Luận án Phương pháp xác định mòn dọc trục VMĐB trên thiết bị thử nghiệm với điều kiện tải và tốc độ quay thay đổi, chịu tác động của môi trường theo TCVN 7699-2-30
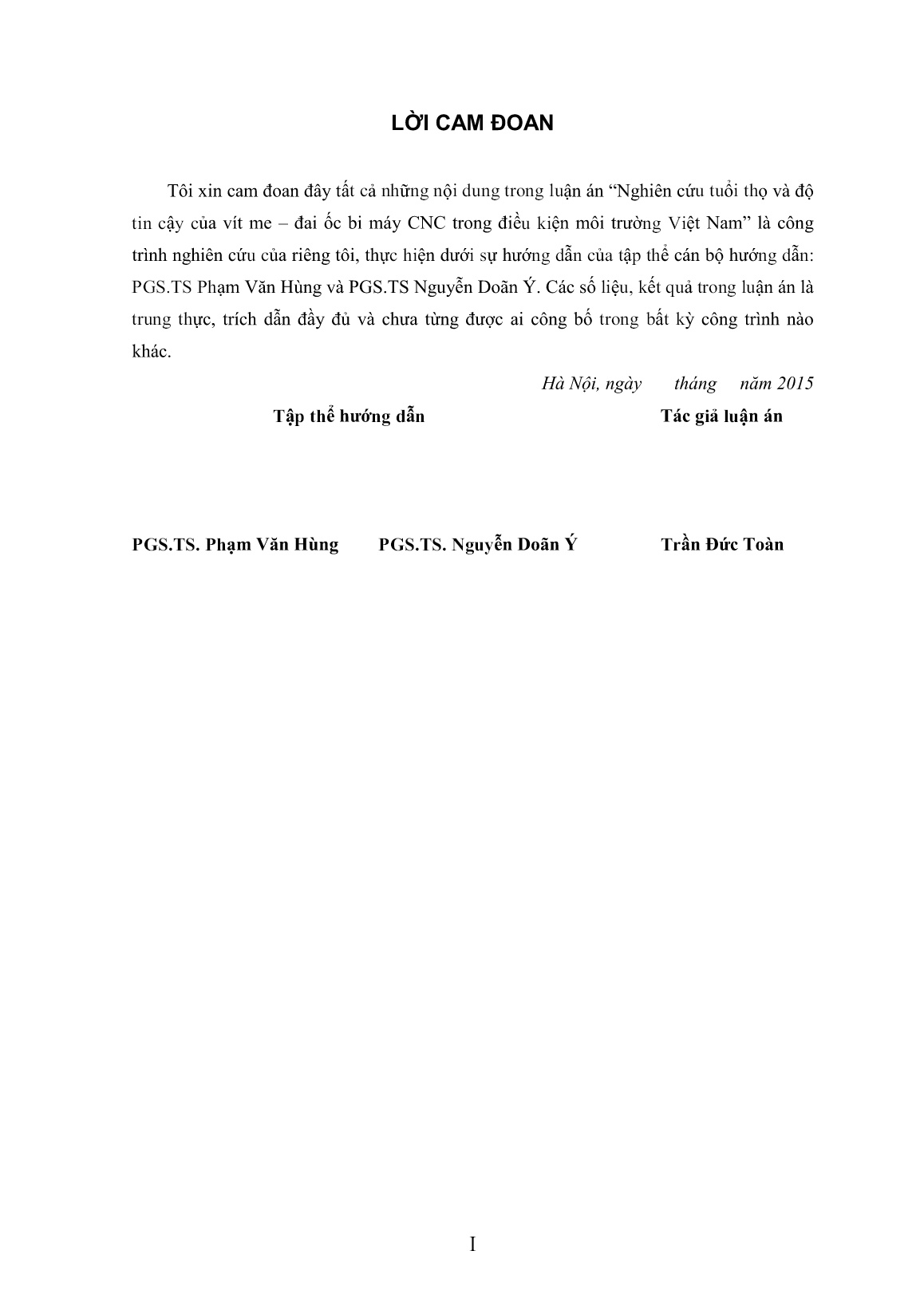
Trang 1
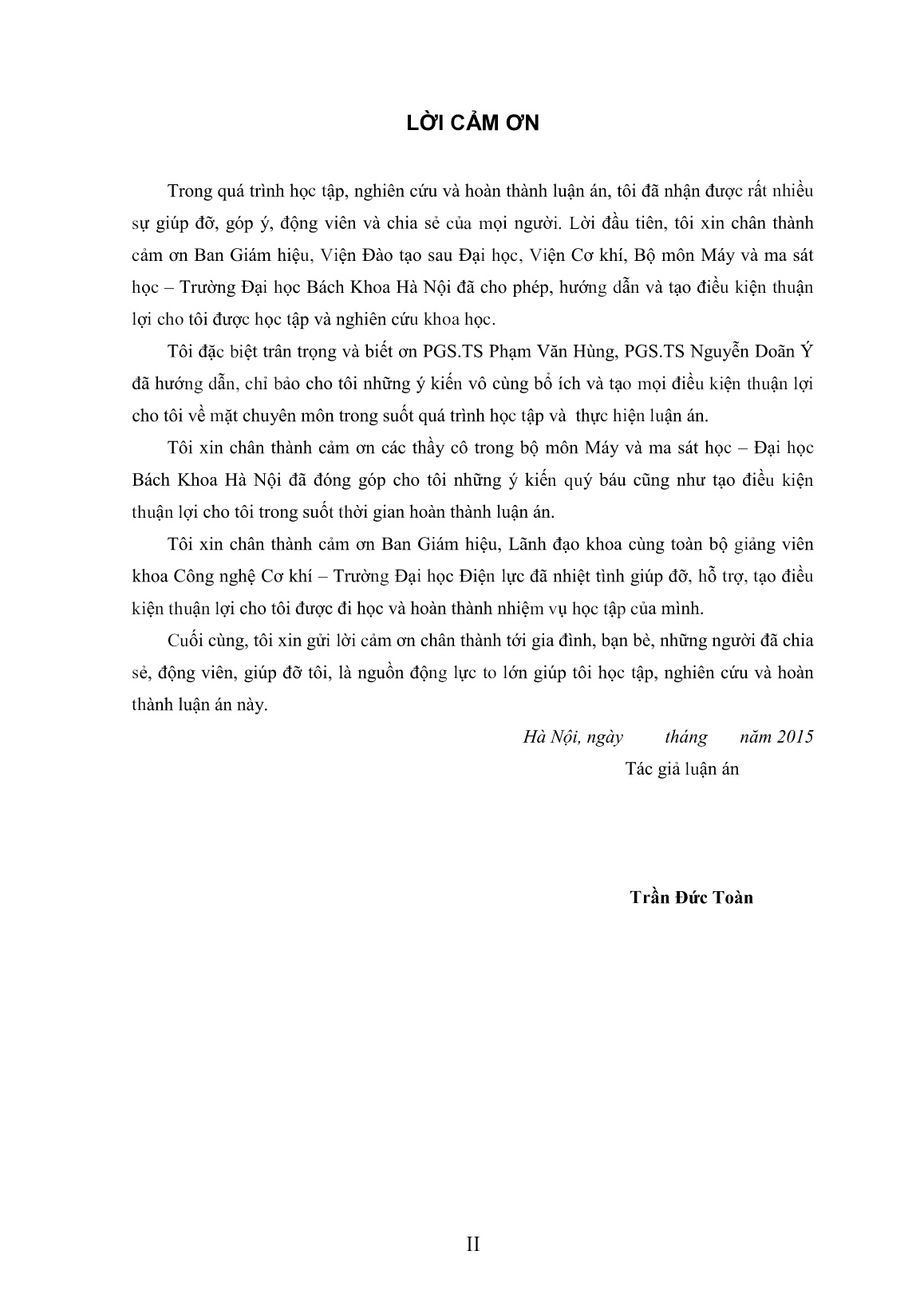
Trang 2
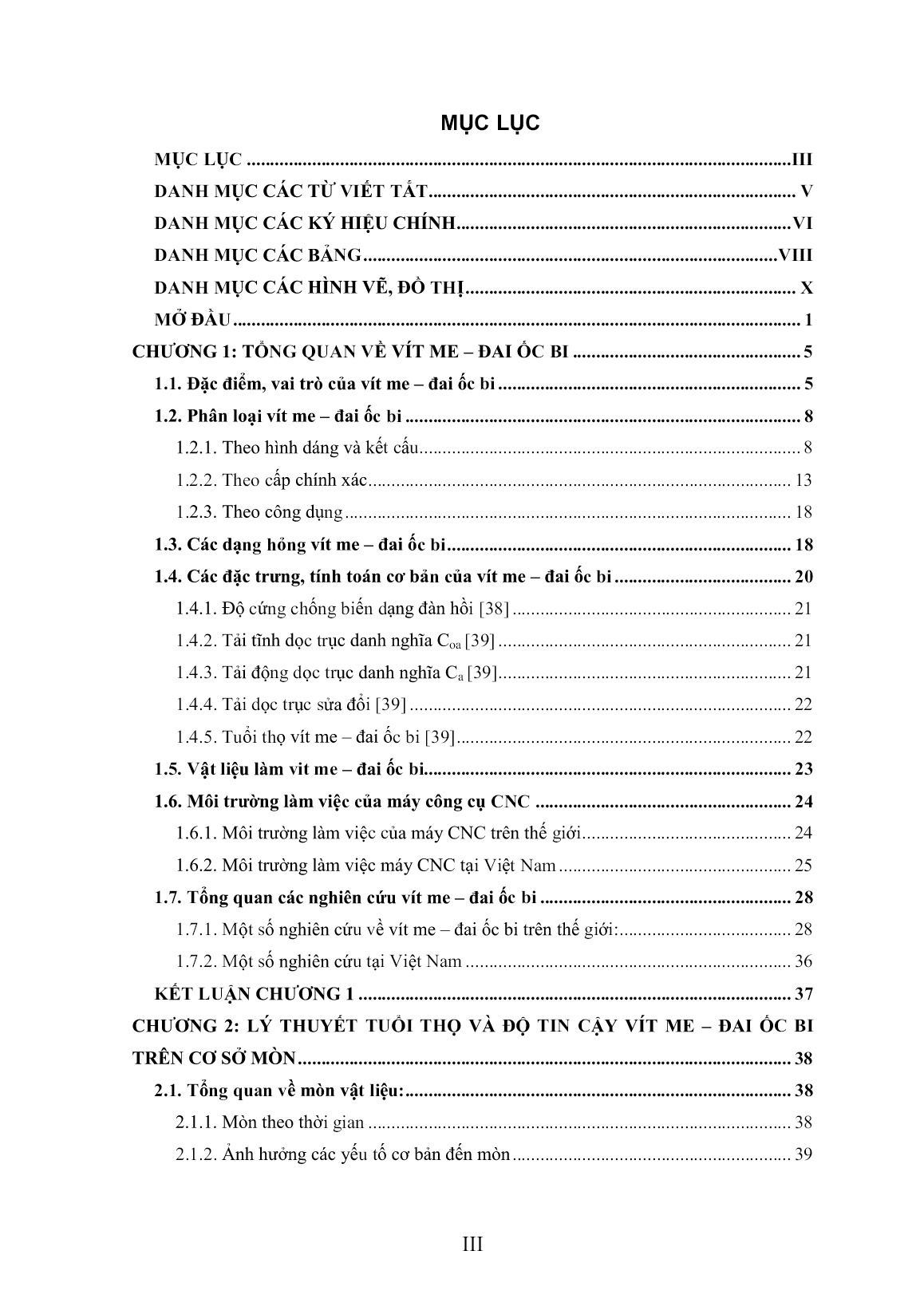
Trang 3

Trang 4
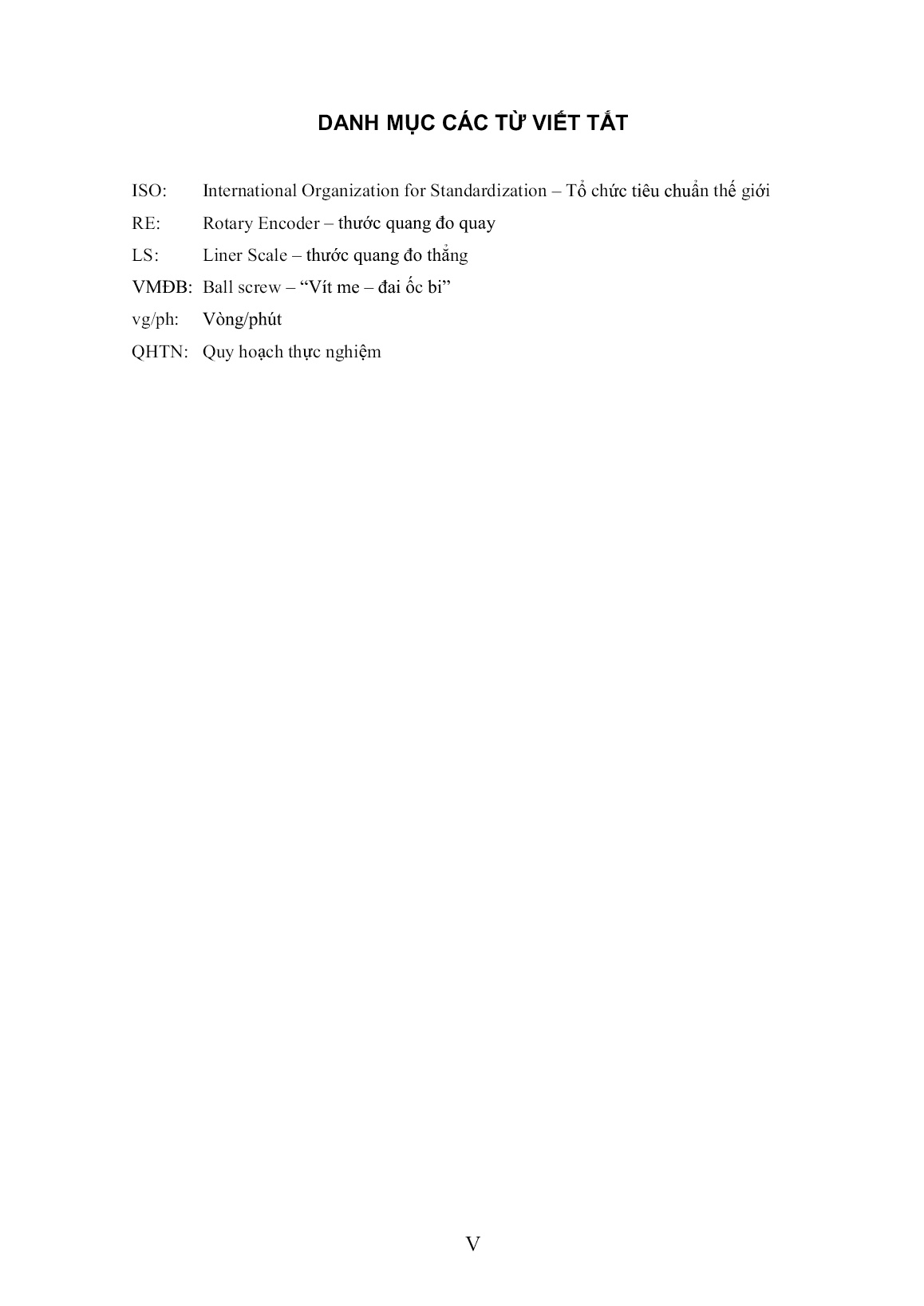
Trang 5
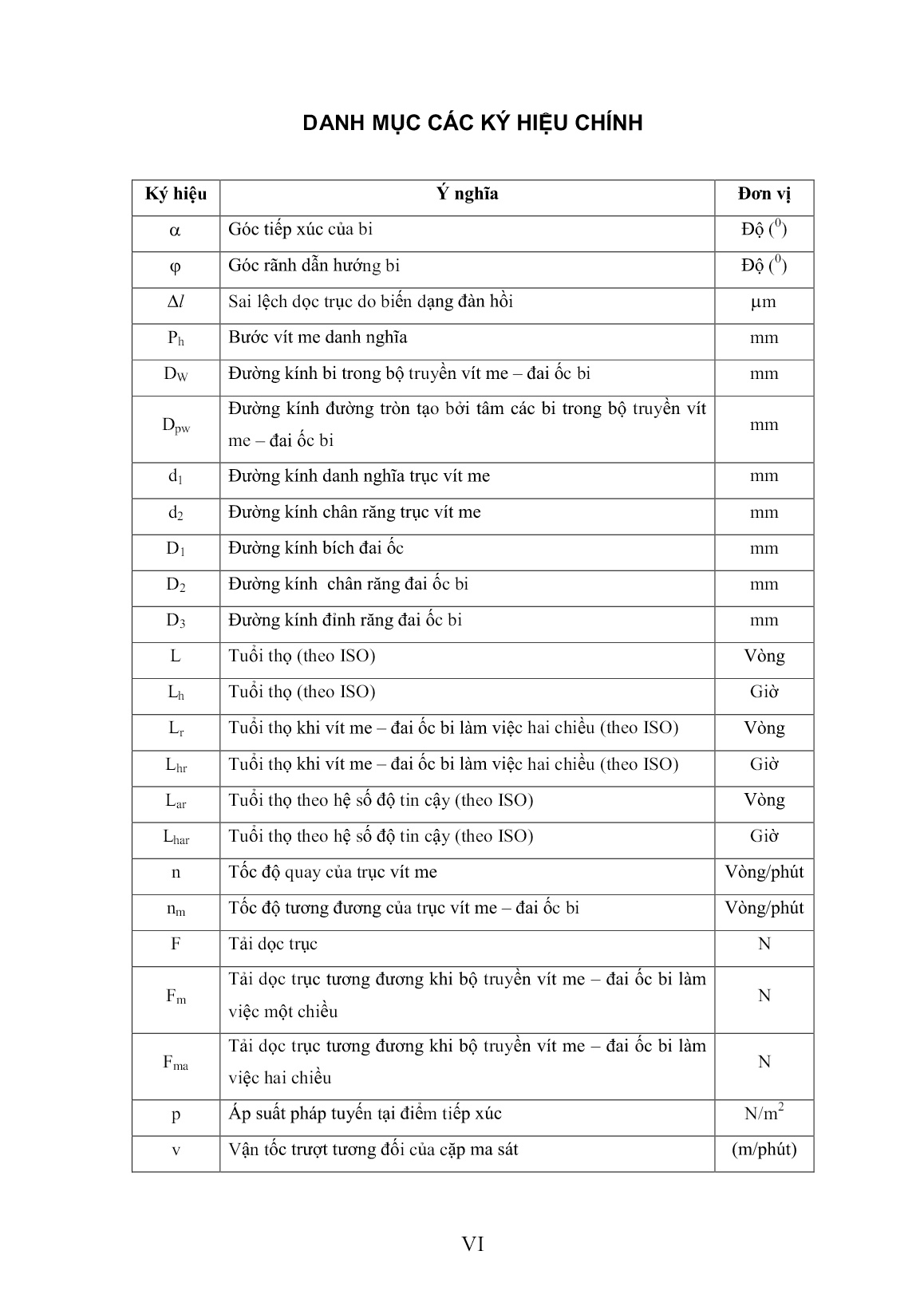
Trang 6
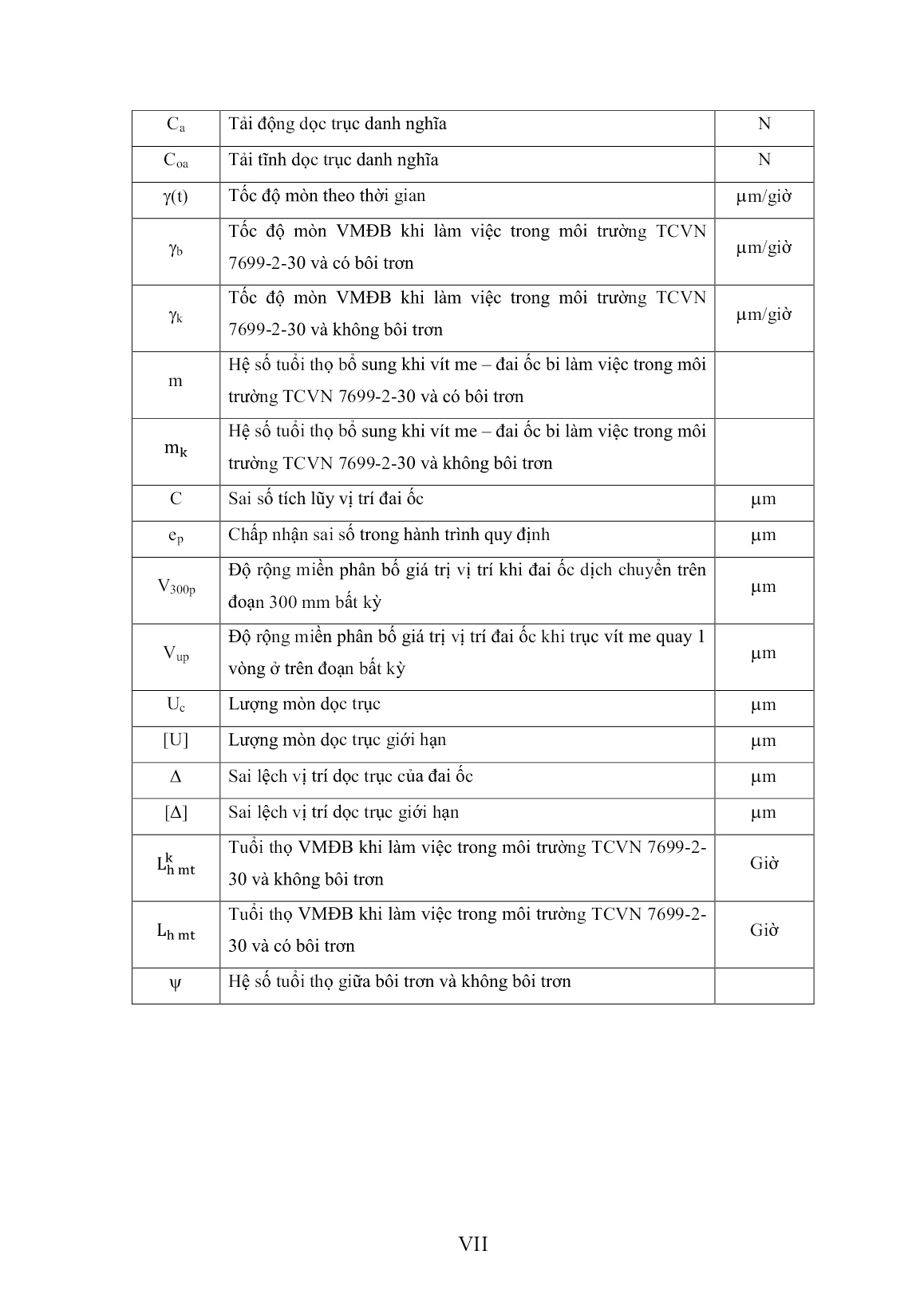
Trang 7
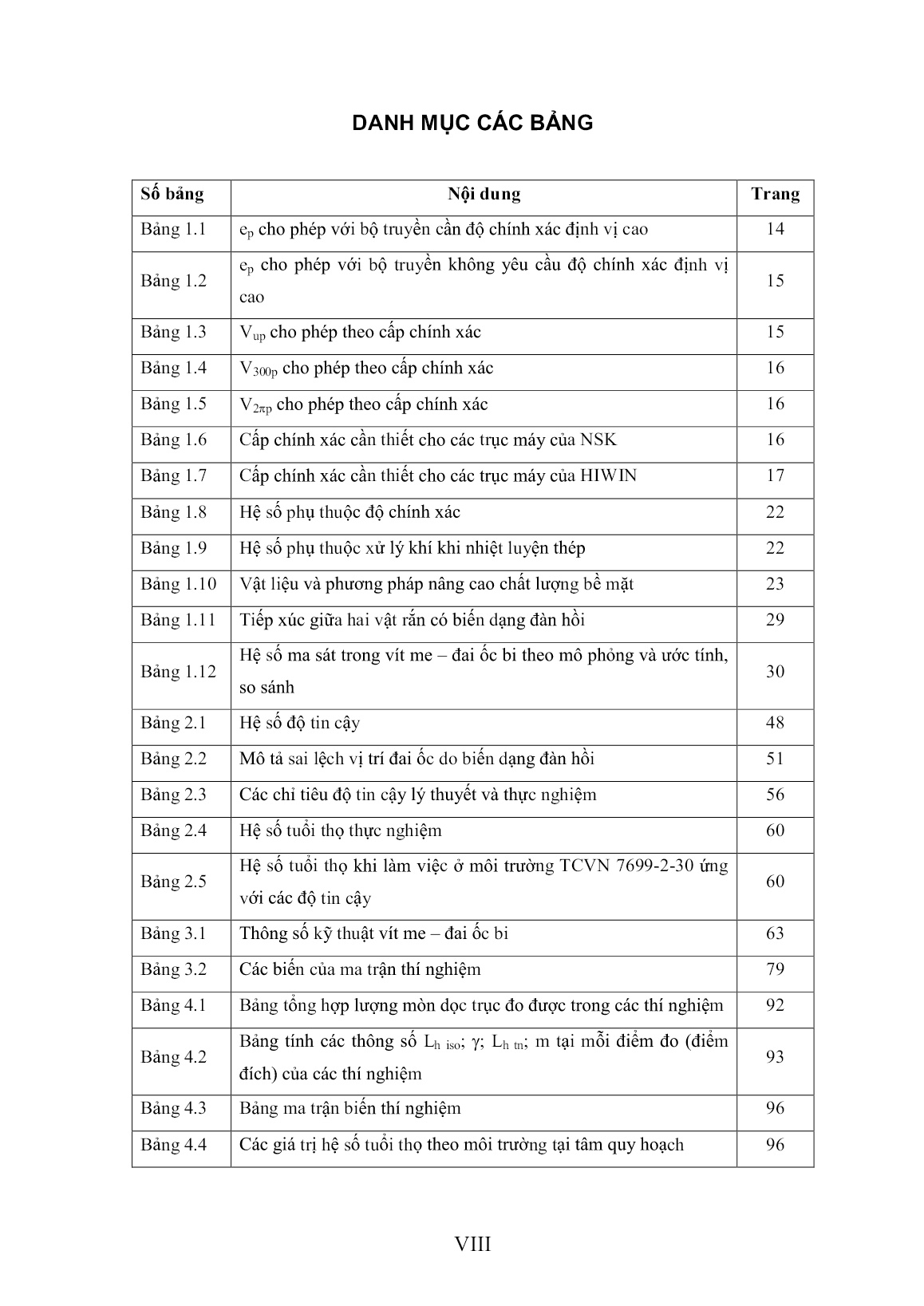
Trang 8
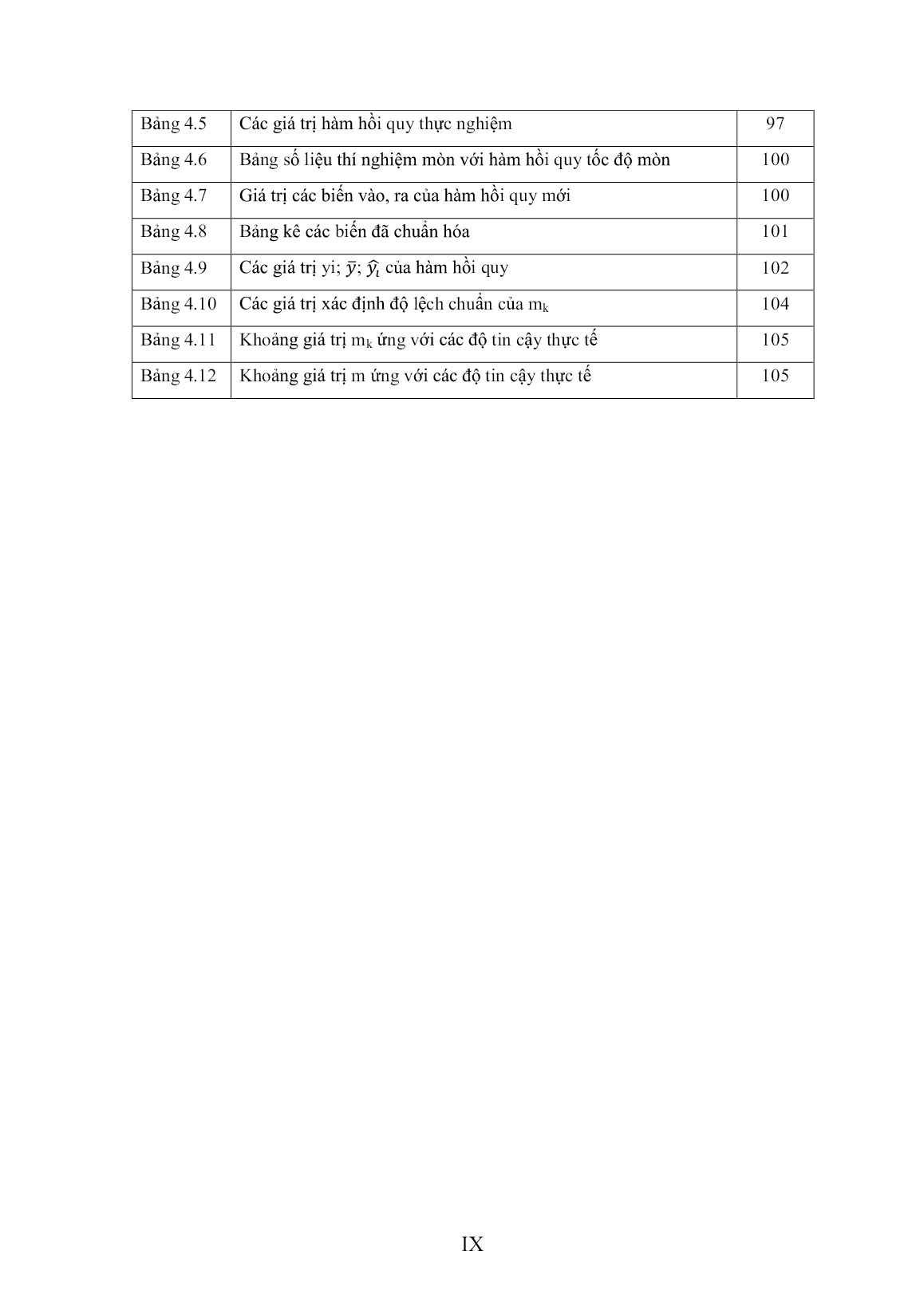
Trang 9
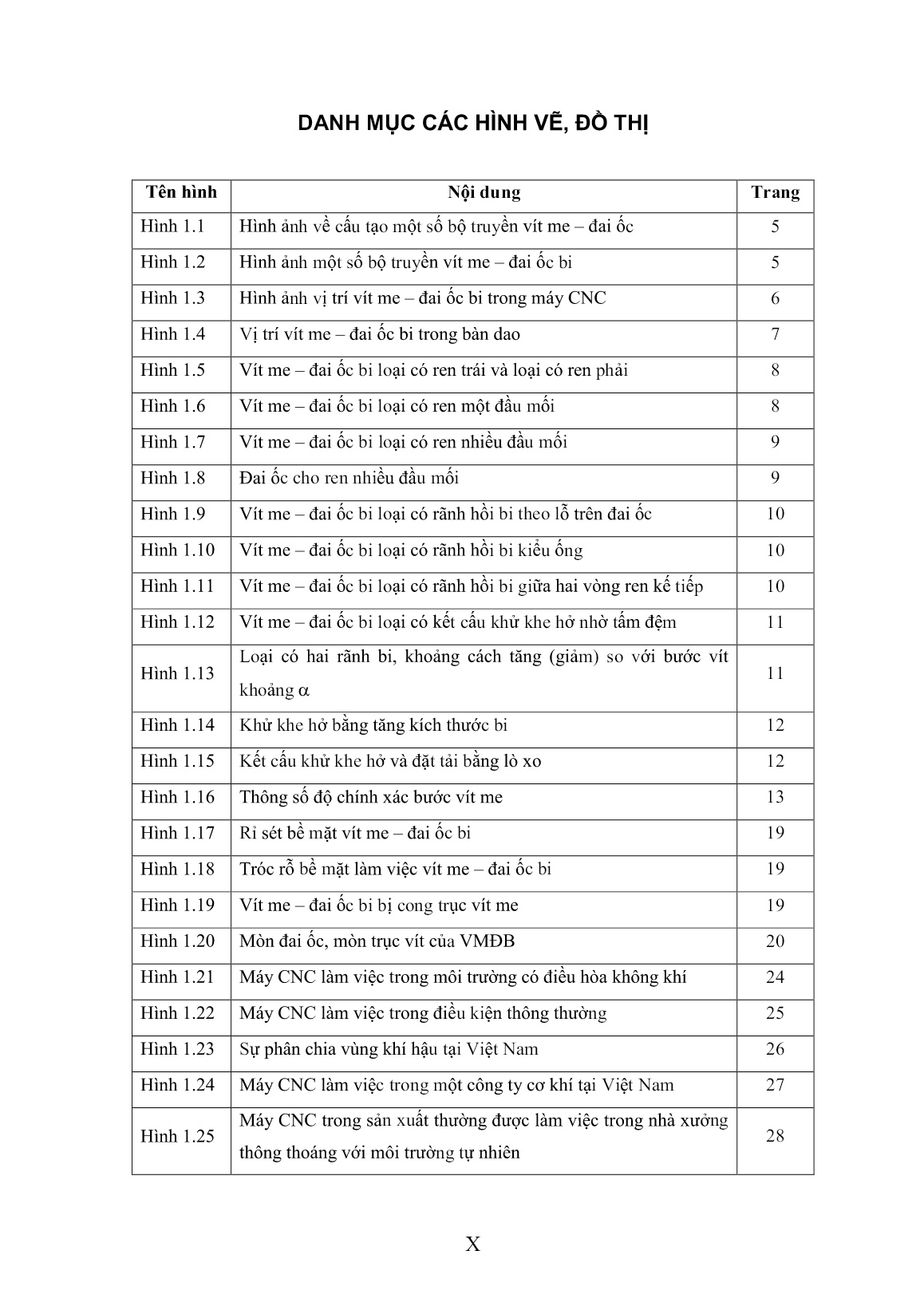
Trang 10
Tải về để xem bản đầy đủ
Bạn đang xem 10 trang mẫu của tài liệu "Luận án Phương pháp xác định mòn dọc trục VMĐB trên thiết bị thử nghiệm với điều kiện tải và tốc độ quay thay đổi, chịu tác động của môi trường theo TCVN 7699-2-30", để tải tài liệu gốc về máy hãy click vào nút Download ở trên.
Tóm tắt nội dung tài liệu: Luận án Phương pháp xác định mòn dọc trục VMĐB trên thiết bị thử nghiệm với điều kiện tải và tốc độ quay thay đổi, chịu tác động của môi trường theo TCVN 7699-2-30
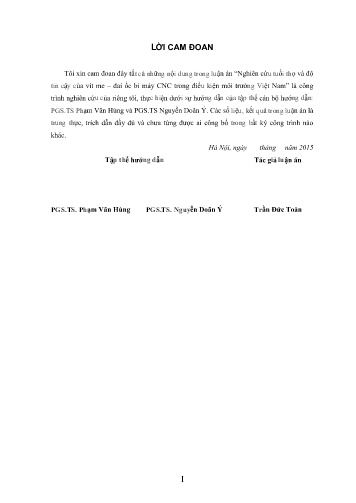
là tỷ số tính phần trăm giữa lượng hơi có thực trong không khí so với lượng hơi có trong không khí bão hòa với cùng nhiệt độ. Độ ẩm tương đối là đại lượng thể hiện lượng hơi nước có trong một đơn vị thể tích không khí và nói lên khả năng hòa tan thêm hơi nước trong không khí so với mức tối đa. Bởi vậy trong thực tế thường sử dụng khái niệm độ ẩm tương đối thay vì sử dụng khái niệm độ ẩm tuyệt đối. Khi lượng hơi nước trong không khí tăng lên, tiếp xúc với chất bôi trơn làm suy giảm tính năng bôi trơn của chất bôi trơn. Lượng oxy trong không khí có cơ hội tiếp xúc với bề mặt ma sát nhiều hơn tạo điều kiện cho việc hình thành lớp oxyt trên bề mặt. Lớp oxyt này có cơ tính khác hẳn với cơ tính của lớp kim loại nền. Khi hai bề mặt ma sát tương tác với nhau tại vị trí có lớp màng oxyt, ứng suất giữa lớp bề mặt và lớp kim loại nền có sự chênh lệch lớn làm lớp màng oxyt dễ bị bong tróc, gây mòn vật liệu [5]. - Tác động do biến đổi nhiệt độ và độ ẩm Do các chi tiết trong máy, thiết bị có kích thước, yêu cầu kỹ thuật khác nhau nên chúng thường được làm bằng các vật liệu khác nhau. Khi biến đổi nhiệt độ xảy ra, các chi tiết có vật liệu và kích thước khác nhau sẽ có hệ số giãn nở (co) nhiệt khác nhau dẫn tới hiện tượng biến đổi tăng tải trong các chi tiết máy (co, kéo), hoặc thay đổi đặc tính tải (tải tĩnh trở thành tải động, hoặc xung,..), làm suy giảm tính năng kỹ thuật của máy. Độ ẩm tương