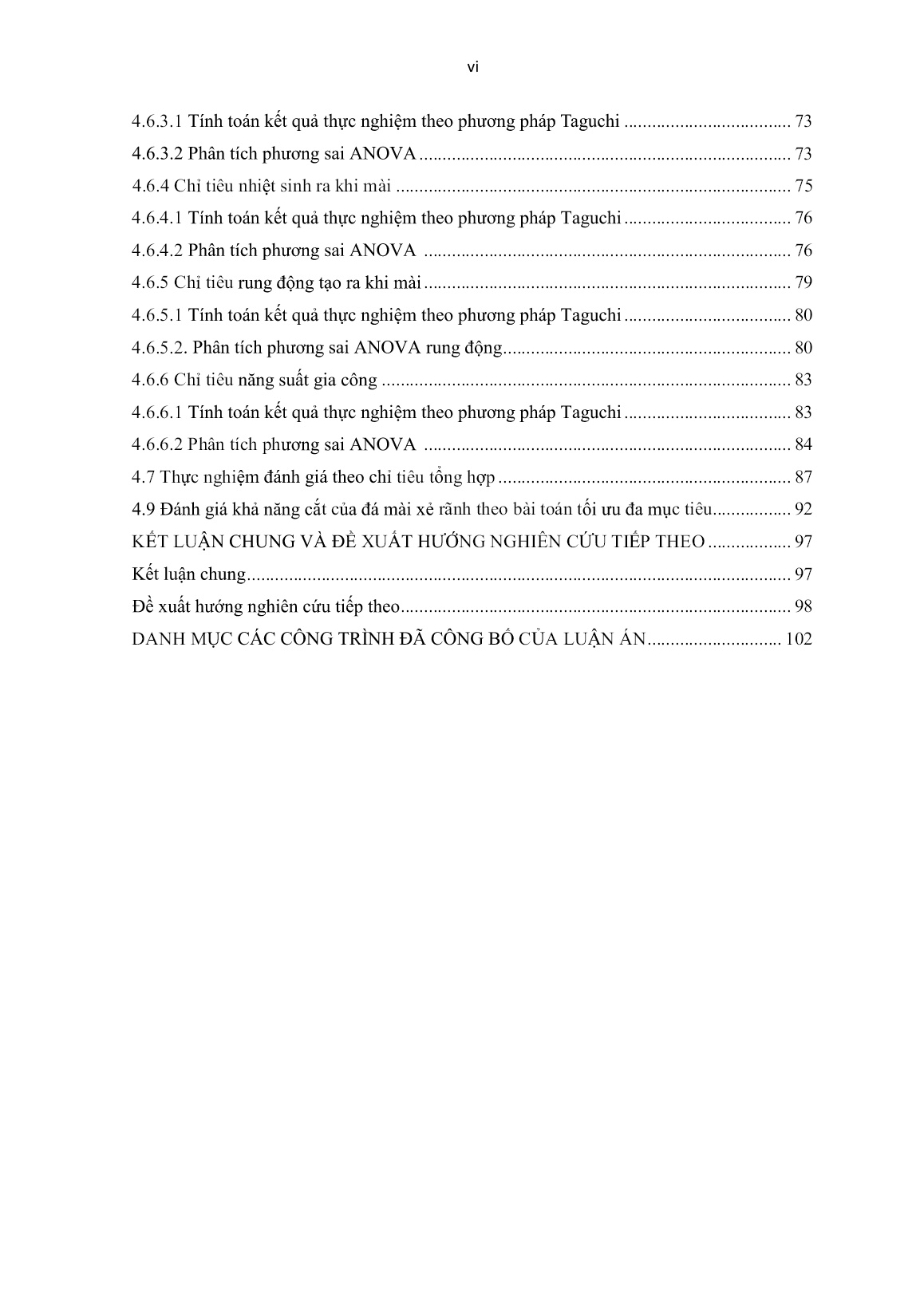
Trang 6
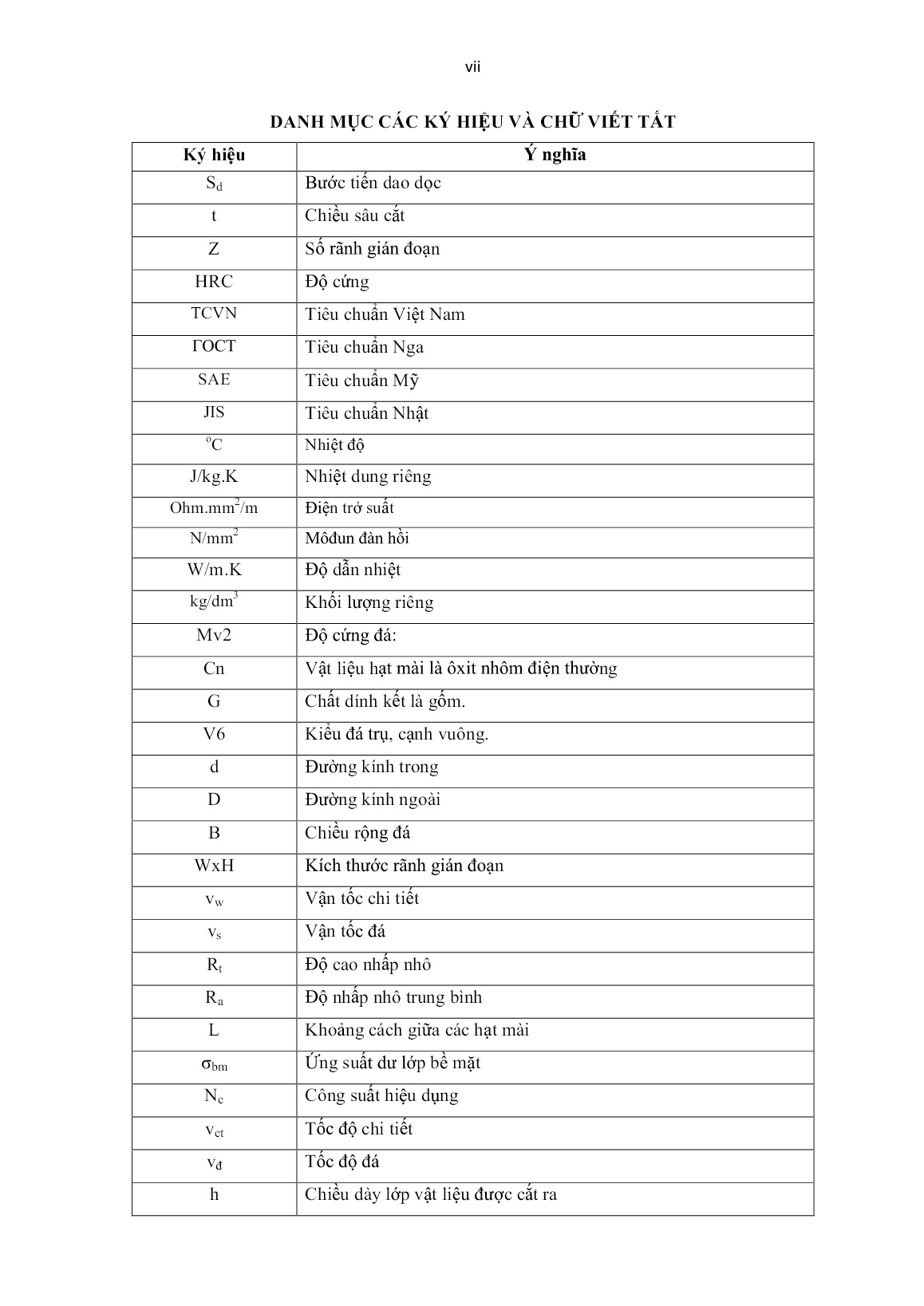
Trang 7
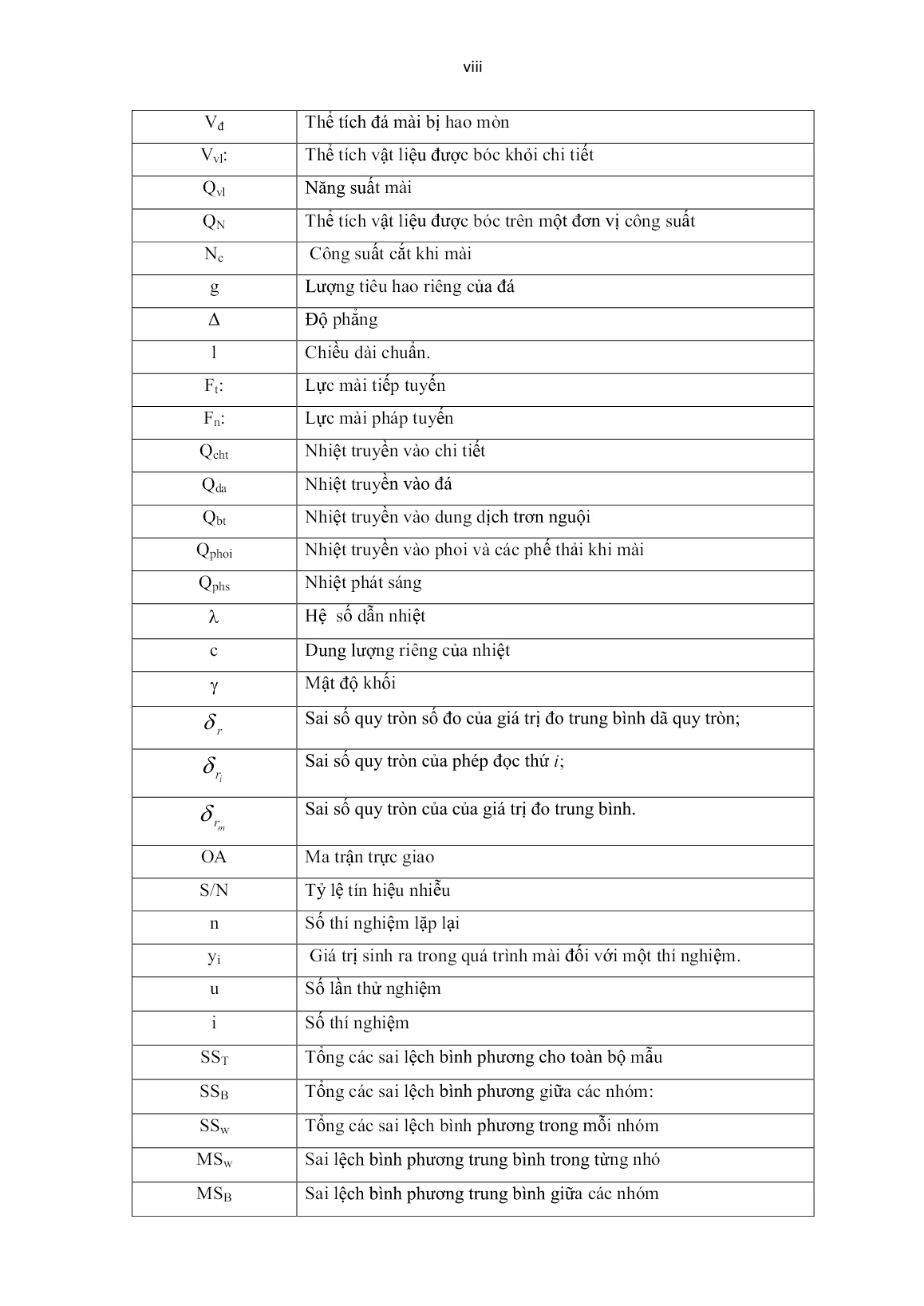
Trang 8
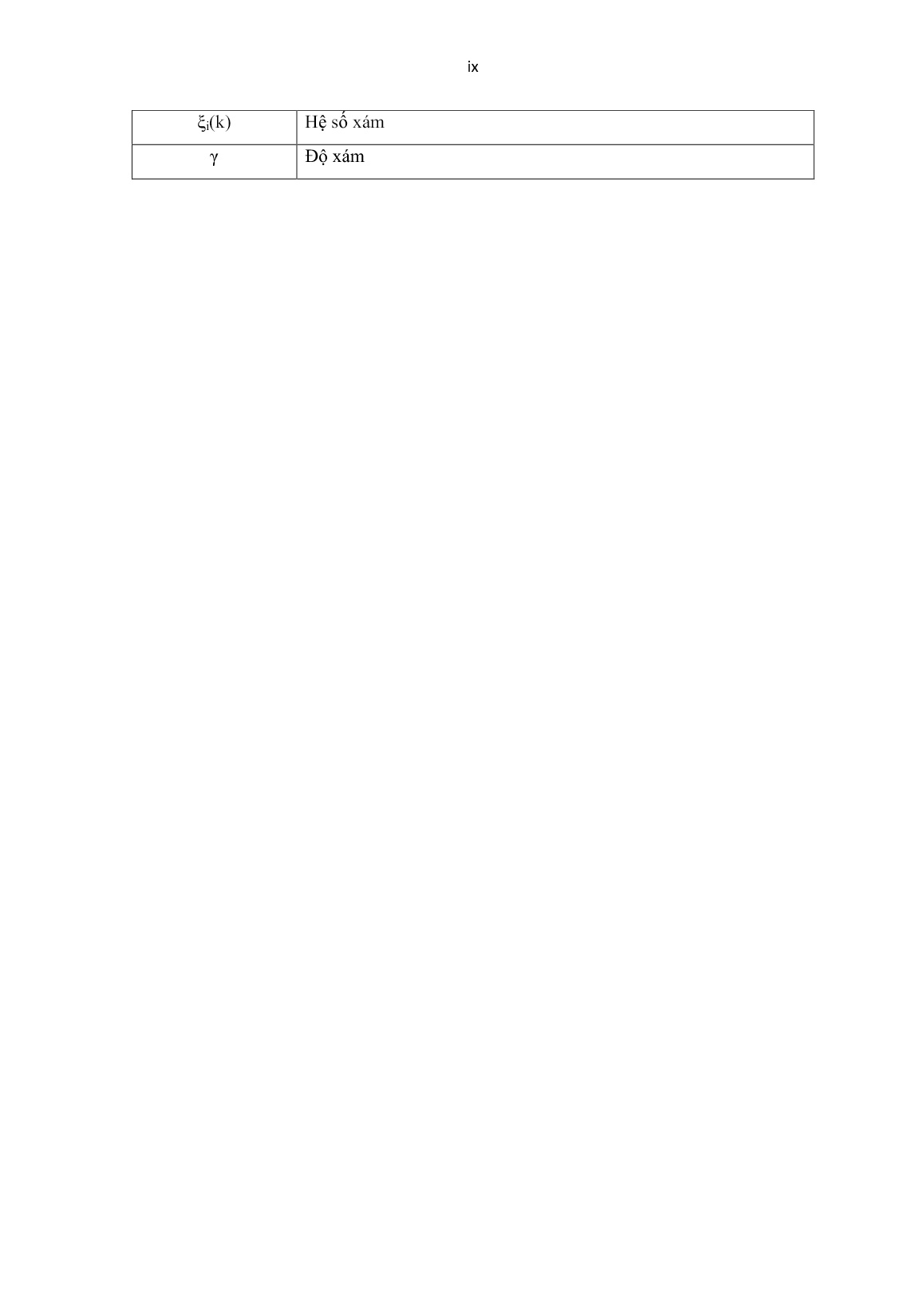
