Luận án Nghiên cứu nâng cao hiệu quả nghiền bột giấy khi dùng máy nghiền dạng đĩa trong ngành công nghiệp giấy
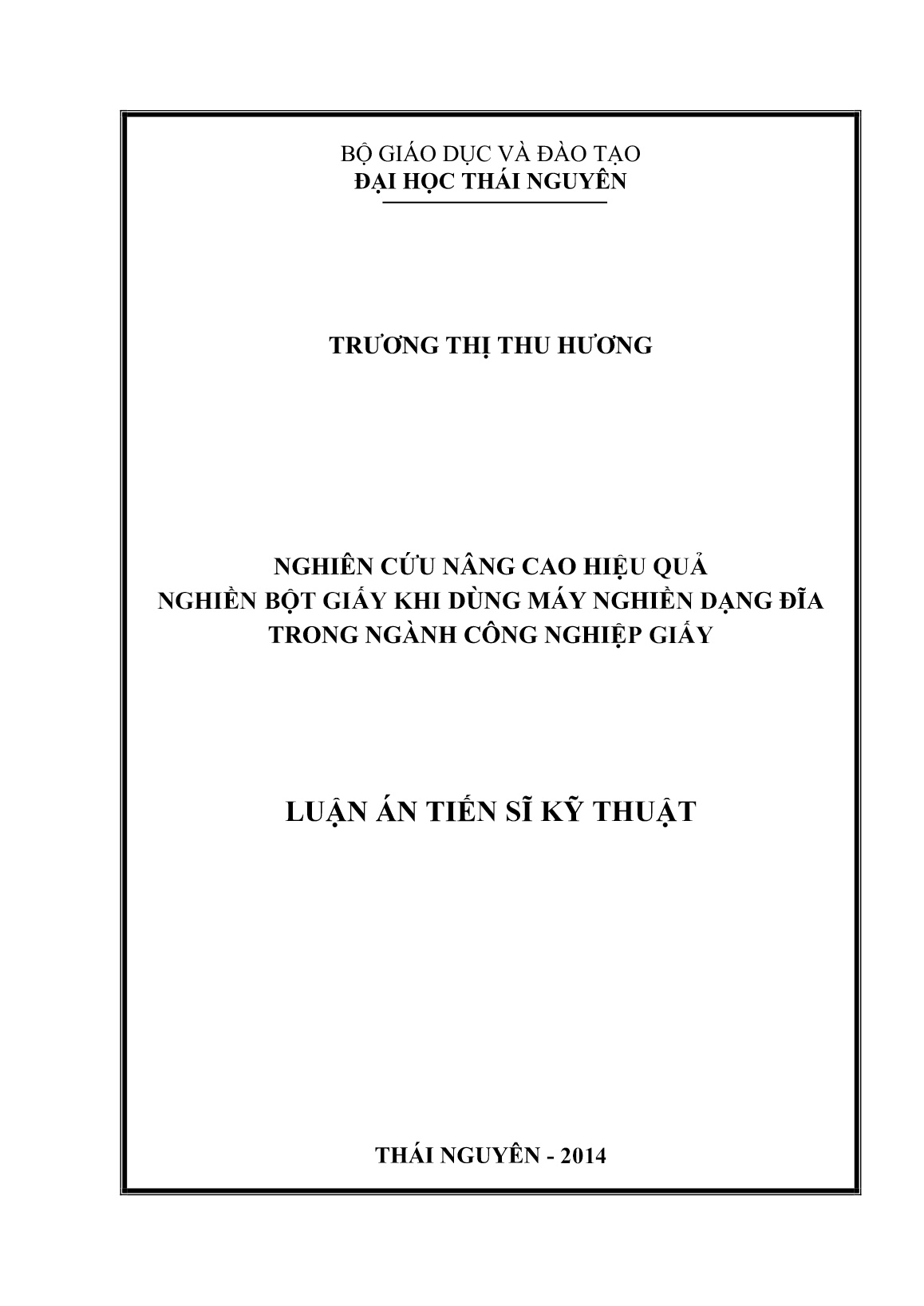
Trang 1

Trang 2
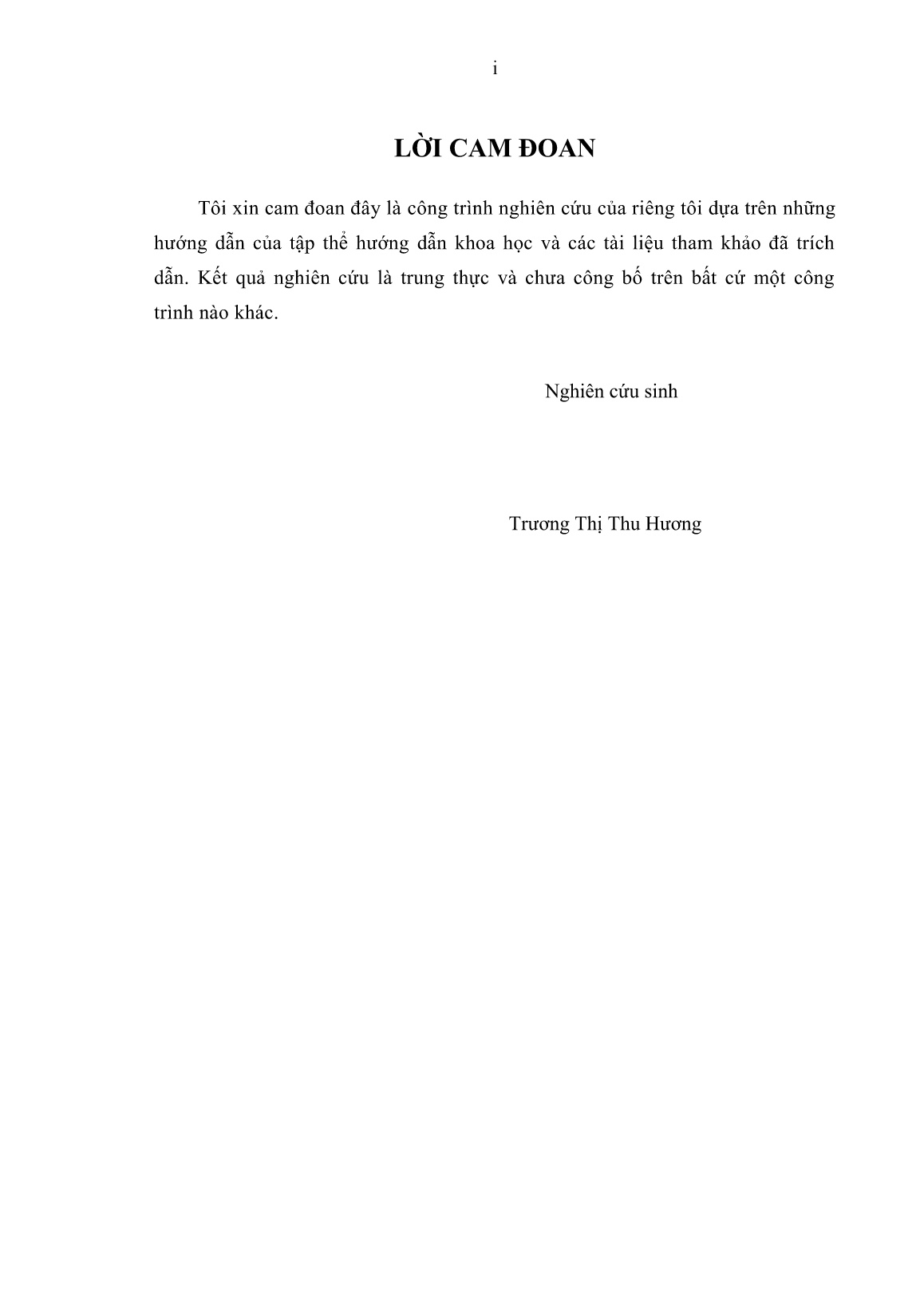
Trang 3
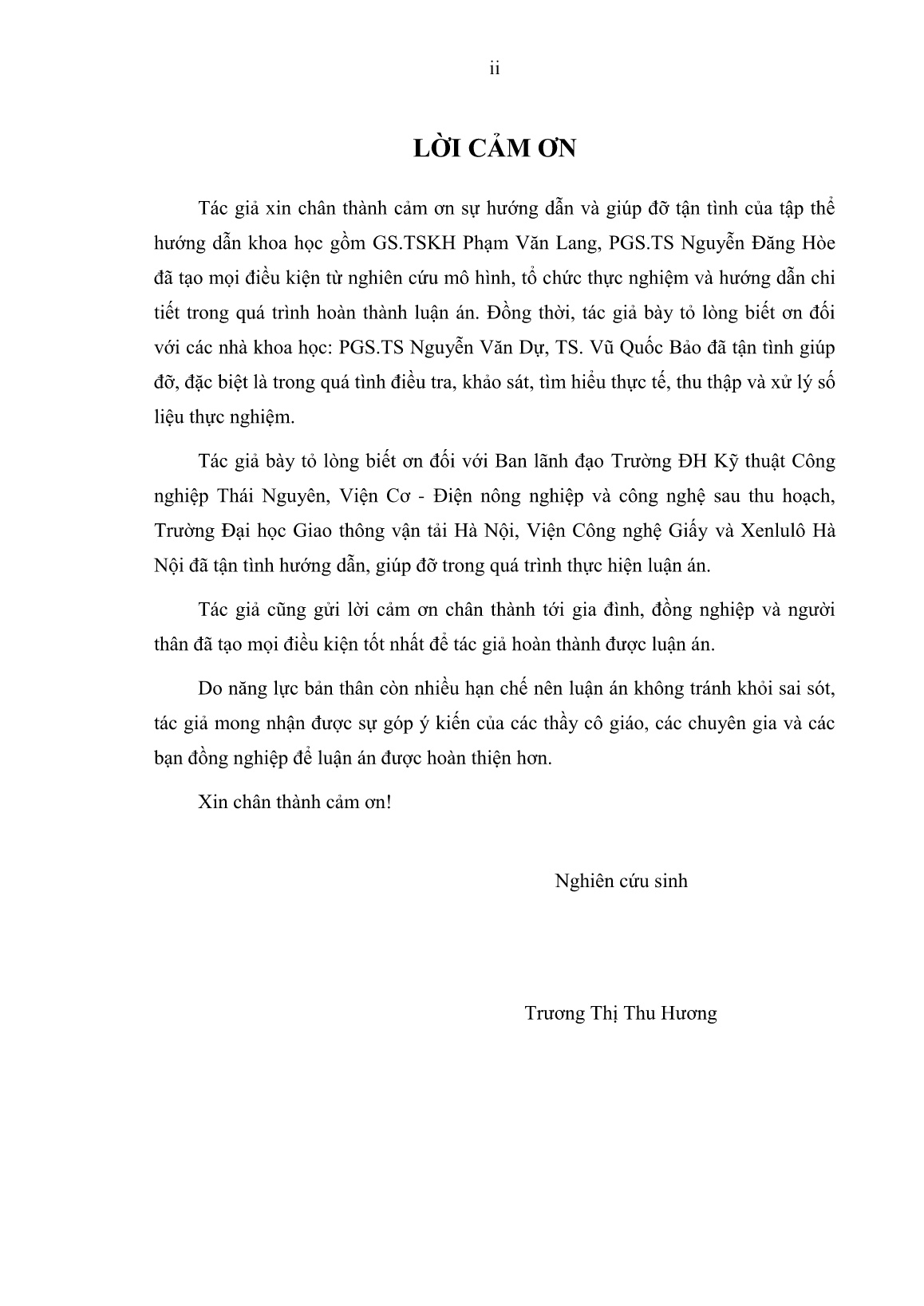
Trang 4
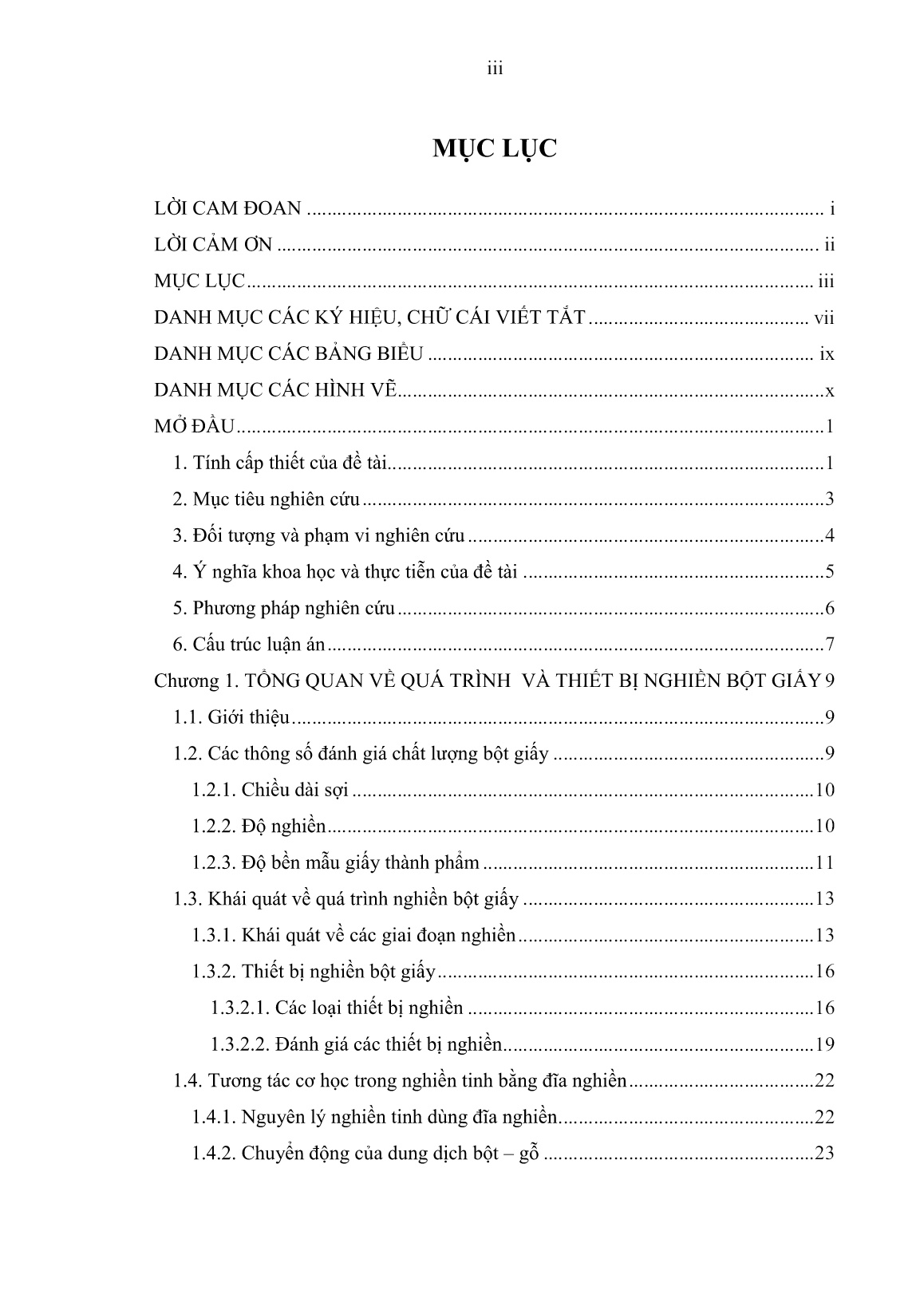
Trang 5
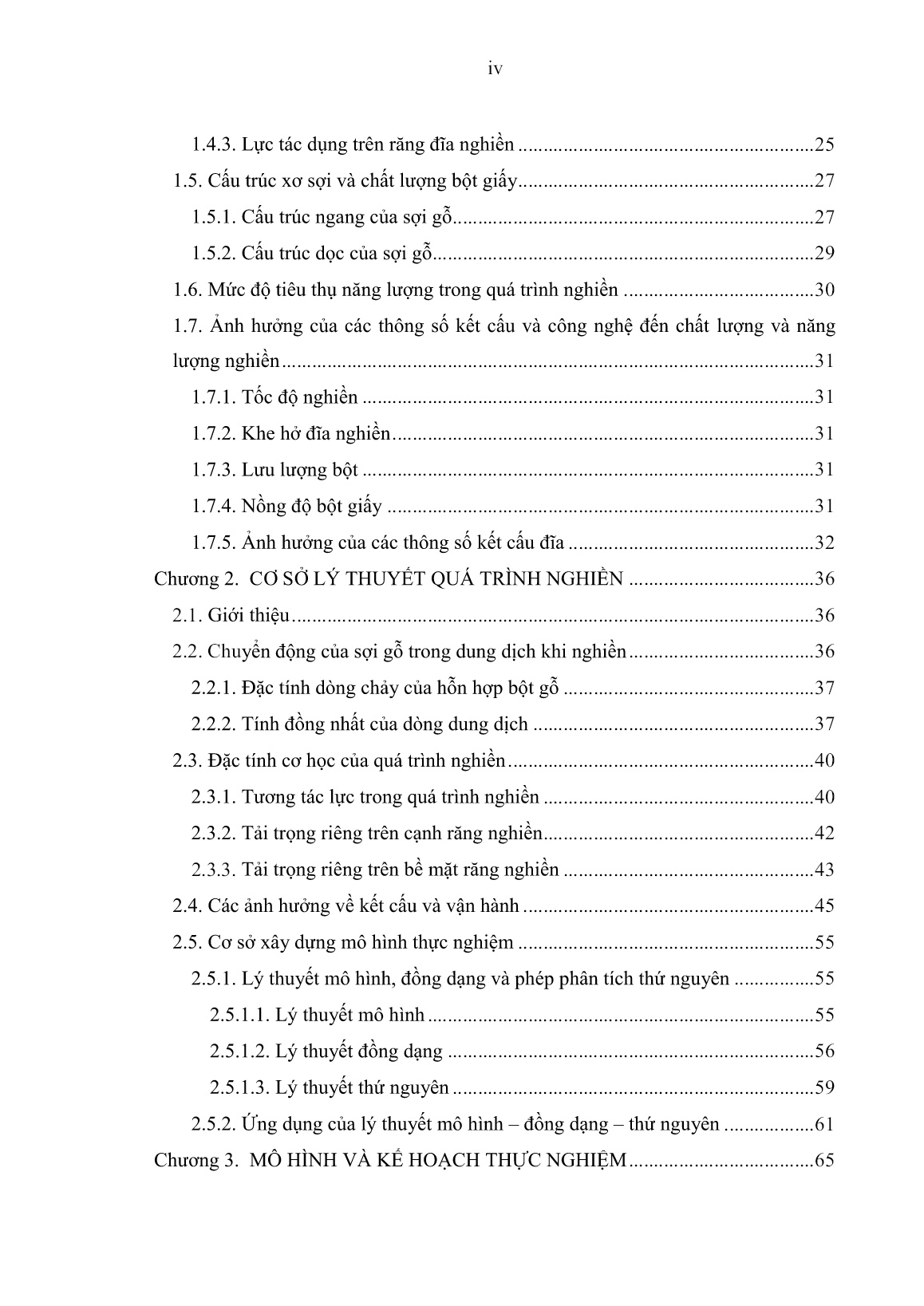
Trang 6
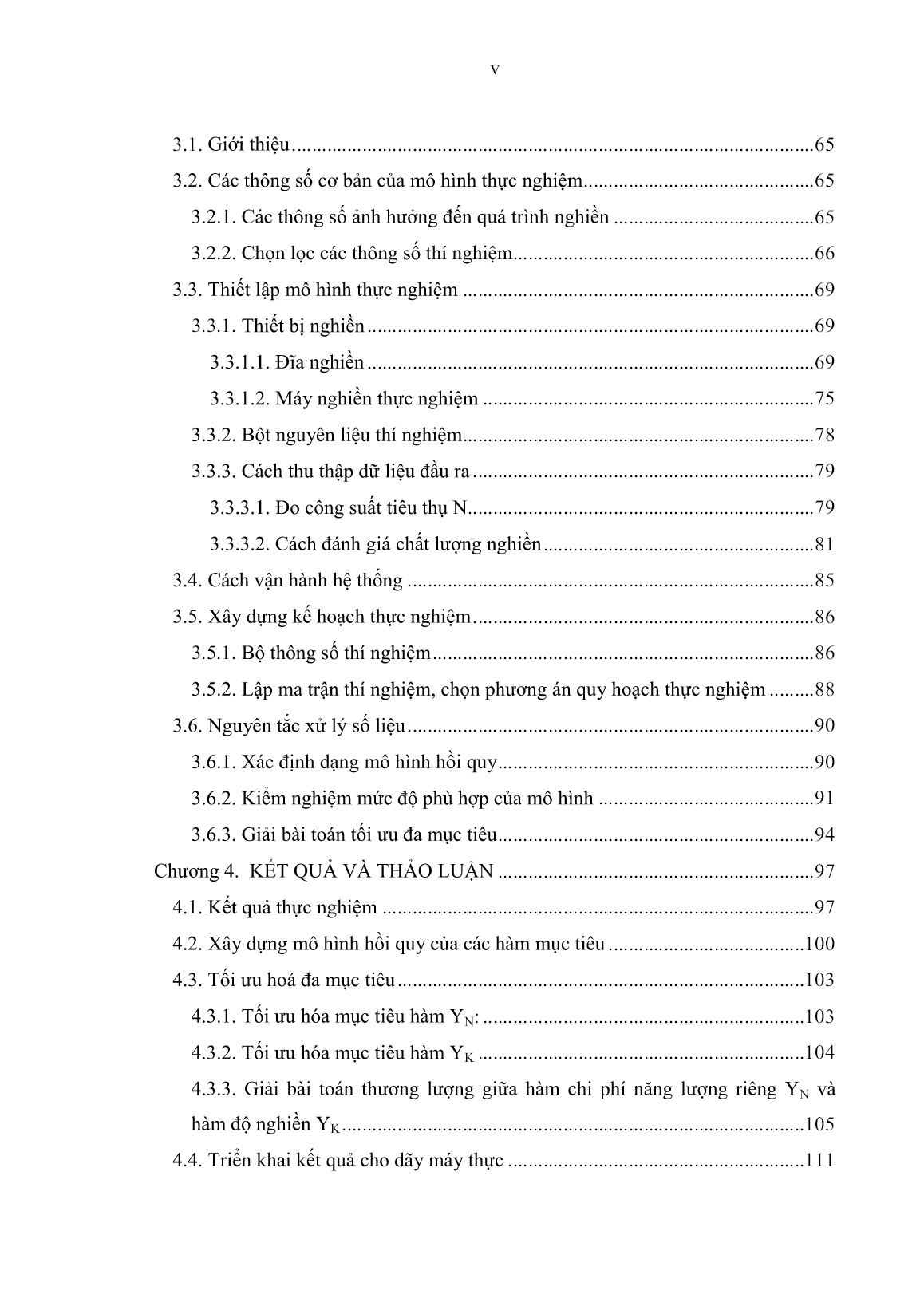
Trang 7
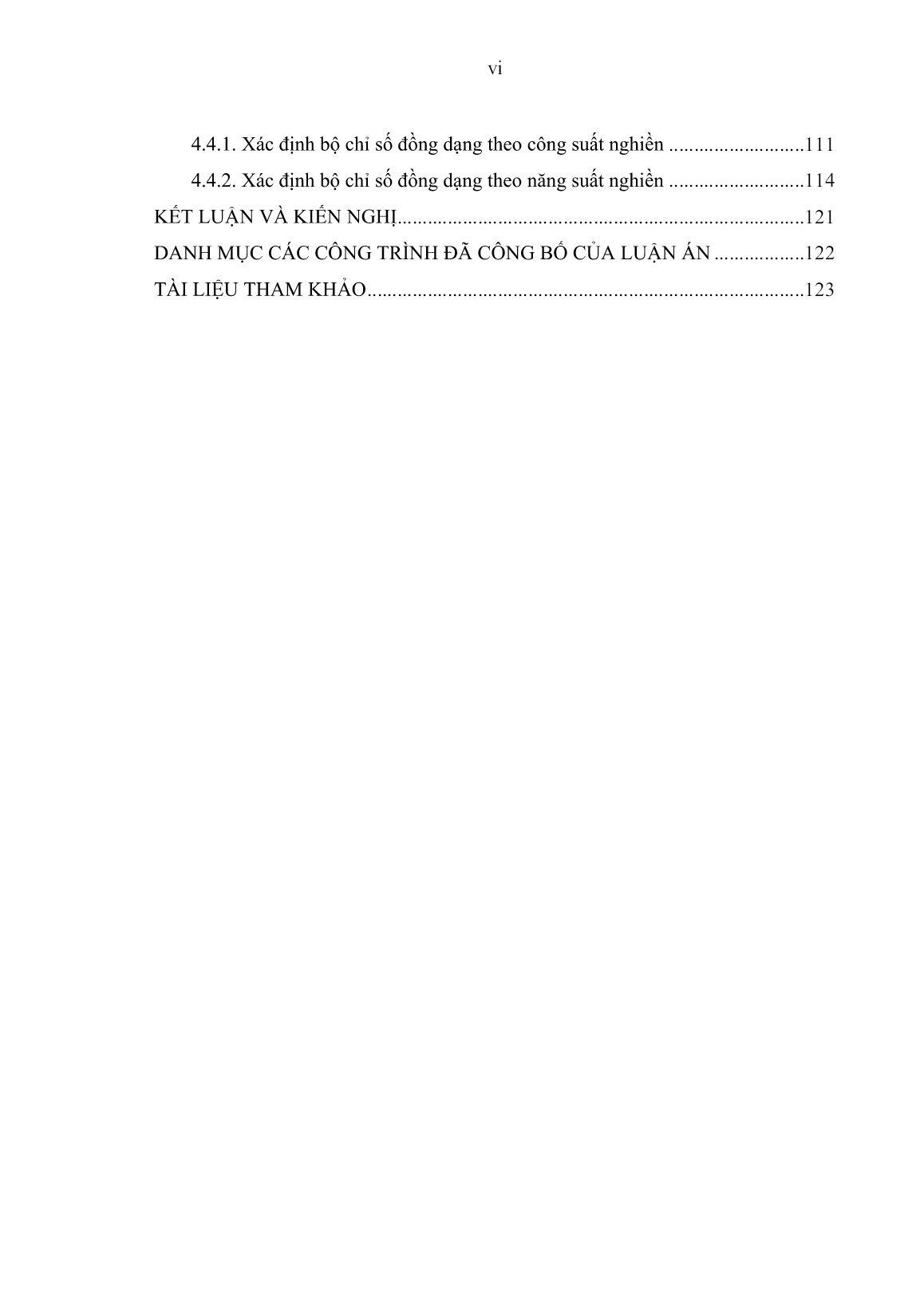
Trang 8
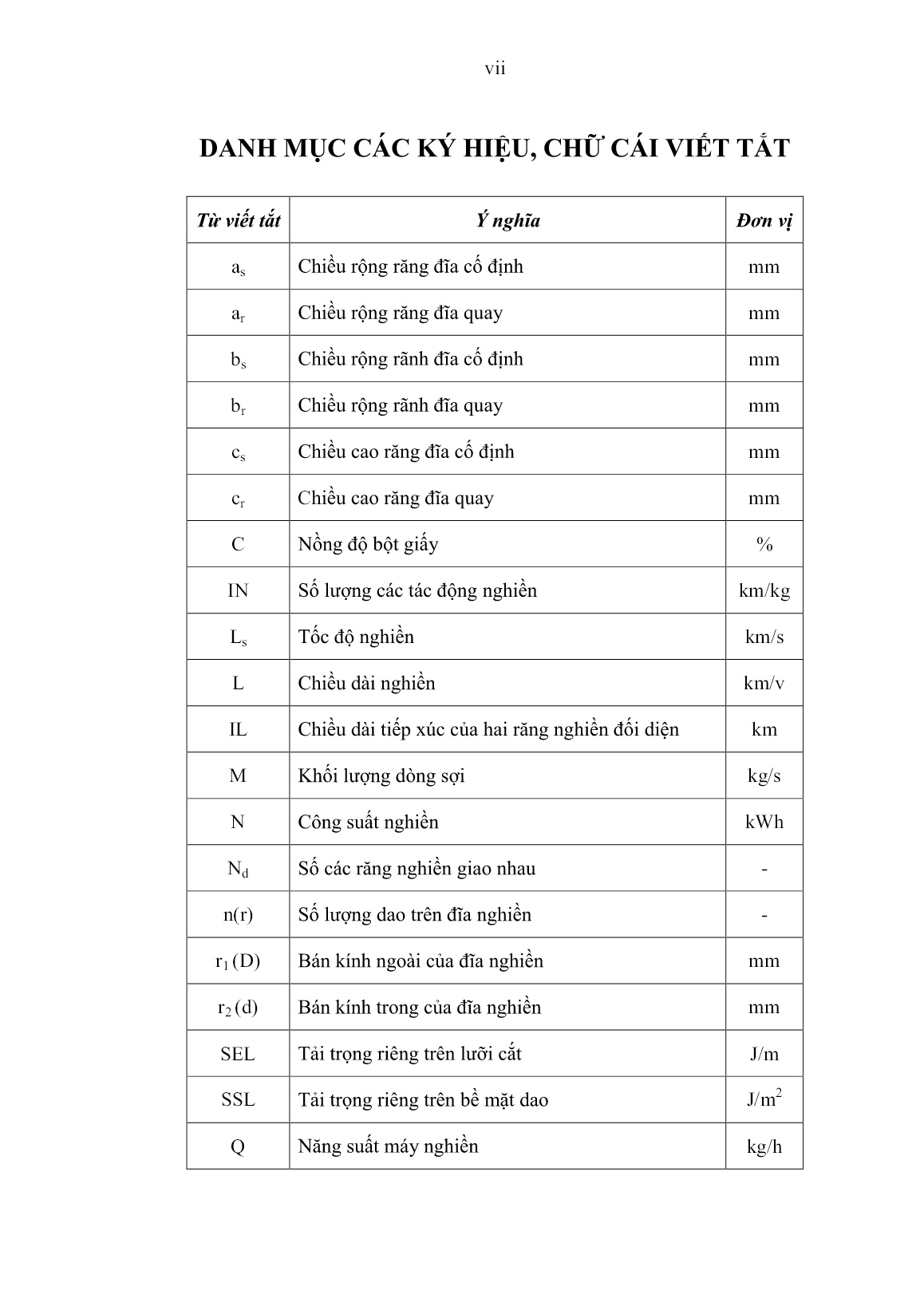
Trang 9
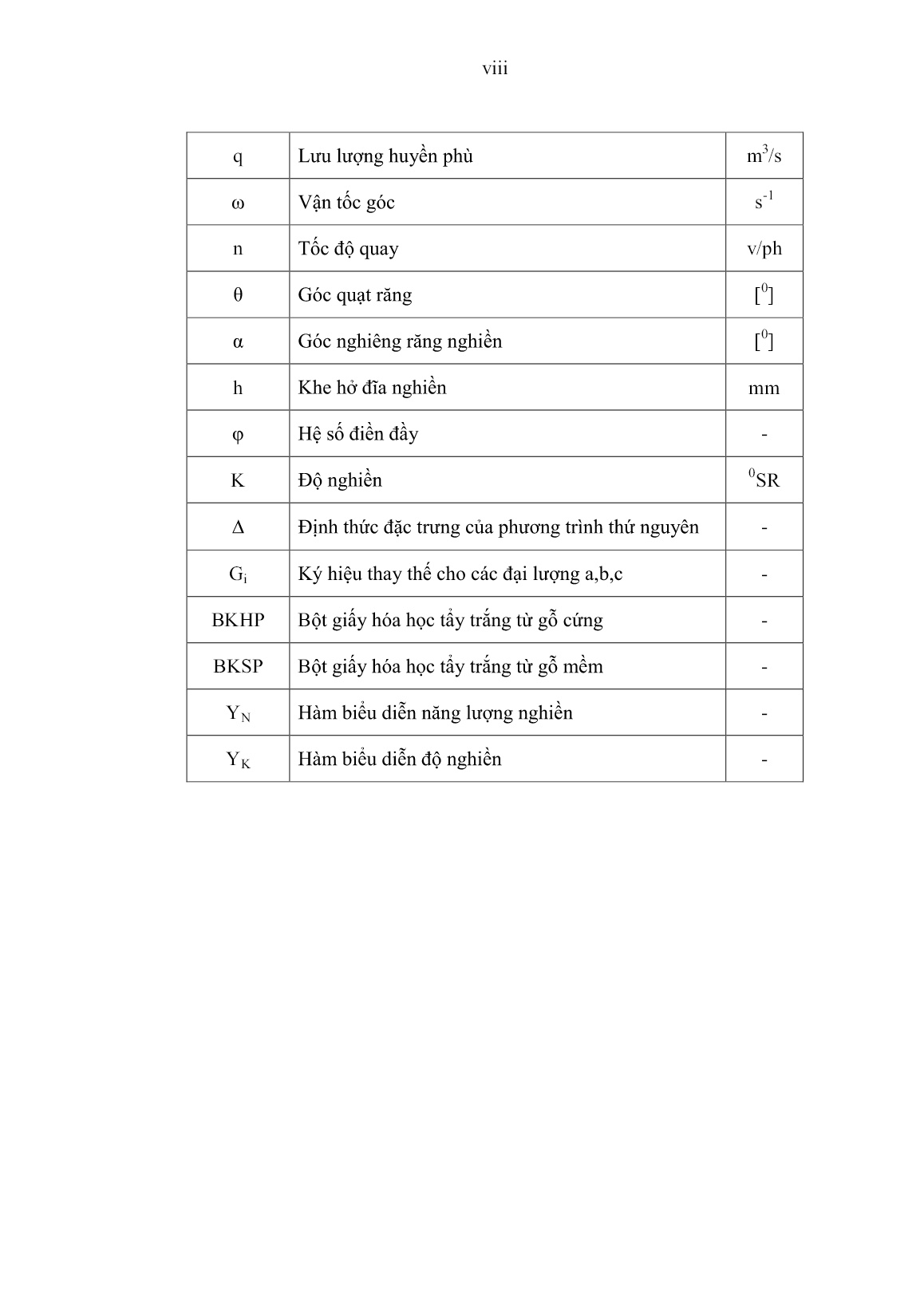
Trang 10
Tải về để xem bản đầy đủ
Bạn đang xem 10 trang mẫu của tài liệu "Luận án Nghiên cứu nâng cao hiệu quả nghiền bột giấy khi dùng máy nghiền dạng đĩa trong ngành công nghiệp giấy", để tải tài liệu gốc về máy hãy click vào nút Download ở trên.
Tóm tắt nội dung tài liệu: Luận án Nghiên cứu nâng cao hiệu quả nghiền bột giấy khi dùng máy nghiền dạng đĩa trong ngành công nghiệp giấy
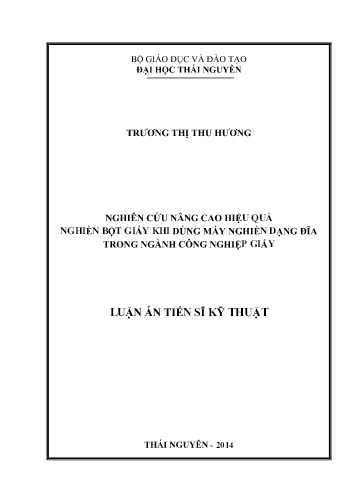
2.3 [9], [46]. Hình 2.3. Các kiểu bố trí răng nghiền 47 Trong các bố trí răng nghiền trên, kiểu (II), (III), (VI), (IX) là các kiểu đĩa nghiền đƣợc phân thành nhiều miền nghiền khác nhau từ tâm đĩa đến chu vi đĩa. Các dạng đĩa nghiền này thƣờng để nghiền dăm gỗ hoặc bán thành phẩm ở nồng độ cao trong giai đoạn nghiền đầu tiên vì kết cấu hình học của đĩa cho phép gia công vật liệu một cách tuần tự từ cắt khúc, cắt thớ và gia công thớ. Tuy nhiên, để tăng cƣờng độ nghiền bằng cách tăng quãng đƣờng chuyển động của vật liệu sợi ở khe hở làm việc, phƣơng án sử dụng cơ cấu nghiền có các vách ngăn ở các rãnh giữa các răng nghiền đã đƣợc đề xuất (kiểu IV, V và VII). Những vách ngăn này cản trở chuyển động trƣợt của xơ sợi bột nghiền theo các rãnh và đƣa chúng đến vùng nghiền. Mặt khác, các rãnh ngăn này làm thay đổi diện tích tiết diện dọc của vùng làm việc chính, tạo ra sự phân bố tốc độ của luồng hỗn hợp nghiền do đó có thể hỗ trợ cho việc tăng tác động của các răng nghiền lên xơ sợi bột giấy. Do đó, chúng phù hợp với quá trình nghiền bột giấy ở nồng độ cao. Việc bố trí răng đĩa nghiền theo kiểu (I) và kiểu (III) có thể đƣợc minh họa cụ thể hơn ở hình 2.4. Hình 2.4. Các dạng đĩa nghiền a. Các răng không song song; b. Các răng song song với nhau Hình 2.4a biểu diễn dạng đĩa có răng không song song, các răng tạo với phƣơng hƣớng kính một góc bằng hằng số. Cƣờng độ nghiền thấp cho phép xử lý sợi tốt. Cách tốt nhất để đạt đƣợc cƣờng độ nghiền thấp là cấu tạo đĩa nghiền phải đƣợc thiết kế để tạo ra nhiều răng nghiền mà vẫn có khả năng chịu tác động thủy lực và chịu