đối không khí cao có ảnh hưởng lớn hơn đến sự mài mòn chi tiết máy. Thực tế cho thấy độ ẩm tương đối của không khí chỉ thực sự có ảnh hưởng đáng kể tới sự tạo thành lớp oxyt trên bề mặt và ăn mòn các chi tiết máy khi chúng có giá trị từ 80% đến 100%. Khi ở vùng có độ ẩm tương đối cao, không khí tiếp xúc với bề mặt có chênh lệch nhiệt độ khoảng > 50C sẽ rất dễ rơi vào vùng không khí quá bão hòa, dẫn đến hiện tượng đọng sương (hơi nước ngưng tụ) trên bề mặt có tiếp xúc với không khí. Chênh lệch nhiệt độ càng cao càng làm tăng lượng hơi nước ngưng tụ trên bề mặt, làm suy giảm tính năng bôi trơn, thẩm thấu và oxy hóa bề mặt kim loại, gây bong, tróc, mòn khi có tải. 42 Hình 2.3 thể hiện biểu đồ biến đổi nhiệt ẩm của không khí ở áp suất 760 mmHg. Hình 2.3 Biểu đồ biến đổi nhiệt ẩm của không khí [74] Dựa trên số liệu của biểu đồ nhiệt ẩm Y-D của không khí ở mức áp suất khí quyển 760 mm Hg, khi nhiệt độ và độ ẩm cùng biến đổi với điều kiện RH 500C, các tác động lên khả năng làm việc của máy, chi tiết máy chỉ đơn thuần là tổng toán học từng tác động của nhiệt độ, độ ẩm (độ ẩm không khí không thể đạt mức bão hòa khi ở nhiệt độ cao >500C). Khi độ ẩm tương đối trong môi trường ở mức cao (RH 80% RH100%) và nhiệt độ dưới 500C, kết hợp với biến động nhiệt độ với tốc độ cao (khoảng 50C/giờ) làm 43 chênh lệch nhiệt độ giữa mối trường và bề mặt ma sát lớn, hơi nước trong không khí gặp bề mặt có nhiệt độ nhỏ hơn hoặc bằng nhiệt độ đọng sương sẽ ngưng kết trên bề mặt đó (ngưng tụ nước trên bề mặt ma sát). Lượng biến đổi nhiệt độ và tốc độ biến đổi là cơ sở xác định thời gian và lượng hơi nước đọng thành sương trên bề mặt. Ở mức áp suất khí quyển khác, nhiệt độ giới hạn mà ở đó độ ẩm tương đối của không khí có thể đạt mức bão hòa (RH 100%) sẽ thay đổi. Sự có mặt của hơi nước ngưng tụ trên bề mặt vật liệu là kết quả của sự biến đổi có điều kiện của cả nhiệt độ và độ ẩm không khí (khi nhiệt độ biến đổi với tốc độ cao, biên độ lớn và kèm thêm độ ẩm tương đối của không khí cao) [18]. Hơi nước ngưng tụ có thể xuất hiện tại mọi vị trí bề mặt thiết bị có tiếp xúc với môi trường, nếu bề mặt chi tiết được bảo vệ bằng lớp dầu bôi trơn, nước thẩm thấu vào lớp dầu, gây biến tính và giảm khả năng bôi trơn, bảo vệ của dầu và oxy hóa bề mặt kim loại. Nhiệt độ biến đổi với biên độ lớn, tốc độ cao, kết hợp với độ ẩm tương đối của không khí ở mức cao (RH 80%) dẫn đến các hiện tượng: Tăng tải, hoặc hay đổi đặc tính tải; Xuất hiện đọng sương trên bề mặt ma sát. Đây là một môi trường khá khắc nghiệt nếu các cặp ma sát làm việc ở điều