Tóm tắt Luận án Nghiên cứu chế tạo và đánh giá khả năng cắt gọt của đá mài CBN liên kết kim loại bằng phương pháp mạ điện
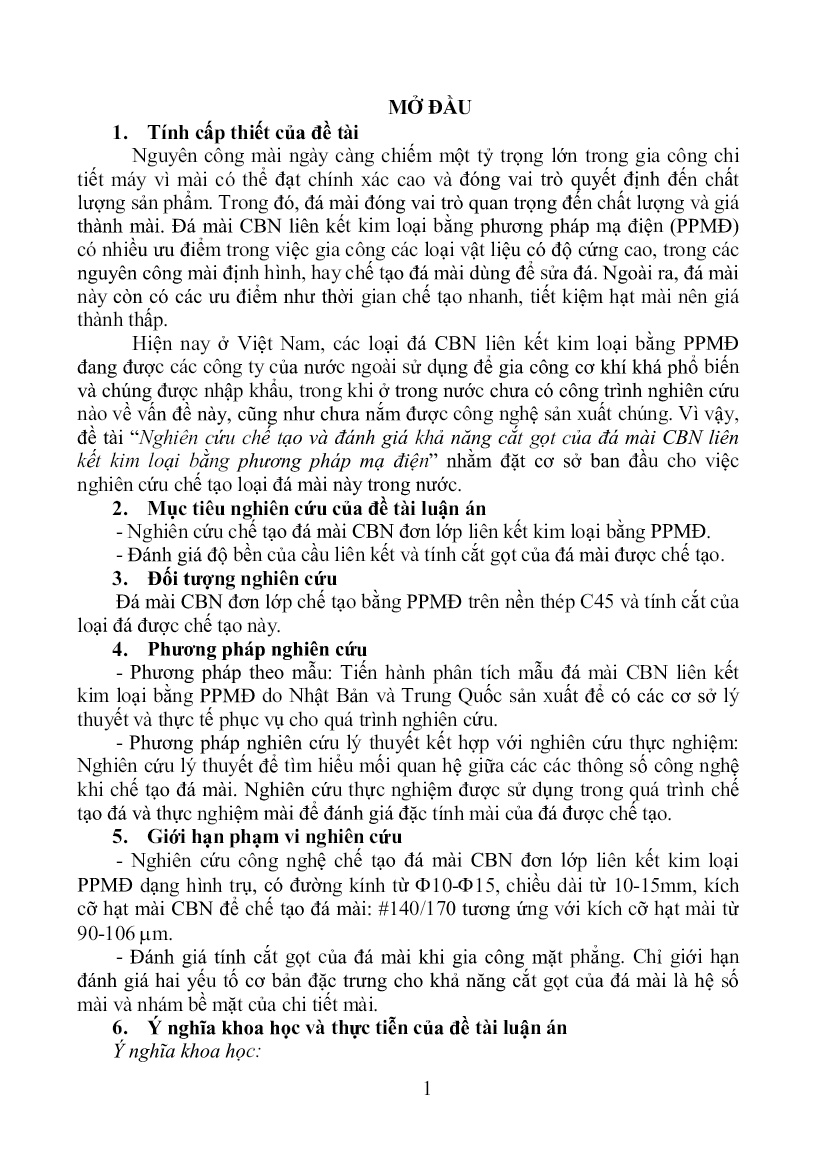
Trang 1
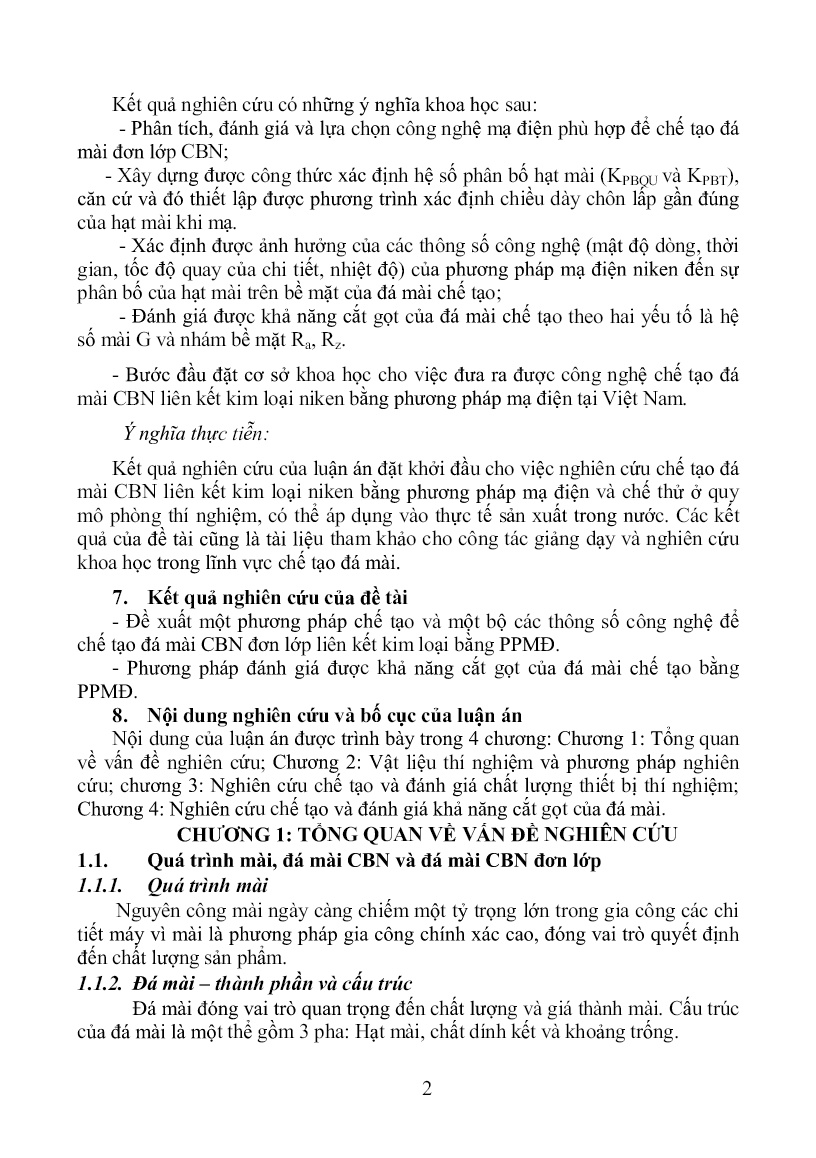