phá vỡ răng trong quá trình nghiền [21], [22]. So sánh hai kiểu thiết kế đĩa trên thì dạng đĩa răng thẳng song song (hình 2.4b) cung cấp nhiều răng nghiền sẽ làm tăng chiều dài nghiền (ki-lô- mét/vòng), cho cƣờng độ nghiền thấp còn thiết 48 kế đĩa loại răng toả theo phƣơng bán kính thì răng và rãnh của chúng phải tiếp tục mở rộng dần từ bán kính trong đến bán kính ngoài của đĩa. Nghĩa là đĩa nghiền có dạng răng toả theo phƣơng bánh kính sẽ không cung cấp nhiều răng nghiền giao nhau nhƣ dạng răng thẳng song song. Đĩa có răng thẳng song song có nhiều hoen 86% các răng giao nhau so với dạng răng thẳng toả tròn nên nó cho phép cƣờng độ nghiền thấp để phát triển độ bền của sợi tốt hơn nên mẫu đĩa hình 2.4b là mẫu đĩa tốt hơn so với mẫu đĩa ở hình 2.4a. Từ hai kiểu đĩa trên, một số thiết kế khác đã đƣợc đề xuất gồm trên mặt đĩa có nhiều vùng nghiền, răng có dạng cung tròn, răng nhô ra hoặc thu vào (Hình 2.5) a) b) c) d) Hình 2.5. Một số kiểu đĩa nghiền a. Tạo nhiều vùng nghiền b. Răng hình cung tròn c. Răng nhô ra d. Răng thu vào Hình 2.5a là kiểu đĩa nghiền đƣợc phân thành ba vùng nghiền gồm vùng phân phối, vùng nghiền thô và vùng nghiền mịn. Hình 2.5b là kiểu đĩa nghiền có các răng đƣợc tạo thành các cung tròn ở vùng phân phối và răng thẳng ở phần chu vi đĩa. Hình 2.5c là kiểu đĩa nghiền tƣơng tự hình 2.5b nhƣng phần răng nghiền đƣợc bố trí 49 nhô ra tận chu vi đĩa và hình 2.5a là kiểu đĩa nghiền có vùng phân phối, vùng nghiền răng thẳng, song song nhau và răng nghiền không đƣợc bố trí ra đến chu vi đĩa. Tuy nhiên, với các dạng đĩa nghiền trên thì cách bố trí răng và kích thƣớc hình học răng đĩa nghiền cho chiều dài nghiền khác nhau đáng kể (Hình 2.6). Hình 2.6. Chiều dài nghiền của các mẫu đĩa khác nhau Khi nghiền, năng lƣợng đƣợc chuyển từ động cơ đến đĩa quay, đến các răng và đến sợi. Khi năng lƣợng đƣợc chuyển đến các răng nghiền, đĩa nghiền nào có chiều dài nghiền lớn thì năng lƣợng đƣợc chuyển đến sợi nhiều nhất và do đó sợi đƣợc xử lý nhiều nhất [46]. Trong ba dạng đĩa trên, dạng đĩa răng thẳng và răng song song (hình 2.6c) có cấu tạo đơn giản nhƣng cho chiều dài nghiền lớn nhất (55km/v) do đó nhiều năng lƣợng đƣợc chuyển đến nghiền sợi hơn so với dạng đĩa hình 2.6a (11.5km/v) và hình 2.6b (45 km/v). Mặt khác, từ phần 1.3.1 (chƣơng 1) có thể thấy, khi nghiền mảnh, yêu cầu quan trọng nhất là phá vỡ các mảnh gỗ và tách đƣợc các sợi riêng rẽ. Quá trình này đòi hỏi tác động cơ học với năng lƣợng cao nên tạo ra một lƣợng hơi lớn giữa các đĩa nghiền làm nhiệt độ và áp suất tăng cao. Do đó, đĩa nghiền dùng cho quá trình