Luận án Nghiên cứu ảnh hưởng của chế độ cắt đến độ nhám bề mặt răng và lượng mòn dao khi cắt tinh bánh răng côn cung tròn bằng đầu dao hợp kim cứng
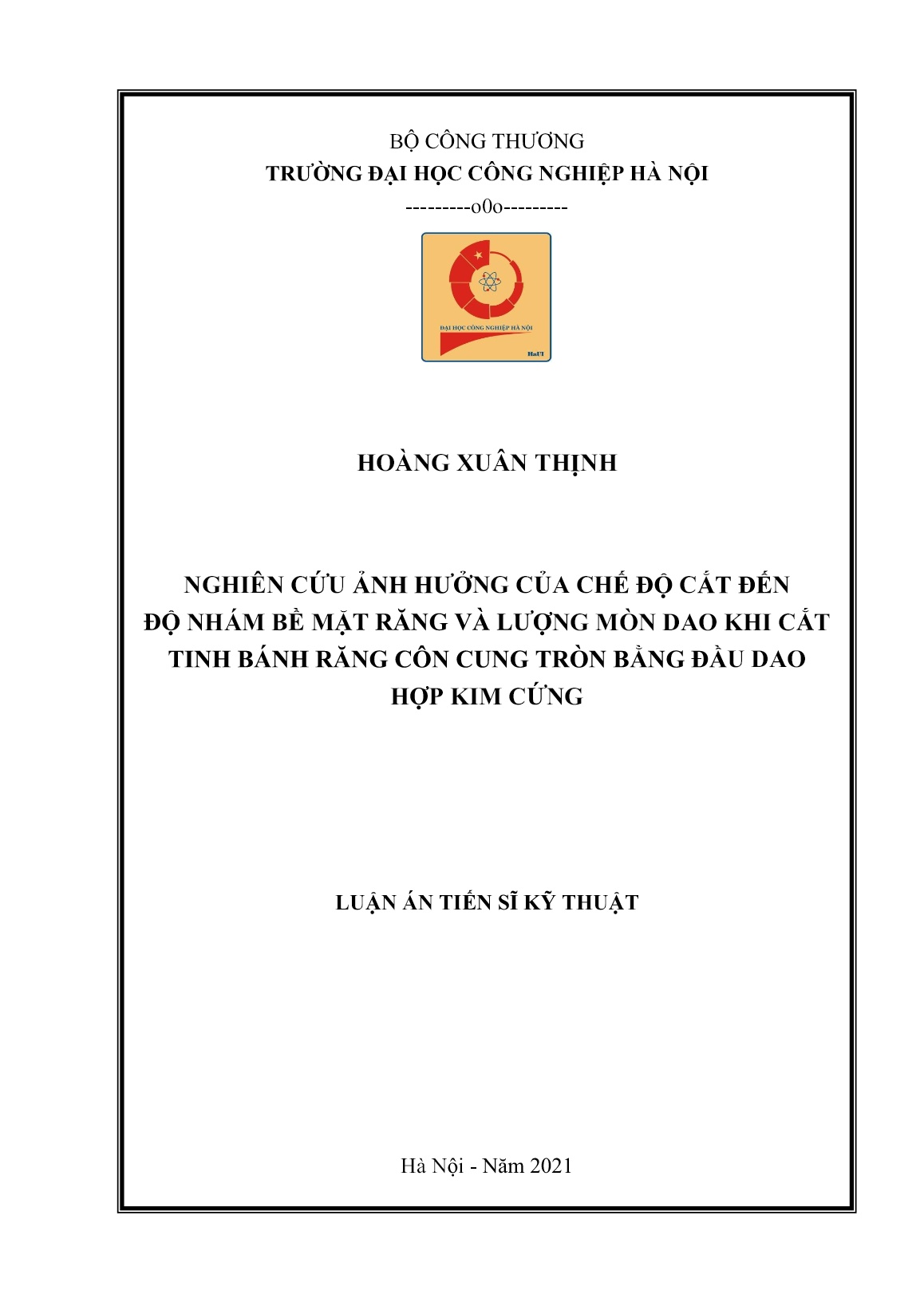
Trang 1
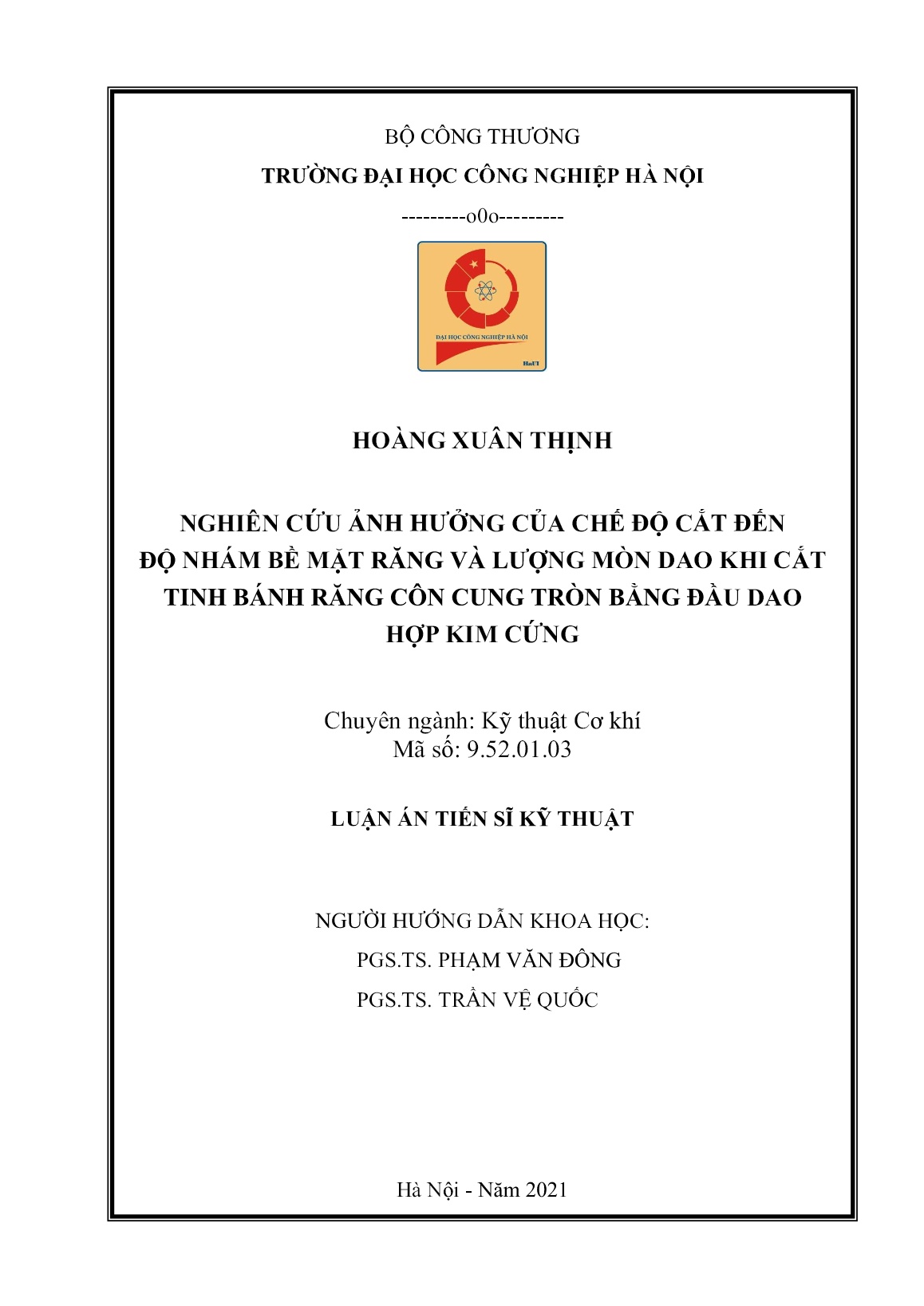
Trang 2
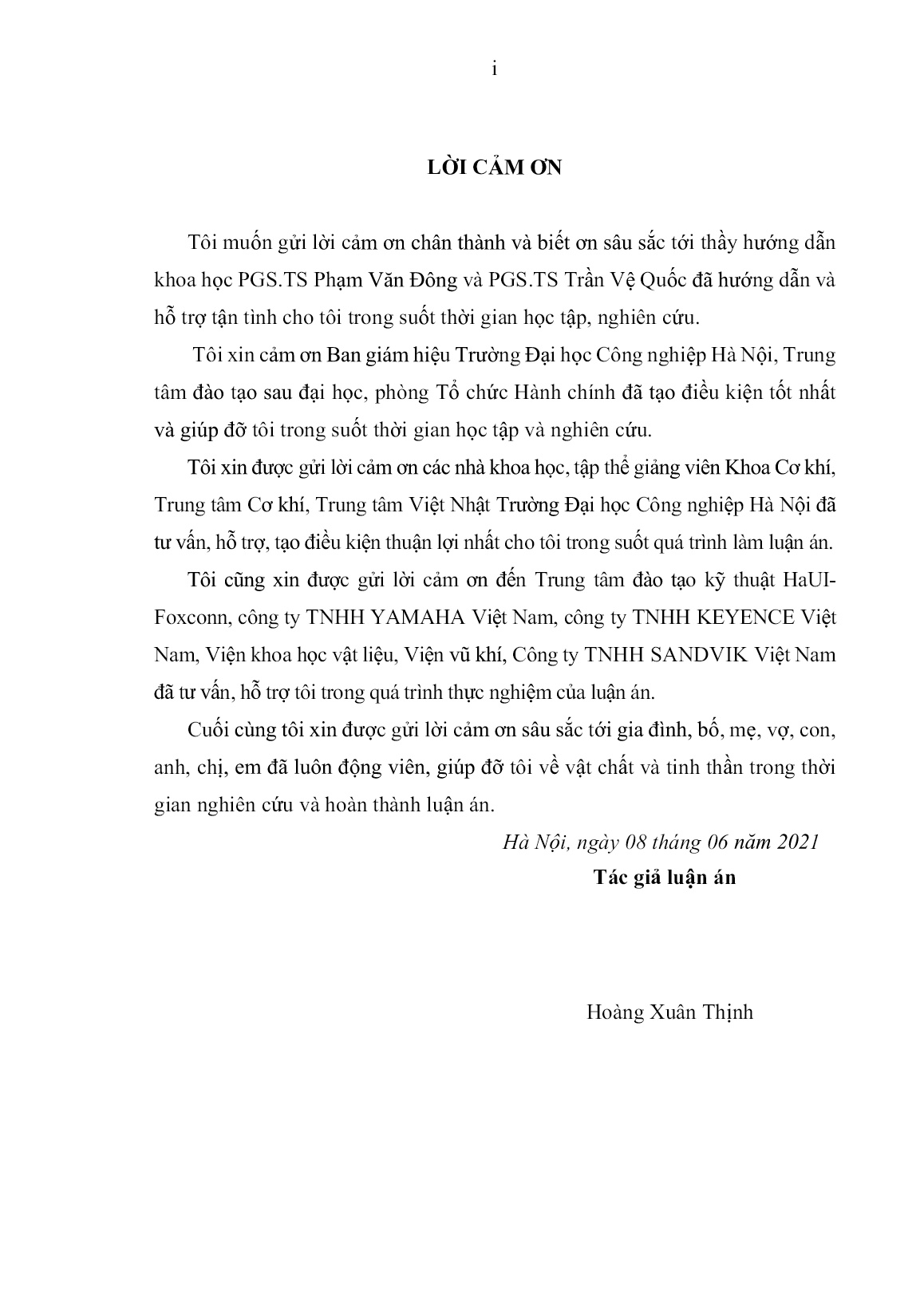
Trang 3
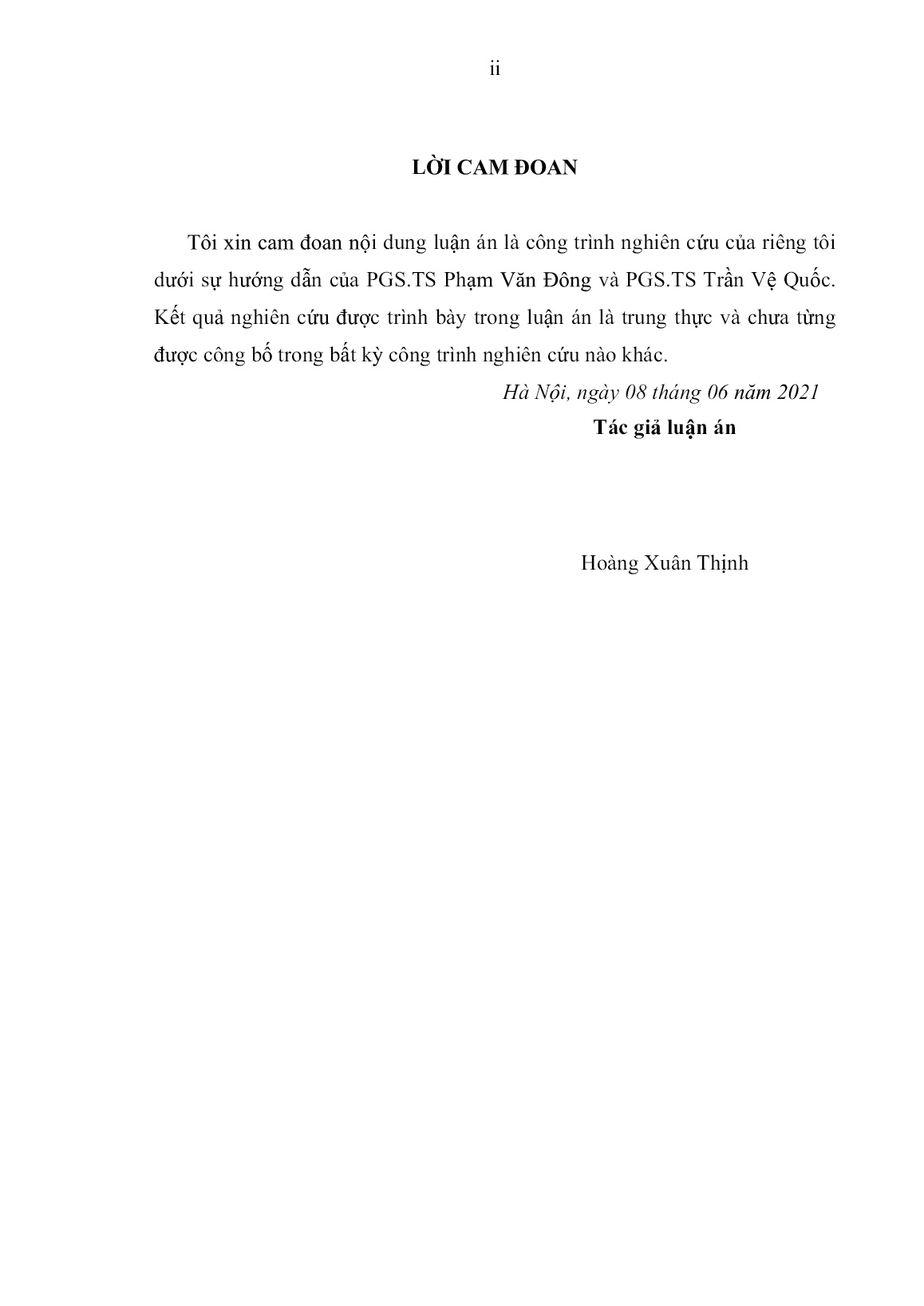
Trang 4
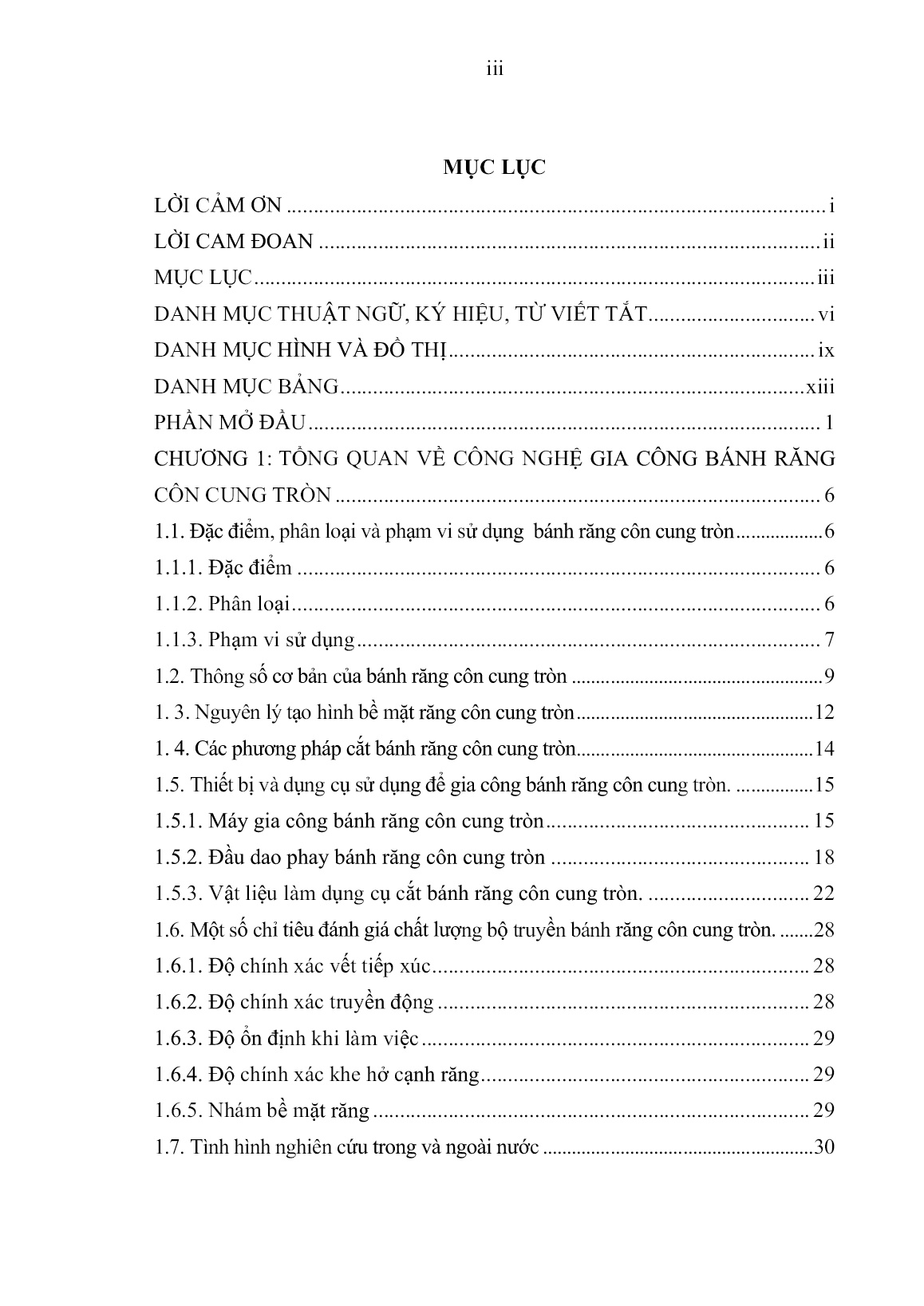
Trang 5
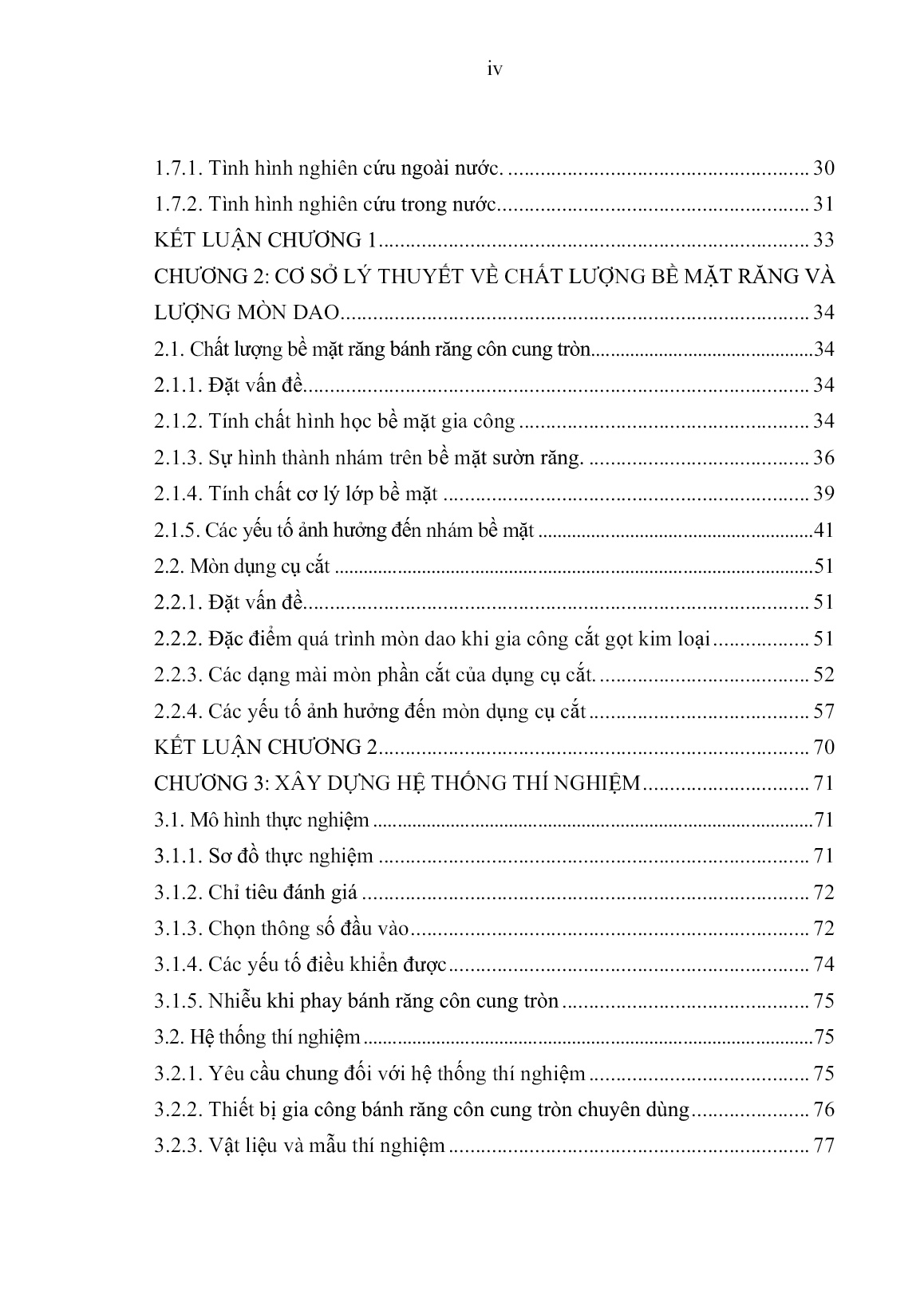
Trang 6
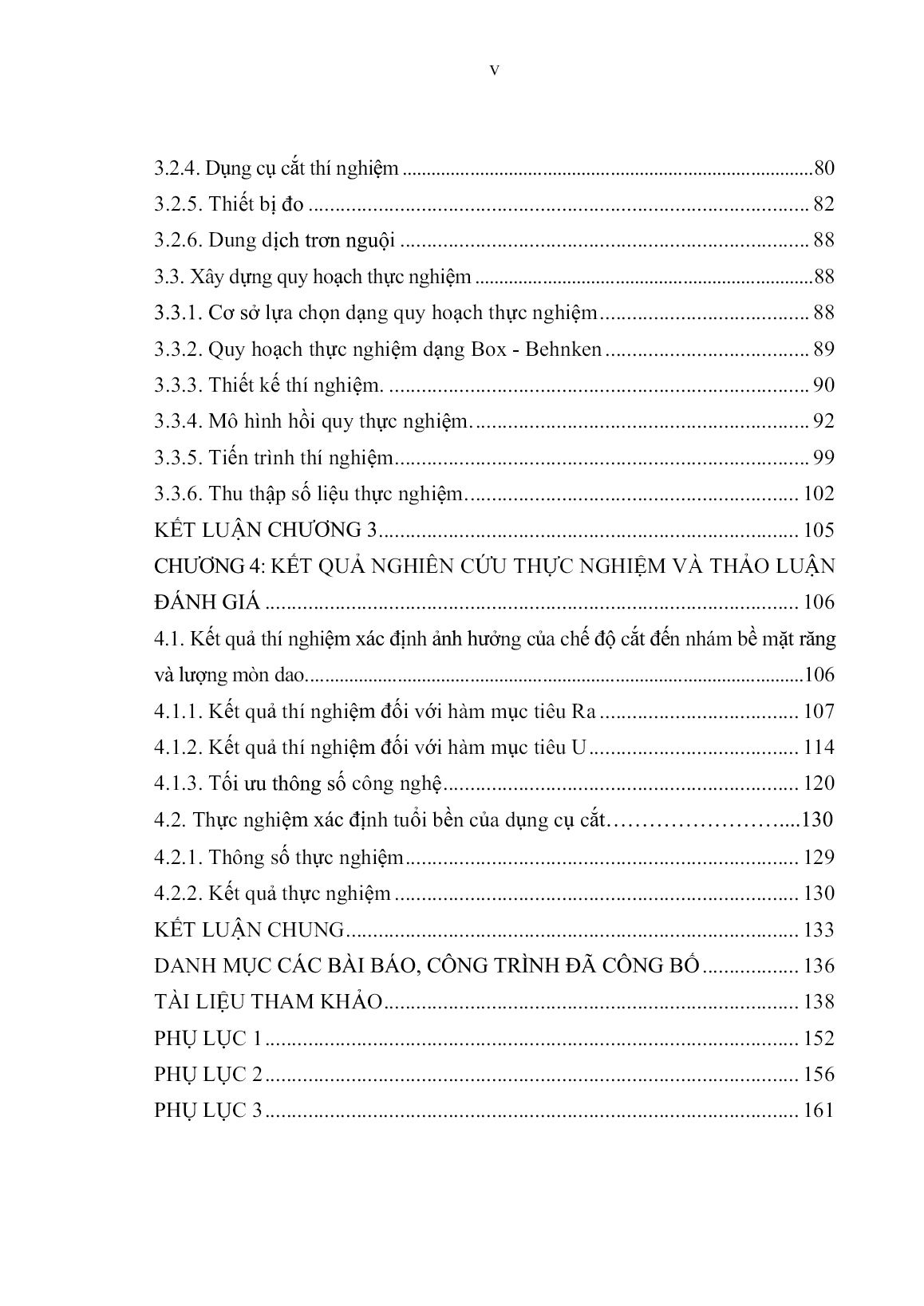
Trang 7
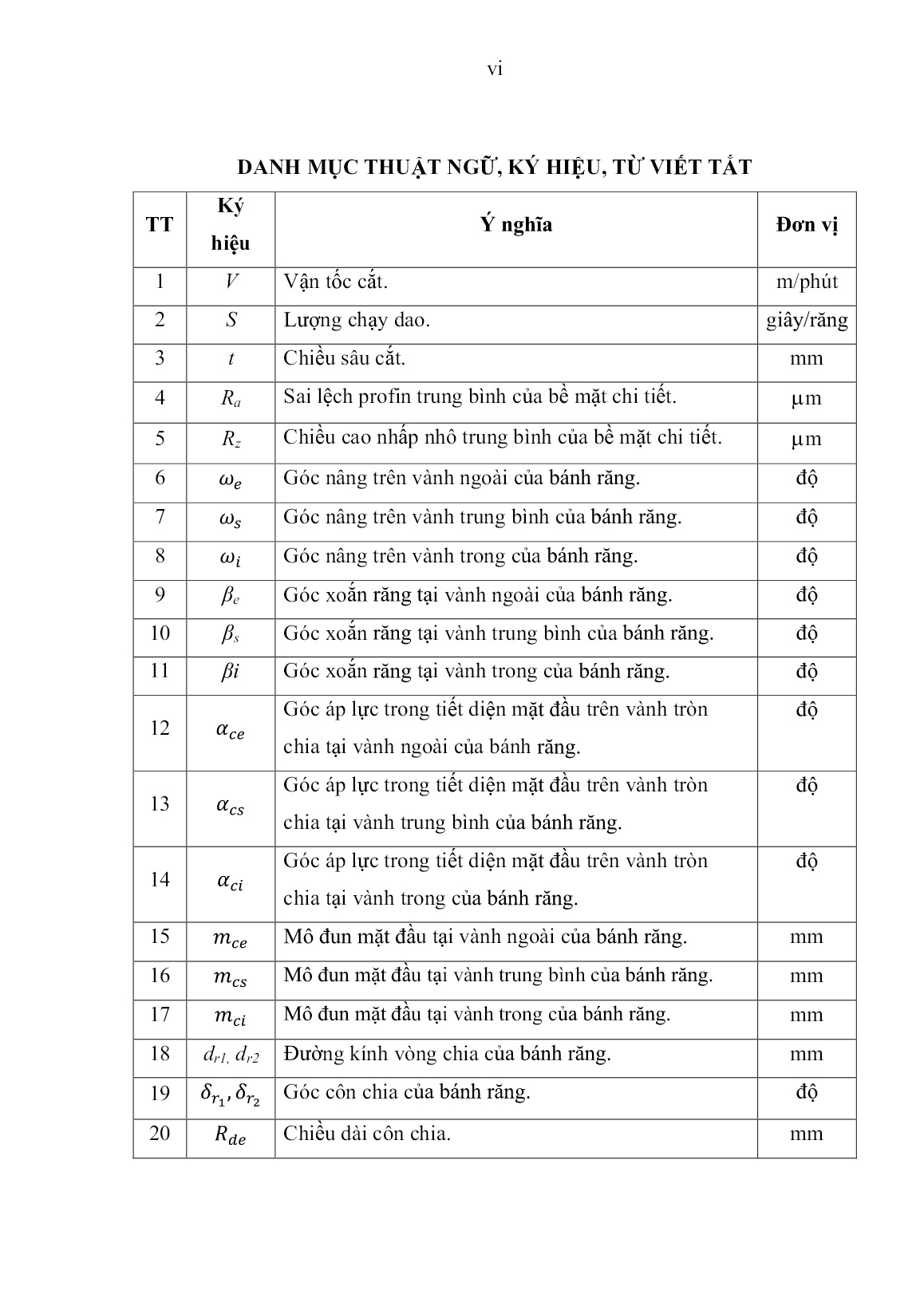
Trang 8
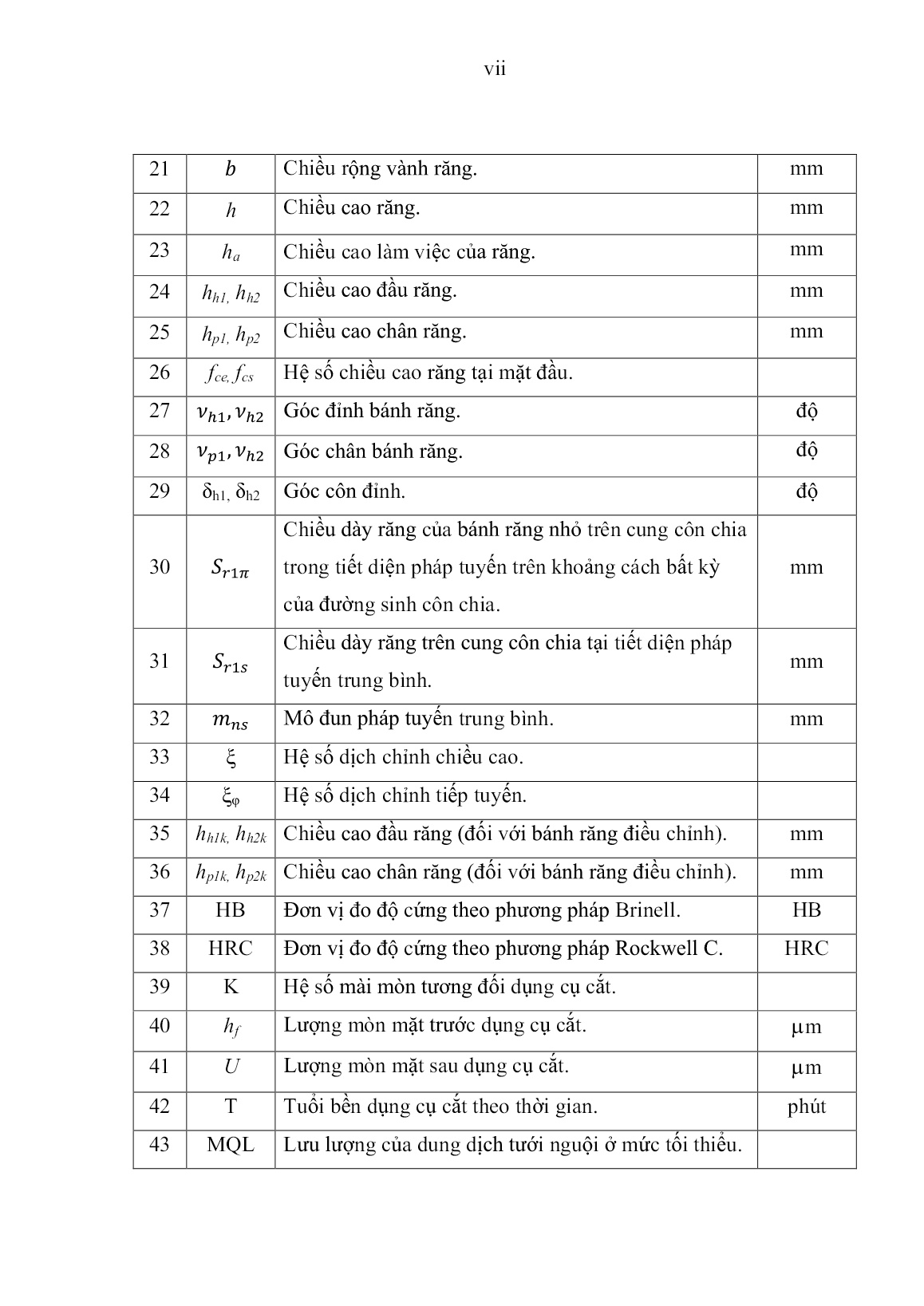
Trang 9
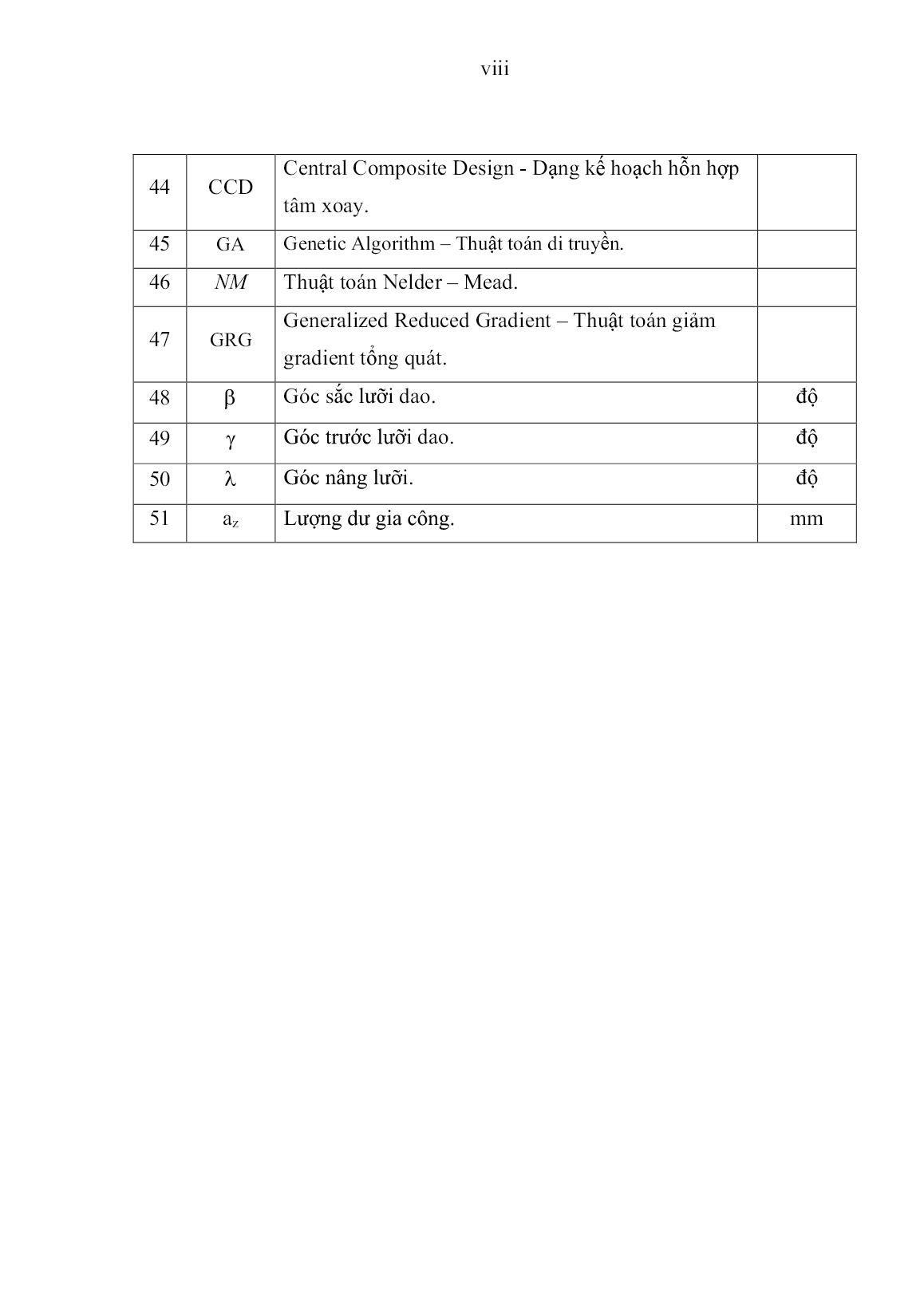
Trang 10
Tải về để xem bản đầy đủ
Bạn đang xem 10 trang mẫu của tài liệu "Luận án Nghiên cứu ảnh hưởng của chế độ cắt đến độ nhám bề mặt răng và lượng mòn dao khi cắt tinh bánh răng côn cung tròn bằng đầu dao hợp kim cứng", để tải tài liệu gốc về máy hãy click vào nút Download ở trên.
Tóm tắt nội dung tài liệu: Luận án Nghiên cứu ảnh hưởng của chế độ cắt đến độ nhám bề mặt răng và lượng mòn dao khi cắt tinh bánh răng côn cung tròn bằng đầu dao hợp kim cứng
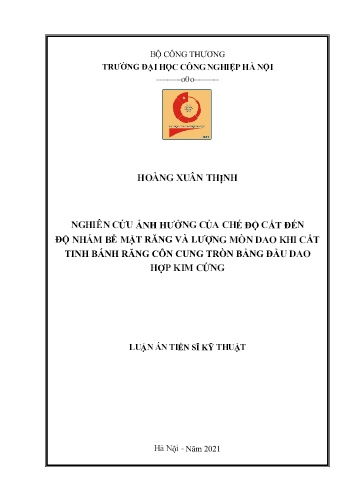
I 2:1 I 4:1 U Hình 2.18. Mòn mặt sau dao phay bánh răng côn cung tròn [22] Quá trình mòn dụng cụ theo thời gian cũng giống như quá trình mòn các chi tiết máy khi làm việc. Ở giai đoạn đầu dao bị mòn nhanh (mòn ban đầu) – đoạn AO, sau đó đến giai đoạn mòn ổn định (quá trình làm việc) - đoạn AB (hình 2.19). Sau quá trình mòn ổn định là giai đoạn mòn phá hủy – đoạn BC, 54 giai đoạn này dụng cụ không làm việc nữa, trị số (U) được chọn làm chuẩn mài mòn [22]. U(m) C B A (I) (II) (III) 0 T1 T2 T(phút) Hình 2.19. Quan hệ giữa lượng mòn và thời gian [22]. 2.2.3.2. Mài mòn theo mặt trước Trong quá trình cắt, do phoi trượt trên mặt trước hình thành một trung tâm áp lực cách lưỡi cắt một khoảng nào đó nên mặt trước bị mòn theo dạng lưỡi liềm. Vết lõm lưỡi liềm đó trên mặt trước do vật liệu dụng cụ cắt bị bóc theo phoi trong quá trình chuyển động như hình 2.20. Vết lõm lưỡi liềm thường xảy ra dọc theo lưỡi cắt và được đánh giá bởi chiều rộng lưỡi liềm B. Chiều sâu hf và khoảng cách từ lưỡi dao đến rãnh Kz đo theo mặt trước [11], [22]. B B h a b B-B I 2:1 I Kz 4:1 B hf Hình 2.20. Mòn mặt trước dao phay bánh răng côn cung tròn [22] 55 Mài mòn theo mặt trước thường xảy ra khi cắt các loại vật liệu dẻo với chiều dày cắt lớn (a > 0,6mm). Trong trường hợp đó nhiệt cắt ở mặt trước cao hơn nhiệt độ ở mặt sau. Vì mặt trước bị mài mòn theo dạng lưỡi liềm (phoi trượt và có trung tâm áp lực) nên lượng mòn theo mặt trước được đánh giá