Tóm tắt Luận án Nghiên cứu xây dựng hệ thống trợ giúp thiết kế quy trình công nghệ gia công chi tiết trên máy phay CNC
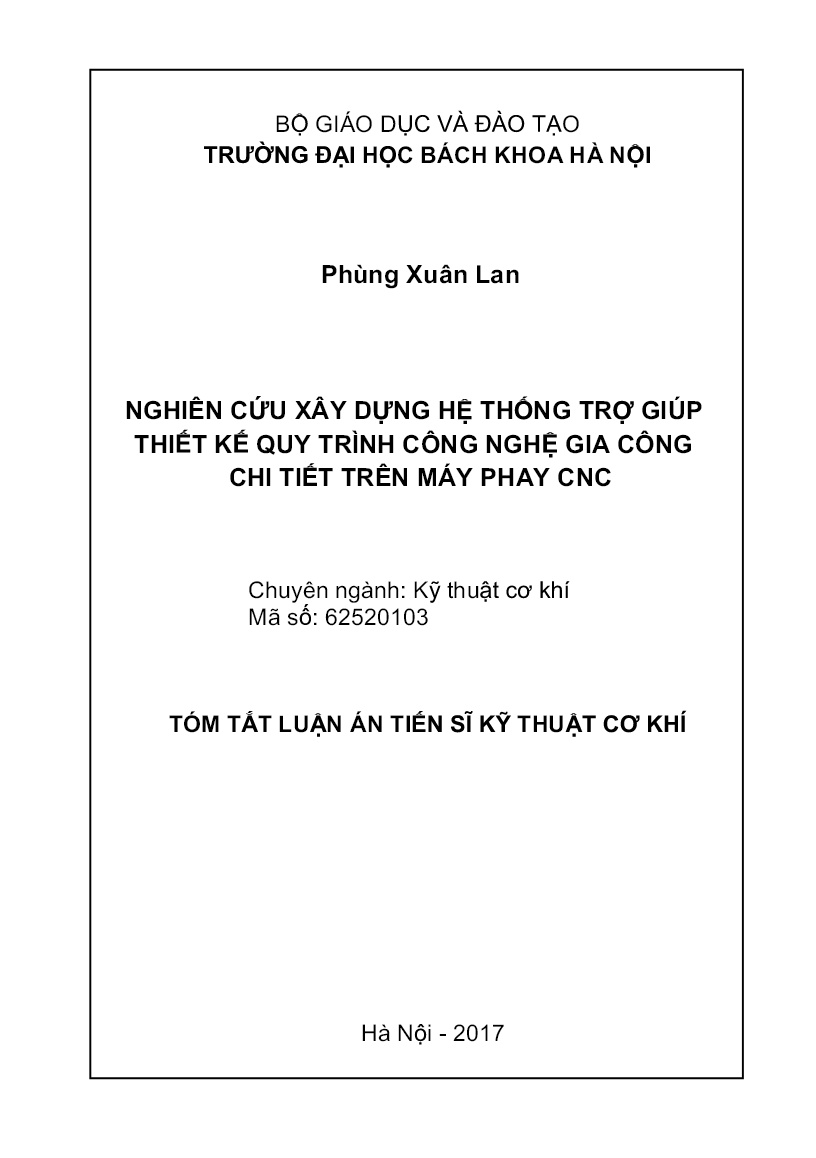
Trang 1
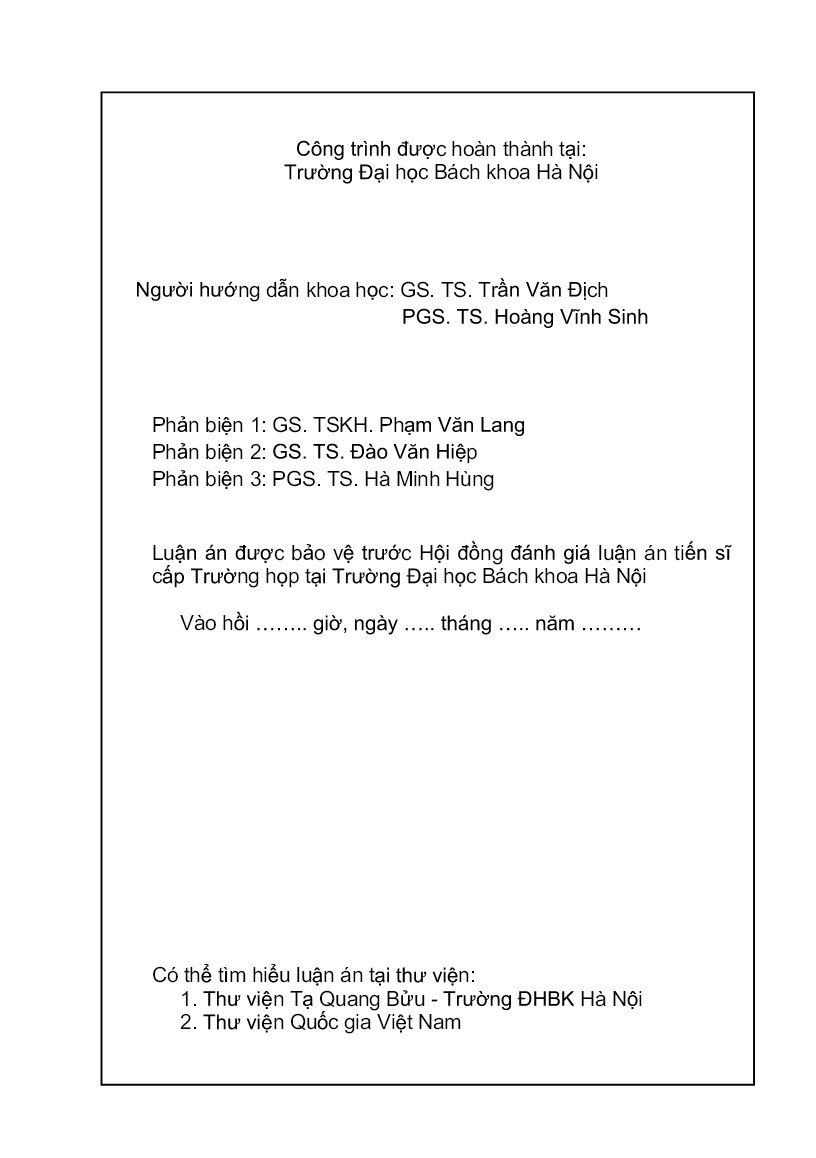
Trang 2