Trang 9
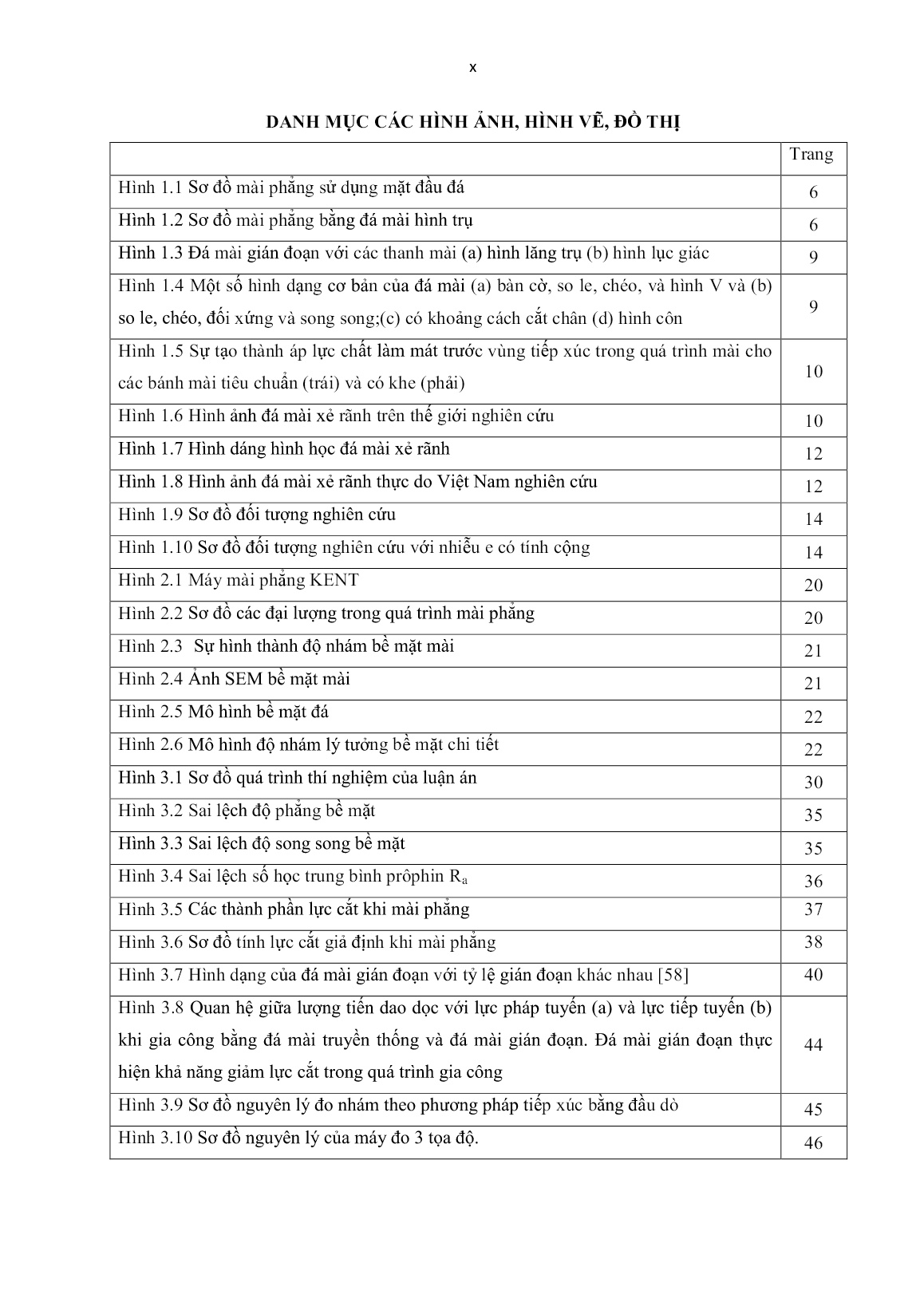
Trang 10
Tải về để xem bản đầy đủ
Bạn đang xem 10 trang mẫu của tài liệu "Luận án Nghiên cứu khả năng cắt của đá mài xẻ rãnh nghiêng trên bề mặt đá mài chế tạo thử nghiệm tại Việt Nam khi mài phẳng vật liệu SKD11 nhiệt luyện", để tải tài liệu gốc về máy hãy click vào nút Download ở trên.