kiện này. Đặc biệt, với những chi tiết làm bằng vật liệu dễ oxy hóa bề mặt khi không được bảo vệ, nguyên tử oxy trong nước khi nước tự phân tách sẽ oxyt hóa bề mặt, đồng thời tạp chất do bụi bẩn trong không khí ngưng tụ trong các hạt sương chui vào giữa hai bề mặt tiếp xúc có tác dụng như những hạt mài li ty làm trầy xước, bong tróc và mòn cặp vật liệu nhanh chóng. Sự khắc nghiệt của điều kiện môi trường miền Bắc với biến động nhiệt lớn, độ ẩm tương đối cao, thể hiện qua TCVN 7699-2-30 và được ghi nhận bởi rất nhiều trường hợp suy giảm độ chính xác của máy, thiết bị trên thực tế là cơ sở triển khai nghiên cứu đề tài. 2.1.3. Tiêu chuẩn quốc gia TCVN 7699-2-30 về thử nghiệm môi trƣờng * Phạm vi áp dụng: Tiêu chuẩn này để mô phỏng và xác định sự thích hợp của các linh kiện, thiết bị hoặc các sản phẩm khác khi được sử dụng, vận chuyển, bảo quản trong các điều kiện có độ ẩm cao kết hợp với sự thay đổi nhiệt độ theo chu kỳ và thường tạo ra sự ngưng tụ trên bề mặt. * Yêu cầu kết cấu tủ thử: Nhiệt độ tủ thử phải thay đổi theo chu kỳ trong khoảng từ 250C ± 30C đến nhiệt độ giới hạn trên (phương án 1: 400C hoặc phương án 2: 550C) với dung sai và tốc độ thay đổi quy định nếu thuộc đối tượng áp dụng. 44 Dung sai nhiệt độ tổng ±30C. Miền dung sai này là thích hợp để tính đến sai số tuyệt đối của phép đo cũng như các thay đổi chậm về nhiệt độ và sự biến đổi nhiệt độ của không gian làm việc. Có thể cần phải giữ dao động trong thời gian ngắn ở phạm vi ± 0,50C để duy trì độ ẩm yêu cầu. Độ ẩm tương đối trong không gian làm việc được duy trì trong các giới hạn theo các giai đoạn và phương án được chọn. Phải cẩn thận để đảm bảo nhiệt độ, độ ẩm tại các điểm trong tủ thử phải nằm trong giới hạn yêu cầu. Chú ý đến sự trao đổi nhiệt của không khí. Nước ngưng tụ phải được xả ra liên tục từ tủ thử và không được sử dụng lại cho đến khi nước được làm tinh khiết trở lại. Phải đảm bảo rằng không có nước ngưng tụ rơi lên mẫu thử. * Mức khắc nghiệt: Có hai phương án quy định mức khắc nghiệt, phối hợp giữa nhiệt độ giới hạn trên và số chu kỳ quyết định mức khắc nghiệt của thử nghiệm. Mức khắc nghiệt thứ nhất: 550C Số chu kỳ thử nghiệm 1; 2; 6. Mức khắc nghiệt thứ hai: 400C Số chu kỳ thử nghiệm 2; 6; 12; 21; 56. * Mô tả chu kỳ 24h: Giai đoạn tăng nhiệt: “Nhiệt độ của tủ thử phải được tăng lên nhiệt độ giới hạn trên thích hợp mô tả trong quy định kỹ thuật liên quan. Nhiệt độ giới hạn trên phải đạt được trong thời gian 3h ± 30’ với tốc độ nằm trong các giới hạn xác định bởi diện tích được tô đậm như hình 2a và 2b” Sự ngưng tụ có thể