Luận án Nghiên cứu xác định các tham số nhiệt động lực học của động cơ tua bin phản lực trên cơ sở các kích thước hình học
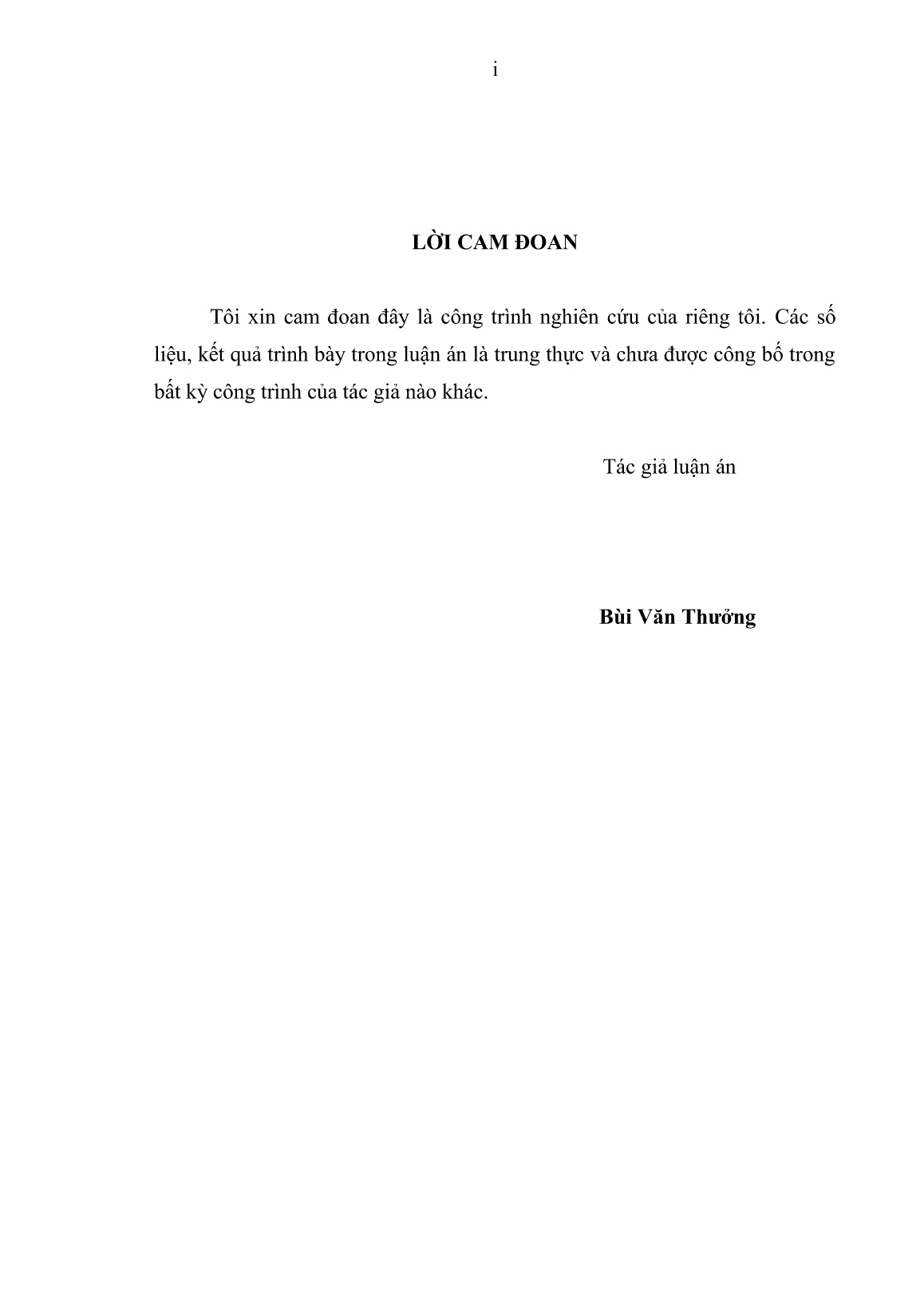
Trang 1
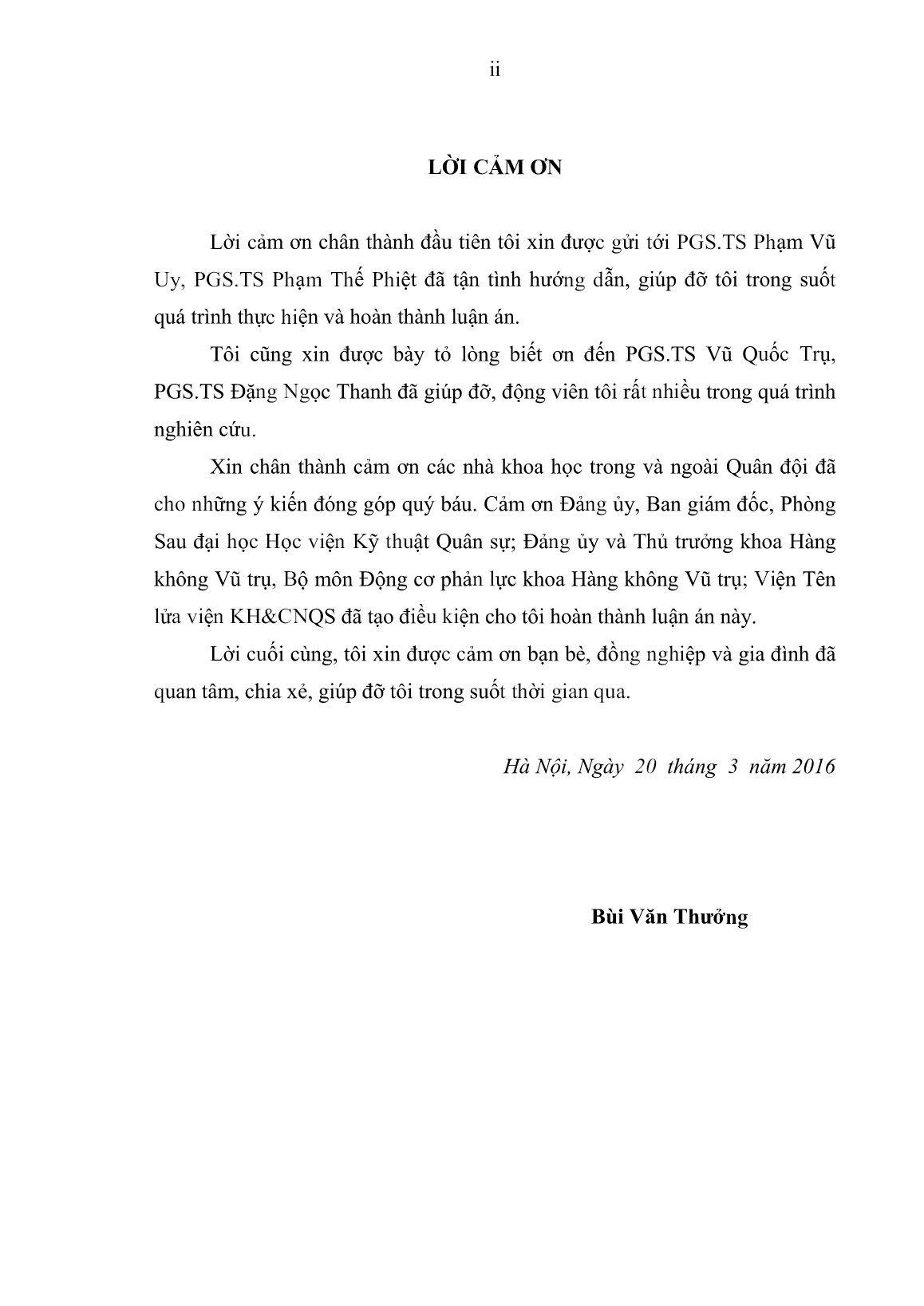
Trang 2
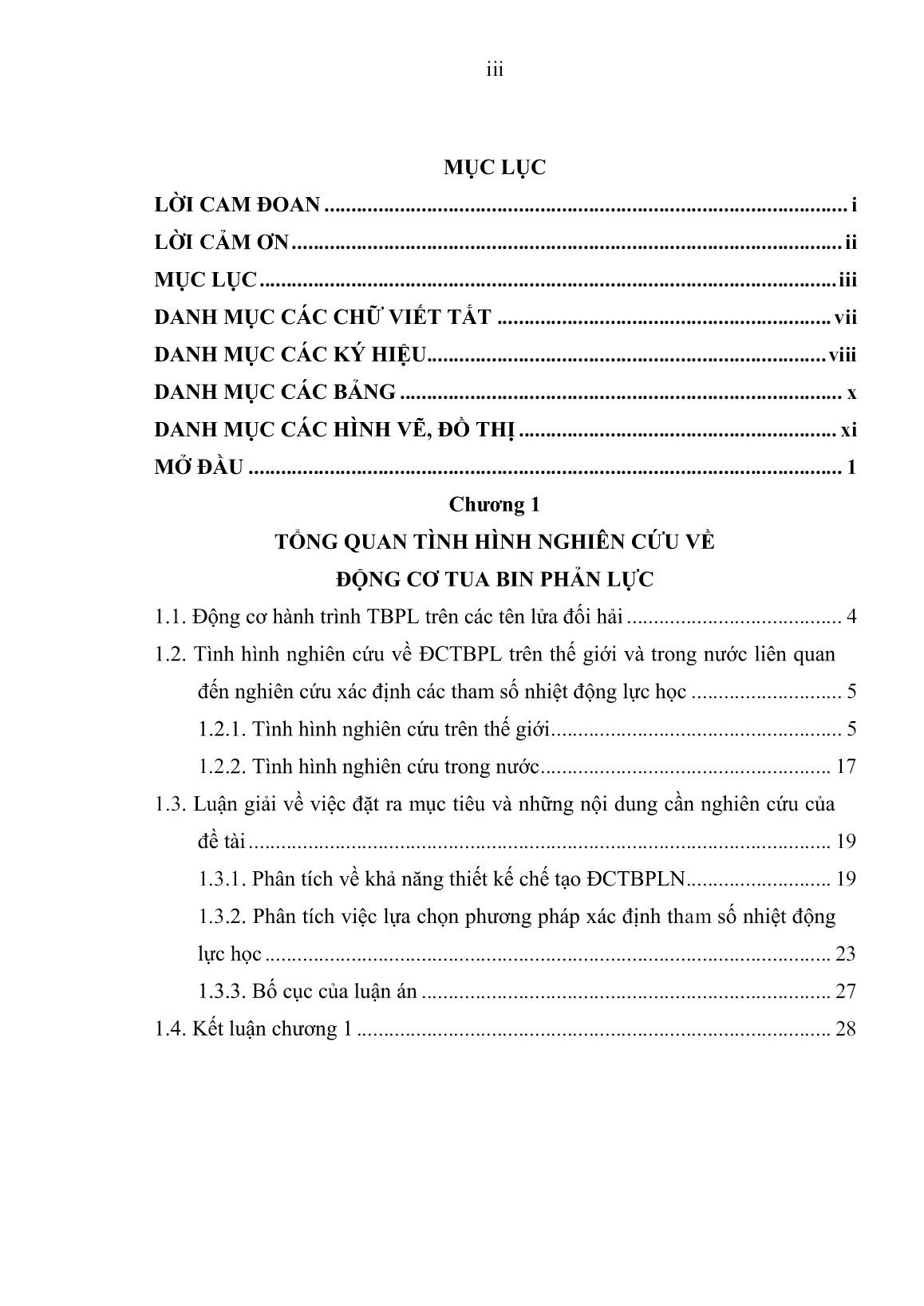
Trang 3
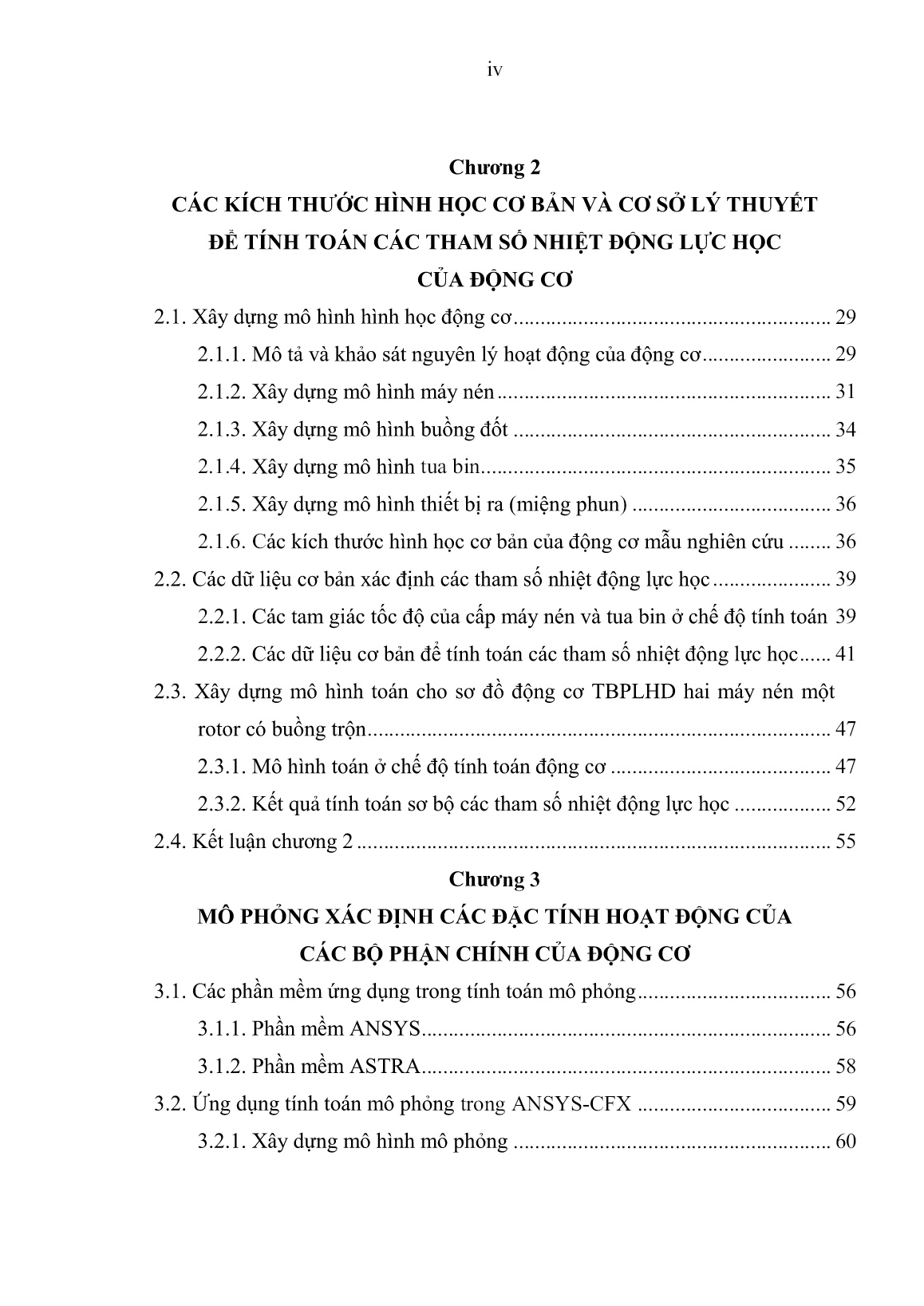
Trang 4
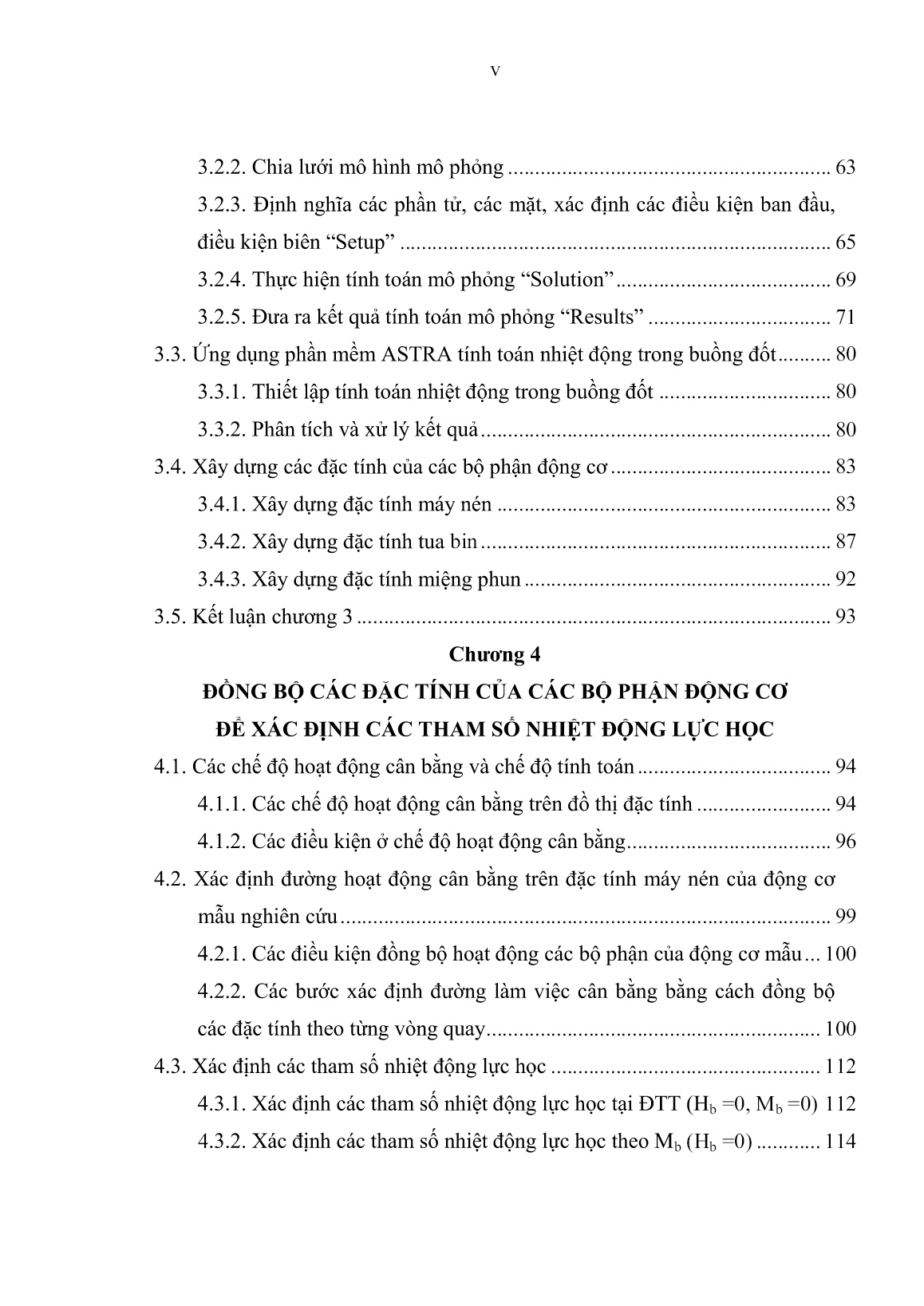
Trang 5
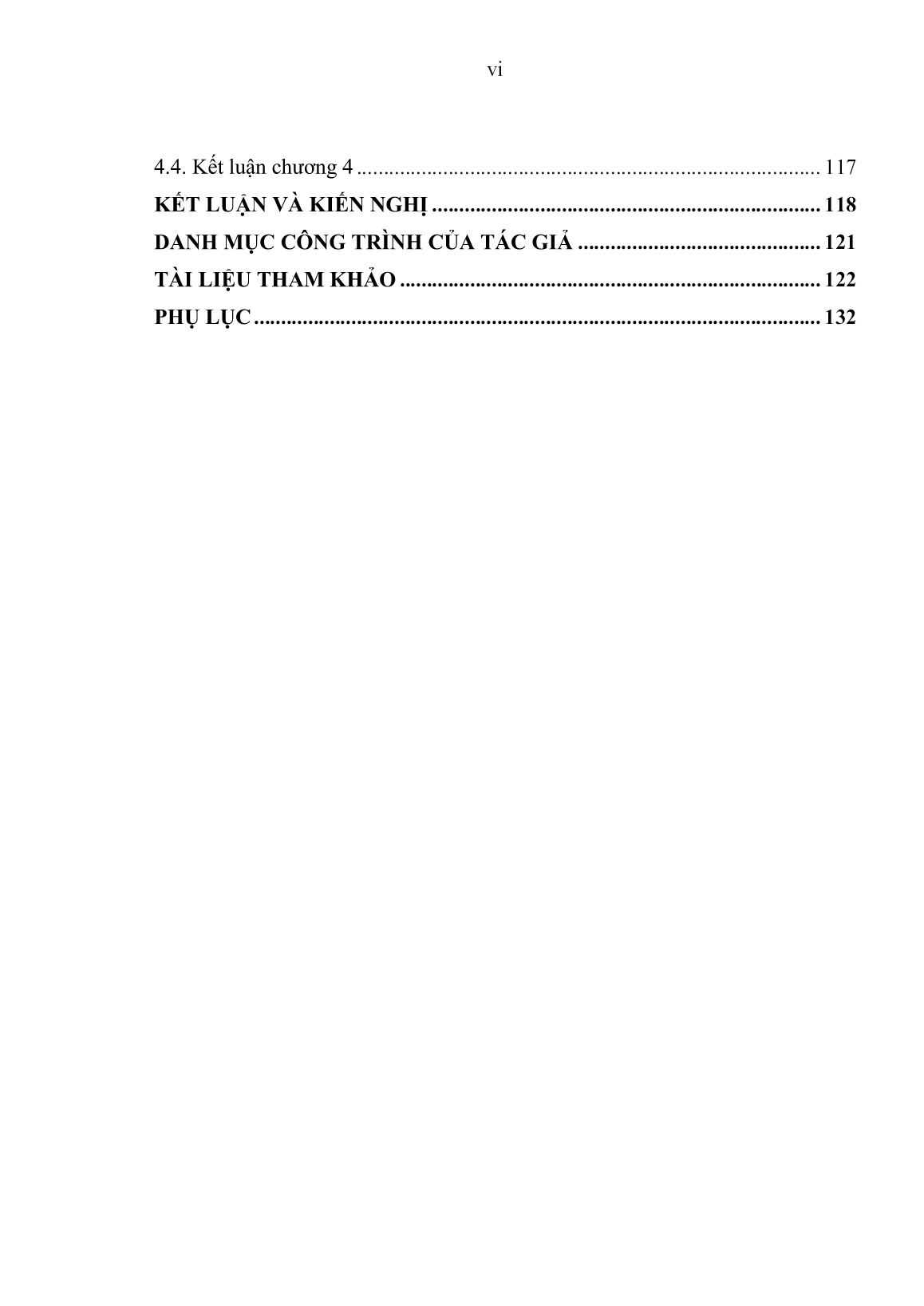
Trang 6
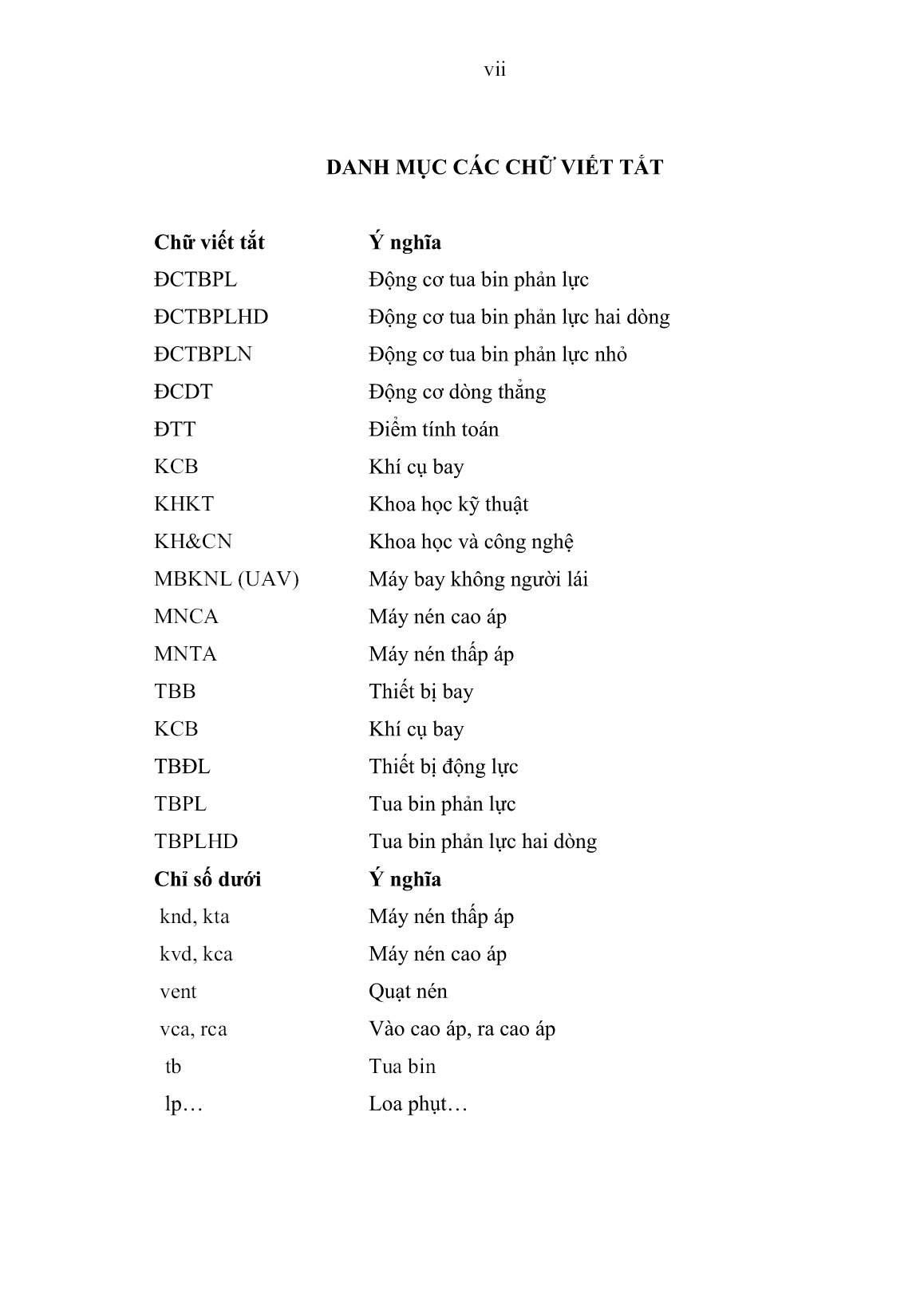
Trang 7
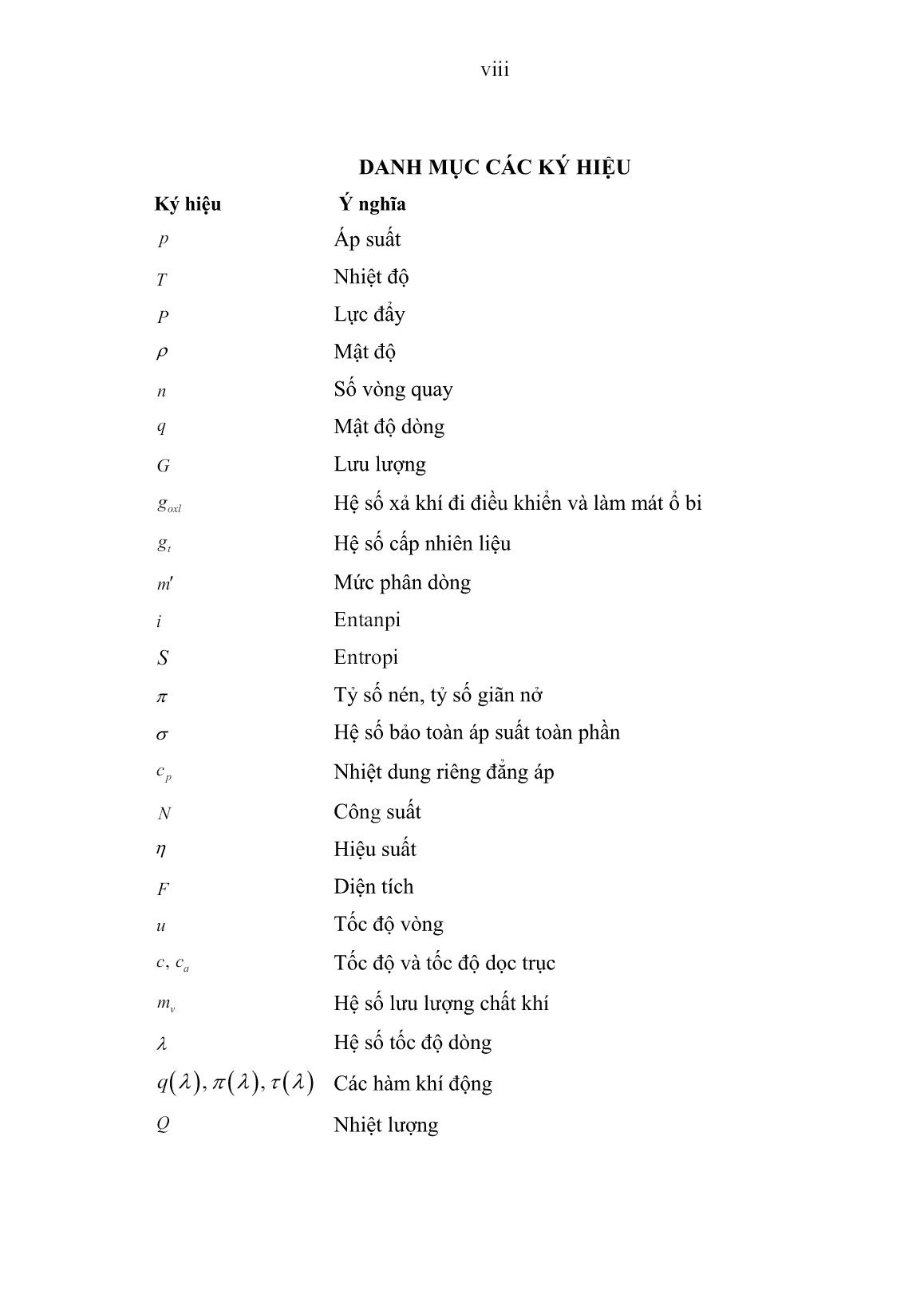
Trang 8
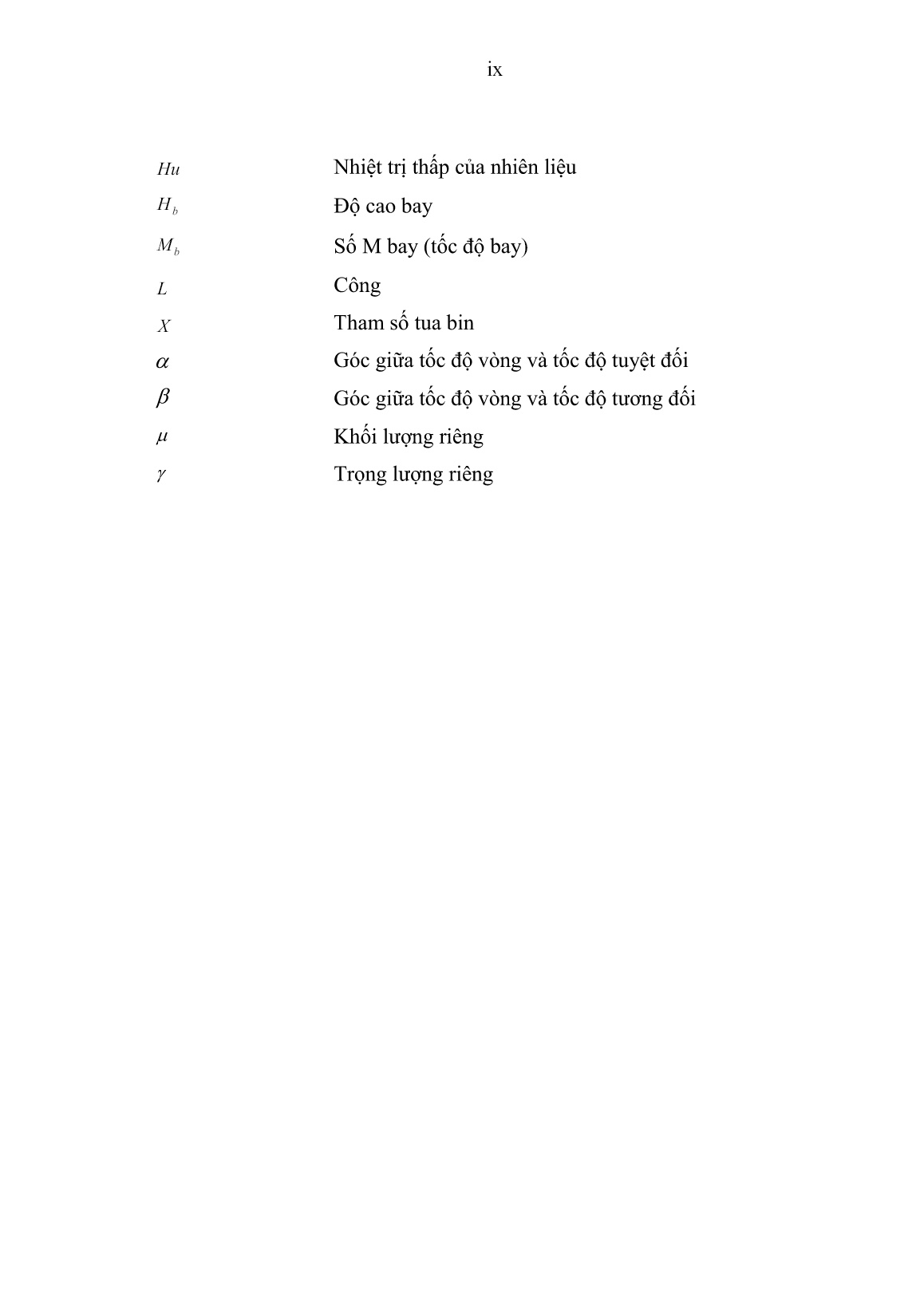
Trang 9
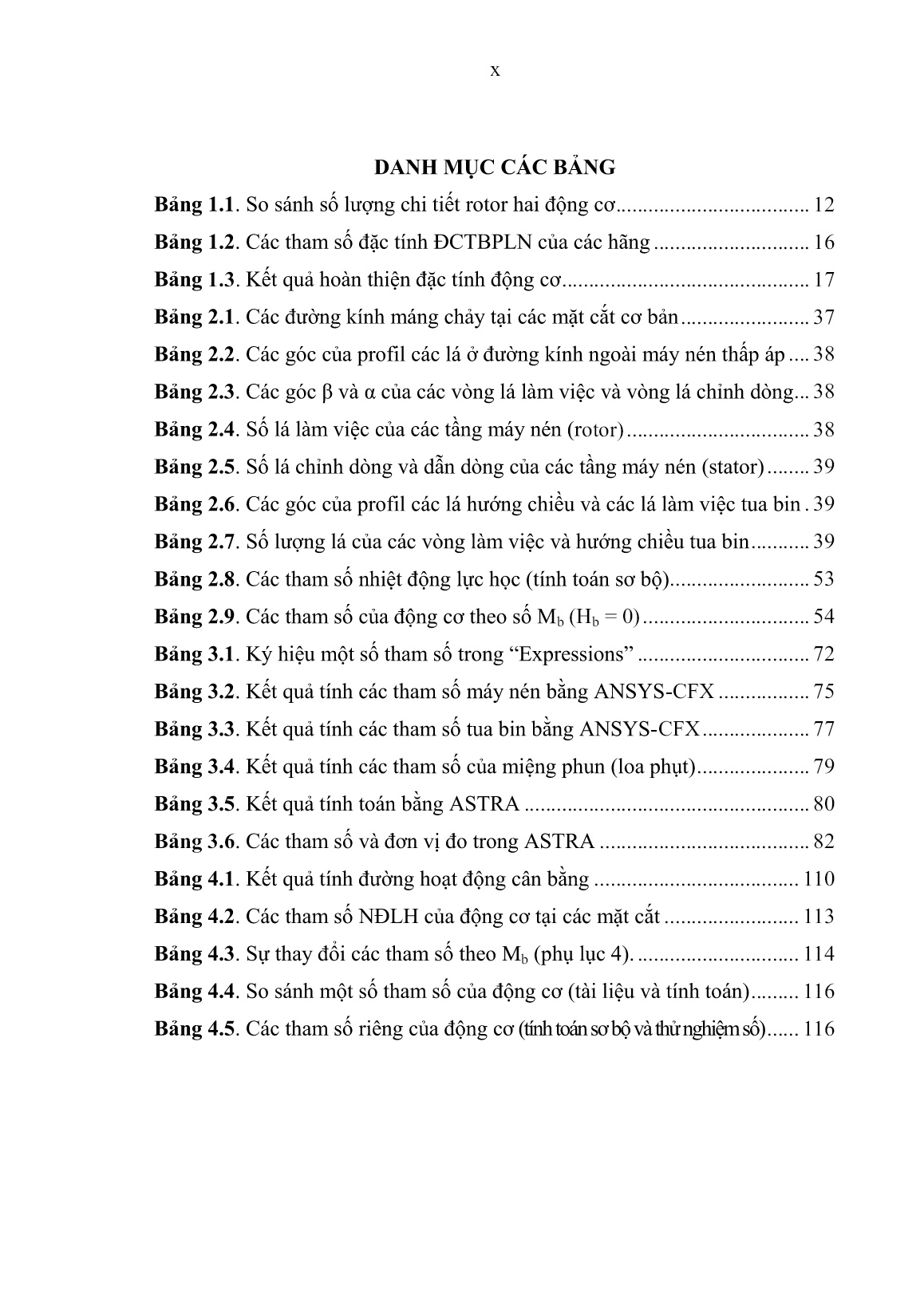
Trang 10
Tải về để xem bản đầy đủ
Bạn đang xem 10 trang mẫu của tài liệu "Luận án Nghiên cứu xác định các tham số nhiệt động lực học của động cơ tua bin phản lực trên cơ sở các kích thước hình học", để tải tài liệu gốc về máy hãy click vào nút Download ở trên.
Tóm tắt nội dung tài liệu: Luận án Nghiên cứu xác định các tham số nhiệt động lực học của động cơ tua bin phản lực trên cơ sở các kích thước hình học
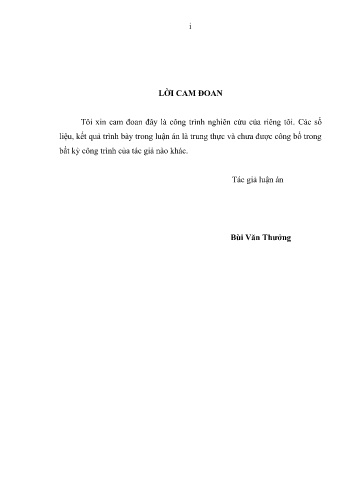
II Căn cứ các tham số dòng khí qua tua bin của dòng trong và dòng ngoài ta xác định được các tham số ở buồng trộn (trước loa phụt): 51 Tzvcm T zventII,. p zvcm p zventII II (2.23) 1 m 1 m pzcm cm.., p zt p zvcm . (2.24) m ... Cpv T zventII C pg T zt Tzcm 1. mC pcm Xác định các tham số tốc độ, nhiệt độ, áp suất tại tiết diện tới hạn và tiết diện loa phụt: Trường hợp giãn nở hoàn toàn ppch : kcm -1 kp kcm C f. 2.cm R T . 1- h (2.25) c1 c cm zcm kpcm-1 zcm . cp Trường hợp giãn nở không hoàn toàn ppch ta tính tốc độ tại tiết diện tới hạn: kcm -1 k 1 kcm C f. 2.cm R T . 1- (2.26) c2 c cm zcm kcm-1 ckp Đối với sơ đồ động cơ mẫu tại tiết diện tới hạn Fkp dòng khí giãn nở chưa hoàn toàn (chủ yếu ở chế độ nmax), nhưng phía sau vẫn còn tiếp tục giãn nở nhờ vật trung tâm là bề mặt ngoài của khối sinh khí nên dòng khí ra khỏi loa phụt giãn nở hoàn toàn được tính theo vận tốc tương đương Cc : 2 pp- C pzcm. cp C C T.,-,ch2 T Tc p . (2.27) c c22 c c zcmk c mcm.. q c2 p cscm c 2. .Rcm kcm -1 p . C 2 Trong đó: p zcm cp , T T c2 ; c22 c zcm k ckp cm 2. .Rcm kcm 1 52 11 C k 11 kkcm 11 k cm c2 ,q cm . 1 cm . 2 ; c2 c 2 c 2 c 2 kcm kkcm cm 1 2. .RTcm . c2 kcm 1 kcm kcm 1 kpcm 1 2 c2 pzcm. cp c22 1 . c ,p cs , c . kpcm 1 c2 h Như vậy, khi thoát khỏi động cơ dòng sản phẩm cháy giãn nở hoàn toàn. Xác định các tham số riêng của động cơ: ggt. 1- oxl ggt. 1- oxl PCVud 1 . c - b , Cud (2.28) 1 m Pmud .1 ggt. 1- oxl 22 1 .CVcb - 1 m L (2.29) e 2 2 Pmud .1 Vb Vb e , v P ud . , 0 Pud (2.30) 2.gt . Hu . 