nghiền mảnh cần đƣợc thiết kế với nhiều vùng nghiền gồm vùng nghiền phá và vùng nghiền mịn. Mảnh gỗ sẽ nhận tác động nghiền đầu tiên tại vùng nghiền phá với các răng nghiền thô và khe hở lớn. Sau đó, nhờ lực ly tâm, chúng đƣợc chuyển đến vùng nghiền mịn với các răng nghiền mau hơn và khe hở nhỏ dần ra đến chu vi đĩa. Tuy nhiên, khi nghiền bột, mục đích chính của quá trình này là thay đổi tính chất của sợi đã đƣợc tách ra từ cấu trúc gỗ để đáp ứng đƣợc yêu cầu của sản phẩm giấy. Quá trình nghiền bột đƣợc thực hiện tại nồng độ thấp, khe hở nhỏ, sự sinh hơi 50 và sinh nhiệt ít hơn so với giai đoạn nghiền mảnh. Vì vậy, đối với quá trình nghiền bột thì việc thiết kế đĩa nghiền với vùng nghiền phá là không cần thiết. Mặt khác, để tăng chiều dài nghiền, để đơn giản trong thiết kế, chế tạo và để thuận lợi trong quá trình vận chuyển bột trong vùng nghiền thì tác giả đề xuất phƣơng án thiết kế đĩa với một loại răng đƣợc phân bố song song và kéo dài trên bề mặt đĩa nghiền. Mỗi dạng đĩa đều có tác động trực tiếp đến chất lƣợng bột nghiền, chế độ động học xảy ra giữa các răng, rãnh nghiền và vấn đề tiêu thụ năng lƣợng nghiền. Vì vậy, chúng cần đƣợc nghiên cứu đầy đủ ứng với từng chế độ nghiền cụ thể. Việc lựa chọn các kích cỡ chiều rộng răng (a), rộng rãnh (b) cũng phụ thuộc lớn vào loại vật liệu nghiền và mục đích nghiền. Khi nghiền bột sợi ngắn hoặc mục đích nghiền là cắt ngắn sợi thì chiều rộng răng nghiền thƣờng hẹp, khi nghiền sợi dài hoặc mục đích nghiền là chổi hóa sợi thì chiều rộng răng nghiền thƣờng lớn hơn [21], [22]. Bột gỗ mềm thƣờng có xơ sợi dài và bền đòi hỏi chiều rộng răng và chiều rộng rãnh nghiền lớn hơn so với sợi bột gỗ cứng thƣờng có xơ sợi ngắn và yếu. Các thông số đĩa nghiền phụ thuộc vào loại vật liệu sợi (bảng 2.1) [46]. Bảng 2.1. Kích thƣớc răng nghiền với các loại xơ sợi Kích thƣớc Xơ sợi gỗ mềm Xơ sợi gỗ cứng Chiều rộng răng nghiền, mm 3.0 - 5.0 1.5 - 3.0 Chiều rộng rãnh nghiền, mm 3.0 - 5.0 1.5 3.0 Chiều cao răng nghiền, mm 5.0 - 7.0 5.0 Mặt khác, tùy theo độ bền của răng, nghiền sợi gỗ cứng đòi hỏi các răng nghiền hẹp hơn so với nghiền sợi gỗ mềm, chiều rộng rãnh nghiền ảnh hƣởng trực tiếp đến tuổi thọ của đĩa, xử lý sợi khi nghiền và sự vận chuyển của bột trong máy nghiền [46]. Nhƣ đã biết từ chƣơng 1, trong quá trình nghiền luôn tồn tại chuyền động xoáy tròn của bột trong rãnh nghiền. Chuyển động xoáy tròn đảm bảo bột giấy đƣợc quay 51 vòng để đƣợc nghiền nhiều lần trƣớc khi rời khỏi máy nghiền [46]. Do vậy, việc thu hẹp khoảng cách giữa các răng cũng có tới hạn do lực cản trong dòng chuyển động của