xuất hiện trên mẫu trong giai đoạn tăng nhiệt độ này. Giai đoạn ổn định nhiệt: Nhiệt độ phải được duy trì trong các giới hạn quy định đối với nhiệt độ giới hạn trên (± 20C) trong vòng 12h ±30’ tính từ khi bắt đầu chu kỳ. Trong giai đoạn này, độ ẩm tương đối phải là 93% RH ± 3% RH, trong 15 phút đầu và 15 phút kết thúc, độ ẩm phải đạt từ 90% RH đến 100% RH. Giai đoạn hạ nhiệt: Chọn một trong hai phương án thích hợp cho mẫu thử - Chọn phương án 2 (hình 2b, trang 191 của TCVN 7699-2-30:2007) do sự thích hợp với tất cả các loại mẫu [18]. Nhiệt độ phải được hạ xuống 250C ± 30C trong từ 3 đến 6 giờ. Độ ẩm tương đối không được nhỏ hơn RH 80%. Sau đó, nhiệt độ phải được duy trì ở 250C ± 30C với độ ẩm tương đối không được nhỏ hơn 95% RH cho đến khi kết thúc chu kỳ 24h. 45 Sự kết hợp biến đổi từng yếu tố nhiệt độ, độ ẩm theo thời gian của chu trình 24 giờ được mô tả bởi hình 2.4 Hình 2.4 Mô tả chu trình nhiệt ẩm [18] * Giai đoạn tạo ổn định: Để nhiệt độ đạt được ổn định 250C ± 30C cho chu trình đầu tiên bằng cách: a) Đặt mẫu thử trong tủ riêng trước khi đưa vào tủ thử hoặc b) Điều chỉnh nhiệt độ tủ thử đến 250C ± 30C sau khi đưa mẫu vào và duy trì mẫu ở mức này cho đến khi mẫu đạt đến nhiệt độ ổn định. Giai đoạn tạo ổn định được thể hiện trên hình 2.5 Hình 2.5 Giai đoạn tạo ổn định [18] N h iệ t đ ộ m ô i tr ư ờ n g Đ ộ ẩ m t ư ơ n g đ ố i (% ) Thời gian Thời gian để độ ẩm RH% đạt từ 95% đến 100% không quá 1 giờ N h iệ t đ ộ m ô i tr ư ờ n g Đ ộ ẩ m t ư ơ n g đ ố i (% ) 46 Trong quá trình ổn định nhiệt độ bằng cả hai phương pháp, độ ẩm tương đối phải nằm trong các giới hạn quy định cho các điều kiện không khí tiêu chuẩn dùng trong thử nghiệm. Sau giai đoạn ổn định, với mẫu ở trong tủ thử, độ ẩm tương đối phải được tăng lên không nhỏ hơn RH 95% ở nhiệt độ xung quanh bằng 250C ± 30C. 2.2. Tuổi thọ vít me – đai ốc bi 2.2.1. Tuổi thọ vít me – đai ốc bi theo lý thuyết Thông thường, tuổi thọ các chi tiết, kết cấu máy được xác định phụ thuộc yêu cầu và điều kiện làm việc của chi tiết, kết cấu. Tuổi thọ được xác định theo độ bền: khả năng chịu tải tĩnh; khả năng chịu tải động; mòn; mỏi (khi làm việc nhiều chu trình) hoặc Tuổi thọ theo độ chính xác làm việc. Đa phần các chi tiết máy, kết cấu đều được thiết kế, chế tạo để làm việc với độ chính xác làm việc nhất định trong điều kiện tải động và phải làm việc nhiều chu trình, do đó bài toán xác định tuổi thọ thường là bài toán tổng hợp xác định số chu trình làm việc khi chịu tải mà độ chính xác làm việc vẫn ở trong một mức nhất định, gồm bài toán xác định độ bền mỏi