1- g oxl Le ggt 1- oxl Hu 1 m mMdc dc dc , dc . (2.31) GPv Hệ thống các công thức trên là mô hình toán để xác định sơ bộ các tham số nhiệt động lực học cho động cơ có sơ đồ TBPLHD, hai máy nén, một rotor và có buồng trộn (sơ đồ động cơ mẫu nghiên cứu). 2.3.2. Kết quả tính toán sơ bộ các tham số nhiệt động lực học Áp dụng tính toán sơ bộ các tham số nhiệt động lực học cho động cơ mẫu nghiên cứu ở chế độ tính toán (phụ lục 2.2) nhận được các kết quả trong bảng 2.8. 53 Bảng 2.8. Các tham số nhiệt động lực học (tính toán sơ bộ) Mặt cắt Tốc độ dọc trục Nhiệt độ [K] Áp suất [Pa] chính m/s H 288,0 101325,0 196,5 V 288,0 99298,5 196,5 Vent 367,7 214394,4 158,0 VCA 367,7 214394,4 169,3 K 616,1 1056814,8 134,5 G 1180,4 1025110,4 209,9 T 831,6 210648,4 153,3 CM 635,1 197672,9 153,3 C 543,2 101325,0 447,3 H’ 543,2 101325,0 447,3 Hình 2.13. Sự biến đổi các tham số nhiệt động lực học (tính toán sơ bộ) Tính toán sơ bộ các tham số riêng và lực đẩy của động cơ: g.(1 g ) N . s PCV 1 t oxl . 451.12 ; ud c b 1 m kg PPGN ud. v 3418.78 ; gt.(1 g oxl ) kg kg Cud 0.683 0.0683 ; Pud .(1 m ) DaN . hr N . hr 54 2 Pmud .(1 ) Mdc kg e 0.277 ; dc 12.539 ; 2.gt . Hu .(1 g oxl ) Gv kg/ s M kg dc 0.0278 . dc PN Bảng 2.9. Các tham số của động cơ theo số Mb (Hb = 0) Cud Pud Số M P [N] Gv [kg/s] [kg/N.h] [N.s/kg] 0 3418,78 0,068 451,17 7,576 0,2 2997,52 0,080 383,10 7,759 0,4 2775,25 0,098 315,03 8,327 0,6 2699,86 0,125 246,96 9,333 0,8 2751,47 0,172 178,89 10,874 0,85 2783,13 0,190 161,87 11,358 1 2922,90 0,278 110,82 13,092 Hình 2.14. Sự biến đổi các tham số của động cơ theo Mb Từ kết quả tính toán sơ bộ so sánh với một số tham số của động cơ trong các tài liệu khai thác nhận thấy vẫn nằm trong dải giá trị cho phép, ví dụ lực 55 đẩy động cơ trong khoảng 2750 N đến 3400 N, ở đây chưa xét đến việc tự động điều chỉnh lượng nhiên liệu vào động cơ khi thay đổi tốc độ và độ cao bay; áp suất sau máy nén khoảng 10 at phù hợp với tham số khí trích đi điều khiển cánh lái, tiêu hao nhiên liệu riêng Cud > 0.122 kg/N.h (Mb = 0.8), hay tốc độ vòng quay máy phát điện trong khoảng 80- 100%... 2.4. Kết luận chƣơng 2 1. Tiếp thu kết quả nghiên cứu đã được công bố về khai thác động cơ hành trình [12], đã chọn ra đủ số lượng các kích thước để tính toán theo phương pháp kinh điển và hệ thống hóa được các số liệu kích thước hình học cơ bản, quan trọng nhất làm cơ sở cho những nghiên cứu sâu hơn về nhiệt động lực học của đối tượng nghiên cứu – cũng là cơ sở tính toán thiết kế ngược theo mẫu. 2. Đã thiết lập cơ sở lý thuyết xác định các điều kiện làm việc phối hợp của các thành phần động cơ TBPL theo dạng mẫu nghiên cứu. Xác định các mối quan hệ của các tham số nhiệt động lực học và các tham số hình học làm cơ sở cho việc tính toán xác định các tham số nhiệt động lực học cho dạng sơ đồ động cơ TBPL hai dòng, hai máy nén, một rotor. 