bởi hệ số mài mòn tương đối. ℎ 퐾 = (2.4) + 퐾 2 Hệ số mài mòn tương đối (K) là tỷ lệ giữa chiều sâu rãnh và chiều rộng rãnh. Lượng (B/2 + Kz) là khoảng cách từ tâm rãnh đến lưỡi cắt, hf là chiều sâu rãnh (hình 2.20). Hệ số mài mòn tương đối cho phép trên mặt trước đối với dụng cụ cắt bằng hợp kim cứng (K= 0,4), đối với dụng cụ cắt bằng thép gió có thể chọn lớn hơn. Tùy thuộc vào điều kiện cắt mà giá trị (K) có thể đạt trước hoặc sau (U). Ở một số nguyên công đặc biệt, chỉ tiêu đánh giá lượng mòn cho phép của dụng cụ phụ thuộc rất nhiều vào độ chính xác gia công và độ nhấp nhô bề mặt. Trong các trường hợp đó chỉ tiêu đánh giá lượng mòn được xác định theo phương pháp tuyến với bề mặt gia công (lượng mòn hướng kính). Chỉ tiêu này được gọi là chỉ tiêu mòn kích thước [11], [22]. 2.2.3.3. Mài mòn đồng thời mặt trước và mặt sau Dụng cụ bị mòn mặt trước và mặt sau tạo thành lưỡi cắt mới như hình 2.21. Chiều rộng vát trên mặt trước giảm dần từ hai phía và do đó độ bền lưỡi cắt giảm. Trường hợp này thường gặp khi gia công vật liệu dẻo với chiều dày cắt ar = 0,1÷ 0,5 (mm) [11], [22]. 56 B B h a b B-B I 2:1 I 4:1 U B hf Hình 2.21. Mòn mặt trước và mặt sau dao phay bánh răng côn cung tròn [22] 2.2.3.4. Mòn tù lưỡi cắt Ở dạng này dụng cụ bị mòn dọc theo lưỡi cắt, tạo thành dạng cung hình trụ. Bán kính được đo trong bề mặt vuông góc với lưỡi cắt như hình 2.22. Dạng mòn này thường gặp khi gia công các loại vật liệu có tính dẫn nhiệt kém, đặc biệt khi gia công các vật liệu dẻo. Do nhiệt cắt tập trung ở mũi dao nên dao bị tù nhanh. B B h a b B-B I 2:1 I 4:1 Hình 2.22. Mòn tù lưỡi cắt dao phay bánh răng côn cung tròn [22] 57 Nhận xét: Trong các dạng mòn thì mòn mặt sau của dụng cụ cắt nhận được nhiều quan tâm trong thực tế sản xuất nói chung và gia công bánh răng côn cung tròn nói riêng. Mòn mặt sau của dụng cụ cắt ảnh hưởng trực tiếp đến độ chính xác kính thước và chất lượng bề mặt sườn răng của bánh răng sau khi gia công. Vì những lý do này, nghiên cứu ảnh hưởng mòn mặt sau và tuổi bền của dụng cụ cắt là tiêu chí quan trọng để đánh giá chất lượng của chi tiết và khả năng gia công của dụng cụ cắt. 2.2.4. Các yếu tố ảnh hưởng đến mòn dụng cụ cắt 2.2.4.1. Ảnh hưởng của vận tốc cắt đến mòn dụng cụ cắt. Khi gia công thép các bon ở tốc độ cắt thấp, nhiệt cắt không cao, phoi kim loại tách dễ, biến dạng của lớp kim loại không đều. Vì vậy nhám bề mặt thấp nhưng dụng cụ cắt sẽ mòn ít hơn, độ bền cao hơn. Khi tăng tốc độ cắt lên khoảng 20 ÷ 30(m/phút) thì nhiệt cắt và lực cắt đều tăng gây ra biến dạng dẻo mạnh, ở mặt trước và mặt sau của dao kim loại bị