Trang 2
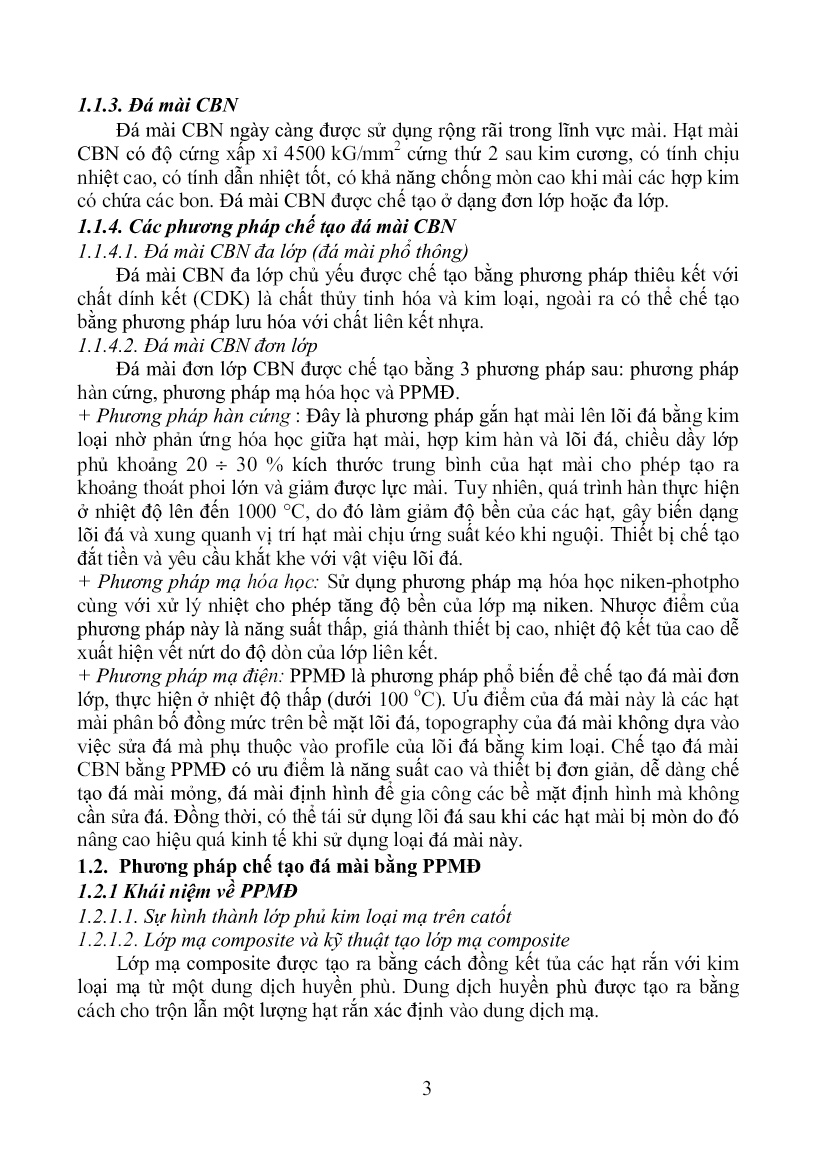
Trang 3
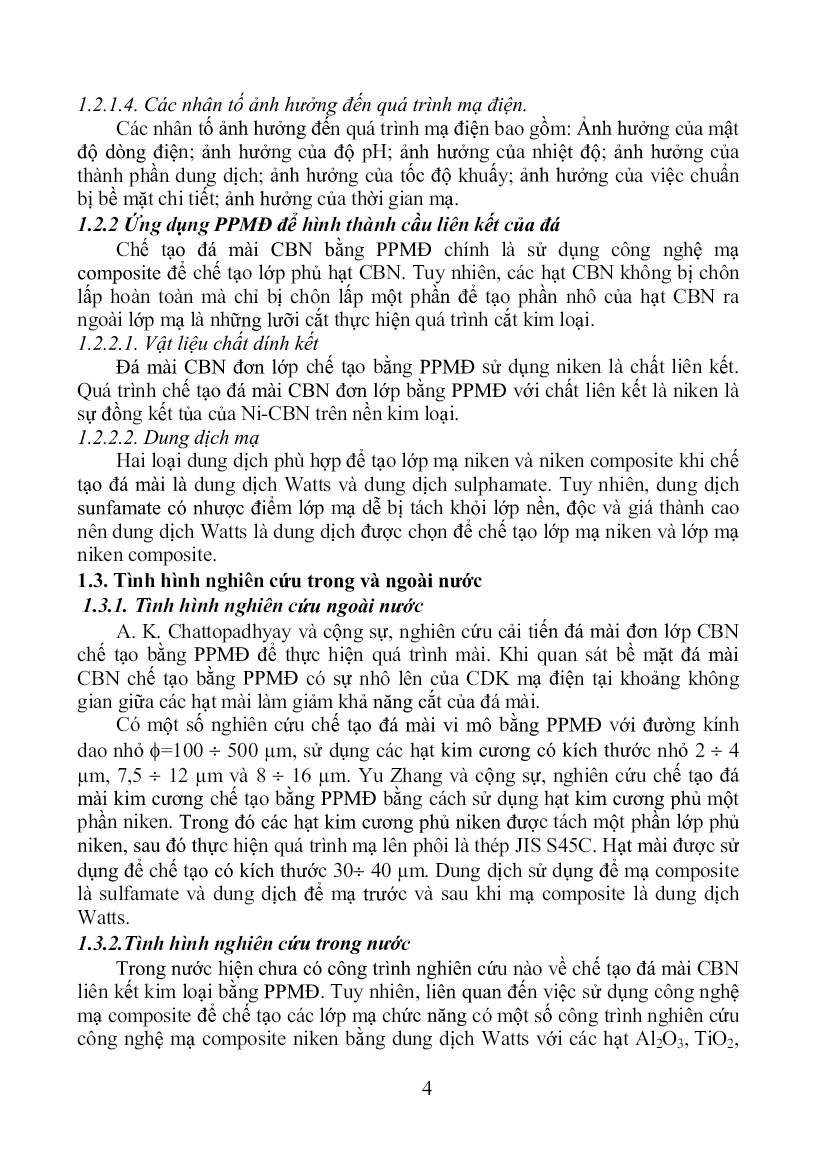
Trang 4
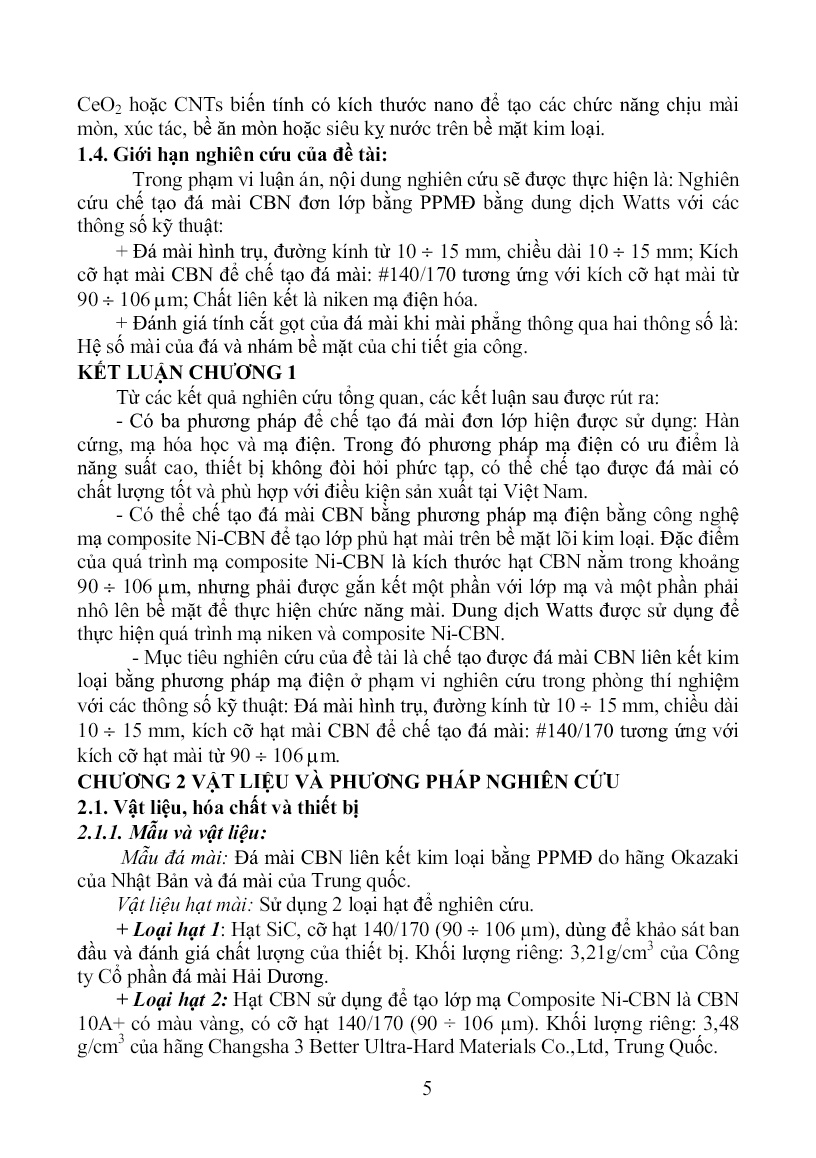
Trang 5
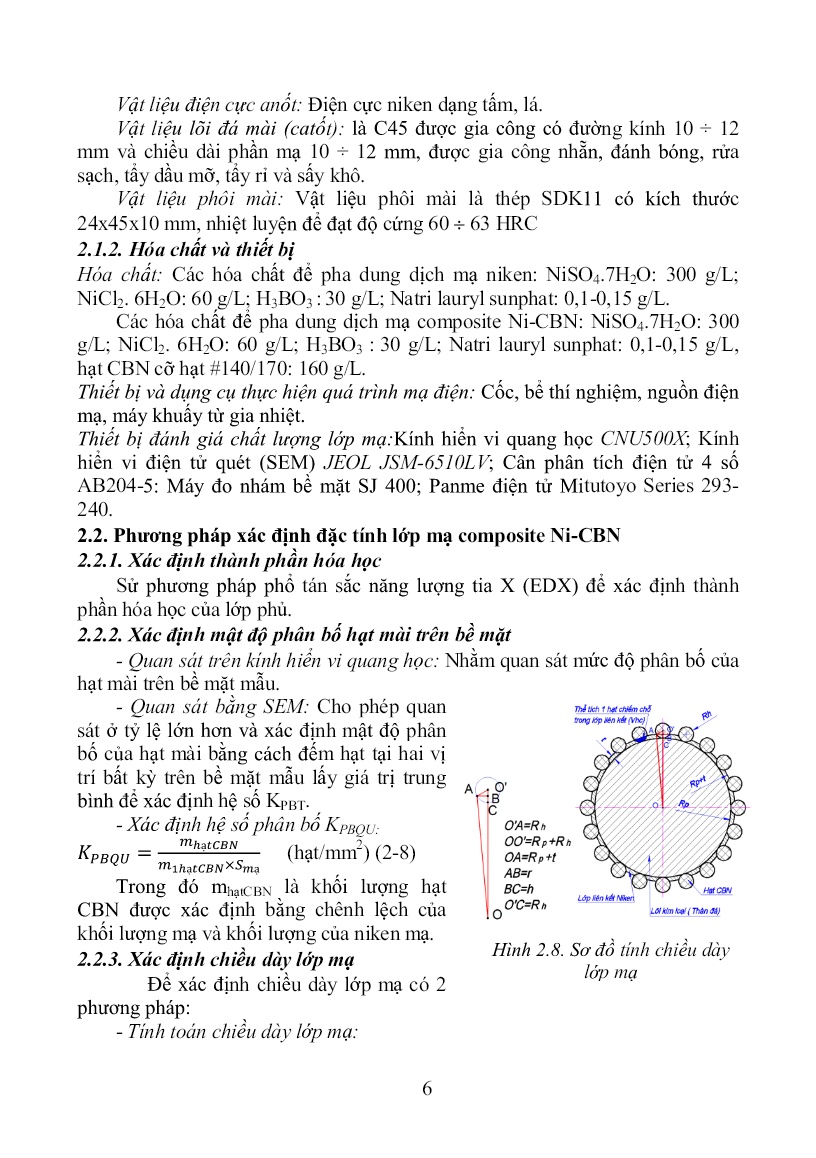