bột giấy quyết định. Lực cản này lại phụ thuộc vào tính chất, thành phần và nồng độ bột giấy. Lực cản bột giấy tăng lên khi nồng độ bột tăng và chiều dài trung bình xơ sợi lớn. Khi nghiền, xơ sợi bột giấy đƣợc xử lý khi các bề mặt răng của đĩa roto và đĩa stato tiếp xúc với nhau. Nhờ áp suất tại đầu ra của máy bột giấy đƣợc đẩy ra khỏi buồng nghiền. Do có sự chênh lệch áp suất giữa đầu ra và đầu vào của máy nghiền nên một phần bột giấy không thoát ra mà ở trong rãnh của đĩa stato và chuyển động về phía tâm của máy nghiền. Vì vậy, luôn có một phần bột nằm trong rãnh chuyển động xoáy tròn (đã trình bày cụ thể trong chƣơng 1). Nếu nhƣ kích thƣớc và chiều sâu rãnh không đủ lớn, dòng huyền phù sẽ không chuyển động tạo vòng xoáy và không tạo đƣợc bó sợi cho quá trình nghiền tiếp theo. Mặt khác, khi chuyển động xoáy, các xơ sợi cọ sát với thành dao, mép răng và các xơ sợi với nhau, nhờ vậy mà xơ sợi đƣợc nghiền. Để dòng bột có thể chuyển động đƣợc trong rãnh nghiền thì kích thƣớc rãnh và chiều sâu của rãnh dao phải phù hợp với điều kiện thủy lực, tức là phụ thuộc vào độ dài xơ sợi và nồng độ bột nghiền. Nếu xơ sợi càng dài thì kích thƣớc rãnh càng lớn [45], [46]. Chiều dài nghiền phụ thuộc vào thông số thiết kế đĩa [46] và đƣợc xác định bằng phƣơng trình 2.15. R2 L n( r ). n ( r ) dr (2.15) sr R1 Số răng nghiền dao nhau tạo bởi một điểm di chuyển dọc theo mép răng nghiền là: 2 rr33 2 cos .bc . 21 Nd 8 (2.16) a b 2 . q 3 Trong đó: + L: Chiều dài nghiền, km/v. + a, b: chiều rộng răng, chiều rộng rãnh nghiền, mm. 52 + ns(r), nr(r): Số lƣợng răng nghiền trên đĩa cố định và đĩa quay. + r1, r2: Bán kính ngoài và bán kính trong của đĩa nghiền. + q: Lƣu lƣợng huyền phù. Biểu thức (2.15) và (2.16) cho thấy, chiều rộng răng, rộng rãnh, chiều cao răng, góc nghiêng răng đều quan hệ chặt chẽ tới kết quả quá trình nghiền. Chiều rộng của răng (a) là yếu tố liên quan mật thiết với số lƣợng răng và số lần cắt qua giữa hai răng nghiền đối diện. Nếu chiều rộng của răng nhỏ thì số lƣợng răng và số lần cắt qua giữa răng dao nghiền đối diện sẽ tăng và do đó sẽ tăng lƣợng xơ sợi nhƣng số xơ sợi bị cắt ngắn lại ít nhất. Chiều rộng của rãnh ảnh hƣởng đến dòng bột giấy chảy trong máy nghiền. Chiều rộng và chiều sâu của rãnh giảm sẽ giúp cho xơ sợi dễ dàng đƣợc tiếp xúc với lƣỡi dao nghiền, thúc đẩy quá trình nghiền nhƣng làm giảm khả năng chứa huyền phù và tốc độ dòng huyền phù bột giấy. Ngƣợc lại, nếu chiều sâu rãnh lớn sẽ làm cho dòng huyền phù đi qua máy nghiền mà không đƣợc nghiền. Góc nghiêng răng ( ) ảnh hƣởng đến số lƣợng và chiều dài răng