và bài toán xác định số chu trình làm việc ứng với mức tải, vận tốc để độ chính xác làm việc của VMĐB ở từng cấp chính xác. Trên cơ sở nghiên cứu, thống kê các thí nghiệm do mỏi, lập được đồ thị quan hệ ứng suất với số chu kỳ thay đổi ứng suất N mà chi tiết, cụm chi tiết chịu được đến khi hỏng [12]. Phương trình đường cong mỏi được viết dưới dạng: mN = C (2.4) Trong đó: C: Hằng số; m: Bậc của đường cong mỏi; N: Số chu kỳ thay đổi ứng suất; : Ứng suất. Hình 2.6 Đồ thị đường cong mỏi [12] Với những cặp ma sát có tiếp xúc đàn hồi. Trong quá trình ma sát, thể tích lớp vật liệu bề mặt chịu ứng suất biến thiên theo chu kỳ. Tác động mỗi chu kỳ không mất đi mà bị tích lũy lại các hư hỏng, dẫn đến phá hủy. Tuy nhiên “số chu kỳ ma sát dẫn đến phá hủy vật Ứ n g s u ất Số chu kỳ thay đổi Ứng suất 47 liệu hay bậc của đường cong mỏi phải xác định bằng thực nghiệm. Số mũ của thông số mỏi trên thực tế đặc trưng cho tất cả quá trình hóa lý khi ma sát, hiện nay không tính toán được mà phải xác định qua thực nghiệm. Thứ nhất: Thử nghiệm mòn; thứ hai: thí nghiệm trên thiết bị đo tiếp xúc cục bộ cho vật liệu không tương tác cơ hóa với môi trường. Khi thử nghiệm mòn, “sử dụng kết quả thử nghiệm mòn ở hiện trường và trong phòng thí nghiệm để tổng hợp hoặc kiểm nghiệm lại các dữ kiện. Nhược điểm chủ yếu của phương pháp này là số mẫu thử nghiệm ít, để có độ chính xác cao phải tốn nhiều thời gian và kinh phí” [5]. Với bộ truyền VMĐB, tuổi thọ được xác định theo số chu trình làm việc khi đặt tải mà vẫn đạt cấp chính xác nhất định, và được tính toán dựa trên vật liệu, kích thước, độ chính xác, nhẵn bóng bề mặt, công nghệ xử lý bề mặt,... Các thông số này được tổng hợp và thể hiện qua giá trị tải tĩnh cho phép Coa; giá trị tải động cho phép Ca và các hệ số tuổi thọ phụ thuộc vào độ cứng bề mặt fh; cấp chính xác fac; quá trình nấu chảy vật liệu fm; được tính toán và cho bởi nhà sản xuất trên cơ sở quy định về tuổi thọ các bộ truyền vít me bi trong tiêu chuẩn ISO [35-39] Tuổi thọ cho bộ truyền không được đặt tải trước [39] Tuổi thọ cho bộ truyền làm việc một chiều Tuổi thọ tính theo số vòng quay L (vòng) ( ) (vòng) (2.5) Tuổi thọ tính theo giờ Lh (h) (h) (2.6) Trong đó: ∑ : tốc độ quay tương đương của trục vít me; nj : giá trị tốc độ trục vít me ở chế độ làm việc thứ j; qj: tỷ lệ phần trăm trục vít làm việc ở tốc độ nj; √∑ : tải tương đương; Fj: giá trị tải dọc trục vít me ở chế độ làm việc thứ j; qj: tỷ lệ phần trăm trục vít làm việc ở tốc độ nj và Fj. Tuổi thọ cho bộ truyền làm việc hai chiều: ( ) (vòng) (2.7) Trong đó: L1,2: Tuổi thọ cho chiều 1 là L1 và chiều 2 là L2; Fm1,2: Tải tương đương ở chiều 1 là Fm1 và chiều 2 là Fm2. 