chảy dẻo. Khi lớp kim loại bị nén chặt ở mặt trước và nhiệt độ cao làm tăng hệ số ma sát ở vùng cắt sẽ hình thành lẹo dao. Lẹo dao làm tăng nhám bề mặt gia công. Nếu tiếp tục tăng tốc độ cắt, lẹo dao bị nung nóng nhanh hơn, vùng kim loại bị phá huỷ, lực dính của lẹo dao không thắng nổi lực ma sát của dòng phoi và lẹo dao bị cuốn đi, thường lẹo dao biến mất ứng với tốc độ cắt trong khoảng 30 ÷ 60(m/phút). Với tốc độ cắt lớn (lớn hơn 60 m/phút) thì lẹo dao không hình thành được nên dao sẽ bị mòn nhanh hơn hay tuổi bền dao thấp đi lúc đó nhám bề mặt gia công giảm [9]. Fritz Klocke và cộng sự [61] khi khảo sát ảnh hưởng của vận tốc cắt đến lượng mòn dao khi gia bằng dụng cụ cắt có phủ lớp (Al,Cr)N đã xây dựng được biểu đồ như trong hình 2.23. Trong đó, VB là lượng mòn dao (mm), “l” là một chỉ số để qui ước tuổi bền của dao tính. Khi l=1 có nghĩa là cần thay hoặc mài lại dao. 58 Quan sát hình 2.23 cho thấy: lượng mòn dao sẽ tăng nếu giảm vận tốc cắt. Tuy nhiên ảnh hưởng của vận tốc cắt đến lượng mòn dao là không nhiều. Khi vận tốc cắt thay đổi gần 3 lần từ 750 ÷ 2000 (m/phút) thì lượng mòn dao cũng thay đổi khá ít. Hình 2.23. Ảnh hưởng của vận tốc cắt đến lượng mòn dao khi gia bằng dụng cụ cắt có phủ lớp (Al,Cr)N [61] 2.2.4.2. Ảnh hưởng của lượng chạy dao đến mòn dụng cụ cắt. Lượng chạy dao ngoài ảnh hưởng mang tính chất hình học còn ảnh hưởng lớn đến mức độ biến dạng dẻo và biến dạng đàn hồi ở bề mặt gia công, làm cho nhám và lượng mòn dụng cụ cắt thay đổi [5], [6]. Tuy nhiên, theo nghiên cứu của hãng dụng cụ cắt SandVik [121] cho thấy lượng chạy dao có ảnh hưởng đến tuổi bền của dụng cụ cắt. Ibrahim và cộng sự [81] đã nghiên cứu so sánh tuổi bền của bốn loại dụng cụ cắt khi gia công hai loại hợp kim là Ti5553 và Ti6Al4V. Trong nghiên cứu này, họ đã chọn giới hạn mòn cho phép của mặt sau dụng cụ cắt là 0.4mm. Kết quả nghiên cứu của họ được trình bày trong các hình 2.24 và hình 2.25 (trong đó Vc là vận tốc cắt, fz là lượng chạy dao, ap là chiều sâu cắt). Quan sát hình 2.24a là trường hợp gia công với vận tốc cắt 70 (m/phút), chiều sâu cắt 0,5 (mm) cho thấy: 59 - Đối với dụng cụ cắt H13A, tuổi bền của dao khi gia công với lượng chạy dao 0,15(mm/răng) có giá trị lớn hơn nhiều so với khi gia công với lượng chạy dao có giá trị 0,1(mm/răng) và 0,2(mm/răng). - Khi sử dụng vật liệu dụng cụ cắt có ký hiệu variant1, nếu gia công với lượng chạy dao 0,1(mm/răng) và 0,15(mm/răng) thì tuổi bền của dao lớn hơn nhiều so với khi gia công với lượng chạy dao 0,2(mm/răng). - Đối với dụng cụ cắt có vật liệu được ký hiệu là variant4, khi gia công