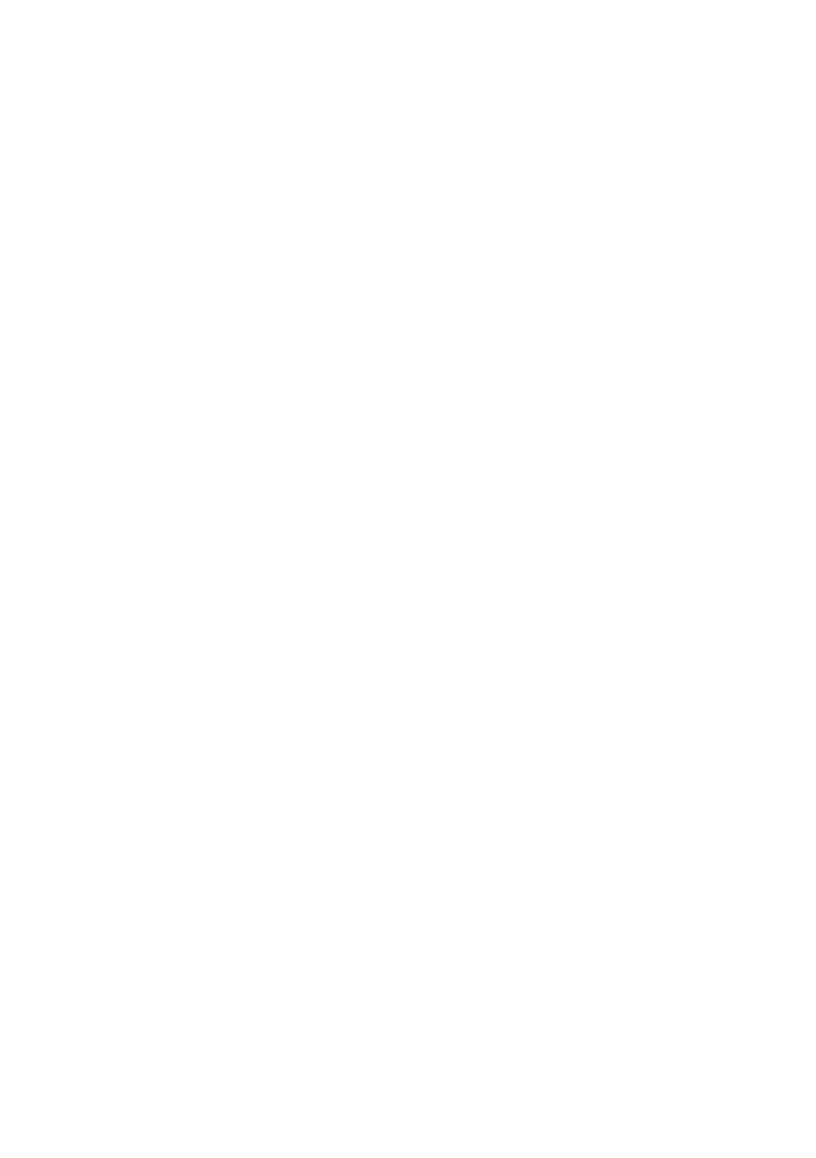
Trang 3
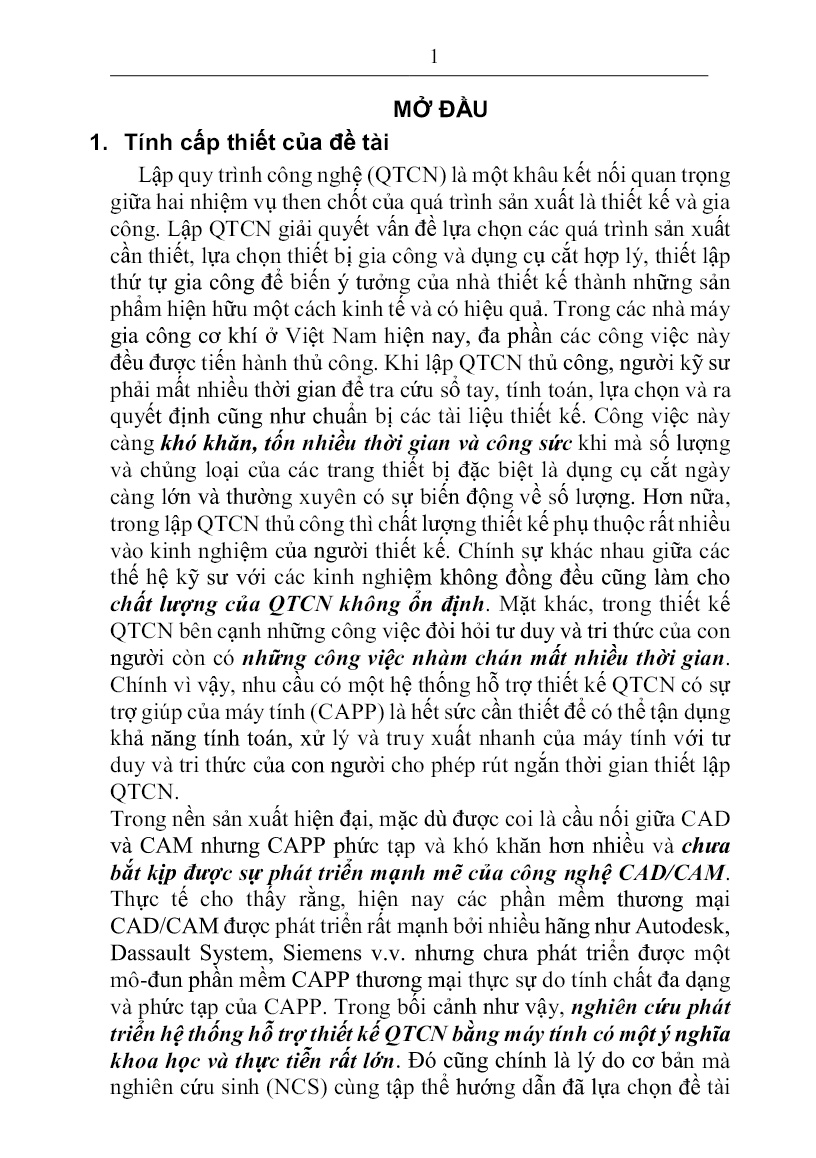
Trang 4
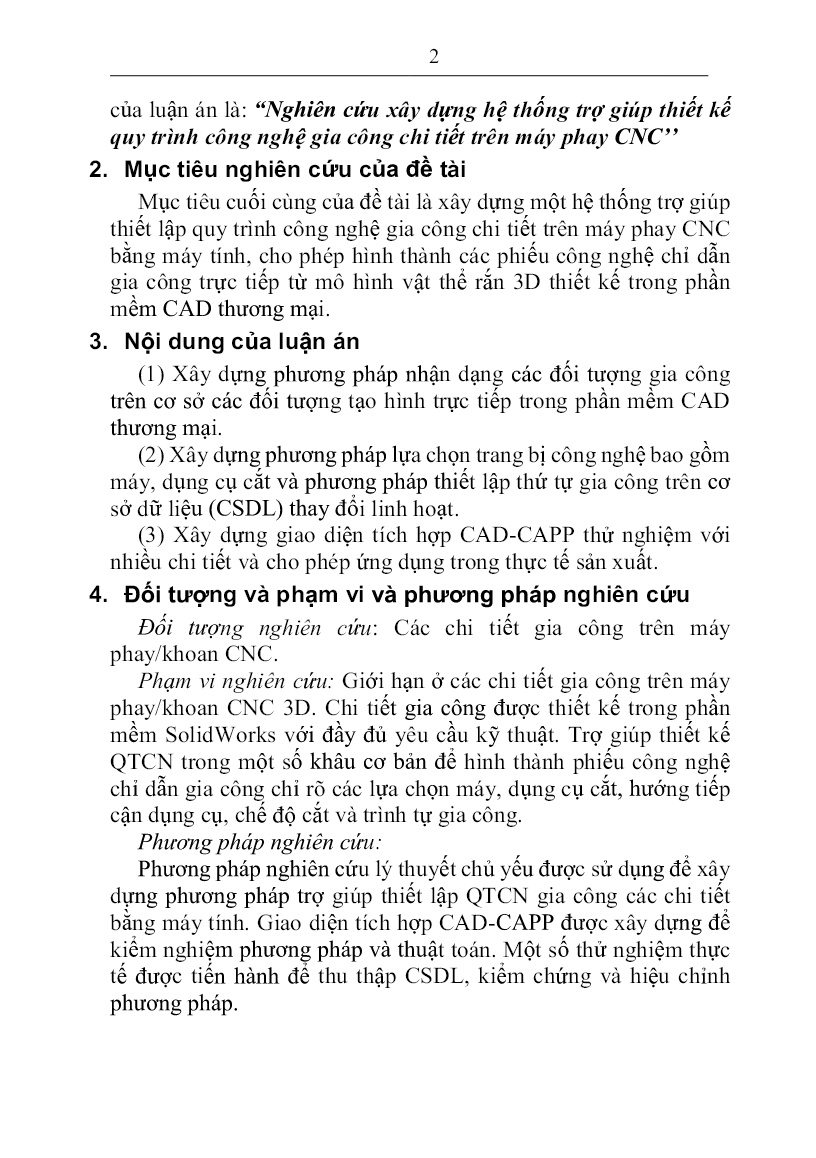
Trang 5
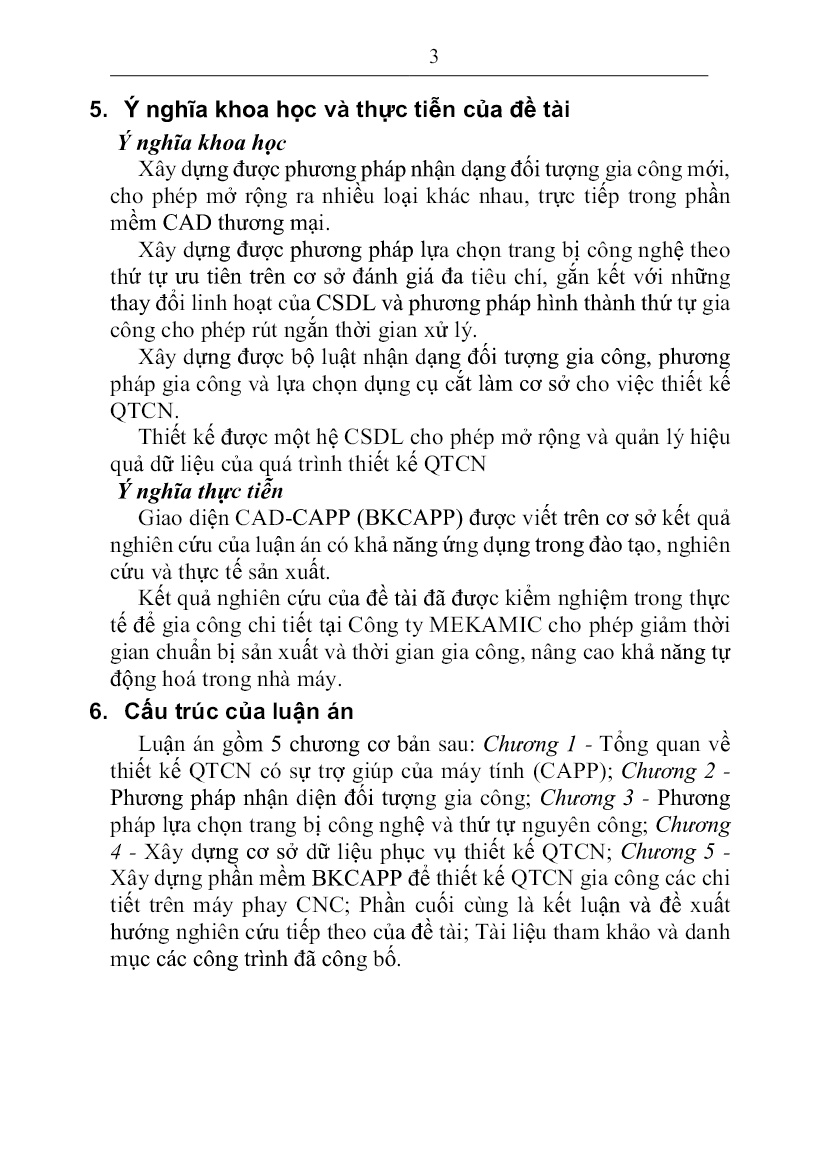
Trang 6