Trang 6

Trang 7
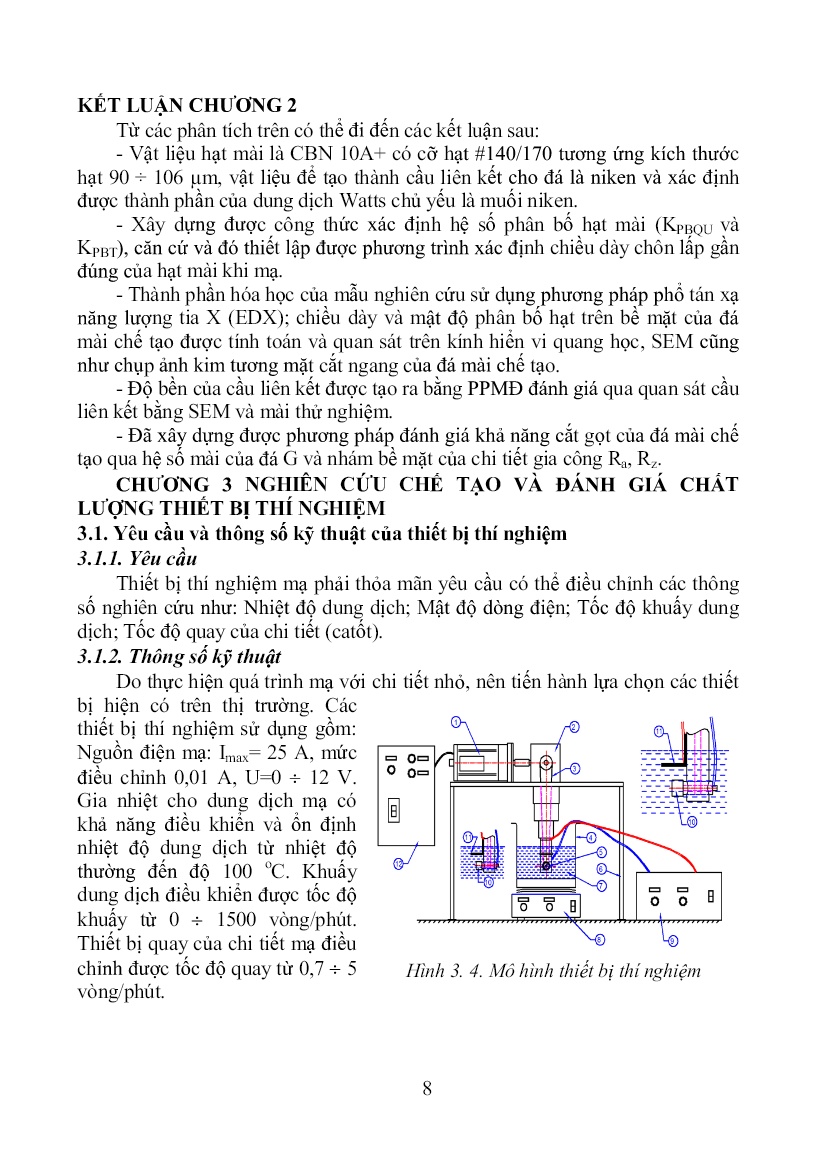
Trang 8
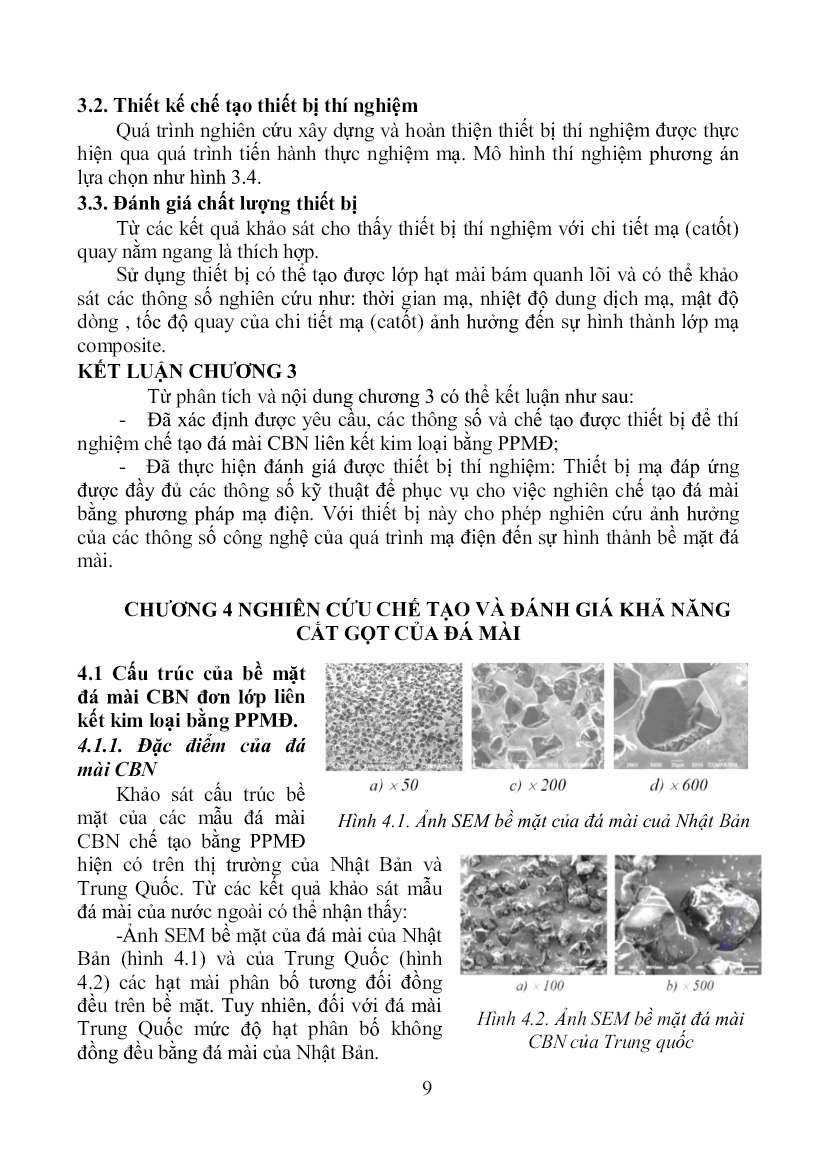
Trang 9
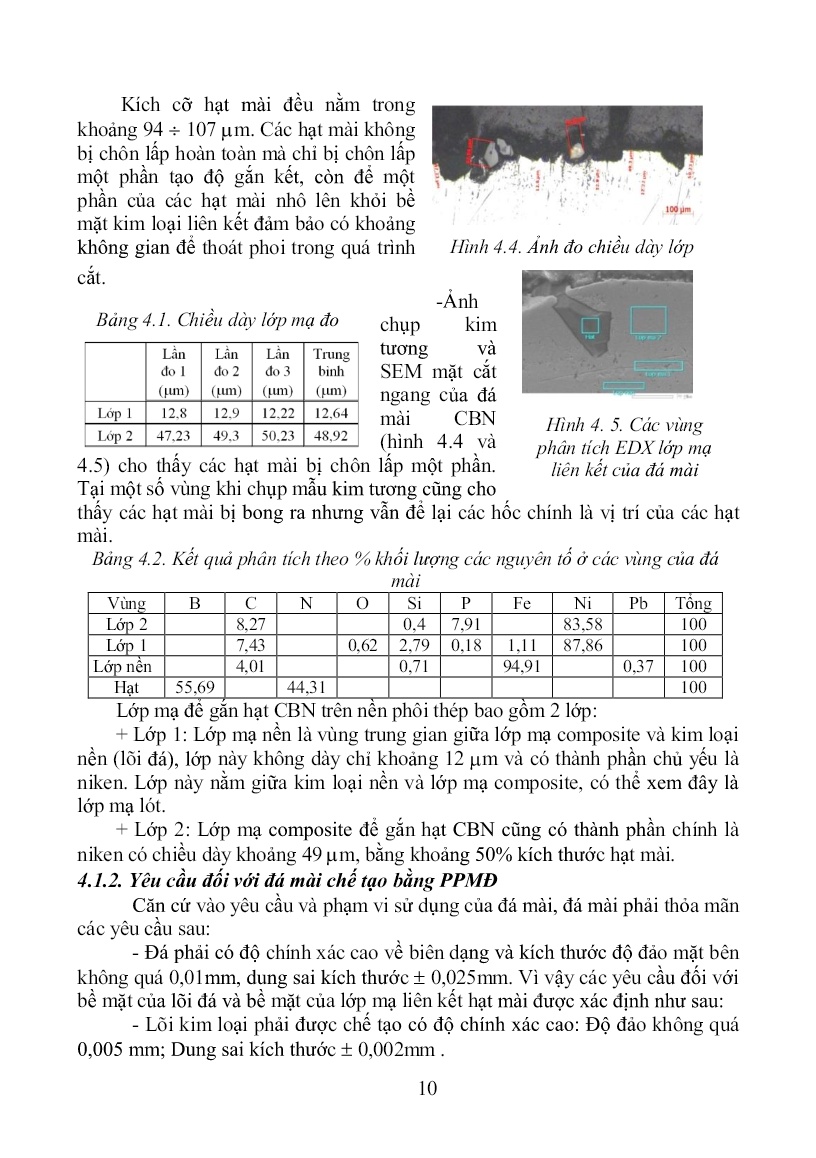
Trang 10
Tải về để xem bản đầy đủ
Bạn đang xem 10 trang mẫu của tài liệu "Tóm tắt Luận án Nghiên cứu chế tạo và đánh giá khả năng cắt gọt của đá mài CBN liên kết kim loại bằng phương pháp mạ điện", để tải tài liệu gốc về máy hãy click vào nút Download ở trên.