3. Bằng phương pháp truyền thống, kết hợp với đề xuất cách tính lặp đã tính toán xác định sơ bộ được các tham số nhiệt động lực học của đối tượng nghiên cứu chủ yếu dựa trên các kích thước hình học (lực đẩy sai lệch hơn 7 %), các tham số riêng hoàn toàn phù hợp với các tham số của các động cơ hiện đại (hình 1.1, bảng 1.2, phụ lục 1). 4. Sau khi so sánh sơ bộ một số số liệu liên quan đã có thể khẳng định rằng các số liệu thu được nằm trong khoảng các số liệu thống kê cho các loại động cơ này nên có thể được sử dụng như những định hướng ban đầu cho những nghiên cứu tính toán tiếp theo. 56 Chƣơng 3 MÔ PHỎNG XÁC ĐỊNH CÁC ĐẶC TÍNH HOẠT ĐỘNG CỦA CÁC BỘ PHẬN CHÍNH CỦA ĐỘNG CƠ Từ phân tích trong phần tổng quan đã nêu rõ, với sự phát triển mạnh của kỹ thuật tính toán số, hiện đã tồn tại nhiều phần mềm chuyên dụng có thể giúp chúng ta nghiên cứu các đặc điểm hoạt động của các bộ phận của động cơ mẫu nghiên cứu (có kích thước hình học đã xác định) trong môi trường thử nghiệm mô phỏng số. Cũng trong phân tích tình hình nghiên cứu hiện nay, chúng ta đã có trong tay hai công cụ mạnh là phần mềm ANSYS và ASTRA. Trong chương thứ 3 này sẽ tập trung vào việc ứng dụng các phần mềm chuyên dụng đó để xác định các đặc tính hoạt động của các bộ phận của đối tượng động cơ cần nghiên cứu. Vì như đã biết, đặc tính hoạt động của các bộ phận sẽ tạo cơ sở để nghiên cứu hoạt động chung của toàn bộ động cơ. 3.1. Các phần mềm ứng dụng trong tính toán mô phỏng 3.1.1. Phần mềm ANSYS ANSYS là một phần mềm mạnh được phát triển và ứng dụng rộng rãi trên thế giới [13], [16], sử dụng để giải các bài toán cơ học vật rắn, cơ học thủy khí, các bài toán về điện-từ trường, các bài toán về nhiệt và đặc biệt là các bài toán về các máy cánh (máy nén, cánh quạt, tua bin) bằng các mô đun ANSYS-CFX, ANSYS-TurboGrid. ANSYS là phần mềm giải các bài toán bằng phương pháp thể tích hữu hạn để phân tích các bài toán về cơ, nhiệt, thủy khí, điện từ; chuyển các phương trình vi phân, phương trình đạo hàm riêng từ dạng giải tích về dạng số trên mô hình hình học thực với các kích thước thực, các mô hình đưa vào tính toán càng chuẩn như vật thật thì độ chính xác tính toán càng cao. 57 