với lượng chạy dao 0,15(mm/răng) thì tuổi bền của dao đạt giá trị lớn nhất, tiếp đến là trường hợp gia công với lượng chạy dao 0,1(mm/răng). Khi gia công với lượng chạy dao 0,2(mm/răng) thi tuổi bền của dao là nhỏ nhất. Quan sát hình 2.24b là trường hợp gia công với vận tốc cắt 115(m/phút), chiều sâu cắt 0,5(mm) cho thấy: cả ba loại dụng cụ cắt H13A, variant1 và variant4, tuổi bền của dao khi gia công với lượng chạy dao 0,1(mm/răng) có giá trị lớn hơn nhiều so với khi gia công với lượng chạy dao có giá trị 0,15(mm/răng) và 0,2(mm/răng). Có nghĩa là khi tăng lượng chạy dao sẽ làm cho tuổi bền của dao giảm. Hình 2.24. Tuổi bền của dao khi gia công hợp kim Ti5533 ở những giá trị khác nhau của chế độ cắt [81] Quan sát hình 2.24c là trường hợp gia công với vận tốc cắt 70(m/phút), chiều sâu cắt 2(mm) cho thấy: 60 - Tuổi bền của dụng cụ cắt H13A khi gia công với lượng chạy dao 0,1(mm/răng) và 0,2(mm/răng) có giá trị lớn hơn so với khi gia công với lượng chạy dao 0,15(mm/răng). - Đối với ba loại vật liệu dụng cụ cắt 1105, variant1 và variant4: khi gia công với lượng chạy dao 0,1(mm/răng) tuổi bền của dao là lớn nhất, tiếp theo đó là đến tuổi bền của dao khi lượng chạy dao là 0,15(mm/răng). Trường hợp khi lượng chạy dao là 0,2(mm/răng) thì tuổi bền của dao là nhỏ nhất. Như vậy có thể thấy, với ba loại dụng cụ cắt này (1105, variant1 và variant4) thì khi tăng lượng chạy dao sẽ làm giảm tuổi bền của dao. Quan sát hình 2.25 cho thấy: - Trong cả ba trường hợp khác nhau về lượng chạy dao (0,1mm/răng – hình 2.25a; 0,15 mm/ răng – hình 2.25b và 0,2 mm/răng – hình 2.25c) thì với cả ba loại dụng cụ cắt (H13A, variant1 và variant4) khi gia công hợp kim Ti6Al4V tuổi bền của dao sẽ lớn hơn khi gia công hợp kim Ti5533. Hình 2.25. So sánh tuổi bền của dao khi gia công hai loại hợp kim Ti5533 và Ti6Al4V ở những giá trị khác nhau của chế độ cắt [81] - Khi gia công vật liệu Ti6Al4V với lượng chạy dao 0,1(mm/răng) và 0,15 (mm/răng) thì dụng cụ cắt variant1 có tuổi bền lớn nhất, tiếp theo là đến tuổi bền của dụng cụ cắt variant4, dụng cụ cắt H13A có tuổi bền nhỏ nhất. Kết quả này cũng phù hợp với trường hợp khi gia công vật liệu Ti5533. 61 - Khi gia công với lượng chạy dao 0,2(mm/răng), nếu vật liệu gia công là Ti6Al4V thì dụng cụ cắt variant4 có tuổi bền cao nhất, tiếp theo là đến tuổi bền của dụng cụ cắt variant1, dụng cụ cắt H13A có tuổi bền nhỏ nhất. - Với vật liệu gia công là Ti5533, khi lượng chạy dao là 0,2(mm/răng) thì tuổi bền của dụng cụ cắt variant1 và variant4 là tương đương nhau và lớn hơn tuổi bền của dụng cụ cắt H13A. - Với cả ba loại