Tóm tắt nội dung tài liệu: Luận án Nghiên cứu khả năng cắt của đá mài xẻ rãnh nghiêng trên bề mặt đá mài chế tạo thử nghiệm tại Việt Nam khi mài phẳng vật liệu SKD11 nhiệt luyện
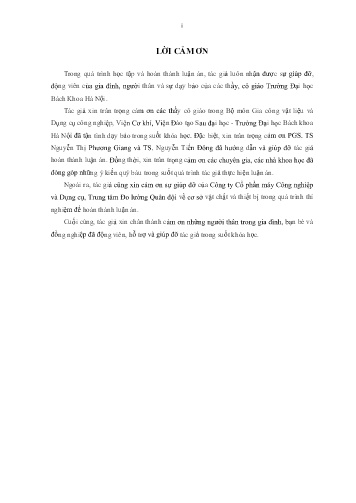
: Hằng số ảnh hưởng tới tuổi bền. T: Nhiệt độ cắt. 34 e. Đánh giá bằng năng lượng tiêu hao riêng của đá Lượng tiêu hao riêng của đá là lượng hạt mài cần thiết để cắt ra một đơn vị thể tích vật liệu (3.7) Trong đĩ: Vvl: Thể tích vật liệu được bĩc khỏi chi tiết Vđ: Thể tích đá mài bị hao mịn f. Đánh giá bằng đặc tính cắt của đá - Đánh giá bằng lực cắt khi gia cơng - Đánh giá bằng nhiệt cắt khi gia cơng - Đánh giá bằng rung động khi gia cơng - Chất lượng chi tiết gia cơng (chỉ tiêu độ phẳng, độ nhám) Đá mài cĩ khả năng cắt tốt là khi gia cơng lực cắt bé, cơng suất bé, nhiệt cắt thấp, độ mịn của đá ít nhưng năng suất gia cơng cao và chất lượng bề mặt tốt. Ngồi các chỉ tiêu đánh giá trên [7] cịn đánh giá theo chỉ tiêu: Quá trình phát tia lửa điện khi mài; Độ mịn và tuổi bền của đá; đánh giá bằng năng lượng đơn vị khi mài. 3.6 Đánh giá khả năng cắt của đá mài xẻ rãnh nghiêng chế tạo thử nghiệm tại Việt Nam Từ các phân tích ở trên và mục tiêu của luận án tác giả đưa ra các bài tốn tối ưu cục bộ sau: - Bài tốn về cực tiểu hĩa sai lệch độ phẳng bề mặt gia cơng - Bài tốn về cực tiểu hĩa độ nhám - Bài tốn về cực tiểu hĩa nhiệt phát sinh trong quá trình mài - Bài tốn về cực tiểu hĩa lực cắt trong quá trình mài - Bài tốn về cực tiêu hĩa rung động - Bài tốn về cực đại năng suất mài. - Thực nghiệm đánh giá ảnh hưởng tổng hợp của các thơng số đến khả năng cắt của đá mài gián đoạn. - Đánh giá tối ưu đa mục tiêu Như vậy, từ các bài tốn trên sẽ đánh giá khả năng cắt của đá mài xẻ rãnh nghiêng chế tạo tại Việt Nam khi mài phẳng vật liệu SKD11đã nhiệt luyện đánh giá theo các chỉ tiêu riêng biệt, chỉ tiêu tổng hợp để nâng cao chất lượng chi tiết gia cơng và năng suất gia cơng và giải bài tốn quy hoạch đa mục tiêu theo phương pháp Taguchi, phân tích quan hệ Taguchi - grey và phân tích phương sai (ANOVA). 35 3.6.1 Đánh giá theo chỉ tiêu chất lượng chi tiết gia cơng a. Đánh giá theo sai lệch về kích thước chiều cao [17][15] Kích thước danh nghĩa - Kích thước được dùng để xác định các kích thước giới hạn khi sử dụng các sai lệch trên và sai lệch dưới. Kích thước thực - Kích thước của một yếu tố (bề mặt) được xác định bằng phép đo. Kích thước giới hạn - Hai kích thước cực hạn cho phép của một yếu tố, giữa chúng chứa kích thước thực, kể cả kích thước giới hạn. Sai lệch - Hiệu đại số giữa kích thước thực, hoặc (kích thước giới hạn) và kích thước danh nghĩa tương ứng. b. Đánh giá theo sai lệch về độ phẳng bề mặt [15] Định nghĩa: Theo TCVN 384-1993 sai lệch về độ phẳng là khoảng cách lớn nhất từ các điểm của bề mặt thực tới mặt phẳng áp trong giới hạn của phần chuẩn (hình 3.2). Dung sai độ phẳng - Trị số cho phép lớn nhất của sai lệch về độ phẳng. mặt phẳng áp L2 L1 mặt phẳng thực Hình 3.2 Sai lệHìnhch đIII-12ộ phẳng bề mặt c. Đánh giá theo sai lệch về độ song song [15] Theo TCVN 2510-78 sai lệch về độ song song của mặt phẳng là hiệu khoảng cách lớn nhất và nhỏ nhất giữa các mặt phẳng áp trong giới hạn của phần chuẩn (hình 3.3 ). Hình 3.3 Sai lệch độ song song bề mặt 36 d. Đánh giá theo độ nhám bề mặt bề mặt [15] Các thơng số đánh giá độ nhám bề mặt: Để đánh giá độ nhám bề mặt người ta dùng các thơng số hình học của chúng, các thơng số này được xác định trong khoảng chiều dài chuẩn l và được tính tốn so với đường chuẩn (hình 3.4). Chiều dài chuẩn – chiều dài của phần bề mặt được chọn để đo độ nhám bề mặt,khơng tính đến dạng nhấp nhơ khác cĩ bước sĩng lớn hơn 1 (ví dụ sĩng bề mặt). Theo tiêu chuẩn TCVN 2511-1995 các thơng số độ nhám gồm cĩ: 1. Sai lệch số học trung bình prơphin Ra: Định nghĩa: Trị số số học trung bình của các giá trị tuyệt đối của sai lệch prơphin trong khoảng chiều dài chuẩn. 