Bản chất của phần mềm ANSYS là giải hệ phương trình Navier- Stokes, mô tả chuyển động của dòng chảy trong động cơ [13], [35], [36], sử dụng các phương trình: + Phương trình bảo toàn khối lượng ( Phương trình liên tục) div v 0 (3.1) t Trong đó: ρ: Khối lượng riêng. v: Vận tốc dòng chất lưu. + Phương trình bảo toàn động lượng u p 2 x e div u V div gradu . fx t x3 x v p 2 y e div v V div gradv . f y (3.2) t y3 y w p 2 z e div w V div gradw . fz t z3 z Trong đó: u, v, w: là thành phần vận tốc theo phương x, y, z. p: áp suất, µ: hệ số nhớt động lực học, τ: ten xơ ứng suất, f: ngoại lực khối. + Phương trình bảo toàn năng lượng E div E V pdiv V div k. gradT div V Wfh q t (3.3) trong đó: E: năng lượng toàn phần, k: hệ số dẫn nhiệt, T: nhiệt độ, Wf: công của ngoại lực thể tích, qh: thông lượng nhiệt tác dụng lên chất lưu. 58 Các phương trình trên kết hợp thành hệ phương trình Navier- Stokes mô tả chuyển động của dòng lưu chất chảy qua động cơ. Giải quyết hệ phương trình này ta sẽ biết được trạng thái của dòng lưu chất chảy qua các phần của động cơ và các giá trị nghiệm của chúng. Để giải hệ phương trình Navier- Stokes cần thêm các phương trình: + Phương trình trạng thái: p RT (3.4) Trong đó: ρ là mật độ, T là nhiệt độ, R là hằng số chất khí. 1 + Biểu thức Newton: 21 S (3.5) 3 Trong đó: - ten xơ ứng suất nhớt, S - ten xơ tỉ suất biến dạng, 1 Ten xơ đơn vị. + Định luật Fourier: q k T (3.6) C Trong đó: k - hệ số dẫn nhiệt, k p với Pr là hằng số Prandtl, Pr q - Thông lượng nhiệt. 3.1.2. Phần mềm ASTRA ASTRA là phần mềm tính toán nhiệt động lực học dựa trên mô hình cân bằng pha và hóa học ở nhiệt độ cao, được ứng dụng trong các trường đại học khoa học kỹ thuật của Liên bang Nga [23]. ASTRA được viết trên ngôn ngữ lập trình FORTRAN 4.0, là phần mềm tính toán xác định các tham số của sản phẩm cháy ở mặt cắt cuối của buồng đốt dựa trên nguyên lý entropi cực đại của hệ nhiệt động trong buồng đốt. Nếu sau quá trình cháy diễn ra quá trình chảy thì các tham số cuối của quá 59 trình cháy sẽ là tham số đầu của quá trình chảy. Tính toán quá trình chảy là xác định các tham số ở từng mặt cắt khác nhau của luồng chảy. Quá trình thực tế của sự chảy rất gần với mô hình sự chảy cân bằng vì thế mô hình chảy cân bằng được sử dụng rộng rãi trong tính toán mô phỏng. Để xây dựng thuật toán của mô hình thì ở mỗi ―điểm‖ kết thúc của mỗi quá trình cần biết hai thông số trạng thái nhiệt động. Vì vậy, đối với mô hình cháy khi áp suất không đổi (trong buồng đốt của động cơ) thì cần cho trước hai tham số nhiệt