nghiền cũng nhƣ quá trình vận chuyển bột giữa các đĩa nghiền. Góc dao tăng sẽ làm tăng chiều dài nghiền do đó sẽ tăng cƣờng quá trình nghiền và tăng lƣợng xơ sợi. Mặt khác, giả sử xét trƣờng hợp hai răng nghiền tiếp xúc với nhau khi răng đĩa quay trƣợt và nén lên răng đĩa cố định nhƣ hình 2.7. Hình 2.7. Tiếp xúc giữa hai dao nghiền Nhƣ có thể thấy trên hình 2.7, tại vị trí tiếp xúc, vận tốc v tại một điểm bất kỳ thuộc đĩa quay trong quá trình nghiền đƣợc phân tích thành hai thành phần vt và vg. Trong đó, vg là vận tốc theo phƣơng song song với răng đĩa nghiền cố định. Đây là thành phần chính tạo nên sự cọ xát, nén xơ sợi và một phần tạo nên quá trình cắt xơ 53 sợi. Thành phần vt là vận tốc theo phƣơng tiếp tuyến chủ yếu tạo nên sự trƣợt của răng đĩa quay trên răng đĩa cố định và một phần tạo nên sự nén xơ sợi trong quá trình nghiền. Từ đó có thể thấy rằng, công suất nghiền hữu ích là công suất để thực hiện quá trình phân tơ, chổi hóa xơ sợi và một phần để thực hiện quá trình cắt ngắn xơ sợi, phục vụ cho quá trình tạo hình tờ giấy sau này. Tuy nhiên, để thuận lợi trong quá trình nghiên cứu, ta gọi vt là thành phần tạo ra công suất thực hiện quá trình chuyển động có ích chủ yếu tạo ra sự cắt sợi và vg là thành phần tạo ra công suất nén xơ sợi có ích chủ yếu tạo ra sự phân tơ sợi. Việc xác định các thành phần này đƣợc thực hiện nhƣ sau: Giả sử, xét trƣờng hợp khi răng đĩa nghiền quay cắt qua răng đĩa nghiền cố định khi chuyển động từ vị trí A đến vị trí B trong khoảng thời gian từ t đến t +dt với OA là cung tròn bán kính , OB là cung tròn bán kính +d và d đƣợc xác định bởi đọan AC. Đoạn AB và AD đƣợc xác định bởi các góc r và s tạo bởi phƣơng của răng đĩa nghiền quay và phƣơng của răng đĩa nghiền cố định với tia OC (Hình 2.8). Hình 2.8. Sự dịch chuyển của răng đĩa nghiền quay trên răng đĩa nghiền cố định trong quá trình nghiền Xét các tam giác vuông ACB và tam giác ACD, dễ dàng thu đƣợc vận tốc tạo ra sự cắt sợi và phân tơ sợi khi nghiền nhƣ sau: 54 2 2 2 0 sin vg ; với rs 0 (2.17) sin rs 0 sin cos rs arcsin vt ; với rs 0 (2.18) sin rs Nhận xét: Từ hai phƣơng trình 2.17 và 2.18 có thể nhận thấy, đĩa nghiền quay và đĩa nghiền cố định không thể bố trí có phƣơng trùng khít lên nhau. Mặt khác, trong giai đoạn nghiền sơ bộ, cần ƣu tiên quá trình cắt ngắn xơ sợi hơn quá trình phân tơ, chổi hóa sợi, vì vậy cần tăng giá trị vận tốc theo phƣơng tiếp tuyến vt và ngƣợc lại trong giai đoạn nghiền tinh, cần ƣu tiên quá trình phân tơ, chổi hóa xơ sợi hơn quá trình cắt ngắn xơ sợi, vì vậy cần tăng giá trị vận tốc theo phƣơng của răng đĩa