Tóm tắt nội dung tài liệu: Tóm tắt Luận án Nghiên cứu chế tạo và đánh giá khả năng cắt gọt của đá mài CBN liên kết kim loại bằng phương pháp mạ điện
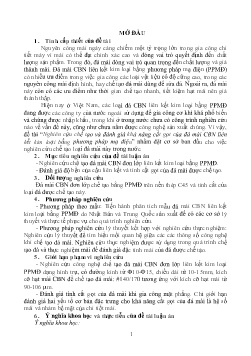
X (EDX) để xác định thành phần hóa học của lớp phủ. 2.2.2. Xác định mật độ phân bố hạt mài trên bề mặt - Quan sát trên kính hiển vi quang học: Nhằm quan sát mức độ phân bố của hạt mài trên bề mặt mẫu. - Quan sát bằng SEM: Cho phép quan sát ở tỷ lệ lớn hơn và xác định mật độ phân bố của hạt mài bằng cách đếm hạt tại hai vị trí bất kỳ trên bề mặt mẫu lấy giá trị trung bình để xác định hệ số KPBT. - Xác định hệ số phân bố KPBQU: (hạt/mm 2 ) (2-8) Trong đó mhạtCBN là khối lượng hạt CBN được xác định bằng chênh lệch của khối lượng mạ và khối lượng của niken mạ. 2.2.3. Xác định chiều dày lớp mạ Để xác định chiều dày lớp mạ có 2 phương pháp: - Tính toán chiều dày lớp mạ: Hình 2.8. Sơ đồ tính chiều dày lớp mạ 7 Sơ đồ tính chiều dày lớp mạ được mô tả như hình 2.8, với các giả thiết sau: Các hạt mài phân bố đồng đều trên bề mặt của lớp mạ; Các hạt mài hình cầu và có kích thước bằng nhau Rh; Khối lượng niken mạ tính theo định luật Faraday. Chiều dày lớp mạ được xác định từ phương trình 2-19: (2-19) Trong đó : ; ; ; - Đo chiều dày lớp mạ: Tiến hành làm mẫu cắt ngang mẫu đá mài sau đó tiến hành đo chiều dày lớp mạ và chụp ảnh SEM. 2.2.4. Đánh giá độ bền liên kết của hạt mài và kim loại liên kết Máy mài thử nghiệm được thể hiện trên hình 2.9, các chuyển động của các trục được điều khiển bằng CNC với mức dịch chuyển nhỏ nhất là 1µm. Thực hiện mài thực nghiệm theo các điều kiện mài: Vận tốc mài: 12,56 m/s; Chiều sâu mài: 0,005; 0,010 mm; Bước tiến dao: 300 mm/phút; Mài nghịch; Không bôi trơn. Quan sát cầu liên kết và tiến hành mài thực nghiệm để đánh giá khả năng cắt gọt của đá mài, qua đó đánh giá độ bền cầu liên kết. Khả năng cắt của đá mài được đánh giá thông qua hai chỉ tiêu hệ số mài và nhám bề mặt của chi tiết gia công. 2.3. Quy hoạch thực nghiệm (QHTN) nghiên cứu ảnh hƣởng của một số thông số công nghệ đến sự phân bố hạt trong lớp mạ composite Ni-CBN 2.3.1. Chọn các thông số nghiên cứu: Nhiều yếu tố ảnh hưởng đến sự phân bố của hạt mài khi chế tạo đá mài, tuy nhiên, giới hạn chỉ nghiên cứu 4 yếu tố: Nhiệt độ dung dịch mạ: 50 - 60 o C, mật độ dòng: 1 8 A/dm 2 , thời gian mạ composite: 5 15 phút, tốc độ quay chi tiết: 0,7 3 vòng/phút. 2.3.2. Phương pháp QHTN Để nghiên cứu ảnh hưởng các thông số đến sự phân bố của hạt mài khi chế tạo đá mài, tiến hành thay đổi từng thông số, còn các thông số còn lại cố định, sau đó lại lần lượt làm tương tự với các thông số khác. Căn cứ vào kết quả thí nghiệm nhận được chọn một bộ 3 thông số hợp lý để nghiên cứu ảnh hưởng đồng thời nhằm tìm ra hàm mục tiêu là mật độ phân bố của hạt mài. Sử dụng phương pháp QHTN bề mặt chỉ tiêu (Response Surface Design) với dạng thiết kế hỗn hợp tâm xoay (CCD- Central Composite Design). Hình 2.9. Máy mài thực nghiệm 8 KẾT LUẬN CHƢƠNG 2 Từ các phân tích trên có thể đi đến các kết luận sau: - Vật liệu hạt mài là CBN 10A+ có cỡ hạt #140/170 tương ứng kích thước hạt 90 ÷ 106 µm, vật liệu để tạo thành cầu liên kết cho đá là niken và xác định được thành phần của dung dịch Watts chủ yếu là muối niken. - Xây dựng được công thức xác định hệ số phân bố hạt mài (KPBQU và KPBT), căn cứ và đó thiết lập được phương trình xác định chiều dày chôn lấp gần đúng của hạt mài khi mạ. - Thành phần hóa học của mẫu nghiên cứu sử dụng phương pháp phổ tán xạ năng lượng tia X (EDX); chiều dày và mật độ phân bố hạt trên bề mặt của đá mài chế tạo được tính toán và quan sát trên kính hiển vi quang học, SEM cũng như chụp ảnh kim tương mặt cắt ngang của đá mài chế tạo. - Độ bền của cầu liên kết được tạo ra bằng PPMĐ đánh giá qua quan sát cầu liên kết bằng SEM và mài thử nghiệm. - Đã xây dựng được phương pháp đánh giá khả năng cắt gọt của đá mài chế tạo qua hệ số mài của đá G và nhám bề mặt của chi tiết gia công Ra, Rz. CHƢƠNG 3 NGHIÊN CỨU CHẾ TẠO VÀ ĐÁNH GIÁ CHẤT LƢỢNG THIẾT BỊ THÍ NGHIỆM 3.1. Yêu cầu và thông số kỹ thuật của thiết bị thí nghiệm 3.1.1. Yêu cầu Thiết bị thí nghiệm mạ phải thỏa mãn yêu cầu có thể điều chỉnh các thông số nghiên cứu như: Nhiệt độ dung dịch; Mật độ dòng điện; Tốc độ khuấy dung dịch; Tốc độ quay của chi tiết (catốt). 3.1.2. Thông số kỹ thuật Do thực hiện quá trình mạ với chi tiết nhỏ, nên tiến hành lựa chọn các thiết bị hiện có trên thị trường. Các thiết bị thí nghiệm sử dụng gồm: Nguồn điện mạ: Imax= 25 A, mức điều chỉnh 0,01 A, U=0 12 V. Gia nhiệt cho dung dịch mạ có khả năng điều khiển và ổn định nhiệt độ dung dịch từ nhiệt độ thường đến độ 100 o C. Khuấy dung dịch điều khiển được tốc độ khuấy từ 0 1500 vòng/phút. Thiết bị quay của chi tiết mạ điều chỉnh được tốc độ quay từ 0,7 5 vòng/phút. Hình 3. 