động và thường là áp suất và entanpi của nhiên liệu (p = const, I = const), kết quả là các tham số nhiệt động lực học và thành phần lý hóa của sản phẩm cháy. 3.2. Ứng dụng tính toán mô phỏng trong ANSYS-CFX Việc xây dựng mô hình trong ANSYS-CFX thông qua môđun BladeGen thực sự rất khó để áp dụng cho đối tượng máy nén và tua bin nhiều cấp, môđun BladeGen chỉ cho phép xây dựng mô hình mô phỏng cho một tầng máy nén hoặc tua bin (gọi chung là các máy cánh ―Turbo‖). Để mô phỏng cho các máy cánh nhiều tầng cần mô phỏng từng tầng của nó, việc ghép nối giữa các tầng trên nguyên tắc kết quả của tầng trước là đầu vào của tầng sau; việc thiết lập mô hình mô phỏng bằng ANSYS cho máy nén nhiều tầng chỉ các hãng hàng đầu thế giới tiến hành và được đánh giá là thành tựu lớn của mô phỏng số [16]. Để khắc phục khó khăn này, giải pháp là sử dụng phần mềm vẽ cơ khí Inventor để dựng hình 3D cho các máy cánh, sau đó phỏng theo cách cắt hình của BladeGen phân chia các máy cánh thành nhiều khối (theo từng tầng lá) và từ mỗi khối cắt giữ lại một múi phần tử (elements) mà ở đó có chứa một lá cánh. Ghép nối các phần tử kế tiếp nhau tạo thành mô hình kết cấu máy cánh sau đó mới đưa trực tiếp vào ANSYS-CFX. Để tính toán mô phỏng trong ANSYS-CFX phải thực hiện qua 5 bước: xây dựng mô hình hình học ―Geometry‖, tiến hành chia lưới trên cơ sở mô 60 hình hình học ―Mesh‖, Định nghĩa các khối, các mặt trên mô hình, các điều kiện ban đầu và các điều kiện biên ―Setup‖, thực hiện tính toán mô phỏng ―Solution‖, đưa ra các kết quả tính toán mô phỏng ―Results‖. 3.2.1. Xây dựng mô hình mô phỏng Sau khi nhập từ mô hình vẽ cơ khí vào ANSYS-CFX sẽ nhận được mô hình mô phỏng ―DesignModeler‖, ở đó đã thể hiện được cách dựng hình của BladeGen. Để giảm thiểu khối lượng tính toán mô hình này thay thế việc mô phỏng mỗi vòng lá cánh chỉ bằng một lá cánh đơn tương ứng của vòng đó và các lá đơn đại diện cho các vòng lá được sắp xếp kế tiếp nhau tạo thành mô hình mô phỏng cho máy nén thấp áp (hai tầng đầu), máy nén cao áp (vòng dẫn dòng và sáu tầng sau) và tua bin hai tầng, hình 3.1, 3.2. Hình dạng phối trí máy nén dựng lại trong môi trường ANSYS-CFX được thể hiện trên hình 3.7 gồm: các lá máy nén của hai cấp nén đầu (MNTA) và các lá của 6 cấp nén sau (MNCA). Hình 3.1. Mô hình ―DesignModeler‖ máy nén trong ANSYS-CFX 61 Hình 3.2. Mô hình ―DesignModeler‖ tua bin trong ANSYS-CFX Trên các mô hình thể hiện được các thành phần của máy cánh đưa vào mô phỏng, vùng tính toán của các phần là vùng mà không khí hoặc sản phẩm cháy chiếm