nghiền cố định vg. Xét ở giai đoạn nghiền tinh, chủ yếu yêu cầu phân tơ sợi nên cần tăng vg. Khi tăng vg, cần xem xét đến thành phần góc nghiêng của răng nghiền ( ) và góc giao nhau giữa răng đĩa nghiền quay và đĩa nghiền cố định ( rs). Để vg tăng có thể thực hiện bằng cách giảm sin và sin rs. Điều này đồng nghĩa với việc giảm giá trị góc rs (với điều kiện rs 0) . Mặt khác, theo phƣơng trình (2.16), số các răng nghiền giao nhau tại một điểm dịch chuyển dọc theo răng đĩa cố định (Nd ) tăng khi giá trị góc nghiêng răng nghiền ( ) nhỏ. Tuy nhiên, khi quá nhỏ thì quá trình dịch chuyển của dòng sợi bột giấy trong đĩa nghiền khó khăn và chiều dài nghiền giảm. Hiện tƣợng này làm giảm số sợi bột giấy đƣợc đi qua máy nghiền và giảm cơ hội sợi bột giấy đƣợc tiếp xúc với răng đĩa nghiền để đƣợc nghiền. Do đó, đây có thể là một nguyên nhân làm giảm năng suất nghiền và chất lƣợng bột nghiền. Từ những phân tích trên đây có thể thấy rằng, góc nghiêng răng nghiền là một thông số quan trọng cần đƣợc quan tâm đầy đủ, cẩn thận để phù hợp với đặc thù nguyên liệu của Việt Nam. Việc xác định đƣợc thông số phù hợp là một công việc 55 quan trọng nhằm nâng cao hiệu quả nghiền bột giấy cho các cơ sở sản xuất giấy trong nƣớc hiện nay. Tóm lại, các nghiên cứu lý thuyết nêu trên đã cho thấy, các thông số kết cấu có ảnh hƣởng trực tiếp đến chất lƣợng bột giấy thành phẩm. Nhận xét này càng củng cố cơ sở cho giả thuyết khoa học của đề tài: Thông số kết cấu của đĩa nghiền và chế độ vận hành có quan hệ mật thiết với chất lƣợng bột giấy và năng lƣợng tiêu thụ cho quá trình nghiền. Nghiên cứu thực nghiệm là một cách thức hiệu quả và có ý nghĩa ứng dụng cao để kiểm chứng giả thuyết khoa học. Phần tiếp theo sẽ trình bày cơ sở để xây dựng mô hình thực nghiệm cho nghiên cứu. 2.5. Cơ sở xây dựng mô hình thực nghiệm 2.5.1. Lý thuyết mô hình, đồng dạng và phép phân tích thứ nguyên 2.5.1.1. Lý thuyết mô hình Mô hình là một biểu diễn một hệ thống kỹ thuật thông qua hoặc các khái niệm, hoặc các phƣơng trình toán học, hoặc bằng vật thể thực. Tƣơng ứng với mỗi cách biểu diễn đó, sẽ có các dạng: mô hình khái niệm, mô hình toán, hoặc mô hình vật lý. Mô hình đƣợc sử dụng để tái tạo một thiết bị, hệ thống thực nhƣng hoặc đơn giản hơn, hoặc nhỏ gọn hơn. Hơn nữa, sử dụng mô hình cho phép thiết lập các điều kiện thử nghiệm mà nhiều khi không có sẵn trong thực tế. Nói cách khác, mô hình là một công cụ hữu hiệu cho phép thử nghiệm ứng xử của một đối tƣợng, một hệ thống kỹ thuật trong điều kiện làm việc có thể điều khiển đƣợc theo ý ngƣời thử nghiệm. Nghiên cứu trên mô hình