1 l R Y x dx a (3.8) l 0 Hay gần đúng ; 1 n Ra Yi (3.9) n i 1 Trong đĩ, l - Chiều dài chuẩn. Hình 3.4 Sai lệch số học trung bình prơphin Ra 2. Chiều cao nhấp nhơ prơphin theo mười điểm Rz: Định nghĩa: Trị số trung bình của tổng các giá trị tuyệt đối của chiều cao năm đỉnh cao nhất và chiều sâu của năm rãnh thấp nhất của prơphin trong khoảng chiều dài chuẩn. 5 5 Ypmi Yvmi i 1 i 1 R (3.10) z 5 Trong đĩ : -Ypmi : chiều cao đỉnh thứ i trong năm đỉnh cao nhất. -Yvmi : chiều sâu rãnh thứ i trong năm rãnh thấp nhất. 37 Trong sản xuất cho phép đánh giá độ nhám bề mặt bằng một trong hai thơng số trên. Việc chọn chi tiêu nào Ra hoặc Rz là tùy thuộc vào chất lượng bề mặt và đặc tính kết cấu của bề mặt. Trong sản xuất sử dụng phổ biến chỉ tiêu Ra vì nĩ cho phép ta đánh giá chính xác hơn và thuận lợi hơn những bề mặt cĩ yêu cầu độ nhám trung bình. Đối với những bề mặt cĩ độ nhám quá thơ hoặc nhỏ thì dùng chỉ tiêu Rz lại cho ta khả năng đánh giá chính xác hơn là dùng chỉ tiêu Ra. e. Đánh giá theo chỉ tiêu lực cắt Lực cắt khi mài thường khơng lớn (trung bình khoảng 300 ÷ 400N) vì tiết diện phoi cắt bé. Tuy nhiên cơng suất tiêu hao khi mài lớn vì tốc độ cắt khi mài cao. Xét những tác dụng trên hạt mài (hình 3.5). P: Lực cắt tồn phần Py: Lực cắt hướng kính Pz: Lực cắt tiếp tuyến Hình 3.5 Các thành phần lực cắt khi mài phẳng [1] Trên mặt trước của hạt mài cĩ các lực phân bố pháp tuyến N1, N2Nn và ma sát F1, F2,Fn. Lực cắt đặc trưng cho quá trình mài về phương diện vật lý. Lực cắt khi mài là nguồn động lực gây ra các biến dạng đàn hồi của hệ thống cơng nghệ, rung động, nhiệt cắt trong vùng gia cơng và nĩ cũng xác định chế độ mịn của đá mài. Khi lực cắt tăng, tuổi bền của đá giảm, độ chính xác gia cơng giảm và độ nhám bề mặt tăng lên. Đặc biệt, những thay đổi tức thời của lực cắt là nguyên nhân chính gây ra các dao động cưỡng bức của đầu đá tạo nên sĩng bề mặt và dạng sai số khác. Độ lớn của lực cắt phụ thuộc vào số lượng hạt mài đồng thời tham gia cắt, chiều dày lớp kim loại do mỗi hạt mài bĩc đi, hệ số ma sát giữa bề mặt chi tiết với đá mài. Lực cắt là thơng số cơ bản quyết định đặc tính mịn của đá mài. Lực P tác dụng trên hạt mài cĩ thể phân thành hai thành phần: Px theo phương tốc độ cắt, và Py nén hạt mài về phía bề mặt được gia cơng (hình 3.6). 38 Hình 3.6 Sơ đồ tính lực cắt giả định khi mài phẳng [1] Nếu phân tích hai lực này theo phương vuơng gĩc và song song với phương chạy dao sẽ cĩ hai thành phần Py và Pz. Xuất phát từ sơ đồ này cĩ mối quan hệ : (3.11) Với: γx: Gĩc trước của hạt mài tại điểm x. : Hệ số ma sát ở mặt trước của dụng cụ. Ta cĩ thể nhận xét rằng, cơng thức trên chỉ cĩ tính tương đối, vì gĩc γ phụ thuộc vào chiều sâu ăn vào kim loại và độ mịn của hạt mài.Chiều sâu này khơng cố định, mà thay đổi liên tục theo thời gian. Mặt khác số lượng hạt mài rất lớn, chiều cao nhơ ra khỏi chất dính kết khơng đều nhau, hệ số ma sát phụ thuộc rất nhiều vào điều kiện gia cơng như thành phần vật liệu, dung dịch trơn nguộiNhư vậy, cơng thức này chỉ cĩ ý nghĩa tham khảo. Nĩ khơng thể sử dụng trong các điều kiện sản xuất cụ thể. Khi nghiên cứu động học quá trình cắt của từng hạt mài riêng lẻ các nhà nghiên cứu đưa ra sơ đồ tính giả địnhcĩ thể thay thế các lực thành phần đĩ bằng hai lực tổng hợp N, F đặt tại điểm x (hình 3.6). Trên hình vẽ, N là lực cắt vuơng gĩc với mặt cắt tức thời của từng hạt mài, lực này cĩ xu hướng giữ cho hạt mài khơng tách ra khỏi bề mặt gia cơng và xác định từ điều kiện bền theo ứng suất cắt của vật liệu gia cơng. S là lực cần để thắng ma sát.T phản lực tạo bởi ma sát giữa bề mặt làm việc của hạt mài với vật liệu hạt mài khi chúng chuyển động tương đối với nhau.. Khi xây dựng mơ hình lực cắt cho quá trình mài [8] cũng đưa ra cơng thức tính lực cắt như sau: PN = N(sinγx + µcosγx ) (3.12) Pz = N(cosγx - µsinγx ) (3.13) PN: Lực cắt hướng kính tổng cộng Pz: Lực cắt tiếp tuyến tổng cộng 39 ’ Phân tích lực cân bằng N (cĩ giá trị bằng N) ra các thành phần: S1 tác dụng trên mặt trượt (mm); S2 tác dụng thẳng gĩc với mặt trượt(mm). Lực F (lực cân bằng của F) được phân thành T1, và T2. 