4. Mô hình thiết bị thí nghiệm 9 3.2. Thiết kế chế tạo thiết bị thí nghiệm Quá trình nghiên cứu xây dựng và hoàn thiện thiết bị thí nghiệm được thực hiện qua quá trình tiến hành thực nghiệm mạ. Mô hình thí nghiệm phương án lựa chọn như hình 3.4. 3.3. Đánh giá chất lƣợng thiết bị Từ các kết quả khảo sát cho thấy thiết bị thí nghiệm với chi tiết mạ (catốt) quay nằm ngang là thích hợp. Sử dụng thiết bị có thể tạo được lớp hạt mài bám quanh lõi và có thể khảo sát các thông số nghiên cứu như: thời gian mạ, nhiệt độ dung dịch mạ, mật độ dòng , tốc độ quay của chi tiết mạ (catốt) ảnh hưởng đến sự hình thành lớp mạ composite. KẾT LUẬN CHƢƠNG 3 Từ phân tích và nội dung chương 3 có thể kết luận như sau: - Đã xác định được yêu cầu, các thông số và chế tạo được thiết bị để thí nghiệm chế tạo đá mài CBN liên kết kim loại bằng PPMĐ; - Đã thực hiện đánh giá được thiết bị thí nghiệm: Thiết bị mạ đáp ứng được đầy đủ các thông số kỹ thuật để phục vụ cho việc nghiên chế tạo đá mài bằng phương pháp mạ điện. Với thiết bị này cho phép nghiên cứu ảnh hưởng của các thông số công nghệ của quá trình mạ điện đến sự hình thành bề mặt đá mài. CHƢƠNG 4 NGHIÊN CỨU CHẾ TẠO VÀ ĐÁNH GIÁ KHẢ NĂNG CẮT GỌT CỦA ĐÁ MÀI 4.1 Cấu trúc của bề mặt đá mài CBN đơn lớp liên kết kim loại bằng PPMĐ. 4.1.1. Đặc điểm của đá mài CBN Khảo sát cấu trúc bề mặt của các mẫu đá mài CBN chế tạo bằng PPMĐ hiện có trên thị trường của Nhật Bản và Trung Quốc. Từ các kết quả khảo sát mẫu đá mài của nước ngoài có thể nhận thấy: -Ảnh SEM bề mặt của đá mài của Nhật Bản (hình 4.1) và của Trung Quốc (hình 4.2) các hạt mài phân bố tương đối đồng đều trên bề mặt. Tuy nhiên, đối với đá mài Trung Quốc mức độ hạt phân bố không đồng đều bằng đá mài của Nhật Bản. Hình 4.1. Ảnh SEM bề mặt của đá mài cuả Nhật Bản Hình 4.2. Ảnh SEM bề mặt đá mài CBN của Trung quốc 10 Kích cỡ hạt mài đều nằm trong khoảng 94 107 m. Các hạt mài không bị chôn lấp hoàn toàn mà chỉ bị chôn lấp một phần tạo độ gắn kết, còn để một phần của các hạt mài nhô lên khỏi bề mặt kim loại liên kết đảm bảo có khoảng không gian để thoát phoi trong quá trình cắt. -Ảnh chụp kim tương và SEM mặt cắt ngang của đá mài CBN (hình 4.4 và 4.5) cho thấy các hạt mài bị chôn lấp một phần. Tại một số vùng khi chụp mẫu kim tương cũng cho thấy các hạt mài bị bong ra nhưng vẫn để lại các hốc chính là vị trí của các hạt mài. Bảng 4.2. Kết quả phân tích theo % khối lượng các nguyên tố ở các vùng của đá mài Vùng B C N O Si P Fe Ni Pb Tổng Lớp 2 8,27 0,4 7,91 83,58 100 Lớp 1 7,43 0,62 2,79 0,18 1,11 87,86 100 Lớp nền 4,01 0,71 94,91 0,37 100 Hạt 55,69 44,31 100 Lớp mạ để gắn hạt CBN trên nền phôi thép bao gồm 2 lớp: + Lớp 1: Lớp mạ nền là vùng trung gian giữa lớp mạ composite và kim loại nền (lõi đá), lớp này không dày chỉ khoảng 12 m và có thành phần chủ yếu là niken. Lớp này nằm giữa kim loại nền và lớp mạ composite, có thể xem đây là lớp mạ lót. + Lớp 2: Lớp mạ composite để gắn hạt CBN cũng có thành phần chính là niken có chiều dày khoảng 49 m, bằng khoảng 50% kích thước hạt mài. 4.1.2. Yêu cầu đối với đá mài chế tạo bằng PPMĐ Căn cứ vào yêu cầu và phạm vi sử dụng của đá mài, đá mài phải thỏa mãn các yêu cầu sau: - Đá phải có độ chính xác cao về biên dạng và kích thước độ đảo mặt bên không quá 0,01mm, dung sai kích thước 0,025mm. Vì vậy các yêu cầu đối với bề mặt của lõi đá và bề mặt của lớp mạ liên kết hạt mài được xác định như sau: - Lõi kim loại phải được chế tạo có độ chính xác cao: Độ đảo không quá 0,005 mm; Dung sai kích thước 0,002mm . Hình 4. 5. Các vùng phân tích EDX lớp mạ liên kết của đá mài Hình 4.4. Ảnh đo chiều dày lớp mạ Bảng 4.1. Chiều dày lớp mạ đo 11 - Đối với lớp mạ phủ hạt CBN: Các hạt mài CBN có cùng kích cỡ hạt mài và phân bố đều trên bề mặt của lõi kim loại, đảm bảo phân bố đồng mức. Phần nhô của hạt mài lên trên chất dính kết (40 55) % kích thước hạt mài phải đủ để đảm bảo khoảng thoát phoi trong quá trình cắt. Lực liên kết của chất dính kết với hạt mài phải đủ để neo giữ hạt mài trong quá trình cắt, nên phần chìm trong chất dính kết phải đủ lớn từ (55 60) % kích thước hạt mài . Mô hình hóa liên kết của hạt mài với CDK: Qua khảo sát bề mặt đá mài CBN chế tạo bằng PPMĐ hiện đang sử dụng ở Việt Nam và một số tài liệu liên quan, có thể mô hình hóa liên kết của đá mài như hình 4.6. Chiều cao khoảng (55 60) % kích thước trung bình của hạt mài. Nếu lớn quá sẽ làm phần nhô của các hạt mài nhô ít làm giảm khoảng thoát phoi và thoát nhiệt trong quá trình mài sẽ gây ra lực cắt và nhiệt cắt tăng, do đó dễ làm hạt mài bị bong ra khỏi chất dính kết. Mật độ của hạt mài và sự phân bố của hạt mài trên bề mặt của đá: Tùy theo yêu cầu sử dụng và điều kiện làm việc của đá, sự phân bố các hạt mài có thể dày và thưa. Trong quá trình mạ, để đảm bảo sự phân bố đồng đều trên các vùng là rất cần thiết. 