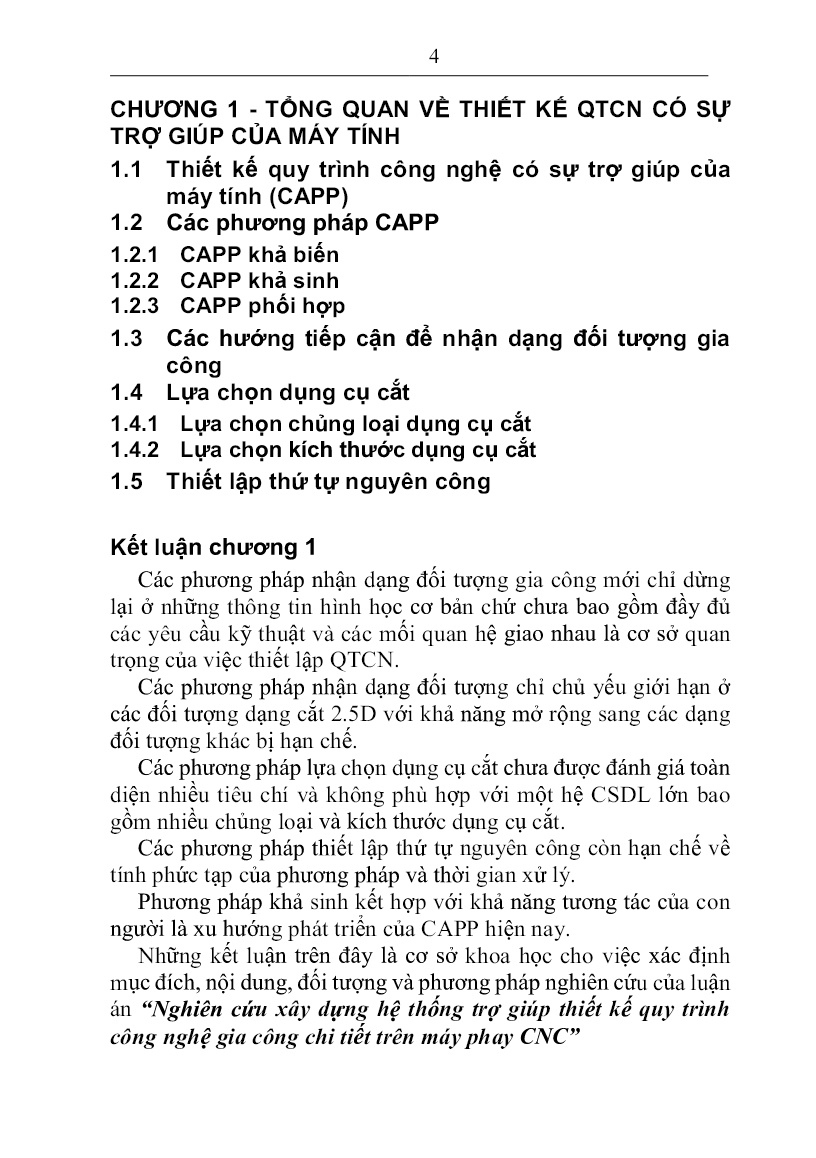
Trang 7
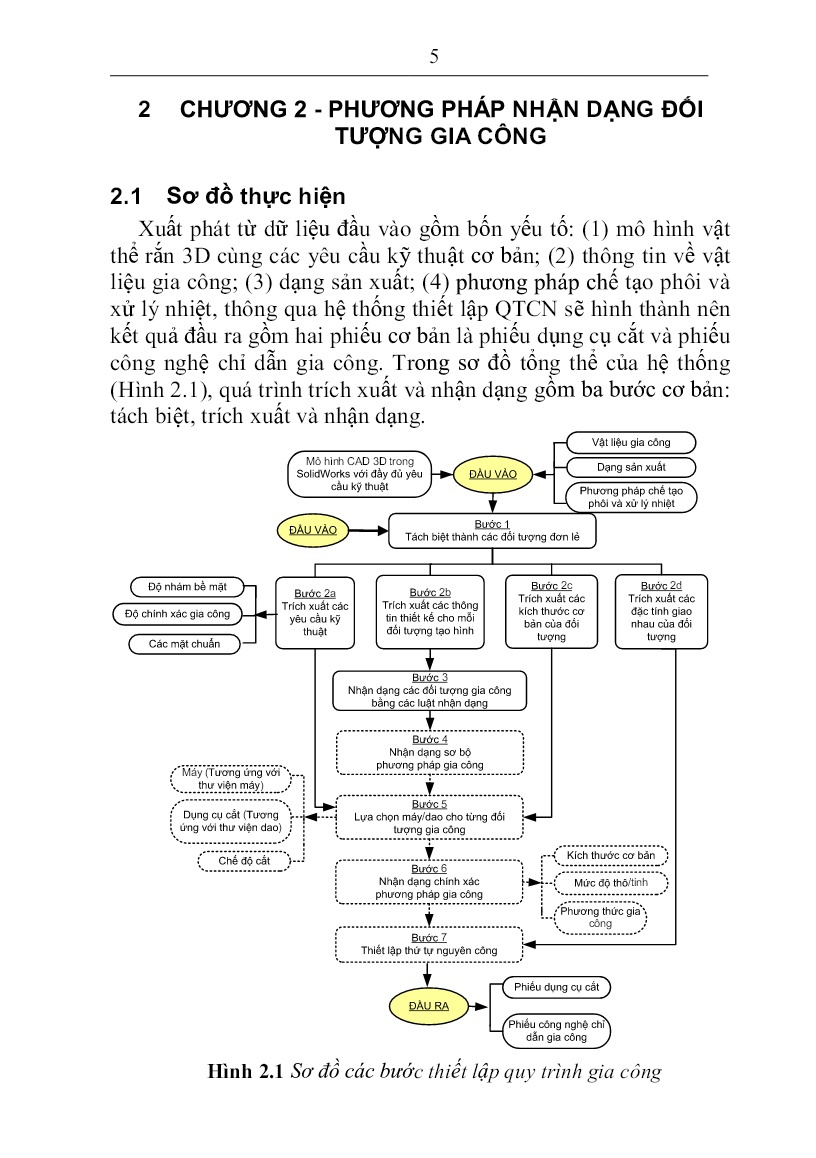
Trang 8
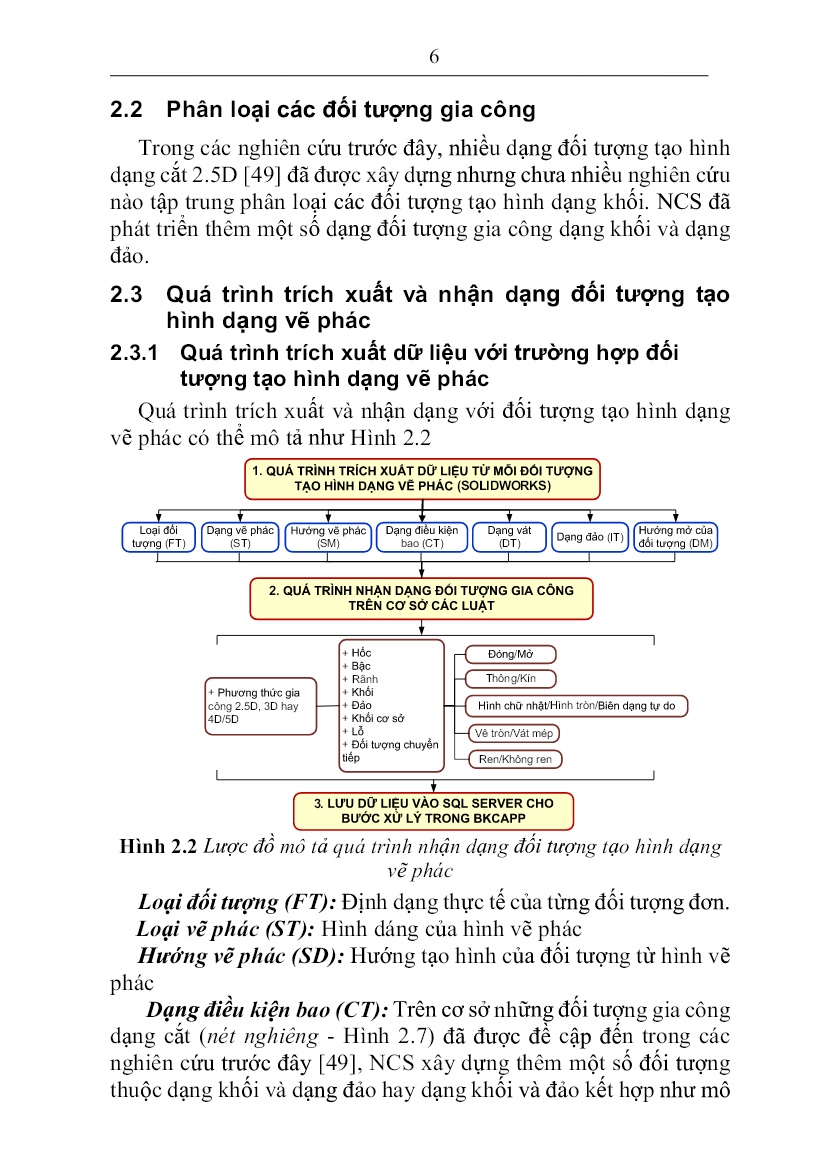
Trang 9
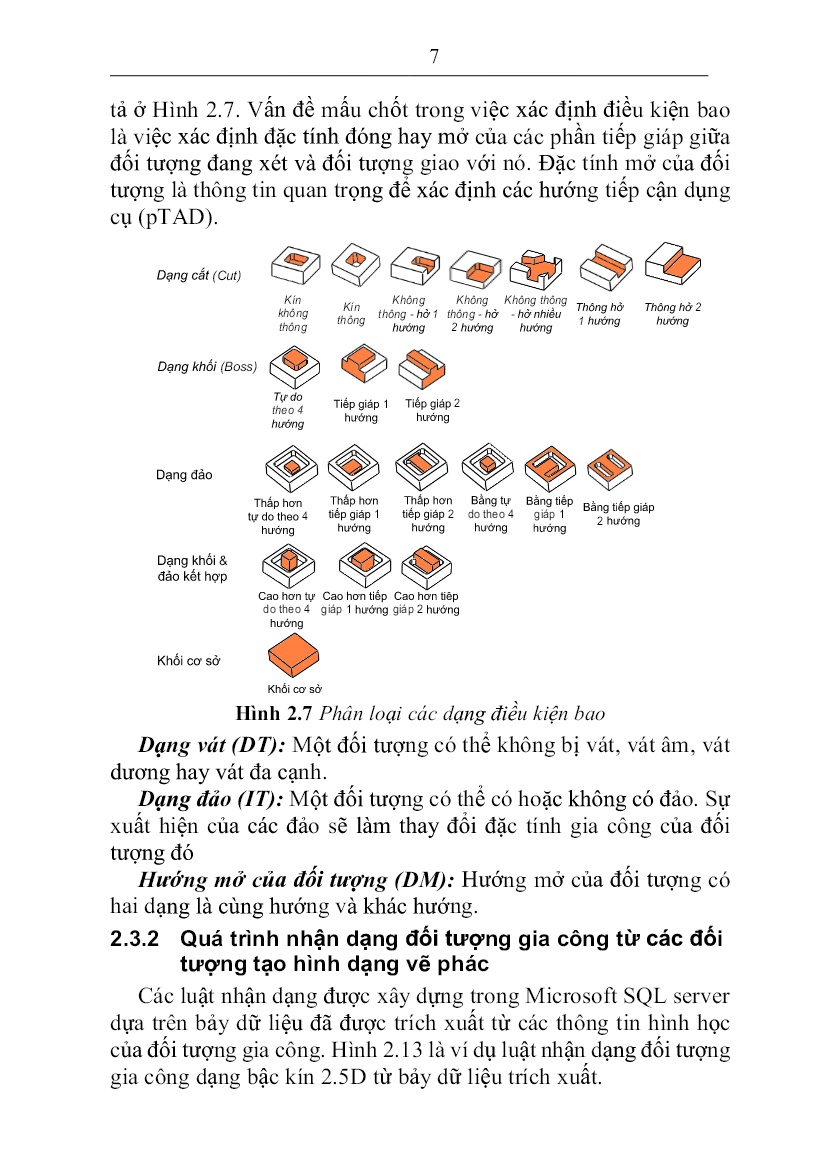
Trang 10
Tải về để xem bản đầy đủ
Bạn đang xem 10 trang mẫu của tài liệu "Tóm tắt Luận án Nghiên cứu xây dựng hệ thống trợ giúp thiết kế quy trình công nghệ gia công chi tiết trên máy phay CNC", để tải tài liệu gốc về máy hãy click vào nút Download ở trên.