48 Tuổi thọ cho bộ truyền được đặt tải trước [39] ( ) (vòng) (2.8) Fma(1) và Fma(2) là tải tương đương thực tế theo chiều 1 của đai ốc 1 và theo chiều 2 của đai ốc 2 (theo mỗi chiều tương ứng có mỗi đai ốc làm việc và chịu tải nén) Tuổi thọ cho các bộ truyền làm việc hai chiều [39] ( ) (vòng) (2.9) Tuổi thọ với hệ số độ tin cậy [39] Theo đơn vị tính số vòng quay: Lar = L . far (vòng) (2.10) Hoặc với vít me – đai ốc bi làm việc hai chiều hoặc đặt tải trước Lar = Lr . far (vòng) (2.11) Theo đơn vị tính giờ “h”: Lhar = Lh . far (h) (2.12) Bảng 2.1 Hệ số độ tin cậy Độ tin cậy far 90 1 95 0,62 96 0,53 97 0,44 98 0,33 99 0,21 2.2.2. Tuổi thọ vít me – đai ốc bi trên cơ sở mòn Tuổi thọ của chi tiết, cụm chi tiết máy thông thường được xác định theo lượng mòn cho phép [U]. Khi lượng mòn U đạt giá trị tới hạn, nó làm thay đổi chế độ lắp ghép, tăng sai lệch hình dáng hình học của bề mặt tiếp xúc dẫn đến va đập của các bề mặt ma sát và chuyển sang quá trình mòn không bình thường. Khi đó, trạng thái hình học tế vi xấu đi, nhấp nhô tăng lên làm tốc độ mòn ngày càng tăng mạnh, kích thước tiết diện giảm làm ứng suất xuất hiện trong các chi tiết máy tăng lên nhanh, khi đạt ch là lúc vật liệu bị chảy dẻo, hoặc nứt gãy, phá hủy [5, 7]. Một thực tế là trong các máy có yêu cầu độ chính xác cao như máy công cụ CNC, từng chi tiết máy được thiết kế và ấn định một cấp chính xác cho phù hợp với cấp chính xác làm việc của toàn máy. Khi làm việc, các cặp chi tiết máy có chuyển động tương đối (cặp ma sát) sẽ mòn, lượng mòn lớn dần, cùng với các yếu tố khác làm cho độ chính xác máy giảm dần, sai số làm việc tăng dần. Khi sai số tăng đến giá trị cho phép (được xác định theo cấp chính xác), là lúc máy không thực hiện được yêu cầu làm việc ban đầu ( yêu 49 cầu về độ chính xác). Như vậy, do mòn cùng một số yếu tố khác, độ chính xác máy suy giảm và hết tuổi thọ của máy. Bộ tiêu chuẩn quốc tế ISO 3408 về VMĐB quy định cách tính tuổi thọ của từng bộ truyền VMĐB cụ thể. Đồng thời cũng quy định sai lệch dọc trục cho phép tối đa của VMĐB ứng với từng cấp chính xác. Do vậy, nếu tìm được mối quan hệ giữa sai lệch vị trí với lượng mòn, cùng với việc xác định cụ thể các yếu tố ảnh hưởng tới sai lệch vị trí đai ốc sẽ cho phép tính toán tuổi thọ VMĐB qua mòn. VMĐB cùng với ổ đỡ chặn của nó khi chịu tải và chuyển động có thể được mô hình hóa phục vụ tính toán, xác định vị trí đai ốc, giống như hệ đàn hồi gồm 3 chi tiết được mô tả như 3 lò