chỗ, mỗi phần được giới hạn bởi các mặt bao sẽ được định nghĩa trong phần ―setup‖ trước khi đặt các điều kiện tính toán. Các lá máy cánh được định nghĩa là tường ―wall đứng yên‖ đối với các vòng chỉnh dòng, dẫn dòng máy nén và các vòng hướng chiều tua bin, ―tường quay‖ đối với các lá làm việc của máy nén và tua bin (hình 3.3, 3.4). Hình 3.3. Mô hình biểu diễn các bề mặt và các lá máy nén 62 Như vậy, một cấp nén có một dãy lá quay đứng trước và một dãy lá đứng yên đứng sau và cứ tiếp tục xếp xen kẽ như vậy tạo ra máy nén nhiều cấp. Hình 3.4. Mô hình biểu diễn các bề mặt và các lá tua bin Các dãy lá hướng chiều tua bin đứng trước còn các dãy lá làm việc đứng sau, trên hình 3.4 là tua bin hai cấp. Hình 3.5. Kích thước hình học khung bao của các phần máy nén 63 Hình 3.6. Kích thước hình học khung bao của các phần tua bin Dòng chảy trong máy nén và tua bin được giới hạn bởi các mặt của khung bao và các lá (các lá có thể đứng yên hoặc quay). Hình 3.7. Hình phối trí máy nén thấp áp và cao áp ANSYS-CFX cho phép biểu diễn số lượng lá các cấp nén và tua bin tùy ý bằng cách ghép các phần tử ―element‖ xung quanh trục tạo ra hình ảnh hoàn chỉnh, hình 3.7. 3.2.2. Chia lƣới mô hình mô phỏng Khi ghép các phần tử mô hình hình học, giữa các phần tử là các mặt tiếp giáp nên việc chia lưới sao cho khớp được giữa phần tử trước và sau, nếu chia bằng tay thì vô cùng phức tạp; vì vậy, việc chia lưới được tiến hành chia tự 64 động. Các kích thước lưới và bề mặt có thể chọn mặc định hoặc đặt tùy ý sao cho độ mịn có thể chấp nhận được sau khi đã chạy thử đảm bảo được độ hội tụ RMS nhỏ hơn hoặc bằng 1.e – 4, mô hình chia lưới hình 3.8, 3.9. Hình 3.8. Chia lưới mô hình máy nén Hình 3.9. Chia lưới mô hình tua bin Ở những vùng có các lá hoặc các vùng tiếp giáp các phần tử mật độ lưới dầy hơn và chế độ tự động chia lưới sẽ khớp được các mắt lưới của các mặt tiếp giáp giữa các phần tử. 65 3.2.3. Định nghĩa các phần tử, các mặt, xác định các điều kiện ban đầu, điều kiện biên “Setup” Để thiết lập các điều kiện cho tính toán mô phỏng ta giả thiết điều kiện môi trường khảo sát là điều kiện tiêu chuẩn với áp suất đặc trưng tham chiếu (reference pressure) p = 101325 Pa, nhiệt độ T = 288K, động cơ hoạt động trên mặt đất Hb = 0 m, Mb = 0. Môi chất công tác là khí thực đối với máy nén và sản phẩm khí cháy đối với tua bin, điều kiện mô hình dòng chảy bảo toàn năng lượng (total energy), mô hình tính toán áp dụng là mô hình chảy rối (k- epsilon). Chiều quay của rotor đối với các mô hình cả máy nén và tua bin được