dụng cụ cắt thì khi lượng chạy dao tăng sẽ làm cho tuổi bền của dao giảm. Tuy nhiên ảnh hưởng của lượng chạy dao đến tuổi bền của dao là không giống nhau đối với các loại dao khác nhau. Ví dụ, xét trường hợp khi sử dụng dao variant1 để gia công vật liệu Ti6Al4V, khi lượng chạy dao tăng từ 0,1 ÷ 0,15(mm/răng) thì tuổi bền của dao giảm từ 72(phút) xuống 38(phút); khi lượng chạy dao tăng từ 0,15 ÷ 0,2(mm/răng) thì tuổi bền của dao giảm từ 38(phút) xuống 12(phút). Vấn đề này cũng xảy ra tương tự khi sử dụng những loại dụng cụ khác nhau để gia công những loại vật liệu khác nhau trong từng điều kiện về giá trị của lượng chạy dao. 2.2.4.3. Ảnh hưởng của chiều sâu cắt đến mòn dụng cụ cắt. Ảnh hưởng của chiều sâu cắt đến mòn dao không nhiều như vận tốc cắt và lượng chạy dao. Tuy nhiên, nếu chiều sâu cắt quá lớn dẫn đến rung động trong quá trình cắt tăng lên, do đó độ nhấp nhô tế vi bề mặt tăng, dao dễ vỡ và mòn nhanh. Ngược lại, chiều sâu cắt quá nhỏ sẽ làm cho dao bị trượt trên bề mặt gia công và xảy ra hiện tượng cắt không liên tục dẫn đến độ nhấp nhô tế vi bề mặt tăng. Hiện tượng gây trượt dao thường ứng với giá trị của chiều sâu cắt trong khoảng 0,01÷ 0,02(mm) [121]. 2.2.4.4. Ảnh hưởng đồng thời các yếu tố đến mòn dụng cụ cắt. Zhaoju Zhu và cộng sự [118] khi thí nghiệm phay hợp kim của titan (titanium alloy-Ti6Al4V) bằng mảnh cắt có ký hiệu Walter JDXTIZY4GWT /20*40*50R0 để đánh giá lượng mòn mặt sau của dao. Một số thông số cơ bản về chế độ cắt đã 62 được họ sử dụng trong nghiên cứu này có giá trị như trong bảng 2.1. Từ kết quả nghiên cứu, họ đã xây dựng được biểu đồ như hình 2.26. Bảng 2.1. Giá trị của một số thông số công nghệ đã được sử dụng [118] Số mảnh cắt: 4 Góc xoắn: 450 Đường kính dao: 20 (mm) Chiều dài dao: 105(mm) Vận tốc cắt: 120 (m/phút) Lượng chạy dao: 0,1(mm/răng) Chiều sâu cắt: 18 (mm) Chi ều rộng cắt: 0,8(mm) Tốc độ trục chính:1909,92 (v/phút) Lư ợng chạy dao: 763,97(mm/phút) Quan sát hình 2.26 cho thấy: với chế độ công nghệ như trong bảng 2.1 thì giai đoạn mòn ban đầu của dụng cụ cắt kéo dài trong khoảng thời gian là 40 (phút), sau giai đoạn này mặt sau của dụng cụ cắt đã mòn 0,05(mm). Giai đoạn mòn bình thường kéo dài trong khoảng thời gian 130 (phút) với lượng mòn khoảng 0,12(mm). Khi thời gian cắt vượt quá 170 (phút) thì hiện tượng mòn khốc liệt xảy ra, dao bị mòn rất nhanh, đây cũng chính là giới hạn về tuổi bền của dao. Hình 2.26. Lượng mòn mặt sau của dao khi phay Ti6Al4V) dao Walter JDXTIZY4GWT/20*40*50R0 [118] Palanisamy và cộng sự [94] khi nghiên cứu ảnh hưởng của vận tốc cắt, lượng chạy dao và chiều