là một trong những phƣơng pháp nghiên cứu thực nghiệm hiện đại dùng để nghiên cứu các hiện tƣợng phức tạp. Trong nghiên cứu kỹ thuật, thƣờng sử dụng mô hình toán học hoặc mô hình vật lý. Mô hình toán học là một hệ thống các phƣơng trình toán học mô tả quan hệ tƣơng tác trong hệ thống. Mô hình vật lý bao gồm các đối tƣợng vật lý thực, có kích thƣớc thu nhỏ hoặc giữ nguyên so với đối tƣợng, hệ thống thực cần nghiên cứu. Vấn đề cần quan tâm khi xây dựng mô hình nghiên cứu là, cần xác định các hệ số tỷ lệ giữa các giá trị của đại lƣợng đặc trƣng trong hệ thống thực với các giá trị đó của mô hình thực nghiệm. Lý thuyết đồng dạng (similarity theory hoặc similitude 56 theory) có thể đƣợc sử dụng để xác định các hệ số tỷ lệ khi xây dựng mô hình thực nghiệm và quan trọng hơn, để chuyển đổi các thông số thu đƣợc từ kết quả nghiên cứu trên mô hình sang các hệ thống thực. 2.5.1.2. Lý thuyết đồng dạng a. Giới thiệu Lý thuyết đồng dạng là học thuyết về phƣơng pháp nghiên cứu các hiện tƣợng, đối tƣợng vật lý thông qua các phép phân tích về tính đồng dạng, tỷ lệ đồng dạng giữa chúng. Quan hệ về kích thƣớc, hình học giữa mô hình thực nghiệm và hệ thống thực thƣờng đƣợc xác định một cách dễ dàng thông qua hệ số tỷ lệ. Tuy nhiên, việc xác định các thông số thử nghiệm về điều kiện làm việc thì không đơn giản nhƣ vậy. Các thông số về nhiệt độ, áp suất, vận tốc, tính chất dòng chảy... phải đƣợc xác định một cách độc lập và khoa học. Lý thuyết đồng dạng chỉ ra rằng, các điều kiện để đảm bảo hai hệ (ở đây là hệ thống thực và mô hình thực nghiệm) đƣợc coi là đồng dạng khi: - Đồng dạng hình học (Geometric similarity): Hai hệ có cùng hình dáng hình học, có kích thƣớc theo tỷ lệ. - Đồng dạng động học (Kinematic similarity): Dòng chảy của chất lỏng trong cả hai hệ phải tƣơng tự nhau về tốc độ và hƣớng dòng chảy. - Đồng dạng động lực học (Dynamic similarity): Tỷ lệ giữa các thành phần lực tác động lên các phần tử của chất lỏng trong hai hệ là nhƣ nhau. Để thoả mãn các điều kiện đồng dạng nói trên, các yêu cầu cơ bản cần thoả mãn là: - Các tham số mô tả hệ thống phải đƣợc định danh thông qua việc sử dụng các nguyên tắc của cơ học môi trƣờng liên tục. - Cần sử dụng phép phân tích thứ nguyên (Dimensional analysis) để loại bỏ tối đa số biến phụ thuộc, đồng thời sử dụng tối đa các tham số không thứ nguyên. 