0 Vì gĩc = 90 – (γx+ θ) (3.14) Nên S1 = N[cos( γx+ θ)+ µsin( γx+ θ)] (3.15) S2 = N[sin(x+ θ)+ µcos (x+ θ)] (3.16) Kim loại sẽ được cắt ra với điều kiện: ’ S1 = τs – μ .S2 (3.17) Trong đĩ: τs - ứng suất tiếp. f - diện tích cắt. µ’- hệ số ma sát trong trên mặt trượt. Giải các phương trình trên ta được: Pz = (3.18) PN = (3.19) γ θ Phân tích hai phương trình trên ta cĩ nhận xét sau ’ Lực Pz và PN phụ thuộc vào tính chất vật liệu gia cơng (τs, µ, μ ), kích thước kim loại bị cắt f, gĩc trước γ và các điều kiện cắt khác. Lực PN lớn hơn Pz và tỷ số tăng lên khi giảm chiều dày và tăng gĩc cắt. Lực tổng hợp R khi mài (hình 3.5) (bằng tích của P với số hạt mài đồng thời tham gia cắt) được phân tích thành 3 thành phần: lực tiếp tuyến Pz, lực hướng kính Py và lực chiều trục Px. Theo một trong các tài liệu về lý thuyết quá trình gia cơng vật liệu và gia cơng bằng hạt mài phân tích cho thấy: lực sinh ra khi mài là một trong các thơng số quan trọng để đánh giá khả năng gia cơng của đá. Thơng thường thành phần lực này sẽ được chia làm ba thành phần theo phương tiếp tuyến Pt, pháp tuyến Pn, và dọc trục Pz. Lực dọc trục Pz này thường được bỏ qua do sự ảnh hưởng tương đối nhỏ đến quá trình cắt. Chỉ cịn lại lực pháp tuyến Pn là lực cĩ ảnh hưởng lớn tới quá trình hình thành bề mặt gia cơng và độ nhám bề mặt gia cơng. Trong khi đĩ, lực tiếp tuyến lại cĩ ảnh hưởng chính chủ yếu đến cơng suất của máy và tuổi bền làm việc của đá.. Do lực cắt thay đổi liên tục trong quá trình gia cơng làm cho biến dạng đàn hồi của hệ thống cơng nghệ và vận tốc bĩc kim loại thực tế cũng thay đổi theo, ứng suất nhiệt tại các 40 điểm khác nhau của bề mặt gia cơng sẽ khơng giống nhau. Chất lượng bề mặt vật mài do đĩ bị giảm, các cơ cấu máy bị mịn trước thời hạn và khơng đều nhau, tuổi bền đá giảm. Từ nhiều phân tích cho rằng “ lực cắt là nguyên nhân gây ra sự gãy vỡ của vật liệu gia cơng trong quá trình cắt” [21] đã cơng bố một loại đá mài trịn cĩ bề mặt làm việc theo từng đoạn như hình 3.7 với tỷ lệ và sự phân bố khác nhau được thực hiện thí nghiệm theo các thơng số như trong bảng 3.1. Kết quả thí nghiệm cho thấy loại đá mới này cĩ ảnh hưởng rõ rệt tới việc giảm lực cắt trong quá trình gia cơng khi so sánh với đá mài truyền thống ở cùng chế độ gia cơng. Hình 3.7 Hình dạng của đá mài gián đoạn với tỷ lệ gián đoạn khác nhau [21] Chú thích 40_1:1 Trong đĩ: 40 là số rãnh đá mài 1:1: Tỷ lệ khoảng cách gián đoạn Bảng 3.1 Các thơng số thí nghiệm thực hiện về: vật liệu gia cơng, vận tốc cắt, lượng tiến đá, chiều sâu cắt [21]. Thép hợp kim: 4140 Vật liệu mài Kích thước:50x5x10mm Đá mài gián đoạn 32AR46-JV40 Vận tốc cắt 29.4m/s Lượng tiến dao 40-150mm/s Chiều sâu cắt 25µm Kết quả cũng chỉ ra rằng, khoảng cách gián đoạn càng lớn và số lượng gián đoạn càng ít thì lực cắt càng giảm đáng kể như trong (hình 3.7). Trong nghiên cứu này chưa đưa ra mối 41 quan hệ giữa lượng giảm của lực cắt với khoảng cách và số lượng gián đoạn trên bề mặt đá [21]. f. Đánh giá theo chỉ tiêu nhiệt cắt Trong quá trình mài, hầu hết cơng suất cắt được chuyển hố thành nhiệt năng, chỉ một phần rất nhỏ cơng suất cắt được chuyển hố thành năng lượng tiềm ẩn làm thay đổi mạng tinh thể của vật liệu. Nhiệt cắt khi mài sẽ gây ra các biến đổi về pha và cấu trúc của vật liệu, thay đổi tính chất của lớp kim loại bề mặt gia cơng như độ cứng lớp kim loại ứng suất dư và vết cháy, vết nứt tế vi trên mặt mài. Lượng nhiệt tỏa ra phân bố trong chi tiết, phoi đá và dung dịch trơn nguội xác định theo phương trình sau : (Ft.Vda) .