sâu cắt đến lượng mòn dao khi gia công thép AISI 1020 bằng dụng cụ cắt làm từ vật liệu P20 (thép gió) đã xác định được rằng vận tốc cắt là thông số có ảnh hưởng lớn nhất đến lượng mòn dao, tiếp theo là đến 63 mức độ ảnh hưởng của lượng chạy dao, chiều sâu cắt là thông số có ảnh hưởng ít nhất đến lượng mòn dao. Ngoài ra, trong nghiên cứu này, họ cũng đã xây dựng được biểu đồ về sự ảnh hưởng tương tác giữa các thông số đến lượng mòn dao như trong các hình 2.27 đến hình 2.29. Quan sát các hình 2.27 đến hình 2.29 cho thấy, khi vận tốc cắt, lượng chạy dao và chiều sâu cắt tăng thì sẽ làm tăng lượng mòn dao. Hình 2.27. Ảnh hưởng tương tác của lượng chạy dao và vận tốc cắt đến lượng mòn dao khi gia công thép AISI 1020 bằng dao P20 [94] Hình 2.28. Ảnh hưởng tương tác của chiều sâu cắt và lượng chạy dao đến lượng mòn dao khi gia công thép AISI 1020 bằng dao P20 [94] 64 Hình 2.29. Ảnh hưởng tương tác của vận tốc cắt và chiều sâu cắt đến lượng mòn dao khi gia công thép AISI 1020 bằng dao P20 [94] Duong Xuan-Truong và cộng sự [55] khi nghiên cứu về lượng mòn dao trong trường hợp sử dụng dao được phủ lớp PVD để gia công thép Inconel 718 đã đưa ra kết luận: cả ba thông số của chế độ cắt gồm vận tốc cắt, lượng chạy dao và chiều sâu cắt đều có ảnh hưởng đáng kể đến lượng mòn dao. Trong đó, vận tốc cắt là thông số có ảnh hưởng lớn nhất đến lượng mòn dao, tiếp theo là đến mức độ ảnh hưởng của chiều sâu cắt, lượng chạy dao là thông số có ảnh hưởng ít nhất đến lượng mòn dao. 2.2.4.5. Ảnh hưởng của vật liệu làm dụng cụ cắt. Ali Riza Motorcu và cộng sự [41] đã nghiên cứu ảnh hưởng của vận tốc cắt và vật liệu dụng cụ cắt đến lượng mòn dao khi phay thép Inconel 718. Hai loại dụng cụ cắt đã được họ sử dụng trong nghiên cứu này là loại dụng cụ cắt phủ TiAlN và loại dụng cụ cắt phủ TiAlN + TiN. Kết quả nghiên cứu của họ được chỉ ra trong hình 2.30. 65 Hình 2.30. Ảnh hưởng của vận tốc cắt và vật liệu dụng cụ cắt đến lượng mòn dao khi gia công thép Inconel 718 [41] Quan sát hình 2.30 cho thấy: - Dụng cụ cắt được phủ TiAlN + TiN có lượng mòn dao nhỏ hơn so với lượng mòn dao của dụng cụ cắt được phủ TiAlN. Hay nói cách khác, tuổi bền của dụng cụ cắt phủ TiAlN + TiN lớn hơn tuổi bền của dụng cụ cắt phủ TiAlN. - Đối với cả hai loại vật liệu dụng cụ cắt, khi tăng vận tốc cắt thì lượng mòn dao tăng rất nhanh. 