xo mắc nối tiếp (ổ chặn, trục vít, đai ốc) [22]. Khi trục vít me đứng yên tại một vị trí góc quay, nếu đặt tải dọc trục lên đai ốc, vị trí đai ốc là tổng hợp vị trí ba chi tiết nối tiếp: ổ chặn; trục vít; đai ốc, gồm kích thước ban đầu cùng lượng biến dạng đàn hồi. Xét một chi tiết chịu biến dạng đàn hồi và mòn để xét ảnh hưởng của mòn đến thay đổi lượng sai lệch vị trí khi chịu tải. Tiếp tục mô hình hóa chi tiết chịu tải và biến dạng đàn hồi là hai chi tiết ghép nối tiếp như hệ hai lò xo nối tiếp, trong đó có một chi tiết (lò xo) có chiều dài ban đầu đúng bằng lượng mòn (L02). Hệ lực F cân bằng cùng được sử dụng trong các trường hợp chịu tải. Hình 2.7 mô tả hệ hai lò xo khi chưa chịu tải, khi chịu tải, khi từng lò xo chịu tải: Khi chưa mòn, chưa chịu tải Khi chưa mòn, chịu tải Khi mòn L02, chịu tải Hình 2.7 Hệ hai lò xo chịu tải Trên hình: F-F: hệ lực cân bằng; : biến dạng đàn hồi khi chưa mòn L01: kích thước còn lại sau mòn; L02: lượng mòn 1: biến dạng đàn hồi của L01; 2: biến dạng đàn hồi của L02 Khi chi tiết chưa mòn, lượng biến dạng của hệ ( t) khi chịu tải: t = (2.13) Khi chi tiết mòn đi lượng L02, lượng biến dạng của hệ ( s) khi chịu tải: s = L02 + 1 (2.14) 50 Sai lệch chiều dài tổng của hệ trước và sau mòn lượng L02: s - t = L02 + 1 - = L02 - 2 (2.15) Lượng biến dạng đàn hồi của vật rắn là vô cùng nhỏ so với kích thước ban đầu của nó ( 2 << L02). Do vậy, coi “ s - t = L02 - 2 L02” và có thể kết luận: “Lượng sai lệch vị trí do mòn chính là lượng mòn”. Sai lệch vị trí dọc trục do mòn của VMĐB là lượng mòn dọc trục. Mối quan hệ giữa lượng mòn dọc trục với lượng mòn theo phương pháp tuyến được xác định dựa vào các kích thước, hình dáng và vị trí hình học tương đối của các chi tiết. Hình 2.8 thể hiện vị trí tương đối giữa bi và trục vít, đai ốc trong bộ truyền VMĐB khi mòn Hình 2.8 Quan hệ giữa mòn tổng cộng và mòn dọc trục Trên hình: : góc nâng ren; : góc tiếp xúc; h: kích thước rãnh bi sau mòn; F: tải (N); mvm; mb; mdo lần lượt là các giá trị mòn của trục vít me, bi, đai ốc. Mòn tổng cộng U (mòn theo phương pháp tuyến các bề mặt tiếp xúc): U = mvm + mb+ mdo (2.16) Chiếu lên phương dọc trục vít me sẽ là lượng mòn dọc trục: Uc = (mtv+ mb+ mdo).Cos .Sin = U.Cos .Sin = z.U (2.17) Trong đó: z = (cos . sin ): hệ số tỷ lệ; UC: lượng mòn dọc trục. Sai lệch dọc trục do mòn ( m) chính bằng lượng mòn dọc trục (Uc),và tuyến tính với lượng mòn tổng cộng U. Giá trị sai lệch vị trí dọc trục của đai ốc là kết quả ảnh hưởng của nhiều nguyên nhân. Nếu tách lọc được ảnh hưởng của nguyên nhân mòn trong giá trị