đặt ngược chiều kim đồng hồ nhìn từ phía sau (mũi tên trên mô hình). Trên mô hình ta tiến hành đặt tên cho các phần tử (elements), ở mô hình máy nén bao gồm 19 phần tử được đặt là R1 đến R8 ứng với các vòng lá làm việc máy nén (các vòng lá làm việc sẽ quay cùng tốc độ vòng quay), các vòng lá chỉnh dòng đứng yên được đặt là S1 đến S8, vòng dẫn dòng trước máy nén cao áp DD (đứng yên), phần thân chuyển tiếp giữa hai máy nén là S_thân, phần bao ngoài của dòng II là OT. Trên mô hình tua bin có 4 phần tử gồm: S1, S2 là các vòng lá hướng chiều (đứng yên) và R1, R2 là các vòng lá làm việc (quay cùng tốc độ). Hình 3.10. Xác định phần tử vòng làm việc máy nén tầng 1: R1 66 Khi thiết lập các điều kiện cho mỗi phần tử bao gồm: tên phần tử, trạng thái quay hoặc đứng yên, nếu quay thì tốc độ là bao nhiêu vòng/phút, ký hiệu phần tử trong mô hình ―DesignModeler‖, số lượng lá trên vòng làm việc đó là bao nhiêu; sau đó mới tiến hành định nghĩa cho các mặt. Hình 3.11. Xác định phần tử vòng hướng chiều tua bin tầng 1: S1 Trên các hình 3.10, 3.11 là ví dụ tượng trưng chọn một trong các phần tử của máy nén (19 phần tử) và tua bin (4 phần tử). Sau khi đặt tên cho tất cả các phần tử tiến hành định nghĩa các mặt cho mỗi phần tử. Các phần tử là các vòng lá chỉnh dòng, dẫn dòng, hướng chiều (passage) và các vòng lá làm việc đều có 6 bề mặt và lá: mặt trong (hud), mặt ngoài (shroud), mặt dòng chảy vào (inlet), mặt dòng chảy ra (outlet), hai mặt biên đối xứng lặp hai bên (periodic symmetrie 1 và 2) và các mặt bao của lá (blade). 67 Hình 3.12. Xác định các bề mặt bao của lá làm việc (blade) tầng 1 máy nén Trên hình 3.12 xác định lá làm việc (blade) tầng 1 (R1) máy nén tạo bởi ba bề mặt. Hình 3.13. Xác định mặt ngoài (shroud) của S1 (phần tử vòng hướng chiều tua bin tầng 1) Các mặt ra (outlet) của phần tử trước tiếp giáp với mặt vào (inlet) của phần tử sau sẽ có một bề mặt mà ANSYS-CFX định nghĩa là mặt giao tiếp (interfaces), hình 3.14, 3.15. 68 Hình 3.14. Xác định mặt giao tiếp (interface) (giữa phần tử đứng yên S1 và phần tử quay R1 của tua bin) Hình 3.15. Các lá và các mặt giao tiếp của tua bin Các phần tử còn lại là: S_than và OT cũng xác định 6 mặt nhưng không có các lá vì ở đó là dòng chảy từ máy nén thấp áp đến cao áp và đoạn sau của dòng ngoài (dòng II), hình 3.16. 69 Hình 3.16. Các bề mặt bao của S_than Điều kiện giải được đặt với bước thời gian (Physical Timescale) 1.e-5s; điều kiện hội tụ bình phương trung bình nhỏ nhất RMS < 1.e-4. Số bước tính lặp lớn nhất được chọn (Max. Iterations) là 1000. 