(60 ÷70 %) = Qcht + Qda + Qbt + Qphoi + Qphs (3.15) Ở đây: (Ft.Vda) - nhiệt do cơng suất chuyển hố thành. Qcht - nhiệt truyền vào chi tiết Qda - nhiệt truyền vào đá Qbt - nhiệt truyền vào dung dịch trơn nguội Qphoi - nhiệt truyền vào phoi và các phế thải khi mài Qphs - nhiệt phát sáng Các nghiên cứu cho thấy, khoảng 70-80% lượng nhiệt toả ra khi mài chuyển vào chi tiết gia cơng và đá mài. Lượng nhiệt này cĩ thể xác định theo cơng thức sau: 1 k c da da Qcht = ; Qda= ; với k = . (3.16) 1 k 1 k c cht cht Với: - Hệ số dẫn nhiệt c - dung lượng riêng của nhiệt - mật độ khối Nhiệt cắt khi mài cĩ thể phân ra ba dạng : 1. Nhiệt độ tức thời tại điểm xảy ra quá trình cắt do một hạt mài gây ra. Tuỳ thuộc vào điều kiện mài, nhiệt độ này cĩ thể thay đổi từ 1000oC tới nhiệt độ nĩng chảy của kim loại. Thời gian tác động rất ngắn 2. Nhiệt độ tiếp xúc trung bình trên tồn bộ chiều rộng đá cĩ giá trị từ 250o đến 1100oC. Dưới tác động của nhiệt độ tiếp xúc trên lớp kim loại bề mặt cĩ thể xuất hiện vết cháy và vết nứt tế vi 42 3. Nhiệt độ trung bình của chi tiết. Tuỳ thuộc vào điều kiện và thời gian mài, tính chất của dung dịch trơn nguội, nhiệt độ trung bình sẽ cĩ giá trị từ 20o đến 350oC. Nhiệt độ trung bình sẽ gây ra biến dạng nhiệt của chi tiết gia cơng Quá trình xuất hiện và phân bố của nhiệt cắt khi mài phụ thuộc vào nhiều yếu tố. Kết quả nghiên cứu của nhiều tác giả cho thấy tồn tại một số quy luật sau: Khi các thành phần của chế độ cắt (v, s, t) tăng thì nhiệt cắt tăng Vận tốc cắt quan hệ với nhiệt độ theo quy luật hàm mũ, hệ số mũ dao động từ khoảng 0,25 - 0,35. Đường kính đá tăng thì nhiệt độ mài giảm Chất dính kết của đá cũng cĩ ảnh hưởng tới nhiệt độ khi mài. Đá mài cĩ chất dính kết bakêlit cĩ khả năng giảm cường độ toả nhiệt tốt hơn so với đá cĩ chất kết dính keramic Khả năng dẫn nhiệt của vật liệu giảm sẽ làm tăng nhiệt độ mài. Để giảm nhiệt độ mài phải giảm số nguồn tạo nhiệt hoặc tăng hiệu suất tạo nhiệt bằng các biện pháp như chọn sơ đồ mài tối ưu, chọn đặc tính đá, chế độ cắt, dung dịch trơn nguội phù hợp. 3.7. Đánh giá theo chỉ tiêu năng suất Theo cơng thức 3.2 trang 33 3.8 Độ khơng đảm bảo đo [16] Độ khơng đảm bảo đo u của phép đo bao gồm hai thành phần là thành phần ngẫu nhiên, được thể hiện qua phạm vi tin cậy v và thành phần sai số hệ thống thay đổi, nhưng ước đốn được độ lệch chuẩn st như sau: u = (|v| + | |) (3.18) Độ khơng đảm bảo đo cịn được tính theo cơng thức: u = v2 2 (3.19) Mà vẫn đúng, vì thành phần được đốn theo các giá trị lớn nhất, tuy rằng các giá trị này ít khi xuất hiện. Trong đĩ - Tổng bình phương m sai số hệ thống ước đốn được. m 2 2 r (3.20) r 1 Nếu thành phần <1/3v, thì cĩ thể bỏ qua và u = v, mà khơng làm tăng giá trị của u hơn 5%. Các sai số hệ thống thay đổi nhưng ước đốn đợc r , thường là sai số của dụng cụ đo, sai số chế tạo mẫu kích thước, độ khơng đảm bảo đo do nhiệt độ, độ khơng đảm bảo đo do lực 43 đo, độ khơng đảm bảo đo của phép đo xác định từng sai số hệ thống khơng đổi riêng rẽ trong tổng các sai số hệ thống khơng đổi, sai số do quy trịn số đo. 0,5 - Giá trị độ chia đối với một phép đọc đến phần mười vạch chia, cịn sai số do ri quy trịn đo đối với các dụng cụ đo chỉ thị hiện số thì của bước số. Từ nhiều kết quả đọc riêng rẽ được làm trịn số, tính được giá trị đo trung bình đã quy trịn và sai số quy trịn số đo của nĩ theo cơng thức: 2 2 (3.21) r ri rm Trong đĩ : - Sai số quy trịn số đo của giá trị đo trung bình dã quy trịn; - Sai số quy trịn của phép đọc thứ i; - Sai số quy trịn của của giá trị đo trung bình. Thơng thường khi đọc đến 0,1 giá trị độ chia, thì giá trị đo cĩ một sai số ước đốn đã đư- ợc tính vào độ lệch chuẩn và vì vậy giá trị đo này cĩ cĩ sai số quy trịn = 0. Sai số quy trịn sẽ được tính vào độ khơng đảm bảo của phép đo: 2 2 2 u = v r (3.22) 1 2 2 Song nếur nh < ut với ut = v , thì cĩ thể bỏ qua mà khơng làm cho u tăng r 3 t hơn 5% giár itrị của nĩ. 3.9 Đo nhám bề mặt bằng phương pháp tiếp xúc rm Khi dịch chuyển một mũi dị theo hướng vuơng gĩc với mặt vật đo, nĩ sẽ chuyển vị theo nhấp nhơ bề mặt của chi tiết, sau khi khuếch đại chuyển vị đưa vào bộ chỉ thị hoặc ghi đồ thị, sẽ cho biết giá