4.1.3. Tiến trình chế tạo lớp bề mặt đá mài Quá trình gắn các hạt mài CBN lên bề mặt lõi kim loại được thực hiện các bước sau: Bước 1: Đánh sạch bề mặt bằng bàn chải, giấy nhám; Bước 2: Làm sạch sơ bộ bề mặt bằng dung dịch để tẩy dầu mỡ; Bước 3: Rửa sạch bằng nước; Bước 4: Làm sạch bằng dung dịch axít HCl 15% để tẩy gỉ và hoạt hóa bề mặt; Bước 5: Rửa sạch bằng nước; Bước 6: Mạ lớp niken lót; Bước 7: Mạ lớp Ni- CBN lần 1: tạo sự bám dính của hạt- gắn hạt; Bước 8: Mạ lớp Ni lần 2: gắn chặt các hạt trên bề mặt thân – chôn lấp hạt. 4.1.4. Chỉ tiêu đánh giá chất lượng lớp mạ composite Ni-CBN Chất lượng lớp mạ được quan tâm đến 2 yếu tố: Mức độ bám, phân bố của hạt trên bề mặt phôi mạ và độ bền liên kết của hạt mài với lớp kim loại liên kết. a) Mức độ phân bố của hạt mài và chiều dày lớp mạ Độ bám và phân bố của hạt mài trên bề mặt phôi mạ được đánh giá nhờ sử dụng kính hiển vi quang học cũng như kính hiển vi điện tử quét (SEM) và phương pháp cân khối lượng. Sự phân bố của hạt mài có thể được xác định thông qua hệ số KPBT và KPBQU. Hệ số KPBT được tính bằng giá trị trung bình mật độ hạt đếm trên ảnh SEM chụp bề mặt tại hai vị trí ngẫu nhiên. Còn KPBQU được xác định theo công thức 2-8. Chiều dày lớp mạ được xác định bằng tính toán có tính đến sự xuất hiện của hạt mài trong lớp mạ qua phương trình 2-19 và qua đo trên ảnh chụp SEM mặt cắt ngang của đá mài được chế tạo. Hình 4.6. Mô hình hóa bề mặt của đá mài 12 b) Tính cắt gọt của bề mặt mạ composite Ni-CBN Mức độ liên kết của hạt mài với bề mặt lõi kim loại được xác định qua quan sát ảnh SEM chụp mặt cắt ngang của đá mài, quan sát mức độ chôn lấp của hạt và sự liên kết của kim loại mạ với hạt và với lớp lõi. Độ bền liên kết của hạt mài với lớp kim loại liên kết đánh giá thông qua quá trình mài thực nghiệm, đánh giá qua hai chỉ tiêu : Hệ số mài G và nhám bề mặt đạt được của phôi Ra, Rz. 4.2. Ảnh hƣởng của một số thông số công nghệ đến sự phân bố của hạt mài khi chế tạo đá mài bằng PPMĐ 4.2.1. Ảnh hưởng của mật độ dòng đến sự phân bố của hạt mài Bảng 4.3. Kết quả thí nghiệm ảnh hưởng của mật độ dòng đến chiều dày lớp mạ và hệ số KPBQU và KPBT (T= 55 0 C, tm = 5 phút, nct = 0,7 v/phút) Bảng 4.3 trình bày kết quả thí nghiệm và các tính toán liên quan hệ số mật độ phân bố hạt mài KPBQU và KPBT và chiều dày chôn lấp của hạt mài trong lớp mạ với mật độ dòng i= 1; 3; 6; 8 A/dm 2 tương ứng với các mẫu M16, M3, M4, M6. Ảnh SEM với độ phóng đại khác nhau của các mẫu được trình bày trên hình 4.11 cho thấy cấu trúc bề mặt của đá mài CBN chế tạo, các hạt phân bố tương đối đồng đều trên bề mặt mẫu. Tuy nhiên, ở mẫu M16 (i= 1A/dm 2 ) một số vùng trên bề mặt mẫu hạt phân bố không đồng đều như trên hình 4.11a, điều này có thể lý giải là do mật độ dòng bé nên trong quá trình mạ composite, lượng niken kết tủa trên bề mặt phôi mạ không đủ để giữ một số hạt mài bám trên bề mặt phôi nên bị bong ra khi phôi quay. Hình 4.13 biểu diễn quy luật phụ thuộc KPBT và KPBQU với mật độ dòng. Như vậy có thể nhận thấy: - Mật độ dòng ảnh hưởng lớn đến khả năng phân bố của hạt mài CBN trên bề mặt phôi mạ. Mức độ bám của hạt mài tăng theo sự tăng của mật độ dòng, điều này cũng thể hiện rõ khi quan sát trên hình 4.11. 13 - Cùng một điều kiện thí nghiệm, ta nhận thấy: Khi mật độ dòng tăng thì lượng hạt mài gắn kết trên bề mặt của đá tăng. Khi mật độ dòng tăng từ 1; 3; 6; 8 A/dm 2 , thì hệ số KPBQU tăng từ 53,48; 66,20; 69,40; 76,93 còn hệ số KPBT nhận các giá trị 64,03; 76,260; 83,20; 91,35. Sự khác nhau giữa KPBQU và KPBT chênh lệch từ 10,07 đến 14,43, nhưng dạng đường cong quan hệ giữa 2 hệ số KPBQU và KPBT với mật độ dòng có cùng một quy luật. Sở dĩ có sự khác nhau giữa 2 hệ số là do sự khác nhau của hạt mài quy ước là hình cầu và hạt mài thực tế có dạng khối nhiều cạnh. Tuy nhiên, xu hướng của đồ thị của cả 2 hệ số KPBQU và KPBT đều có dạng giống nhau, như vậy cả 2 hệ số này đều có thể đặc trưng cho mật độ hạt mài trên bề mặt của đá mài. 4.2.2. Ảnh hưởng của tốc độ quay của chi tiết mạ (catốt) Bảng 4.5 trình bày các kết quả thí nghiệm và các tính toán liên quan hệ số mật độ phân bố hạt mài và chiều dày chôn lấp của hạt mài trong quá trình thí nghiệm với tốc độ quay của chi tiết là nct = 0,7; 1,3; 2; 3v/phút, với các mẫu M3, M9, M11 và M12). Sự phân bố của hạt mài trên bề mặt các mẫu được quan sát trên các ảnh SEM được trình bày tại hình 4.15 cho thấy các hạt phân bố tương đối đồng đều trên bề mặt mẫu. Hình 4.17 thể hiện quan hệ của KPBT và KPBQU với tốc độ quay của chi tiết mạ. Hình 4.11. Ảnh SEM mẫu M16, M3, M4, M6 Hình 4.13. Quan hệ của KPB và mật độ dòng 14 Bảng 4.5. Kết quả thí nghiệm ảnh hưởng của tốc độ quay chi tiết đến chiều dày lớp mạ và hệ số KPBQU và KPBT (T= 55 o C, tm =5 phút, i= 3 A/dm 2 ) Từ kết quả bảng 4.5 và hình 4.17 có thể nhận thấy: - Tốc độ quay chi tiết ảnh hưởng lớn đến khả năng phân bố của hạt mài CBN trên bề mặt phôi mạ. Mức độ bám của hạt mài tăng khi giảm vận tốc quay của chi tiết mạ. Ở tốc độ thấp n=0,7 v/phút (M3) thấy lượng hạt mài bám đều và cũng không chênh