2.2.4.6. Ảnh hưởng của vật liệu gia công đến mòn dụng cụ cắt Sredanović và cộng sự [45] đã thí nghiệm khảo sát ảnh hưởng của độ cứng vật liệu gia công và vận tốc cắt đến tuổi bền của dao được phủ TiAlN trong điều kiện sử dụng dung dịch tưới nguội ở mức tối thiểu (MQL). Vật liệu gia công được sử dụng trong nghiên cứu này là thép X155CrVMo12 có các mức độ cứng 45HRC, 54HRC và 63HRC. Ba giá trị của vận tốc cắt đã được họ sử dụng trong nghiên cứu này là 40(m/ph), 55(m/ph) và 70(m/ph). Kết quả nghiên cứu của họ được chỉ ra trong hình 2.31. 66 Hình 2.31. Tuổi bền của dao khi thay đổi độ cứng vật liệu gia công và vận tốc cắt [45] Quan sát hình 2.31 cho thấy: khi độ cứng vật liệu gia công và vận tốc cắt tăng thì tuổi bền của dao giảm. Trong phạm vi về độ cứng của vật liệu gia công và vận tốc cắt đã khảo sát, dao sẽ có tuổi bền lớn nhất khi gia công vật liệu có độ cứng 45HRC ở vận tốc cắt 40(m/ph), ngược lại khi gia công vật liệu có độ cứng 63HRC ở vận tốc cắt 70(m/ph) thì tuổi bền của dao là nhỏ nhất. Tuy nhiên cũng từ kết quả nghiên cứu của họ cho thấy, tuổi bền của dao là khá nhỏ, tuổi bền của dao có giá trị lớn nhất cũng chỉ vào khoảng 3,5 (phút), điều đó cho thấy việc sử dụng dụng cụ cắt phủ TiAlN để gia công thép X155CrVMo12 là không phù hợp. 2.2.4.7. Ảnh hưởng của phương pháp tưới nguội đến mòn dụng cụ cắt Karaguzel và cộng sự [108] đã nghiên cứu xác định lượng mòn mặt sau của dao khi phay rãnh xoắn trên ba loại vật liệu là Inconel 718, Waspaloy và Ti6Al4V. Dụng cụ cắt đã được sử dụng trong nghiên cứu này là dao phay mặt đầu với 3 mảnh cắt có ký hiệu F40M. Trong nghiên cứu này, với mỗi loại vật liệu cũng đã tiến hành thí nghiệm với ba phương pháp tưới nguội là: gia công 67 khô (dry), gia công theo hình thức tưới tràn (flood cooling) và gia công với lưu lượng của dung dịch tưới nguội ở mức tối thiểu (MQL). Lượng mòn mặt sau của dao khi gia công từng loại vật liệu trong nghiên cứu này được trình bày các hình từ 2.32 đến hình 2.34. Hình 2.32. Ảnh hưởng của phương pháp tưới nguội đến lượng mòn dao khi gia công thép Inconel 718 [108] Hình 2.33. Ảnh hưởng của phương pháp tưới nguội đến lượng mòn dao khi gia công vật liệu Waspaloy [108] 68 Hình 2.34. Ảnh hưởng của phương pháp tưới nguội đến lượng mòn dao khi gia công vật liệu Ti6Al4V [108] Quan sát các hình 32 đến 34 cho thấy: - Đối với cả ba trường hợp khi gia công ba loại vật liệu khác nhau thì gia công không sử dụng dung dịch tưới nguội (gia công khô – Dry) tốc độ mòn dụng cụ là lớn nhất. Điều này cũng dễ thấy vì khi gia công khô, ma sát giữa mặt sau của dụng cụ cắt và bề mặt gia công là rất lớn, nhiệt cắt trong trường hợp này cũng rất lớn làm dao bị mòn với tốc độ nhanh. - Đối với thép Inconel 718, khi mới gia công (thời gian gia công nhỏ hơn 10 phút) thì nếu sử dụng kiểu tưới nguội theo phương pháp MQL sẽ cho tốc độ mòn