Tóm tắt nội dung tài liệu: Tóm tắt Luận án Nghiên cứu xây dựng hệ thống trợ giúp thiết kế quy trình công nghệ gia công chi tiết trên máy phay CNC
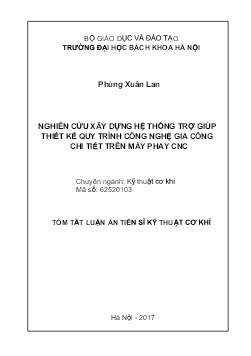
dạng đối tượng gia công từ các đối tượng tạo hình dạng vẽ phác Các luật nhận dạng được xây dựng trong Microsoft SQL server dựa trên bảy dữ liệu đã được trích xuất từ các thông tin hình học của đối tượng gia công. Hình 2.13 là ví dụ luật nhận dạng đối tượng gia công dạng bậc kín 2.5D từ bảy dữ liệu trích xuất. 8 2. Loại vẽ phác (hình chữ nhật) 7. Hướng mở đối tượng (cùng hướng) 1. ExtrudeCut (dạng cắt kéo) 5. Không vát 6. Không đảo 4. Điều kiện bao (không thông, hở hai hướng) Hướng hở 1 Hướng hở 2 Bậc kín 2.5D chữ nhật 3. Hướng vẽ phác (đường thẳng vuông góc) Hình 2.13 Nhận dạng đối tượng gia công là bậc kín 2.5D chữ nhật 2.4 Quá trình trích xuất và nhận dạng đối tượng tạo hình dạng thiết lập đặc tính và vị trí 2.4.1 Quá trình trích xuất đối tượng tạo hình dạng lỗ Mỗi lỗ (HoleWzd) có một đặc trưng cho kiểu lỗ khác nhau và 25 kích thước khác nhau liên quan đến thông số hình học của lỗ. Số lượng và đặc điểm của các kích thước khác 0 sẽ là cơ sở để nhận dạng các đối tượng gia công. 2.4.2 Quá trình nhận dạng đối tượng tạo hình HoleWzd 2.4.3 Quá trình nhận dạng đối tượng tạo hình dạng chuyển tiếp 2.5 Quá trình trích xuất và nhận dạng yêu cầu kỹ thuật 2.6 Quá trình nhận dạng các mối quan hệ giữa các đối tượng tạo hình Kết luận chương 2 Không chỉ trích xuất được các thông tin hình học mà còn cho phép trích xuất các yêu cầu kỹ thuật và các đặc điểm giao nhau giữa các đối tượng. Đã mở rộng việc nhận dạng từ các đối tượng gia công dạng cắt sang dạng khối, dạng đảo và dạng khối đảo kết hợp Bộ luật nhận dạng được thiết lập và quản lý trong CSDL nên tạo điều kiện thuận lợi cho việc mở rộng, hiệu chỉnh do đó tăng khả năng tương tác và mở rộng với người sử dụng. Phương pháp nhận dạng theo đối tượng này được tiến hành hoàn toàn tự động tích hợp trong môi trường thiết kế 3D của SolidWorks nên giải quyết được nút thắt cơ bản trong CAPP là dòng tích hợp CAD/CAPP. 9 3 CHƯƠNG 3 - PHƯƠNG PHÁP LỰA CHỌN TRANG BỊ CÔNG NGHỆ VÀ THỨ TỰ NGUYÊN CÔNG 3.1 Phương pháp lựa chọn dụng cụ cắt 3.1.1 Phương pháp phân tích thứ bậc (AHP) để lựa chọn loại dụng cụ cắt 3.1.1.1 Phương pháp phân tích thứ bậc AHP 3.1.1.2 Phương pháp AHP với những cải tiến trong lựa chọn loại dụng cụ cắt Phương pháp AHP đã được phát triển ở mức cao hơn bằng cách thêm hai tiêu chí lựa chọn đầu tiên cho phép lựa chọn được các phương án loại dụng cụ cắt tương ứng với các dữ liệu đầu vào khác nhau chứ không cố định với chỉ một dữ liệu đầu vào. Lựa chọn dụng cụ cắt tối ưu (Gia công mặt bậc) Đặc tính hình học (SC) Khả năng bóc tách phoi (MRC) Công suất máy yêu cầu (PR) Giá thành dụng cụ cắt (TC) Dao phay ngón liền khối (SEM) Dao phay ngón răng chắp cạnh dài 90 (LEM) Dao phay ngón răng chắp thường 90 (IEM90) Chất lượng (Qa) Các chi phí khác (CR) Dao phay đĩa (SFM) MỤC TIÊU CÁC TIÊU CHÍ LỚN VÀ TIÊU CHÍ THÀNH PHẦN CÁC PHƯƠNG ÁN Tỷ lệ dài/ rộng (AR) Trung bình (M) Thấp (Lo) Cao (Hi) Bề rộng (Wi) Lớn (La) Nhỏ (Sm) Độ cứng vững (SD) Bình thường (No) Yếu (Li) Nặng (He) Thô (Ro) Bán tinh (SF) Tinh (Fi) KẾT QUẢ Loại dụng cụ cắt có mức ưu tiên cao nhất và thứ tự ưu tiên của các loại Hình 3.2 Mô hình cấu trúc thứ bậc (Gia công mặt bậc thẳng) Hình 3.2 là mô hình AHP với trường hợp bậc thẳng. Trên cơ sở đánh giá rời rạc các tiêu chí ví dụ như Hình 3.8, phương pháp AHP sẽ tổng hợp các tiêu chí để có một đánh giá mức độ ưu tiên tổng hợp cho phép lựa chọn một loại dụng cụ cắt tốt hơn như Hình 3.9. 10 Phương pháp AHP cũng là cơ sở để thiết lập bộ luật lựa chọn loại dụng cụ cắt theo thứ tự ưu tiên Hình 3.8 Mức độ ảnh hưởng của các tiêu chí chính Hình 3.9 Mức độ ưu tiên của các phương án lựa chọn 3.1.2 Lựa chọn các kích thước dụng cụ cắt Cơ sở để lựa chọn đường kính dụng cụ cắt trong trường hợp này là khống chế số lượng đường chạy dao tuy nhiên cần hạn chế trường hợp góc ôm toàn bộ dụng cụ cắt. Với trường hợp tổng quát để gia công hốc, các thông số cần xem xét tới được thể hiện trong Bảng 3.6. Toàn bộ các kích thước nêu trong bảng đã được trích 0 0.1 0.2 0.3 0.4 0.5 0.6 Đ ặ c t í n h h ì n h h ọ c C h ấ t l ư ợ n g K h ả n ă n g b ó c t á c h p h o i C ô n g s u ấ t c ắ t y ê u c ầ u G i á t h à n h d ụ n g c ụ c ắ t C á c c h i p h í k h á c M ứ c đ ộ ư u t iê n Dao phay ngón liền khối Dao phay ngón răng chắp cạnh dài Dao phay ngón răng chắp cạnh ngắn Dao phay đĩa 0 0.1 0.2 0.3 Dao phay ngón liền khối Dao phay ngón răng chắp cạnh dài