lệch nhiều với lượng hạt mài bám ở mẫu M9 (n = 1,3 v/phút). - Ở mẫu M11 (n=2v/phút) hạt bám không đều bằng mẫu M3 và mẫu M9. Tuy nhiên nếu quan sát trên bề mặt của M11 (n=3 v/phút) và mẫu M3 (n = 0,7 v/phút) thì thấy có sự khác nhau rõ rệt về mật độ phân bố của hạt mài. - Cùng một điều kiện thí nghiệm, ta nhận thấy: Khi tốc độ quay của chi tiết tăng từ 0,7; 1,3; 2; 3 v/phút, thì hệ số KPBQU giảm từ 66,20; 60,69; 57,49; 8,06 còn hệ số KPBT nhận các giá trị giảm dần 76,26; 69,74; 66,88; 11,01. Hệ số Hình 4.15. Ảnh SEM mẫu M3, M9, M11 và M12 15 KPBQU và KPBT chênh lệch từ 9,05 đến 11,80, đặc biệt là ở mẫu M12 chỉ là 2,95, nhưng dạng đường cong quan hệ giữa 2 hệ số KPBQU và KPBT đều cho thấy khi mật độ dòng tăng thì lượng hạt CBN trên bề mặt phôi mạ tăng. Tuy nhiên, khi tốc độ quay tăng đến 3v/phút thì mật độ phân bố hạt giảm đột ngột. Điều này có thể được lý giải là do khi tốc độ quay tăng đến 3 v/phút thì chiều dày lớp kim loại mạ để gắn các hạt mài CBN chưa đủ để giữ hạt mài nên trên bề mặt phôi nên hạt mài bám trên bề mặt phôi lại bị bong ra khi mẫu mạ quay và chỉ còn lại một số ít hạt mài bám trên bề mặt. Đối với mẫu M12, sự chênh lệch của KPBQU và KPBT rất nhỏ là 2,95 có thể lý giải là do mật độ hạt mài ở mẫu M12 rất thấp nên sự khác nhau về hình dạng của hạt mài quy ước và hạt mài thực tế không làm ảnh hưởng nhiều đến hệ số KPBT. Ở mẫu M11, lượng hạt phân bố quan sát không được đều bằng mẫu M9 và M3. Như vậy, tốc độ quay của chi tiết trong khoảng 0,7 vòng/phút đến 1,3 vòng/phút là phù hợp. 4.2.3. Ảnh hưởng của thời gian mạ composite. Bảng 4.7 trình bày các kết quả thí nghiệm và các tính toán liên quan hệ số mật độ phân bố hạt mài và chiều dày chôn lấp của hạt mài trong quá trình thí nghiệm phụ thuộc vào thời gian mạ composite là 3; 5; 10; 15 phút tương ứng với các mẫu M17; M3; M1 và M8. Bảng 4.7. Kết quả thí nghiệm ảnh hưởng của thời gian mạ composite Ni-CBN đến chiều dày lớp mạ và hệ số KPBQU và KPBT (T= 55 0 C, i= 3 A/dm 2 , nct = 0,7 v/phút) Hình 4.17. Quan hệ của KPB và tốc độ quay chi tiết mạ 16 Hình 4.19 trình bày sự phân bố của hạt mài trên bề mặt mẫu trên các ảnh SEM với độ phóng đại từ 50 đến 500 lần. Sự phụ thuộc của hệ số KPBQU và KPBT với thời gian mạ được thể hiện ở trên hình 4.21. Từ các kết quả trên có thể nhận thấy: -Hạt mài phân bố tương đối đồng đều trên bề mặt mẫu. Tuy nhiên, ở mẫu M17, do thời gian mạ composite tm =3 phút nhỏ nên còn xuất hiện một số vùng hạt mài phân bố chưa đồng đều như trên hình 4.19a. Tại mẫu có thời gian mạ composite lớn M8 (tm = 15 phút), xuất hiện một số hạt bị chồng đề lên nhau trên bề mặt mẫu như quan sát trên hình 4.19d. Qua đó cho thấy, thời gian thích hợp mạ trong khoảng từ 5- 10 phút. - Cùng một điều kiện thí nghiệm, ta nhận thấy: Thời gian mạ composite ảnh hưởng lớn đến mức độ phân bố của hạt mài CBN trên bề mặt phôi mạ. Mức độ bám của hạt mài tăng theo thời gian mạ mạ. Khi thời gian mạ của chi tiết tăng từ 3; 5; 10; 15 phút, thì hệ số KPBQU tăng từ 50,05; 66,20; 72,24; 77,89 còn hệ số KPBT nhận các giá trị tăng dần 59,54; 76,26; 83,61; 91,35. Hệ số KPBQU và KPBT có thể chênh lệch từ 9,41 đến 13,47 nhưng dạng đường cong quan hệ giữa 2 hệ số KPBQU và KPBT đều cho thấy là khi thời gian mạ tăng thì lượng hạt CBN trên bề mặt phôi mạ tăng. - Khi thời gian mạ của chi tiết tăng từ 3; 5; 10; 15 phút, thì hệ số KPBQU tăng từ 50,05; 66,20; 72,24; 77,89 còn hệ số KPBT nhận các giá trị tăng dần Hình 4.21. Quan hệ của KPB và thời gian mạ Hình 4.19. Ảnh SEM mẫu M17, M3, M1 và M8 17 59,54; 76,26; 83,61; 91,35. Hệ số KPBQU và KPBT có thể chênh lệch từ 9,41 đến 13,47 nhưng dạng đường cong quan hệ giữa 2 hệ số KPBQU và KPBT đều cho thấy là khi thời gian mạ tăng thì lượng hạt CBN trên bề mặt phôi mạ tăng. 4.2.4. Ảnh hưởng của nhiệt độ dung dịch mạ. Bảng 4.9. Kết quả thí nghiệm ảnh hưởng của nhiệt độ dung dịch mạ đến chiều dày lớp mạ và hệ số KPBQU và KPBT (i= 3 A/dm 2 , nct = 0,7 v/phút, tm =5 phút) Bảng 4.9 trình bày các kết quả thí nghiệm liên quan KPBQU, KPBT và chiều dày chôn lấp của hạt CBN tại các nhiệt độ dung dịch mạ T= 50; 55; 60 o C với các mẫu M14; M3 và M13. Hình 4.23 là các ảnh SEM bề mặt của các mẫu. Hình 4.25 biểu diễn ảnh hưởng không đáng kể của nhiệt độ dung dịch mạ đến KPBT và KPBQU của hạt trên bề mặt mạ. Từ các kết quả trên có thể nhận thấy: - Các hạt CBN phân bố tương đối đồng đều trên bề mặt lớp mạ. Nhiệt độ dung dịch mạ ảnh hưởng không đáng kể đến mức độ phân bố của hạt mài trên bề mặt phôi mạ trong khoảng nhiệt độ từ 50-60 o C - Khi nhiệt độ dung dịch mạ tăng từ 50; 55; 60 o C, thì hệ số KPBQU nhận các giá trị 63,20; 66,20; 65,29 còn hệ số KPBT nhận các giá trị 74,23; 76,26; 75,86. Hệ số KPBQU và KPBT có thể chênh lệch từ 10,57 đến 11,03 nhưng dạng đường Hình 4.23. Ảnh SEM các mẫu M14, M3 và M13 18
File đính kèm:
tom_tat_luan_an_nghien_cuu_che_tao_va_danh_gia_kha_nang_cat.pdf