dao chậm hơn so với khi sử dụng dung dịch tưới nguội theo hình thức tưới tràn. Tuy nhiên, khi thời gian cắt trên 10 (phút), thì tốc độ mòn dao đối với cả hai trường hợp sử dụng dung dịch tưới nguội (MQL và tưới tràn) là tương đương nhau. - Khi gia công vật liệu Waspaloy, trong giai đoạn đầu của quá trình cắt (thời gian nhỏ hơn 5 phút) thì tốc độ mòn của hai trường hợp sử dụng dịch trơn nguội MQL và tưới tràn sẽ có tốc độ mòn dao là tương đương nhau. Khi thời gian gia công nằm trong khoảng từ 5 ÷ 7 (phút) thì phương pháp tưới nguội theo kiểu 69 MQL cho tốc độ mòn dao nhỏ hơn nhiều so với phương pháp tưới tràn. Tuy nhiên, nếu sau khoảng thời gian 7 (phút) thì phương pháp tưới nguội theo kiểu MQL lại làm cho tốc độ mòn dao lớn hơn rất nhiều so với phương pháp tưới tràn. - Đối với loại vật liệu Ti6Al4V, tốc độ mòn dao theo thời gian là như nhau đối với cả hai trường hợp sử dụng dung dịch tưới nguội là MQL và tưới tràn, tuy nhiên lượng mòn dao khi sử dụng dầu tưới nguội theo phương pháp tưới tràn luôn lớn hơn khi sử dụng dầu tưới nguội theo phương pháp MQL. Nhận xét: Thông qua việc phân tích một số nghiên cứu ở trên cho thấy, có nhiều yếu tố ảnh hưởng đến lượng mòn dao, như vật liệu làm dụng cụ cắt, vật liệu gia công, chế độ tưới nguội, chế độ cắt... Trong đó, khảo sát ảnh hưởng của các thông số về chế độ cắt đến mòn dao đã được thực hiện bởi nhiều nghiên cứu. Tuy nhiên, cũng thông qua những nghiên cứu đó cho thấy, ảnh hưởng của các thông số chế độ cắt đến lượng mòn dao trong từng điều kiện gia công cụ thể là không giống nhau. Chính vì lẽ đó, để xác định được mức độ ảnh hưởng của các thông số chế độ cắt đến lượng mòn dao cũng như xác định được chế độ cắt hợp lý để cải thiện lượng mòn dao (giảm lượng mòn dao) thì cần phải có những nghiên cứu thực nghiệm trong từng điều kiện gia công cụ thể. 70 KẾT LUẬN CHƯƠNG 2 1. Chế độ cắt (V, S, t) là các yếu tố ảnh hưởng lớn đến nhám bề mặt sườn răng và lượng mòn dụng cụ cắt. Nghiên cứu và xây dựng mô hình xác định mối quan hệ toán học giữa các thông số công nghệ này với nhám bề mặt sườn răng và lượng mòn dụng cụ cắt khi gia công bánh răng côn cung tròn là nghiên cứu có ý nghĩa; 2. Nhám bề mặt sườn răng tại vùng tiếp xúc của cặp bánh răng khi ăn khớp là yếu tố quan trọng ảnh hưởng đến chất lượng của bộ truyền. Đây là cơ sở để đánh giá nhám bề mặt sườn răng khi gia công tinh bánh răn
File đính kèm:
luan_an_nghien_cuu_anh_huong_cua_che_do_cat_den_do_nham_be_m.pdf
Thong tin luận án (tiếng Anh).pdf
Thong tin luận án (tiếng việt).pdf
TÓM TẮT LUẬN ÁN (tiếng việt).pdf
TÓM TẮT LUẬN ÁN ( tiếng anh).pdf