trị của nhấp nhơ. Lực đo của mũi dị nhỏ vào khoảng 0,3 1mN, nên khơng làm xước bề mặt của chi tiết. Mũi dị được chế tạo bằng kim cương hoặc đá saphia,cĩ dạng hình cơn hoặc hình tháp. Bán kính đầu dị được quy định theo tiêu chuẩn ISO 3274: r 2 1 m;r 5 2 m;r 10 3 m Bán kính mũi dị ảnh hưởng đến kết quả đo nhám .thực nghiệm cho thấy rằng, khi đo nhám với độ chính xác cao sử dụng mũi dị cĩ bán kính 2µm, thơng thường sử dụng mũi dị cĩ bán kính là 5µm. 44 0 0 10 10 Gĩc mũi dị theo quy định là 60 và 90 . Chú ý rằng, gĩc này cũng cĩ ảnh 5 5 hưởng đến kết quả đo. Chất lượng đồ thị nhám ghi được phụ thuộc vào vận tốc đầu dị. Đĩ là nguyên tắc của các máy đo nhám theo phương pháp tiếp xúc .máy này được gọi là Profinmet dùng để đo độ nhám độ sáng,biên dạng hoặc các mặt bậc tế vi. Sơ đồ nguyên lý làm việc của hệ thống đo nhám bề mặt theo phương pháp tiếp xúc được chỉ dẫn trên hình (3.8). Hình 3.8 Sơ đồ nguyên lý đo nhám theo phương pháp tiếp xúc bằng đầu dị Trong đĩ: 1, 2: bộ cảm ứng 3: đường sống trượt 4: đầu tựa 5: mũi dị Khi đo hệ thống dị của máy hoặc tỳ lên bề mặt chi tiết đo nhờ đầu tựa tạo thành hệ thống dị dao động, hoặc khơng dùng đầu tựa, tạo thành hệ thống dị tự do. Ở hệ thống dị dao động, cĩ thể đo được các dịch chuyển tương đối giữa đầu tựa và mũi dị.cịn trong hệ thống dị tự do phải điều chỉnh cần thận bề mặt đo dựa theo đường sống trượt thẳng của đầu dị. Đường sống trượt cĩ thể dùng loại đệm khí ,cĩ chiều dài 100 mm, sai số sống trượt nhỏ hơn 0,1µm. Khi dị, đầu tựa tiếp xúc vào chi tiết đo, chuyển dịch tương đối giữa đầu tựa và mũi dị được bộ cảm ứng 1 tiếp nhận. Chuyển dịch này phản ánh độ nhám bề mặt, cịn độ sĩng và sai lệch hình dạng được bộ cảm ừng tiếp nhận bằng đầu tựa, nếu khơng cho đầu tựa tiếp xúc vào bề mặt đo, dịch chuyển của mũi dị sẽ được ghi trên đồ thị và qua đồ thi này sẽ xác định được sai lệch hình dạng của bề mặt chi tiết đo. Hệ thống đo nhám loại này cĩ thể đo độ nhám trên các chiều dài khác nhau, chiều dài lớn nhất tới 40 mm. Chuyển dịch theo phương đứng của mũi dị được khuyếch đại tới 100.000 lần. Phạm vi đo nhám từ 0,01 250m . 45 3.10 Đo sai lệch về độ phẳng bề mặt trên máy đo tọa độ[16] 3.10.1. Khái niệm Máy đo tọa độ (Coordinate Measuring Machine - CMM) là thiết bị vạn năng, dùng để thực hiện các phép đo các thơng số hình học theo phương pháp một tiếp điểm. Thơng số cần đo được tính tốn từ tọa độ các điểm đo, nhờ các thuật tốn và chương trình tính tốn xử lý được cài đặt sẵn trong máy, rồi hiển thị kết quả đo trên màn hình. Các máy đo ba tọa độ cịn được dùng để quét hình dạng của vật thể, dùng để thiết kế ngược khi tạo mẫu. Máy đo tọa độ thường là các máy đo cĩ 3 phương chuyển vị đo x, y, z. Bàn đo được làm bằng đá granít. Đầu đo được gắn trên giá đầu đo, được lắp trên thân trượt theo phương z. Khi đầu đo được điều chỉnh đến một điểm đo nào đĩ, thì 3 đầu đọc sẽ cho ta biết tọa độ x, y, z tương ứng với độ chính xác cĩ thể lên đến 0,1 micromet (hình 3.9). Máy CMM cĩ thể được chia ra hai loại: loại tiếp xúc và khơng tiếp xúc. Loại máy đo kiểu tiếp xúc sử dụng đầu dị và trong quá trình đo thì đầu dị này tiếp xúc với bề mặt chi tiết cần đo. Cịn loại máy cịn lại sử dụng “đầu dị” quang học chẳng hạn như dùng tia Laser, dùng sĩng siêu âm tần số thấp,... Ngồi việc đo kích thước của vật thể, các máy CMM cịn cĩ một số ứng dụng khác. Hình 3.9 Sơ đồ nguyên lý của máy đo 3 tọa độ. 3.10.2 Các hệ tọa độ sử dụng trong máy đo CMM Trong cơng nghệ đo tọa độ, cĩ thể sử dụng các hệ tọa độ ba chiều như sau (hình 3.9): - Hệ tọa độ Đề các với ba tọa độ dài x, y và z (hình 3.9, a); - Hệ tọa độ trụ với hai tọa độ dài , z và một tọa độ gĩc (hình 3.9, b); - Hệ tọa độ cầu với một tọa độ dài r và hai tọa độ gĩc và (hình 3.9, c). Tọa
File đính kèm:
luan_an_nghien_cuu_kha_nang_cat_cua_da_mai_xe_ranh_nghieng_t.pdf
Nội dung tóm tắt luận án.pdf
Thông tin đưa trên mạng tiếng anh.pdf
Thông tin đưa trên mạng tiếng việt.pdf