Dao phay ngón răng chắp cạnh ngắn Dao phay đĩa 0.2809 0.2527 0.2961 0.1784 11 xuất trong quá trình nhận dạng đối tượng gia công dạng hốc 2.5D. Số lượng trong bộ dụng cụ cắt gia công hốc tùy thuộc vào sự tương quan và sai khác giữa các kích thước tạo hình của hốc. Xác định DF: Đường kính của dụng cụ cắt lần cuối 𝑅𝐹𝑚𝑖𝑛 = { = 𝑀𝑖𝑛(𝑅𝑠, 𝑅𝑏 , 𝐷𝑠 2 , 𝐷𝑏 2 , 𝐷𝑖𝑖 2 , 𝐷𝑜𝑠 2 , 𝐷𝑠𝑖 2 ) ≠ 0 (3.11) 𝐷𝐹 = 𝑘𝐹 × 𝑅𝐹𝑚𝑖𝑛 (3.12) Xác định DR: Đường kính của dụng cụ cắt thô 𝑅𝑅𝑚𝑖𝑛 = { = 𝑀𝑖𝑛( 𝐷𝑠𝑠 2 , 𝑀𝑠𝑖 2 , 𝐴𝑜𝑠 2 , 𝑀𝑠𝑖 2 ) ≠ 0 (3.13) 𝐷𝑅 = 𝑘𝑅 × (𝑅𝑅𝑚𝑖𝑛 × 𝑎1 + 𝑅𝑅𝑚𝑖𝑛 × 𝑎2) × 𝑎0 (3.14) 𝑎𝑜 { = 0 𝑛ế𝑢 𝑅𝐹𝑚𝑖𝑛 > 𝑅𝑅𝑚𝑖𝑛 2 = 1 𝑘ℎá𝑐 (3.15) 𝑎1 { = 1 𝑛ế𝑢 𝑅𝐹𝑚𝑖𝑛 ≤ 𝑅𝑅𝑚𝑖𝑛 2 𝑣à 𝑅𝐹𝑚𝑖𝑛 > 𝑅𝑅𝑚𝑖𝑛 8 = 0 𝑘ℎá𝑐 (3.16) 𝑎2 { = 1 𝑛ế𝑢 𝑅𝐹𝑚𝑖𝑛 < 𝑅𝑅𝑚𝑖𝑛 8 = 0 𝑘ℎá𝑐 (3.17) Xác định DSF: Bán kính của dụng cụ cắt trung gian (nếu cần) 𝐷𝑆𝐹 = 𝑘𝑆𝐹 × 𝑅𝑅𝑚𝑖𝑛 4 × 𝑎2 (3.18) Bảng 3.6 Các loại kích thước cơ bản của hốc STT Kí hiệu Loại kích thước 1 Rs Bán kính góc lượn nhỏ nhất theo mặt cạnh 2 Rb Bán kính góc lượn nhỏ nhất theo mặt đáy 3 Ds Khoảng vát nhỏ nhất theo mặt cạnh 4 Db Khoảng vát nhỏ nhất theo mặt đáy 5 Dos Khoảng cách nhỏ nhất giữa các mặt hở 6 Dsi Khoảng cách nhỏ nhất giữa mặt cạnh hốc và mặt cạnh đảo 7 Dii Khoảng cách nhỏ nhất giữa hai đảo 8 Dss Bề rộng nhỏ nhất của hốc 9 Msi Khoảng cách lớn nhất giữa mặt hốc và mặt cạnh đảo 10 Aos Khoảng cách trung bình giữa các mặt hở 11 Am Góc nhỏ nhất hợp giữa các mặt cạnh 12 3.1.3 Thuật toán lựa chọn dụng cụ cắt Sơ đồ khối mô tả các bước lựa chọn dụng cụ cắt mô tả như Hình 3.11. Dữ liệu họ dụng cụ và cán dụng cụ Dữ liệu mảnh cắt Dữ liệu vật liệu cắt Bước 4: Tìm kiếm họ và cán dụng cụ tương ứng Bước 6: Lựa chọn mảnh cắt qua luật i > N Có họ dụng cụ Dữ liệu thông số chế độ cắt Bước 8: Xác định thông tin chế độ cắt (Hiệu chỉnh nếu cần) Xuất ra loại dụng cụ đầu tiên trong thứ tự ưu tiên KẾT THÚC Đ Đ S Với mỗi đối tượng gia công Luật lựa chọn phương pháp gia công tương ứng với dụng cụ cắt và đối tượng gia công Xác định phương pháp gia công chính xác Đưa ra yêu cầu mua dụng cụ cắt BẮT ĐẦU Bước 1: Xác định sơ bộ các phương pháp gia công Bước 3: Xác định N loại dụng cụ theo thứ tự ưu tiên bằng phương pháp AHP i = 0 Bước 2: Xác định sơ bộ kích thước dụng cụ cắt Có mác dụng cụ S Bước 5: Lựa chọn kích thước dụng cụ cắt (Hiệu chỉnh trong phạm vi) và tìm mác dụng cụ Bước 3a: Xây dựng mô hình AHP cho lựa chọn loại dụng cụ cắt Bước 3b: Thiết lập bộ luật lựa chọn thứ tự ưu tiên các loại dụng cụ trên cơ sở AHP Bước 3c: Mã hóa các dữ liệu đầu vào tùy từng dạng gia công Bước 3d: Duyệt qua bộ luật lựa chọn loại dụng cụ cắt S i = i+1 Có mác mảnh cắt Có vật liệu mảnh cắt Đ S S Đ Đ Bước 9: Xác định chính xác dụng cụ cắt được chọn Bước 7: Xác định vật liệu mảnh cắt Dữ liệu dụng cụ cắt Hình 3.11 Sơ đồ khối lựa chọn dụng cụ cắt 13 Toàn bộ quá trình lựa chọn này đều được tiến hành trên CSDL hệ thống. Khi kết thúc vòng lặp mà không dụng cụ cắt nào được xác định thì hệ thống sẽ đưa ra yêu cầu mua dụng cụ cắt ngoài thị trường theo những kích thước và chủng loại được ưu tiên nhất. 3.1.4 Xác định chế độ cắt 3.2 Lựa chọn máy công cụ 3.3 Phương pháp thiết lập thứ tự nguyên công Khi có nhiều phương án lựa chọn máy, dụng cụ cắt và hướng tiếp cận dụng cụ cũng như nhiều thứ tự nguyên công thỏa mãn điều kiện ràng buộc thứ tự thì nhiệm vụ của bài toán này là tìm thứ tự nguyên công trên cơ sở tối thiểu chi phí gia công (Hình 3.15) MO1 M1, TAD1, T1 MO2 M1, TAD3, T4 MOi M4, TAD1, T3 MOn M1, TAD4, T3 Chi phí C1 MO1 M2, TAD1, T2 MO2 M1, TAD1, T3 MOi M4, TAD3, T3 MOn M4, TAD4, T2 Chi phí C2 MO1 M2, TAD1, T2 MOi M4, TAD1, T2 MO2 M2, TAD1, T4 MOn M4, TAD4, T2 Chi phí Ci ... ... MO1 M2, TAD1, T2 MOi M2,TAD1, T2 MOn M4, TAD4, T2 Chi phí Cn Chi phí MIN Bài toán tối ưu hóa thứ tự nguyên công Hình 3.15 Các phương án thiết lập thứ tự nguyên công 3.3.1 Xây dựng các ma trận ràng buộc thứ tự Nguyên tắc 1: Ràng buộc gia công (thô/bán tinh/tinh) Nguyên tắc 2: Ràng buộc chuẩn gốc (mặt chuẩn/gốc ưu tiên gia công trước) Nguyên tắc 3: Ràng buộc công nghệ (thuận lợi cho hướng tiếp cận dụng cụ) Nguyên tắc 4: Ràng buộc gá đặt (thuận lợi cho việc gá đặt) Nguyên tắc 5: Ràng buộc giao nhau tùy vào đặc điểm giao nhau của đối tượng 3.3.2 Tính toán chi phí gia công Chi phí gia công gồm chi phí sử dụng và khấu hao trang bị công nghệ (máy, dụng cụ, đồ gá), chi phí luân chuyển giữa các trang bị và các phụ phí khác 𝐶𝑖𝑗 = 𝑀𝐶𝐶 × 𝑚𝑖𝑗 + 𝑆𝐶𝐶 × 𝑠𝑖𝑗 + 𝑇𝐶𝐶 × 𝑡𝑖𝑗 + 𝑀𝐶𝑗 + 𝑇𝐶𝑗 + 𝑆𝐶𝑗 + 𝑇𝑃𝑖𝑗 (3.24) 14 3.3.3 Thiết lập thứ tự gia công trong trường hợp lựa chọn thiết bị cố định 3.3.3.1 Thuật toán thiết lập N> NumMO i = i+1 Bước 5: Tính toán tổng chi