3.2.4. Thực hiện tính toán mô phỏng “Solution” Thiết lập cho máy nén ―Axial Compressor‖ hoặc cho tua bin ―Axial Turbine‖ các điều kiện biên áp suất tham chiếu của môi trường ―Reference Pressure‖ là 0.1 [MPa] và thiết lập điều kiện ban đầu cho máy nén là ―p-Total Inlet p-Static Outlet‖ (hoặc ―p- Total Inlet Mass Flow Outlet‖) cho một chế độ vòng quay nào đó trong khoảng 28800 – 36000 vòng/phút (100% ứng với 36000 vòng/phút), có nghĩa là áp suất toàn phần và nhiệt độ toàn phần của không khí đầu vào máy nén lấy bằng điều kiện tiêu chuẩn môi trường bên ngoài. Áp suất tĩnh ―đối áp‖ ở cửa ra được thay đổi ứng với mỗi lần ―thử nghiệm‖, đối áp chính là để điều chỉnh lưu lượng dòng chảy qua máy cánh. Như vậy, ở một chế độ vòng quay phải ―thử nghiệm‖ nhiều lần, kết quả mỗi lần trên đồ thị đặc tính sẽ xác định được một điểm trên đồ thị của các tham số tương ứng, nối các điểm sẽ có đường đặc tính mà ở đó n = const. Ở tua bin lấy điều kiện vào là áp suất toàn phần và nhiệt độ toàn phần sau buồng đốt động cơ và cũng thay đổi đối áp tĩnh ở cửa ra ta cũng xác định được các đặc tính của tua bin tương tự như ở máy nén. 70 Các lựa chọn cho điều kiện ban đầu: Dải áp suất tĩnh Dải lƣu lƣợng cửa Trong Điều kiện ban đầu cửa ra ra luận án Các điều kiện chung: Reference Pressure = 0.1 [MPa], T-Total = 288K, Total Energy, k-Epsilon. ―p-Total Inlet p-Static 3.0 7.6at 5.83 8.21 [kg/s] Áp dụng Outlet‖ 1.68at ―p-Total Inlet Mass Không áp Không áp dụng Không áp dụng Flow Outlet‖ dụng ―Mass Flow Inlet p- Không áp Không áp dụng Không áp dụng Static Outlet‖ dụng Sở dĩ trong luận án áp dụng phương án ―p-Total Inlet p-Static Outlet‖ là vì động cơ hai dòng nên không cố định lưu lượng mà để động cơ tự động điều chỉnh phân bổ lưu lượng giữa hai dòng phụ thuộc vào tốc độ vòng quay và đối áp tĩnh ở cửa ra ―p-Static Outlet‖, tức là tự điều chỉnh lại mức phân dòng m nhằm ngăn ngừa ―hóc khí‖ cho MNCA khi vòng quay còn nhỏ. Còn điều kiện tại cửa vào là áp suất và nhiệt độ môi trường trong điều kiện khí quyển chuẩn (cho máy nén), và áp suất và nhiệt độ sau buồng đốt (cho tua bin). Thông thường khi chương trình chạy đạt độ hội tụ thì sẽ dừng lại, bước lặp (Iterations) khoảng 500 -600. Một số chế độ gần biên giới hóc khí hoặc khu vực nghẽn dòng nếu bước lặp đã lớn khoảng 700- 1000 mà chưa hội tụ, nếu sự biến đổi các tham số lặp đi lặp lại theo c
File đính kèm:
luan_an_nghien_cuu_xac_dinh_cac_tham_so_nhiet_dong_luc_hoc_c.pdf
Bia LA.docx
Bia Tom tat.docx
Thong tin dong gop moi.docx
Tom tat.pdf
Trich yeu LA.docx