sai lệch vị trí tổng sẽ giúp xây dựng mối liên hệ giữa mòn dọc trục và sai lệch vị trí của đai ốc. Các nguyên nhân gây sai lệch vị trí đai ốc: Sai lệch do sai số tích lũy bước vít; Sai lệch do biến dạng đàn hồi; Sai lệch do biến dạng nhiệt; Sai lệch do mòn; Sai lệch do rung động và các yếu tố ngẫu nhiên khác,... Xét từng nguyên nhân để biết được đặc điểm tác F F 51 động cũng như ảnh hưởng của nó tới sai lệch vị trí đai ốc, từ đó sẽ cho phép phân biệt, nhận biết ảnh hưởng do nguyên nhân cần quan tâm. Sai lệch vị trí đai ốc do biến dạng đàn hồi phụ thuộc chủ yếu vào tải, vật liệu, và hình dạng, kích thước các chi tiết trục vít; bi; đai ốc, được mô tả bởi bảng 2.2 Bảng 2.2 Mô tả sai lệch vị trí đai ốc do biến dạng đàn hồi Tải nén Tải kéo C h ư a ch ịu t ải C h ư a ch u y ển đ ộ n g K h i ch ịu t ải K h i v ít m e q u ay n v ò n g T h eo R o ta ry E n co d er T h eo L in er S ca le Sai lệch vị trí đai ốc do sai số tích lũy bước vít: Sai lệch giữa khoảng cách danh nghĩa của hai bề mặt ren gần nhất và cùng phía, so với khoảng cách thực tế cũng của hai bề mặt gần nhất, cùng phía là sai lệch bước vít. Lượng sai lệch tích lũy bước vít chính là tích số giữa sai lệch bước vít nhân với số bước vít. 52 Sai lệch vị trí đai ốc do biến dạng nhiệt là một nhân tố quan trọng ảnh hưởng tới sai lệch vị trí đai ốc. Lượng sai lệch này phụ thuộc vào lượng biến đổi nhiệt độ, và vật liệu làm VMĐB. Nói cách khác, nó phụ thuộc vào vật liệu, chế độ công nghệ và thời gian làm việc ở chế độ công nghệ đó. Rung động là kết quả của sự tồn tại khoảng cách giữa các bề mặt lắp ghép khi các chi tiết có chuyển động tương đối, kết hợp với sự lệch tâm giữa trọng tâm của vật với tâm của chuyển động theo chu kỳ. Phương, chiều, độ lớn của tải liên tục thay đổi làm xuất hiện rung động dẫn tới kết quả đo vị trí đai ốc sẽ không ổn định. Khi tập hợp và thể hiện kết quả đo vị trí đai ốc dọc theo hành trình trên biểu đồ, sau nhiều lần đo, sẽ tạo nên một miền phân bố các giá trị đai ốc dọc theo hành trình. Dấu hiệu nhận biết sai lệch vị trí đai ốc do rung động và các yếu tố ngẫu nhiên là sự sai khác giá trị vị trí đai ốc tại các lần đo. Sai lệch do yếu tố rung động và các yếu tố ngẫu nhiên được loại bỏ bằng cách thực hiện nhiều lần một phép đo rồi lấy giá trị trung bình. Như phân tích ở trên, ảnh hưởng của các nguyên nhân: đàn hồi, sai số tích lũy bước vít, rung động, nhiệt độ, ... là những nguyên nhân gây sai lệch vị trí đai ốc, mức độ ảnh hưởng phụ thuộc vào giá trị (
File đính kèm:
luan_an_phuong_phap_xac_dinh_mon_doc_truc_vmdb_tren_thiet_bi.pdf