phí gia công KẾT THÚC Đ S Bước 6: So sánh chi phí gia công và đưa ra thứ tự NC có chi phí gia công nhỏ nhất Bước 1: Sắp xếp các phương án khả thi của bước/NC đầu tiên theo thứ tự ưu tiên MODauTien i = 0 i > NI S NI = số vòng lặp NumMO = tổng số bước/NC N = số bước/NC trong danh sách i = chỉ số của danh sách các phương án thứ tự NC DSThuTuA Bước 2: Lưu mỗi bước/NC MODauTien vào một danh sách DSThuTuA[i] Bước 3: Tìm phương án khả thi của bước/NC tiếp theo trong danh sách thứ i Bước 4: Thêm bước/NC đó vào danh sách DSThuTuA[i] N = N + 1 Đ 1. Danh sách các bước/nguyên công kèm lựa chọn trang bị công nghệ tương ứng 2. Ma trận ràng buộc thứ tự P ĐẦU VÀO Quy trình công nghệ có chi phí gia công nhỏ nhất ĐẦU RA Tính tổng các hàng của ma trận P và lưu vào danh sách TongRP Lưu các bước/NC có tổng hàng bằng 0 vào danh sách MODauTien Các bước/NC chỉ dùng một máy, TAD hay dụng cụ cắt duy nhất được ưu tiên Tính tổng các giá trị P[k, p] tương ứng với mỗi bước/NC trong DSThuTuA[i] Lưu các bước/NC có tổng giá trị P[k, p] bằng TongRP[p] vào danh sách MODemSau Sắp xếp thứ tự ưu tiên của các bước/NC trong MODemSau theo thứ tự tăng dần của chi phí và sự lặp lại thiết bị trong các bước/NC sau Tính chi phí gia công Cjk (j là bước/NC cuối cùng, k là các bước/NC trong MODemSau Thủ tục A Thủ tục B Hình 3.16 Thuật toán thiết lập thứ tự nguyên công 15 Hình 3.16 mô tả sơ đồ khối để thiết lập thứ tự nguyên công với 6 bước cơ bản 3.3.3.2 Kiểm nghiệm thuật toán 3.3.4 Thiết lập thứ tự gia công với trường hợp lựa chọn thiết bị linh hoạt 3.3.4.1 Thuật toán thiết lập 3.3.4.2 Kiểm nghiệm thuật toán Kết quả so sánh trong Hình 3.20 cho thấy các giá trị lớn nhất, giá trị trung bình và giá trị nhỏ nhất qua 10 vòng lặp của phương pháp đề xuất đều nhỏ hơn các phương pháp trước. Điều này thể hiện phương pháp đề xuất đã khoanh vùng được các bước/NC hiệu quả để đưa vào thứ tự nguyên công, do đó chỉ đánh giá và lựa chọn phương án thiết lập thứ tự nguyên công từ những quy trình có mức độ ưu tiên cao. Hình 3.20 So sánh với các thuật toán khác (Thiết bị linh hoạt) Kết luận chương 3 Phương pháp AHP được cải tiến bằng cách thêm hai tiêu chí lựa chọn so với phương pháp AHP truyền thống cho phép sắp xếp loại dụng cụ cắt theo thứ tự ưu tiên linh hoạt với nhiều lựa chọn đầu vào. Số lượng đường chạy dao và mối tương quan giữa các kích thước tạo hình là cơ sở quan trọng để tính toán và lựa chọn bộ dụng 1014 1038 1008 1022 10581053.5 1198 1291 1458 1158 900 1000 1100 1200 1300 1400 1500 G i á t r ị t r u n g b ì n h G i á t r ị l ớ n n h ấ t G i á t r ị n h ỏ n h ấ t C h i p h í g ia c ô n g Thuật toán chọn lọc ghép nhóm Thuật toán tìm kiếm Tabu Thuật toán mô phỏng luyện kim Thuật toán gen 16 cụ cắt cho phép rút ngắn thời gian tìm kiếm dụng cụ, thích hợp với sự đa dạng của CSDL Việc lựa chọn máy theo thứ tự ưu tiên trên cơ sở đánh giá không chỉ giá thành mà còn cả mức độ tải của máy. Các thủ tục kiểm tra ràng buộc thứ tự và sắp xếp thứ tự ưu tiên lựa chọn ở từng bước được lồng vào thuật toán ghép nhóm cho phép giảm thời gian xử lý so với các phương pháp thiết lập thứ tự nguyên công trước. 4 CHƯƠNG 4 - XÂY DỰNG CSDL PHỤC VỤ THIẾT KẾ QTCN 4.1 Thiết kế CSDL 4.1.1 Đặc điểm và cấu trúc của CSDL thiết kế QTCN Cấu trúc gồm 4 nhóm CSDL cơ bản bao gồm CSDL lựa chọn ban đầu, CSDL chi tiết gia công, CSDL nhận dạng và lựa chọn, CSDL mã hóa 4.1.2 Mô hình quản trị CSDL Hình 4.3 mô tả dòng luân chuyển dữ liệu và mô hình quản trị CSDL trong đó CSDL chi tiết gia công là CSDL trung tâm. Nó là CSDL động, luôn thay đổi trong suốt quá trình thiết kế. 4.2 CSDL các lựa chọn ban đầu 4.2.1 CSDL vật liệu gia công 4.2.2 CSDL máy gia công 4.2.3 CSDL dụng cụ cắt 4.3 CSDL chi tiết gia công Với mỗi chi tiết gia công đưa vào hệ thống sẽ hình thành một CSDL với tên gọi là tên của chi tiết gia công. Mỗi khi nhận dạng lại chi tiết gia công toàn bộ dữ liệu trong CSDL này sẽ được loại bỏ để thay thế bằng dữ liệu mới. 4.4 CSDL mã hoá 4.5 CSDL các luật nhận dạng và lựa chọn 4.5.1 Luật nhận dạng đối tượng gia công Luật nhận dạng đối tượng gia công được thiết kế theo hai dạng cơ bản là đối tượng dạng vẽ phác và dạng thiết lập đặc tính, vị trí 17 4.5.2 Luật lựa chọn chủng loại dụng cụ cắt 4.5.3 Luật nhận dạng phương pháp gia công C S D L C h i ti ế t g ia c ô n g C S D L M á y g ia c ô n g C S D L D ụ n g c ụ c ắ t C S D L V ậ t liệ u g ia c ô n g C S D L D ạ n g s ả n x u ấ t C S D L L u ậ t n h ậ n d ạ n g P P g ia c ô n g C S D L L u ậ t lự a c h ọ n đ ặ c t ín h d ụ n g c ụ c ắ t C S D L L u ậ t n h ậ n d ạ n g đ ố i tư ợ n