57 - Giá trị của các tham số không thứ nguyên là nhƣ nhau trong cả hai hệ. Điều này đảm bảo điều kiện đồng dạng động lực học giữa hai hệ. Một số khái niệm của lý thuyết đồng dạng đƣợc tóm tắt nhƣ dƣới đây. Hệ số đồng dạng của một đại lƣợng nào đó là tỷ lệ giữa giá trị đo đại lƣợng đó trên hệ thống thực với giá trị đại lƣợng đó trên mô hình. Hệ số đồng dạng là cơ sở để xác định các thông số kết cấu của mô hình dựa trên cơ sở hệ thống thực. Nó cũng đƣợc dùng để chuyển đổi kết quả nghiên cứu trên mô hình sang dãy máy thực. Chuẩn số đồng dạng (Pk) là tỷ số giữa một đại lƣợng (Ak) với một hay một tập hợp các đại lƣợng khác (A’k) của các hiện tƣợng xảy ra: Pk = Ak/A’k. Để đảm bảo yêu cầu đồng dạng, các chuẩn số đồng dạng của mô hình (PkM) và của hệ thống thực (PkV) phải bằng nhau (PkM = PkV). Chuẩn số đồng dạng thể hiện bản chất lý thuyết đồng dạng và chúng đƣợc biểu diễn bằng chuẩn số đồng dạng thông số (mô tả quan hệ không thứ nguyên các thông số kích thƣớc); chuẩn số đồng dạng giải tích (tập hợp những quan hệ không thứ nguyên của các đại lƣợng vật lý nhƣ chuẩn số đồng dạng Niu tơn - Ne, chuẩn số Râynôn - Re, chuẩn số Frut - Fr, chuẩn số Galilê - Ga). Chuẩn số đồng dạng xác lập mối quan hệ giữa các đại lƣợng của đối tƣợng nghiên cứu. Phụ thuộc vào cách đặt vấn đề nghiên cứu, dạng thông tin đầu vào, số lƣợng và dạng các chuẩn số có thể khác nhau. Qua tính toán ta có thể tìm đƣợc các chuẩn số dẫn xuất phù hợp với đối tƣợng nghiên cứu với đầy đủ tính chất vật lý. Về nguyên tắc, các chuẩn số đồng dạng là các đại lƣợng không thứ nguyên. Với ý nghĩa đó, tất cả các đại lƣợng vật lý (chẳng hạn: góc, hệ số ma sát, hiệu suất...) đƣợc coi nhƣ bất biến của đồng dạng, tức là bảo toàn về mặt hiện tƣợng trong phép biến đổi đồng dạng. Trong nhiều trƣờng hợp, các đại lƣợng thứ nguyên riêng rẽ cần đảm bảo nhƣ nhau, nghĩa là có hệ số đồng dạng bằng nhau, tức là: x0 xc 1 (2.19) xM Trong đó: xc: Hệ số đồng dạng; x0: Vật thực; xM: Mô hình 58 Theo lý thuyết đồng dạng vật lý, đồng dạng giữa đối tƣợng và mô hình có cùng hiện tƣợng vật lý, các loại đồng dạng thƣờng đƣợc sử dụng gồm đồng dạng hình học, đồng dạng tĩnh học, đồng dạng động học và đồng dạng động lực học. Đồng dạng động lực học là loại đồng dạng cơ bản khi vận dụng nghiên cứu về máy nghiền và đĩa nghiền bột giấy. b. Định lý đồng dạng - Định lý đồng dạng thứ nhất: Định lý này đƣợc phát biểu nhƣ sau: Nếu hai hệ đồng dạng với nhau thì chúng có chung chuẩn số đồng dạng. Một cách phát biểu khác của định lý thứ nhất là: Các hiện tƣợng đồng dạng có chỉ số đồng dạng là bằng nhau và bằng đơn vị. - Địn
File đính kèm:
luan_an_nghien_cuu_nang_cao_hieu_qua_nghien_bot_giay_khi_dun.pdf
Thong tin LA NCS Truong Thi Thu Huong 07-2014.doc
Tom tat Tieng Anh NCS Truong Thi Thu Huong 07-2014.pdf
Tom_tat Tieng VIet NCS Truong_Thi_Thu_Huong 07-2014.pdf