g g ia c ô n g C S D L L u ậ t lự a c h ọ n l o ạ i d ụ n g c ụ c ắ t D ữ l iệ u d ụ n g c ụ c ắ t D S D u n g C u C a t D ữ l iệ u m á y D S M a y D ữ l iệ u P P g ia c ô n g B u o c N C D ữ l iệ u n h ậ n d ạ n g D T G ia C o n g D ữ l iệ u q u a n h ệ D T G ia o N h a u D ữ l iệ u t ạ o h ìn h D T H in h H o c P h a y D T H in h H o c L o D T H in h H o c C h u y e n T ie p D ữ l iệ u y ê u c ầ u K T Y e u C a u K y T h u a t C h u a n G o c D ữ l iệ u r à n g b u ộ c t h ứ t ự R a n g B u o c D ữ l iệ u t h ứ t ự g ia c ô n g T h u T u N C T o iU u C S D L M ã h ó a C h ứ c n ă n g c ủ a C S D L + X ó a D L + T h ê m D L + H iệ u c h ỉn h D L + L ự a c h ọ n D L C S D L M ã h ó a C h ứ c n ă n g c ủ a C S D L + X ó a D L + T h ê m D L + H iệ u c h ỉn h D L + L ự a c h ọ n D L C h ứ c n ă n g c ủ a C S D L + H iệ u c h ỉn h D L + L ự a c h ọ n D L C S D L M ã h ó a D ữ l iệ u g iá t h à n h tb l_ C h a n g e C o s t C h ứ c n ă n g c ủ a C S D L + H iệ u c h ỉn h D L + L ự a c h ọ n D L C h ứ c n ă n g c ủ a C S D L + X ó a D L + H iệ u c h ỉn h D L + L ự a c h ọ n D L 1 1 1 2 3 4 1 0 5 , 6 , 7 8 a 9 a 9 b 8 b 1 2 1 3 Hình 4.3 Sơ đồ mô tả đường luân chuẩn dữ liệu trong CSDL 18 Kết luận chương 4 Hệ thống CSDL phục vụ thiết kế QTCN đã được xây dựng có các ưu điểm nổi bật sau: Không chỉ xây dựng CSDL mô tả thông tin còn có CSDL các luật nhận dạng và lựa chọn. Các CSDL được thiết kế đảm bảo tính chuẩn hóa và có khả năng liên kết với các CSDL khác. Các luật nhận dạng được thiết lập trên cơ sở các dữ liệu được mã hóa. Với hệ thống CSDL này hoàn toàn có thể xây dựng được thuật toán và tiến hành xây dựng các chương trình máy tính đảm bảo truy xuất và xử lý dữ liệu được dễ dàng và nhanh chóng. 5 CHƯƠNG 5 - XÂY DỰNG PHẦM MỀM BKCAPP ĐỂ THIẾT KẾ QTCN GIA CÔNG CHI TIẾT TRÊN MÁY PHAY CNC 5.1 Mô tả về hệ thống BKCAPP Hệ thống gồm hai mô-đun cơ bản như mô tả trong Hình 5.1 Đầu vào: Mô hình vật thể rắn 3D với đầy đủ yêu cầu kỹ thuật Nhận dạng đối tượng gia công trong SolidWorks Lưu trữ các dữ liệu nhận dạng trong Microsoft SQL Server Nhập các dữ liệu lựa chọn ban đầu vào hệ thống BKCAPP Đầu ra: Phiếu dụng cụ cắt, phiếu chỉ dẫn gia công Trợ giúp thiết kế QTCN trong hệ thống BKCAPP Hiển thị trong giao diện BKCAPP Lưu trữ trong CSDL SQL Server Lưu trữ trong định dạng file excel NC1 NC2 NCn Máy Dụng cụ cắt Hướng gá đặt Thứ tự NC Chế độ cắt Hiệu chỉnh toàn bộ CSDL Tương tác, hiệu chỉnh ở các bước trung gian Hình 5.1 Sơ đồ mô tả hệ thống BKCAPP 19 (1) Nhận dạng đối tượng gia công phát triển trong phần mềm SolidWorks 2013 bằng ngôn ngữ VB 7.0 (Hình 5.3); (2) Mô-đun thiết kế QTCN tự động phát triển trong phần mềm Visual C# 2012 (Hình 5.4). CSDL được quản lý trong phần mềm chuyên dụng SQL Server 2012. Hình 5.3 Giao diện kết quả nhận dạng đối tượng gia công trong SolidWorks Hình 5.4 Giao diện lựa chọn đầu vào trong BKCAPP 20 5.2 Thử nghiệm 1 5.3 Thử nghiệm 2 5.3.1 Đặc điểm mô hình Chi tiết là đế gá được sản xuất với dạng sản xuất đơn chiếc, vật liệu S45C, phôi dạng khối/tấm (Hình 5.13) Boss-Extrude1_2 Chamfer2 f4.0 (4) Diameter Hole2 M3 Tapped Hole 1 f4.0 (4) Diameter Hole1 Cut-Extrude1 Boss-Extrude1_5 Cut-Extrude2 Hole1 Boss-Extrude1_4 Chamfer1 Boss-Extrude1_3 f4.0 (4) Diameter Hole1 Boss-Extrude1_0 Boss-Extrude1_1 Đối tượng bị khuất Đối tượng không bị khuất Boss-Extrude: Đối tượng tạo hình dạng khối kéo (Khối cơ sở) Cut-Extrude: Đối tượng tạo hình dạng cắt kéo Diameter Hole: Đối tượng tạo hình lỗ cơ bản Hole: Đối tượng tạo hình lỗ tự tạo Tapped Hole: Đối tượng tạo hình lỗ taro Fillet: Đối tượng tạo hình dạng vê tròn Chamfer: Đối tượng tạo hình dạng vát mép Hình 5.13 Mô hình vật thể rắn 3D trong SolidWorks (Thử nghiệm 02) 5.3.2 Kết quả thiết kế quy trình công nghệ QTCN được xuất tự động từ hệ thống BKCAPP và mô tả như Hình 5.14 5.3.3 Kết quả gia công từ thực tế Chi tiết được gia công theo QTCN đã thiết lập tại Công ty Mekamic. Hình 5.16 thể hiện một số bước gia công thực tế và sản phẩm. 5.3.4 Đánh giá kết quả Chi tiết được gia công đã được đo kiểm đạt yêu cầu kỹ thuật. Hệ thống BKCAPP áp dụng để gia công chi tiết cho phép giảm thời gian chuẩn bị sản xuất lên tới 10 lần, thời gian gá đặt giảm 30%, thời gian gia công giảm 15% (Bảng 5.1, Bảng 5.3). 21 M F 0 1 - M ặ t đ á y - B o s s -E x tr u d e 1 _ 0 M F 0 2 - M ặ t tr ê n - B o s s -E x tr u d e 1 _ 1 M F 0 3 - M ặ t c ạ n h - B o s s -E x tr u d e 1 _ 2 M F 0 4 - M ặ t b ê n t rê n - B o s s -E x tr u d e 1 _ 3 M F 0 5 - M ặ
File đính kèm:
tom_tat_luan_an_nghien_cuu_xay_dung_he_thong_tro_giup_thiet.pdf